某SUV轎車后背門內(nèi)外板一模三件工藝開發(fā)
2019-04-10 23:49:41· 來源:蘇傳義,邰偉彬 鍛造與沖壓
某SUV轎車后背門分總成如圖1所示,主要由后背門外板-上部、后背門外板-下部、后背門內(nèi)板和左右燈盒5個(gè)零件組成,其中,后背門外板-上/下部材料為ST07Z-05-60/60,料厚為0.7mm;內(nèi)板材料為ST07Z-60/60,料厚為0.7mm。后背門外板-上部
某SUV轎車后背門分總成如圖1所示,主要由后背門外板-上部、后背門外板-下部、后背門內(nèi)板和左右燈盒5個(gè)零件組成,其中,后背門外板-上/下部材料為ST07Z-05-60/60,料厚為0.7mm;內(nèi)板材料為ST07Z-60/60,料厚為0.7mm。后背門外板-上部與后背門外板-下部采用激光焊接,然后與燈盒焊接,最后與后背門內(nèi)板采用機(jī)器人壓合,完成后背門分總成產(chǎn)品。
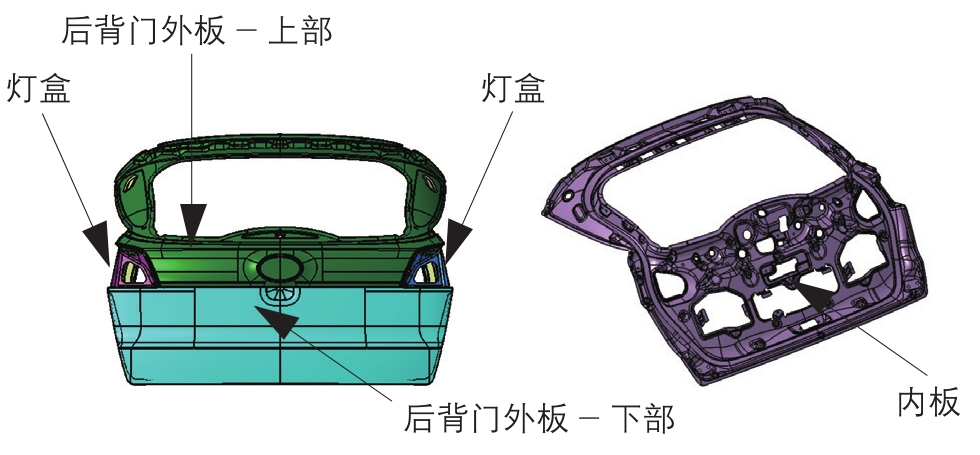
圖1 轎車后背門分總成
常規(guī)工藝規(guī)劃方案
為了充分利用大型沖壓設(shè)備,提高生產(chǎn)效率,后背門內(nèi)板、后背門外板-上部兩個(gè)件采用一模雙槽的工藝規(guī)劃方案,共需四道工序分別為拉延、側(cè)修邊沖孔、側(cè)修邊沖孔翻邊、側(cè)沖孔翻邊整形,如圖2所示。
后背門外板-下部的工藝規(guī)劃方案為單獨(dú)制作,由拉延、修邊沖孔、翻邊三道工序完成,如圖3所示。

圖2 一模雙槽工藝規(guī)劃方案
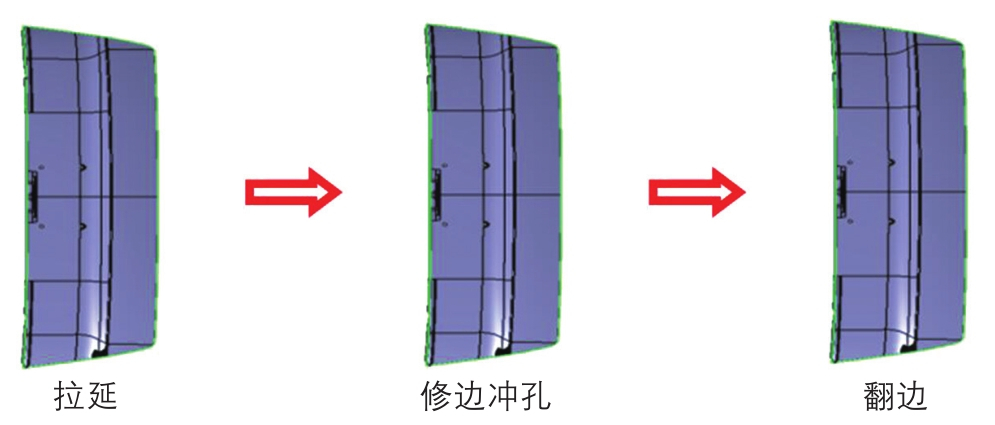
圖3 后背門外板-下部工藝規(guī)劃方案
這三個(gè)產(chǎn)品共需7套模具,需要組織兩次生產(chǎn),采用常規(guī)工藝方案生產(chǎn)效率低。
一模三件工藝規(guī)劃方案
本文通過產(chǎn)品開發(fā)的同步工程,提出一種新的工藝規(guī)劃方案,即一模三件工藝規(guī)劃方案,在產(chǎn)品開發(fā)過程中,進(jìn)行CAE分析,確定方案的可行性。
外板-上部與下部對接拉延成形,采用一張板料,與內(nèi)板一起制作,采用雙槽結(jié)構(gòu),共需4道工序分別為拉延、側(cè)修邊沖孔、側(cè)修邊沖孔翻邊、側(cè)沖孔翻邊整形,如圖4所示。
圖4 一模三件工藝規(guī)劃方案
這套方案生產(chǎn)三個(gè)產(chǎn)品共需4套模具,一次沖壓生產(chǎn)即可完成三個(gè)件的制作,生產(chǎn)效率高。
后背門外板-上部、下部對接工藝可行性分析
后背門外板-上部、下部對接拉延是否可行,是該方案的核心。這是一種全新的工藝方案,國內(nèi)沒有這方面的先例,所以必須進(jìn)行CAE模擬分析,進(jìn)行方案可行性確定。
⑴拉延造型設(shè)計(jì)。
由于后背門外板-上部的下側(cè)需要側(cè)翻邊、側(cè)整形,所以不能在此側(cè)對接,只能在上側(cè)對接,根據(jù)后背門外板-下部的形狀特點(diǎn),其下側(cè)與后背門外板-上部的上側(cè)對接,進(jìn)行拉延工藝設(shè)計(jì),如圖5所示。
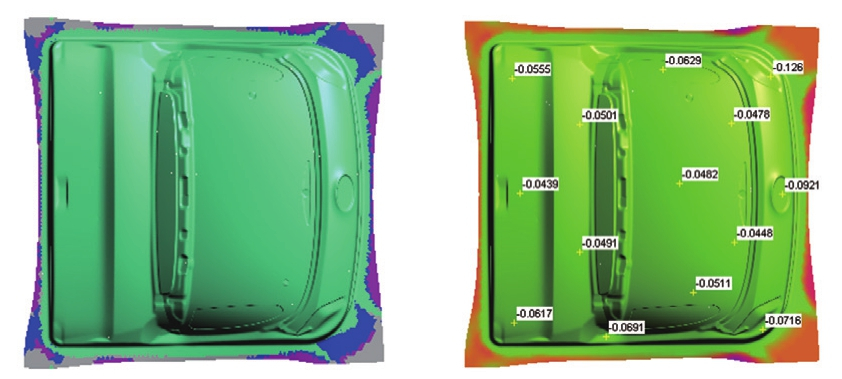
圖5 拉延造型
⑵拉延CAE模擬分析。
模擬分析主要檢查開裂、起皺、棱線滑移、沖擊線、制件的變薄率等是否滿足質(zhì)量要求。經(jīng)過多輪CAE分析,包括放大產(chǎn)品圓角、更改產(chǎn)品形狀、調(diào)整壓料面、改善工藝補(bǔ)充等措施,得到較好的CAE分析結(jié)果:沒有起皺開裂現(xiàn)象,變薄率可達(dá)到4%以上,如圖6所示。
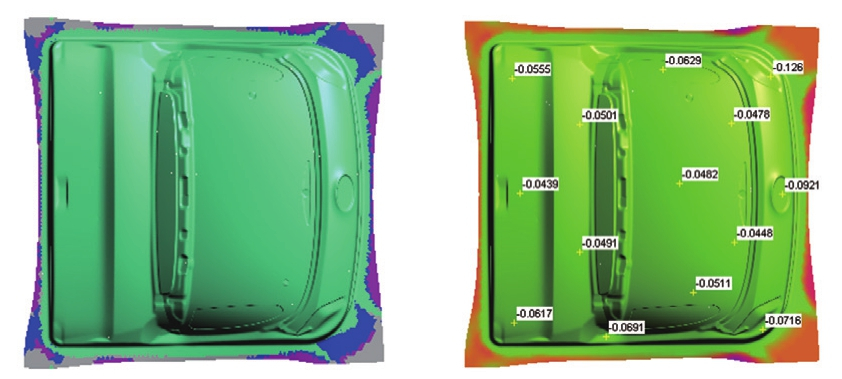
圖6 CAE模擬分析結(jié)果
特征棱線滑移線狀態(tài)分析,如圖7所示。其中,特征線1:后背門外板-上部主特征線最小曲率半徑R12mm,材料經(jīng)過凸模圓角產(chǎn)生的滑移線8mm。由于是凸模剛與板料接觸時(shí)產(chǎn)生的滑移,此時(shí)接觸壓力小,圓角大,不會產(chǎn)生面品缺陷;特征線2:后背門外板-上部特征線最小曲率半徑R3mm,材料經(jīng)過凸模圓角產(chǎn)生的滑移線3mm。由于是凸模剛與板料接觸時(shí)產(chǎn)生的滑移,此時(shí)接觸壓力小,當(dāng)圓角逐漸形成后,板料不再滑移,不會產(chǎn)生面品缺陷;特征線3:后背門外板-下部特征線最小曲率半徑R5.5mm,材料經(jīng)過凸模圓角產(chǎn)生的滑移線4mm。由于是凸模剛與板料接觸時(shí)產(chǎn)生的滑移,此時(shí)接觸壓力小,當(dāng)圓角逐漸形成后,板料不再滑移,不會產(chǎn)生面品缺陷。
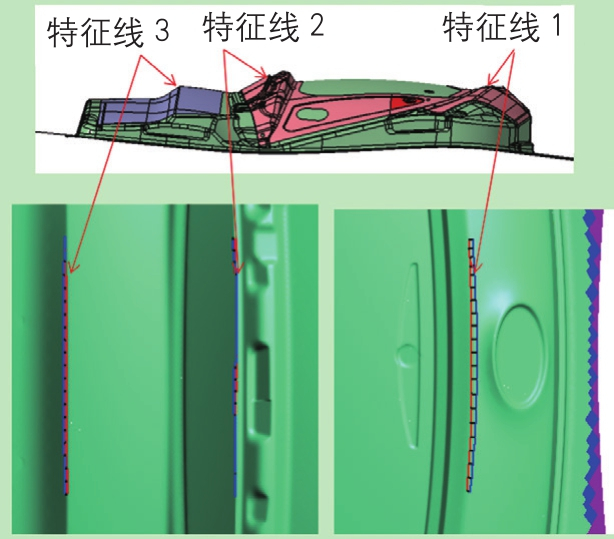
圖7 特征棱線滑移線狀態(tài)分析
⑶后序模擬分析結(jié)果。
后背門外板-上部拉延以后,各工序的模擬分析結(jié)果如圖8所示。通過CAE分析,后背門外板-上部、下部對接拉延工藝方案可行。
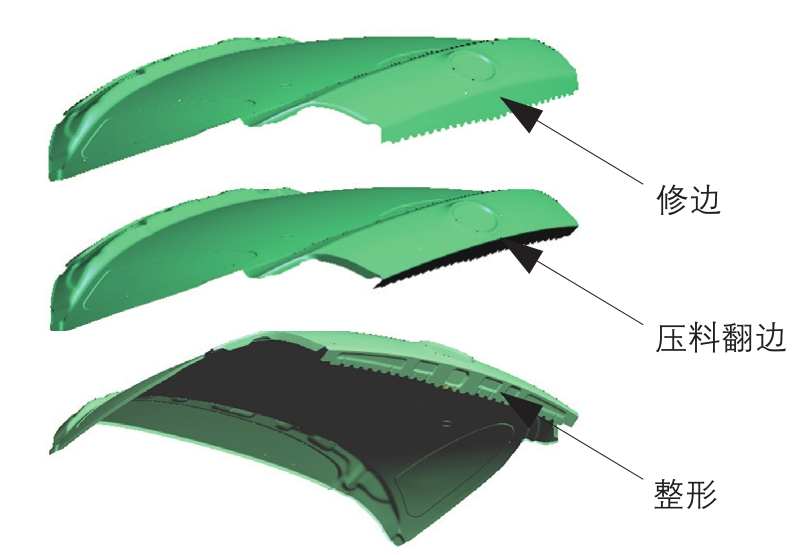
圖8 后序模擬分析結(jié)果
后背門外板-上部、下部沖壓工藝過程
后背門外板-上部、下部4道工序的沖壓工藝過程如圖9所示。另外,后背門外板-上部與下部搭接處的孔無法在4序內(nèi)完成,為了節(jié)省模具投資,在焊裝車間增加氣動(dòng)沖孔工裝完成,如圖10所示。
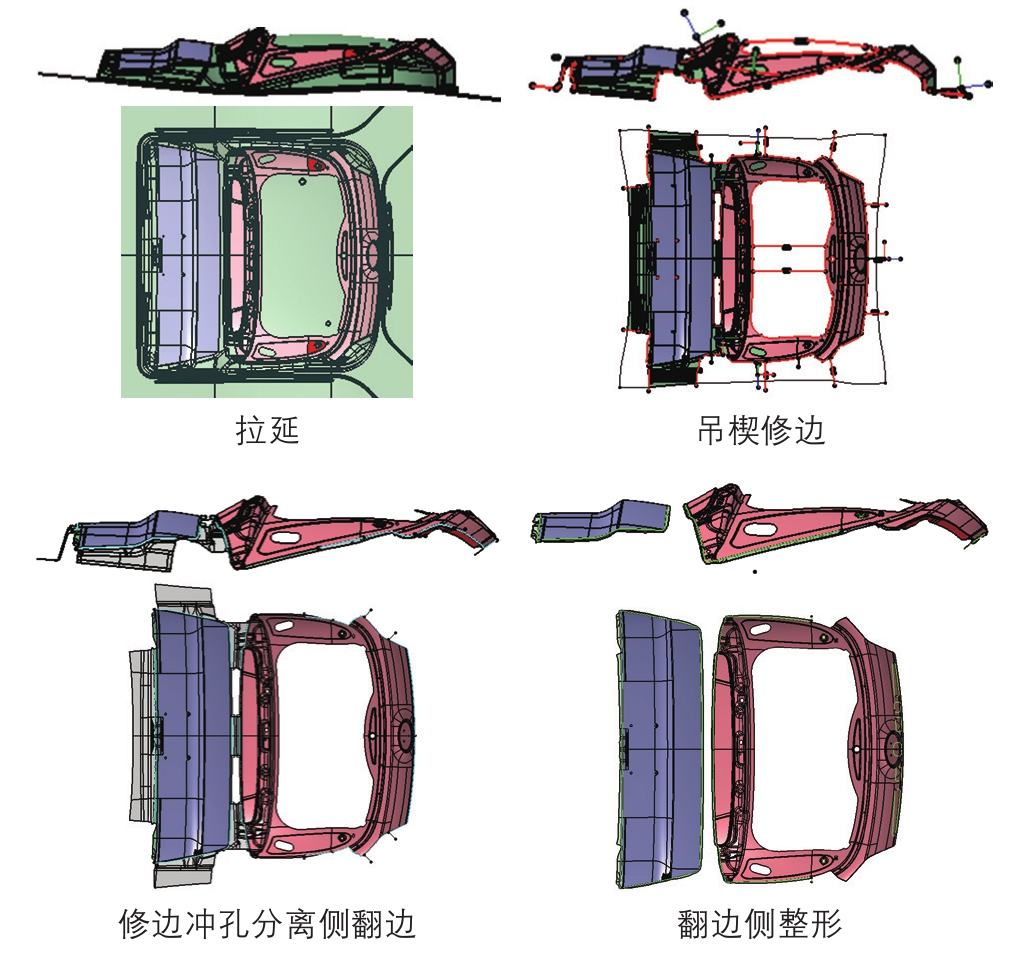
圖9 沖壓工藝過程圖
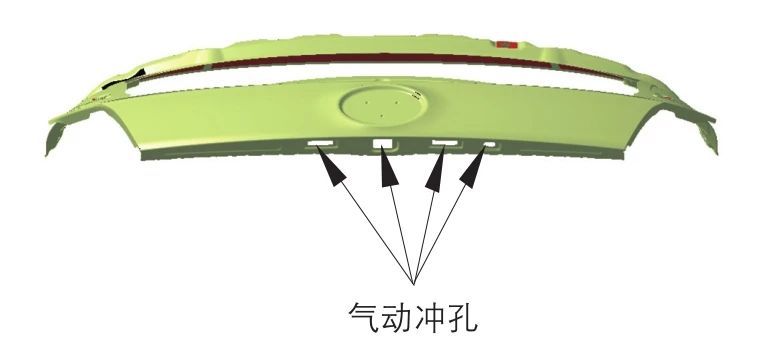
圖10 氣動(dòng)沖孔
后背門內(nèi)板沖壓工藝過程
⑴后背門內(nèi)板拉延CAE分析。后背門內(nèi)板采用單動(dòng)拉延結(jié)構(gòu),由于形狀復(fù)雜以及拉延深度深,存在多處開裂、起皺問題,經(jīng)過多輪CAE分析,產(chǎn)品得到優(yōu)化,但產(chǎn)品工藝性仍然不算太好,還要依賴沖壓工藝解決。在矩形板料上沖制兩個(gè)工藝孔,并且在拉延到底前10mm刺破,這樣就解決了開裂和起皺問題,如圖11所示。
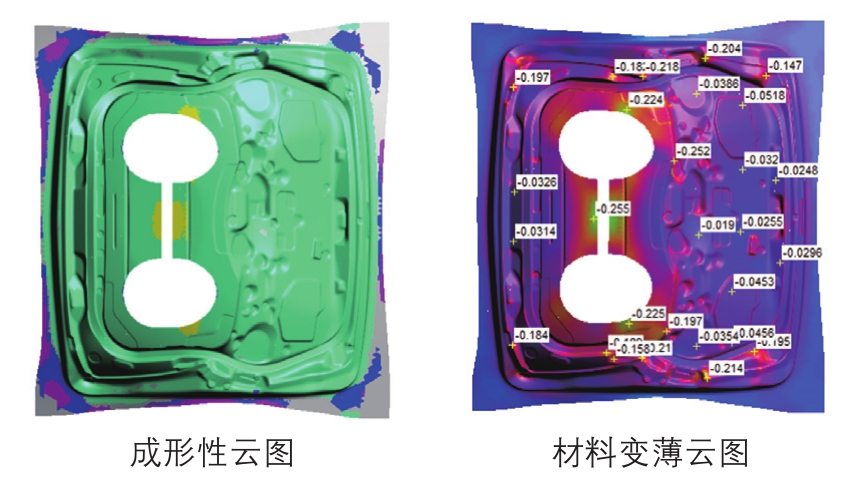
圖11 CAE模擬分析結(jié)果
⑵后背門內(nèi)板沖壓工藝過程。 后背門內(nèi)板4道工序的沖壓工藝過程,如圖12所示。
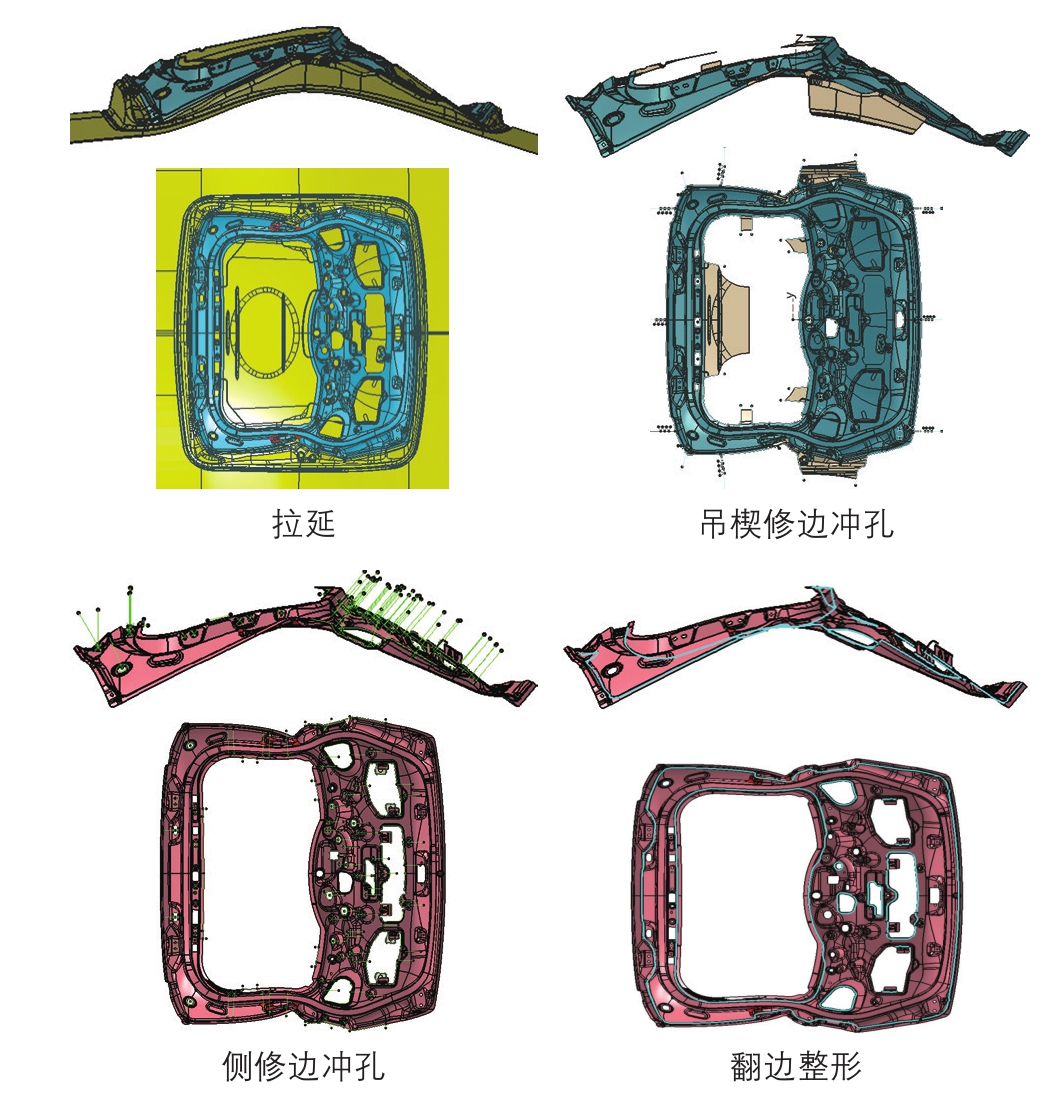
圖12 后背門內(nèi)板沖壓工藝過程圖
生產(chǎn)驗(yàn)證
通過產(chǎn)品開發(fā)過程的同步工程方法,提前進(jìn)行工藝方案的規(guī)劃,并進(jìn)行沖壓工藝可行性分析,沖壓工藝設(shè)計(jì),輸出合理的沖壓工藝方案,使一模三件工藝得到實(shí)際應(yīng)用。它的優(yōu)點(diǎn)是:⑴節(jié)省了三套模具,降低了模具投資。⑵一次生產(chǎn)三件,提高了生產(chǎn)效率,降低了生產(chǎn)成本。⑶減少材料消耗定額,材料利用率提高12%左右。批量生產(chǎn)實(shí)物照片,如圖13所示。
圖13 生產(chǎn)實(shí)物照片
——本文節(jié)選自《鍛造與沖壓》2019年第6期。
舉報(bào) 0
收藏 0
分享 128
-
乘用車金屬沖壓
2025-05-29 -
沖壓技術(shù)在電機(jī)疊片制造的應(yīng)用
2024-09-06 -
車身零部件包邊質(zhì)量控制要點(diǎn)
2024-09-05 -
輕量化技術(shù)——熱汽脹形工藝技術(shù)解析
2024-09-04
最新資訊
-
跨越速運(yùn)憑什么“圈粉”萬千客戶?“
2025-07-01 14:42
-
數(shù)智破局啟新篇?生態(tài)共生再啟程 —
2025-06-27 20:13
-
助力汽車零部件產(chǎn)線智能化升級,西門
2025-06-27 13:59
-
BBA集體轉(zhuǎn)向!放棄全面電動(dòng)化
2025-06-26 17:32
-
比換柜省錢,比自研省心,西門子Xcel
2025-06-25 15:07