簡單分析寶沃是如何打造出混線生產(chǎn)8車型生產(chǎn)體系
2018-03-01 13:30:48· 來源:車云 作者:Stylish
在寶沃工廠的對外介紹上,都提到工廠內(nèi)「可以實現(xiàn)8車型混線生產(chǎn)」的生產(chǎn)系統(tǒng),在二期建設完成后,可以實現(xiàn)年產(chǎn)量36萬臺。當然,當前寶沃只有BX5和BX7兩款車型。而且對于一個復活時間尚且不長的汽車品牌來說,短期內(nèi)推出8款完全不同的車型也是不太可能的。
對于汽車制造商來說,「制造」是根基。而在通往工業(yè)4.0的過程中,每一家制造商其實都選擇了不同的發(fā)展路線。昨天,車云菌前往參觀了寶沃汽車在北京密云郊區(qū)的工廠。單從自動化率這個數(shù)字去比較,這家工廠的自動化率并不是很高。不過從整體工廠的設計來看,寶沃的目標也是明確:能夠柔性化生產(chǎn)多車型。而且從當前來看,寶沃的目標從某種程度上說也是實現(xiàn)了。
在寶沃工廠的對外介紹上,都提到工廠內(nèi)「可以實現(xiàn)8車型混線生產(chǎn)」的生產(chǎn)系統(tǒng),在二期建設完成后,可以實現(xiàn)年產(chǎn)量36萬臺。當然,當前寶沃只有BX5和BX7兩款車型。而且對于一個復活時間尚且不長的汽車品牌來說,短期內(nèi)推出8款完全不同的車型也是不太可能的。不過此前有消息提到,寶沃可能將會在北京車展上推出BX7的純電動版本BXi7。因而這8款車型或許是當前兩款車型及后續(xù)新車的不同動力總成版本。
從這個概念也可以看出,寶沃對工廠的期望是,在后續(xù)新產(chǎn)品跟上時,能夠盡快地投入生產(chǎn)并下線,避免產(chǎn)品在生產(chǎn)階段出現(xiàn)乏力過程。
眾所周知,從智能化程度來說,要想混線生產(chǎn)8款不同產(chǎn)品,要求是很高的。不僅是生產(chǎn)線本身的智能化程度,車輛零部件的通用性、車身底盤的平臺化設計都是必須的。那么,寶沃工廠是怎么實現(xiàn)的呢?
我們先看兩個關(guān)鍵部分。
首先是柔性化針對的內(nèi)容。根據(jù)工廠經(jīng)理的介紹,工廠生產(chǎn)線可以生產(chǎn)轎車與SUV,所有可生產(chǎn)的車型,最大尺寸在5300ⅹ2000ⅹ1850mm以內(nèi),最大質(zhì)量在2300公斤以下,軸距范圍在2300-3200mm之間。因而,寶沃工廠是在工裝設備與生產(chǎn)線的選擇設計時考慮到,其能夠滿足不同尺寸、重量與軸距的車型需求。
然后是自動化設備與管理體系。
根據(jù)寶沃官方介紹資料,目前寶沃工廠的自動化機器人有547臺:其中沖壓22臺,包括運輸機器人與自動裝箱機器人;車身443臺,主要完成點焊、弧焊、螺柱焊、車頂激光釬焊,涂膠、滾邊以及打磨等連接工藝的自動化;油漆車間76臺,主要完成內(nèi)外表面自動化噴涂以及車身底部涂膠的自動化;總裝車間6臺,主要完成玻璃涂膠和安裝的自動化。
在制造的供應管理系統(tǒng)中,據(jù)介紹,寶沃也設有訂單管理與物流管理體系,能夠根據(jù)具體訂單進行生產(chǎn),實現(xiàn)某種程度上的定制化設計,訂單交付周期最短是23天。這里的定制化設計當然是有條件的。生產(chǎn)線具備多車型混線生產(chǎn)能力,如果是具體到特定車型,則會是在選裝配置與車身顏色等的區(qū)別。
從自動化設備的設置中可以看到,為了讓工廠具備多車型混線生產(chǎn)的能力,除了沖壓車間之外,寶沃是在重點工藝,即是涉及到大部件的連接、拼裝等地,進行了自動化的設計來提高生產(chǎn)效率。具體到不同的工藝中,自動化的設計也有所不同。
在沖壓車間,當前的生產(chǎn)過程基本實現(xiàn)了100%自動化。根據(jù)沖壓車間負責人的介紹,沖壓車間同時保持在工作狀態(tài)的工廠是18名,主要是用在監(jiān)控設備的運行、模具更換、下線后的產(chǎn)品檢測環(huán)節(jié)。
與焊裝、總裝等工藝不同,沖壓并非是混線生產(chǎn)的方式,而是一個沖壓模具對應一個零件。沖壓車間會根據(jù)工廠的整體產(chǎn)量、庫存量設置每一個零件的生產(chǎn)數(shù)量,一次性生產(chǎn)完成后,再更換成下一個零件的模具進行生產(chǎn),生產(chǎn)以3天為一周期,模具更換的時間為3分鐘。從生產(chǎn)效率來說,某個零件生產(chǎn)得越多當然效率越高,因為省去了更換模具與原材料的時間。但是同樣的,如果不能與產(chǎn)能想匹配,那么庫存也會越多。
在生產(chǎn)過程中,每一個生產(chǎn)零件都有編號,模具會與管理系統(tǒng)連接,查看當前零件編號是否屬于與模具相對應,以免出現(xiàn)誤加工。
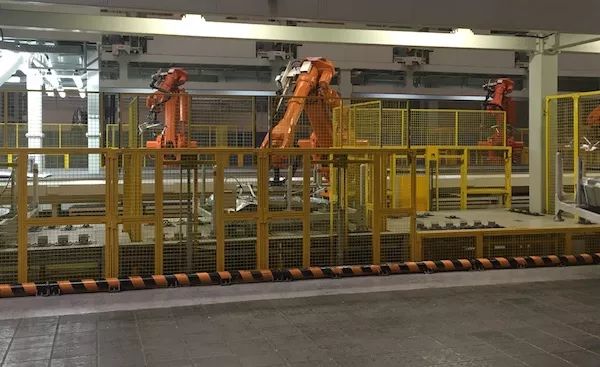
▲沖壓車間自動裝箱機器人
而為了實現(xiàn)沖壓件的自動裝箱,在產(chǎn)品下線處設有一個照相設備。照相設備拍照后會檢測出沖壓件在產(chǎn)線上的定位并將其發(fā)給裝箱機器人,裝箱機器人會根據(jù)定位調(diào)整吸附的角度,以便于沖壓件能夠裝入對應的容器中。在容器存滿后的轉(zhuǎn)運過程則是由人工運輸完成。
一般來說車身的焊裝車間是相對容易實現(xiàn)90%以上的高自動化率車身,而寶沃的車身車間目前是60%。在參觀時,車云菌發(fā)現(xiàn),大部分的分裝線焊接均是人工完成,而在車身總拼的工位則是自動化設備完成,為了滿足8車型需求,設有可以滿足8種不同車身總拼的工裝設備。與沖壓不同,因為需要完成混線生產(chǎn),因而車間的生產(chǎn)管理系統(tǒng)的內(nèi)容會更加復雜。
相比之下,總裝車身的自動化率要更低。前面提到,總裝車間的自動化率是在玻璃的涂膠與安裝工位上,設有6臺機器人,可以實現(xiàn)前后風擋玻璃的自動涂膠與安裝,包括監(jiān)測定位、涂膠與安裝三類機器人。
另外,在總裝車間,還設有AVG車輛。我們知道,AVG可以根據(jù)預先設好的路線(鋪在路面的磁條)自動運行,一般用來進行車間內(nèi)的物流運送。寶沃總裝車間中,AVG用在部分生產(chǎn)線中運輸大型部件,比如將底盤運送到“結(jié)婚”工位。
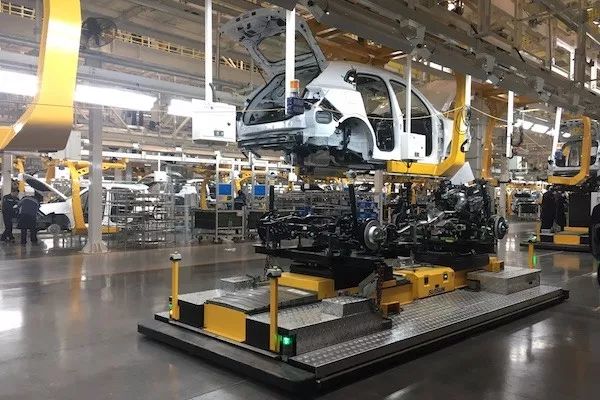
▲AVG車輛運送底盤到結(jié)婚工位
可以說,寶沃工廠是在柔性化與自動化之間進行了平衡。前面提到,要完成實現(xiàn)8車型的柔性化生產(chǎn),如果又同時要求高自動化率,那么也就意味著工廠內(nèi)智能化設備的量級式增加,隨之而來的,是整個生產(chǎn)管理系統(tǒng)在管理控制上的復雜化。而這,都是需要時間來逐步提升的。在有限的時間中,優(yōu)先解決最關(guān)鍵的需求,再逐步升級,或許也不失為一條路線。
在寶沃工廠的對外介紹上,都提到工廠內(nèi)「可以實現(xiàn)8車型混線生產(chǎn)」的生產(chǎn)系統(tǒng),在二期建設完成后,可以實現(xiàn)年產(chǎn)量36萬臺。當然,當前寶沃只有BX5和BX7兩款車型。而且對于一個復活時間尚且不長的汽車品牌來說,短期內(nèi)推出8款完全不同的車型也是不太可能的。不過此前有消息提到,寶沃可能將會在北京車展上推出BX7的純電動版本BXi7。因而這8款車型或許是當前兩款車型及后續(xù)新車的不同動力總成版本。
從這個概念也可以看出,寶沃對工廠的期望是,在后續(xù)新產(chǎn)品跟上時,能夠盡快地投入生產(chǎn)并下線,避免產(chǎn)品在生產(chǎn)階段出現(xiàn)乏力過程。
眾所周知,從智能化程度來說,要想混線生產(chǎn)8款不同產(chǎn)品,要求是很高的。不僅是生產(chǎn)線本身的智能化程度,車輛零部件的通用性、車身底盤的平臺化設計都是必須的。那么,寶沃工廠是怎么實現(xiàn)的呢?
我們先看兩個關(guān)鍵部分。
首先是柔性化針對的內(nèi)容。根據(jù)工廠經(jīng)理的介紹,工廠生產(chǎn)線可以生產(chǎn)轎車與SUV,所有可生產(chǎn)的車型,最大尺寸在5300ⅹ2000ⅹ1850mm以內(nèi),最大質(zhì)量在2300公斤以下,軸距范圍在2300-3200mm之間。因而,寶沃工廠是在工裝設備與生產(chǎn)線的選擇設計時考慮到,其能夠滿足不同尺寸、重量與軸距的車型需求。
然后是自動化設備與管理體系。
根據(jù)寶沃官方介紹資料,目前寶沃工廠的自動化機器人有547臺:其中沖壓22臺,包括運輸機器人與自動裝箱機器人;車身443臺,主要完成點焊、弧焊、螺柱焊、車頂激光釬焊,涂膠、滾邊以及打磨等連接工藝的自動化;油漆車間76臺,主要完成內(nèi)外表面自動化噴涂以及車身底部涂膠的自動化;總裝車間6臺,主要完成玻璃涂膠和安裝的自動化。
在制造的供應管理系統(tǒng)中,據(jù)介紹,寶沃也設有訂單管理與物流管理體系,能夠根據(jù)具體訂單進行生產(chǎn),實現(xiàn)某種程度上的定制化設計,訂單交付周期最短是23天。這里的定制化設計當然是有條件的。生產(chǎn)線具備多車型混線生產(chǎn)能力,如果是具體到特定車型,則會是在選裝配置與車身顏色等的區(qū)別。
從自動化設備的設置中可以看到,為了讓工廠具備多車型混線生產(chǎn)的能力,除了沖壓車間之外,寶沃是在重點工藝,即是涉及到大部件的連接、拼裝等地,進行了自動化的設計來提高生產(chǎn)效率。具體到不同的工藝中,自動化的設計也有所不同。
在沖壓車間,當前的生產(chǎn)過程基本實現(xiàn)了100%自動化。根據(jù)沖壓車間負責人的介紹,沖壓車間同時保持在工作狀態(tài)的工廠是18名,主要是用在監(jiān)控設備的運行、模具更換、下線后的產(chǎn)品檢測環(huán)節(jié)。
與焊裝、總裝等工藝不同,沖壓并非是混線生產(chǎn)的方式,而是一個沖壓模具對應一個零件。沖壓車間會根據(jù)工廠的整體產(chǎn)量、庫存量設置每一個零件的生產(chǎn)數(shù)量,一次性生產(chǎn)完成后,再更換成下一個零件的模具進行生產(chǎn),生產(chǎn)以3天為一周期,模具更換的時間為3分鐘。從生產(chǎn)效率來說,某個零件生產(chǎn)得越多當然效率越高,因為省去了更換模具與原材料的時間。但是同樣的,如果不能與產(chǎn)能想匹配,那么庫存也會越多。
在生產(chǎn)過程中,每一個生產(chǎn)零件都有編號,模具會與管理系統(tǒng)連接,查看當前零件編號是否屬于與模具相對應,以免出現(xiàn)誤加工。
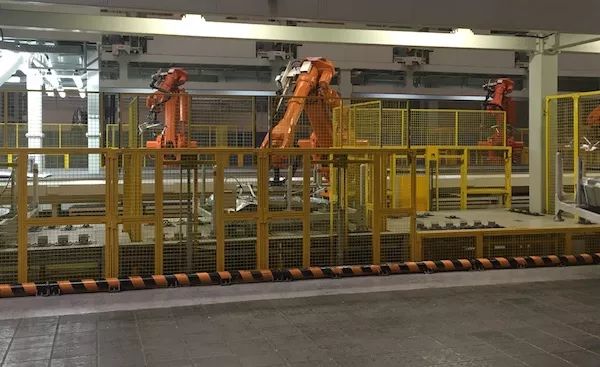
▲沖壓車間自動裝箱機器人
而為了實現(xiàn)沖壓件的自動裝箱,在產(chǎn)品下線處設有一個照相設備。照相設備拍照后會檢測出沖壓件在產(chǎn)線上的定位并將其發(fā)給裝箱機器人,裝箱機器人會根據(jù)定位調(diào)整吸附的角度,以便于沖壓件能夠裝入對應的容器中。在容器存滿后的轉(zhuǎn)運過程則是由人工運輸完成。
一般來說車身的焊裝車間是相對容易實現(xiàn)90%以上的高自動化率車身,而寶沃的車身車間目前是60%。在參觀時,車云菌發(fā)現(xiàn),大部分的分裝線焊接均是人工完成,而在車身總拼的工位則是自動化設備完成,為了滿足8車型需求,設有可以滿足8種不同車身總拼的工裝設備。與沖壓不同,因為需要完成混線生產(chǎn),因而車間的生產(chǎn)管理系統(tǒng)的內(nèi)容會更加復雜。
相比之下,總裝車身的自動化率要更低。前面提到,總裝車間的自動化率是在玻璃的涂膠與安裝工位上,設有6臺機器人,可以實現(xiàn)前后風擋玻璃的自動涂膠與安裝,包括監(jiān)測定位、涂膠與安裝三類機器人。
另外,在總裝車間,還設有AVG車輛。我們知道,AVG可以根據(jù)預先設好的路線(鋪在路面的磁條)自動運行,一般用來進行車間內(nèi)的物流運送。寶沃總裝車間中,AVG用在部分生產(chǎn)線中運輸大型部件,比如將底盤運送到“結(jié)婚”工位。
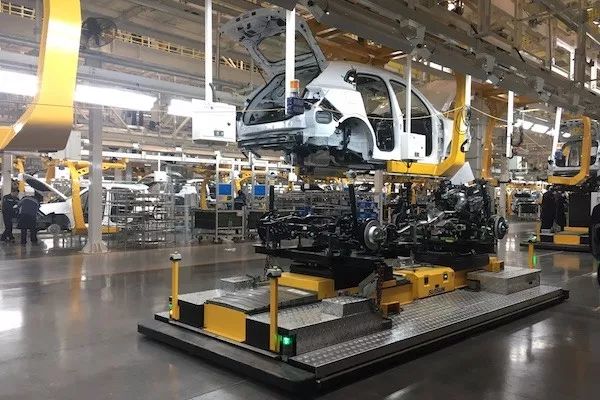
▲AVG車輛運送底盤到結(jié)婚工位
可以說,寶沃工廠是在柔性化與自動化之間進行了平衡。前面提到,要完成實現(xiàn)8車型的柔性化生產(chǎn),如果又同時要求高自動化率,那么也就意味著工廠內(nèi)智能化設備的量級式增加,隨之而來的,是整個生產(chǎn)管理系統(tǒng)在管理控制上的復雜化。而這,都是需要時間來逐步提升的。在有限的時間中,優(yōu)先解決最關(guān)鍵的需求,再逐步升級,或許也不失為一條路線。
編輯推薦
最新資訊
-
跨越速運憑什么“圈粉”萬千客戶?“
2025-07-01 14:42
-
數(shù)智破局啟新篇?生態(tài)共生再啟程 —
2025-06-27 20:13
-
助力汽車零部件產(chǎn)線智能化升級,西門
2025-06-27 13:59
-
BBA集體轉(zhuǎn)向!放棄全面電動化
2025-06-26 17:32
-
比換柜省錢,比自研省心,西門子Xcel
2025-06-25 15:07