大凸緣薄壁件沖壓成形失效分析及解決方案
2019-03-25 14:58:45· 來源:顧建剛 鍛造與沖壓
某排氣組件中單件XX.034前板為大凸緣薄壁零件,在開發(fā)前期采用常規(guī)拉深工藝進行試制,發(fā)現(xiàn)中間拉深部位出現(xiàn)了不同程度的減薄及破裂等失效現(xiàn)象,后通過對失效件進行研究分析,精確工藝計算,合理優(yōu)化成形方案,完善模具結(jié)構(gòu),成功克服失效
某排氣組件中單件XX.034前板為大凸緣薄壁零件,在開發(fā)前期采用常規(guī)拉深工藝進行試制,發(fā)現(xiàn)中間拉深部位出現(xiàn)了不同程度的減薄及破裂等失效現(xiàn)象,后通過對失效件進行研究分析,精確工藝計算,合理優(yōu)化成形方案,完善模具結(jié)構(gòu),成功克服失效現(xiàn)象,順利完成試制。通過對零件工序間工藝余料的精確計算,提出沖壓件工序間“儲料”概念,為后續(xù)類似結(jié)構(gòu)件成形提供成熟經(jīng)驗。
XX.034前板為某動力裝置排氣組件之組成單件,外形整體為拉深件,中間拉深方向與外緣拉深方向成反向,最外緣直徑與內(nèi)圓直徑比值達3.86,為典型的大凸緣件。
由于此件形狀規(guī)則,同時材料具有良好的沖壓性能,在試制前期采用常規(guī)拉深工藝,中間拉深模采用常規(guī)90°變形率拉深法(即凹模為直角過渡),但在實際加工過程中發(fā)現(xiàn)中間拉深部位轉(zhuǎn)接R角處出現(xiàn)了劇烈減薄及破裂等失效現(xiàn)象。
針對失效現(xiàn)象,對實物零件進行解剖分析研究,嘗試減小工序間變形率,提出工序間進行“儲料”概念,通過精確計算,重新編排工藝路線,解決了上述減薄、破裂等問題。
零件工藝性分析
XX.034前板零件如圖1所示。
材料
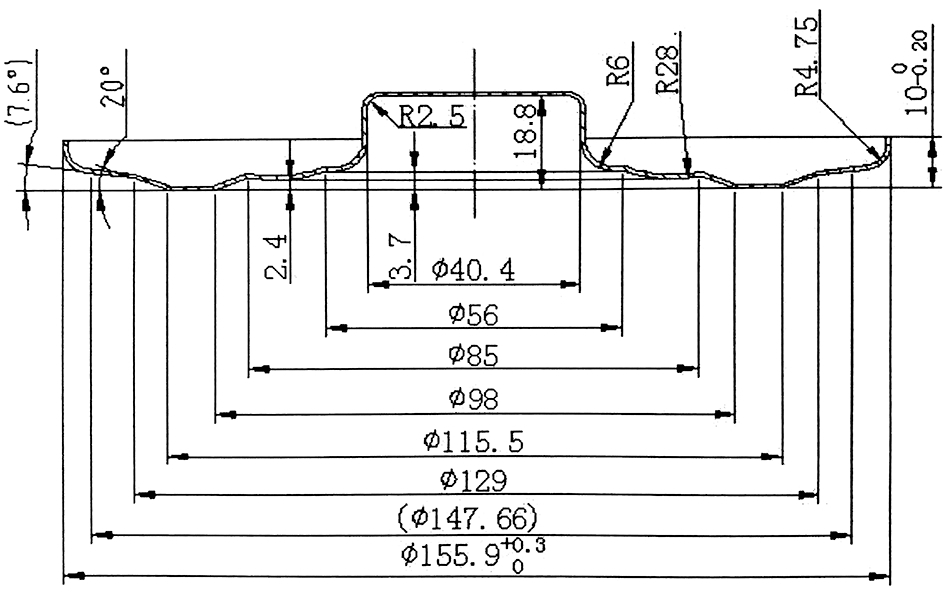
圖1 XX.034前板產(chǎn)品圖
XX.034前板材料為1Cr18Ni9Ti,為奧氏體不銹鋼,料厚為0.8mm。此鋼不能用熱處理強化,冷加工是強化的唯一手段,工序間可通過熱處理進行恢復(fù)塑性,消除冷作硬化等現(xiàn)象。此鋼具有良好的塑性、韌性及沖壓性能,其塑性與日常使用較為廣泛的優(yōu)質(zhì)碳素結(jié)構(gòu)鋼具體對比如表1所示,熱處理退火狀態(tài)伸長率達40%,而20鋼退火狀態(tài)為25%。
表1 材料機械性能對比表

外形尺寸
XX.034前板其壁厚為0.8mm,中間部位有一拉深處,內(nèi)圓尺寸為φ40.4mm,拉深深度為18.8 mm。由于零件功能性要求,凸緣設(shè)計為多型面,各型面均在一定直徑處相接,最外凸緣也為拉深處,與中間拉深部位呈反向,高度為10mm。整體結(jié)構(gòu)較為規(guī)則,最外緣直徑與內(nèi)圓直徑比值達3.86(155.9/40.4=3.86),屬大凸緣類結(jié)構(gòu)件。
試制問題及分析
失效現(xiàn)象
對XX.034前板進行工藝性分析,其中間內(nèi)圓尺寸為φ40.4mm,拉深高度為18.8mm,高徑比為0.465(18.8/40.4=0.465),此比值屬可一次性拉深成形范疇,再者由于其材料本身具有優(yōu)良的沖壓性,所以在前期安排試制工藝及模具結(jié)構(gòu)設(shè)計時,按常規(guī)思路將中間拉深模具設(shè)計為90°變形率拉深法(即凹模為直角過渡),通過一次成形到位。但投入試模過程中發(fā)現(xiàn),中間拉深處幾乎每件均出現(xiàn)了轉(zhuǎn)接R處破裂現(xiàn)象,如圖2所示,無法制出合格零件。
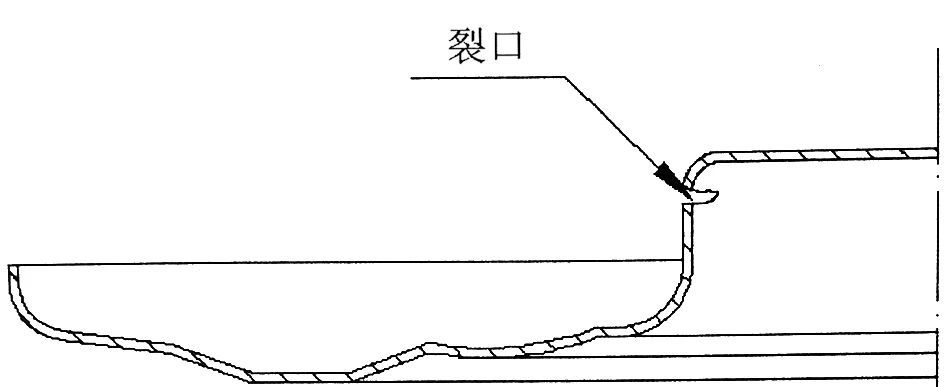
圖2 轉(zhuǎn)接R破裂示意圖
問題分析
由于試模件出現(xiàn)上述問題,為此開展原因查找及問題分析。在拉深過程中,裂口處對應(yīng)凸模圓角處,凸模圓角處是側(cè)壁和底部的過渡區(qū),材料承受側(cè)壁較大的拉應(yīng)力、凸模圓角的壓力和彎曲作用而產(chǎn)生的壓應(yīng)力和切向拉應(yīng)力,在這個區(qū)間的側(cè)壁與底部轉(zhuǎn)角處稍上的地方拉深開始時它處于凸、凹模間,需要轉(zhuǎn)移的材料較少,受變形的程度小,冷作硬化程度低,加之該處材料厚度變薄,使傳力的截面積變小,成為整個拉深件強度最薄弱的地方。同時將失效件進行剖切,對壁厚進行分析,如圖3所示。
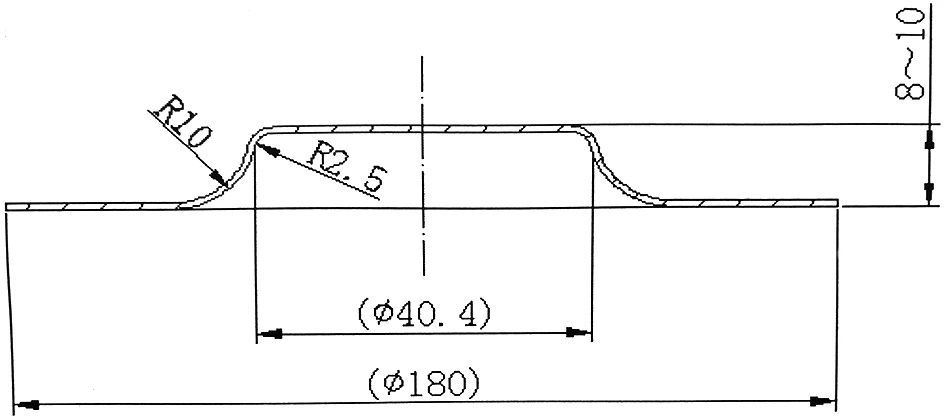
圖3 失效零件剖切示意圖
由圖3剖切實物圖可以看出在拉深底部轉(zhuǎn)接R處(畫圈處)壁厚出現(xiàn)了嚴(yán)重減薄現(xiàn)象,經(jīng)測量已減薄至0.3mm(原始料厚0.8mm),此處成為了薄弱區(qū)域,所以在此位置最先出現(xiàn)了破裂現(xiàn)象。
通過分析,出現(xiàn)上述現(xiàn)象的主要原因在于由于零件凸緣過大,外凸緣展開后是中間拉深部位的四倍之多。這樣造成了外面凸緣的抗拉深力大大超出了中間部位的成形拉深力,外面的材料很難流入中間拉深部位,使中間拉深部位的變形材料不能得到外凸緣材料的及時補充而破裂。
解決方案
工藝優(yōu)化
要解決此零件中間拉深部位的破裂問題,首先要使拉深部位的變形材料在變形過程中能夠及時得到外凸緣材料的補充,為此制定如下成形步驟。
⑴將拉深成形的凹模R加大。一般情況下,此R是零件壁厚的5倍左右,零件壁厚為0.8mm,按理論計算應(yīng)為R4,零件實際設(shè)計要求為R6,雖對成形有利,但為降低風(fēng)險,優(yōu)化方案給定的數(shù)值是為R10,先拉深到8~10mm的深度,進行固溶處理,消除應(yīng)力,以利于再次成形(圖4)。
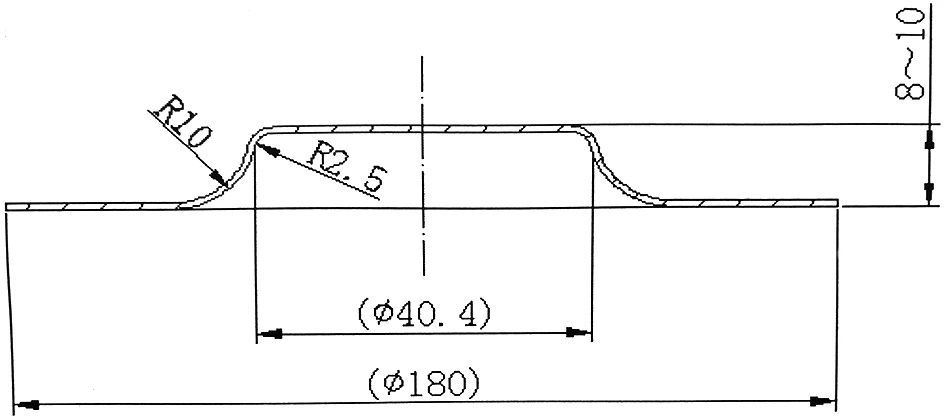
圖4 初步拉深示意圖
⑵二次拉深成形時,將模具設(shè)計成外凸緣有一斜角的形狀,其角度為
,凹模成形R仍采取加大的R10,此R10在外凸緣上沿圓周為φ125.3mm,中間部位的形狀基本不變(圖5)。
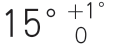
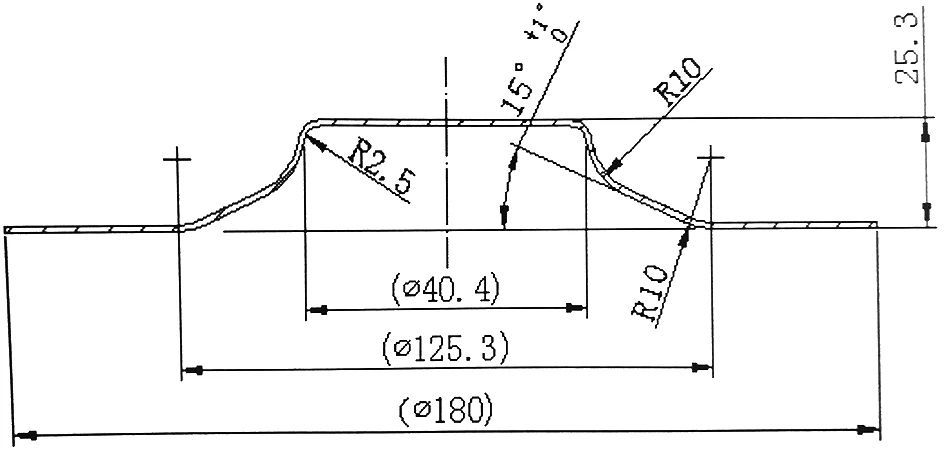
圖5 二次拉深示意圖
這樣處理使比較容易被拉深成形的外凸緣材料能及時補充給中間拉深成形處。此次拉深后,零件高度為25.3mm,而零件的最后成形高度為18.8mm。25.3-18.8=6.5mm,多出的6.5mm高度值就為下一步成形提供了所需材料的來源。
⑶再次成形時,將φ40.4mm的凸緣R10壓成R6,φ40.4mm的深度也增加到15.1mm,去掉R6,其直壁深度(包括底部R2.5mm)為9.1mm,至此中間部位φ40.4mm的拉深成形已經(jīng)完成。通過模具型面可預(yù)成形到位,如圖6所示。
圖6 型面成形示意圖
在這道工序中,考慮到外凸緣的多型面,可以與中間部位的成形同時進行,只是不能進行最外面的反向拉深。因為反向拉深時材料的變形劇烈,拉深力較大,很容易使圖5中φ125.3mm以內(nèi)的多余材料向反向拉深處φ147.66~φ155.9mm處流動,造成R10變?yōu)镽6這個地方因無材料補充而變薄或破裂。為避免此種情況發(fā)生,可將最外面的反向拉深放到最后進行,先把R6和凸緣上的型面完成。這樣原來高出的6.5mm處多余的材料,能補充給R10變?yōu)镽6,以及外凸緣上的多型面所需的材料,即可比較順利地完成拉深成形。
⑷反向拉深φ155.9mm,高度不小于12mm的外緣壁。這一步反向拉深是屬于正常的沖壓成形工藝(圖7),易實現(xiàn)。
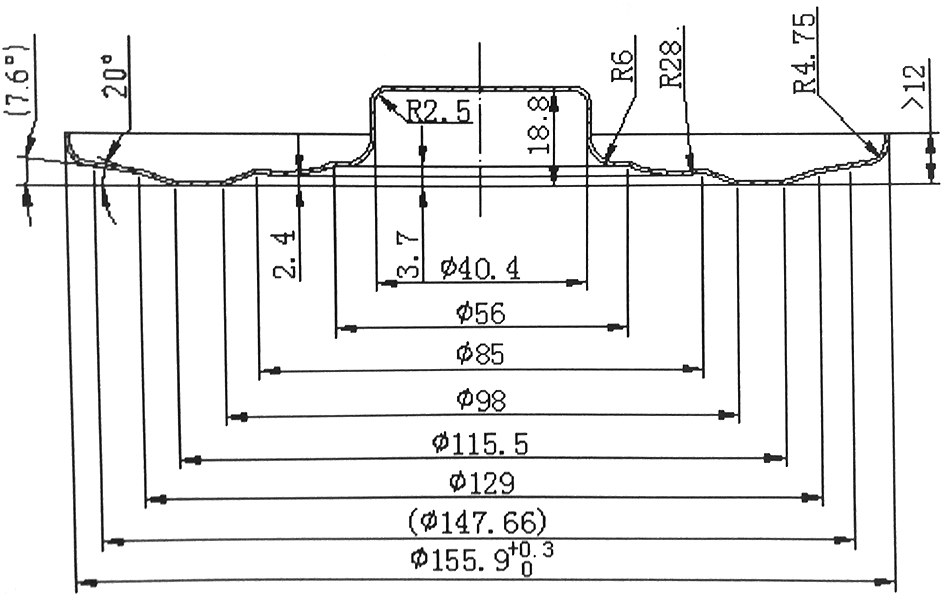
圖7 外緣反拉深成形示意圖
⑸將拉深成形好的零件進行車加工,去除外緣多余料。
至此,零件加工完成。
工藝優(yōu)化前后對比分析
⑴成形要素對比。
現(xiàn)就常規(guī)拉深成形(前)與斜角過渡成形(后)比較分析如下,比較示意圖如圖8所示。
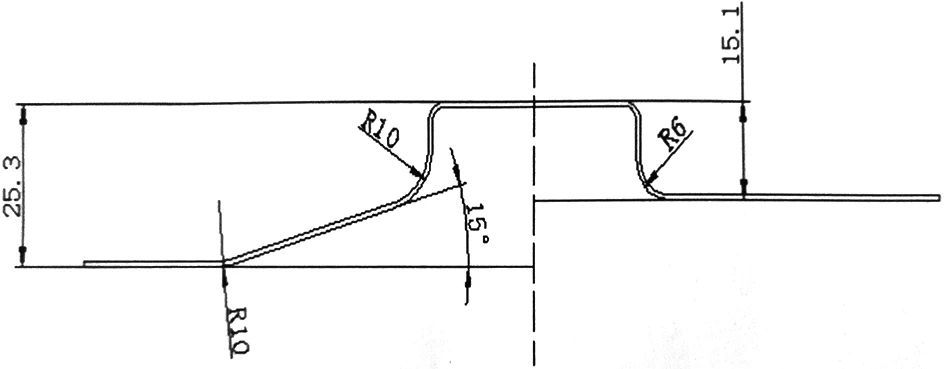
圖8 優(yōu)化前后方案比較示意圖
1)常規(guī)拉深成形。
①沿φ40.4mm拉深處的凸緣R6,拉深深度15.1mm;
②材料曲率變化90°;
③外凸緣(毛坯)與拉深成形直徑比:190(下料直徑)/40.4=4.703,比值過大,不利于拉深成形,外凸緣材料抗力太大,難以向成形處流動補充。
2)采取優(yōu)化后拉深。
①沿φ40.4mm拉深處的凸緣R10,拉深深度8~10mm(圖4);
②R10處的材料曲率變化約45°,是正常拉深的50%,有利于成形;
③外凸緣(毛坯)與拉深成形處直徑比:190(下料直徑)/125.3=1.516,比值較小,加上15°的成形角,材料的變化曲率也很小,外凸緣的材料比較容易向成形處流動補充,所以較容易成形(圖5)。
⑵中間過程材料分布計算對比。
在此沖壓成形過程中,遵循材料體積基本相等原則,根據(jù)上述原則進行材料分析計算,材料計算對比示意圖如圖9所示。
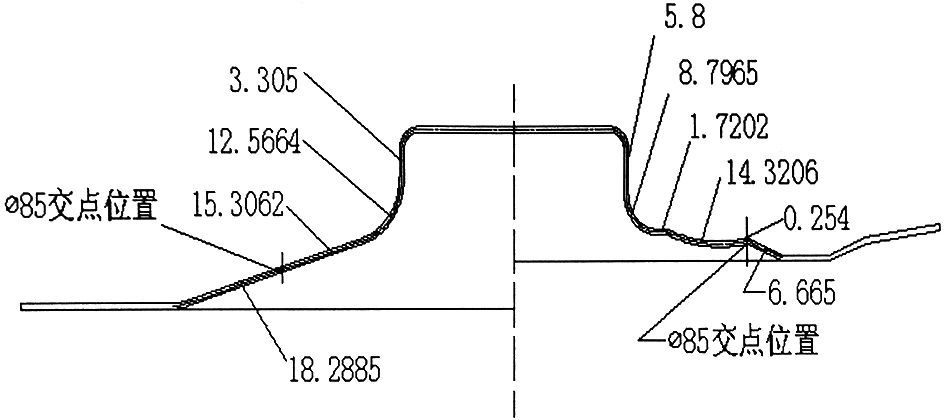
圖9 優(yōu)化前后方案材料分布計算比較示意圖
(注:圖中各段線性值均可在cad軟件中測量出)
1)常規(guī)拉深(φ85mm交點處)材料展開計算。
5.8+8.7965+1.7202+14.3206+0.254=30.8913 mm
6.665-6.25=0.415mm(斜邊比直邊多0.415mm,需要再補充0.415mm的材料;6.25mm為6.665mm區(qū)域內(nèi)投影直線長度)。
2)優(yōu)化方案拉深(φ85mm交點處)材料展開計算。
3.305+12.5664+15.3062=31.1776mm
①兩種方案材料差值:
31.17-30.89=0.28mm,表明優(yōu)化后材料可多余0.28(φ85mm交點以內(nèi)的材料);
②15°斜角材料差值:(分段計算)
15.3062-14.78=0.526mm(14.78mm為15.3062mm區(qū)域內(nèi)投影直線長度);
18.2885-17.67=0.618mm(17.67mm為18.2885mm區(qū)域內(nèi)投影直線長度);
0.618+0.526=1.144mm(表明斜邊比直邊多1.144mm);
1.144-0.415=0.729mm
通過上述計算,表明采用優(yōu)化方案后,將多余的1.144mm材料補充給前面區(qū)域成形所需要的0.415mm,還剩余0.729mm可供后面凸緣的多型面成形。采取優(yōu)化方案后完全能夠滿足零件最后成形所需要的材料。
模具結(jié)構(gòu)設(shè)計
在上述成形方案中,總共需要兩套模具即可完成,如圖10、圖11所示。

圖10 預(yù)成形模結(jié)構(gòu)示意圖
1-橫銷 2-推料桿 3-模柄 4-連接螺釘 5-上模 6-凸模7-下模 8-頂桿 9-下模板
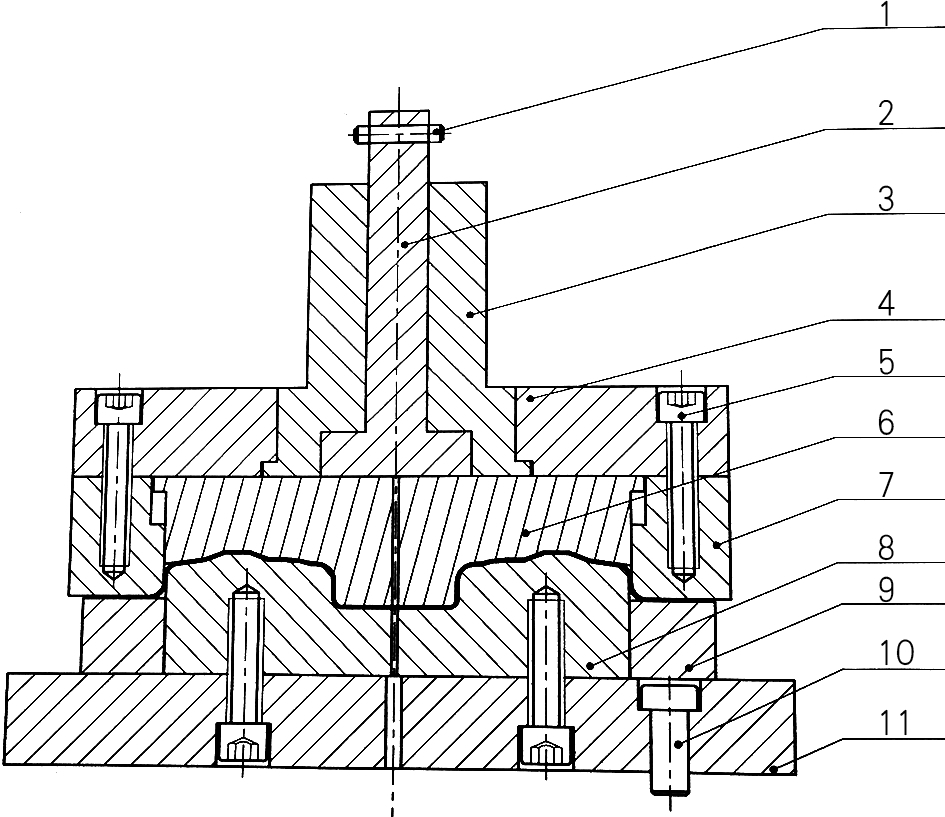
圖11 成形模結(jié)構(gòu)示意圖
1-橫銷 2-推料桿 3-模柄 4-上模板 5-連接螺釘 6-內(nèi)型芯7-凹模 8-凸凹模 9-壓邊圈 10-頂桿 11-下模板
⑴預(yù)成形模,用于淺拉深及制成斜角。
⑵成形模,用于中間部位拉深成形及最終凸緣成形。
此成形模具可做兩用,在上述第三步成形中只需用內(nèi)型芯及凹模,可拆去7凹模,當(dāng)進行第四步外凸緣反向拉深時可用上凹模成形。
總結(jié)
通過精確數(shù)值模擬計算,采取有效的拉深途徑,避免成形過程中零件破裂,產(chǎn)生報廢,從而實現(xiàn)零件的批量合格生產(chǎn)。經(jīng)過生產(chǎn)實踐,證明大凸緣薄壁零件的沖壓成形,不能直接按照常規(guī)的沖壓成形方法進行加工,而要根據(jù)不同的零件情況采取相應(yīng)的措施,才能達到成形目的,同時此方法也可為同類零件的加工成形借鑒使用。
—— 來源:《鍛造與沖壓》 2019年第4期
舉報 0
收藏 0
分享 114
-
乘用車金屬沖壓
2025-05-29 -
沖壓技術(shù)在電機疊片制造的應(yīng)用
2024-09-06 -
車身零部件包邊質(zhì)量控制要點
2024-09-05 -
輕量化技術(shù)——熱汽脹形工藝技術(shù)解析
2024-09-04
最新資訊
-
跨越速運憑什么“圈粉”萬千客戶?“
2025-07-01 14:42
-
數(shù)智破局啟新篇?生態(tài)共生再啟程 —
2025-06-27 20:13
-
助力汽車零部件產(chǎn)線智能化升級,西門
2025-06-27 13:59
-
BBA集體轉(zhuǎn)向!放棄全面電動化
2025-06-26 17:32
-
比換柜省錢,比自研省心,西門子Xcel
2025-06-25 15:07