機(jī)器人在線檢測如何應(yīng)用于車身制造?
2018-06-22 15:52:33· 來源:汽車實(shí)用技術(shù)雜志社
伴隨日趨激烈的國內(nèi)汽車市場,各汽車主機(jī)廠的核心競爭力大體可總結(jié)為造型、性能及質(zhì)量三大方面。尤其是汽車質(zhì)量這一方面,最能夠體現(xiàn)一款汽車的口碑,也會間接的影響市場認(rèn)可及銷售能力。
作者:李金山,李彥賀單位:奇瑞商用車(安徽)有限公司
原標(biāo)題:淺談機(jī)器人在線檢測技術(shù)在車身制造中的應(yīng)用
1 機(jī)器人在線檢測技術(shù)在車身制造過程中應(yīng)用的必要性
伴隨日趨激烈的國內(nèi)汽車市場,各汽車主機(jī)廠的核心競爭力大體可總結(jié)為造型、性能及質(zhì)量三大方面。尤其是汽車質(zhì)量這一方面,最能夠體現(xiàn)一款汽車的口碑,也會間接的影響市場認(rèn)可及銷售能力。
汽車制造作為一個系統(tǒng)化的制造工程,而作為汽車整車制造過程中最重要的工序之一的車身制造,作業(yè)內(nèi)容復(fù)雜且質(zhì)量指標(biāo)要求高。車身制造過程的重要質(zhì)量指標(biāo)一般分為車身尺寸質(zhì)量、焊接質(zhì)量、外觀質(zhì)量、匹配質(zhì)量等,其中車身尺寸質(zhì)量是最影響整車裝配性的質(zhì)量指標(biāo)之一。目前國內(nèi)對于車身制造過程中的車身尺寸的檢測方式大多采用線下檢測,即采用雙懸臂測量儀在專業(yè)的三坐標(biāo)測量室(恒溫恒濕)內(nèi)對車身進(jìn)行檢測(如圖1所示),通常一條車身生產(chǎn)線單班次每日測量樣本不會超過2臺份,且測量周期長,一般為2-3小時/臺車,檢測報告制作周期約為0.5小時。一般取得當(dāng)日車身生產(chǎn)過程中尺寸報告需要自線上下車后的2.5~3.5小時左右,而此時生產(chǎn)線仍然繼續(xù)生產(chǎn),如果車身尺寸狀態(tài)存在較大偏差,問題車身已生產(chǎn)62.5~87.5臺車(以25JPH為例)。無法做到及時反饋車身誤差信息,若產(chǎn)生不可修復(fù)性的車身尺寸偏差,所產(chǎn)生的損失不可預(yù)估。
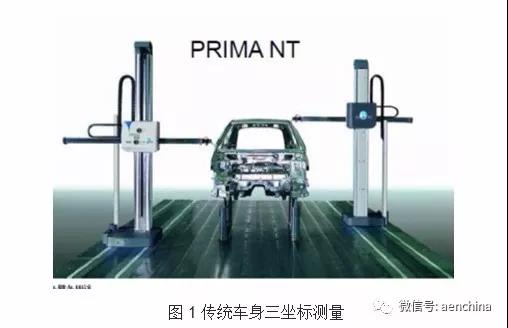
為解決此類問題,國內(nèi)部分主機(jī)廠已意識到車身制造過程中在線檢測技術(shù)的重要性,并且部分主機(jī)廠已投入應(yīng)用固定式在線檢測技術(shù),如紅外線在線檢測技術(shù)。但由于固定式的局限性,效果不夠理想,檢測位置較為單一且只能檢測單一車型,無法滿足車身實(shí)際生產(chǎn)過程中的質(zhì)量需要。為此一種柔性化的車身尺寸在線檢測技術(shù)在車身制造過程中的應(yīng)用勢在必行。
2機(jī)器人在線檢測技術(shù)在車身制造過程中應(yīng)用的目的
目前國內(nèi)汽車白車身生產(chǎn)線發(fā)展日新月異,為響應(yīng)國家提出的“中國制造2025”這一主題,柔性化、自動化、智能化及高節(jié)拍是未來汽車白車身生產(chǎn)線開發(fā)的趨勢,如何滿足這一趨勢是目前車身制造過程在線檢測刻不容緩的一大課題。
2.1 滿足車身制造過程中柔性化在線檢測需求
固定式、單一車型的在線檢測技術(shù)已不能滿足目前白車身生產(chǎn)線柔性化需求,為此在線檢測技術(shù)也應(yīng)具備柔性化功能。目前世界上車身尺寸檢測設(shè)備相對比較完善(主要有紅外線、藍(lán)光、白光等檢測系統(tǒng)),而柔性化的檢測技術(shù)需完善的車身尺寸檢測設(shè)備及可滿足一定移動軌跡的載體即可實(shí)現(xiàn),其中載體應(yīng)同時具備位置度及重復(fù)定位精度要求。具體項目可依據(jù)不同需求可選擇不同的工裝活設(shè)備作為載體,而目前以機(jī)器人作為載體是符合車身柔性化制造需求的最佳對象(如圖2ab所示)。
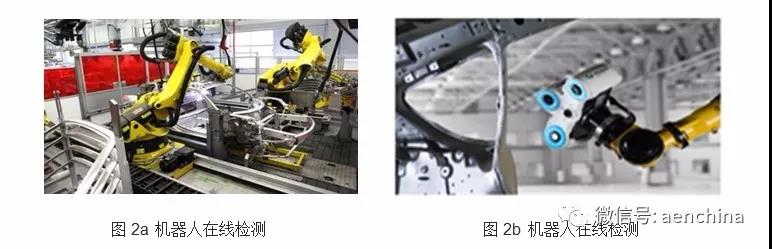
2.2滿足車身制造過程中尺寸檢測及時性需求
傳統(tǒng)的車身檢測方式由于檢測周期長且只能對車身進(jìn)行抽檢。而機(jī)器人在線檢測技術(shù)可以實(shí)現(xiàn)非接觸、快速等檢測優(yōu)點(diǎn),不僅能夠快速反饋車身尺寸信息,而且也可體現(xiàn)出車身尺寸趨勢及重要車身尺寸偏差在線預(yù)警功能,能夠及時為工藝分析改進(jìn)提供依據(jù),符合未來車身制造自動化、智能化及高節(jié)拍的質(zhì)量需求。
3機(jī)器人在線檢測技術(shù)工作原理
3.1在線檢測系統(tǒng)-機(jī)器人構(gòu)成
在線監(jiān)測系統(tǒng)主要構(gòu)成部分如下:
①重復(fù)位置精度較高的機(jī)器人,如KUKA、ABB等一流品牌機(jī)器人;
②專業(yè)的視覺傳感器;
③包含服務(wù)器模塊、數(shù)據(jù)處理計算機(jī)、圖像處理系統(tǒng)及用戶界面程序等的測量專用數(shù)據(jù)控制柜;
④相應(yīng)的RFID系統(tǒng)、光柵及Z向傳感器等PLC控制系統(tǒng)構(gòu)成。
其中作為輸入端的是視覺拍攝系統(tǒng)并對待測對象進(jìn)行數(shù)據(jù)收集。通常組成部分是半導(dǎo)體激光束作為信息的輸入端,可實(shí)現(xiàn)與待測對象不進(jìn)行接觸(傳統(tǒng)檢測系統(tǒng)采用接觸式)、對待測對象的特征進(jìn)行信息收集。該輸入端的技術(shù)參數(shù)要求:工作距離200mm左右、精度±0.05mm、分辨率0.01mm、分辨率0.01mm及相關(guān)的穩(wěn)定輔助支架等。
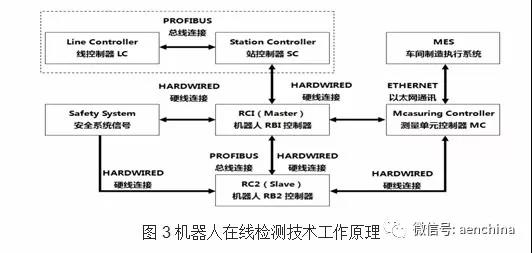
3.1.1 系統(tǒng)布置
以通常的白車身自動化生產(chǎn)線為例,在線檢測工位可布置2-4臺在線檢測機(jī)器人(具體依據(jù)實(shí)際需求為準(zhǔn)),通過3D數(shù)據(jù)模擬仿真,并結(jié)合線體的實(shí)際布置及既定生產(chǎn)節(jié)拍,最大限度滿足需求的前提下,最終明確在線檢測機(jī)器人的布置位置及數(shù)量。
3.1.2 檢測點(diǎn)仿真及方案
(1)檢測點(diǎn)數(shù)量的設(shè)定
以30JPH的白車身自動化焊裝線為例,滑橇的轉(zhuǎn)運(yùn)(包含升降)時間約為18s,單個檢測點(diǎn)的花費(fèi)時間約2-2.5s。綜上,配置4臺在線檢測機(jī)器人可實(shí)現(xiàn)檢測點(diǎn)的最大數(shù)量為:【(120-18)/2】*4=204個。
(2)檢測點(diǎn)的預(yù)選、仿真及最終確定
白車身焊裝線通常共由五個關(guān)鍵區(qū)域組成:側(cè)圍區(qū)域、發(fā)艙區(qū)域、前地板區(qū)域、后地板區(qū)域及車身骨架區(qū)域。若僅設(shè)置一個工位的在線檢測系統(tǒng),盡可能多的設(shè)置檢測點(diǎn),則對于白車身檢測效果越明顯,在仿真模擬前,參考傳統(tǒng)三坐標(biāo)檢測點(diǎn)并依據(jù)檢測點(diǎn)的重要程度進(jìn)行預(yù)設(shè)定檢測點(diǎn),依據(jù)預(yù)設(shè)定檢測點(diǎn)位置進(jìn)行數(shù)字化模擬仿真,并依據(jù)現(xiàn)場實(shí)際驗(yàn)證結(jié)果作為導(dǎo)向從而最終確認(rèn)檢測點(diǎn)位置及數(shù)量。
3.1.3 在線檢測效果
(1)焊裝自動線通過滑撬將待測白車身骨架轉(zhuǎn)運(yùn)至機(jī)器人在線檢測工位,待車身定位完成后,控制器給在線檢測工位控制器發(fā)射“到位”信號、控制器給在線檢測系統(tǒng)控制柜發(fā)射“車型”信號、控制柜向檢測機(jī)器人發(fā)動“啟動”信號、機(jī)器人接到信號后運(yùn)行、機(jī)器人將每個檢測點(diǎn)的檢測值向檢測控制器發(fā)射“測量請求”和“測點(diǎn)ID”信號、待檢測控制器發(fā)回的“測量完成”信號、在線檢測系統(tǒng)接到信號后啟動測量并對檢測結(jié)果進(jìn)行記錄、再通過檢測分析軟件進(jìn)行處理。單個檢測點(diǎn)結(jié)束后繼續(xù)向機(jī)器人發(fā)射“測量完成”信號、機(jī)器人收到“測量完成”信號后開始向下一檢測點(diǎn)運(yùn)行,直至完成所有既定檢測點(diǎn)的測量。
(2)在線檢測系統(tǒng)可取得的效果:
通過機(jī)器人在線檢測系統(tǒng)的應(yīng)用,既可實(shí)現(xiàn)對生產(chǎn)過程中異常車身尺寸波動的預(yù)警,又可實(shí)現(xiàn)檢測數(shù)據(jù)庫的搭建。
①通過對過程異常車身尺寸示警,規(guī)避了批量問題車身的生產(chǎn)且能夠正向識別問題,降低不合格產(chǎn)品數(shù)量;
②車身檢測數(shù)據(jù)庫的搭建,通過對指定時間段的車身數(shù)據(jù)匯總分析,有利于逆向識別整車裝配所產(chǎn)生的問題位置,便于問題解決,提高問題解決效率。
3.1.4 影響在線檢測系統(tǒng)精度的因素
通過查閱相關(guān)資料并實(shí)地跟蹤驗(yàn)證確認(rèn)后,影響在線檢測系統(tǒng)精度因素如下:
①信號輸入端在檢測過程中應(yīng)確保與檢測點(diǎn)的投影面保持垂直狀態(tài),越接近90°,檢測精度越高,反之,精度越差;
②機(jī)器人在線檢測系統(tǒng)中機(jī)器人本體在同一姿態(tài)不同溫度(極限溫度與通常溫度)環(huán)境下運(yùn)行過程中波動較大,經(jīng)不完全統(tǒng)計,精度波動值在0.2mm左右。非極限溫度下,波動可忽略不計;
③檢測點(diǎn)應(yīng)選取特征明顯的點(diǎn),同一臺車經(jīng)在線檢測后用傳統(tǒng)三坐標(biāo)測量儀檢測后發(fā)現(xiàn),特征越明顯的檢測點(diǎn),在線檢測的測量精度越高;
④機(jī)器人在線檢測系統(tǒng)所選取的重復(fù)性定位精度越高的機(jī)器人,檢測特征點(diǎn)的精度越高。
4 總 結(jié)
通過對機(jī)器人在線檢測系統(tǒng)的應(yīng)用,可取得如下優(yōu)點(diǎn):
4.1 白車身焊裝線所有車身關(guān)鍵檢測點(diǎn)都可實(shí)現(xiàn)100%檢測,并可針對異常車身進(jìn)行預(yù)警,規(guī)避批量問題車身生產(chǎn),降低企業(yè)不合格品所產(chǎn)生成本,同時提高檢測效率。
4.2 白車身在線檢測可實(shí)現(xiàn)車身尺寸數(shù)據(jù)庫搭建,通過對指定時間段的車身數(shù)據(jù)匯總分析,有利于逆向識別整車裝配所產(chǎn)生的問題位置,便于問題解決,提高問題解決效率。
原標(biāo)題:淺談機(jī)器人在線檢測技術(shù)在車身制造中的應(yīng)用
1 機(jī)器人在線檢測技術(shù)在車身制造過程中應(yīng)用的必要性
伴隨日趨激烈的國內(nèi)汽車市場,各汽車主機(jī)廠的核心競爭力大體可總結(jié)為造型、性能及質(zhì)量三大方面。尤其是汽車質(zhì)量這一方面,最能夠體現(xiàn)一款汽車的口碑,也會間接的影響市場認(rèn)可及銷售能力。
汽車制造作為一個系統(tǒng)化的制造工程,而作為汽車整車制造過程中最重要的工序之一的車身制造,作業(yè)內(nèi)容復(fù)雜且質(zhì)量指標(biāo)要求高。車身制造過程的重要質(zhì)量指標(biāo)一般分為車身尺寸質(zhì)量、焊接質(zhì)量、外觀質(zhì)量、匹配質(zhì)量等,其中車身尺寸質(zhì)量是最影響整車裝配性的質(zhì)量指標(biāo)之一。目前國內(nèi)對于車身制造過程中的車身尺寸的檢測方式大多采用線下檢測,即采用雙懸臂測量儀在專業(yè)的三坐標(biāo)測量室(恒溫恒濕)內(nèi)對車身進(jìn)行檢測(如圖1所示),通常一條車身生產(chǎn)線單班次每日測量樣本不會超過2臺份,且測量周期長,一般為2-3小時/臺車,檢測報告制作周期約為0.5小時。一般取得當(dāng)日車身生產(chǎn)過程中尺寸報告需要自線上下車后的2.5~3.5小時左右,而此時生產(chǎn)線仍然繼續(xù)生產(chǎn),如果車身尺寸狀態(tài)存在較大偏差,問題車身已生產(chǎn)62.5~87.5臺車(以25JPH為例)。無法做到及時反饋車身誤差信息,若產(chǎn)生不可修復(fù)性的車身尺寸偏差,所產(chǎn)生的損失不可預(yù)估。
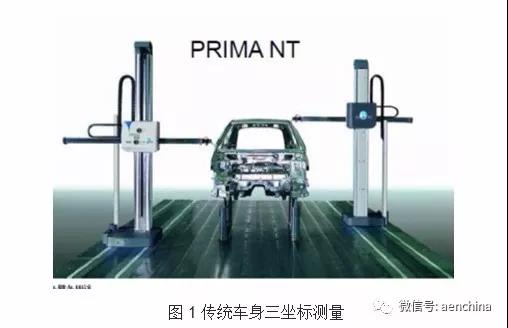
為解決此類問題,國內(nèi)部分主機(jī)廠已意識到車身制造過程中在線檢測技術(shù)的重要性,并且部分主機(jī)廠已投入應(yīng)用固定式在線檢測技術(shù),如紅外線在線檢測技術(shù)。但由于固定式的局限性,效果不夠理想,檢測位置較為單一且只能檢測單一車型,無法滿足車身實(shí)際生產(chǎn)過程中的質(zhì)量需要。為此一種柔性化的車身尺寸在線檢測技術(shù)在車身制造過程中的應(yīng)用勢在必行。
2機(jī)器人在線檢測技術(shù)在車身制造過程中應(yīng)用的目的
目前國內(nèi)汽車白車身生產(chǎn)線發(fā)展日新月異,為響應(yīng)國家提出的“中國制造2025”這一主題,柔性化、自動化、智能化及高節(jié)拍是未來汽車白車身生產(chǎn)線開發(fā)的趨勢,如何滿足這一趨勢是目前車身制造過程在線檢測刻不容緩的一大課題。
2.1 滿足車身制造過程中柔性化在線檢測需求
固定式、單一車型的在線檢測技術(shù)已不能滿足目前白車身生產(chǎn)線柔性化需求,為此在線檢測技術(shù)也應(yīng)具備柔性化功能。目前世界上車身尺寸檢測設(shè)備相對比較完善(主要有紅外線、藍(lán)光、白光等檢測系統(tǒng)),而柔性化的檢測技術(shù)需完善的車身尺寸檢測設(shè)備及可滿足一定移動軌跡的載體即可實(shí)現(xiàn),其中載體應(yīng)同時具備位置度及重復(fù)定位精度要求。具體項目可依據(jù)不同需求可選擇不同的工裝活設(shè)備作為載體,而目前以機(jī)器人作為載體是符合車身柔性化制造需求的最佳對象(如圖2ab所示)。
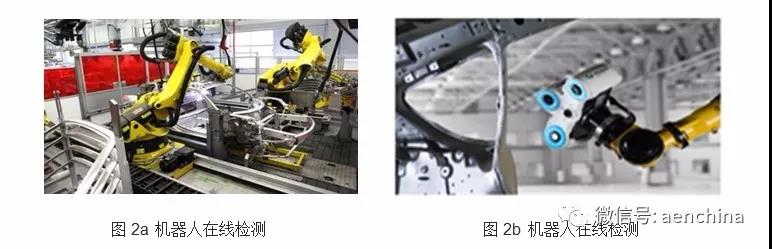
2.2滿足車身制造過程中尺寸檢測及時性需求
傳統(tǒng)的車身檢測方式由于檢測周期長且只能對車身進(jìn)行抽檢。而機(jī)器人在線檢測技術(shù)可以實(shí)現(xiàn)非接觸、快速等檢測優(yōu)點(diǎn),不僅能夠快速反饋車身尺寸信息,而且也可體現(xiàn)出車身尺寸趨勢及重要車身尺寸偏差在線預(yù)警功能,能夠及時為工藝分析改進(jìn)提供依據(jù),符合未來車身制造自動化、智能化及高節(jié)拍的質(zhì)量需求。
3機(jī)器人在線檢測技術(shù)工作原理
3.1在線檢測系統(tǒng)-機(jī)器人構(gòu)成
在線監(jiān)測系統(tǒng)主要構(gòu)成部分如下:
①重復(fù)位置精度較高的機(jī)器人,如KUKA、ABB等一流品牌機(jī)器人;
②專業(yè)的視覺傳感器;
③包含服務(wù)器模塊、數(shù)據(jù)處理計算機(jī)、圖像處理系統(tǒng)及用戶界面程序等的測量專用數(shù)據(jù)控制柜;
④相應(yīng)的RFID系統(tǒng)、光柵及Z向傳感器等PLC控制系統(tǒng)構(gòu)成。
其中作為輸入端的是視覺拍攝系統(tǒng)并對待測對象進(jìn)行數(shù)據(jù)收集。通常組成部分是半導(dǎo)體激光束作為信息的輸入端,可實(shí)現(xiàn)與待測對象不進(jìn)行接觸(傳統(tǒng)檢測系統(tǒng)采用接觸式)、對待測對象的特征進(jìn)行信息收集。該輸入端的技術(shù)參數(shù)要求:工作距離200mm左右、精度±0.05mm、分辨率0.01mm、分辨率0.01mm及相關(guān)的穩(wěn)定輔助支架等。
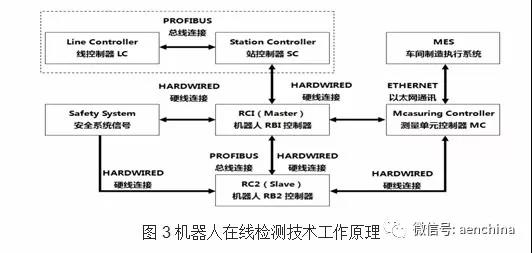
3.1.1 系統(tǒng)布置
以通常的白車身自動化生產(chǎn)線為例,在線檢測工位可布置2-4臺在線檢測機(jī)器人(具體依據(jù)實(shí)際需求為準(zhǔn)),通過3D數(shù)據(jù)模擬仿真,并結(jié)合線體的實(shí)際布置及既定生產(chǎn)節(jié)拍,最大限度滿足需求的前提下,最終明確在線檢測機(jī)器人的布置位置及數(shù)量。
3.1.2 檢測點(diǎn)仿真及方案
(1)檢測點(diǎn)數(shù)量的設(shè)定
以30JPH的白車身自動化焊裝線為例,滑橇的轉(zhuǎn)運(yùn)(包含升降)時間約為18s,單個檢測點(diǎn)的花費(fèi)時間約2-2.5s。綜上,配置4臺在線檢測機(jī)器人可實(shí)現(xiàn)檢測點(diǎn)的最大數(shù)量為:【(120-18)/2】*4=204個。
(2)檢測點(diǎn)的預(yù)選、仿真及最終確定
白車身焊裝線通常共由五個關(guān)鍵區(qū)域組成:側(cè)圍區(qū)域、發(fā)艙區(qū)域、前地板區(qū)域、后地板區(qū)域及車身骨架區(qū)域。若僅設(shè)置一個工位的在線檢測系統(tǒng),盡可能多的設(shè)置檢測點(diǎn),則對于白車身檢測效果越明顯,在仿真模擬前,參考傳統(tǒng)三坐標(biāo)檢測點(diǎn)并依據(jù)檢測點(diǎn)的重要程度進(jìn)行預(yù)設(shè)定檢測點(diǎn),依據(jù)預(yù)設(shè)定檢測點(diǎn)位置進(jìn)行數(shù)字化模擬仿真,并依據(jù)現(xiàn)場實(shí)際驗(yàn)證結(jié)果作為導(dǎo)向從而最終確認(rèn)檢測點(diǎn)位置及數(shù)量。
3.1.3 在線檢測效果
(1)焊裝自動線通過滑撬將待測白車身骨架轉(zhuǎn)運(yùn)至機(jī)器人在線檢測工位,待車身定位完成后,控制器給在線檢測工位控制器發(fā)射“到位”信號、控制器給在線檢測系統(tǒng)控制柜發(fā)射“車型”信號、控制柜向檢測機(jī)器人發(fā)動“啟動”信號、機(jī)器人接到信號后運(yùn)行、機(jī)器人將每個檢測點(diǎn)的檢測值向檢測控制器發(fā)射“測量請求”和“測點(diǎn)ID”信號、待檢測控制器發(fā)回的“測量完成”信號、在線檢測系統(tǒng)接到信號后啟動測量并對檢測結(jié)果進(jìn)行記錄、再通過檢測分析軟件進(jìn)行處理。單個檢測點(diǎn)結(jié)束后繼續(xù)向機(jī)器人發(fā)射“測量完成”信號、機(jī)器人收到“測量完成”信號后開始向下一檢測點(diǎn)運(yùn)行,直至完成所有既定檢測點(diǎn)的測量。
(2)在線檢測系統(tǒng)可取得的效果:
通過機(jī)器人在線檢測系統(tǒng)的應(yīng)用,既可實(shí)現(xiàn)對生產(chǎn)過程中異常車身尺寸波動的預(yù)警,又可實(shí)現(xiàn)檢測數(shù)據(jù)庫的搭建。
①通過對過程異常車身尺寸示警,規(guī)避了批量問題車身的生產(chǎn)且能夠正向識別問題,降低不合格產(chǎn)品數(shù)量;
②車身檢測數(shù)據(jù)庫的搭建,通過對指定時間段的車身數(shù)據(jù)匯總分析,有利于逆向識別整車裝配所產(chǎn)生的問題位置,便于問題解決,提高問題解決效率。
3.1.4 影響在線檢測系統(tǒng)精度的因素
通過查閱相關(guān)資料并實(shí)地跟蹤驗(yàn)證確認(rèn)后,影響在線檢測系統(tǒng)精度因素如下:
①信號輸入端在檢測過程中應(yīng)確保與檢測點(diǎn)的投影面保持垂直狀態(tài),越接近90°,檢測精度越高,反之,精度越差;
②機(jī)器人在線檢測系統(tǒng)中機(jī)器人本體在同一姿態(tài)不同溫度(極限溫度與通常溫度)環(huán)境下運(yùn)行過程中波動較大,經(jīng)不完全統(tǒng)計,精度波動值在0.2mm左右。非極限溫度下,波動可忽略不計;
③檢測點(diǎn)應(yīng)選取特征明顯的點(diǎn),同一臺車經(jīng)在線檢測后用傳統(tǒng)三坐標(biāo)測量儀檢測后發(fā)現(xiàn),特征越明顯的檢測點(diǎn),在線檢測的測量精度越高;
④機(jī)器人在線檢測系統(tǒng)所選取的重復(fù)性定位精度越高的機(jī)器人,檢測特征點(diǎn)的精度越高。
4 總 結(jié)
通過對機(jī)器人在線檢測系統(tǒng)的應(yīng)用,可取得如下優(yōu)點(diǎn):
4.1 白車身焊裝線所有車身關(guān)鍵檢測點(diǎn)都可實(shí)現(xiàn)100%檢測,并可針對異常車身進(jìn)行預(yù)警,規(guī)避批量問題車身生產(chǎn),降低企業(yè)不合格品所產(chǎn)生成本,同時提高檢測效率。
4.2 白車身在線檢測可實(shí)現(xiàn)車身尺寸數(shù)據(jù)庫搭建,通過對指定時間段的車身數(shù)據(jù)匯總分析,有利于逆向識別整車裝配所產(chǎn)生的問題位置,便于問題解決,提高問題解決效率。
編輯推薦
最新資訊
-
跨越速運(yùn)憑什么“圈粉”萬千客戶?“
2025-07-01 14:42
-
數(shù)智破局啟新篇?生態(tài)共生再啟程 —
2025-06-27 20:13
-
助力汽車零部件產(chǎn)線智能化升級,西門
2025-06-27 13:59
-
BBA集體轉(zhuǎn)向!放棄全面電動化
2025-06-26 17:32
-
比換柜省錢,比自研省心,西門子Xcel
2025-06-25 15:07