簡(jiǎn)單分析轎車變速器中間軸的冷擠壓成形技術(shù)
2018-03-13 09:33:27· 來源:鍛造與沖壓
通過本文可知,采用冷擠壓工藝生產(chǎn)汽車中間軸鍛件能夠?qū)崿F(xiàn)可靠的工藝,并且提高材料利用率。同時(shí),采用FORGE模擬軟件來分析產(chǎn)品成形情況相對(duì)更接近實(shí)際,擠壓后鍛件尺寸穩(wěn)定,表面光潔度高。
通過本文可知,采用冷擠壓工藝生產(chǎn)汽車中間軸鍛件能夠?qū)崿F(xiàn)可靠的工藝,并且提高材料利用率。同時(shí),采用FORGE模擬軟件來分析產(chǎn)品成形情況相對(duì)更接近實(shí)際,擠壓后鍛件尺寸穩(wěn)定,表面光潔度高。
中間軸是用在轎車變速器DCT270上的一種傳動(dòng)軸,其材料為20CrNi2MoH,形狀尺寸如圖1所示。該零件為軸對(duì)稱形狀,圖示左側(cè)有一臺(tái)階,兩端均有縮徑,采用常規(guī)機(jī)械切削方法加工時(shí),材料利用率低,工作效率很低,難以滿足生產(chǎn)要求。采用冷鍛技術(shù)成形該傳動(dòng)軸,成形零件精度高,機(jī)械加工量小,可達(dá)到圖紙要求。
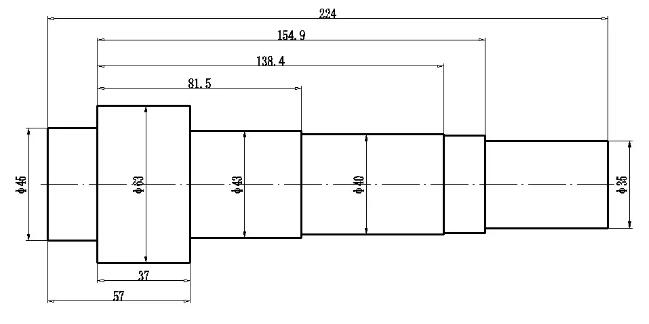
圖1 中間軸零件圖
中間軸冷鍛鍛件圖設(shè)計(jì)
該零件結(jié)構(gòu)為軸對(duì)稱形狀,且不復(fù)雜;材料為20CrNi2MoH,退火狀態(tài)硬度≤160HB,強(qiáng)度不高,除左側(cè)大臺(tái)階外,其余變形抗力不大;技術(shù)要求的尺寸精度和表面粗糙度要求一般,冷鍛零件的表面粗糙度可達(dá)Ra=0.8~0.4μm,公差等級(jí)在IT8~I(xiàn)T7,故冷鍛工藝完全可滿足該零件的各項(xiàng)要求。按冷鍛工藝要求和零件形狀所設(shè)計(jì)鍛件圖,如圖2所示。
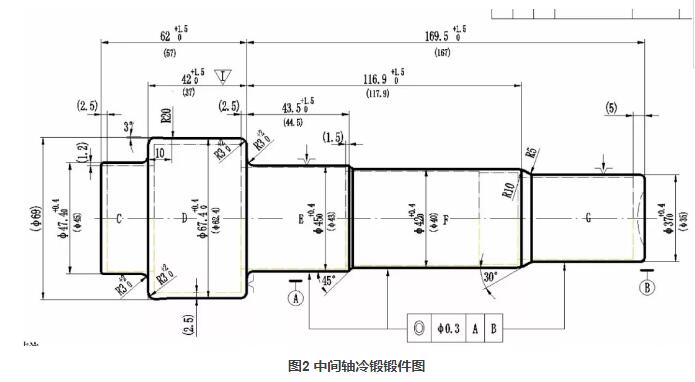
圖2 中間軸冷鍛鍛件圖
中間軸冷鍛成形工藝及模擬成形
冷鍛工藝方案
觀察中間軸鍛件圖,中間臺(tái)階直徑為φ67.4mm,兩端最小直徑分別為φ47.4mm和φ37mm,兩端均有變形,應(yīng)采用減徑擠壓。若采用φ67.4mm毛坯一次成形,由直徑φ67.4mm變?yōu)?phi;37mm,斷面縮減率ε為69.8% ,在減徑擠壓中,這么大的擠壓比會(huì)造成棒料中間鐓粗鼓脹,兩端縮徑不能成形,且易產(chǎn)生裂紋,采用其他直徑的棒料一次成形也非常困難。所以經(jīng)過計(jì)算和分析將該零件的成形工序分為三步。第1步先用φ48mm的坯料將兩端縮徑擠出直徑為φ44.6mm和φ47mm的臺(tái)階,同時(shí)將鐓粗部分先聚料到φ51mm,斷面縮減率ε為13.7%,采用開式鐓擠工藝。第2步再將坯料由φ44.6mm擠壓到φ41.8mm,斷面縮減率ε為12.2%,同時(shí)將φ48.2mm和φ51mm部分同時(shí)鐓粗到φ65mm。第3步將坯料由φ41.8mm擠壓到φ37mm,斷面縮減率ε為21.6% ,同時(shí)將φ65mm采用閉式鐓粗的方式鐓粗到φ67.4 mm。根據(jù)經(jīng)驗(yàn)入口角選擇15°。FORGE模擬的成形工步如圖3所示,各工步實(shí)物照片如圖4所示。
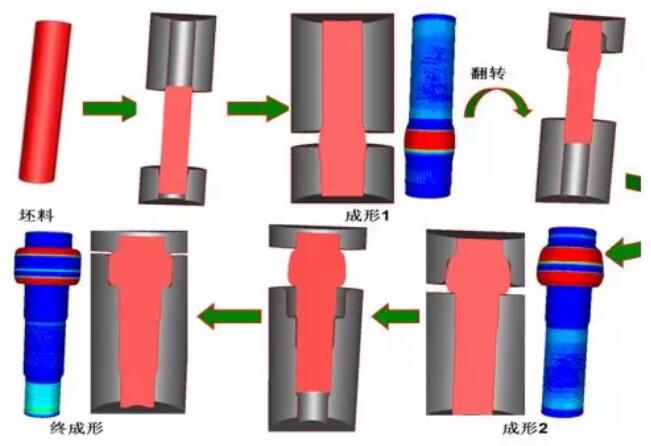
圖3 FORGE成形模擬
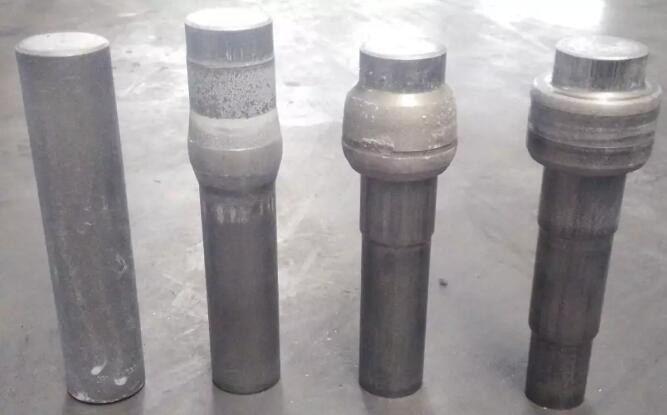
圖4 各工步實(shí)物照片
成形模擬及成形力
利用模擬軟件驗(yàn)證以上工藝的可行性。
第1序模擬過程中,鍛件成形穩(wěn)定,縮頸成形力在80t左右,聚料鐓粗的成形力為270t,成形較好,成形力分配較合理。圖5所示為中間軸第1序成形狀況及成形力。
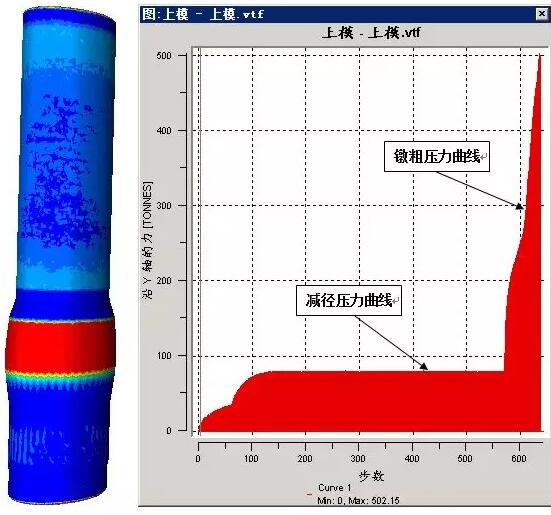
圖5 中間軸第1序成形狀況及成形力
第2序模擬過程中,鍛件成形穩(wěn)定,縮頸成形力在82t左右,聚料鐓粗的成形力為300t,成形較好,成形力分配較合理。圖6所示為中間軸第2序成形狀況及成形力。
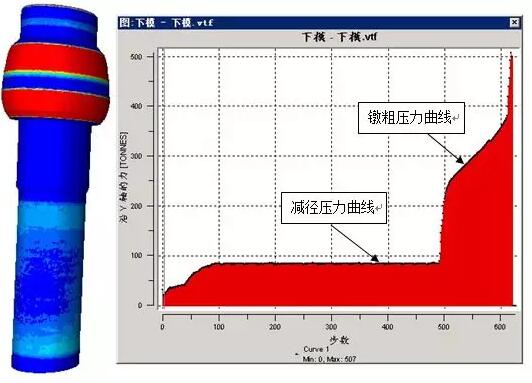
圖6 中間軸第2序成形狀況及成形力
第3序模擬過程中,鍛件成形穩(wěn)定,縮頸成形力在100t左右,聚料鐓粗的成形力將近700t,成形較好,成形力分配較合理。圖7所示中間軸第3序成形狀況及成形力。
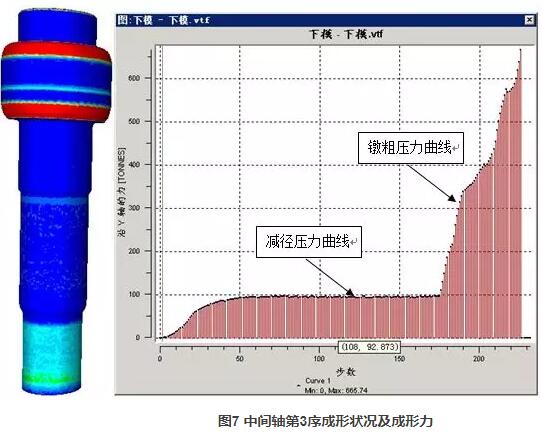
有限元成形模擬分析
用FORGE軟件進(jìn)行數(shù)值模擬,采用Pro/E三維實(shí)體軟件繪制相關(guān)模具、坯料模型,然后保存為STP格式??紤]到模具的彈性變形量相對(duì)較小,同時(shí)為了簡(jiǎn)化模擬過程,將模具設(shè)置為剛性體,坯料(或鍛件)設(shè)置為塑性體。又因?yàn)槭抢鋽D壓鍛造,將模具、坯料的初始溫度設(shè)為室溫20℃。模擬分析中材料選用20CrMnTiTempo,退火狀態(tài),等網(wǎng)格尺寸值設(shè)為1,摩擦文件(與模具)、熱交換文件(與模具)設(shè)置為中等,儲(chǔ)存步長(zhǎng)設(shè)置1;定義壓機(jī)為機(jī)械壓機(jī)。成形過程如圖8所示。
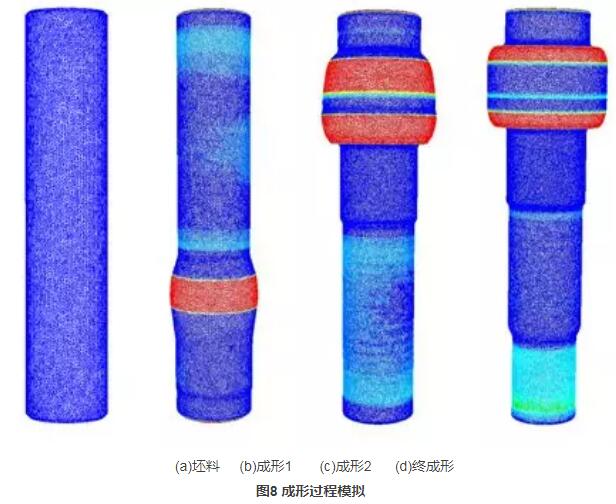
經(jīng)模擬,可以看出各工序變形均勻穩(wěn)定,網(wǎng)格沒有發(fā)生畸變,模具充填充分,鍛件形狀達(dá)到設(shè)計(jì)要求,芯部沒有錯(cuò)裂。
球化退火
球化退火是一種常用的熱處理工藝,主要適用于各種高碳工具鋼。球化退火目的在于降低硬度,改善切削加工性能,并為后面的工藝做準(zhǔn)備。本文將20CrNi2MoH合金結(jié)構(gòu)鋼采用球化退火工藝,用臺(tái)車式電阻爐進(jìn)行工藝試驗(yàn)。
加熱溫度為影響球化退火質(zhì)量的首要條件。若加熱溫度過高,則碳化物溶解太多,奧氏體成分均勻,這將減少球化核心,退火后易獲得片狀珠光體。若加熱溫度太低,則碳化物溶解,甚至可能使珠光體中的部分片狀碳化物保留下來,使鋼材退火后硬度偏高。
保溫時(shí)間必須合適。若保溫時(shí)間過長(zhǎng),則得到的球化組織不均勻,若保溫時(shí)間過短,則原始組織中的片狀碳化物難以破碎,都達(dá)不到良好的球化效果。
冷卻速度直接影響碳化物的顆粒大小和均勻性。當(dāng)加熱溫度一定時(shí),冷卻速度小,奧氏體向珠光體轉(zhuǎn)變時(shí)在高溫區(qū)經(jīng)歷的時(shí)間就長(zhǎng),因而析出的碳化物進(jìn)行聚集的時(shí)間充分,形成的碳化物顆粒較大。反之,冷卻速度大,碳化物便來不及聚集長(zhǎng)大,因而得到的是細(xì)粒狀組織,硬度偏高。
經(jīng)過多次試驗(yàn),最后確定出,20CrNi2MoH的球化退火工藝如表1所示。
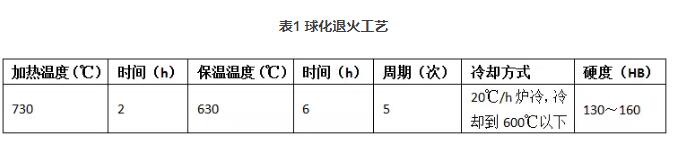
實(shí)際球化退火得到組織中,除得到大量小球狀,點(diǎn)狀珠光體外,還有少量片狀珠光體分布在鐵素體集體上。多次試驗(yàn)證明,合金鋼想得到全部的球狀珠光體非常困難,總是存在少量片狀珠光體,但總體看來,金相組織全部屬于球狀珠光體組織。
輸入軸冷鍛模具結(jié)構(gòu)
生產(chǎn)中我們采用通用冷鍛模架,預(yù)成形和終成形工序的模芯結(jié)構(gòu)簡(jiǎn)圖分別如圖9所示。凹模結(jié)構(gòu)均采用組合式凹模,凹模與外套采用過盈配合,以施加預(yù)緊力,減少冷鍛時(shí)模具開裂。凹模內(nèi)芯材料一般采用基體鋼YXR3材料涂層(調(diào)質(zhì)HRC58~60),外套采用H13材料(調(diào)質(zhì)HRC43~45),凹模頂桿采用Cr12MoV材料(調(diào)質(zhì)HRC58~60)。組合凹模受力較大的地方采用典型的2層預(yù)應(yīng)力結(jié)構(gòu),受力不大的地方采用單層預(yù)應(yīng)力結(jié)構(gòu)。
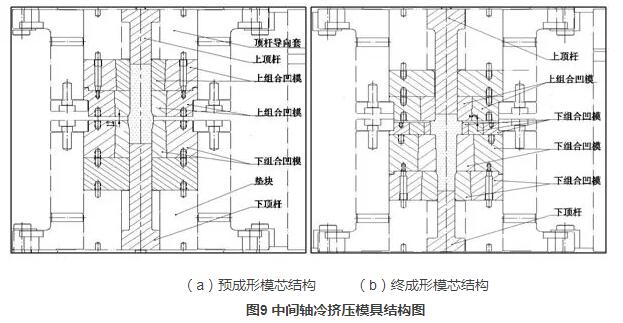
工藝過程及成形情況
汽車中間軸所采用的工藝流程為:下料→軟化處理→噴丸→制坯→潤(rùn)滑處理→三工步冷鍛成形→清理→探傷→終檢入庫(kù)。下料后對(duì)棒料進(jìn)行球化退火,退火后硬度在HB150~160之間。鍛件的晶粒度≥5級(jí),實(shí)際檢驗(yàn)為7級(jí),冷擠壓后鍛件圖及加工圖如圖10所示。
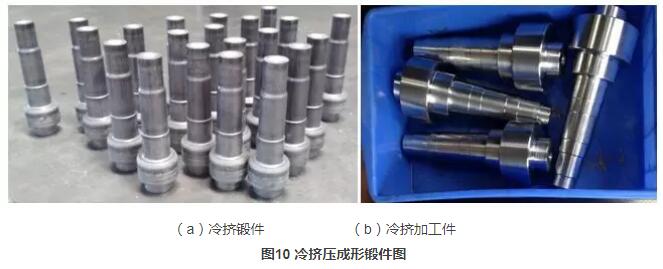
總結(jié)
⑴用冷擠壓工藝生產(chǎn)汽車中間軸鍛件工藝可靠,材料利用率高。
⑵采用FORGE模擬軟件分析產(chǎn)品成形情況比較接近實(shí)際,擠壓后鍛件尺寸穩(wěn)定,表面光潔度高。
中間軸是用在轎車變速器DCT270上的一種傳動(dòng)軸,其材料為20CrNi2MoH,形狀尺寸如圖1所示。該零件為軸對(duì)稱形狀,圖示左側(cè)有一臺(tái)階,兩端均有縮徑,采用常規(guī)機(jī)械切削方法加工時(shí),材料利用率低,工作效率很低,難以滿足生產(chǎn)要求。采用冷鍛技術(shù)成形該傳動(dòng)軸,成形零件精度高,機(jī)械加工量小,可達(dá)到圖紙要求。
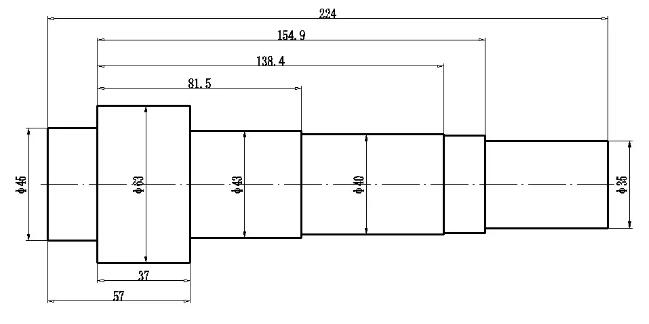
圖1 中間軸零件圖
中間軸冷鍛鍛件圖設(shè)計(jì)
該零件結(jié)構(gòu)為軸對(duì)稱形狀,且不復(fù)雜;材料為20CrNi2MoH,退火狀態(tài)硬度≤160HB,強(qiáng)度不高,除左側(cè)大臺(tái)階外,其余變形抗力不大;技術(shù)要求的尺寸精度和表面粗糙度要求一般,冷鍛零件的表面粗糙度可達(dá)Ra=0.8~0.4μm,公差等級(jí)在IT8~I(xiàn)T7,故冷鍛工藝完全可滿足該零件的各項(xiàng)要求。按冷鍛工藝要求和零件形狀所設(shè)計(jì)鍛件圖,如圖2所示。
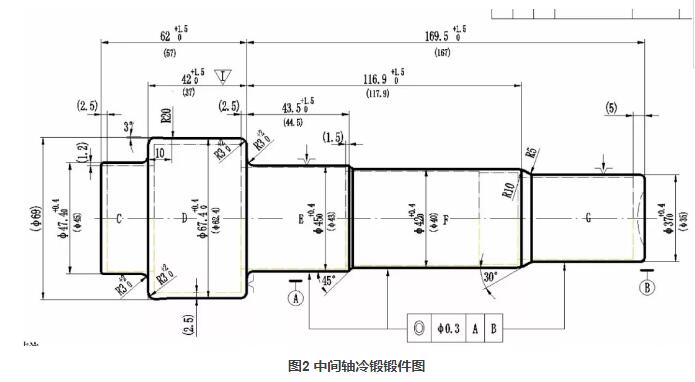
圖2 中間軸冷鍛鍛件圖
中間軸冷鍛成形工藝及模擬成形
冷鍛工藝方案
觀察中間軸鍛件圖,中間臺(tái)階直徑為φ67.4mm,兩端最小直徑分別為φ47.4mm和φ37mm,兩端均有變形,應(yīng)采用減徑擠壓。若采用φ67.4mm毛坯一次成形,由直徑φ67.4mm變?yōu)?phi;37mm,斷面縮減率ε為69.8% ,在減徑擠壓中,這么大的擠壓比會(huì)造成棒料中間鐓粗鼓脹,兩端縮徑不能成形,且易產(chǎn)生裂紋,采用其他直徑的棒料一次成形也非常困難。所以經(jīng)過計(jì)算和分析將該零件的成形工序分為三步。第1步先用φ48mm的坯料將兩端縮徑擠出直徑為φ44.6mm和φ47mm的臺(tái)階,同時(shí)將鐓粗部分先聚料到φ51mm,斷面縮減率ε為13.7%,采用開式鐓擠工藝。第2步再將坯料由φ44.6mm擠壓到φ41.8mm,斷面縮減率ε為12.2%,同時(shí)將φ48.2mm和φ51mm部分同時(shí)鐓粗到φ65mm。第3步將坯料由φ41.8mm擠壓到φ37mm,斷面縮減率ε為21.6% ,同時(shí)將φ65mm采用閉式鐓粗的方式鐓粗到φ67.4 mm。根據(jù)經(jīng)驗(yàn)入口角選擇15°。FORGE模擬的成形工步如圖3所示,各工步實(shí)物照片如圖4所示。
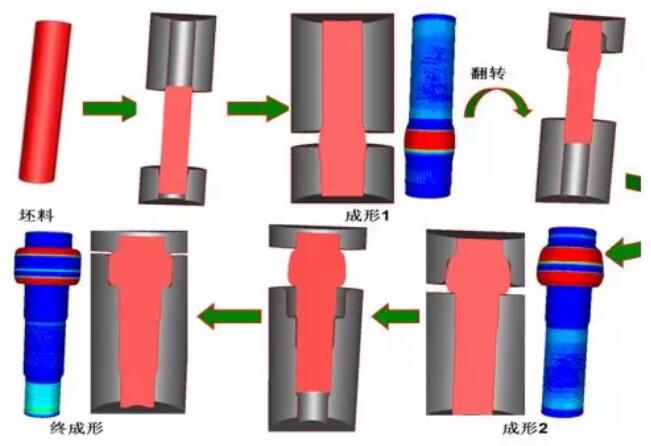
圖3 FORGE成形模擬
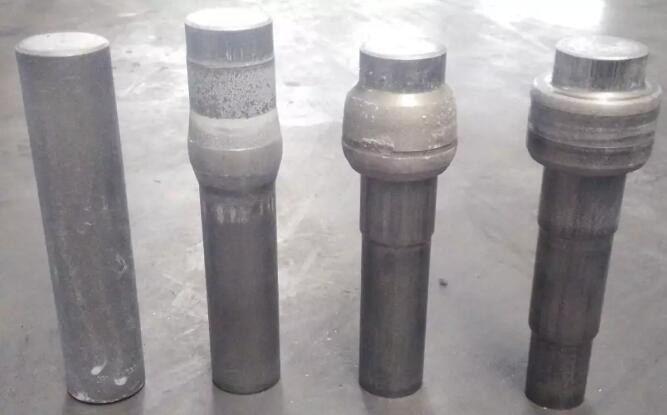
圖4 各工步實(shí)物照片
成形模擬及成形力
利用模擬軟件驗(yàn)證以上工藝的可行性。
第1序模擬過程中,鍛件成形穩(wěn)定,縮頸成形力在80t左右,聚料鐓粗的成形力為270t,成形較好,成形力分配較合理。圖5所示為中間軸第1序成形狀況及成形力。
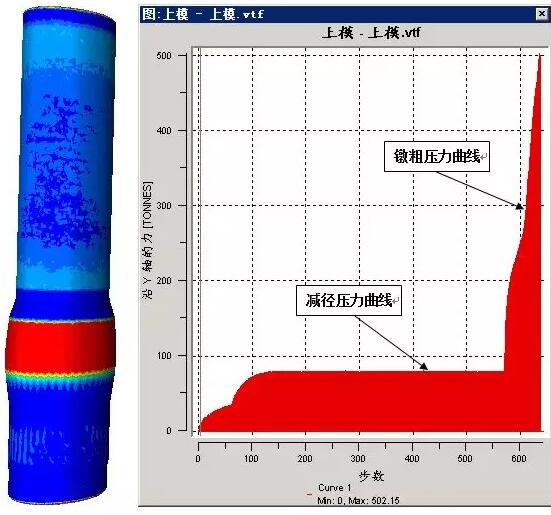
圖5 中間軸第1序成形狀況及成形力
第2序模擬過程中,鍛件成形穩(wěn)定,縮頸成形力在82t左右,聚料鐓粗的成形力為300t,成形較好,成形力分配較合理。圖6所示為中間軸第2序成形狀況及成形力。
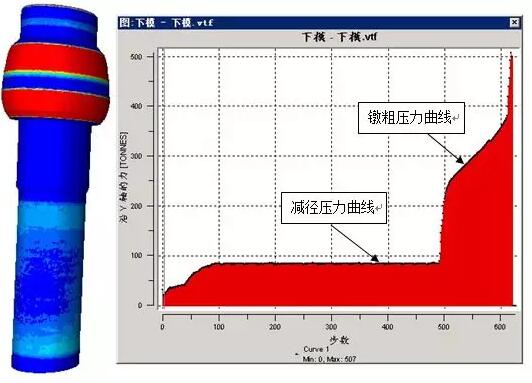
圖6 中間軸第2序成形狀況及成形力
第3序模擬過程中,鍛件成形穩(wěn)定,縮頸成形力在100t左右,聚料鐓粗的成形力將近700t,成形較好,成形力分配較合理。圖7所示中間軸第3序成形狀況及成形力。
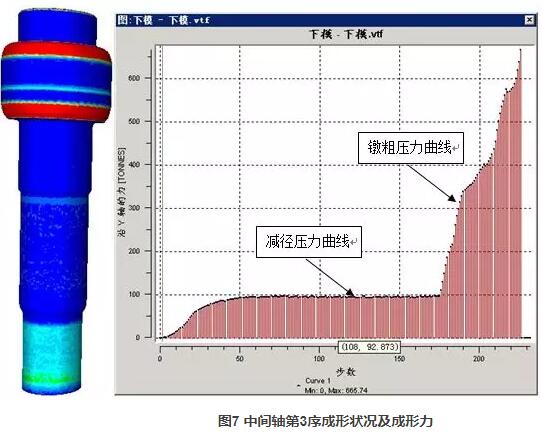
有限元成形模擬分析
用FORGE軟件進(jìn)行數(shù)值模擬,采用Pro/E三維實(shí)體軟件繪制相關(guān)模具、坯料模型,然后保存為STP格式??紤]到模具的彈性變形量相對(duì)較小,同時(shí)為了簡(jiǎn)化模擬過程,將模具設(shè)置為剛性體,坯料(或鍛件)設(shè)置為塑性體。又因?yàn)槭抢鋽D壓鍛造,將模具、坯料的初始溫度設(shè)為室溫20℃。模擬分析中材料選用20CrMnTiTempo,退火狀態(tài),等網(wǎng)格尺寸值設(shè)為1,摩擦文件(與模具)、熱交換文件(與模具)設(shè)置為中等,儲(chǔ)存步長(zhǎng)設(shè)置1;定義壓機(jī)為機(jī)械壓機(jī)。成形過程如圖8所示。
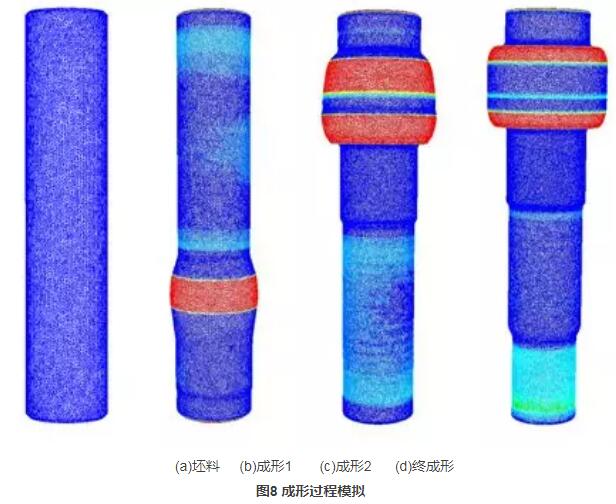
經(jīng)模擬,可以看出各工序變形均勻穩(wěn)定,網(wǎng)格沒有發(fā)生畸變,模具充填充分,鍛件形狀達(dá)到設(shè)計(jì)要求,芯部沒有錯(cuò)裂。
球化退火
球化退火是一種常用的熱處理工藝,主要適用于各種高碳工具鋼。球化退火目的在于降低硬度,改善切削加工性能,并為后面的工藝做準(zhǔn)備。本文將20CrNi2MoH合金結(jié)構(gòu)鋼采用球化退火工藝,用臺(tái)車式電阻爐進(jìn)行工藝試驗(yàn)。
加熱溫度為影響球化退火質(zhì)量的首要條件。若加熱溫度過高,則碳化物溶解太多,奧氏體成分均勻,這將減少球化核心,退火后易獲得片狀珠光體。若加熱溫度太低,則碳化物溶解,甚至可能使珠光體中的部分片狀碳化物保留下來,使鋼材退火后硬度偏高。
保溫時(shí)間必須合適。若保溫時(shí)間過長(zhǎng),則得到的球化組織不均勻,若保溫時(shí)間過短,則原始組織中的片狀碳化物難以破碎,都達(dá)不到良好的球化效果。
冷卻速度直接影響碳化物的顆粒大小和均勻性。當(dāng)加熱溫度一定時(shí),冷卻速度小,奧氏體向珠光體轉(zhuǎn)變時(shí)在高溫區(qū)經(jīng)歷的時(shí)間就長(zhǎng),因而析出的碳化物進(jìn)行聚集的時(shí)間充分,形成的碳化物顆粒較大。反之,冷卻速度大,碳化物便來不及聚集長(zhǎng)大,因而得到的是細(xì)粒狀組織,硬度偏高。
經(jīng)過多次試驗(yàn),最后確定出,20CrNi2MoH的球化退火工藝如表1所示。
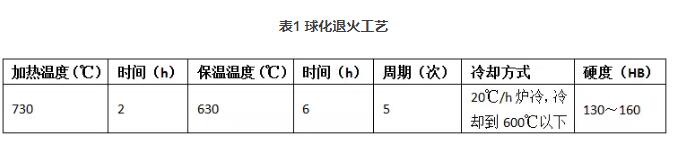
實(shí)際球化退火得到組織中,除得到大量小球狀,點(diǎn)狀珠光體外,還有少量片狀珠光體分布在鐵素體集體上。多次試驗(yàn)證明,合金鋼想得到全部的球狀珠光體非常困難,總是存在少量片狀珠光體,但總體看來,金相組織全部屬于球狀珠光體組織。
輸入軸冷鍛模具結(jié)構(gòu)
生產(chǎn)中我們采用通用冷鍛模架,預(yù)成形和終成形工序的模芯結(jié)構(gòu)簡(jiǎn)圖分別如圖9所示。凹模結(jié)構(gòu)均采用組合式凹模,凹模與外套采用過盈配合,以施加預(yù)緊力,減少冷鍛時(shí)模具開裂。凹模內(nèi)芯材料一般采用基體鋼YXR3材料涂層(調(diào)質(zhì)HRC58~60),外套采用H13材料(調(diào)質(zhì)HRC43~45),凹模頂桿采用Cr12MoV材料(調(diào)質(zhì)HRC58~60)。組合凹模受力較大的地方采用典型的2層預(yù)應(yīng)力結(jié)構(gòu),受力不大的地方采用單層預(yù)應(yīng)力結(jié)構(gòu)。
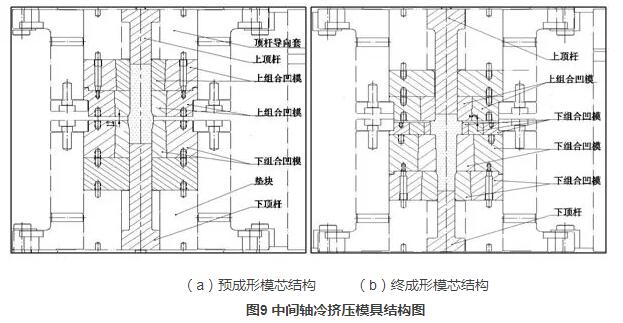
工藝過程及成形情況
汽車中間軸所采用的工藝流程為:下料→軟化處理→噴丸→制坯→潤(rùn)滑處理→三工步冷鍛成形→清理→探傷→終檢入庫(kù)。下料后對(duì)棒料進(jìn)行球化退火,退火后硬度在HB150~160之間。鍛件的晶粒度≥5級(jí),實(shí)際檢驗(yàn)為7級(jí),冷擠壓后鍛件圖及加工圖如圖10所示。
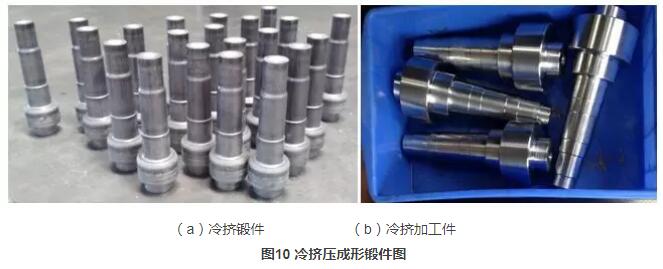
總結(jié)
⑴用冷擠壓工藝生產(chǎn)汽車中間軸鍛件工藝可靠,材料利用率高。
⑵采用FORGE模擬軟件分析產(chǎn)品成形情況比較接近實(shí)際,擠壓后鍛件尺寸穩(wěn)定,表面光潔度高。
編輯推薦
最新資訊
-
跨越速運(yùn)憑什么“圈粉”萬(wàn)千客戶?“
2025-07-01 14:42
-
數(shù)智破局啟新篇?生態(tài)共生再啟程 —
2025-06-27 20:13
-
助力汽車零部件產(chǎn)線智能化升級(jí),西門
2025-06-27 13:59
-
BBA集體轉(zhuǎn)向!放棄全面電動(dòng)化
2025-06-26 17:32
-
比換柜省錢,比自研省心,西門子Xcel
2025-06-25 15:07