虛擬加工技術在東風日產(chǎn)鍛造生產(chǎn)中的應用
2018-09-07 13:11:06· 來源:杜蓮蓮,高磊 鍛造與沖壓
隨著工業(yè)4.0的發(fā)展,機械化、數(shù)字化和無線互聯(lián)相組合構建了新的體系,很多工廠也相繼提出了建設智能工廠的藍圖。對于鍛造工廠來說,要建設智能化工廠,需要的不僅僅是智能化的生產(chǎn)控制中心、全自動的生產(chǎn)線和自動化的倉儲物流,智能化的
隨著工業(yè)4.0的發(fā)展,機械化、數(shù)字化和無線互聯(lián)相組合構建了新的體系,很多工廠也相繼提出了建設智能工廠的藍圖。對于鍛造工廠來說,要建設智能化工廠,需要的不僅僅是智能化的生產(chǎn)控制中心、全自動的生產(chǎn)線和自動化的倉儲物流,智能化的生產(chǎn)過程管控是建設智能工廠的一大重要基石。隨著汽車的輕量化發(fā)展,鍛造產(chǎn)品也在逐步進行輕量化,不管從鍛件結(jié)構上還是加工余量上都有了較大的改進,尤其是加工余量的減小對鍛造工藝和鍛造品質(zhì)管控來說是一個較大的挑戰(zhàn)。鍛造的虛擬加工技術及時在這樣的背景下應運而生,下面以鍛造曲軸為例來進行說明。
虛擬加工技術工作原理
在曲軸輕量化的基礎上,曲軸的曲柄基本不再進行加工或者加工余量非常小,而這也導致曲軸的不平衡可修正的范圍變小。這對曲軸鍛造工藝水平的要求也就越來越高,因此能夠在鍛造毛坯狀態(tài)就判斷出曲軸的加工余量是否足夠以及加工后的動平衡是否達標,對鍛造工程來說也就變得越來越必要,可以有效的減少自工程不良品的數(shù)量以及減少后工程加工不良品的工時。當然,判斷產(chǎn)品是否合格只是其中一個方面,更重要的是要能夠通過產(chǎn)品的狀態(tài)查找出造成產(chǎn)品不良的原因。
虛擬加工技術能夠在鍛造毛坯狀態(tài)下測定曲軸的加工余量、靜平衡量并給出動平衡修正的建議值,同時可以通過收集每個平衡塊的數(shù)據(jù)預測查找不平衡的原因,并有針對性的對鍛造工藝進行調(diào)整。
虛擬加工機(圖1)是通過激光掃描器及測量感應器將夾持的工件進行3D數(shù)據(jù)采集后傳入計算機的虛擬加工系統(tǒng)中進行計算分析的設備。
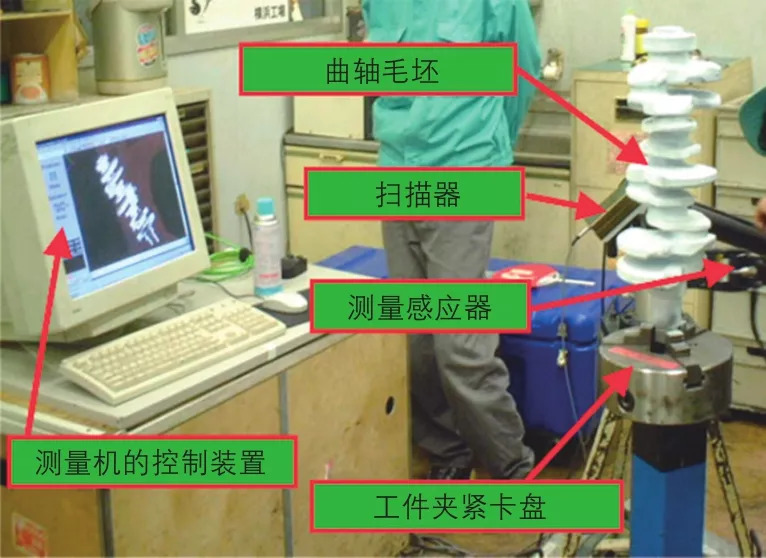
圖1 虛擬加工機
曲軸虛擬加工系統(tǒng)(圖2)主要由6部分構成:①測量3D數(shù)據(jù)→②生成立體數(shù)據(jù)→③確定加工定位點→④模擬加工演算→⑤計算體積、重心→⑥計算平衡數(shù)據(jù)。
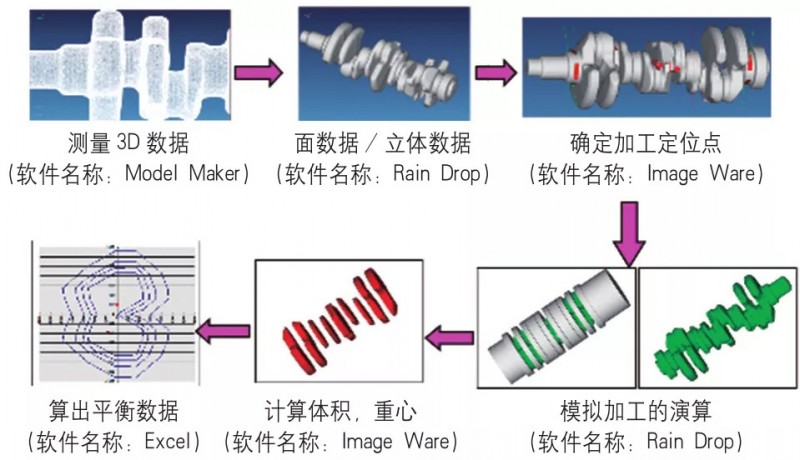
圖2 曲軸虛擬加工系統(tǒng)
⑴測量3D數(shù)據(jù)。
通過激光掃描器及測量感應器將采集到的工件的點數(shù)據(jù)傳入計算機中。
⑵面數(shù)據(jù)/立體數(shù)據(jù)。
將點數(shù)據(jù)轉(zhuǎn)換成立體數(shù)據(jù)和面數(shù)據(jù),形成了與實際工件一致的3D圖形,便于后續(xù)分析。
⑶確定加工定位點。
為了更真實的模擬實際加工的數(shù)據(jù),采用實際加工生產(chǎn)線的定位基準作為虛擬加工的定位點。
⑷模擬加工演算。
根據(jù)實際的加工量模擬加工鍛造曲軸毛坯,得出曲軸加工后的形狀,便于核算其不平衡量。
⑸計算體積、重心。
分別計算出每個曲柄的體積和重心,分析出每個部位與理論值之間的偏差值。
⑹計算平衡數(shù)據(jù)。
最終計算出前后兩端的平衡中心,數(shù)據(jù)如果落在可修正范圍內(nèi),則可通過調(diào)整加工中心孔位置使曲軸達成平衡。虛擬加工平衡值的平均誤差約為37.5g·cm。
虛擬加工技術在曲軸鍛造生產(chǎn)中的應用
虛擬加工技術不僅僅能夠預測曲軸的不平衡量,在生產(chǎn)中還有多種應用。曲軸是有很多不規(guī)則形狀曲面的鍛件,在生產(chǎn)過程中的抽樣檢查一般只能做到對主要的產(chǎn)品尺寸進行檢查,無法進行產(chǎn)品全部尺寸的檢查,而虛擬加工技術可以采集到產(chǎn)品的3D形狀,可對產(chǎn)品的任何一部分的數(shù)據(jù)進行確認和分析,可以很好的指導生產(chǎn),提升產(chǎn)品的品質(zhì)。
⑴為加工生產(chǎn)線提供平衡調(diào)整建議。
以直列四缸曲軸為例,通過虛擬加工系統(tǒng)測量出不平衡量并描繪出中心孔的目標坐標和計算坐標,同時給出中心孔的調(diào)整量。
同一個批次20件工件的平均值作為本批次工件加工中心孔的初始坐標值,可以大幅度的降低加工時動平衡的修正量以及減少因超出修正范圍而造成的動平衡不良的廢品,既降低了曲軸加工的動平衡不良率,又節(jié)約了動平衡修正的工時。
⑵通過鍛造曲軸毛坯形狀檢查進行工藝調(diào)整。
虛擬加工技術可將掃描到的3D圖形與標準圖形進行對比(圖3),利用顏色標示出其與標準圖形的差距,可以一目了然的看出產(chǎn)品的哪一個部位超出了公差范圍,給生產(chǎn)線的品質(zhì)改善和工藝調(diào)整找出了明確的點。
虛擬加工技術可對曲軸的任何斷面進行輪廓檢查(圖4),對于形狀差異較大的部位可以調(diào)取其斷面輪廓進行具體分析,能夠更準確的查找鍛造過程中鍛件變形的原因,更快的做出有針對性的對策。
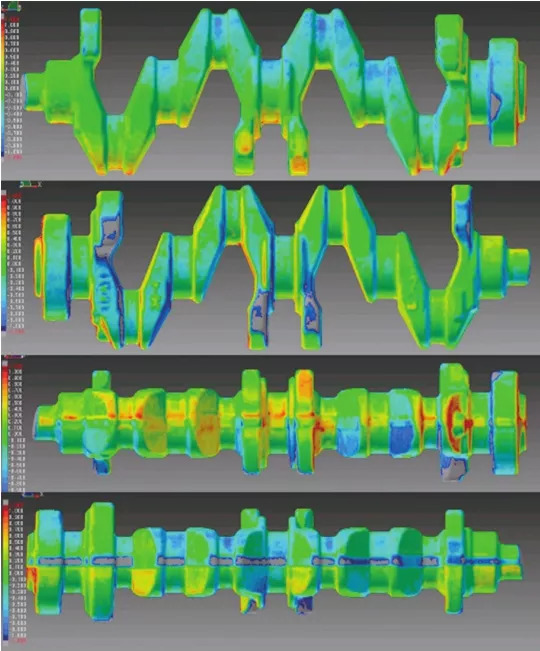
圖3 鍛件形狀檢查圖
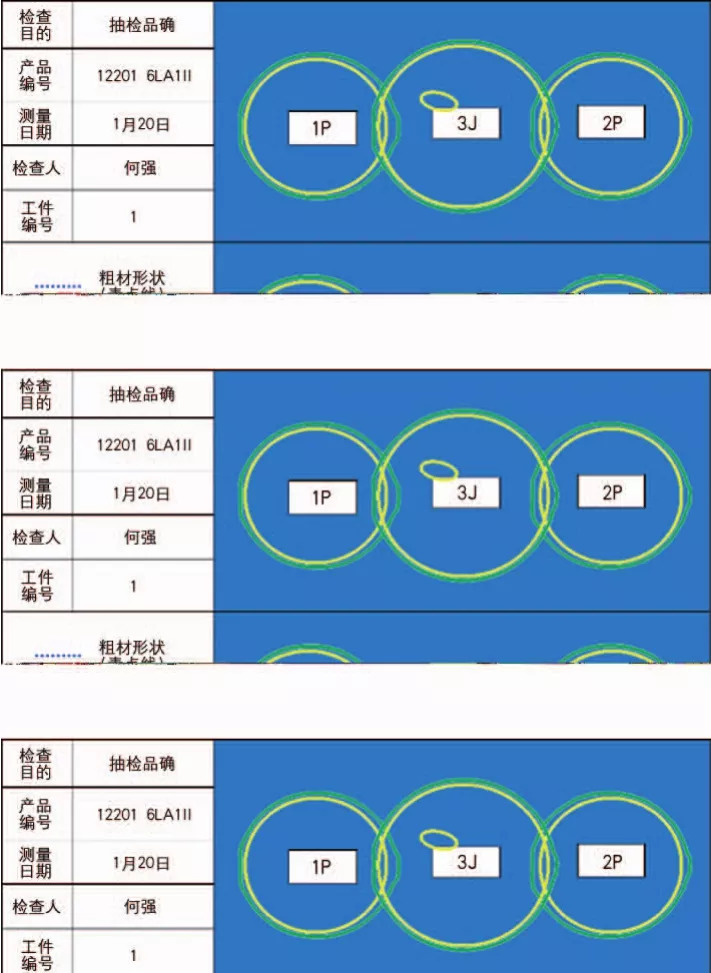
圖4 斷面輪廓檢查圖
⑶通過虛擬加工預測加工后曲軸的外觀品質(zhì)。
通過虛擬加工技術可以模擬出鍛件加工后的3D圖形,可以一目了然的看出加工部位在加工后是否有黑皮殘留,這將便于找出鍛件磕碰傷、凹坑、欠肉等不良的極限樣本,也可以為一些需要打磨修復的鍛件表面?zhèn)O立打磨標準,避免了上加工生產(chǎn)線進行試加工的麻煩。圖5所示為鍛件表面磕碰或打磨痕跡模擬,圖6所示為鍛件欠肉部位加工模擬。
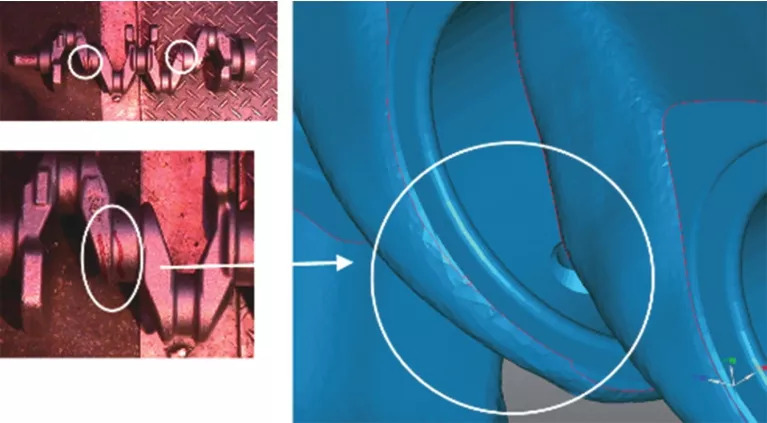
圖5 鍛件表面磕碰或打磨痕跡模擬
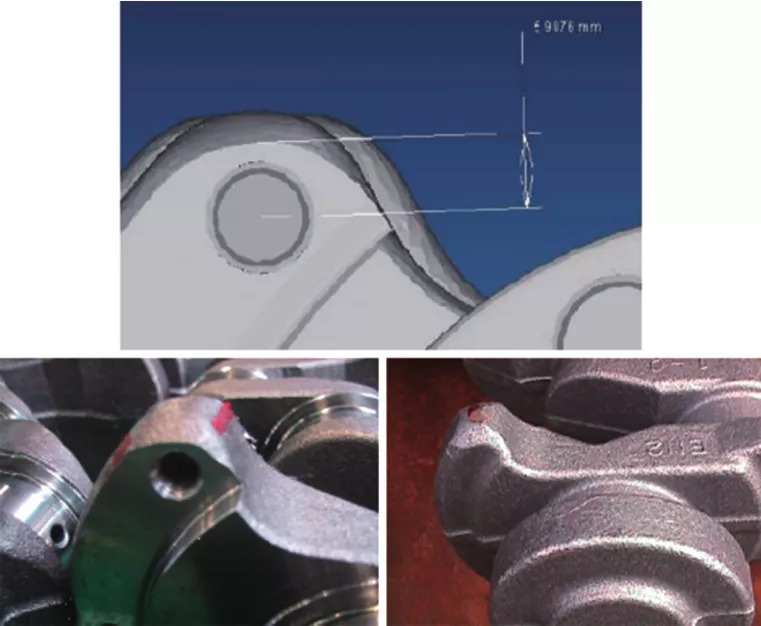
圖6 鍛件欠肉部位加工模擬
⑷通過掃描模具可以進行模具改善。
鍛造模具在生產(chǎn)過程中會產(chǎn)生磨損,這對產(chǎn)品的品質(zhì)及生產(chǎn)的穩(wěn)定性也會產(chǎn)生較大的影響,掌握模具的實際磨損情況對改善產(chǎn)品品質(zhì)、提升模具壽命、降低模具成本等至關重要,而虛擬加工技術可以通過掃描使用后的模具表面確認模具表面磨損的實際情況,將數(shù)據(jù)進行反饋,根據(jù)反饋的數(shù)據(jù)可進行多方面的對策,使用更高耐磨的焊材進行補焊,根據(jù)數(shù)據(jù)在模具設計上進行預對策,等等。
結(jié)束語
綜上所述,虛擬加工技術在曲軸鍛造生產(chǎn)中有著非常重要的地位,其最重要的便是能夠在毛坯狀態(tài)下預測其加工后的平衡值,并且能夠得到每個平衡塊的數(shù)據(jù),可明確的找出導致不平衡量較大的具體部位,為鍛造工程的改善提供了明確的方向,有效地解決了加工前無法判斷平衡、加工后無法找出導致不平衡部位的窘?jīng)r。另外,虛擬加工技術也能夠?qū)Ξa(chǎn)品進行全方位模擬,為品質(zhì)改善、工藝改善、模具改善、模具設計等方面提供重要的指導,這也使得虛擬加工技術在鍛造生產(chǎn)中占有越來越重要的指導地位。
——本文選自《鍛造與沖壓》2018年第17期
虛擬加工技術工作原理
在曲軸輕量化的基礎上,曲軸的曲柄基本不再進行加工或者加工余量非常小,而這也導致曲軸的不平衡可修正的范圍變小。這對曲軸鍛造工藝水平的要求也就越來越高,因此能夠在鍛造毛坯狀態(tài)就判斷出曲軸的加工余量是否足夠以及加工后的動平衡是否達標,對鍛造工程來說也就變得越來越必要,可以有效的減少自工程不良品的數(shù)量以及減少后工程加工不良品的工時。當然,判斷產(chǎn)品是否合格只是其中一個方面,更重要的是要能夠通過產(chǎn)品的狀態(tài)查找出造成產(chǎn)品不良的原因。
虛擬加工技術能夠在鍛造毛坯狀態(tài)下測定曲軸的加工余量、靜平衡量并給出動平衡修正的建議值,同時可以通過收集每個平衡塊的數(shù)據(jù)預測查找不平衡的原因,并有針對性的對鍛造工藝進行調(diào)整。
虛擬加工機(圖1)是通過激光掃描器及測量感應器將夾持的工件進行3D數(shù)據(jù)采集后傳入計算機的虛擬加工系統(tǒng)中進行計算分析的設備。
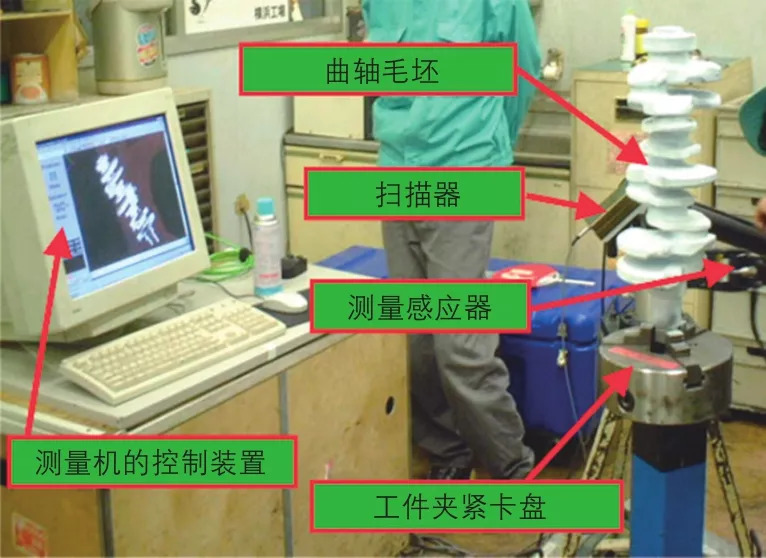
圖1 虛擬加工機
曲軸虛擬加工系統(tǒng)(圖2)主要由6部分構成:①測量3D數(shù)據(jù)→②生成立體數(shù)據(jù)→③確定加工定位點→④模擬加工演算→⑤計算體積、重心→⑥計算平衡數(shù)據(jù)。
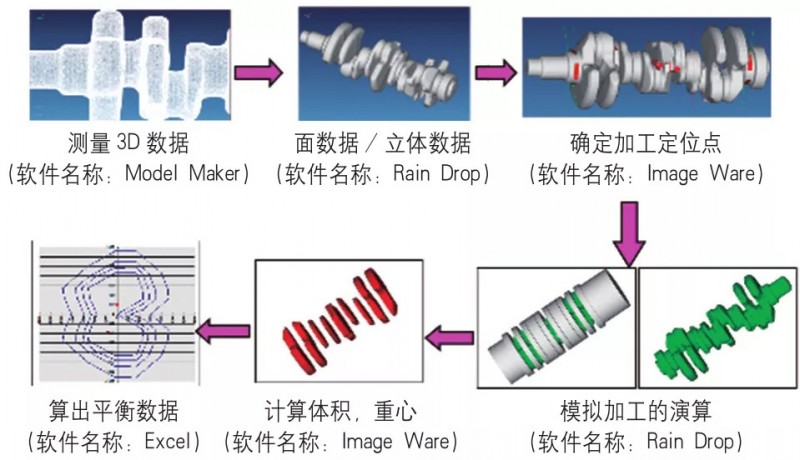
圖2 曲軸虛擬加工系統(tǒng)
⑴測量3D數(shù)據(jù)。
通過激光掃描器及測量感應器將采集到的工件的點數(shù)據(jù)傳入計算機中。
⑵面數(shù)據(jù)/立體數(shù)據(jù)。
將點數(shù)據(jù)轉(zhuǎn)換成立體數(shù)據(jù)和面數(shù)據(jù),形成了與實際工件一致的3D圖形,便于后續(xù)分析。
⑶確定加工定位點。
為了更真實的模擬實際加工的數(shù)據(jù),采用實際加工生產(chǎn)線的定位基準作為虛擬加工的定位點。
⑷模擬加工演算。
根據(jù)實際的加工量模擬加工鍛造曲軸毛坯,得出曲軸加工后的形狀,便于核算其不平衡量。
⑸計算體積、重心。
分別計算出每個曲柄的體積和重心,分析出每個部位與理論值之間的偏差值。
⑹計算平衡數(shù)據(jù)。
最終計算出前后兩端的平衡中心,數(shù)據(jù)如果落在可修正范圍內(nèi),則可通過調(diào)整加工中心孔位置使曲軸達成平衡。虛擬加工平衡值的平均誤差約為37.5g·cm。
虛擬加工技術在曲軸鍛造生產(chǎn)中的應用
虛擬加工技術不僅僅能夠預測曲軸的不平衡量,在生產(chǎn)中還有多種應用。曲軸是有很多不規(guī)則形狀曲面的鍛件,在生產(chǎn)過程中的抽樣檢查一般只能做到對主要的產(chǎn)品尺寸進行檢查,無法進行產(chǎn)品全部尺寸的檢查,而虛擬加工技術可以采集到產(chǎn)品的3D形狀,可對產(chǎn)品的任何一部分的數(shù)據(jù)進行確認和分析,可以很好的指導生產(chǎn),提升產(chǎn)品的品質(zhì)。
⑴為加工生產(chǎn)線提供平衡調(diào)整建議。
以直列四缸曲軸為例,通過虛擬加工系統(tǒng)測量出不平衡量并描繪出中心孔的目標坐標和計算坐標,同時給出中心孔的調(diào)整量。
同一個批次20件工件的平均值作為本批次工件加工中心孔的初始坐標值,可以大幅度的降低加工時動平衡的修正量以及減少因超出修正范圍而造成的動平衡不良的廢品,既降低了曲軸加工的動平衡不良率,又節(jié)約了動平衡修正的工時。
⑵通過鍛造曲軸毛坯形狀檢查進行工藝調(diào)整。
虛擬加工技術可將掃描到的3D圖形與標準圖形進行對比(圖3),利用顏色標示出其與標準圖形的差距,可以一目了然的看出產(chǎn)品的哪一個部位超出了公差范圍,給生產(chǎn)線的品質(zhì)改善和工藝調(diào)整找出了明確的點。
虛擬加工技術可對曲軸的任何斷面進行輪廓檢查(圖4),對于形狀差異較大的部位可以調(diào)取其斷面輪廓進行具體分析,能夠更準確的查找鍛造過程中鍛件變形的原因,更快的做出有針對性的對策。
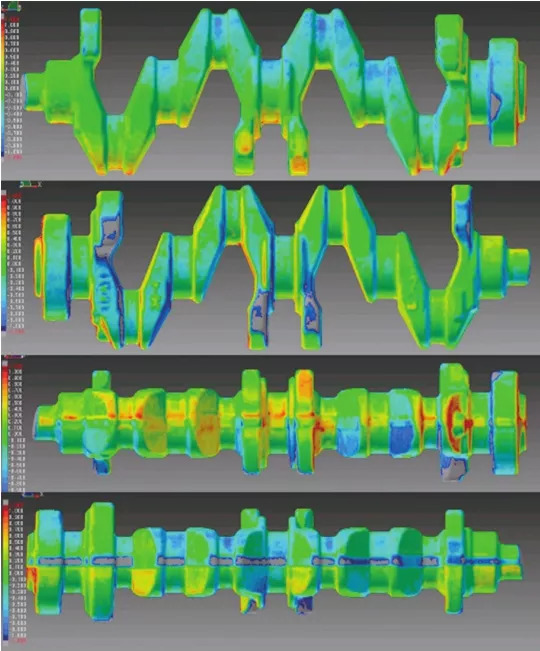
圖3 鍛件形狀檢查圖
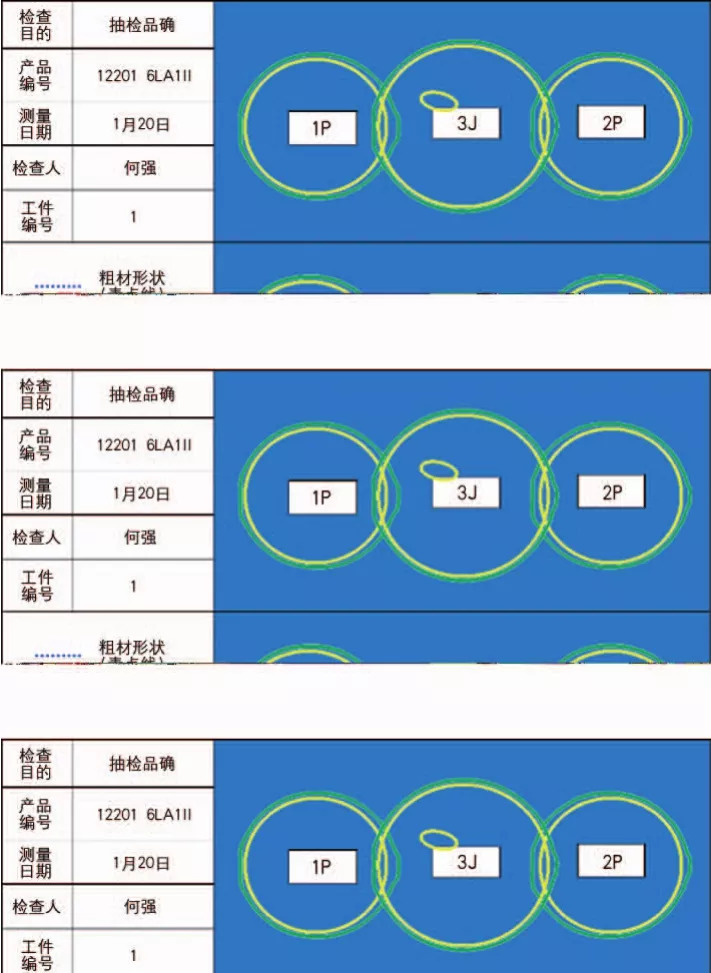
圖4 斷面輪廓檢查圖
⑶通過虛擬加工預測加工后曲軸的外觀品質(zhì)。
通過虛擬加工技術可以模擬出鍛件加工后的3D圖形,可以一目了然的看出加工部位在加工后是否有黑皮殘留,這將便于找出鍛件磕碰傷、凹坑、欠肉等不良的極限樣本,也可以為一些需要打磨修復的鍛件表面?zhèn)O立打磨標準,避免了上加工生產(chǎn)線進行試加工的麻煩。圖5所示為鍛件表面磕碰或打磨痕跡模擬,圖6所示為鍛件欠肉部位加工模擬。
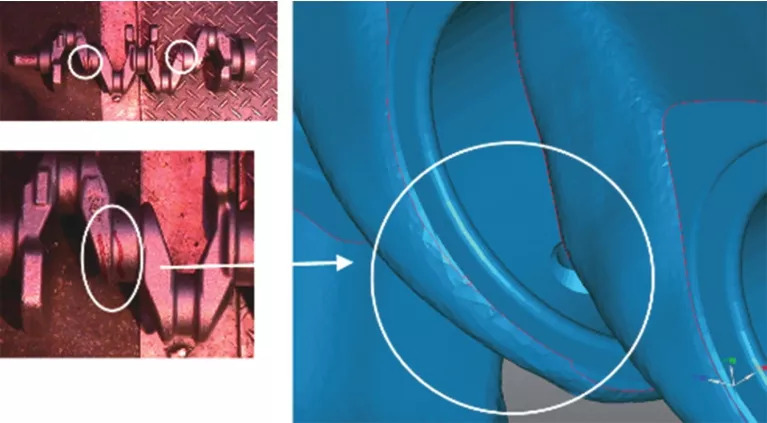
圖5 鍛件表面磕碰或打磨痕跡模擬
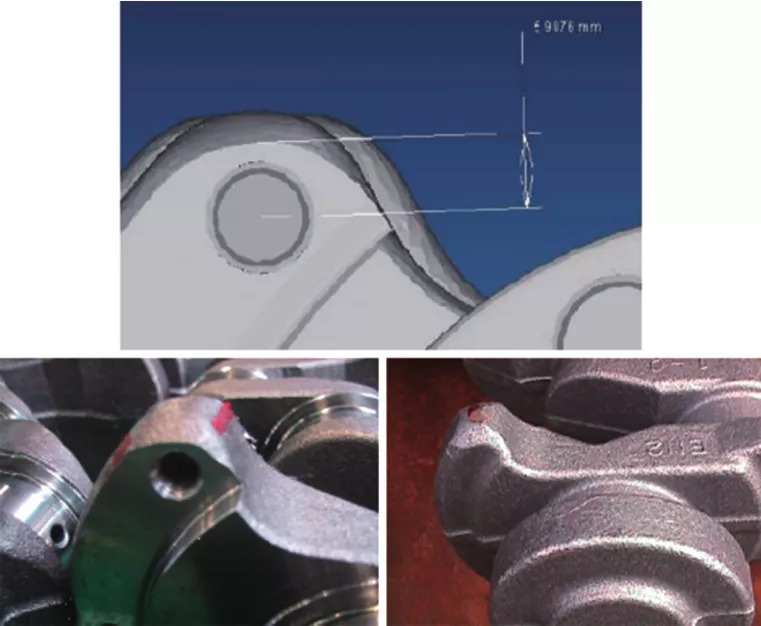
圖6 鍛件欠肉部位加工模擬
⑷通過掃描模具可以進行模具改善。
鍛造模具在生產(chǎn)過程中會產(chǎn)生磨損,這對產(chǎn)品的品質(zhì)及生產(chǎn)的穩(wěn)定性也會產(chǎn)生較大的影響,掌握模具的實際磨損情況對改善產(chǎn)品品質(zhì)、提升模具壽命、降低模具成本等至關重要,而虛擬加工技術可以通過掃描使用后的模具表面確認模具表面磨損的實際情況,將數(shù)據(jù)進行反饋,根據(jù)反饋的數(shù)據(jù)可進行多方面的對策,使用更高耐磨的焊材進行補焊,根據(jù)數(shù)據(jù)在模具設計上進行預對策,等等。
結(jié)束語
綜上所述,虛擬加工技術在曲軸鍛造生產(chǎn)中有著非常重要的地位,其最重要的便是能夠在毛坯狀態(tài)下預測其加工后的平衡值,并且能夠得到每個平衡塊的數(shù)據(jù),可明確的找出導致不平衡量較大的具體部位,為鍛造工程的改善提供了明確的方向,有效地解決了加工前無法判斷平衡、加工后無法找出導致不平衡部位的窘?jīng)r。另外,虛擬加工技術也能夠?qū)Ξa(chǎn)品進行全方位模擬,為品質(zhì)改善、工藝改善、模具改善、模具設計等方面提供重要的指導,這也使得虛擬加工技術在鍛造生產(chǎn)中占有越來越重要的指導地位。
——本文選自《鍛造與沖壓》2018年第17期
舉報 0
收藏 0
分享 106
-
乘用車金屬沖壓
2025-05-29 -
沖壓技術在電機疊片制造的應用
2024-09-06 -
車身零部件包邊質(zhì)量控制要點
2024-09-05 -
輕量化技術——熱汽脹形工藝技術解析
2024-09-04
最新資訊
-
跨越速運憑什么“圈粉”萬千客戶?“
2025-07-01 14:42
-
數(shù)智破局啟新篇?生態(tài)共生再啟程 —
2025-06-27 20:13
-
助力汽車零部件產(chǎn)線智能化升級,西門
2025-06-27 13:59
-
BBA集體轉(zhuǎn)向!放棄全面電動化
2025-06-26 17:32
-
比換柜省錢,比自研省心,西門子Xcel
2025-06-25 15:07