基于尺寸和表面質(zhì)量的頂蓋模具型面補(bǔ)償方法
2019-06-10 12:09:28· 來源:鍛造與沖壓 作者:趙中元,王林
針對(duì)奧迪車型天窗頂蓋沖壓模具,提出在設(shè)計(jì)階段通過對(duì)各工序模具進(jìn)行型面補(bǔ)償來保證零件的質(zhì)量;結(jié)合產(chǎn)品質(zhì)量要求,確定型面補(bǔ)償內(nèi)容為零件型面尺寸的回彈補(bǔ)償和局部表面的凹陷補(bǔ)償;結(jié)合型面補(bǔ)償?shù)牧鞒?,采用有限元分析軟件,?duì)全工序的
針對(duì)奧迪車型天窗頂蓋沖壓模具,提出在設(shè)計(jì)階段通過對(duì)各工序模具進(jìn)行型面補(bǔ)償來保證零件的質(zhì)量;結(jié)合產(chǎn)品質(zhì)量要求,確定型面補(bǔ)償內(nèi)容為零件型面尺寸的回彈補(bǔ)償和局部表面的凹陷補(bǔ)償;結(jié)合型面補(bǔ)償?shù)牧鞒?,采用有限元分析軟件,?duì)全工序的型面回彈進(jìn)行數(shù)值模擬分析,確定模具型面的補(bǔ)償方案和補(bǔ)償量,最終應(yīng)用于實(shí)際生產(chǎn),得到較為理想的結(jié)果。
頂蓋作為車身關(guān)鍵外覆蓋件之一,其沖壓件的質(zhì)量直接影響著后續(xù)的焊接工藝和車身的最終質(zhì)量;奧迪車型由于其自身質(zhì)量標(biāo)準(zhǔn)以及頂蓋與側(cè)圍采用激光焊接工藝,因而對(duì)頂蓋沖壓?jiǎn)渭某叽缇群捅砻尜|(zhì)量有著相對(duì)更高的要求。然而由于鋼板材料本身的特性以及頂蓋產(chǎn)品結(jié)構(gòu)的特點(diǎn),零件在沖壓成形后會(huì)產(chǎn)生回彈且無法避免;進(jìn)而導(dǎo)致零件尺寸發(fā)生偏差以及表面產(chǎn)生一些無法避免的質(zhì)量缺陷。在模具調(diào)試階段對(duì)這些問題進(jìn)行優(yōu)化時(shí),往往需要對(duì)型面進(jìn)行頻繁的燒焊甚至將模具降面,影響模具的制造進(jìn)度,成本也大幅提高。如果在設(shè)計(jì)階段,根據(jù)產(chǎn)品質(zhì)量要求和以往車型的實(shí)際生產(chǎn)經(jīng)驗(yàn),結(jié)合數(shù)值模擬分析,對(duì)模具各工序型面進(jìn)行合理的補(bǔ)償,那么不僅可以有效保證零件的質(zhì)量,還可以大幅提高效率,降低模具制造成本。
產(chǎn)品特征及沖壓工藝概述
天窗頂蓋產(chǎn)品如圖1 所示,產(chǎn)品外表面為一張A級(jí)曲面;按照頂蓋在車身上的位置、產(chǎn)品結(jié)構(gòu)主要可以分為以下幾個(gè)區(qū)域:前風(fēng)窗區(qū)域A、與側(cè)圍激光焊接區(qū)域B、天窗區(qū)域C 和尾部(近背門處)流水槽區(qū)域D,從各區(qū)域輪廓線法向的截面特征可以看出,產(chǎn)品四周相對(duì)于整車Z 向均為負(fù)角,流水槽區(qū)域形狀較為復(fù)雜,而且深度也相對(duì)較大。
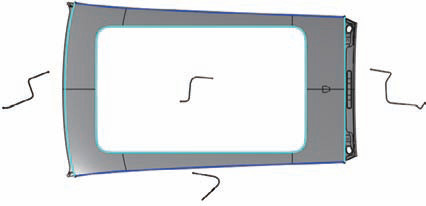
圖1 典型頂蓋產(chǎn)品
根據(jù)產(chǎn)品結(jié)構(gòu)特征,結(jié)合沖壓工藝設(shè)計(jì)的基本理論,其沖壓工藝設(shè)計(jì)如圖2 所示,共需要六道工序:前風(fēng)窗區(qū)域通過拉延、修邊、整形、斜楔整形及沖孔五道工序成形;側(cè)圍焊接區(qū)域通過拉延、修邊、翻邊及斜楔翻邊四道工序成形;天窗區(qū)域采用拉延、修邊、翻整三道工序成形,其中翻整工序采用夾料整形;流水槽區(qū)域的成形工藝直接影響著零件最終質(zhì)量,成形難度相對(duì)較大,需要拉延、預(yù)修邊、一次整形、斜楔整形、修邊沖孔、上翻加切邊六道工序成形,并且一次整形和斜楔整形的區(qū)域兩側(cè)采用壓料整形,以保證成形質(zhì)量最優(yōu)及調(diào)試便捷。
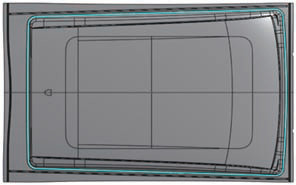
(a) OP20 拉延
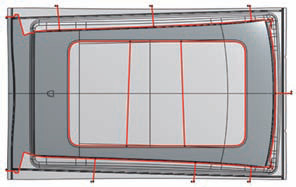
(b) OP30 修邊
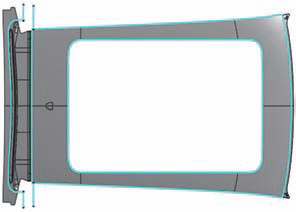
(c) OP40 翻整
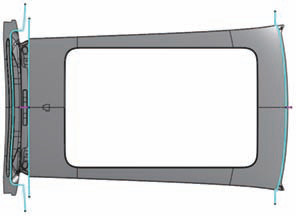
(d) OP50 側(cè)整
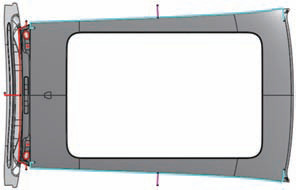
(e) OP60 側(cè)整修邊
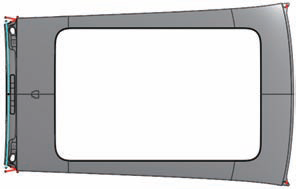
(f) OP70 翻整修邊
圖2 沖壓工藝
型面補(bǔ)償內(nèi)容
尺寸
頂蓋產(chǎn)品本身曲率較小且單一,產(chǎn)品剛度相對(duì)較差,結(jié)合多個(gè)車型的生產(chǎn)經(jīng)驗(yàn),剛度不僅影響著沖壓件尺寸和表面質(zhì)量的穩(wěn)定性,也對(duì)焊接工藝的穩(wěn)定性有著較大的影響。為保證成形后的產(chǎn)品剛性,要求中心區(qū)域自由型面尺寸控制在0.5 ~ 1.0mm 之間,即保證頂蓋稍外凸;為保證匹配間隙和目視效果,車身前后兩端和天窗的輪廓公差要求為±0.3mm;車身兩側(cè)與側(cè)圍搭接區(qū)域輪廓要做到0 ~ 0.5mm,并且長(zhǎng)度在300mm 內(nèi)尺寸偏差的波動(dòng)量不超過0.2mm,以保證激光焊接的焊縫質(zhì)量;在主型面尺寸穩(wěn)定合格的前提下,只要對(duì)輪廓進(jìn)行了合理的公差偏移和加工偏差預(yù)留,對(duì)翻邊工序預(yù)留合理的回彈角,那么輪廓尺寸便比較容易保證,因此尺寸保障的關(guān)鍵在于對(duì)主型面進(jìn)行回彈補(bǔ)償以保證零件主型面尺寸合格。
表面質(zhì)量
圖3 為完成天窗和流水槽區(qū)域成形后,結(jié)合應(yīng)力狀態(tài),對(duì)可能產(chǎn)生表面缺陷區(qū)域的模擬預(yù)測(cè),通過模擬結(jié)果可以看出,產(chǎn)生表面缺陷的區(qū)域主要有產(chǎn)品四角、天窗四角和流水槽上方的表面;由于產(chǎn)品造型和沖壓工藝的特點(diǎn),成形結(jié)束零件內(nèi)部應(yīng)力釋放后,局部會(huì)存在殘余應(yīng)力,且應(yīng)力分布不均勻,從而使零件產(chǎn)生表面缺陷,工藝上很難消除,實(shí)際生產(chǎn)經(jīng)驗(yàn)也確實(shí)如此。對(duì)于表面區(qū)域,要求黑車無扣分項(xiàng);對(duì)流水槽結(jié)構(gòu)面的區(qū)域,由于是內(nèi)可視區(qū),同樣要求無起皺、沖擊線等缺陷;產(chǎn)品四個(gè)角部以及結(jié)構(gòu)面部分表面質(zhì)量通過合理的沖壓工藝以及后續(xù)調(diào)試比較容易保證;難點(diǎn)是天窗四角和流水槽上方的表面凹陷,尤其是天窗角部在安裝完天窗之后,表面質(zhì)量經(jīng)常會(huì)發(fā)生惡化,從而對(duì)單件的要求更高;因此需要通過對(duì)局部型面進(jìn)行凹陷補(bǔ)償,以保障零件的表面質(zhì)量。
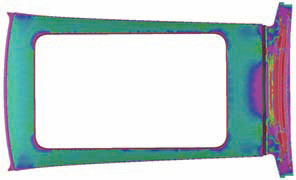
圖3 表面缺陷預(yù)測(cè)
型面補(bǔ)償方法
補(bǔ)償流程概述
通過前述分析,為保障零件質(zhì)量,需要對(duì)頂蓋的模具型面進(jìn)行針對(duì)尺寸回彈和局部表面凹陷的補(bǔ)償;型面補(bǔ)償進(jìn)行的前提是沖壓工藝模擬的各項(xiàng)評(píng)價(jià)指標(biāo),如減薄率、起皺開裂、滑移線、沖擊線等能夠滿足質(zhì)量要求并且工藝足夠穩(wěn)定,即工藝“最優(yōu)化”;整個(gè)工作流程如圖4 所示,首先結(jié)合零件的測(cè)量方式,對(duì)全工序進(jìn)行精確回彈模擬,根據(jù)各工序的回彈模擬結(jié)果,分析回彈產(chǎn)生的原因和工序,如果回彈后的零件尺寸無法滿足產(chǎn)品公差要求,則根據(jù)回彈產(chǎn)生的工序確定回彈補(bǔ)償方案,結(jié)合產(chǎn)品公差要求和回彈量確定補(bǔ)償量;補(bǔ)償之后,對(duì)結(jié)果進(jìn)行二次模擬驗(yàn)證,保證回彈之后的尺寸在公差允許的范圍之內(nèi),然后進(jìn)行各工序的模面替換,最后對(duì)局部區(qū)域進(jìn)行表面凹陷補(bǔ)償,完成整個(gè)補(bǔ)償工作。
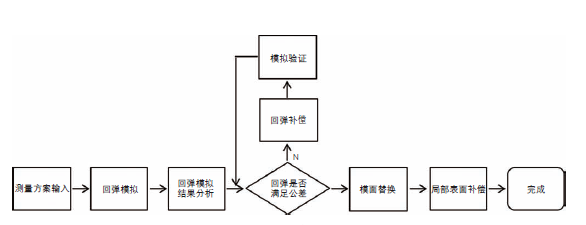
圖4 型面補(bǔ)償流程
彈模擬分析
采用Autoform 分別對(duì)各工序的回彈進(jìn)行模擬,回彈模擬的參數(shù)設(shè)置按照Autoform 軟件標(biāo)準(zhǔn)。實(shí)際生產(chǎn)過程中,單件的測(cè)量過程是在測(cè)量支架上完成的,支架形式如圖5 所示;由于產(chǎn)品本身剛性較差,產(chǎn)品自身重力也會(huì)對(duì)成品件的回彈結(jié)果產(chǎn)生一定的影響,因此回彈輸出結(jié)果是綜合考慮重力和夾持狀態(tài)的回彈,但過度的夾持也會(huì)導(dǎo)致型面發(fā)生扭曲,真實(shí)的回彈被強(qiáng)行消除,從而使回彈補(bǔ)償無法實(shí)現(xiàn);因此考慮采用一種優(yōu)化的夾持方案,即僅考慮支撐和圖5 處標(biāo)示的夾持,以保證回彈結(jié)果能夠真實(shí)的體現(xiàn)出實(shí)際狀態(tài)。
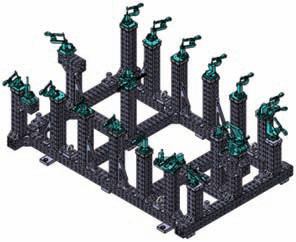
圖5 測(cè)量支架
圖6 為各工序成形完成后的回彈狀態(tài),OP20 拉延成形后,拉延件中部稍有塌陷,周邊法蘭發(fā)生翹曲。OP30 切邊后應(yīng)力釋放,零件中部塌陷顯著增加;OP40 四周及天窗翻邊完成后,產(chǎn)品初步定形,回彈后前角翹曲,中部塌陷;OP50 前后側(cè)整形之后,翹曲顯著增大;OP60 相對(duì)前序,趨勢(shì)一致,但區(qū)域和回彈量有所變化;OP70 由于僅對(duì)局部進(jìn)行翻邊成形,對(duì)整體型面的回彈影響不大,回彈結(jié)果與OP60 基本一致。
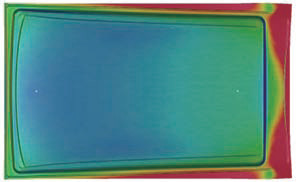
(a) OP20 拉延
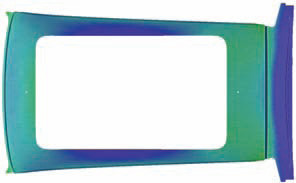
(b) OP30 修邊
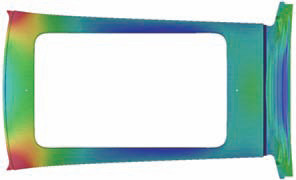
(c) OP40 翻整
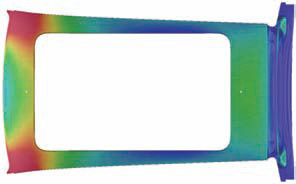
(d) OP50 側(cè)整
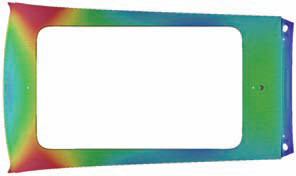
(e) OP60 側(cè)整修邊
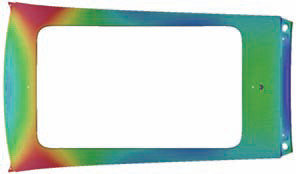
(f) OP70 翻整修邊
圖6 各工序回彈狀態(tài)
型面補(bǔ)償
綜合上述分析,結(jié)合表面質(zhì)量?jī)?yōu)化,型面補(bǔ)償方案設(shè)計(jì)如圖7 所示,在OP20 到OP60 對(duì)主型面進(jìn)行尺寸回彈補(bǔ)償,在OP50 對(duì)流水槽局部型面進(jìn)行尺寸回彈補(bǔ)償;在OP40 對(duì)天窗角部表面缺陷進(jìn)行補(bǔ)償;在OP40 和OP50 對(duì)流水槽區(qū)域的表面缺陷進(jìn)行補(bǔ)償;側(cè)翻邊回彈角度按照1.5°~ 3°預(yù)留,OP70 不采取補(bǔ)償。根據(jù)計(jì)算得到的回彈結(jié)果和表面調(diào)試相關(guān)經(jīng)驗(yàn),補(bǔ)償區(qū)域見圖8a 和8b,尺寸方面,兩個(gè)前角下壓4mm,中間型面隆起1.2mm;流水槽局部補(bǔ)償0 ~ 1.5mm;表面方面,天窗四角補(bǔ)償0.05 ~ 0.15mm,流水槽上方補(bǔ)償0 ~ 0.2mm。補(bǔ)償后的回彈模擬結(jié)果見圖8c,模擬結(jié)果基本達(dá)到了預(yù)期。
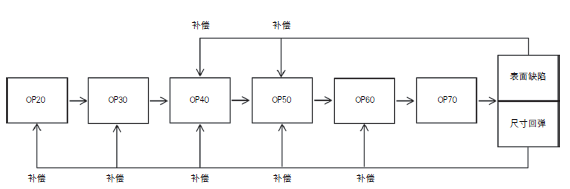
圖7 型面補(bǔ)償方案
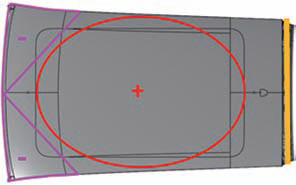
(a) 尺寸補(bǔ)償區(qū)域
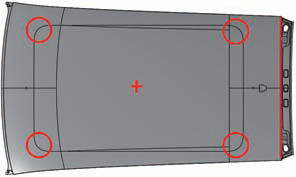
(b) 表面補(bǔ)償區(qū)域
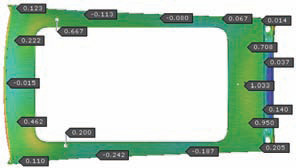
(c) 補(bǔ)償后回彈結(jié)果
圖8 補(bǔ)償區(qū)域和最終結(jié)果
實(shí)際零件質(zhì)量
采用補(bǔ)償后的模具型面制造模具,模具加工裝配完畢,完成各工序著色研配和翻邊間隙確認(rèn)后,零件的尺寸狀態(tài)和天窗口的表面質(zhì)量狀態(tài)如圖9 所示,型面尺寸基本控制在公差內(nèi),中間區(qū)域的最大量在1mm 左右;達(dá)到了預(yù)期效果,焊接后白車身質(zhì)量沒有問題,未進(jìn)行二次整改;天窗前角基本無缺陷,后角為C1 類缺陷(單件油石打磨局部不連續(xù),后續(xù)黑車光影稍有不順,用戶不會(huì)抱怨),流水槽上方也是C1 類缺陷;由此可以看出,通過前期對(duì)型面進(jìn)行補(bǔ)償,很好地保證了零件的質(zhì)量,相較于以往車型的多輪整改,大大提高了效率。
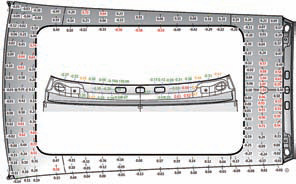
(a) 型面尺寸
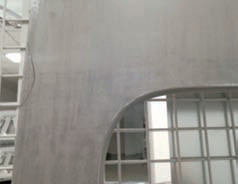
(b) 天窗前角
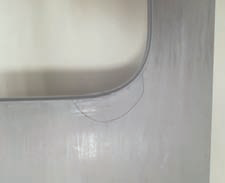
(c) 天窗后角
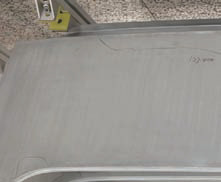
(d) 流水槽上方
圖9 實(shí)際零件的尺寸和表面狀態(tài)
結(jié)束語
對(duì)于沖壓模具制造,在滿足零件質(zhì)量要求的前提下,如何降低模具成本和縮短制造周期,是業(yè)內(nèi)人士不斷探討的話題;在前期設(shè)計(jì)階段,結(jié)合以往生產(chǎn)經(jīng)驗(yàn),對(duì)零件的質(zhì)量缺陷進(jìn)行分析預(yù)測(cè),并采取有效措施,無疑會(huì)帶來非常明顯的效果;本文基于某車型頂蓋,對(duì)設(shè)計(jì)階段采用型面補(bǔ)償來保證零件質(zhì)量的整體思路和方法進(jìn)行了論述;首先通過對(duì)零件質(zhì)量要求的分析論述,得出主型面的尺寸精度和局部的表面質(zhì)量是保證零件質(zhì)量達(dá)標(biāo)的關(guān)鍵;據(jù)此確定型面補(bǔ)償是針對(duì)尺寸回彈和局部表面凹陷兩方面內(nèi)容的補(bǔ)償;按照補(bǔ)償流程,通過數(shù)值模擬分析結(jié)合實(shí)際生產(chǎn)經(jīng)驗(yàn),確定了各序型面的補(bǔ)償方案和補(bǔ)償量。采用補(bǔ)償后的型面制造沖壓模具,最終獲得了理想的結(jié)果。希望這種針對(duì)型面尺寸和表面質(zhì)量的補(bǔ)償思路能夠給制造高品質(zhì)沖壓外覆蓋件模具提供一定參考。
舉報(bào) 0
收藏 0
分享 117
-
乘用車金屬?zèng)_壓
2025-05-29 -
沖壓技術(shù)在電機(jī)疊片制造的應(yīng)用
2024-09-06 -
車身零部件包邊質(zhì)量控制要點(diǎn)
2024-09-05 -
輕量化技術(shù)——熱汽脹形工藝技術(shù)解析
2024-09-04
最新資訊
-
跨越速運(yùn)憑什么“圈粉”萬千客戶?“
2025-07-01 14:42
-
數(shù)智破局啟新篇?生態(tài)共生再啟程 —
2025-06-27 20:13
-
助力汽車零部件產(chǎn)線智能化升級(jí),西門
2025-06-27 13:59
-
BBA集體轉(zhuǎn)向!放棄全面電動(dòng)化
2025-06-26 17:32
-
比換柜省錢,比自研省心,西門子Xcel
2025-06-25 15:07