【技術(shù)分享】汽車輪轂用改性鎂合金鍛造工藝
2020-04-27 21:37:44· 來(lái)源:NGA集團(tuán) 作者:郝孟軍,宮濤,代艷霞
以應(yīng)用于汽車輪轂的改性鎂合金AZ80-0. 5V-0. 1Ti為例,通過(guò)模擬計(jì)算和試驗(yàn)的方法,研究了成形溫度、模具工作速度、下模窗口處圓角半徑等工藝參數(shù)對(duì)鎂合金輪轂鍛造的影響,并對(duì)其結(jié)果進(jìn)行對(duì)比分析,獲得了優(yōu)良的鎂合金輪轂鍛造工藝參數(shù)。
以應(yīng)用于汽車輪轂的改性鎂合金AZ80-0. 5V-0. 1Ti為例,通過(guò)模擬計(jì)算和試驗(yàn)的方法,研究了成形溫度、模具工作速度、下模窗口處圓角半徑等工藝參數(shù)對(duì)鎂合金輪轂鍛造的影響,并對(duì)其結(jié)果進(jìn)行對(duì)比分析,獲得了優(yōu)良的鎂合金輪轂鍛造工藝參數(shù)。通過(guò)試驗(yàn)驗(yàn)證了仿真計(jì)算的有效性,其結(jié)果表明: 坯料溫度<370℃時(shí),鍛造鎂合金輪輞處產(chǎn)生開裂,坯料溫度>390℃時(shí),窗口部位出現(xiàn)裂紋; 模具工作速度為5~7mm·s-1時(shí),鎂合金輪轂鍛造成形質(zhì)量較好; 下模窗口處圓角半徑為20mm時(shí),鎂合金輪轂質(zhì)量較好。其方法和思路可為汽車輪轂及相似產(chǎn)品的工藝參數(shù)設(shè)計(jì)和優(yōu)化提供一定的參考和借鑒。
關(guān)鍵詞:鎂合金;鍛造工藝;輪轂?zāi)>?;坯料溫度;汽車輪?br />
鎂合金是金屬結(jié)構(gòu)材料中較輕的金屬,被譽(yù)為21世紀(jì)的綠色工程結(jié)構(gòu)材料,其質(zhì)量輕、比強(qiáng)度高、彈性模量低、加工性能優(yōu)、可回收以及具有優(yōu)異的減震性能等特點(diǎn),目前已被應(yīng)用在汽車零部件上[1 - 3]。汽車輪轂作為汽車上最重要的部件之一,要求其質(zhì)量輕,同時(shí)其受載復(fù)雜,包括行駛過(guò)程中的垂直壓力,車輛在起動(dòng)、制動(dòng)時(shí)動(dòng)態(tài)扭矩的作用以及車輛在行駛過(guò)程中轉(zhuǎn)彎等動(dòng)態(tài)載荷[4 - 6]。為此,將鎂合金材料引入汽車輪轂是一可行趨勢(shì)。本文以改型鎂合金材料AZ80-0. 5V-0. 1Ti作為研究對(duì)象,對(duì)其鍛造加工工藝參數(shù)進(jìn)行了仿真和試驗(yàn)研究,為鎂合金應(yīng)用于輪轂的工藝設(shè)計(jì)提供了參考。
鎂合金汽車輪轂結(jié)構(gòu)及生產(chǎn)特點(diǎn)
輪轂結(jié)構(gòu)
汽車輪轂由輪輻、輪緣、輪輞等構(gòu)成,作為重要的車輛零部件,其結(jié)構(gòu)設(shè)計(jì)應(yīng)滿足功能性、工藝性、安全性、經(jīng)濟(jì)性等要求,并具有一定的剛度、強(qiáng)度及較長(zhǎng)的疲勞壽命等[7-8]。圖1為汽車輪轂示意圖。
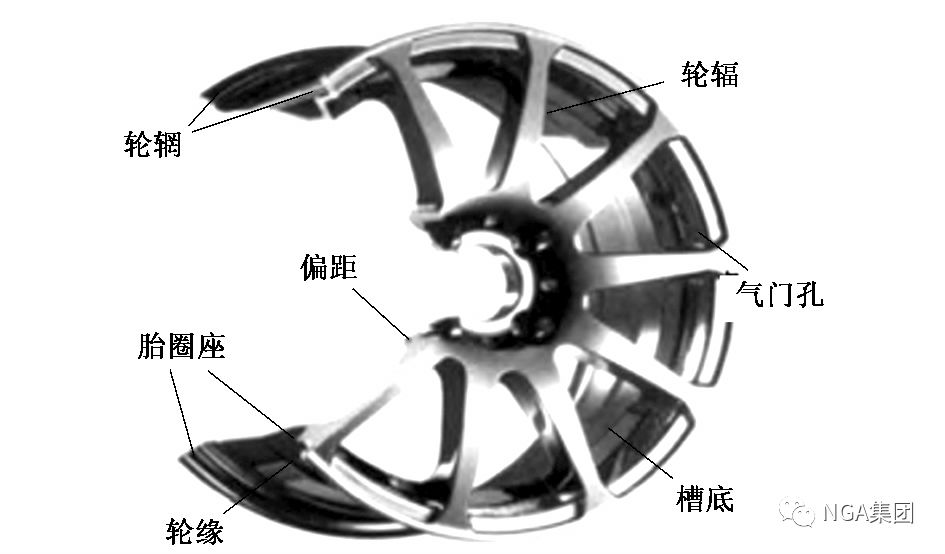
圖1 鎂合金汽車輪轂
鎂合金輪轂鍛造的特點(diǎn)
鎂合金輪轂主要有鍛造和鑄造兩種生產(chǎn)方式,且兩種方式各有優(yōu)缺點(diǎn)。本文以某型汽車輪轂作為研究對(duì)象,其輪轂的三維模型如圖2所示,輪轂包含10個(gè)窗口,以及輪輻、輪輞等主要部分,窗口處有一個(gè)溝槽與冒口相連。從外觀上看,輪轂結(jié)構(gòu)復(fù)雜,本文采用鍛造、配合銑削加工進(jìn)行生產(chǎn)工藝研究。

圖2 輪轂三維俯視圖
鎂合金輪轂的優(yōu)勢(shì)明顯,但是其缺點(diǎn)也比較明顯,主要包括以下幾條:(1) 熔煉過(guò)程中鎂合金燒損嚴(yán)重,同時(shí)易產(chǎn)生金屬夾雜和非金屬夾雜;(2)鎂合金極易氧化,表面防護(hù)困難;(3) 深加工性較差;(4) 熔煉過(guò)程的環(huán)境污染[9 - 10]。針對(duì)以上鍛造缺點(diǎn),本文選擇優(yōu)良的鎂合金材料,進(jìn)行相應(yīng)的工藝研究。
鎂合金輪轂鍛造
改性鎂合金AZ80-0. 5V-0. 1Ti的相關(guān)性能
本文研究采用改性鎂合金AZ80-0. 5V-0. 1Ti(其中,A 代表金屬鋁,Z代表金屬鋅,8代表鋁含量為8%,0代表鋅含量小于1%,0. 5V代表釩含量為0. 5%,0. 1Ti代表鈦含量為0. 1%),其密度約為1. 84 g·cm-3,約為鋁的2/3,是比鋁更輕量化的輕質(zhì)材料。該鎂合金的彈性模量只有45GPa,在外力作用下可以很好地避免構(gòu)件應(yīng)力集中,經(jīng)壓力鑄造后再加工所得部件的比強(qiáng)度高,且耐腐蝕性較純鎂有大幅提高。目前,影響鎂合金大規(guī)模應(yīng)用的因素之一就是其耐腐蝕性差,鎂合金AZ80-0. 5V-0. 1Ti基本上消除了該缺點(diǎn),特別是釩、鈦元素可以有效地控制鎂合金中碳化物的增加,并細(xì)化晶粒,提高鎂合金的韌性、沖擊性能和耐磨損性能,能夠在汽車零部件制作上廣泛應(yīng)用[11 - 12]。
鎂合金鍛造應(yīng)力模擬分析
本文選用ANSYS軟件,首先對(duì)輪轂鍛造過(guò)程及鍛造參數(shù)進(jìn)行仿真模擬,然后根據(jù)仿真結(jié)果進(jìn)行工藝參數(shù)比對(duì)。從圖2可以看出,輪轂結(jié)構(gòu)滿足軸對(duì)稱結(jié)構(gòu),為此本文選取對(duì)稱部分進(jìn)行建模。AZ80-0. 5V-0. 1Ti鎂合金仿真的材料模型參數(shù)如表1所示。
表1 AZ80-0. 5V-0. 1Ti鎂合金的相關(guān)性能參數(shù)
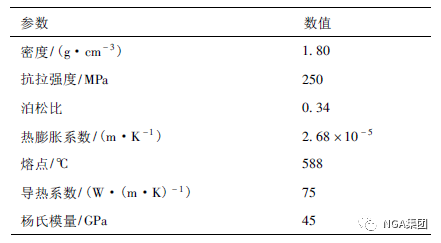
鎂合金輪轂在鍛造各階段的受力情況、變形過(guò)程及規(guī)律是隨著鍛造過(guò)程不斷變化的。圖3a為鍛造初期的應(yīng)力云圖,可以看出:窗口處的應(yīng)力較大,為主要變形區(qū)域,此區(qū)域窗口( 圖3a中A區(qū)域) 的圓角處是其與輪輞、輪緣的過(guò)渡區(qū)域,在鍛造過(guò)程中極易產(chǎn)生缺陷; 其余區(qū)域應(yīng)力值較小,在42MPa以下,遠(yuǎn)低于常溫下的材料屈服強(qiáng)度,因此,在鍛造過(guò)程中不易產(chǎn)生鍛造缺陷。圖3b為鍛造后期的應(yīng)力云圖,隨著鍛造上模向下運(yùn)動(dòng),窗口圓角處和輪輻側(cè)壁圓角區(qū)域的應(yīng)力比較集中,輪轂成形后此區(qū)域應(yīng)力最大,極易產(chǎn)生鍛造缺陷。
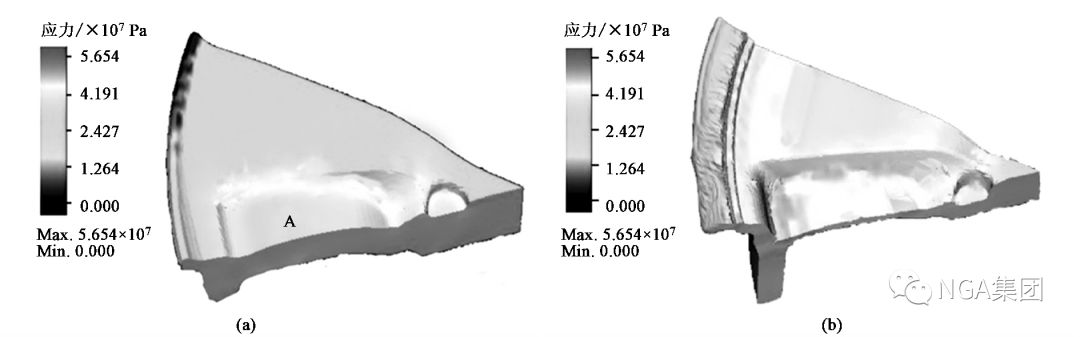
圖3 輪轂鍛造過(guò)程中的應(yīng)力分布情況
(a) 鍛造初期(b) 鍛造后期
工藝參數(shù)對(duì)鎂合金輪轂鍛造的影響的模擬分析
成形溫度的影響
成形溫度是鎂合金輪轂鍛造的重要參數(shù)之一,因鎂合金的伸長(zhǎng)率與溫度有關(guān),溫度升高,鎂合金塑性提高,有利于鎂合金的輪轂鍛造; 但是,溫度過(guò)高會(huì)導(dǎo)致腐蝕氧化,晶粒粗大,增大變形抗力。模擬工藝參數(shù)設(shè)定如下: 下模窗口處圓角半徑為30mm,模具工作速度為6mm·s-1,摩擦系數(shù)為0. 1,成形溫度分別為350,370,390 和410 ℃。仿真結(jié)果如圖4所示。
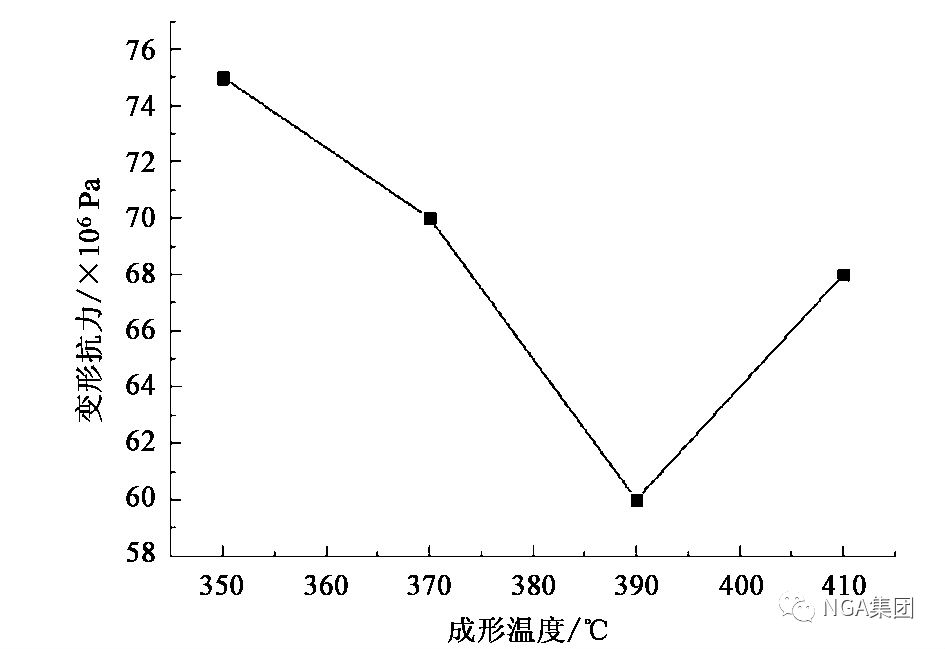
圖4 成形溫度對(duì)變形抗力的影響
鍛件變形抗力與成形溫度關(guān)系較大,成形溫度的適當(dāng)增加使得鎂合金的塑性變形能力提高,有利于金屬流動(dòng),變形抗力下降。但是,隨成形溫度進(jìn)一步升高,鎂合金內(nèi)部氧化,導(dǎo)致塑性降低、變形抗力上升。因此,成形溫度宜選擇在370~390 ℃之間。
模具工作速度對(duì)變形抗力的影響
材料的變形速度一般情況下體現(xiàn)在模具的工作速度上,本文在不同的模具工作速度下進(jìn)行仿真計(jì)算。其模擬參數(shù)設(shè)定如下: 成形溫度為380℃,摩擦系數(shù)為0. 1,下模窗口處圓角半徑為30mm,模具工作速度分別為5,7和9mm·s-1。仿真結(jié)果如圖5所示。
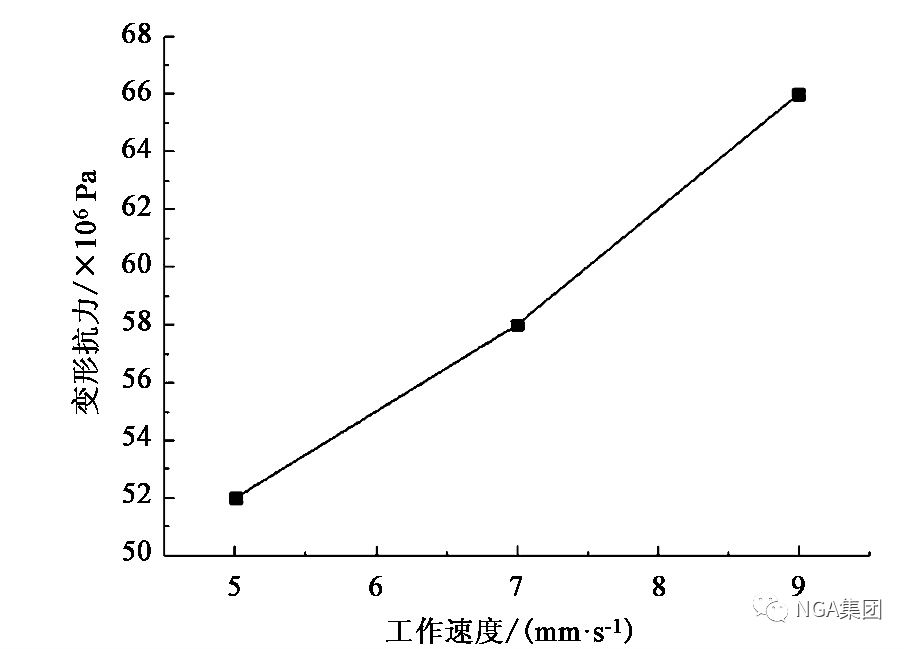
圖5 模具工作速度對(duì)變形抗力的影響
模具工作速度的增大,導(dǎo)致變形抗力增加。因此,結(jié)合實(shí)際生產(chǎn)情況和工作效率,量減小模具工作速度,工作速度宜選擇在5~7mm·s-1之間。
下模窗口處圓角半徑對(duì)鎂合金輪轂鍛造的影響
為研究下模窗口( 圖6a中的B區(qū)域) 圓角半徑對(duì)鎂合金輪轂鍛造的影響,選擇不同下模窗口處圓角半徑進(jìn)行仿真計(jì)算,結(jié)合模型的實(shí)際生產(chǎn)加工和重量要求等情況,其模擬模型參數(shù)設(shè)定如下:成形溫度為380℃,模具工作速度為6mm·s-1,摩擦系數(shù)為0. 1,下模窗口處圓角半徑分別為12,16和20mm。模擬結(jié)果如圖6所示。
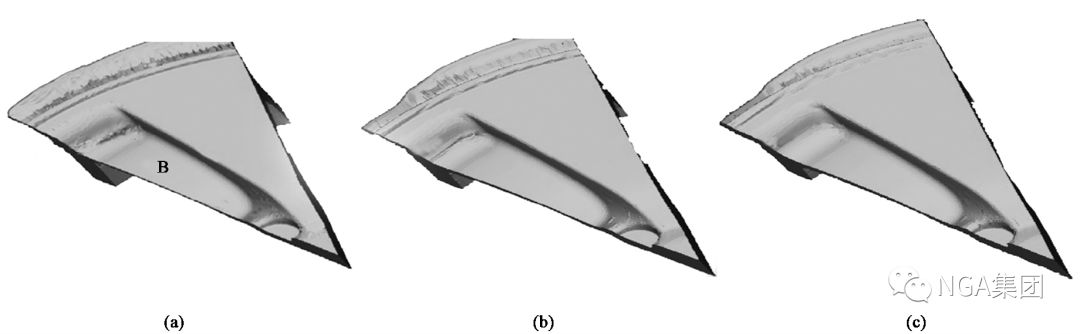
圖6 下模窗口處圓角半徑對(duì)鎂合金輪轂鍛造的影響(仿真結(jié)果)
(a) R12mm (b) R16mm (c) R20mm
從圖6可以看出:下模窗口處圓角半徑為12mm時(shí),圓角處出現(xiàn)嚴(yán)重的橫向折疊;圓角半徑為16mm時(shí),折疊現(xiàn)象減少;圓角半徑為20mm時(shí),折疊現(xiàn)象基本消失。這是因?yàn)閳A角半徑的增大,使得金屬液流動(dòng)阻力減小,充型順暢,同時(shí)減小了此處的應(yīng)力集中情況。
鎂合金輪轂鍛造試驗(yàn)
鍛造模具
本文依照模擬試驗(yàn)結(jié)果,結(jié)合該型輪轂的實(shí)際鍛造生產(chǎn),設(shè)計(jì)的鍛造模具如圖7所示。
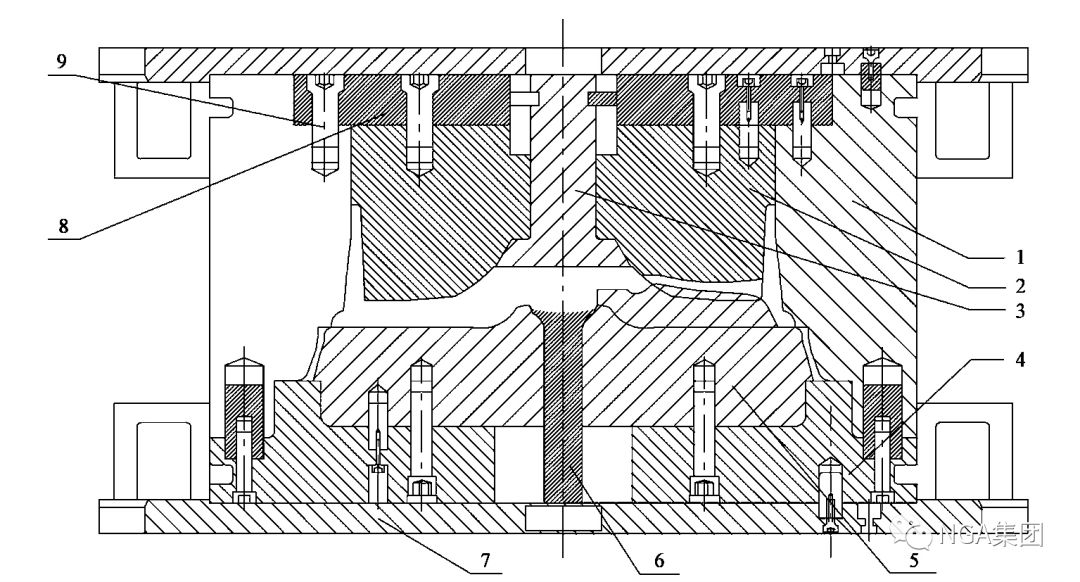
圖7 鍛造模具裝配示意圖
1. 上模座2. 上模芯3. 上頂料器4. 下模座5. 下模6. 下頂料器7. 模板8. 承壓板9. 連接螺栓
成形溫度對(duì)鎂合金輪轂鍛造的影響
進(jìn)一步對(duì)該型輪轂進(jìn)行鍛造試驗(yàn),其試驗(yàn)成形溫度T在350~ 410℃之間,試驗(yàn)結(jié)果如下:T<370℃時(shí),塑性變形能力差,輪輞處出現(xiàn)開裂現(xiàn)象,見(jiàn)圖8a;T>390℃時(shí),窗口部位出現(xiàn)疊狀的裂紋,見(jiàn)圖8b;T在370~390℃時(shí),鍛件外觀質(zhì)量較好,沒(méi)有開裂或疊狀缺陷,見(jiàn)圖8c。試驗(yàn)結(jié)果與仿真結(jié)果基本保持一致。
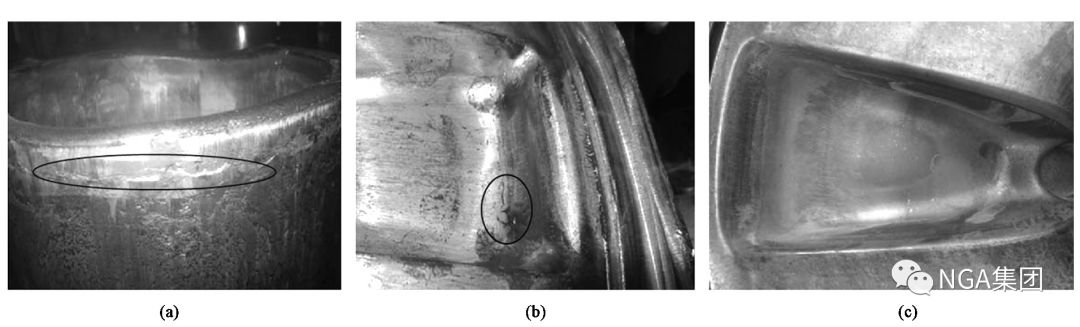
圖8 成形溫度對(duì)鎂合金輪轂鍛造的影響
(a) T< 370℃ (b)T > 390℃ (c) 370℃ <T< 390℃
模具工作速度對(duì)鎂合金輪轂鍛造的影響
模具工作速度分別為5,7和9mm·s-1,試驗(yàn)結(jié)果如圖9所示。工作速度為5和7mm·s-1時(shí),質(zhì)量良好,如圖9a和圖9b所示;工作速度為9mm·s-1時(shí),缺陷出現(xiàn)在窗口區(qū)域,如圖9c所示。試驗(yàn)結(jié)果與仿真結(jié)果基本一致。
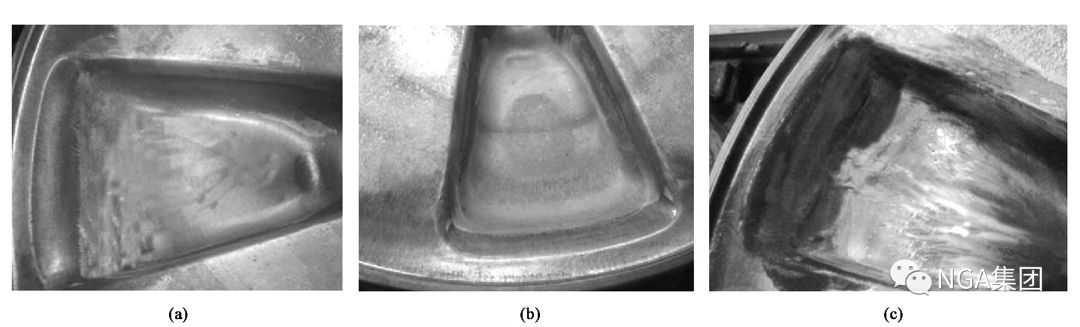
圖9 模具工作速度對(duì)鎂合金輪轂鍛造的影響
(a) 5mm·s-1 (b) 7mm·s-1 (c) 9mm·s-1
下模窗口處圓角半徑對(duì)鎂合金輪轂鍛造的影響
從試驗(yàn)的經(jīng)濟(jì)性和有效性等方面考慮,借鑒仿真分析結(jié)果,其下模窗口處圓角半徑分別選擇16和20mm兩種進(jìn)行試驗(yàn)。圓角半徑為16mm時(shí),鎂合金輪轂窗口處出現(xiàn)疊裝缺陷,如圖10a所示;圓角半徑增加至20mm時(shí),鎂合金鍛造輪轂窗口處成形良好,沒(méi)有出現(xiàn)折疊現(xiàn)象, 如圖10b所示。
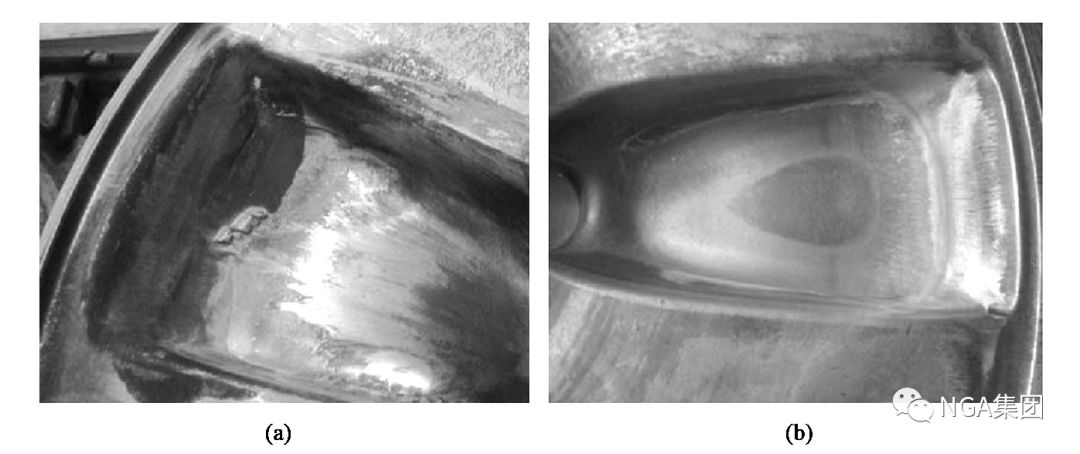
圖10 下模窗口處圓角半徑對(duì)鎂合金輪轂鍛造的影響(試驗(yàn)結(jié)果)
(a) R16mm (b) R20mm
結(jié)語(yǔ)
(1) 坯料溫度<370℃時(shí),鍛造鎂合金輪輞處產(chǎn)生開裂。坯料溫度>390℃時(shí),窗口部位出現(xiàn)裂紋。
(2) 模具工作速度為5~7mm·s-1時(shí),鎂合金輪轂鍛造成形質(zhì)量較好。工作速度超過(guò)9mm·s-1時(shí),變形抗力增加,輪轂窗口部位容易產(chǎn)生裂紋或折疊缺陷。
(3) 下模圓角半徑≤16mm時(shí),鍛造輪轂窗口處出現(xiàn)疊裝缺陷;下模圓角半徑為20mm時(shí),鎂合金輪轂質(zhì)量較好。
(4) 本文試驗(yàn)結(jié)果可以應(yīng)用于鎂合金輪轂鍛造生產(chǎn)中,同時(shí)試驗(yàn)結(jié)果與模擬計(jì)算結(jié)果的相互吻合,表明采用數(shù)值模擬計(jì)算軟件是切實(shí)可靠的,為以后其他類似研究提供了參考。
本文來(lái)自:期刊《鍛壓技術(shù)》
作者:郝孟軍,宮濤,代艷霞
舉報(bào) 0
收藏 0
分享 175
-
乘用車金屬?zèng)_壓
2025-05-29 -
沖壓技術(shù)在電機(jī)疊片制造的應(yīng)用
2024-09-06 -
車身零部件包邊質(zhì)量控制要點(diǎn)
2024-09-05 -
輕量化技術(shù)——熱汽脹形工藝技術(shù)解析
2024-09-04
最新資訊
-
數(shù)智破局啟新篇?生態(tài)共生再啟程 —
2025-06-27 20:13
-
助力汽車零部件產(chǎn)線智能化升級(jí),西門
2025-06-27 13:59
-
BBA集體轉(zhuǎn)向!放棄全面電動(dòng)化
2025-06-26 17:32
-
比換柜省錢,比自研省心,西門子X(jué)cel
2025-06-25 15:07
-
采埃孚售后再制造中心喬遷臨港 領(lǐng)航
2025-06-25 14:44