寶沃汽車創(chuàng)新建設(shè)智能工廠與智慧物流系統(tǒng)
2018-06-26 15:40:40· 來(lái)源:物流技術(shù)與應(yīng)用
寶沃汽車率先在國(guó)內(nèi)汽車行業(yè)實(shí)現(xiàn)了工業(yè)4.0智能工廠部署,并入選工信部發(fā)布的“2017年中德智能制造合作試點(diǎn)示范項(xiàng)目”。作為智能工廠的重要組成部分,寶沃采用多項(xiàng)創(chuàng)新技術(shù)建設(shè)智慧供應(yīng)鏈及物流系統(tǒng)創(chuàng)新,亮點(diǎn)頗多,值得借鑒。
寶沃汽車率先在國(guó)內(nèi)汽車行業(yè)實(shí)現(xiàn)了工業(yè)4.0智能工廠部署,并入選工信部發(fā)布的“2017年中德智能制造合作試點(diǎn)示范項(xiàng)目”。作為智能工廠的重要組成部分,寶沃采用多項(xiàng)創(chuàng)新技術(shù)建設(shè)智慧供應(yīng)鏈及物流系統(tǒng)創(chuàng)新,亮點(diǎn)頗多,值得借鑒。
隨著《中國(guó)制造2025》戰(zhàn)略的推廣與實(shí)施,位于北京的寶沃汽車采用 “德國(guó)工業(yè)4.0”智能制造模式,率先在國(guó)內(nèi)汽車行業(yè)建設(shè)智能工廠,以領(lǐng)先全球的智能制造體系入選工信部發(fā)布的“2017年中德智能制造合作試點(diǎn)示范項(xiàng)目”。寶沃汽車北京工廠實(shí)現(xiàn)智能制造的背后,離不開智慧物流系統(tǒng)及敏捷、透明化供應(yīng)鏈體系的強(qiáng)大支撐力。日前,本刊記者采訪了寶沃汽車集團(tuán)物流規(guī)劃部助理高級(jí)經(jīng)理曹曉剛,請(qǐng)他分享了寶沃汽車智能工廠與物流系統(tǒng)的規(guī)劃建設(shè)情況以及專業(yè)經(jīng)驗(yàn)。
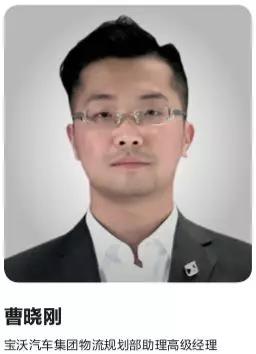
打造柔性智能工廠
2013年3月,寶沃汽車集團(tuán)按照德國(guó)工業(yè)4.0標(biāo)準(zhǔn)開始建設(shè)柔性智能工廠。經(jīng)過團(tuán)隊(duì)的精心規(guī)劃設(shè)計(jì),創(chuàng)新研發(fā)與嚴(yán)謹(jǐn)實(shí)施,2017年寶沃汽車柔性智能工廠正式亮相;同年9月該工廠被工信部正式評(píng)為“中德智能制造合作試點(diǎn)示范項(xiàng)目”;同年11月該工廠被科爾尼汽車商業(yè)評(píng)論授予“中國(guó)最佳工廠—柔性卓越獎(jiǎng)”。
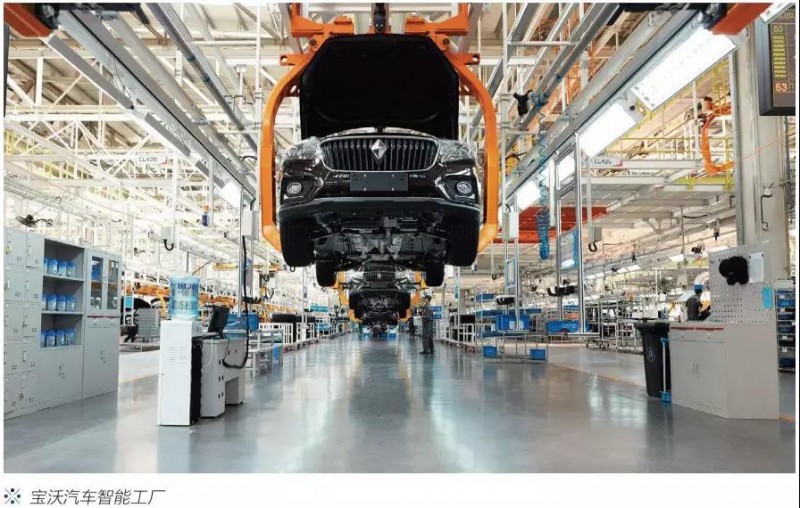
1.工廠概況
整個(gè)工廠占地面積110萬(wàn)m2,2015年6月工廠一期項(xiàng)目建設(shè)完成,生產(chǎn)節(jié)拍達(dá)到30JPH,生產(chǎn)能力達(dá)18萬(wàn)輛/年;2018年6月二期項(xiàng)目即將建設(shè)完成,生產(chǎn)節(jié)拍將達(dá)60JPH,生產(chǎn)能力將達(dá)36萬(wàn)輛/年。之所以說(shuō)該工廠極具“柔性”,最為直觀的體現(xiàn)就是,按照規(guī)劃,寶沃汽車工廠一條生產(chǎn)線將可生產(chǎn)8種車型,從轎車到SUV,從小型車到大型車,只要整車尺寸不超過5300mm(L)×2000mm(W)×1850mm(H),軸距在2300mm-3200mm之間的車型都能夠生產(chǎn),甚至可支持左/右舵車型、汽油動(dòng)力、柴油動(dòng)力、混合動(dòng)力以及新能源車型。
2.主要布局及功能
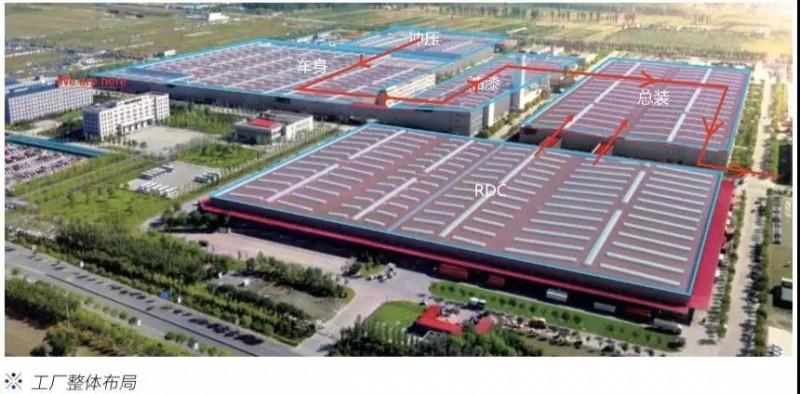
整個(gè)工廠包括沖壓、車身、油漆、總裝四大工藝車間以及RDC(物流分發(fā)中心),涵蓋了沖壓、焊裝、涂裝、總裝、檢測(cè)、物流、IT等完整的整車生產(chǎn)工藝。各車間主要布局及功能如下:
沖壓車間占地面積2.4 萬(wàn)㎡,完成每個(gè)車型的23個(gè)大型內(nèi)外覆蓋件制造,生產(chǎn)線自動(dòng)化程度100%。該車間應(yīng)用TBS雙機(jī)器人傳輸系統(tǒng),提高不同工序間零件搬運(yùn)的靈活度、負(fù)載能力及穩(wěn)定性;應(yīng)用線尾自動(dòng)裝箱系統(tǒng),防止零件變形,減輕了員工作業(yè)強(qiáng)度。
車身車間總占地面積9.9萬(wàn)㎡,采用互聯(lián)機(jī)器人、柔性NC定位系統(tǒng)、柔性?shī)A具切換系統(tǒng)、自動(dòng)化輸送系統(tǒng),標(biāo)準(zhǔn)化工藝體系、三層環(huán)網(wǎng)智能管理系統(tǒng)、國(guó)際安全標(biāo)準(zhǔn),主線自動(dòng)化率95%;采用柔性智能生產(chǎn)線,在同一條生產(chǎn)線可完成8個(gè)不同的車型無(wú)節(jié)拍損失自動(dòng)切換和混線生產(chǎn)。
油漆車間總面積5.68萬(wàn)㎡,采用高泳透力電泳漆、水性面漆、2K清漆及免中涂噴涂工藝,車身防腐壽命長(zhǎng)達(dá)12年;采用機(jī)器人自動(dòng)涂膠、內(nèi)外表面機(jī)器人自動(dòng)噴涂、快速換色系統(tǒng),快速響應(yīng)客戶對(duì)車身顏色的個(gè)性化需求;采用沸石轉(zhuǎn)輪+RTO、TNV等廢氣處理技術(shù),滿足最嚴(yán)苛的環(huán)保標(biāo)準(zhǔn)。
總裝車間總面積6.41萬(wàn)㎡,采用“平臺(tái)化+個(gè)性化”模塊化技術(shù)、“h”型的生產(chǎn)布局及智能物流系統(tǒng),滿足客戶個(gè)性化的定制需求:4條SPS地面自動(dòng)輸送線(內(nèi)飾1/內(nèi)飾2/車門/儀表),零件自動(dòng)上線率45%;6條大件空中自動(dòng)輸送線(發(fā)動(dòng)機(jī)變速箱/保險(xiǎn)杠/前端模塊/輪胎/座椅/儀表等大型零件),將物料空中自動(dòng)直送工位,減少2400m地面人工配送距離,降低地面物流復(fù)雜度,防止零件磕碰損傷。
RDC占地面積5萬(wàn)㎡,分為中小件和大件兩個(gè)庫(kù)區(qū),主要負(fù)責(zé)廠內(nèi)零部件的分裝和配送上線。
3.信息系統(tǒng)建設(shè)
信息系統(tǒng)對(duì)于智能工廠的打造尤為重要,寶沃汽車對(duì)此非常重視。結(jié)合客戶個(gè)性化訂單,以超級(jí) BOM一車一單為基礎(chǔ),通過ERP系統(tǒng)協(xié)同 MES、物流執(zhí)行系統(tǒng)LES(Logistics Excution System),實(shí)現(xiàn)大規(guī)模個(gè)性化定制生產(chǎn)。常規(guī)車型可實(shí)時(shí)交付客戶,個(gè)性化訂制車型從接到訂單開始包括物料準(zhǔn)備、生產(chǎn)排產(chǎn)、制造、運(yùn)輸?shù)拳h(huán)節(jié),交付時(shí)間最短23天。
其中,ERP系統(tǒng)采用目前全球最新的基于APO on HANA 的內(nèi)存處理技術(shù),在60JPH生產(chǎn)節(jié)拍下,能夠在15 分鐘內(nèi)完成排產(chǎn), 30 分鐘內(nèi)生成物料需求計(jì)劃(MRP),可實(shí)現(xiàn)快速排產(chǎn)和插單,滿足大規(guī)模個(gè)性化定制的要求,比傳統(tǒng)技術(shù)節(jié)省70%時(shí)間,目前全球僅寶沃、戴姆勒、沃爾沃在使用這項(xiàng)技術(shù)。
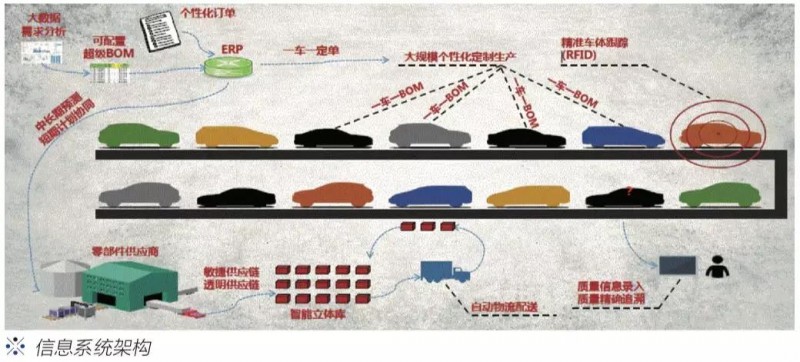
通過MES構(gòu)建透明工廠,實(shí)現(xiàn)基于制造全流程的產(chǎn)線、工位及作業(yè)節(jié)點(diǎn)的標(biāo)準(zhǔn)化和數(shù)字化;采用工業(yè)以太網(wǎng)和HMI技術(shù),實(shí)現(xiàn)設(shè)備互聯(lián);對(duì)生產(chǎn)計(jì)劃、質(zhì)量控制、防錯(cuò)、追溯進(jìn)行可視化管理;對(duì)整車生產(chǎn)制造過程中的工藝數(shù)據(jù)及參數(shù)信息進(jìn)行生命周期的數(shù)據(jù)管理。
創(chuàng)新開發(fā)的LES系統(tǒng)作為統(tǒng)一的物流執(zhí)行平臺(tái),整合了基于GPS定位技術(shù)的運(yùn)輸管理系統(tǒng)、JIS/JIT準(zhǔn)時(shí)化配送模式、基于RFID無(wú)線射頻技術(shù)的自動(dòng)化出入庫(kù)管理、自動(dòng)化立體庫(kù)、SPS系統(tǒng)、大件直送等自動(dòng)化上線技術(shù),從而實(shí)現(xiàn)了敏捷、透明的供應(yīng)鏈體系,能夠滿足8車型柔性化的生產(chǎn)物料需求,物流配送準(zhǔn)確率100%,供貨響應(yīng)時(shí)間縮短80%。
敏捷透明化的供應(yīng)鏈
1.循環(huán)取貨規(guī)劃
50%以上的供應(yīng)商集中在江浙滬。限于工廠所處位置以及北京市政規(guī)劃,寶沃汽車周邊無(wú)法設(shè)立配套零部件產(chǎn)業(yè)園。在此條件下,要想降低物流運(yùn)輸成本和零件庫(kù)存成本,節(jié)省庫(kù)區(qū)面積,實(shí)現(xiàn)零件全過程在途監(jiān)控,實(shí)施全國(guó)循環(huán)取貨對(duì)于提升供應(yīng)鏈效率、降低成本顯得十分必要。因此,寶沃汽車制定了詳細(xì)的循環(huán)取貨機(jī)制,并在逐步實(shí)施:
對(duì)于供貨距離60公里以內(nèi)的本地供應(yīng)商,直送到工廠;
供貨距離300公里以內(nèi)的京津冀供應(yīng)商,優(yōu)先循環(huán)取貨到工廠;
供貨距離1500公里以內(nèi)的華東、東北供應(yīng)商,優(yōu)先循環(huán)取貨到工廠/VMI庫(kù);
供貨距離1500公里以上的其他供應(yīng)商,占比很小,條件具備的循環(huán)取貨。
2.創(chuàng)新的TWD物料拉動(dòng)模式
傳統(tǒng)的物料拉動(dòng)模式依賴于現(xiàn)場(chǎng)作業(yè)人員,拉動(dòng)方式粗放,異常頻發(fā),供應(yīng)商裝載率低,道口/叉車作業(yè)不均衡;寶沃汽車已經(jīng)對(duì)119家供應(yīng)商推廣實(shí)施了TWD(層級(jí)拉動(dòng))模式,由信息系統(tǒng)替代人工,實(shí)行MIN/MAX/車輛過點(diǎn)拉動(dòng),時(shí)間窗合理均衡排布,最終供應(yīng)商裝載率、整體物流效率均大幅度提升。
3.智能入廠協(xié)同
受限于廠房面積,寶沃汽車需要嚴(yán)格控制供應(yīng)商零部件的入廠時(shí)間,在時(shí)間和空間調(diào)度上做的更為精細(xì)。為此,通過ETCP、微信、RFID、LES多系統(tǒng)協(xié)作,實(shí)現(xiàn)了車輛即時(shí)掃描、即時(shí)排隊(duì),保證了入廠車輛均衡穩(wěn)定,提高了50%作業(yè)效率。整套系統(tǒng)為業(yè)內(nèi)首創(chuàng)。
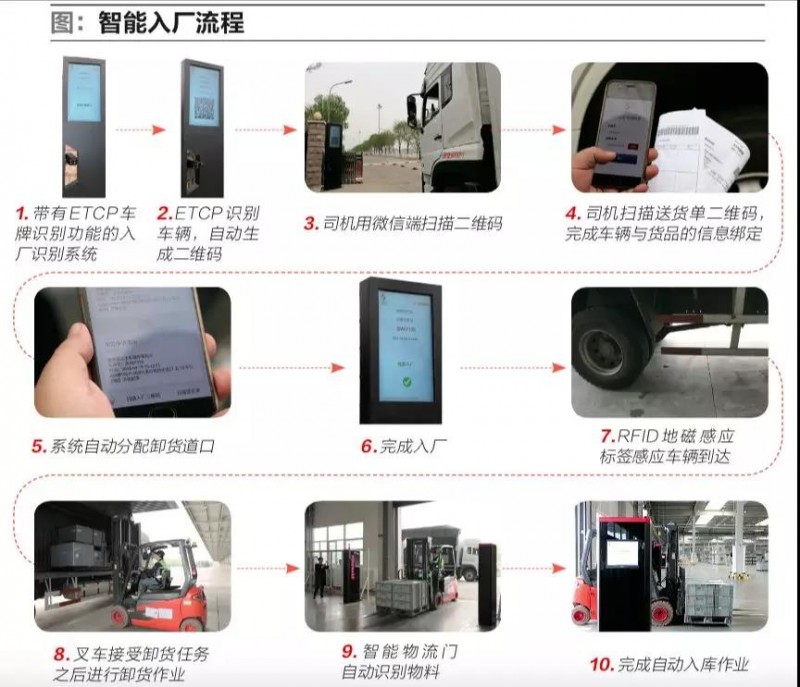
具體作業(yè)流程是:卡車到達(dá)廠區(qū)門口,ETCP車牌自動(dòng)識(shí)別系統(tǒng)識(shí)別卡車車牌,并記錄卡車出入廠時(shí)間;司機(jī)登錄微信公眾號(hào),掃描送貨單,送貨單與卡車信息完成綁定;司機(jī)掃描門口顯示屏上的二維碼,系統(tǒng)自動(dòng)分配車位;車輛進(jìn)入指定區(qū)域等待,系統(tǒng)提示卸貨時(shí)間,車輛到達(dá)卸貨口;在每個(gè)卸貨道口均裝有RFID地磁感應(yīng)標(biāo)簽,該標(biāo)簽可以自動(dòng)識(shí)別車位占用及釋放情況,進(jìn)行卸貨時(shí)間統(tǒng)計(jì)以及超時(shí)預(yù)警提示;車輛到達(dá)卸貨道口,通過系統(tǒng)提示車載電腦并完成卸貨作業(yè)。LES系統(tǒng)預(yù)提示空箱返空作業(yè),并可統(tǒng)計(jì)卡車在廠時(shí)間。
4.透明供應(yīng)鏈
曹曉剛提到,汽車產(chǎn)品更新?lián)Q代很快,庫(kù)存越多損失越大。為了降低供應(yīng)鏈上整體庫(kù)存,保證及時(shí)供應(yīng),避免斷貨情況,寶沃汽車將通過透明供應(yīng)鏈管理把所有的庫(kù)存和成本都實(shí)現(xiàn)目視化,帶動(dòng)整個(gè)產(chǎn)業(yè)鏈升級(jí)。
通過SAP、LES、TMS系統(tǒng)協(xié)作,實(shí)現(xiàn)供應(yīng)商零部件從出廠到寶沃工廠全過程覆蓋,實(shí)現(xiàn)低成本、高效率、高協(xié)同、透明化的供應(yīng)物流模式。將LES系統(tǒng)管理范圍從工廠擴(kuò)展到VMI庫(kù)甚至是零部件供應(yīng)商,實(shí)現(xiàn)供應(yīng)鏈全過程信息系統(tǒng)管理,同時(shí)與庫(kù)存預(yù)警相結(jié)合,保證零件及時(shí)供應(yīng)。
5.實(shí)施大數(shù)據(jù)管理
寶沃汽車與微軟(Microsoft)合作,定制化開發(fā)了寶沃汽車的LES,目前已完成兩期建設(shè),完全可以支持多車型柔性化的物流及供應(yīng)鏈業(yè)務(wù)需求。通過建立PFEP(Plan For Every Parts)數(shù)據(jù)體系,打造物流大數(shù)據(jù)系統(tǒng)。將零件信息、供應(yīng)鏈物流信息、倉(cāng)儲(chǔ)信息、供應(yīng)商信息、包裝信息、線邊信息等資源不斷進(jìn)行整合優(yōu)化,將所有的信息化設(shè)備和系統(tǒng)都與大數(shù)據(jù)系統(tǒng)關(guān)聯(lián),并進(jìn)行大數(shù)據(jù)分析。
6. 循環(huán)環(huán)保包裝應(yīng)用
寶沃汽車推動(dòng)零部件物流全程應(yīng)用循環(huán)圍板箱,尺寸規(guī)格標(biāo)準(zhǔn),便于倉(cāng)儲(chǔ)、運(yùn)輸?shù)龋岣吡宋锪餍?;比采用金屬料架成本低;頂蓋、底托為HDPE(低壓高密度聚乙烯),圍板為PP(聚丙烯)蜂窩板,材料環(huán)保。
智慧物流系統(tǒng)及裝備
智慧物流系統(tǒng)與裝備的創(chuàng)新應(yīng)用是滿足生產(chǎn)需求、保證物流效率的有效舉措。曹曉剛坦言,想要滿足8個(gè)車型的高效率混線生產(chǎn)對(duì)物流所帶來(lái)的壓力非常大。在寶沃汽車高層領(lǐng)導(dǎo)對(duì)物流系統(tǒng)建設(shè)的重視與支持下,經(jīng)過不斷的探索與實(shí)踐,目前部分智慧物流系統(tǒng)及裝備已經(jīng)投入應(yīng)用,還有部分項(xiàng)目正在實(shí)施。
1.SPS智能揀選系統(tǒng)
SPS智能揀選系統(tǒng)在汽車行業(yè)得到了普遍應(yīng)用,但是寶沃汽車的SPS智能揀選系統(tǒng)有著獨(dú)特的創(chuàng)新點(diǎn),極度彰顯了柔性化和智能化特點(diǎn)。
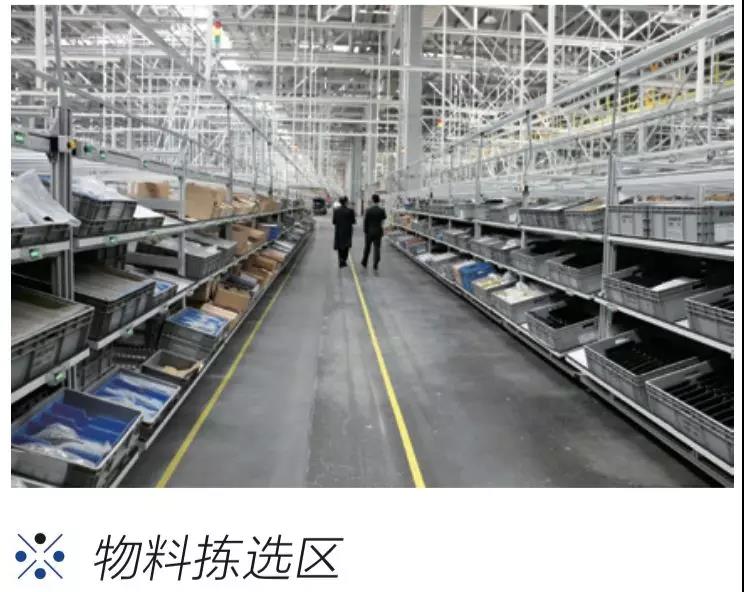
硬件方面,料架依據(jù)人體工程學(xué)設(shè)計(jì),選用輕量化鋁合金材質(zhì),采用方便、柔性化的標(biāo)準(zhǔn)件拼裝。整個(gè)系統(tǒng)中還應(yīng)用了紅外體感式指示燈、掃碼設(shè)備、車載電腦、穿戴設(shè)備、AGV等大量的先進(jìn)硬件設(shè)備,。
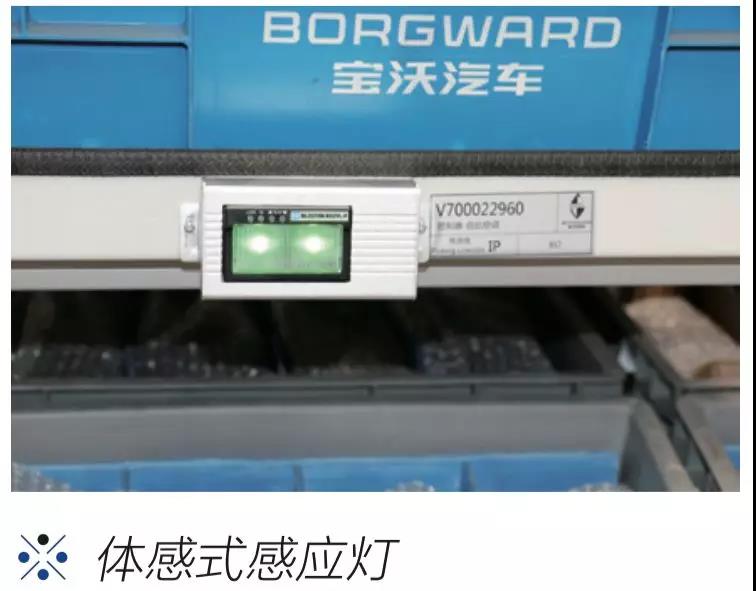
軟件方面,業(yè)內(nèi)首家通過LES、PTL系統(tǒng)的深度交互,可以滿足8車型柔性化的智能揀貨作業(yè)指示;首創(chuàng)投料防錯(cuò)功能,通過穿戴掃描設(shè)備和貨架上安裝的紅外體感式指示燈,確保投料準(zhǔn)確性;整個(gè)系統(tǒng)采用并聯(lián)模式,以每個(gè)貨格為一個(gè)單元,可以按照需求調(diào)整零部件存放位置,以滿足不斷增加的新車型生產(chǎn)需求;使用AGV智能調(diào)度系統(tǒng),不同路段運(yùn)行速度可調(diào),可優(yōu)化AGV數(shù)量。
整個(gè)系統(tǒng)的使用,減少了線邊面積占用,降低了人員作業(yè)強(qiáng)度,使揀選和投料作業(yè)準(zhǔn)確率高達(dá)100%。
2.無(wú)線射頻識(shí)別技術(shù)(RFID)
在寶沃汽車工廠中,可以看到大量的RFID技術(shù)應(yīng)用。如,所有的周轉(zhuǎn)包裝器具上都將裝有具備抗金屬干擾、抗沖擊特性的RFID標(biāo)簽;在物料入廠檢收、入庫(kù)以及出庫(kù)等所有物流環(huán)節(jié)都將應(yīng)用RFID智能物流門,智能物流門能夠快速批量讀取零件包裝上的RFID標(biāo)簽數(shù)據(jù),信息讀取準(zhǔn)確率高達(dá)99.99%,還能實(shí)現(xiàn)無(wú)人化作業(yè);在高位貨架及動(dòng)態(tài)庫(kù)位環(huán)節(jié)應(yīng)用RFID車載模塊,可實(shí)現(xiàn)庫(kù)位自動(dòng)校驗(yàn),出入庫(kù)準(zhǔn)確率達(dá)100%。以包裝箱為單位的RFID技術(shù)創(chuàng)新應(yīng)用,實(shí)現(xiàn)了整個(gè)供應(yīng)鏈過程透明、可追溯。

寶沃汽車成為業(yè)內(nèi)首批實(shí)現(xiàn)汽車行業(yè)供應(yīng)鏈RFID技術(shù)集成應(yīng)用的企業(yè),創(chuàng)造了多項(xiàng)專利技術(shù),最終將打造出無(wú)人化、透明化的物流體系,今后通過配合無(wú)人機(jī)的使用還可以實(shí)現(xiàn)庫(kù)存無(wú)人化盤點(diǎn)。這為寶沃汽車工業(yè)4.0工廠實(shí)現(xiàn)自動(dòng)化、智能化生產(chǎn)與物流提供了強(qiáng)大助力。
3.AGV廠內(nèi)物料配送
在廠內(nèi)物流配送環(huán)節(jié),大規(guī)模使用AGV代替叉車或牽引車作業(yè),大幅提高物流作業(yè)自動(dòng)化率。車間內(nèi)行駛的AGV搭載多臺(tái)套料架配送,配合SPS系統(tǒng),實(shí)現(xiàn)了總裝車間、車身車間內(nèi)智能化物料配送;目前寶沃還在研究應(yīng)用激光導(dǎo)航AGV搭載標(biāo)準(zhǔn)包裝、器具,完成車身料架工序間轉(zhuǎn)運(yùn)以及RDC向總裝車間配送,預(yù)計(jì)于未來(lái)兩年內(nèi)投入使用。
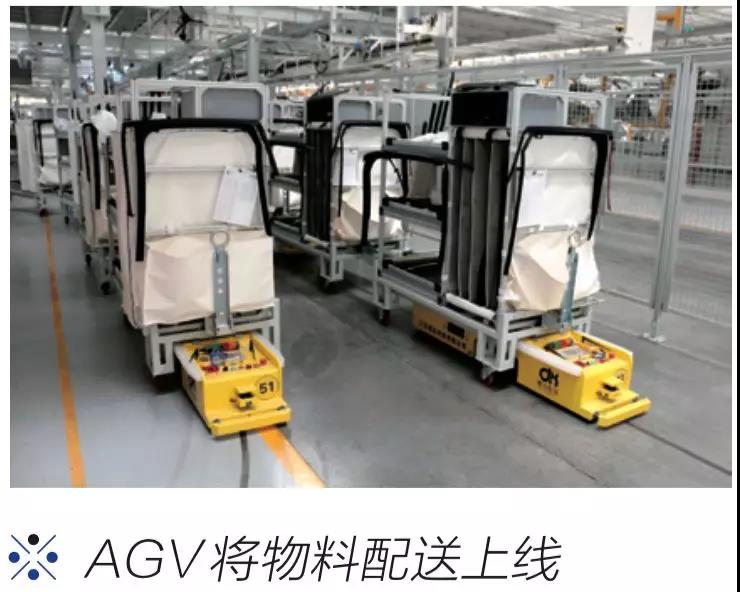
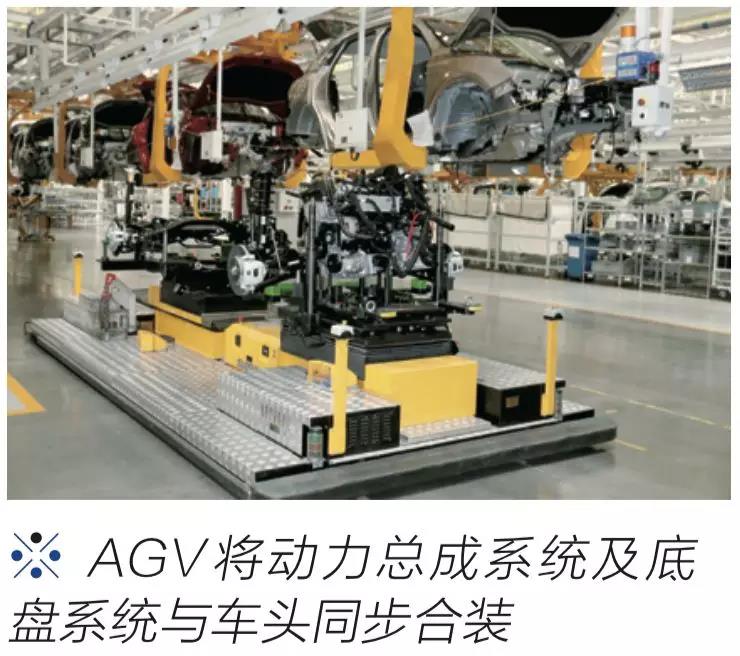
4.自動(dòng)化立體庫(kù)
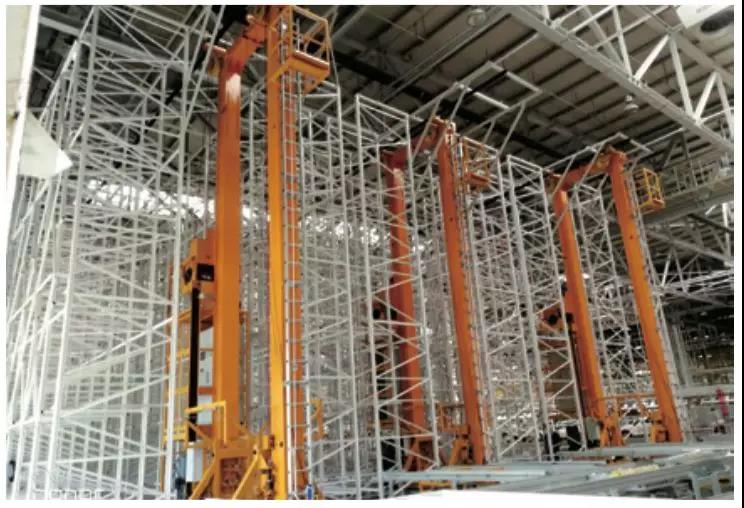
(1)座椅立體庫(kù)
由于座椅供應(yīng)商距離寶沃汽車工廠距離較遠(yuǎn),且座椅種類多,庫(kù)存管理難度高。經(jīng)過嚴(yán)密考量,寶沃汽車發(fā)現(xiàn)無(wú)論是從成本、準(zhǔn)確率還是效率方面考慮,在工廠內(nèi)建設(shè)座椅立體庫(kù)是最合適的選擇。因此,寶沃汽車也成為了業(yè)內(nèi)首家應(yīng)用座椅立體庫(kù)的企業(yè)。
整個(gè)立體庫(kù)有3個(gè)巷道,1200個(gè)貨位,使用高速堆垛機(jī)完成座椅的出入庫(kù)、排序上線及庫(kù)存管理等功能。在座椅翻包環(huán)節(jié)創(chuàng)新性采用了360度旋轉(zhuǎn)的AGV,極大降低了機(jī)械機(jī)構(gòu)的設(shè)計(jì)和制作難度。立體庫(kù)作業(yè)能力可達(dá)90JPH,全部通過WCS系統(tǒng)管理,最大程度保障了座椅供應(yīng)的柔性化和準(zhǔn)時(shí)性。
(2)料箱立體庫(kù)
在寶沃汽車的方案設(shè)計(jì)中,由料箱包裝的物料入庫(kù)后將被直接放置到入庫(kù)道口,由一臺(tái)機(jī)器臂抓取放到輸送鏈上,自動(dòng)輸送入庫(kù);立體庫(kù)系統(tǒng)與LES系統(tǒng)對(duì)接,LES下達(dá)出庫(kù)任務(wù)后,立體庫(kù)自動(dòng)將物料下架并分配到相應(yīng)道口,由機(jī)械手或者人放到AGV小車,完成配送。一期項(xiàng)目中主要實(shí)施自動(dòng)化立體庫(kù),規(guī)劃貨位數(shù)量8000個(gè),可兼容6種不同規(guī)格的箱型,零部件種類達(dá)2000多種。
通過料箱自動(dòng)化立體庫(kù)的應(yīng)用,重點(diǎn)零部件可由自動(dòng)立體庫(kù)完成出入庫(kù)、分揀作業(yè),倉(cāng)儲(chǔ)能力提升5倍,分揀效率提升2倍;該自動(dòng)化立體庫(kù)將接RFID、SPS、自動(dòng)化配送項(xiàng)目,實(shí)現(xiàn)互聯(lián)互通,完成基礎(chǔ)廠內(nèi)物流的自動(dòng)化平臺(tái)搭建。
未來(lái)發(fā)展規(guī)劃
隨著智能制造的不斷推進(jìn),汽車企業(yè)越來(lái)越重視搭建自動(dòng)化與智能化物流體系,逐步加大投入。而寶沃汽車在智慧供應(yīng)鏈及物流系統(tǒng)建設(shè)方面積極探索,勇于創(chuàng)新,已有多項(xiàng)應(yīng)用成果落地,無(wú)疑走在了行業(yè)發(fā)展前列。但寶沃汽車在智慧物流體系方面的建設(shè)絕不止于此。
寶沃汽車計(jì)劃到2020年初步建成智能化物流體系。為了實(shí)現(xiàn)這一目標(biāo),公司已經(jīng)制定了三步走戰(zhàn)略:第一階段,完成標(biāo)準(zhǔn)化打造;第二階段,實(shí)現(xiàn)自動(dòng)化/省人化;第三階段實(shí)現(xiàn)無(wú)人化/智能化。
曹曉剛表示,目前國(guó)內(nèi)汽車產(chǎn)業(yè)上下游的物流自動(dòng)化水平普遍較低,物流成本占比相當(dāng)高。伴隨著中國(guó)制造產(chǎn)業(yè)的不斷升級(jí),以及汽車行業(yè)競(jìng)爭(zhēng)的不斷加劇,發(fā)展智能物流必將被越來(lái)越多的汽車制造廠和零部件供應(yīng)商重視。寶沃汽車高層十分重視和支持智能制造的建設(shè),寶沃也將繼續(xù)下大力氣進(jìn)行研發(fā)和實(shí)踐,希望能夠在智能物流領(lǐng)域的探索中為行業(yè)做出一些貢獻(xiàn)。
隨著《中國(guó)制造2025》戰(zhàn)略的推廣與實(shí)施,位于北京的寶沃汽車采用 “德國(guó)工業(yè)4.0”智能制造模式,率先在國(guó)內(nèi)汽車行業(yè)建設(shè)智能工廠,以領(lǐng)先全球的智能制造體系入選工信部發(fā)布的“2017年中德智能制造合作試點(diǎn)示范項(xiàng)目”。寶沃汽車北京工廠實(shí)現(xiàn)智能制造的背后,離不開智慧物流系統(tǒng)及敏捷、透明化供應(yīng)鏈體系的強(qiáng)大支撐力。日前,本刊記者采訪了寶沃汽車集團(tuán)物流規(guī)劃部助理高級(jí)經(jīng)理曹曉剛,請(qǐng)他分享了寶沃汽車智能工廠與物流系統(tǒng)的規(guī)劃建設(shè)情況以及專業(yè)經(jīng)驗(yàn)。
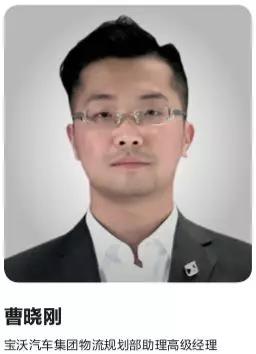
打造柔性智能工廠
2013年3月,寶沃汽車集團(tuán)按照德國(guó)工業(yè)4.0標(biāo)準(zhǔn)開始建設(shè)柔性智能工廠。經(jīng)過團(tuán)隊(duì)的精心規(guī)劃設(shè)計(jì),創(chuàng)新研發(fā)與嚴(yán)謹(jǐn)實(shí)施,2017年寶沃汽車柔性智能工廠正式亮相;同年9月該工廠被工信部正式評(píng)為“中德智能制造合作試點(diǎn)示范項(xiàng)目”;同年11月該工廠被科爾尼汽車商業(yè)評(píng)論授予“中國(guó)最佳工廠—柔性卓越獎(jiǎng)”。
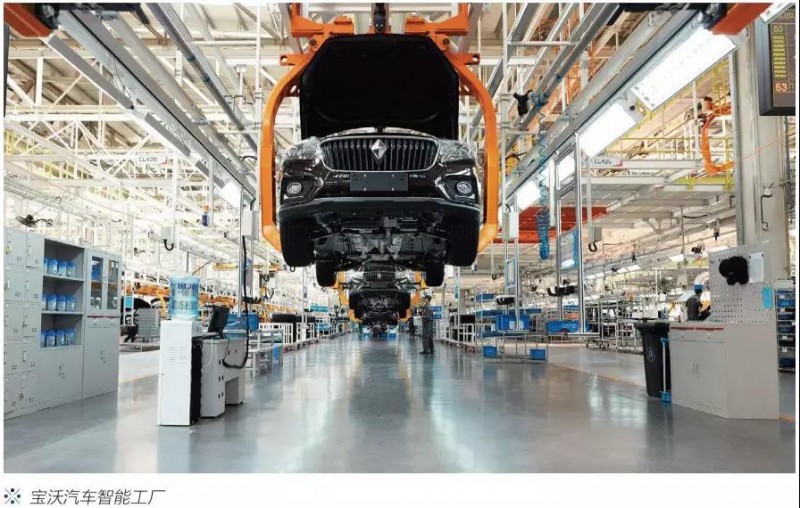
1.工廠概況
整個(gè)工廠占地面積110萬(wàn)m2,2015年6月工廠一期項(xiàng)目建設(shè)完成,生產(chǎn)節(jié)拍達(dá)到30JPH,生產(chǎn)能力達(dá)18萬(wàn)輛/年;2018年6月二期項(xiàng)目即將建設(shè)完成,生產(chǎn)節(jié)拍將達(dá)60JPH,生產(chǎn)能力將達(dá)36萬(wàn)輛/年。之所以說(shuō)該工廠極具“柔性”,最為直觀的體現(xiàn)就是,按照規(guī)劃,寶沃汽車工廠一條生產(chǎn)線將可生產(chǎn)8種車型,從轎車到SUV,從小型車到大型車,只要整車尺寸不超過5300mm(L)×2000mm(W)×1850mm(H),軸距在2300mm-3200mm之間的車型都能夠生產(chǎn),甚至可支持左/右舵車型、汽油動(dòng)力、柴油動(dòng)力、混合動(dòng)力以及新能源車型。
2.主要布局及功能
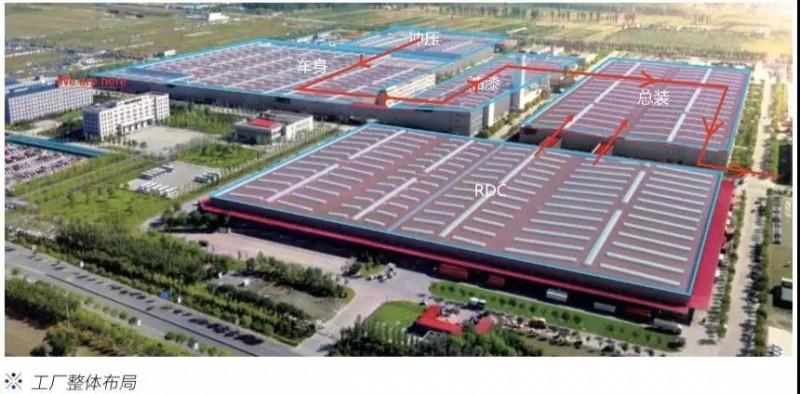
整個(gè)工廠包括沖壓、車身、油漆、總裝四大工藝車間以及RDC(物流分發(fā)中心),涵蓋了沖壓、焊裝、涂裝、總裝、檢測(cè)、物流、IT等完整的整車生產(chǎn)工藝。各車間主要布局及功能如下:
沖壓車間占地面積2.4 萬(wàn)㎡,完成每個(gè)車型的23個(gè)大型內(nèi)外覆蓋件制造,生產(chǎn)線自動(dòng)化程度100%。該車間應(yīng)用TBS雙機(jī)器人傳輸系統(tǒng),提高不同工序間零件搬運(yùn)的靈活度、負(fù)載能力及穩(wěn)定性;應(yīng)用線尾自動(dòng)裝箱系統(tǒng),防止零件變形,減輕了員工作業(yè)強(qiáng)度。
車身車間總占地面積9.9萬(wàn)㎡,采用互聯(lián)機(jī)器人、柔性NC定位系統(tǒng)、柔性?shī)A具切換系統(tǒng)、自動(dòng)化輸送系統(tǒng),標(biāo)準(zhǔn)化工藝體系、三層環(huán)網(wǎng)智能管理系統(tǒng)、國(guó)際安全標(biāo)準(zhǔn),主線自動(dòng)化率95%;采用柔性智能生產(chǎn)線,在同一條生產(chǎn)線可完成8個(gè)不同的車型無(wú)節(jié)拍損失自動(dòng)切換和混線生產(chǎn)。
油漆車間總面積5.68萬(wàn)㎡,采用高泳透力電泳漆、水性面漆、2K清漆及免中涂噴涂工藝,車身防腐壽命長(zhǎng)達(dá)12年;采用機(jī)器人自動(dòng)涂膠、內(nèi)外表面機(jī)器人自動(dòng)噴涂、快速換色系統(tǒng),快速響應(yīng)客戶對(duì)車身顏色的個(gè)性化需求;采用沸石轉(zhuǎn)輪+RTO、TNV等廢氣處理技術(shù),滿足最嚴(yán)苛的環(huán)保標(biāo)準(zhǔn)。
總裝車間總面積6.41萬(wàn)㎡,采用“平臺(tái)化+個(gè)性化”模塊化技術(shù)、“h”型的生產(chǎn)布局及智能物流系統(tǒng),滿足客戶個(gè)性化的定制需求:4條SPS地面自動(dòng)輸送線(內(nèi)飾1/內(nèi)飾2/車門/儀表),零件自動(dòng)上線率45%;6條大件空中自動(dòng)輸送線(發(fā)動(dòng)機(jī)變速箱/保險(xiǎn)杠/前端模塊/輪胎/座椅/儀表等大型零件),將物料空中自動(dòng)直送工位,減少2400m地面人工配送距離,降低地面物流復(fù)雜度,防止零件磕碰損傷。
RDC占地面積5萬(wàn)㎡,分為中小件和大件兩個(gè)庫(kù)區(qū),主要負(fù)責(zé)廠內(nèi)零部件的分裝和配送上線。
3.信息系統(tǒng)建設(shè)
信息系統(tǒng)對(duì)于智能工廠的打造尤為重要,寶沃汽車對(duì)此非常重視。結(jié)合客戶個(gè)性化訂單,以超級(jí) BOM一車一單為基礎(chǔ),通過ERP系統(tǒng)協(xié)同 MES、物流執(zhí)行系統(tǒng)LES(Logistics Excution System),實(shí)現(xiàn)大規(guī)模個(gè)性化定制生產(chǎn)。常規(guī)車型可實(shí)時(shí)交付客戶,個(gè)性化訂制車型從接到訂單開始包括物料準(zhǔn)備、生產(chǎn)排產(chǎn)、制造、運(yùn)輸?shù)拳h(huán)節(jié),交付時(shí)間最短23天。
其中,ERP系統(tǒng)采用目前全球最新的基于APO on HANA 的內(nèi)存處理技術(shù),在60JPH生產(chǎn)節(jié)拍下,能夠在15 分鐘內(nèi)完成排產(chǎn), 30 分鐘內(nèi)生成物料需求計(jì)劃(MRP),可實(shí)現(xiàn)快速排產(chǎn)和插單,滿足大規(guī)模個(gè)性化定制的要求,比傳統(tǒng)技術(shù)節(jié)省70%時(shí)間,目前全球僅寶沃、戴姆勒、沃爾沃在使用這項(xiàng)技術(shù)。
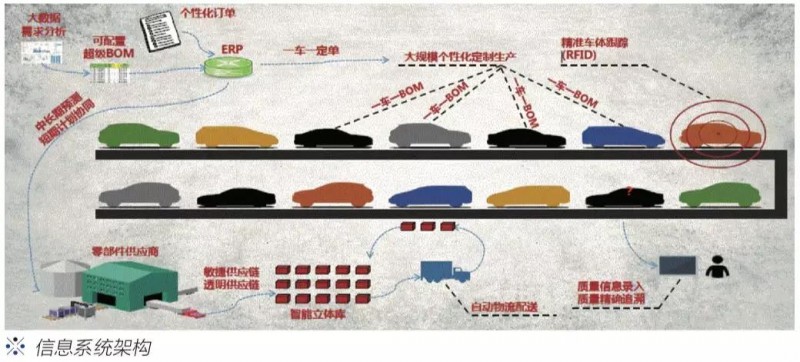
通過MES構(gòu)建透明工廠,實(shí)現(xiàn)基于制造全流程的產(chǎn)線、工位及作業(yè)節(jié)點(diǎn)的標(biāo)準(zhǔn)化和數(shù)字化;采用工業(yè)以太網(wǎng)和HMI技術(shù),實(shí)現(xiàn)設(shè)備互聯(lián);對(duì)生產(chǎn)計(jì)劃、質(zhì)量控制、防錯(cuò)、追溯進(jìn)行可視化管理;對(duì)整車生產(chǎn)制造過程中的工藝數(shù)據(jù)及參數(shù)信息進(jìn)行生命周期的數(shù)據(jù)管理。
創(chuàng)新開發(fā)的LES系統(tǒng)作為統(tǒng)一的物流執(zhí)行平臺(tái),整合了基于GPS定位技術(shù)的運(yùn)輸管理系統(tǒng)、JIS/JIT準(zhǔn)時(shí)化配送模式、基于RFID無(wú)線射頻技術(shù)的自動(dòng)化出入庫(kù)管理、自動(dòng)化立體庫(kù)、SPS系統(tǒng)、大件直送等自動(dòng)化上線技術(shù),從而實(shí)現(xiàn)了敏捷、透明的供應(yīng)鏈體系,能夠滿足8車型柔性化的生產(chǎn)物料需求,物流配送準(zhǔn)確率100%,供貨響應(yīng)時(shí)間縮短80%。
敏捷透明化的供應(yīng)鏈
1.循環(huán)取貨規(guī)劃
50%以上的供應(yīng)商集中在江浙滬。限于工廠所處位置以及北京市政規(guī)劃,寶沃汽車周邊無(wú)法設(shè)立配套零部件產(chǎn)業(yè)園。在此條件下,要想降低物流運(yùn)輸成本和零件庫(kù)存成本,節(jié)省庫(kù)區(qū)面積,實(shí)現(xiàn)零件全過程在途監(jiān)控,實(shí)施全國(guó)循環(huán)取貨對(duì)于提升供應(yīng)鏈效率、降低成本顯得十分必要。因此,寶沃汽車制定了詳細(xì)的循環(huán)取貨機(jī)制,并在逐步實(shí)施:
對(duì)于供貨距離60公里以內(nèi)的本地供應(yīng)商,直送到工廠;
供貨距離300公里以內(nèi)的京津冀供應(yīng)商,優(yōu)先循環(huán)取貨到工廠;
供貨距離1500公里以內(nèi)的華東、東北供應(yīng)商,優(yōu)先循環(huán)取貨到工廠/VMI庫(kù);
供貨距離1500公里以上的其他供應(yīng)商,占比很小,條件具備的循環(huán)取貨。
2.創(chuàng)新的TWD物料拉動(dòng)模式
傳統(tǒng)的物料拉動(dòng)模式依賴于現(xiàn)場(chǎng)作業(yè)人員,拉動(dòng)方式粗放,異常頻發(fā),供應(yīng)商裝載率低,道口/叉車作業(yè)不均衡;寶沃汽車已經(jīng)對(duì)119家供應(yīng)商推廣實(shí)施了TWD(層級(jí)拉動(dòng))模式,由信息系統(tǒng)替代人工,實(shí)行MIN/MAX/車輛過點(diǎn)拉動(dòng),時(shí)間窗合理均衡排布,最終供應(yīng)商裝載率、整體物流效率均大幅度提升。
3.智能入廠協(xié)同
受限于廠房面積,寶沃汽車需要嚴(yán)格控制供應(yīng)商零部件的入廠時(shí)間,在時(shí)間和空間調(diào)度上做的更為精細(xì)。為此,通過ETCP、微信、RFID、LES多系統(tǒng)協(xié)作,實(shí)現(xiàn)了車輛即時(shí)掃描、即時(shí)排隊(duì),保證了入廠車輛均衡穩(wěn)定,提高了50%作業(yè)效率。整套系統(tǒng)為業(yè)內(nèi)首創(chuàng)。
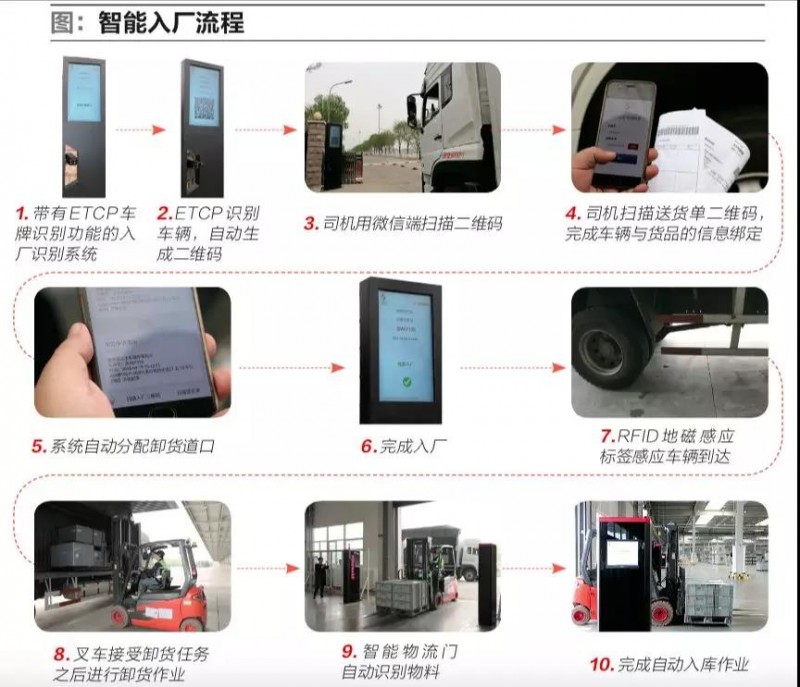
具體作業(yè)流程是:卡車到達(dá)廠區(qū)門口,ETCP車牌自動(dòng)識(shí)別系統(tǒng)識(shí)別卡車車牌,并記錄卡車出入廠時(shí)間;司機(jī)登錄微信公眾號(hào),掃描送貨單,送貨單與卡車信息完成綁定;司機(jī)掃描門口顯示屏上的二維碼,系統(tǒng)自動(dòng)分配車位;車輛進(jìn)入指定區(qū)域等待,系統(tǒng)提示卸貨時(shí)間,車輛到達(dá)卸貨口;在每個(gè)卸貨道口均裝有RFID地磁感應(yīng)標(biāo)簽,該標(biāo)簽可以自動(dòng)識(shí)別車位占用及釋放情況,進(jìn)行卸貨時(shí)間統(tǒng)計(jì)以及超時(shí)預(yù)警提示;車輛到達(dá)卸貨道口,通過系統(tǒng)提示車載電腦并完成卸貨作業(yè)。LES系統(tǒng)預(yù)提示空箱返空作業(yè),并可統(tǒng)計(jì)卡車在廠時(shí)間。
4.透明供應(yīng)鏈
曹曉剛提到,汽車產(chǎn)品更新?lián)Q代很快,庫(kù)存越多損失越大。為了降低供應(yīng)鏈上整體庫(kù)存,保證及時(shí)供應(yīng),避免斷貨情況,寶沃汽車將通過透明供應(yīng)鏈管理把所有的庫(kù)存和成本都實(shí)現(xiàn)目視化,帶動(dòng)整個(gè)產(chǎn)業(yè)鏈升級(jí)。
通過SAP、LES、TMS系統(tǒng)協(xié)作,實(shí)現(xiàn)供應(yīng)商零部件從出廠到寶沃工廠全過程覆蓋,實(shí)現(xiàn)低成本、高效率、高協(xié)同、透明化的供應(yīng)物流模式。將LES系統(tǒng)管理范圍從工廠擴(kuò)展到VMI庫(kù)甚至是零部件供應(yīng)商,實(shí)現(xiàn)供應(yīng)鏈全過程信息系統(tǒng)管理,同時(shí)與庫(kù)存預(yù)警相結(jié)合,保證零件及時(shí)供應(yīng)。
5.實(shí)施大數(shù)據(jù)管理
寶沃汽車與微軟(Microsoft)合作,定制化開發(fā)了寶沃汽車的LES,目前已完成兩期建設(shè),完全可以支持多車型柔性化的物流及供應(yīng)鏈業(yè)務(wù)需求。通過建立PFEP(Plan For Every Parts)數(shù)據(jù)體系,打造物流大數(shù)據(jù)系統(tǒng)。將零件信息、供應(yīng)鏈物流信息、倉(cāng)儲(chǔ)信息、供應(yīng)商信息、包裝信息、線邊信息等資源不斷進(jìn)行整合優(yōu)化,將所有的信息化設(shè)備和系統(tǒng)都與大數(shù)據(jù)系統(tǒng)關(guān)聯(lián),并進(jìn)行大數(shù)據(jù)分析。
6. 循環(huán)環(huán)保包裝應(yīng)用
寶沃汽車推動(dòng)零部件物流全程應(yīng)用循環(huán)圍板箱,尺寸規(guī)格標(biāo)準(zhǔn),便于倉(cāng)儲(chǔ)、運(yùn)輸?shù)龋岣吡宋锪餍?;比采用金屬料架成本低;頂蓋、底托為HDPE(低壓高密度聚乙烯),圍板為PP(聚丙烯)蜂窩板,材料環(huán)保。
智慧物流系統(tǒng)及裝備
智慧物流系統(tǒng)與裝備的創(chuàng)新應(yīng)用是滿足生產(chǎn)需求、保證物流效率的有效舉措。曹曉剛坦言,想要滿足8個(gè)車型的高效率混線生產(chǎn)對(duì)物流所帶來(lái)的壓力非常大。在寶沃汽車高層領(lǐng)導(dǎo)對(duì)物流系統(tǒng)建設(shè)的重視與支持下,經(jīng)過不斷的探索與實(shí)踐,目前部分智慧物流系統(tǒng)及裝備已經(jīng)投入應(yīng)用,還有部分項(xiàng)目正在實(shí)施。
1.SPS智能揀選系統(tǒng)
SPS智能揀選系統(tǒng)在汽車行業(yè)得到了普遍應(yīng)用,但是寶沃汽車的SPS智能揀選系統(tǒng)有著獨(dú)特的創(chuàng)新點(diǎn),極度彰顯了柔性化和智能化特點(diǎn)。
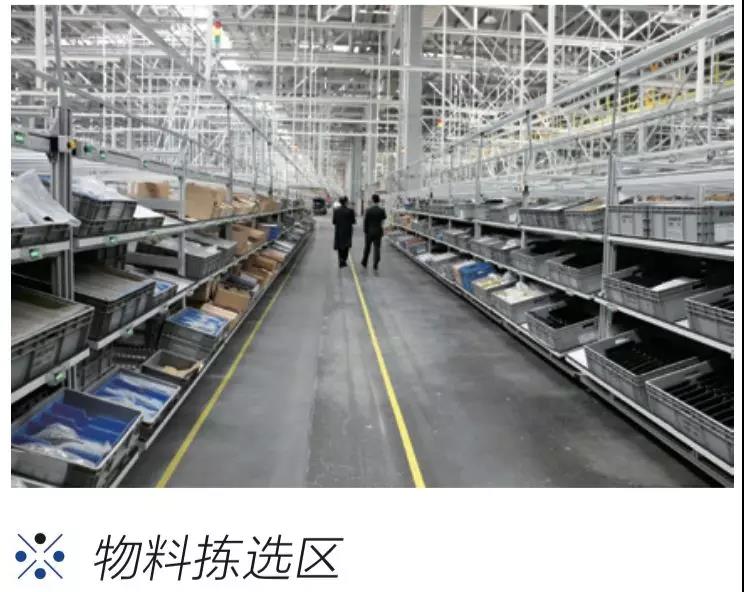
硬件方面,料架依據(jù)人體工程學(xué)設(shè)計(jì),選用輕量化鋁合金材質(zhì),采用方便、柔性化的標(biāo)準(zhǔn)件拼裝。整個(gè)系統(tǒng)中還應(yīng)用了紅外體感式指示燈、掃碼設(shè)備、車載電腦、穿戴設(shè)備、AGV等大量的先進(jìn)硬件設(shè)備,。
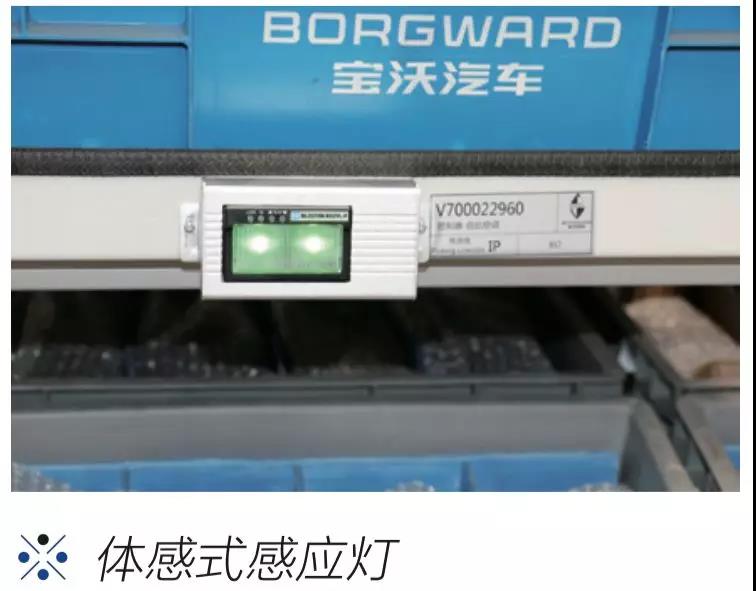
軟件方面,業(yè)內(nèi)首家通過LES、PTL系統(tǒng)的深度交互,可以滿足8車型柔性化的智能揀貨作業(yè)指示;首創(chuàng)投料防錯(cuò)功能,通過穿戴掃描設(shè)備和貨架上安裝的紅外體感式指示燈,確保投料準(zhǔn)確性;整個(gè)系統(tǒng)采用并聯(lián)模式,以每個(gè)貨格為一個(gè)單元,可以按照需求調(diào)整零部件存放位置,以滿足不斷增加的新車型生產(chǎn)需求;使用AGV智能調(diào)度系統(tǒng),不同路段運(yùn)行速度可調(diào),可優(yōu)化AGV數(shù)量。
整個(gè)系統(tǒng)的使用,減少了線邊面積占用,降低了人員作業(yè)強(qiáng)度,使揀選和投料作業(yè)準(zhǔn)確率高達(dá)100%。
2.無(wú)線射頻識(shí)別技術(shù)(RFID)
在寶沃汽車工廠中,可以看到大量的RFID技術(shù)應(yīng)用。如,所有的周轉(zhuǎn)包裝器具上都將裝有具備抗金屬干擾、抗沖擊特性的RFID標(biāo)簽;在物料入廠檢收、入庫(kù)以及出庫(kù)等所有物流環(huán)節(jié)都將應(yīng)用RFID智能物流門,智能物流門能夠快速批量讀取零件包裝上的RFID標(biāo)簽數(shù)據(jù),信息讀取準(zhǔn)確率高達(dá)99.99%,還能實(shí)現(xiàn)無(wú)人化作業(yè);在高位貨架及動(dòng)態(tài)庫(kù)位環(huán)節(jié)應(yīng)用RFID車載模塊,可實(shí)現(xiàn)庫(kù)位自動(dòng)校驗(yàn),出入庫(kù)準(zhǔn)確率達(dá)100%。以包裝箱為單位的RFID技術(shù)創(chuàng)新應(yīng)用,實(shí)現(xiàn)了整個(gè)供應(yīng)鏈過程透明、可追溯。

寶沃汽車成為業(yè)內(nèi)首批實(shí)現(xiàn)汽車行業(yè)供應(yīng)鏈RFID技術(shù)集成應(yīng)用的企業(yè),創(chuàng)造了多項(xiàng)專利技術(shù),最終將打造出無(wú)人化、透明化的物流體系,今后通過配合無(wú)人機(jī)的使用還可以實(shí)現(xiàn)庫(kù)存無(wú)人化盤點(diǎn)。這為寶沃汽車工業(yè)4.0工廠實(shí)現(xiàn)自動(dòng)化、智能化生產(chǎn)與物流提供了強(qiáng)大助力。
3.AGV廠內(nèi)物料配送
在廠內(nèi)物流配送環(huán)節(jié),大規(guī)模使用AGV代替叉車或牽引車作業(yè),大幅提高物流作業(yè)自動(dòng)化率。車間內(nèi)行駛的AGV搭載多臺(tái)套料架配送,配合SPS系統(tǒng),實(shí)現(xiàn)了總裝車間、車身車間內(nèi)智能化物料配送;目前寶沃還在研究應(yīng)用激光導(dǎo)航AGV搭載標(biāo)準(zhǔn)包裝、器具,完成車身料架工序間轉(zhuǎn)運(yùn)以及RDC向總裝車間配送,預(yù)計(jì)于未來(lái)兩年內(nèi)投入使用。
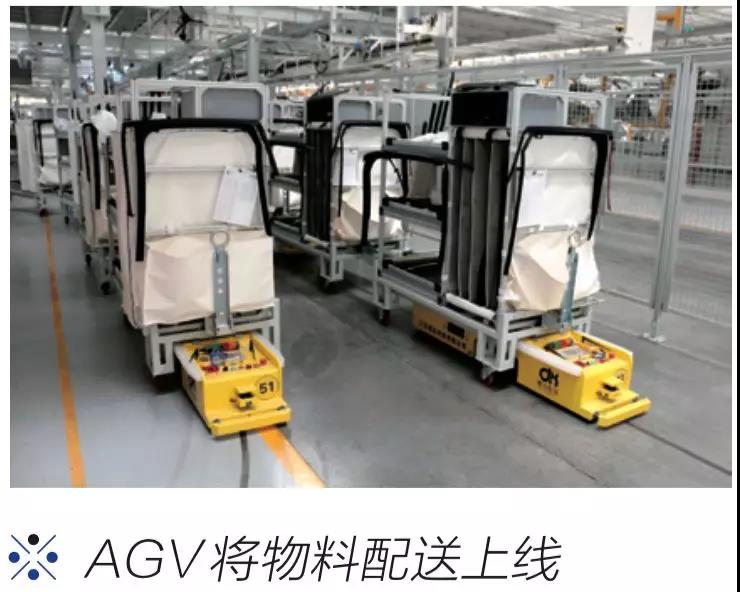
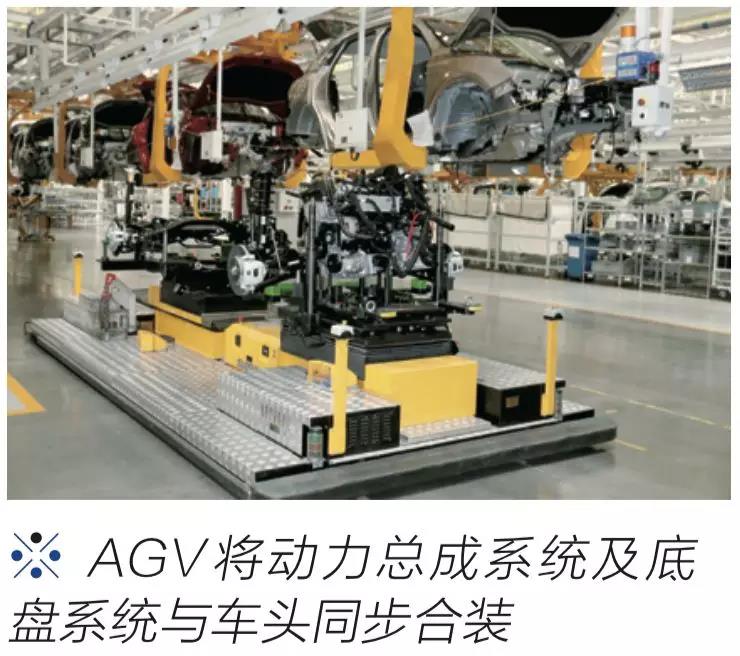
4.自動(dòng)化立體庫(kù)
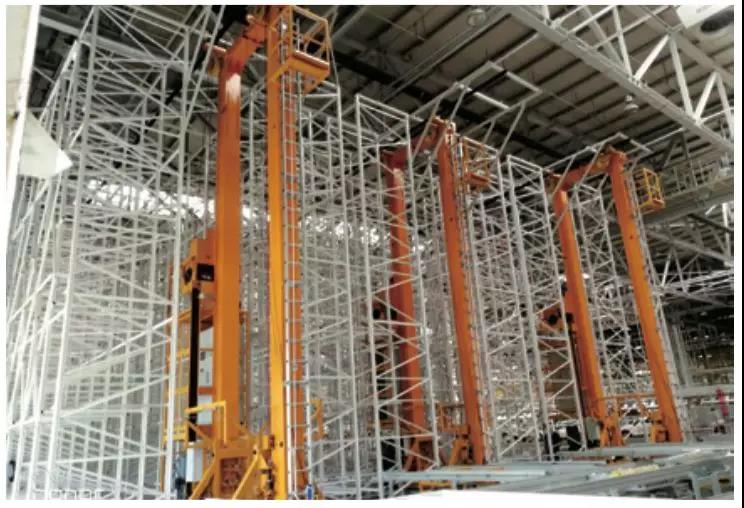
(1)座椅立體庫(kù)
由于座椅供應(yīng)商距離寶沃汽車工廠距離較遠(yuǎn),且座椅種類多,庫(kù)存管理難度高。經(jīng)過嚴(yán)密考量,寶沃汽車發(fā)現(xiàn)無(wú)論是從成本、準(zhǔn)確率還是效率方面考慮,在工廠內(nèi)建設(shè)座椅立體庫(kù)是最合適的選擇。因此,寶沃汽車也成為了業(yè)內(nèi)首家應(yīng)用座椅立體庫(kù)的企業(yè)。
整個(gè)立體庫(kù)有3個(gè)巷道,1200個(gè)貨位,使用高速堆垛機(jī)完成座椅的出入庫(kù)、排序上線及庫(kù)存管理等功能。在座椅翻包環(huán)節(jié)創(chuàng)新性采用了360度旋轉(zhuǎn)的AGV,極大降低了機(jī)械機(jī)構(gòu)的設(shè)計(jì)和制作難度。立體庫(kù)作業(yè)能力可達(dá)90JPH,全部通過WCS系統(tǒng)管理,最大程度保障了座椅供應(yīng)的柔性化和準(zhǔn)時(shí)性。
(2)料箱立體庫(kù)
在寶沃汽車的方案設(shè)計(jì)中,由料箱包裝的物料入庫(kù)后將被直接放置到入庫(kù)道口,由一臺(tái)機(jī)器臂抓取放到輸送鏈上,自動(dòng)輸送入庫(kù);立體庫(kù)系統(tǒng)與LES系統(tǒng)對(duì)接,LES下達(dá)出庫(kù)任務(wù)后,立體庫(kù)自動(dòng)將物料下架并分配到相應(yīng)道口,由機(jī)械手或者人放到AGV小車,完成配送。一期項(xiàng)目中主要實(shí)施自動(dòng)化立體庫(kù),規(guī)劃貨位數(shù)量8000個(gè),可兼容6種不同規(guī)格的箱型,零部件種類達(dá)2000多種。
通過料箱自動(dòng)化立體庫(kù)的應(yīng)用,重點(diǎn)零部件可由自動(dòng)立體庫(kù)完成出入庫(kù)、分揀作業(yè),倉(cāng)儲(chǔ)能力提升5倍,分揀效率提升2倍;該自動(dòng)化立體庫(kù)將接RFID、SPS、自動(dòng)化配送項(xiàng)目,實(shí)現(xiàn)互聯(lián)互通,完成基礎(chǔ)廠內(nèi)物流的自動(dòng)化平臺(tái)搭建。
未來(lái)發(fā)展規(guī)劃
隨著智能制造的不斷推進(jìn),汽車企業(yè)越來(lái)越重視搭建自動(dòng)化與智能化物流體系,逐步加大投入。而寶沃汽車在智慧供應(yīng)鏈及物流系統(tǒng)建設(shè)方面積極探索,勇于創(chuàng)新,已有多項(xiàng)應(yīng)用成果落地,無(wú)疑走在了行業(yè)發(fā)展前列。但寶沃汽車在智慧物流體系方面的建設(shè)絕不止于此。
寶沃汽車計(jì)劃到2020年初步建成智能化物流體系。為了實(shí)現(xiàn)這一目標(biāo),公司已經(jīng)制定了三步走戰(zhàn)略:第一階段,完成標(biāo)準(zhǔn)化打造;第二階段,實(shí)現(xiàn)自動(dòng)化/省人化;第三階段實(shí)現(xiàn)無(wú)人化/智能化。
曹曉剛表示,目前國(guó)內(nèi)汽車產(chǎn)業(yè)上下游的物流自動(dòng)化水平普遍較低,物流成本占比相當(dāng)高。伴隨著中國(guó)制造產(chǎn)業(yè)的不斷升級(jí),以及汽車行業(yè)競(jìng)爭(zhēng)的不斷加劇,發(fā)展智能物流必將被越來(lái)越多的汽車制造廠和零部件供應(yīng)商重視。寶沃汽車高層十分重視和支持智能制造的建設(shè),寶沃也將繼續(xù)下大力氣進(jìn)行研發(fā)和實(shí)踐,希望能夠在智能物流領(lǐng)域的探索中為行業(yè)做出一些貢獻(xiàn)。
編輯推薦
最新資訊
-
跨越速運(yùn)憑什么“圈粉”萬(wàn)千客戶?“
2025-07-01 14:42
-
數(shù)智破局啟新篇?生態(tài)共生再啟程 —
2025-06-27 20:13
-
助力汽車零部件產(chǎn)線智能化升級(jí),西門
2025-06-27 13:59
-
BBA集體轉(zhuǎn)向!放棄全面電動(dòng)化
2025-06-26 17:32
-
比換柜省錢,比自研省心,西門子Xcel
2025-06-25 15:07