汽車沖壓材料成本控制策略探討
摘要
為從材料成本控制角度降低沖壓成本,從材料利用率提升、鈑金制造新工藝應用、合理選材 3 個方面,結(jié)合具體的應用案例,探討了汽車沖壓材料成本的控制策略。首先,針對材料利用率可從產(chǎn)品協(xié)同開發(fā)、沖壓工藝優(yōu)化及沖壓廢料再利用 3 個方面進行提升。其次,鈑金制造新工藝方面可采用輥壓、集成式熱成形等工藝代替單件沖壓或多件單獨沖壓后點焊的工藝。最后,針對合理選材,給出了同強度鋼材選擇原則、烘烤硬化鋼代替無間隙原子鋼和高強度鋼的應用建議。
關(guān)鍵詞:材料成本 材料利用率 產(chǎn)品協(xié)同 工藝優(yōu)化 合理選材
1 前言
隨著全球汽車行業(yè)的快速發(fā)展和競爭的加劇,主機廠對降低成本、提高效率和保持競爭力的需求日益凸顯[1]。材料成本控制作為汽車沖壓制造的重要一環(huán),成為汽車制造企業(yè)關(guān)注的焦點之一。有效的材料成本控制不僅可以直接降低生產(chǎn)成本,還可以提高資源利用效率,推動工藝技術(shù)的創(chuàng)新,提升產(chǎn)品質(zhì)量,從而實現(xiàn)企業(yè)的可持續(xù)發(fā)展。
汽車沖壓件的制造成本包括一次性成本和長期成本[2]。一次性成本主要包括設(shè)備成本與模具成本,長期成本包括設(shè)備部件的損耗成本、人員成本、能源成本、材料成本等。其中,材料成本隨著產(chǎn)量增加呈線性增加,材料成本控制對于沖壓降本非常重要[3-5]。
本文從產(chǎn)品協(xié)同開發(fā)、沖壓工藝優(yōu)化、廢料的利用、新工藝應用、選材的原則等方面探討汽車沖壓材料成本控制的具體策略和方法。
綜合來看,材料成本的控制措施主要包括 3 個方面:提升材料利用率、采用新的鈑金制造工藝、合理選材。本文針對這 3 個方面,結(jié)合具體應用案例進行探討。
2 材料利用率提升
材料利用率可從產(chǎn)品協(xié)同開發(fā)、沖壓工藝優(yōu)化以及沖壓廢料再利用 3 個維度提升[6]。
2.1 產(chǎn)品協(xié)同開發(fā)
在沖壓件同步工程階段,產(chǎn)品設(shè)計決定零件的材料利用率上限[7]。因此,需要以材料利用率為目標進行產(chǎn)品協(xié)同開發(fā),對產(chǎn)品進行合理的合并、拆分、優(yōu)化局部特征及公差定義。
2.1.1 零件合并設(shè)計
圖 1 為某車型的后蓋合并設(shè)計案例,原始方案設(shè)計分為后蓋上部與后蓋下部 2 個零件,材料均為厚度為 0.6 mm 的 CR210IF,將 2 個零件合并設(shè)計為一體式后蓋,可以減少拉延補充面,材料利用率由43.9% 提升至 46.9%。
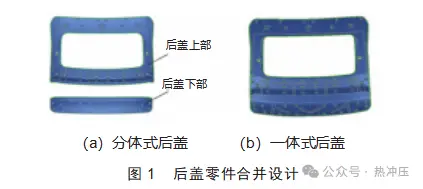
2.1.2 零件拆分設(shè)計
圖2為某車型的側(cè)圍C柱內(nèi)板拆分設(shè)計案例,將整體式零件拆為2個零件,并焊接。零件拆分后,沖壓綜合材料利用率由45.3%提升至50.4%。
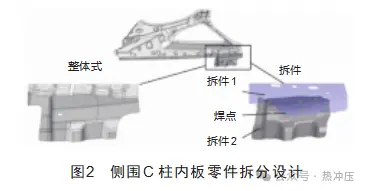
需要注意的是,拆件方案雖有利于零件材料利用率提升及成形性控制,但會增加焊接成本,對NVH 性能可能有不利影響,需要基于更全面的評價結(jié)果進行方案取舍。
2.1.3 零件局部優(yōu)化
圖 3 為拼焊板(Tailor-Welded-Blank,TWB)天窗加強件拼焊縫位置優(yōu)化示例,該零件由厚度為2.4 mm 和 1.5 mm 的 CR3 拼焊而成,在保證車輛強度及沖壓成形性能的前提下,將焊縫由中間位置向兩側(cè)移動,當移動距離為 70 mm 時,所需料片總質(zhì)量由 20.3 kg 減少至 19.0 kg,單車約減少 1.3 kg材料。
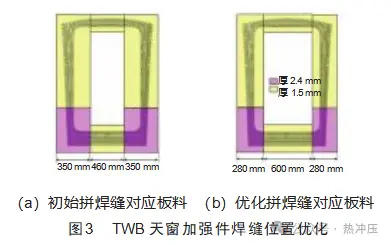
2.1.4 合理定義零件公差
常規(guī)產(chǎn)品邊界公差要求為±0.5 mm,需要采用 拉延后精切邊的工藝,一般工藝要求留有 5~ 10 mm 切邊余量 。若將產(chǎn)品邊界公差放大為±2 mm,則可在工藝上對零件邊線使用預開法 ,對影響材料利用率的敏感區(qū)域進行板料邊界精準預測 ,經(jīng)過拉延或成形后即可滿足邊界公差要求 ,取消后序精切邊 。 圖 4為熱成形加強件案例 ,圖 4a 為常規(guī)公差定義下的沖壓狀態(tài) ,料片尺寸較大且沖壓后料片距離零件邊界有較大余量,圖 4b 為合理公差定義后的沖壓狀態(tài) ,料片尺寸較小且沖壓后料片距 離零件邊界幾乎沒有余量,材料利用率由 85.3% 提升至 91.2%。
2.2 沖壓工藝優(yōu)化
沖壓工藝方案對材料利用率具有顯著影響,本質(zhì)上是考慮如何減少工藝補充面造成的材料浪費,可以通過淺拉延及其衍生方法的應用、合并拉延、零件嵌套拉延以及合理的落料排樣提升材料利用率。
2.2.1 淺拉延及其衍生方法的應用
在保證零件質(zhì)量的前提下,盡可能減小補充面可提升材料利用率,淺拉延是最常用的方法,下面介紹淺拉延及其衍生方法。
a. 單純淺拉延:零件的拉延深度直接決定工藝補充面的面積,淺拉延可以顯著減小工藝補充面的面積,進而提升材料利用率。圖 5 為某翼子板采用不同拉延深度的材料利用率對比,圖 5a 為采用較深的壓料面設(shè)計的深拉延狀態(tài),圖 5b 為壓料面抬升后的淺拉延狀態(tài),采用淺拉延后材料利用率由 33.6% 提升至 37.5%。
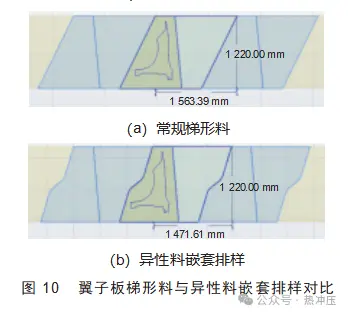
一般來說,門外板、牌照板等平坦零件可采用鎖死筋與淺拉延配合的方式大幅提升材料利用率。但為保證材料被充分拉伸,零件通常有最小減薄率的要求,以利于回彈尺寸及表面質(zhì)量控制,實際應用時應結(jié)合仿真結(jié)果確定最小拉延深度。
b. 開口拉延:當零件某個方向或某些局部的拉
延深度為 0 時即為開口拉延,屬于淺拉延的衍生方法。圖6為側(cè)圍內(nèi)板采用開口拉延和閉口拉延的對比,在零件上、下兩側(cè)將圖 6a 的封閉拉延設(shè)計改為圖 6b 的開口拉延,可使卷料寬度由 1 300 mm 減小至 1 160 mm。
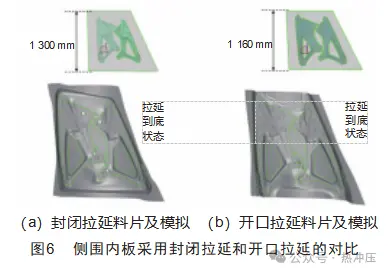
需要注意的是,開口拉延狀態(tài)下零件的拉伸充分性低于封閉拉延,需要基于零件的拉伸狀態(tài)以及回彈情況確定更合理的拉延方案。
c. 三動拉延:三動拉延為淺拉延的另一種衍生方法。一般而言,拉延工藝的壓料面均設(shè)置于零件的同一側(cè),以保證壓料閉合狀態(tài)良好。例如,單動拉延時壓料面均位于零件下方,雙動拉延時壓料面均位于零件上方。對于深度較大的零件,該設(shè)計往往需要較大的工藝補充面,而采用三動拉延可大幅降低工藝補充面,即外部的壓料面設(shè)計成上部和下部均為運動部件。
以后蓋內(nèi)板為例,圖 7 為采用三動拉延和傳統(tǒng)拉延的工藝面對比,三動拉延工藝面可以使工藝面的線長顯著小于傳統(tǒng)拉延工藝面,特別是在零件的緩沖塊安裝面和鎖安裝面附近,線長減少量可達 70~80 mm,從而顯著提升材料利用率。
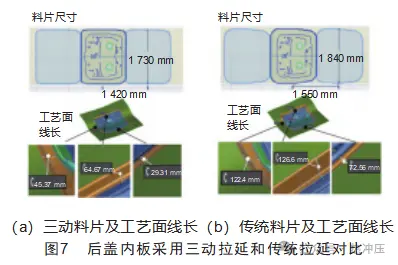
2.2.2 合并成形
對于門外板、無框門內(nèi)板、部分后蓋等常見的覆蓋件,采用合并成形能夠顯著提高材料利用率。圖 8 為典型零件采用合并成形方式的案例,門外板材料利用率由圖 8a 單獨拉延的 73.2% 提升至圖 8b合并拉延的 77.3%。
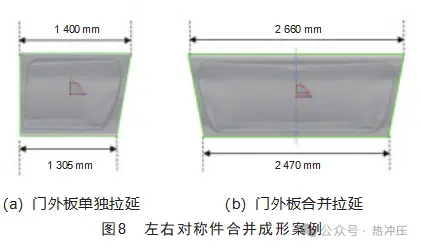
合并成形不僅局限于左右對稱零件,只要 2 個或多個零件使用的材料相同且零件尺寸和型面走勢滿足合并成形工藝要求即可進行合并成形設(shè)計。需要注意的是,該設(shè)計需在同步工程階段進行模擬驗證。
2.2.3 套件生產(chǎn)
還有一種特殊的合并成形是在較大零件的非產(chǎn)品區(qū)域嵌套較小的零件。例如,前蓋內(nèi)板減輕孔、門內(nèi)板窗孔、后蓋窗孔、天窗加強件窗孔等區(qū)域均可以考慮嵌套具有相同材料屬性的小尺寸簡單零件。圖 9 為后蓋嵌套前蓋鎖加強件,綜合材料利用率由嵌套前的 53.5% 提升至嵌套后 56.4%。
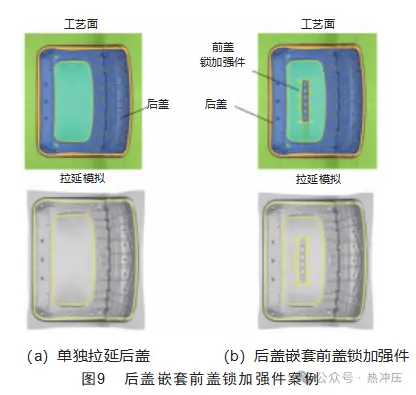
2.2.4 落料排樣
對料片尺寸的優(yōu)化也是常用的材料降本手段,本質(zhì)上是減少工藝補充面的材料消耗。將常規(guī)的方料、梯形料等規(guī)則形狀料片改為不規(guī)則的形狀,進行落料嵌套,可在一定程度上提升利用率。
圖 10 為翼子板排樣優(yōu)化案例,從圖 10a 的常規(guī)梯形料優(yōu)化為圖 10b 的異性料嵌套排樣后,單個零件可節(jié)省約 0.3 kg 材料。需要注意的是,異形料增加了落料模具成本,因此,需要結(jié)合預期產(chǎn)量等指標綜合考慮總成本的影響。
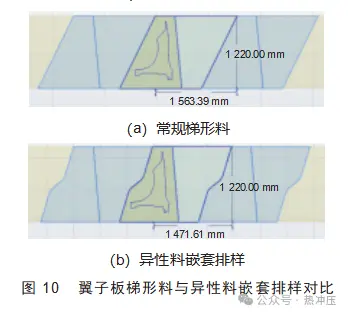
上述案例是針對一個零件的料片進行優(yōu)化與嵌套排樣。此外,還可以對不同的零件在同一個卷料上進行嵌套排樣,從而達到更高的綜合材料利用率。
對料片進行嵌套同樣存在風險,例如,開模后如果發(fā)生零件設(shè)計變更,嵌套方案的調(diào)整靈活性比方料或梯形料等常規(guī)方案要差,某些情況下可能會犧牲材料利用率,因此,需要結(jié)合零件的更改可能性進行合理選擇。
2.3 廢料再利用
將沖壓廢料再利用于其他零件能夠大幅降低材料成本。以冷沖鋼材 CR3 為例,沖壓廢料銷售費用比沖壓前的原材料采購費用低約 5 元/kg。沖壓廢料分為拉延前和拉延后 2 種。拉延前廢料是在開卷落料階段產(chǎn)生的,廢料與母材性能一致。拉延后廢料是拉延后切割獲得的,相比母材已經(jīng)有一定的減薄和塑性變形強化。
2.3.1 拉延前的廢料利用
側(cè)圍等零件通常有較大落料廢料,可用于較小零件的沖壓。圖 11 為某側(cè)圍廢料再利用案例,其門洞及車頂區(qū)域的 3 塊廢料可分別用于 2 個隔板、2 個行禮箱封板及 1 個尾燈支架蓋板零件沖壓,單個側(cè)圍可重復利用的廢料約為 0.75 kg。
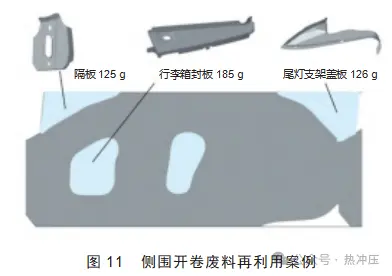
常規(guī)落料線無專門收集廢料的裝置,需按照廢料收集的需要進行改造,一般采用廢料小車。
2.3.2 拉延后的廢料利用
由于拉延后的廢料性能發(fā)生變化,需進行試驗得到拉延后材料的參數(shù),基于更新的模擬材料卡進行零件可制造性分析,才可應用于其他零件的制造。
表 1 為厚度為 0.8 mm 的 CR3 用于某車頂拉伸前后的材料參數(shù)對比,拉伸后選取天窗區(qū)域材料進行性能檢測,材料拉伸后的成形性能相關(guān)指標均有不同程度的降低。
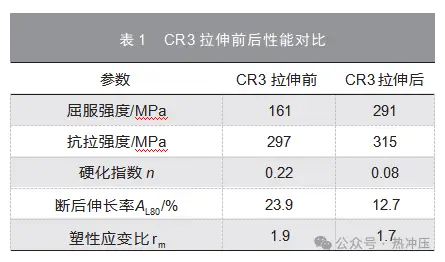
圖 12 為基于 2 種不同的材料參數(shù)對相同拉延工藝下的尾燈封板進行成形模擬的結(jié)果,使用拉伸后的 CR3成形性明顯惡化。因此,對拉延后的廢料利用務必要基于合理的材料性能作為分析前提。
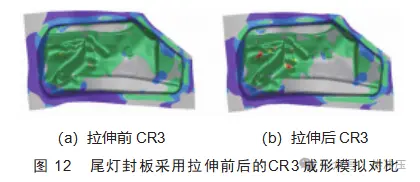
圖 13 為車頂拉延后天窗區(qū)域廢料利用案例。圖 13a 方案 1 是將廢料用于 4 個相同的車頂后橫梁,圖 13b 方案 2 是將廢料用于 3 個不同零件,包括1 對左右對稱件 D 柱加強板和 1 個非對稱件車頂后橫梁。該車型所有車頂都有天窗,從零件數(shù)量配比的角度看,更推薦方案 2,因為車頂與廢料再生產(chǎn)的零件數(shù)量配比是 1∶1,更經(jīng)濟。
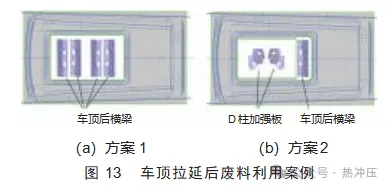
3 應用鈑金制造替代工藝
某些特定的產(chǎn)品可采用替代工藝,相比常規(guī)單件冷沖壓工藝或者多個單件沖壓后再焊接為總成的工藝具有更大的材料成本優(yōu)勢。常用的替代工藝包括輥壓和集成式熱成形。
3.1 輥壓
導軌、門檻、梁類件可采用輥壓工藝代替沖壓,典型零件有前后防撞梁、座椅滑軌、座椅橫梁、門檻加強件、車窗玻璃導軌等[8],目前已有部分量產(chǎn)車型使用輥壓制造出厚度為 2.0 mm、抗拉強度為 1 700 MPa 的梁類件。
圖 14 為某車窗玻璃導軌結(jié)構(gòu)及輥壓成形模擬結(jié)果,相比沖壓可提升材料利用率及生產(chǎn)效率。
3.2 集成式熱成形
集成式熱成形可以代替“多個單件沖壓后再 焊接”,熱成形需要的補充面相較冷沖壓要小 ,同 時節(jié)省了 2 個沖壓件用于焊接的搭接區(qū)域。
圖 15 為該方案的典型應用案例 ,用于一體式(a)拉伸前 CR3 (b)拉伸后 CR3門環(huán)制造 。
圖 15a 為常規(guī)方案,需要將多個件單獨 沖壓成形后再焊接為整體門環(huán) 。 圖 15b 為集成式 熱成形方案,將料片拼焊為環(huán)形料片后,再整體熱成形 。零件質(zhì)量由 23. 1 kg 減輕至 19.2 kg,原材料 由 41.3 kg 減輕至 32. 1 kg。
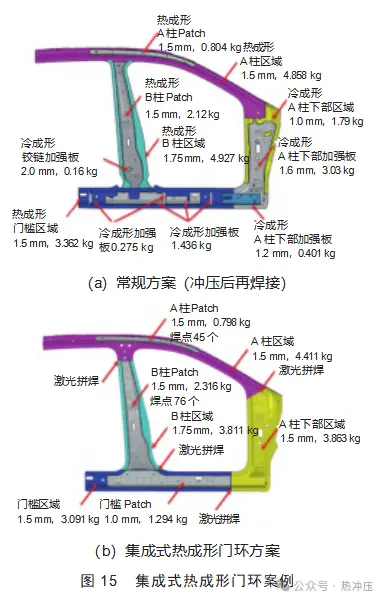
2 種方案的經(jīng)濟性對比如表 2 所示 。 目前熱成形門環(huán)最成熟的方案是鋁硅鍍層板加鍍層剝離拼焊,由于專利保護原因,其單片坯料成本較高。近年來 ,針對原材料的薄鍍層 、鍍鋅 、無鍍層等低成本材料方案以及針對拼焊工藝的無剝離鍍層或半剝離鍍層填絲焊已有大量研究 。隨著這些低成本方案的逐步成熟 ,集成式熱成形技術(shù)的成本優(yōu)勢會更加明顯。
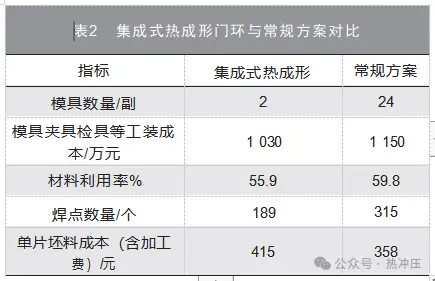
需要注意的是,集成式熱成形門環(huán)相比常規(guī)門環(huán)方案有一定的技術(shù)難度,包括:拼焊板質(zhì)量的控制、大尺寸熱成形件的生產(chǎn)穩(wěn)定性、焊縫位置的成形性控制、采用低成本裸板需要進行噴丸處理難以保證生產(chǎn)穩(wěn)定性等。
4 合理選材
材料的牌號、厚度、鍍層等對材料價格均有影響,進行產(chǎn)品定義時,在滿足車輛性能要求的前提下合理選材可顯著降低成本。下面針對外覆蓋件常用材料說明低成本選材的原則。
4.1 同強度鋼材選擇原則
相同強度的鋼材,其價格一般與零件的成形性正相關(guān),即成形性越好的材料價格越高,因此,盡可能通過優(yōu)化零件結(jié)構(gòu),使性能一般的材料滿足成形性要求。
例 如 ,相 同 厚 度 的 CR3 相 比 CR4 成 本 約 低350 元/t。圖 16為針對 CR3門內(nèi)板的成形性優(yōu)化案例,原始產(chǎn)品拔模角度較小,采用 CR4 成形性符合要求,采用CR3成形開裂。將產(chǎn)品拔模角放大,采用CR3也能夠滿足成形性要求,從而降低材料成本。
4.2 烘烤硬化鋼代替無間隙原子鋼
在設(shè)計翼子板、門外板、前蓋外板等覆蓋件時,有 2 種鋼經(jīng)常被選用:一是無間隙原子鋼,在超低碳鋼中加入適量的鈦或鈮,使鋼中的碳、氮間隙原子完全被固定成碳、氮化物,鋼中沒有間隙原子存在;二是烘烤硬化鋼,在低碳鋼或超低碳鋼中保留一定量的固溶碳原子,必要時通過添加磷等固溶強化元素提高強度[9],鋼板成形后經(jīng)涂漆烘烤處理,強度及抗凹性會進一步提高[10]。
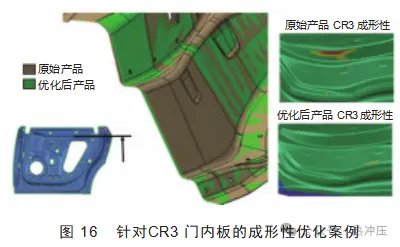
為降低成本,充分利用烘烤硬化鋼的成本優(yōu)勢與烘烤后性能提升的特點替代無間隙原子鋼。表3為無間隙原子鋼 CR210IF 與烘烤硬化鋼 CR180BH的對比,油漆烘房烘烤前二者成形性均可滿足零件成形要求,烘烤后二者強度指標較為接近,后者價格比前者低約 150 元/t,因此,可在保證成形性及零件強度與抗凹形的前提下顯著降低成本。
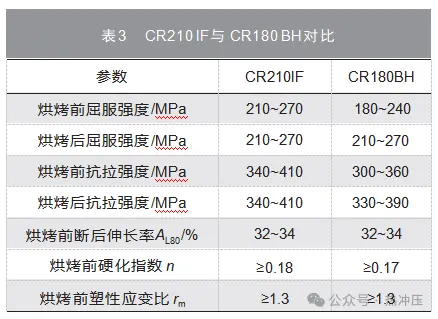
需要注意的是,烘烤硬化鋼具有時效性,通常需要在生產(chǎn)后 3~6 個月內(nèi)使用完畢。
4.3 選用高強度鋼材
采用厚度更薄的高強鋼替代低強度鋼可降低材料成本,該方案常見于結(jié)構(gòu)件,也可用于部分外覆蓋件。
表 4 為門外板采用常規(guī)材料 CR180BH 與替代材料 DP500 的對比,由于后者強度更高,抗凹性更好,可將零件厚度由 0.65 mm 減小至 0.6 mm,甚至更低。以某 A 級 SUV 為例,相比 CR180BH,采用DP500 可降低整車 4 個門外板材料約 1.25 kg,在材料單價少量增加的情況下,顯著降低材料成本。
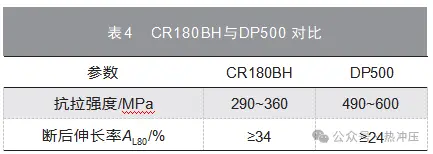
需要注意的是,采用 DP500 進行外覆蓋件設(shè)計需要針對高強鋼回彈進行合理的尺寸補償控制。
5 結(jié)束語
本文從材料利用率提升、鈑金制造新工藝應用、合理選材 3 個方面探討了汽車沖壓材料成本的控制策略,得到以下結(jié)論:
a 提升材料利用率本質(zhì)上是要盡可能減少工藝補充面的面積。具體實現(xiàn)途徑包括:對產(chǎn)品進行合理的劃分和公差定義,采用盡可能小的成形深度和補充面設(shè)計沖壓工藝,對無法避免的工藝廢料進行再利用。
b 采用特殊工藝并設(shè)計相應的零件。采用輥壓、集成式熱成形等工藝代替?zhèn)鹘y(tǒng)工藝,可一定程度上降低材料成本。
c 在不影響零件功能及成形質(zhì)量的前提下,應選用綜合成本更低的材料。如基于同強度鋼材選擇原則,采用烘烤硬化鋼代替無間隙原子鋼;用更薄的高強度鋼替代厚的低強度鋼等。
如何更好地兼顧材料成本、產(chǎn)品功能要求及制造質(zhì)量穩(wěn)定性,是上述策略實施過程中需要重點關(guān)注的問題,也是需要進一步研究的課題。
參考文獻:
[1] 劉曉林. 成本定生死,車企開啟技術(shù)和材料降本新競賽[N].經(jīng)濟觀察報, 2024-01-29(14).
[2] 劉可偉 . 汽車行業(yè)沖壓成本的控制方法[J]. 模具制造,2021, 21(10): 6-9.
[3] 呂良, 段英慧, 韓振強, 等. 整車廠沖壓件完全成本構(gòu)成簡析[J]. 鍛造與沖壓, 2020(10): 56-60.
[4] 曹亞東, 羅亮 . 汽車沖壓件成本核算方法研究[J]. 汽車實用技術(shù), 2018(24): 283-285.
[5] 徐明琦, 王彥, 閆麗紅, 等. 材料技術(shù)在商用車沖壓成本控制中的應用[J]. 汽車工藝與材料, 2018(11): 53-56.
[6] 王文華 . 汽車沖壓件成本模型研究[J]. 汽車工藝師,2023(4): 60-64.
[7] 蔣磊, 陳天鐸, 王龍, 等. 提升白車身覆蓋件材料利用率的沖壓工藝方案[J]. 汽車工程師, 2020(9): 13-16.
[8] 謝貴山, 黃宗斌, 趙肖斌, 等. 汽車車身的輕量化設(shè)計探討[J]. 汽車零部件, 2023(2): 80-84.
[9] 胡吟萍, 李國彬, 段小平, 等. 汽車覆蓋件用熱鍍鋅烘烤硬化鋼 H180BD的開發(fā)[C]// 2009年汽車用鋼生產(chǎn)及應用技術(shù)國際研討會, 2024.
[10] 葉仲超, 段小平. 烘烤硬化鋼的硬化特性及機理[J]. 鋼
鐵研究, 2011, 39(1): 35-37.
-
乘用車金屬沖壓
2025-05-29 -
沖壓技術(shù)在電機疊片制造的應用
2024-09-06 -
車身零部件包邊質(zhì)量控制要點
2024-09-05 -
輕量化技術(shù)——熱汽脹形工藝技術(shù)解析
2024-09-04
最新資訊
-
跨越速運憑什么“圈粉”萬千客戶?“
2025-07-01 14:42
-
數(shù)智破局啟新篇?生態(tài)共生再啟程 —
2025-06-27 20:13
-
助力汽車零部件產(chǎn)線智能化升級,西門
2025-06-27 13:59
-
BBA集體轉(zhuǎn)向!放棄全面電動化
2025-06-26 17:32
-
比換柜省錢,比自研省心,西門子Xcel
2025-06-25 15:07