簡析長城汽車3DEXPERIENCE平臺的面向設計人員工程CAE在產(chǎn)品研發(fā)中的應用
2018-01-15 16:45:02· 來源:達索系統(tǒng)SIMULIA 2017年用戶大會優(yōu)秀論文 作者:滕孟巖 馬曉磊 李志強
在保證產(chǎn)品性能的前提下,最大可能的縮短研發(fā)周期是車企最迫切的需求,本文講述了達索的3DEXPERIENCE平臺中的CAE工具在我公司縮短汽車產(chǎn)品設計周期,提升設計人員設計能力上的應用。
本文來自:
達索系統(tǒng)SIMULIA 2017年用戶大會優(yōu)秀論文
滕孟巖,馬曉磊,李志強
長城汽車股份有限公司技術中心,河北省汽車工程技術研究中心,保定 071000
摘要:在保證產(chǎn)品性能的前提下,最大可能的縮短研發(fā)周期是車企最迫切的需求,本文講述了達索的3DEXPERIENCE平臺中的CAE工具在我公司縮短汽車產(chǎn)品設計周期,提升設計人員設計能力上的應用。
關鍵詞:縮短研發(fā)周期;3DEXPERIENCE平臺;提升設計能力;
1. 前言
進入21世紀尤其是中國加入WTO以來,汽車產(chǎn)業(yè)面臨的競爭壓力日益激烈,競爭的殘酷性要求企業(yè)必須迅速開發(fā)新車型,快速響應市場才能生存和發(fā)展[1]??焖夙憫袌鼍鸵笃嚻髽I(yè)在保證產(chǎn)品可靠性的基礎上,設計速度要更快、性能要更好、成本要更低。為了滿足這種挑戰(zhàn),很多企業(yè)已經(jīng)采用了CAE技術來縮短研發(fā)周期和改善產(chǎn)品性能。然而傳統(tǒng)的CAE分析是由專業(yè)的CAE部門開展,這些部門只進行CAE分析。需要設計部門輸入設計方案,分析完成后將分析結果及優(yōu)化方案反饋給設計部,設計部根據(jù)CAE、總布置、成型等多方意見進行設計修改,然后再發(fā)送CAE部門分析,多次循環(huán)才能完成產(chǎn)品設計,這樣不利于縮短產(chǎn)品設計周期,同時設計人員不能直接看到CAE結果,不知為何優(yōu)化,只能被動接受CAE優(yōu)化建議,不利于設計人員能力提升。這樣大大限制了CAE在設計過程中的作用。
3DEXPERIENCE平臺將產(chǎn)品設計與CAE分析完美的集成在了一起,設計工程師可以在熟悉的設計界面下直接進行CAE分析,更有利于設計人員學習;同時由于沒有幾何形狀的傳遞和轉換,數(shù)據(jù)完整性得到保證。
2. 3DEXPERIENCE平臺中CAE工具介紹
3DEXPERIENCE平臺針對不同學科有不同的CAE工具,本文重點介紹MDS及DRD模塊。
2.1 MDS
在靜力學載荷下進行常規(guī)的強度/剛度分析來評估產(chǎn)品的壽命來指導設計修改。
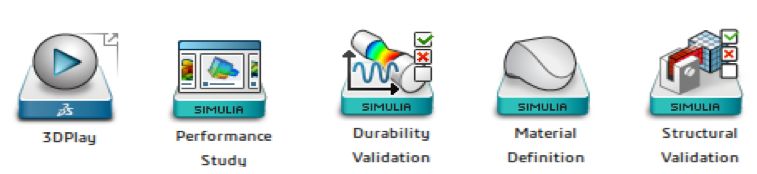
圖2.1 MDS模塊下命令
分析類型:結構分析、模態(tài)分析、熱分析、疲勞分析等;
模塊特點:具有向導式分析流程,操作十分簡便,易學;
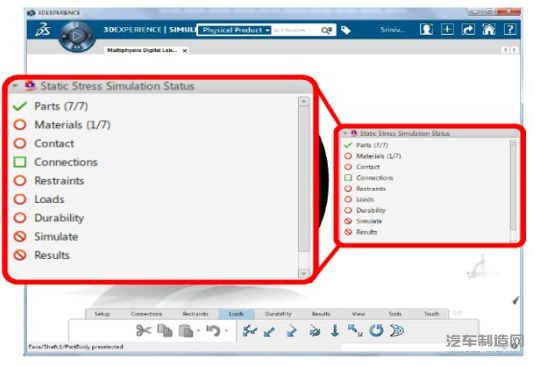
2.2 MDS向導式分析流程界面
2.2 DRD
在大量的載荷情況下利用有限元技術來評估產(chǎn)品的結構完整性,來進行指導設計決策 。

圖2.3 DRD模塊下命令
分析類型:靜力學分析、模態(tài)分析、頻響分析、屈曲分析、瞬態(tài)響應分析、穩(wěn)態(tài)傳熱分析、瞬態(tài)傳熱分析等;

圖2.4 DRD分析類型
模塊特點:操作命令分塊管理,可選網(wǎng)格類型全面,分析類型全面,操作比較簡便;
3. 應用情況
3.1 分析內容
MDS及DRD可以進行點焊、縫焊、螺栓連接、接觸、綁定、彈簧連接等絕大多數(shù)常用連接,可以進行車身、底盤中大部分件的分析。

圖3.1 DRD連接命令
長城汽車自2016年開始使用MDS及DRD模塊,以車身、底盤等部門做試點,先后經(jīng)過數(shù)次培訓,目前已有數(shù)百名設計人員掌握MDS及DRD模塊,可以獨立使用3DEXPERIENCE平臺進行產(chǎn)品設計與CAE分析,現(xiàn)階段主要進行單件及由焊接、螺栓連接組成的總成件分析,包括ACC支架等小支架,鑄鋁下擺臂、轉向節(jié)等鑄造單件,ECU支架總成、翼子板總成等較簡單的總成級部件的剛度強度及模態(tài)分析。
已經(jīng)開展的部分分析項目分析結果如圖3.2所示:
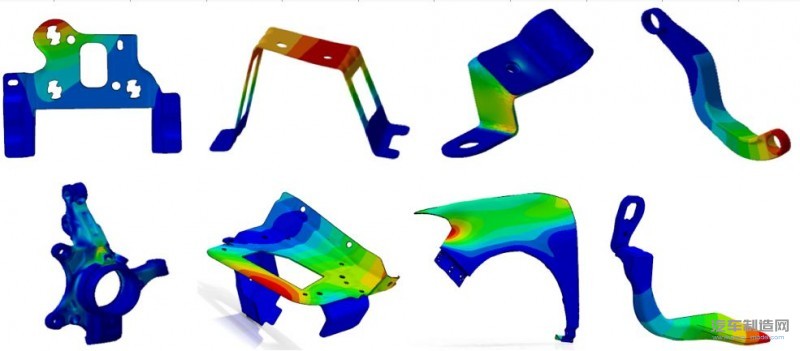
圖2.2 部分分析項目分析結果示意圖
3.2 分析精度對比
采用MDS及DRD進行支架剛度分析(網(wǎng)格均自動生成),結果與CAE分析結果相比精度均在95%以上,完全滿足設計CAE對分析結果精度的要求。
部分部件精度對比結果如圖3.3所示:
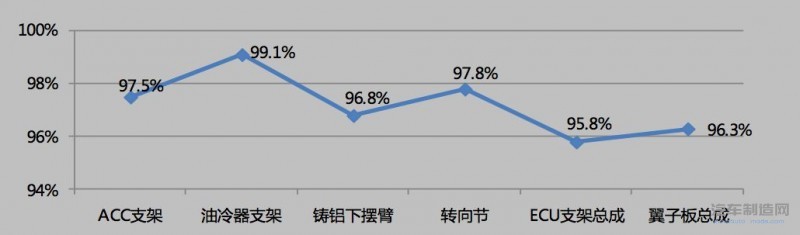
圖3.3MDS/DRD剛度分析結果與CAE分析結果精度對比
3.3 分析周期
采用MDS及DRD進行CAE分析,通常有限元模型創(chuàng)建、模型計算只需要幾分鐘到十幾分鐘,操作簡便易學;同時由于沒有幾何形狀的傳遞和轉換,數(shù)據(jù)完整性也能得到最大保證。
部分部件分析周期如圖3.4所示:
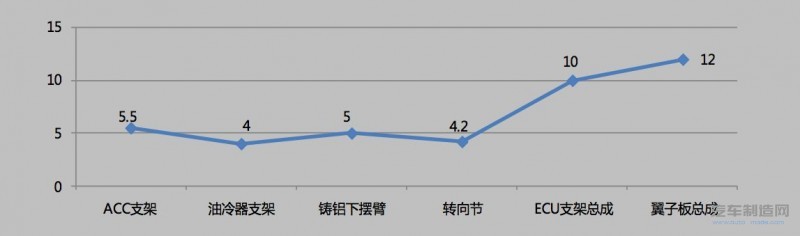
圖3.4 部分部件MDS/DRD分析周期(模型創(chuàng)建+計算單位min)
4. 公司收益
4.1 提升設計質量、縮短研發(fā)周期
底盤設計人員在某SUV車型轉向節(jié)設計中,使用3DEXPERIENCE平臺中的CAE工具,在設計完成后用5~10分鐘對轉向節(jié)進行初步分析,識別危險及薄弱位置,而后在設計環(huán)境下完成優(yōu)化,從而提升了設計質量,進而設計與CAE之間的交流輪次減少了1/4,縮短了產(chǎn)品研發(fā)周期。
4.2 多方案選優(yōu),快速準確的確定最優(yōu)方案
車身設計人員在某SUV雨刮支架的設計中,在面對多個設計方案不知該如何選擇的時候,使用3DEXPERIENCE平臺中的CAE工具完成對不同方案的對比分析,來選擇最佳的設計方案。
如表4.1所示:
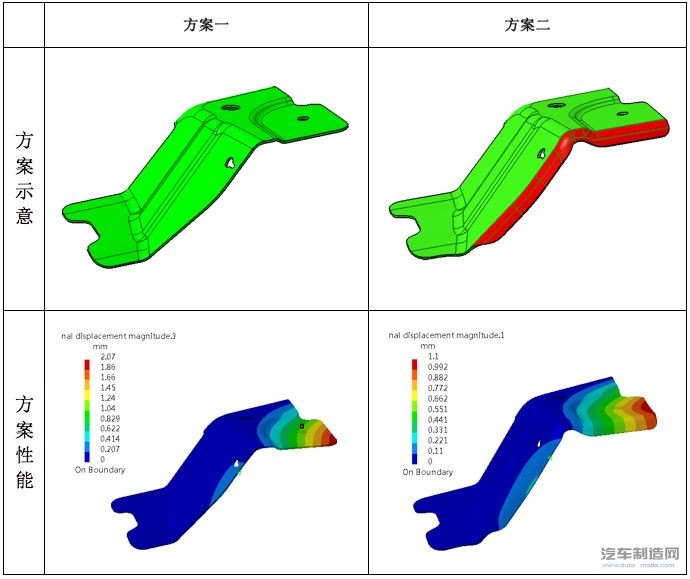
表4.1 某SUV右側雨刮支架多方案選優(yōu)
通過使用3DEXPERIENCE平臺中的CAE工具分析可知:增加翻邊后剛度顯著提升,且通過對比不同翻邊長度下部件的剛度變化,確定了翻邊最佳長度。
5. 結論
3DEXPERIENCE平臺中的CAE工具具有操作簡便、用時少、分析精度高的特點,能夠縮短汽車產(chǎn)品研發(fā)周期,有利于設計人員快速積累設計經(jīng)驗,能夠提升設計人員設計水平。
6. 參考文獻
1. 宋凱,王超,成艾國,周澤?;诳勺児r的車身覆蓋件抗凹性全流程優(yōu)化方法。機械科學與技術。
達索系統(tǒng)SIMULIA 2017年用戶大會優(yōu)秀論文
滕孟巖,馬曉磊,李志強
長城汽車股份有限公司技術中心,河北省汽車工程技術研究中心,保定 071000
摘要:在保證產(chǎn)品性能的前提下,最大可能的縮短研發(fā)周期是車企最迫切的需求,本文講述了達索的3DEXPERIENCE平臺中的CAE工具在我公司縮短汽車產(chǎn)品設計周期,提升設計人員設計能力上的應用。
關鍵詞:縮短研發(fā)周期;3DEXPERIENCE平臺;提升設計能力;
1. 前言
進入21世紀尤其是中國加入WTO以來,汽車產(chǎn)業(yè)面臨的競爭壓力日益激烈,競爭的殘酷性要求企業(yè)必須迅速開發(fā)新車型,快速響應市場才能生存和發(fā)展[1]??焖夙憫袌鼍鸵笃嚻髽I(yè)在保證產(chǎn)品可靠性的基礎上,設計速度要更快、性能要更好、成本要更低。為了滿足這種挑戰(zhàn),很多企業(yè)已經(jīng)采用了CAE技術來縮短研發(fā)周期和改善產(chǎn)品性能。然而傳統(tǒng)的CAE分析是由專業(yè)的CAE部門開展,這些部門只進行CAE分析。需要設計部門輸入設計方案,分析完成后將分析結果及優(yōu)化方案反饋給設計部,設計部根據(jù)CAE、總布置、成型等多方意見進行設計修改,然后再發(fā)送CAE部門分析,多次循環(huán)才能完成產(chǎn)品設計,這樣不利于縮短產(chǎn)品設計周期,同時設計人員不能直接看到CAE結果,不知為何優(yōu)化,只能被動接受CAE優(yōu)化建議,不利于設計人員能力提升。這樣大大限制了CAE在設計過程中的作用。
3DEXPERIENCE平臺將產(chǎn)品設計與CAE分析完美的集成在了一起,設計工程師可以在熟悉的設計界面下直接進行CAE分析,更有利于設計人員學習;同時由于沒有幾何形狀的傳遞和轉換,數(shù)據(jù)完整性得到保證。
2. 3DEXPERIENCE平臺中CAE工具介紹
3DEXPERIENCE平臺針對不同學科有不同的CAE工具,本文重點介紹MDS及DRD模塊。
2.1 MDS
在靜力學載荷下進行常規(guī)的強度/剛度分析來評估產(chǎn)品的壽命來指導設計修改。
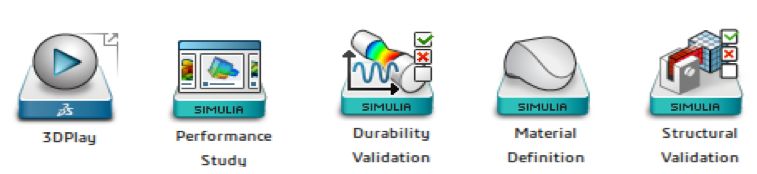
圖2.1 MDS模塊下命令
分析類型:結構分析、模態(tài)分析、熱分析、疲勞分析等;
模塊特點:具有向導式分析流程,操作十分簡便,易學;
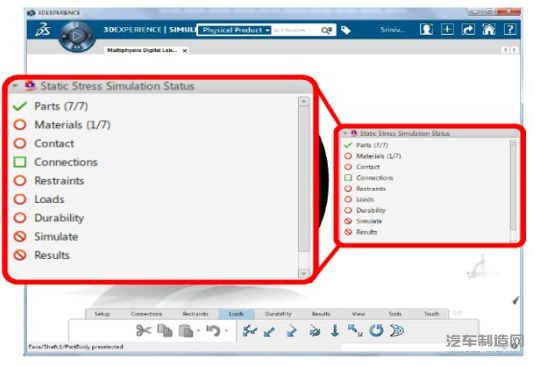
2.2 MDS向導式分析流程界面
2.2 DRD
在大量的載荷情況下利用有限元技術來評估產(chǎn)品的結構完整性,來進行指導設計決策 。

圖2.3 DRD模塊下命令
分析類型:靜力學分析、模態(tài)分析、頻響分析、屈曲分析、瞬態(tài)響應分析、穩(wěn)態(tài)傳熱分析、瞬態(tài)傳熱分析等;

圖2.4 DRD分析類型
模塊特點:操作命令分塊管理,可選網(wǎng)格類型全面,分析類型全面,操作比較簡便;
3. 應用情況
3.1 分析內容
MDS及DRD可以進行點焊、縫焊、螺栓連接、接觸、綁定、彈簧連接等絕大多數(shù)常用連接,可以進行車身、底盤中大部分件的分析。

圖3.1 DRD連接命令
長城汽車自2016年開始使用MDS及DRD模塊,以車身、底盤等部門做試點,先后經(jīng)過數(shù)次培訓,目前已有數(shù)百名設計人員掌握MDS及DRD模塊,可以獨立使用3DEXPERIENCE平臺進行產(chǎn)品設計與CAE分析,現(xiàn)階段主要進行單件及由焊接、螺栓連接組成的總成件分析,包括ACC支架等小支架,鑄鋁下擺臂、轉向節(jié)等鑄造單件,ECU支架總成、翼子板總成等較簡單的總成級部件的剛度強度及模態(tài)分析。
已經(jīng)開展的部分分析項目分析結果如圖3.2所示:
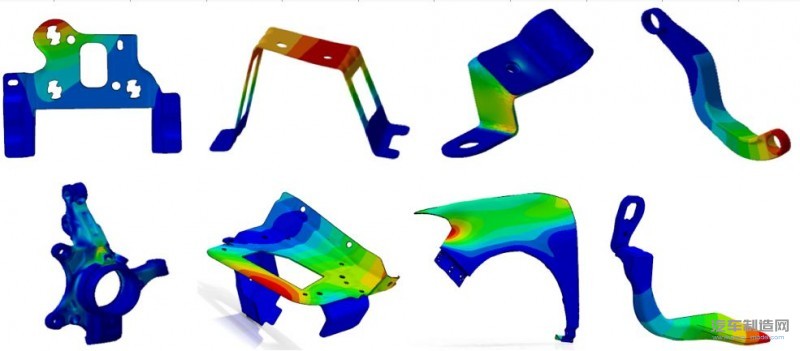
圖2.2 部分分析項目分析結果示意圖
3.2 分析精度對比
采用MDS及DRD進行支架剛度分析(網(wǎng)格均自動生成),結果與CAE分析結果相比精度均在95%以上,完全滿足設計CAE對分析結果精度的要求。
部分部件精度對比結果如圖3.3所示:
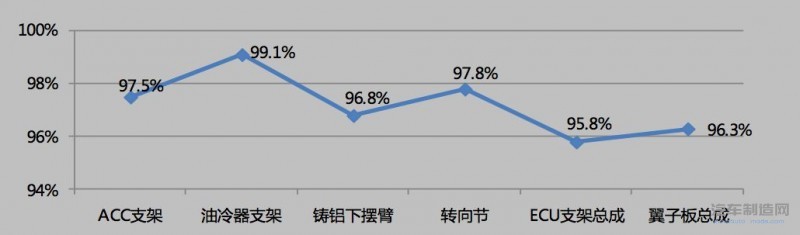
圖3.3MDS/DRD剛度分析結果與CAE分析結果精度對比
3.3 分析周期
采用MDS及DRD進行CAE分析,通常有限元模型創(chuàng)建、模型計算只需要幾分鐘到十幾分鐘,操作簡便易學;同時由于沒有幾何形狀的傳遞和轉換,數(shù)據(jù)完整性也能得到最大保證。
部分部件分析周期如圖3.4所示:
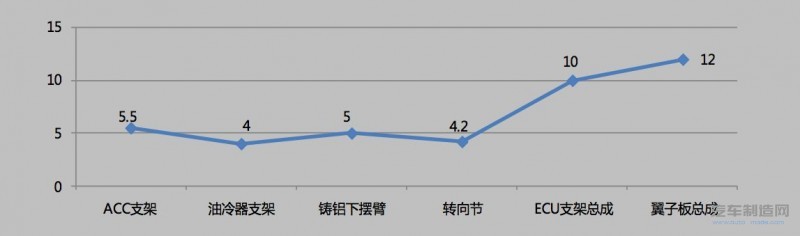
圖3.4 部分部件MDS/DRD分析周期(模型創(chuàng)建+計算單位min)
4. 公司收益
4.1 提升設計質量、縮短研發(fā)周期
底盤設計人員在某SUV車型轉向節(jié)設計中,使用3DEXPERIENCE平臺中的CAE工具,在設計完成后用5~10分鐘對轉向節(jié)進行初步分析,識別危險及薄弱位置,而后在設計環(huán)境下完成優(yōu)化,從而提升了設計質量,進而設計與CAE之間的交流輪次減少了1/4,縮短了產(chǎn)品研發(fā)周期。
4.2 多方案選優(yōu),快速準確的確定最優(yōu)方案
車身設計人員在某SUV雨刮支架的設計中,在面對多個設計方案不知該如何選擇的時候,使用3DEXPERIENCE平臺中的CAE工具完成對不同方案的對比分析,來選擇最佳的設計方案。
如表4.1所示:
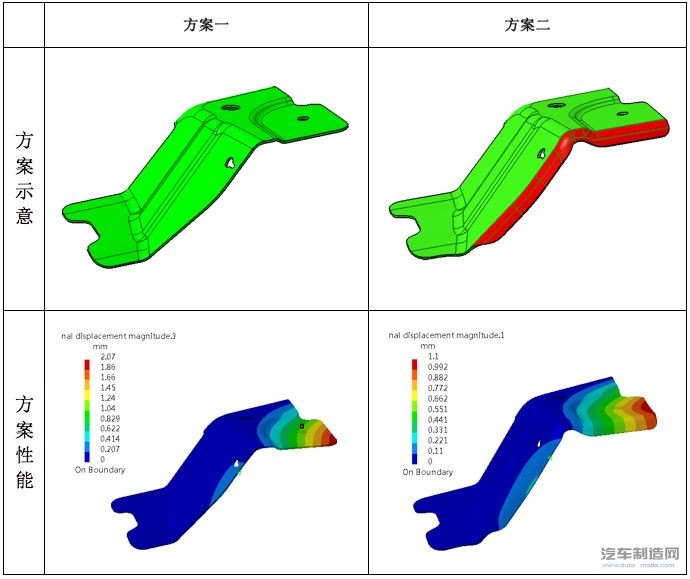
表4.1 某SUV右側雨刮支架多方案選優(yōu)
通過使用3DEXPERIENCE平臺中的CAE工具分析可知:增加翻邊后剛度顯著提升,且通過對比不同翻邊長度下部件的剛度變化,確定了翻邊最佳長度。
5. 結論
3DEXPERIENCE平臺中的CAE工具具有操作簡便、用時少、分析精度高的特點,能夠縮短汽車產(chǎn)品研發(fā)周期,有利于設計人員快速積累設計經(jīng)驗,能夠提升設計人員設計水平。
6. 參考文獻
1. 宋凱,王超,成艾國,周澤?;诳勺児r的車身覆蓋件抗凹性全流程優(yōu)化方法。機械科學與技術。
編輯推薦
最新資訊
-
跨越速運憑什么“圈粉”萬千客戶?“
2025-07-01 14:42
-
數(shù)智破局啟新篇?生態(tài)共生再啟程 —
2025-06-27 20:13
-
助力汽車零部件產(chǎn)線智能化升級,西門
2025-06-27 13:59
-
BBA集體轉向!放棄全面電動化
2025-06-26 17:32
-
比換柜省錢,比自研省心,西門子Xcel
2025-06-25 15:07