轎車(chē)白車(chē)身沖壓件VAVE降本方案的策略研究
2018-09-13 10:20:20· 來(lái)源:高碩遙 鍛造與沖壓
研究表明,工藝設(shè)計(jì)階段決定了產(chǎn)品制造成本的70% ~ 80%,而設(shè)計(jì)本身的成本僅占產(chǎn)品總成本的10%。在材料價(jià)格不斷上漲和汽車(chē)市場(chǎng)競(jìng)爭(zhēng)日趨激烈的今天,如何在設(shè)計(jì)階段多維度的完成轎車(chē)白車(chē)身沖壓件V A V E 降本方案有著至關(guān)重要的意義。VA
研究表明,工藝設(shè)計(jì)階段決定了產(chǎn)品制造成本的70% ~ 80%,而設(shè)計(jì)本身的成本僅占產(chǎn)品總成本的10%。在材料價(jià)格不斷上漲和汽車(chē)市場(chǎng)競(jìng)爭(zhēng)日趨激烈的今天,如何在設(shè)計(jì)階段多維度的完成轎車(chē)白車(chē)身沖壓件V A V E 降本方案有著至關(guān)重要的意義。
VA(Value analysis)是對(duì)完成品實(shí)施降低成本,擴(kuò)大利潤(rùn)的活動(dòng)。VE(Value engineering)是通過(guò)產(chǎn)品工藝開(kāi)發(fā)期間優(yōu)化產(chǎn)品和工藝、完成目標(biāo)成本的活動(dòng)。隨著環(huán)保和能源意識(shí)的增強(qiáng),市場(chǎng)競(jìng)爭(zhēng)的加劇,各大汽車(chē)廠的成本意識(shí)也越來(lái)越強(qiáng),降成本活動(dòng)自設(shè)計(jì)之初到量產(chǎn)后,無(wú)時(shí)無(wú)刻不在進(jìn)行。研究表明,工藝設(shè)計(jì)階段決定了產(chǎn)品制造成本的70% ~ 80%,而設(shè)計(jì)本身的成本僅占產(chǎn)品總成本的10%。在材料價(jià)格不斷上漲和汽車(chē)市場(chǎng)競(jìng)爭(zhēng)日趨激烈的今天,如何在設(shè)計(jì)階段多維度的完成轎車(chē)白車(chē)身沖壓件VAVE 降本方案有著至關(guān)重要的意義。本文從優(yōu)化零件設(shè)計(jì)、創(chuàng)新沖壓工藝和材料管理角度詳細(xì)介紹轎車(chē)白車(chē)身沖壓件VAVE 降本方案。
優(yōu)化零件設(shè)計(jì)
創(chuàng)新沖壓工藝的成功應(yīng)用要以合適的零件設(shè)計(jì)為前提,同步工程期間,零件設(shè)計(jì)要兼顧滿(mǎn)足功能和優(yōu)化成本的要求,通過(guò)優(yōu)化零件材料和零件形狀更好地實(shí)現(xiàn)降成本的目的。
零件材料設(shè)計(jì)
整車(chē)輕量化是目前汽車(chē)工業(yè)的發(fā)展方向,特別是車(chē)身骨架件的汽車(chē)輕量化設(shè)計(jì),是整車(chē)輕量化的關(guān)鍵。采用高強(qiáng)鋼,特別是超高強(qiáng)度鋼板,是目前車(chē)身輕量化最經(jīng)濟(jì)、有效的方法。歐日等先進(jìn)汽車(chē)制造企業(yè)高強(qiáng)鋼零件的應(yīng)用比例超過(guò)了60%,高強(qiáng)鋼的普及應(yīng)用不僅是汽車(chē)輕量化的重要手段,也是降成本的需求。
零件形狀設(shè)計(jì)
通過(guò)對(duì)產(chǎn)品邊界進(jìn)行合理的“合并、拆分”或“做方、做圓”使產(chǎn)品盡可能規(guī)整,減少局部凸出,如果局部凸出,后續(xù)再做工藝補(bǔ)充部分時(shí),需要保證邊界過(guò)渡平滑緩和或進(jìn)料均勻,從而增加較多的過(guò)渡部分。因此需要對(duì)產(chǎn)品零件“非圓、非方”部位進(jìn)行合并,既減少了零件的數(shù)量,也減少了對(duì)應(yīng)的模具、檢具以及工裝夾具的投資費(fèi)用。
圖1 所示的轎車(chē)某車(chē)型側(cè)圍加強(qiáng)板,原始設(shè)計(jì)方案由3 塊TRIP600 材質(zhì)1.6mm 厚板料與1 塊TRIP600材質(zhì)1.4mm 厚板料拼焊而成。制件前期工藝評(píng)審中,從材料利用率、拼焊加工費(fèi)用、廢品率、余廢料利用和沖壓投資成本等幾方面考慮,將產(chǎn)品拼焊焊縫取消,料厚統(tǒng)一為1.6mm,并提出產(chǎn)品門(mén)洞廢料利用方案,應(yīng)用于轎車(chē)同車(chē)型側(cè)圍內(nèi)板。該側(cè)圍加強(qiáng)板經(jīng)過(guò)前期綜合評(píng)審、分析降成本29.36×2=58.72 元/ 車(chē),模具投資預(yù)算降低173.63 萬(wàn)元。
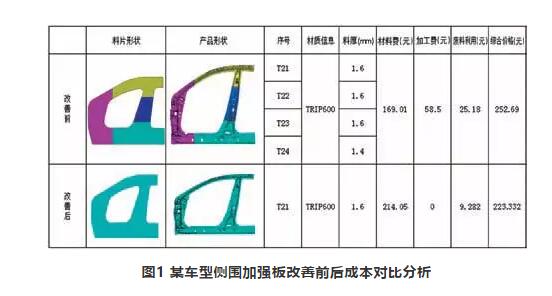
創(chuàng)新沖壓工藝
淺拉延
拉延是常用的沖壓工序,優(yōu)點(diǎn)是提高材料的塑性并能生產(chǎn)穩(wěn)定。但傳統(tǒng)的深拉延工序需要較大的工藝補(bǔ)充面,工藝補(bǔ)充面不是產(chǎn)品面,是工藝延伸面,這部分在后序工序中被切除,造成較大的材料損失。因此,為了顯著提高材料利用率,必須考慮將凸模輪廓線設(shè)計(jì)在零件之內(nèi),用零件的部分形狀做壓料面,這種拉延形式稱(chēng)作淺拉延。
圖2 是采用淺拉延工藝的中地板,優(yōu)化后的凸模輪廓線設(shè)計(jì)在零件產(chǎn)品上,用零件的法蘭邊做壓料面,減小了拉延深度,非常明顯地縮小了工藝補(bǔ)充面,材料利用率由64.5% 提升至83.9%,極大地提高了材料利用率。
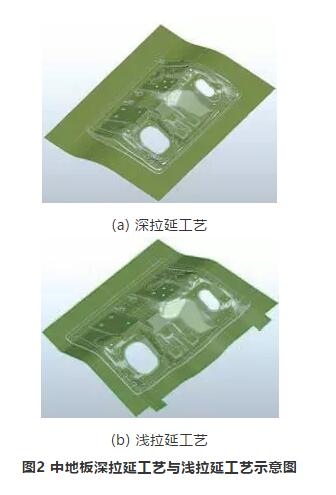
對(duì)件合模拉延
白車(chē)身上存在著大量的左右對(duì)稱(chēng)件,通過(guò)對(duì)件合模共用中間部分的工藝補(bǔ)充面,從而減少單件的工藝補(bǔ)充面,提高材料利用率。但如果受到生產(chǎn)現(xiàn)場(chǎng)的工藝設(shè)備條件限制,導(dǎo)致部分工序無(wú)法進(jìn)行,則使用一模雙腔的合模方式,同樣可以減少一套模具的費(fèi)用。圖3 所示的左/ 右側(cè)C 柱加強(qiáng)板,優(yōu)先考慮采用左右件對(duì)件合模拉延,提高材料利用率的同時(shí)可以提高生產(chǎn)效率。
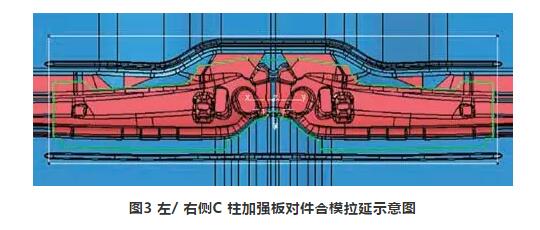
成形代拉延
成形工藝與拉延工藝相比,成形工藝沒(méi)有工藝補(bǔ)充面,成形前的落料片可以進(jìn)行排樣優(yōu)化,因而能極大地提高材料利用率。圖4 是左/ 右連接板,如果采用拉延工藝,則材料利用率僅為51.1%;而采用成形工藝,零件材料利用率提升至64.58%,且模具套數(shù)由原來(lái)的5 套減少為4 套??梢?jiàn),成形工藝不僅能大幅提升零件的材料利用率,而且能有效減少模具套數(shù),節(jié)約開(kāi)發(fā)車(chē)身成本。
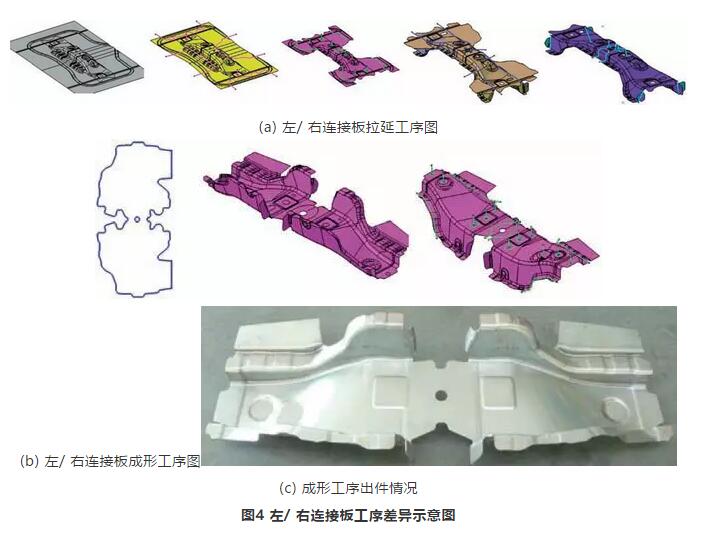
套裁沖壓
VA(Value analysis)是對(duì)完成品實(shí)施降低成本,擴(kuò)大利潤(rùn)的活動(dòng)。VE(Value engineering)是通過(guò)產(chǎn)品工藝開(kāi)發(fā)期間優(yōu)化產(chǎn)品和工藝、完成目標(biāo)成本的活動(dòng)。隨著環(huán)保和能源意識(shí)的增強(qiáng),市場(chǎng)競(jìng)爭(zhēng)的加劇,各大汽車(chē)廠的成本意識(shí)也越來(lái)越強(qiáng),降成本活動(dòng)自設(shè)計(jì)之初到量產(chǎn)后,無(wú)時(shí)無(wú)刻不在進(jìn)行。研究表明,工藝設(shè)計(jì)階段決定了產(chǎn)品制造成本的70% ~ 80%,而設(shè)計(jì)本身的成本僅占產(chǎn)品總成本的10%。在材料價(jià)格不斷上漲和汽車(chē)市場(chǎng)競(jìng)爭(zhēng)日趨激烈的今天,如何在設(shè)計(jì)階段多維度的完成轎車(chē)白車(chē)身沖壓件VAVE 降本方案有著至關(guān)重要的意義。本文從優(yōu)化零件設(shè)計(jì)、創(chuàng)新沖壓工藝和材料管理角度詳細(xì)介紹轎車(chē)白車(chē)身沖壓件VAVE 降本方案。
優(yōu)化零件設(shè)計(jì)
創(chuàng)新沖壓工藝的成功應(yīng)用要以合適的零件設(shè)計(jì)為前提,同步工程期間,零件設(shè)計(jì)要兼顧滿(mǎn)足功能和優(yōu)化成本的要求,通過(guò)優(yōu)化零件材料和零件形狀更好地實(shí)現(xiàn)降成本的目的。
零件材料設(shè)計(jì)
整車(chē)輕量化是目前汽車(chē)工業(yè)的發(fā)展方向,特別是車(chē)身骨架件的汽車(chē)輕量化設(shè)計(jì),是整車(chē)輕量化的關(guān)鍵。采用高強(qiáng)鋼,特別是超高強(qiáng)度鋼板,是目前車(chē)身輕量化最經(jīng)濟(jì)、有效的方法。歐日等先進(jìn)汽車(chē)制造企業(yè)高強(qiáng)鋼零件的應(yīng)用比例超過(guò)了60%,高強(qiáng)鋼的普及應(yīng)用不僅是汽車(chē)輕量化的重要手段,也是降成本的需求。
零件形狀設(shè)計(jì)
通過(guò)對(duì)產(chǎn)品邊界進(jìn)行合理的“合并、拆分”或“做方、做圓”使產(chǎn)品盡可能規(guī)整,減少局部凸出,如果局部凸出,后續(xù)再做工藝補(bǔ)充部分時(shí),需要保證邊界過(guò)渡平滑緩和或進(jìn)料均勻,從而增加較多的過(guò)渡部分。因此需要對(duì)產(chǎn)品零件“非圓、非方”部位進(jìn)行合并,既減少了零件的數(shù)量,也減少了對(duì)應(yīng)的模具、檢具以及工裝夾具的投資費(fèi)用。
圖1 所示的轎車(chē)某車(chē)型側(cè)圍加強(qiáng)板,原始設(shè)計(jì)方案由3 塊TRIP600 材質(zhì)1.6mm 厚板料與1 塊TRIP600材質(zhì)1.4mm 厚板料拼焊而成。制件前期工藝評(píng)審中,從材料利用率、拼焊加工費(fèi)用、廢品率、余廢料利用和沖壓投資成本等幾方面考慮,將產(chǎn)品拼焊焊縫取消,料厚統(tǒng)一為1.6mm,并提出產(chǎn)品門(mén)洞廢料利用方案,應(yīng)用于轎車(chē)同車(chē)型側(cè)圍內(nèi)板。該側(cè)圍加強(qiáng)板經(jīng)過(guò)前期綜合評(píng)審、分析降成本29.36×2=58.72 元/ 車(chē),模具投資預(yù)算降低173.63 萬(wàn)元。
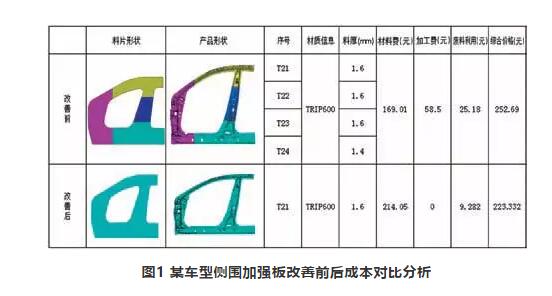
創(chuàng)新沖壓工藝
淺拉延
拉延是常用的沖壓工序,優(yōu)點(diǎn)是提高材料的塑性并能生產(chǎn)穩(wěn)定。但傳統(tǒng)的深拉延工序需要較大的工藝補(bǔ)充面,工藝補(bǔ)充面不是產(chǎn)品面,是工藝延伸面,這部分在后序工序中被切除,造成較大的材料損失。因此,為了顯著提高材料利用率,必須考慮將凸模輪廓線設(shè)計(jì)在零件之內(nèi),用零件的部分形狀做壓料面,這種拉延形式稱(chēng)作淺拉延。
圖2 是采用淺拉延工藝的中地板,優(yōu)化后的凸模輪廓線設(shè)計(jì)在零件產(chǎn)品上,用零件的法蘭邊做壓料面,減小了拉延深度,非常明顯地縮小了工藝補(bǔ)充面,材料利用率由64.5% 提升至83.9%,極大地提高了材料利用率。
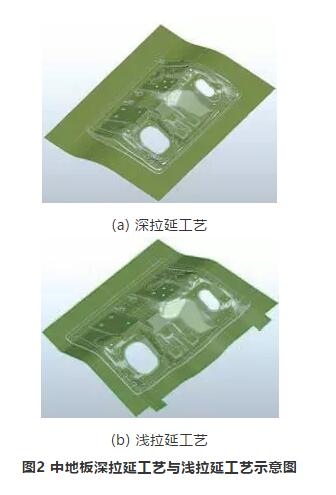
對(duì)件合模拉延
白車(chē)身上存在著大量的左右對(duì)稱(chēng)件,通過(guò)對(duì)件合模共用中間部分的工藝補(bǔ)充面,從而減少單件的工藝補(bǔ)充面,提高材料利用率。但如果受到生產(chǎn)現(xiàn)場(chǎng)的工藝設(shè)備條件限制,導(dǎo)致部分工序無(wú)法進(jìn)行,則使用一模雙腔的合模方式,同樣可以減少一套模具的費(fèi)用。圖3 所示的左/ 右側(cè)C 柱加強(qiáng)板,優(yōu)先考慮采用左右件對(duì)件合模拉延,提高材料利用率的同時(shí)可以提高生產(chǎn)效率。
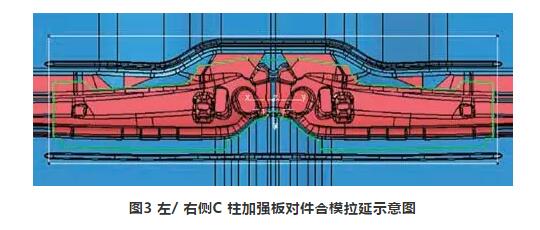
成形代拉延
成形工藝與拉延工藝相比,成形工藝沒(méi)有工藝補(bǔ)充面,成形前的落料片可以進(jìn)行排樣優(yōu)化,因而能極大地提高材料利用率。圖4 是左/ 右連接板,如果采用拉延工藝,則材料利用率僅為51.1%;而采用成形工藝,零件材料利用率提升至64.58%,且模具套數(shù)由原來(lái)的5 套減少為4 套??梢?jiàn),成形工藝不僅能大幅提升零件的材料利用率,而且能有效減少模具套數(shù),節(jié)約開(kāi)發(fā)車(chē)身成本。
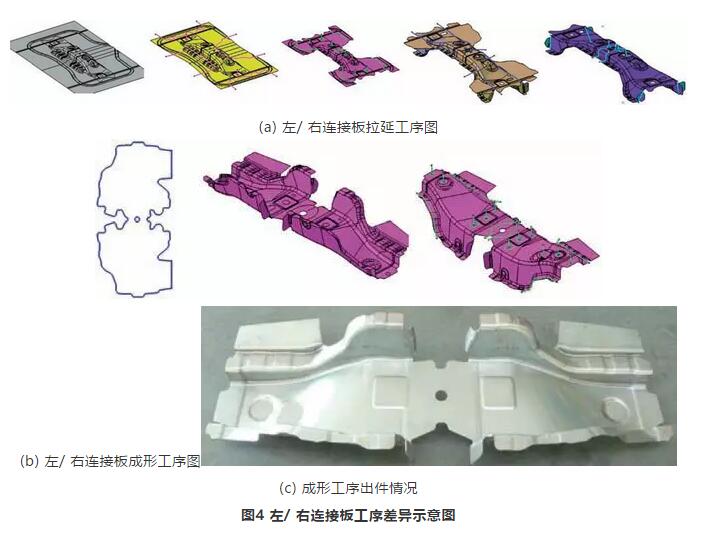
套裁沖壓
舉報(bào) 0
收藏 0
分享 132
-
乘用車(chē)金屬?zèng)_壓
2025-05-29 -
沖壓技術(shù)在電機(jī)疊片制造的應(yīng)用
2024-09-06 -
車(chē)身零部件包邊質(zhì)量控制要點(diǎn)
2024-09-05 -
輕量化技術(shù)——熱汽脹形工藝技術(shù)解析
2024-09-04
最新資訊
-
跨越速運(yùn)憑什么“圈粉”萬(wàn)千客戶(hù)?“
2025-07-01 14:42
-
數(shù)智破局啟新篇?生態(tài)共生再啟程 —
2025-06-27 20:13
-
助力汽車(chē)零部件產(chǎn)線智能化升級(jí),西門(mén)
2025-06-27 13:59
-
BBA集體轉(zhuǎn)向!放棄全面電動(dòng)化
2025-06-26 17:32
-
比換柜省錢(qián),比自研省心,西門(mén)子X(jué)cel
2025-06-25 15:07