汽車輕量化技術(shù)手段探討
2018-07-18 14:59:42· 來源:CST汽車輕量化
本文汽車輕量化是在保證汽車強度和安全性能的前提下,盡可能地降低汽車的質(zhì)量,從而提高汽車的動力利用率,減少燃料消耗,降低排氣污染。汽車輕量化還能提高汽車的駕乘動力學性能(如加速、制動、過彎穩(wěn)定性、碰撞慣性等),而這類性能的改善一直是車輛設(shè)計者、制造商和用戶追求的目標。
摘要:
本文汽車輕量化是在保證汽車強度和安全性能的前提下,盡可能地降低汽車的質(zhì)量,從而提高汽車的動力利用率,減少燃料消耗,降低排氣污染。汽車輕量化還能提高汽車的駕乘動力學性能(如加速、制動、過彎穩(wěn)定性、碰撞慣性等),而這類性能的改善一直是車輛設(shè)計者、制造商和用戶追求的目標。
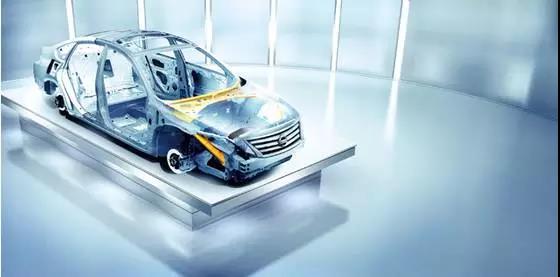
汽車輕量化是目前國內(nèi)外汽車廠商普遍研究的一個熱點,也是未來汽車發(fā)展的必然方向。研究表明,約75%的油耗與整車質(zhì)量有關(guān),降低汽車質(zhì)量就可有效降低油耗以及排放。
大量研究表明,汽車質(zhì)量每下降10%,油耗下降8%,排放下降4%。對商用車的研究表明,汽車質(zhì)量每減1000kg,油耗可降低6%~7%。油耗的下降,意味著CO2、氮氧化物(NOx)等有害氣體排放量的下降。因此,車身變輕對于整車的燃油經(jīng)濟性、車輛控制穩(wěn)定性、碰撞安全性都大有裨益。當前,由于環(huán)保和節(jié)能的需要,汽車輕量化已經(jīng)成為世界汽車發(fā)展的潮流。
構(gòu)成汽車的2萬多個零件中,約有86%是金屬材料,且鋼鐵占了約80%,這表明通過材料的輕量化來減輕汽車自重有巨大潛力。目前,鋁合金、鎂合金、高強度鋼、工程塑料和復(fù)合材料等輕質(zhì)材料的開發(fā)和應(yīng)用在汽車輕量化中發(fā)揮了重大作用。為了提升市場競爭力,國內(nèi)外汽車廠商均在進行汽車輕量化技術(shù)的研究,并力求應(yīng)用到汽車制造中,以保持自己在市場競爭中的有利地位。
但是,汽車輕量化并非只是簡單地降低汽車重量,它必須在保證汽車安全性、整車NVH性能、可制造性以及經(jīng)濟性等各種前提下實現(xiàn)輕量化。同時,汽車輕量化涉及汽車上的每個部件,各個部件之間又相互影響、相互制約,每個部件在材料選擇、制造工藝、結(jié)構(gòu)設(shè)計等方面也都有不同的設(shè)計要求。因此,汽車輕量化是一個多領(lǐng)域技術(shù)綜合作用的系統(tǒng)工程。
汽車輕量化方法
目前,國內(nèi)外實現(xiàn)汽車輕量化的主要技術(shù)手段包括使用新材料、采用新工藝和輕量化結(jié)構(gòu)設(shè)計等三大方面。
1使用新材料
隨著材料科學的發(fā)展,新型高強度、低密度輕質(zhì)材料(如高強度鋼、鋁合金、鎂合金、高分子材料和復(fù)合材料等)在汽車制造中正逐步替代傳統(tǒng)鋼鐵。目前正廣泛研究并逐步應(yīng)用于汽車制造的有:超高強度鋼、鋁合金、鎂合金以及復(fù)合材料等。
國內(nèi)輕量化新材料研究方面,同濟大學將7075鋁合金應(yīng)用于汽車保險杠系統(tǒng)中,通過有限元軟件LS-DYNA對不同厚度保險杠模型的低速碰撞進行仿真分析。在碰撞性能相同的條件下,相比原鋼質(zhì)材料,采用鋁合金可使保險杠質(zhì)量下降20.5%。
上海交通大學通過建立某款轎車發(fā)動機罩板的有限元模型,選擇鋁合金材料替換原有鋼材料,以罩板綜合性能為約束,結(jié)合優(yōu)化設(shè)計方法,考慮板材的成形性因素?;谠间摻Y(jié)構(gòu)空間布局進行全新設(shè)計,在滿足結(jié)構(gòu)性能要求和可制造性的前提下使罩板的質(zhì)量減輕47.1%。
目前發(fā)達國家汽車的單車塑料平均使用量超過150kg,占汽車總重量的12%~20%,而我國單車塑料使用量約占汽車自重的7%~10%。工程塑料在汽車工業(yè)上的應(yīng)用雖然越來越廣泛,但是由于我國汽車零部件標準體系不健全、國內(nèi)企業(yè)科研投入不足、自主創(chuàng)新能力不足等因素的影響,很大程度上制約了我國工程塑料的發(fā)展。
奇瑞汽車股份有限公司汽車工程研究院研究了金屬材料鎂合金在轉(zhuǎn)向盤骨架、儀表板橫梁、變速器殼體、座椅骨架等零部件上的應(yīng)用。同時,上海通用柳州公司和東風公司正計劃推出全復(fù)合材料家庭用小轎車。但以上國內(nèi)材料輕量化技術(shù)主要側(cè)重于理論及技術(shù)可行性的研究,并未充分考慮生產(chǎn)實際中的一些技術(shù)條件及生產(chǎn)成本等限制要求,基本未能投入實際生產(chǎn)。
20世紀90年代,美國鋼鐵協(xié)會AISI成功研制出高強度鋼車身,使車身整備質(zhì)量比普通鋼結(jié)構(gòu)車身減輕了25%,由此開創(chuàng)了使用高強度鋼等新型材料用于汽車輕量化設(shè)計的理念。2006年馬自達汽車公司的新MAZDA Demio大量采用了高強度鋼板,并提高了強度的級別,使新車型車身比原型車輕了22kg。
近年來,奧迪不斷生產(chǎn)全鋁車身,使其TT車型比前代車型重量降低多達90kg,新款A(yù)6減重多達80kg,奧迪R8 GT高性能跑車重量1525kg;2011年7月,德國寶馬汽車在法蘭克福發(fā)布了兩款碳纖維電動汽車,寶馬i系列電動車采用輕型的鋁材質(zhì)底盤及加強型的碳纖維車身結(jié)構(gòu),比傳統(tǒng)電動汽車減輕了250~350kg。
德國概念汽車研究中心對汽車結(jié)構(gòu)的發(fā)展方向進行了預(yù)測,表明多材料結(jié)構(gòu)車身將逐步代替單一的鋼結(jié)構(gòu)車身,目的是根據(jù)不同需求在適當?shù)奈恢眠x用合理的材料,并表示這是實現(xiàn)汽車輕量化的一個非常重要的途徑。國外的汽車廠商及研究機構(gòu)已將新材料廣泛用于生產(chǎn)實踐,并已取得了明顯的輕量化效果。
目前,國內(nèi)汽車所使用的材料大部分為普通鋼材(低碳鋼與中碳鋼),采用新材料可以實現(xiàn)較大的輕量化效果。但是,替換新材料往往都面臨成本高、加工性能差和表面處理難等問題,而且對整車的強度、剛度、疲勞強度、被動安全性能及NVH性能等影響都較大,故新材料的使用需綜合考慮生產(chǎn)成本、加工性能及安全性能等各方面的因素。
2采用新工藝
傳統(tǒng)的加工工藝已不能滿足新材料的使用要求,采用新工藝一方面可以直接帶來輕量化效果,另一方面使部分新材料的引入成為可能,進而推動了輕量化新工藝的發(fā)展。輕量化新工藝主要包括成形新工藝和連接新工藝兩大塊。
前者從傳統(tǒng)的鋼板冷沖壓成形、鑄造等發(fā)展到熱沖壓成形(HPF)、液壓成形(HF)、拼焊板成形(TWBF)、連續(xù)變截面輥軋(TRB)、鋁合金真空輔助壓鑄(VAPC)、鎂合金壓鑄(MDC)、鋁合金擠壓成型(AE)、增量成形(ISF)、彎管成形等。
后者從傳統(tǒng)的焊接方式(電阻點焊、MIG/MAG、激光焊)發(fā)展到激光-MIG復(fù)合焊、雙焦點激光復(fù)合焊(BHLW)、超聲波焊接(USW)、自鉚焊(SPR)、攪拌摩擦焊(FSW)、汽車結(jié)構(gòu)膠粘接(ASAT)、電磁焊接(MDW)等。
(1) 成形新工藝
國內(nèi)方面,阿賽洛、蒂森克虜伯、本特勒等公司建立了超高強度鋼熱沖壓生產(chǎn)線、寶鋼、鞍鋼等鋼鐵生產(chǎn)企業(yè)建立了拼焊板成形生產(chǎn)線基地,為國內(nèi)各大汽車生產(chǎn)廠家配貨。
其它成形新工藝在國內(nèi)汽車生產(chǎn)中的應(yīng)用未見相關(guān)報導(dǎo),而主要是對其進行理論研究,如機械科學研究總院、中國一汽、上海交通大學等在鋁合金材料的超塑成型、擠壓成形、半固態(tài)擠壓鑄造、鋁合金表面處理工藝及連接技術(shù)等方面做了大量研究并取得眾多專利成果,為開發(fā)鋁合金車身提供了重要的技術(shù)支撐及理論依據(jù)。
國外方面,美國通用、福特、克萊斯勒三大汽車公司的門內(nèi)板、側(cè)圍、門框等零件均采用了拼焊板成形技術(shù);沃爾沃(VOLVO)、保時捷、戴姆勒-克萊斯勒、大眾等公司在車身安全件上大多采用了超高強度鋼的熱沖壓成形技術(shù)。
德國大眾公司開發(fā)出了鎂合金汽車覆蓋件的熱沖壓技術(shù),成功地生產(chǎn)出鎂合金汽車門內(nèi)板。美國通用開發(fā)了真空輔助壓鑄和高真空壓鑄技術(shù),用于生產(chǎn)高整體性的車體和底盤零件,采用低壓金屬型鑄造工藝生產(chǎn)了結(jié)構(gòu)用薄壁空心鑄件等。
(2) 連接新工藝
國內(nèi)方面,車身連接工藝還主要為電弧焊、電阻點焊、激光焊、MIG/MAG等傳統(tǒng)焊接方式。而國外方面,傳統(tǒng)的焊接方式正逐漸被取代,如2002年奧迪A8 D3的鉚接點為2400個,而電阻焊鋁焊點全部取消;大眾輝騰的車門焊縫中激光-MIG復(fù)合焊焊縫長度占總長(4980mm)的72%,而MIG焊縫與激光焊焊縫長度之和僅占總長的28%。美國通用汽車在其大部分車型上正廣泛應(yīng)用結(jié)構(gòu)膠技術(shù)作為其實現(xiàn)輕量化的重要手段之一,在保持車身質(zhì)量不變的情況下將車身剛度提高25%左右。
綜上所述,國內(nèi)輕量化新工藝在汽車制造中所占的比重、相關(guān)研究的投入及實踐探索方面均遠遠落后于國外汽車廠商。在國內(nèi)汽車生產(chǎn)制造中,很少涉及輕量化新工藝,車身零部件的制造也基本是靠冷成形加工獲得。國內(nèi)汽車廠家若想生產(chǎn)高質(zhì)量汽車,必須加大力度進行研究,爭取在工藝技術(shù)上有所突破或創(chuàng)新。
3輕量化結(jié)構(gòu)設(shè)計
汽車輕量化結(jié)構(gòu)設(shè)計主要是在滿足設(shè)計性能要求的前提下,盡可能使汽車零部件的材料在空間合理分布,避免不必要的材料利用,以獲得最輕的結(jié)構(gòu)設(shè)計。
國內(nèi)相關(guān)研究方面,中北大學針對某越野車懸架的擺臂結(jié)構(gòu),應(yīng)用輕型的鋁合金材料替代原來的鋼板材料并對其結(jié)構(gòu)進行拓撲優(yōu)化,使該越野車的懸架擺臂減重12.1%。
華南理工大學和浙江吉利汽車研究院有限公司共同研究了在滿足車身模態(tài)、剛度和碰撞安全等多項性能要求前提下的輕量化車身結(jié)構(gòu)多目標優(yōu)化方法,優(yōu)化結(jié)果提高了整車的碰撞安全性,使白車身扭轉(zhuǎn)剛度得到了很好的控制,同時實現(xiàn)了白車身零件的輕量化效果。
大連理工大學提出了一種在概念設(shè)計階段,確定截面幾何特性的算法和基于尺寸向量控制截面形狀的方法以優(yōu)化薄壁桿件的截面形狀,并采用基于粒子群的優(yōu)化算法對桿件截面厚度和形狀進行優(yōu)化,以達到車身的輕量化目的。
吉林大學通過對不同類型薄壁梁的幾何及力學特性的基礎(chǔ)理論分析,考慮車身結(jié)構(gòu)幾何特性、力學特性及工藝因素,對轎車碰撞參數(shù)化結(jié)構(gòu)的建模方式進行研究,分別建立轎車車身部件的有限元模型及其相應(yīng)的參數(shù)化簡化模型,為轎車參數(shù)化結(jié)構(gòu)建模及優(yōu)化奠定基礎(chǔ)。
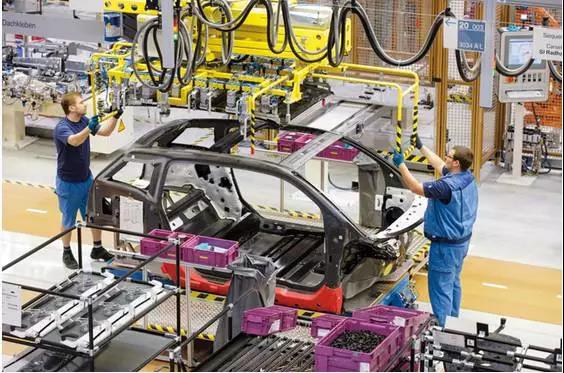
國外方面,英國考文垂大學在滿足汽車碰撞安全性的前提下進行某電動汽車的白車身結(jié)構(gòu)拓撲優(yōu)化,獲得了較優(yōu)的白車身拓撲結(jié)構(gòu),既滿足碰撞安全性能的要求,又實現(xiàn)了白車身的輕量化效果。
美國哥倫比亞大學利用等效靜載荷方法開創(chuàng)了一種新的結(jié)構(gòu)設(shè)計拓撲優(yōu)化方法。
澳大利亞皇家墨爾本理工大學基于有限元平臺提出了一種新的汽車結(jié)構(gòu)快速設(shè)計方法,這種方法在不失精度的情況下可以大大提高分析的效率和計算迭代的步數(shù),并通過某汽車座椅致動器總成的結(jié)構(gòu)優(yōu)化設(shè)計進行了驗證。
韓國漢陽大學和美國喬治華盛頓大學利用等效靜載荷方法來求解非線性動態(tài)響應(yīng)優(yōu)化問題,對車頂進行尺寸優(yōu)化,在滿足車輛側(cè)翻安全的同時使車頂達到了輕量化的效果。
在輕量化結(jié)構(gòu)設(shè)計方面,國內(nèi)外均有大量研究。但國內(nèi)在該部分所做的研究范圍(僅關(guān)心質(zhì)量大的零部件)及深度與國外相關(guān)廠商或研究機構(gòu)還有較大差距。隨著各種新車型的不斷推出,結(jié)構(gòu)優(yōu)化設(shè)計是汽車廠商一直面臨的一個問題,該部分的理論及應(yīng)用價值值得深入研究,以充分挖掘汽車零部件的輕量化潛力,達到輕量化的目的。
綜上所述,汽車輕量化是一個涉及技術(shù)領(lǐng)域廣,影響因素多的系統(tǒng)工程,同時也是目前國內(nèi)外汽車廠商研究的一個重要課題。綜合考慮輕量化研發(fā)及技術(shù)水平現(xiàn)狀等問題,國內(nèi)各汽車廠商急需建立和完善適合自身發(fā)展的輕量化技術(shù)平臺,這對樹立國產(chǎn)汽車產(chǎn)品高端品牌形象,提升其市場競爭力,推動我國汽車制造技術(shù)水平的發(fā)展等都具有重要作用。
本文汽車輕量化是在保證汽車強度和安全性能的前提下,盡可能地降低汽車的質(zhì)量,從而提高汽車的動力利用率,減少燃料消耗,降低排氣污染。汽車輕量化還能提高汽車的駕乘動力學性能(如加速、制動、過彎穩(wěn)定性、碰撞慣性等),而這類性能的改善一直是車輛設(shè)計者、制造商和用戶追求的目標。
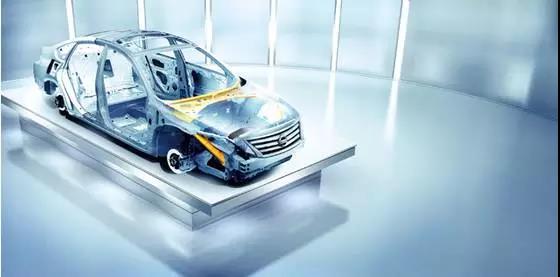
汽車輕量化是目前國內(nèi)外汽車廠商普遍研究的一個熱點,也是未來汽車發(fā)展的必然方向。研究表明,約75%的油耗與整車質(zhì)量有關(guān),降低汽車質(zhì)量就可有效降低油耗以及排放。
大量研究表明,汽車質(zhì)量每下降10%,油耗下降8%,排放下降4%。對商用車的研究表明,汽車質(zhì)量每減1000kg,油耗可降低6%~7%。油耗的下降,意味著CO2、氮氧化物(NOx)等有害氣體排放量的下降。因此,車身變輕對于整車的燃油經(jīng)濟性、車輛控制穩(wěn)定性、碰撞安全性都大有裨益。當前,由于環(huán)保和節(jié)能的需要,汽車輕量化已經(jīng)成為世界汽車發(fā)展的潮流。
構(gòu)成汽車的2萬多個零件中,約有86%是金屬材料,且鋼鐵占了約80%,這表明通過材料的輕量化來減輕汽車自重有巨大潛力。目前,鋁合金、鎂合金、高強度鋼、工程塑料和復(fù)合材料等輕質(zhì)材料的開發(fā)和應(yīng)用在汽車輕量化中發(fā)揮了重大作用。為了提升市場競爭力,國內(nèi)外汽車廠商均在進行汽車輕量化技術(shù)的研究,并力求應(yīng)用到汽車制造中,以保持自己在市場競爭中的有利地位。
但是,汽車輕量化并非只是簡單地降低汽車重量,它必須在保證汽車安全性、整車NVH性能、可制造性以及經(jīng)濟性等各種前提下實現(xiàn)輕量化。同時,汽車輕量化涉及汽車上的每個部件,各個部件之間又相互影響、相互制約,每個部件在材料選擇、制造工藝、結(jié)構(gòu)設(shè)計等方面也都有不同的設(shè)計要求。因此,汽車輕量化是一個多領(lǐng)域技術(shù)綜合作用的系統(tǒng)工程。
汽車輕量化方法
目前,國內(nèi)外實現(xiàn)汽車輕量化的主要技術(shù)手段包括使用新材料、采用新工藝和輕量化結(jié)構(gòu)設(shè)計等三大方面。
1使用新材料
隨著材料科學的發(fā)展,新型高強度、低密度輕質(zhì)材料(如高強度鋼、鋁合金、鎂合金、高分子材料和復(fù)合材料等)在汽車制造中正逐步替代傳統(tǒng)鋼鐵。目前正廣泛研究并逐步應(yīng)用于汽車制造的有:超高強度鋼、鋁合金、鎂合金以及復(fù)合材料等。
國內(nèi)輕量化新材料研究方面,同濟大學將7075鋁合金應(yīng)用于汽車保險杠系統(tǒng)中,通過有限元軟件LS-DYNA對不同厚度保險杠模型的低速碰撞進行仿真分析。在碰撞性能相同的條件下,相比原鋼質(zhì)材料,采用鋁合金可使保險杠質(zhì)量下降20.5%。
上海交通大學通過建立某款轎車發(fā)動機罩板的有限元模型,選擇鋁合金材料替換原有鋼材料,以罩板綜合性能為約束,結(jié)合優(yōu)化設(shè)計方法,考慮板材的成形性因素?;谠间摻Y(jié)構(gòu)空間布局進行全新設(shè)計,在滿足結(jié)構(gòu)性能要求和可制造性的前提下使罩板的質(zhì)量減輕47.1%。
目前發(fā)達國家汽車的單車塑料平均使用量超過150kg,占汽車總重量的12%~20%,而我國單車塑料使用量約占汽車自重的7%~10%。工程塑料在汽車工業(yè)上的應(yīng)用雖然越來越廣泛,但是由于我國汽車零部件標準體系不健全、國內(nèi)企業(yè)科研投入不足、自主創(chuàng)新能力不足等因素的影響,很大程度上制約了我國工程塑料的發(fā)展。
奇瑞汽車股份有限公司汽車工程研究院研究了金屬材料鎂合金在轉(zhuǎn)向盤骨架、儀表板橫梁、變速器殼體、座椅骨架等零部件上的應(yīng)用。同時,上海通用柳州公司和東風公司正計劃推出全復(fù)合材料家庭用小轎車。但以上國內(nèi)材料輕量化技術(shù)主要側(cè)重于理論及技術(shù)可行性的研究,并未充分考慮生產(chǎn)實際中的一些技術(shù)條件及生產(chǎn)成本等限制要求,基本未能投入實際生產(chǎn)。
20世紀90年代,美國鋼鐵協(xié)會AISI成功研制出高強度鋼車身,使車身整備質(zhì)量比普通鋼結(jié)構(gòu)車身減輕了25%,由此開創(chuàng)了使用高強度鋼等新型材料用于汽車輕量化設(shè)計的理念。2006年馬自達汽車公司的新MAZDA Demio大量采用了高強度鋼板,并提高了強度的級別,使新車型車身比原型車輕了22kg。
近年來,奧迪不斷生產(chǎn)全鋁車身,使其TT車型比前代車型重量降低多達90kg,新款A(yù)6減重多達80kg,奧迪R8 GT高性能跑車重量1525kg;2011年7月,德國寶馬汽車在法蘭克福發(fā)布了兩款碳纖維電動汽車,寶馬i系列電動車采用輕型的鋁材質(zhì)底盤及加強型的碳纖維車身結(jié)構(gòu),比傳統(tǒng)電動汽車減輕了250~350kg。
德國概念汽車研究中心對汽車結(jié)構(gòu)的發(fā)展方向進行了預(yù)測,表明多材料結(jié)構(gòu)車身將逐步代替單一的鋼結(jié)構(gòu)車身,目的是根據(jù)不同需求在適當?shù)奈恢眠x用合理的材料,并表示這是實現(xiàn)汽車輕量化的一個非常重要的途徑。國外的汽車廠商及研究機構(gòu)已將新材料廣泛用于生產(chǎn)實踐,并已取得了明顯的輕量化效果。
目前,國內(nèi)汽車所使用的材料大部分為普通鋼材(低碳鋼與中碳鋼),采用新材料可以實現(xiàn)較大的輕量化效果。但是,替換新材料往往都面臨成本高、加工性能差和表面處理難等問題,而且對整車的強度、剛度、疲勞強度、被動安全性能及NVH性能等影響都較大,故新材料的使用需綜合考慮生產(chǎn)成本、加工性能及安全性能等各方面的因素。
2采用新工藝
傳統(tǒng)的加工工藝已不能滿足新材料的使用要求,采用新工藝一方面可以直接帶來輕量化效果,另一方面使部分新材料的引入成為可能,進而推動了輕量化新工藝的發(fā)展。輕量化新工藝主要包括成形新工藝和連接新工藝兩大塊。
前者從傳統(tǒng)的鋼板冷沖壓成形、鑄造等發(fā)展到熱沖壓成形(HPF)、液壓成形(HF)、拼焊板成形(TWBF)、連續(xù)變截面輥軋(TRB)、鋁合金真空輔助壓鑄(VAPC)、鎂合金壓鑄(MDC)、鋁合金擠壓成型(AE)、增量成形(ISF)、彎管成形等。
后者從傳統(tǒng)的焊接方式(電阻點焊、MIG/MAG、激光焊)發(fā)展到激光-MIG復(fù)合焊、雙焦點激光復(fù)合焊(BHLW)、超聲波焊接(USW)、自鉚焊(SPR)、攪拌摩擦焊(FSW)、汽車結(jié)構(gòu)膠粘接(ASAT)、電磁焊接(MDW)等。
(1) 成形新工藝
國內(nèi)方面,阿賽洛、蒂森克虜伯、本特勒等公司建立了超高強度鋼熱沖壓生產(chǎn)線、寶鋼、鞍鋼等鋼鐵生產(chǎn)企業(yè)建立了拼焊板成形生產(chǎn)線基地,為國內(nèi)各大汽車生產(chǎn)廠家配貨。
其它成形新工藝在國內(nèi)汽車生產(chǎn)中的應(yīng)用未見相關(guān)報導(dǎo),而主要是對其進行理論研究,如機械科學研究總院、中國一汽、上海交通大學等在鋁合金材料的超塑成型、擠壓成形、半固態(tài)擠壓鑄造、鋁合金表面處理工藝及連接技術(shù)等方面做了大量研究并取得眾多專利成果,為開發(fā)鋁合金車身提供了重要的技術(shù)支撐及理論依據(jù)。
國外方面,美國通用、福特、克萊斯勒三大汽車公司的門內(nèi)板、側(cè)圍、門框等零件均采用了拼焊板成形技術(shù);沃爾沃(VOLVO)、保時捷、戴姆勒-克萊斯勒、大眾等公司在車身安全件上大多采用了超高強度鋼的熱沖壓成形技術(shù)。
德國大眾公司開發(fā)出了鎂合金汽車覆蓋件的熱沖壓技術(shù),成功地生產(chǎn)出鎂合金汽車門內(nèi)板。美國通用開發(fā)了真空輔助壓鑄和高真空壓鑄技術(shù),用于生產(chǎn)高整體性的車體和底盤零件,采用低壓金屬型鑄造工藝生產(chǎn)了結(jié)構(gòu)用薄壁空心鑄件等。
(2) 連接新工藝
國內(nèi)方面,車身連接工藝還主要為電弧焊、電阻點焊、激光焊、MIG/MAG等傳統(tǒng)焊接方式。而國外方面,傳統(tǒng)的焊接方式正逐漸被取代,如2002年奧迪A8 D3的鉚接點為2400個,而電阻焊鋁焊點全部取消;大眾輝騰的車門焊縫中激光-MIG復(fù)合焊焊縫長度占總長(4980mm)的72%,而MIG焊縫與激光焊焊縫長度之和僅占總長的28%。美國通用汽車在其大部分車型上正廣泛應(yīng)用結(jié)構(gòu)膠技術(shù)作為其實現(xiàn)輕量化的重要手段之一,在保持車身質(zhì)量不變的情況下將車身剛度提高25%左右。
綜上所述,國內(nèi)輕量化新工藝在汽車制造中所占的比重、相關(guān)研究的投入及實踐探索方面均遠遠落后于國外汽車廠商。在國內(nèi)汽車生產(chǎn)制造中,很少涉及輕量化新工藝,車身零部件的制造也基本是靠冷成形加工獲得。國內(nèi)汽車廠家若想生產(chǎn)高質(zhì)量汽車,必須加大力度進行研究,爭取在工藝技術(shù)上有所突破或創(chuàng)新。
3輕量化結(jié)構(gòu)設(shè)計
汽車輕量化結(jié)構(gòu)設(shè)計主要是在滿足設(shè)計性能要求的前提下,盡可能使汽車零部件的材料在空間合理分布,避免不必要的材料利用,以獲得最輕的結(jié)構(gòu)設(shè)計。
國內(nèi)相關(guān)研究方面,中北大學針對某越野車懸架的擺臂結(jié)構(gòu),應(yīng)用輕型的鋁合金材料替代原來的鋼板材料并對其結(jié)構(gòu)進行拓撲優(yōu)化,使該越野車的懸架擺臂減重12.1%。
華南理工大學和浙江吉利汽車研究院有限公司共同研究了在滿足車身模態(tài)、剛度和碰撞安全等多項性能要求前提下的輕量化車身結(jié)構(gòu)多目標優(yōu)化方法,優(yōu)化結(jié)果提高了整車的碰撞安全性,使白車身扭轉(zhuǎn)剛度得到了很好的控制,同時實現(xiàn)了白車身零件的輕量化效果。
大連理工大學提出了一種在概念設(shè)計階段,確定截面幾何特性的算法和基于尺寸向量控制截面形狀的方法以優(yōu)化薄壁桿件的截面形狀,并采用基于粒子群的優(yōu)化算法對桿件截面厚度和形狀進行優(yōu)化,以達到車身的輕量化目的。
吉林大學通過對不同類型薄壁梁的幾何及力學特性的基礎(chǔ)理論分析,考慮車身結(jié)構(gòu)幾何特性、力學特性及工藝因素,對轎車碰撞參數(shù)化結(jié)構(gòu)的建模方式進行研究,分別建立轎車車身部件的有限元模型及其相應(yīng)的參數(shù)化簡化模型,為轎車參數(shù)化結(jié)構(gòu)建模及優(yōu)化奠定基礎(chǔ)。
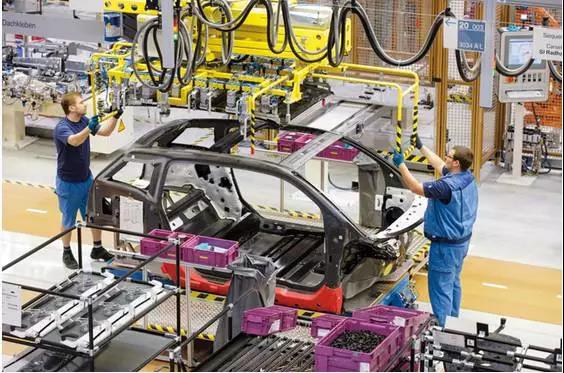
國外方面,英國考文垂大學在滿足汽車碰撞安全性的前提下進行某電動汽車的白車身結(jié)構(gòu)拓撲優(yōu)化,獲得了較優(yōu)的白車身拓撲結(jié)構(gòu),既滿足碰撞安全性能的要求,又實現(xiàn)了白車身的輕量化效果。
美國哥倫比亞大學利用等效靜載荷方法開創(chuàng)了一種新的結(jié)構(gòu)設(shè)計拓撲優(yōu)化方法。
澳大利亞皇家墨爾本理工大學基于有限元平臺提出了一種新的汽車結(jié)構(gòu)快速設(shè)計方法,這種方法在不失精度的情況下可以大大提高分析的效率和計算迭代的步數(shù),并通過某汽車座椅致動器總成的結(jié)構(gòu)優(yōu)化設(shè)計進行了驗證。
韓國漢陽大學和美國喬治華盛頓大學利用等效靜載荷方法來求解非線性動態(tài)響應(yīng)優(yōu)化問題,對車頂進行尺寸優(yōu)化,在滿足車輛側(cè)翻安全的同時使車頂達到了輕量化的效果。
在輕量化結(jié)構(gòu)設(shè)計方面,國內(nèi)外均有大量研究。但國內(nèi)在該部分所做的研究范圍(僅關(guān)心質(zhì)量大的零部件)及深度與國外相關(guān)廠商或研究機構(gòu)還有較大差距。隨著各種新車型的不斷推出,結(jié)構(gòu)優(yōu)化設(shè)計是汽車廠商一直面臨的一個問題,該部分的理論及應(yīng)用價值值得深入研究,以充分挖掘汽車零部件的輕量化潛力,達到輕量化的目的。
綜上所述,汽車輕量化是一個涉及技術(shù)領(lǐng)域廣,影響因素多的系統(tǒng)工程,同時也是目前國內(nèi)外汽車廠商研究的一個重要課題。綜合考慮輕量化研發(fā)及技術(shù)水平現(xiàn)狀等問題,國內(nèi)各汽車廠商急需建立和完善適合自身發(fā)展的輕量化技術(shù)平臺,這對樹立國產(chǎn)汽車產(chǎn)品高端品牌形象,提升其市場競爭力,推動我國汽車制造技術(shù)水平的發(fā)展等都具有重要作用。
- 下一篇:?零件去毛刺工藝概覽
- 上一篇:艾默生并購安沃馳,家族再添新成員
編輯推薦
最新資訊
-
跨越速運憑什么“圈粉”萬千客戶?“
2025-07-01 14:42
-
數(shù)智破局啟新篇?生態(tài)共生再啟程 —
2025-06-27 20:13
-
助力汽車零部件產(chǎn)線智能化升級,西門
2025-06-27 13:59
-
BBA集體轉(zhuǎn)向!放棄全面電動化
2025-06-26 17:32
-
比換柜省錢,比自研省心,西門子Xcel
2025-06-25 15:07