簡(jiǎn)單分析汽車用鋼板電阻點(diǎn)焊工藝參數(shù)優(yōu)化選擇
2018-01-26 17:32:24· 來(lái)源:焊接技術(shù)
電阻點(diǎn)焊是汽車制造行業(yè)中最普遍的連接方式。微型汽車車身共有5000多個(gè)焊點(diǎn),分布在車身地板、頂蓋、前車體等部位,在發(fā)生碰撞時(shí)不同區(qū)域承擔(dān)了吸能、連接、承托等功能。
摘要:焊裝車間多采用多層板搭接進(jìn)行電阻電焊,而電阻電焊過(guò)程的不確定因素較多。為了用較少的試驗(yàn)次數(shù)得到滿足生產(chǎn)要求的試驗(yàn)結(jié)果,以板厚0.8mm+1.4mm+1.8mm的三層低碳鋼板搭接為研究對(duì)象,分析各因素對(duì)多層板材搭接焊點(diǎn)熔核質(zhì)量的影響,獲得了最優(yōu)焊接工藝參數(shù)。試驗(yàn)結(jié)果表明:板厚為0.8mm+1.4mm+1.8mm的三層低碳鋼板搭接最佳焊接工藝參數(shù)為多脈沖軟規(guī)范焊接參數(shù),即三周波,焊接電流8.8/11.1/9.6kA、焊接時(shí)間5/19/5cyc、電極壓力3kN,得到各層搭接板之間熔核直徑大于等于Φ6mm.
前言
電阻點(diǎn)焊是汽車制造行業(yè)中最普遍的連接方式。微型汽車車身共有5000多個(gè)焊點(diǎn),分布在車身地板、頂蓋、前車體等部位,在發(fā)生碰撞時(shí)不同區(qū)域承擔(dān)了吸能、連接、承托等功能。
實(shí)際應(yīng)用中需要將不同厚度、材料的鋼板進(jìn)行點(diǎn)焊連接,同一工位會(huì)出現(xiàn)不同強(qiáng)度、厚度的兩層板或三層板搭接,目前的電阻點(diǎn)焊工藝參數(shù)很難適用于不同厚度的兩層/三層鋼板的連接.
在此以五菱宏光S生產(chǎn)線前車體區(qū)域 1 # 工位(該工位焊接左前大梁焊合件與前圍板焊合總成搭接)為研究對(duì)象,為五菱宏光S車型的不同搭接方式電阻點(diǎn)焊工藝參數(shù)優(yōu)化選擇提供新的思路和方法。
1試驗(yàn)材料和方法
采用小原品牌一體式電阻點(diǎn)焊機(jī)(型號(hào)ST21)額定功率180kV A,配套X型手工焊槍 (型號(hào)UXH-C9625) 進(jìn)行焊接,如圖1所示。
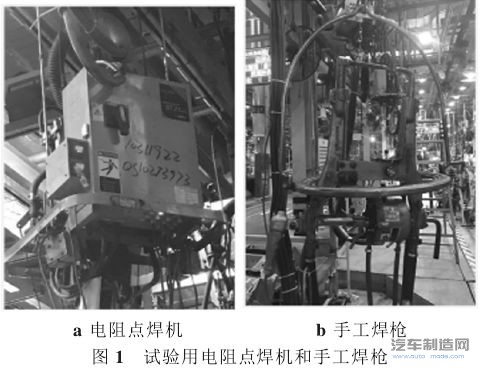
左前大梁和前圍板零件材料均為寶鋼牌號(hào)BLD低碳鋼板,試驗(yàn)用鋼板的化學(xué)成分如表1所示。
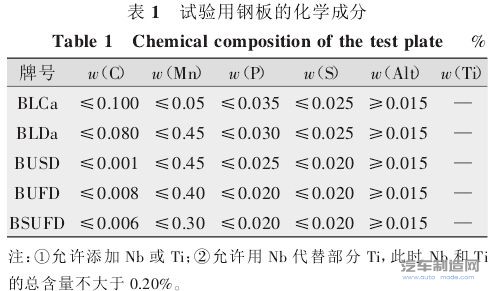
前大梁與前圍板搭接共11個(gè)焊點(diǎn),其中:兩層板搭接焊點(diǎn)10個(gè),板厚0.8mm+1.2mm;三層板搭接焊點(diǎn)1個(gè),板厚0.8mm+1.4mm+1.8mm。
首先選擇同樣汽車用鋼、厚度的試片模擬三層板搭接,使用不同的焊接工藝參數(shù)在三層板試片上進(jìn)行測(cè)試,獲取不同板厚下的工藝參數(shù),以確定符合技術(shù)要求的焊接工藝參數(shù)。
然后在左前大梁和前圍板連接區(qū)域進(jìn)行驗(yàn)證,獲得最終的工藝參數(shù)。根據(jù)搭接零件的主導(dǎo)板厚,參照《上汽通用五菱電阻點(diǎn)焊焊接參數(shù)推薦值》選擇試驗(yàn)用電阻點(diǎn)焊工藝參數(shù)。電阻點(diǎn)焊初始工藝參數(shù)如表2所示。
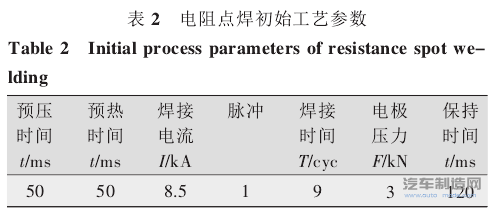
2 試驗(yàn)結(jié)果分析
2.1初始焊接工藝參數(shù)對(duì)焊接的影響
使用板材、厚度、工藝一致的3塊試片(0.8mm+1.4mm+1.8mm),根據(jù)表2的焊接工藝參數(shù),選擇電流8.5kA、電極壓力3kN、焊接時(shí)間9cyc進(jìn)行電阻點(diǎn)焊測(cè)試。焊點(diǎn)熔核尺寸如圖2所示。
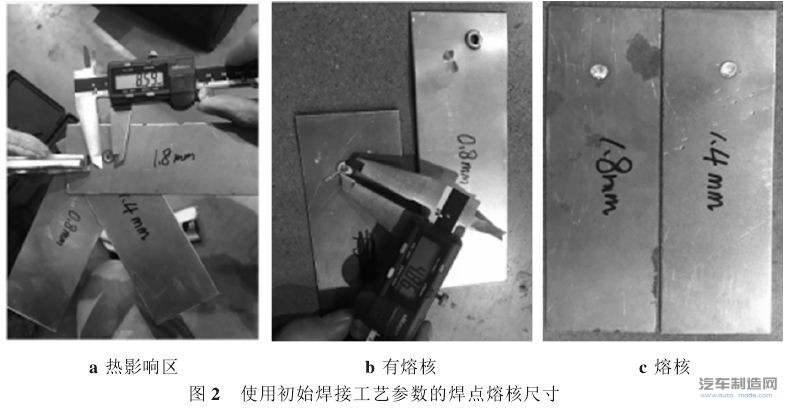
用游標(biāo)卡尺測(cè)量焊點(diǎn)熱影響區(qū)大小為8.59mm(見(jiàn)圖2a);將焊接試片撕裂后,0.8mm+1.4mm板材搭接處存在焊接熔核,熔核尺寸為4.86mm(見(jiàn)圖2b);但1.4mm+1.8mm板材搭接處未形成熔核,撕裂后焊點(diǎn)脆斷表面呈顆粒狀態(tài)(見(jiàn)圖2c).
試驗(yàn)結(jié)果表明,初始焊接工藝參數(shù)不適用于現(xiàn)場(chǎng)實(shí)際搭接狀態(tài),需要逐一調(diào)整焊接工藝參數(shù),使三層板材焊接均有符合要求的焊點(diǎn)熔核。
2.2左前大梁和前圍板連接區(qū)域點(diǎn)焊試驗(yàn)
影響試片焊點(diǎn)熔核尺寸的主要因素有焊接電流、焊接時(shí)間、電極壓力和脈沖,其他參數(shù)保持不變。本試驗(yàn)電極采用球形電極帽,端面尺寸Φ7mm,采取逐一對(duì)比方式進(jìn)行試驗(yàn),焊接工藝參數(shù)見(jiàn)表3.
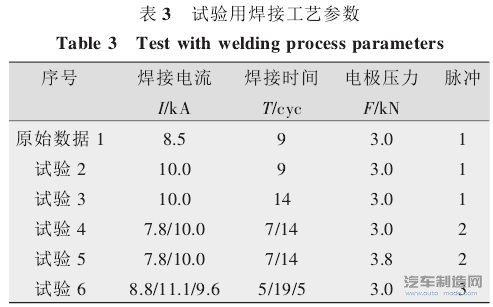
(1) 試驗(yàn)2。保持焊接時(shí)間和電極壓力不變,增加焊接電流至10.0kA(見(jiàn)表3)。試驗(yàn)2的熔核尺寸如圖3所示,將焊接試片撕裂后,0.8mm+1.4mm板材搭接處存在焊接熔核,尺寸Φ5.69mm,如圖3a所示;但1.4mm+1.8mm板材搭接處未形成熔核,撕裂后焊點(diǎn)脆斷表面呈顆粒狀態(tài)如圖3b所示。
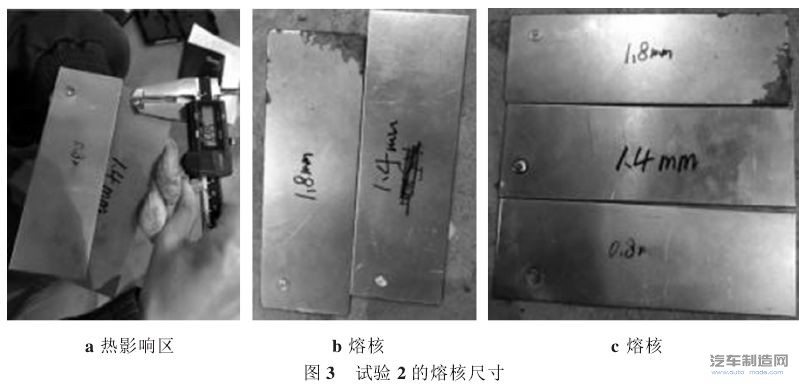
(2) 試驗(yàn)3。保持焊接電流為10.0kA,增加焊接時(shí)間到14cyc,電極壓力保持3.0kN(見(jiàn)表3)。試驗(yàn)3的熔核尺寸如圖4所示,將焊接試片撕裂后,0.8mm+1.4mm板材搭接處存在熔核,但1.4mm+1.8mm板材搭接處仍未形成熔核,且焊點(diǎn)脆斷表明呈顆粒狀態(tài),如圖4c所示。由于該板材三層板材厚度差異較大,焊接參數(shù)單項(xiàng)逐步增加已無(wú)法得到符合標(biāo)準(zhǔn)的焊點(diǎn)熔核,考慮選用2個(gè)焊接脈沖來(lái)增加焊接前的預(yù)熱焊接。
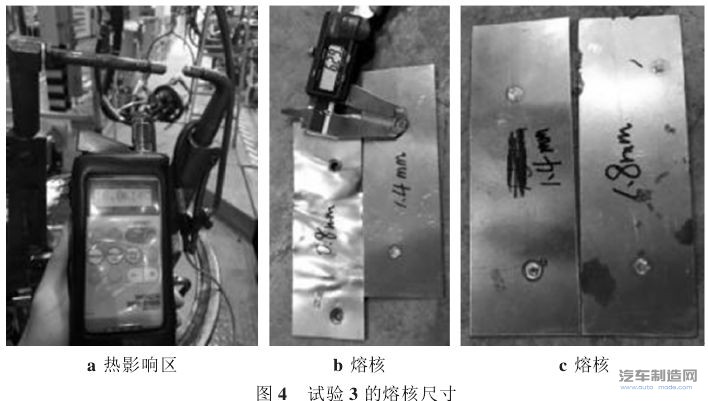
(3) 試驗(yàn)4。在前3個(gè)試驗(yàn)驗(yàn)證結(jié)果的基礎(chǔ)上,選用雙脈沖進(jìn)行試驗(yàn)。第一脈沖:焊接電流7.8kA焊接時(shí)間7cyc;第二脈沖:焊接電流10.0kA,焊接時(shí)間14cyc,電極壓力3.0kN保持不變(見(jiàn)表3)。焊接完成后,焊點(diǎn)熱影響區(qū)明顯變大,直徑為Φ9.6mm,如圖Sa所示;將焊接試片撕裂后,0.8mm+1.4mm板材搭接處存在焊接熔核,熔核尺寸為6.05mm,如圖5b所示;1.4mm+1.8mm板材搭接處未形成熔核,焊點(diǎn)脆斷表明呈顆粒狀態(tài),但承受剪切應(yīng)力明顯大
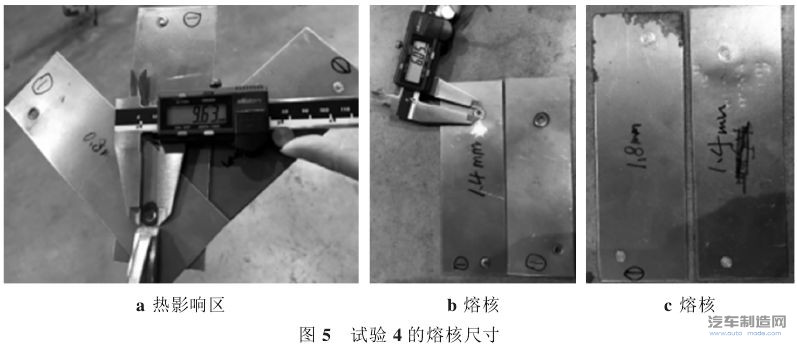
(4) 試驗(yàn)5。在試驗(yàn)4的基礎(chǔ)上,焊接電流、焊接時(shí)間保持不變,增加電極壓力至3.8kN進(jìn)行焊接試片驗(yàn)證(見(jiàn)表3)。焊點(diǎn)熱影響區(qū)尺寸Φ10.75mm已達(dá)到標(biāo)準(zhǔn)上限值,如圖6a所示;撕裂焊點(diǎn)后,0.8mm+1.4mm板材搭接處存在熔核且增大至Φ6.13mm,如圖5b所示;但1.4mm+1.8mm板材搭接處仍未形成明顯熔核,如圖5b所示;如果再單獨(dú)增加焊接電流、焊接時(shí)間或電極壓力,很難再產(chǎn)生明顯效果,且焊點(diǎn)熱影響區(qū)存在過(guò)燒風(fēng)險(xiǎn)。

(5)試驗(yàn)6。在試驗(yàn)5的基礎(chǔ)上,考慮到本工位焊點(diǎn)數(shù)量及生產(chǎn)節(jié)拍要求,選擇焊接參數(shù)中常用的軟規(guī)范,增大為三脈沖焊接參數(shù),增加了主焊接前的預(yù)熱過(guò)程和主焊接后的熔核保持過(guò)程(見(jiàn)表3)第1脈沖:焊接電流8.8kA,焊接時(shí)間5cyc;第2脈沖:焊接電流11.1kA,焊接時(shí)間19cyc;第3脈沖:焊接電流9.6kA,焊接時(shí)間5cyc;電極壓力保持為3.0kN。撕裂焊點(diǎn)后,0.8mm+1.4mm板材搭接存在焊接熔核,測(cè)量熔核尺寸為Φ6.19mm,如圖7a所示;
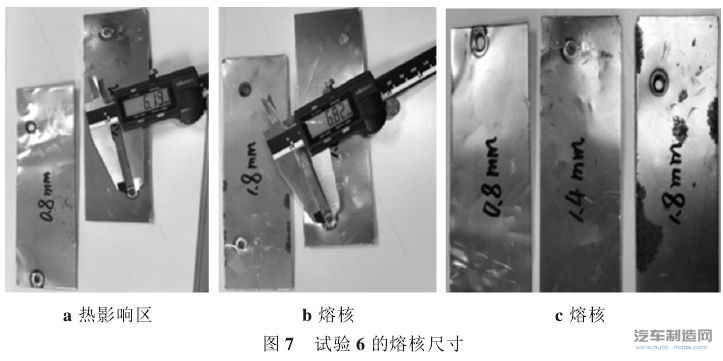
1.4mm+1.8mm板材搭接處存在明顯焊接熔核,熔核尺寸為Φ6.82mm,如圖7b,所示;在中間Φ側(cè)板材(1.4mm厚度)兩側(cè)均有明顯熔核,兩側(cè)板材(0.8mm和1.8mm厚度)存在明顯焊點(diǎn)撕裂的孔洞,如圖7c所示。板材焊點(diǎn)熔核質(zhì)量合格。
所有零件搭接實(shí)際工況均比焊接試片情況復(fù)雜,采取試驗(yàn)6數(shù)據(jù)在實(shí)車上進(jìn)行焊接實(shí)驗(yàn),用鐵錘和鑿子在三層板焊點(diǎn)處(0.8mm+1.4mm+1.8mm)進(jìn)行非破壞實(shí)驗(yàn),上下扳動(dòng)鑿子30°,焊點(diǎn)位置未發(fā)現(xiàn)虛焊,飯金表面無(wú)毛刺和裂紋,實(shí)車非破壞焊點(diǎn)質(zhì)量合格,如圖8所示。
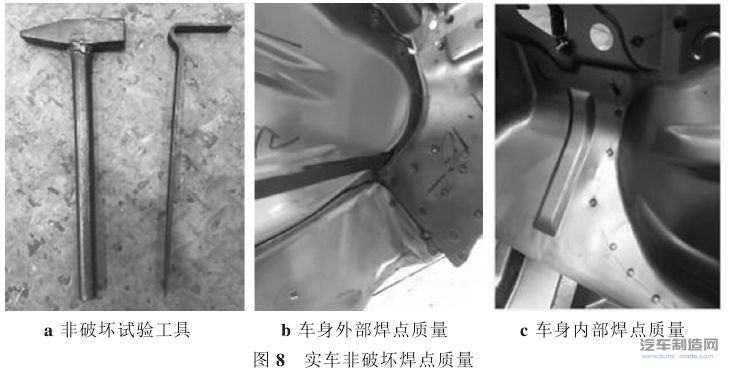
根據(jù)上汽通用五菱公司電阻點(diǎn)焊質(zhì)量要求,定期對(duì)該車型前車體區(qū)域焊點(diǎn)進(jìn)行全破壞實(shí)驗(yàn),大梁焊點(diǎn)兩側(cè)均有焊點(diǎn)熔核,兩側(cè)板材出現(xiàn)拉裂孔洞,焊點(diǎn)質(zhì)量合格,如圖9所示。
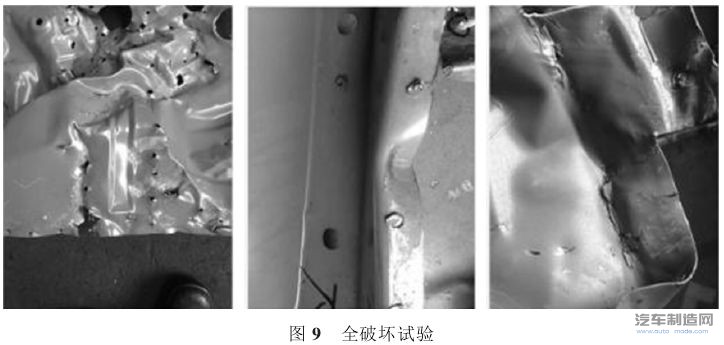
總 結(jié)
(1)獲得脈沖為1,2,3的電阻點(diǎn)焊熔核尺寸情況,綜合考慮三脈沖焊接參數(shù)為:焊接電流8.8/11.1/9.6kA、焊接時(shí)間5/19/5cyc、電極壓力3kN,獲得的各層搭接板之間熔核直徑大于等于6mm,適用于0.8mm+1.4mm+1.8mm厚度差異大的板材搭接點(diǎn)焊。
(二)以左前大梁和前圍板搭接為例,闡述了在兩層板與三層板搭接時(shí),應(yīng)優(yōu)先選擇適用于三層板搭接的焊接工藝參數(shù),解決了板材搭接的焊點(diǎn)熔核問(wèn)題,為其他汽車生產(chǎn)企業(yè)提供一種新的思路及方法。
前言
電阻點(diǎn)焊是汽車制造行業(yè)中最普遍的連接方式。微型汽車車身共有5000多個(gè)焊點(diǎn),分布在車身地板、頂蓋、前車體等部位,在發(fā)生碰撞時(shí)不同區(qū)域承擔(dān)了吸能、連接、承托等功能。
實(shí)際應(yīng)用中需要將不同厚度、材料的鋼板進(jìn)行點(diǎn)焊連接,同一工位會(huì)出現(xiàn)不同強(qiáng)度、厚度的兩層板或三層板搭接,目前的電阻點(diǎn)焊工藝參數(shù)很難適用于不同厚度的兩層/三層鋼板的連接.
在此以五菱宏光S生產(chǎn)線前車體區(qū)域 1 # 工位(該工位焊接左前大梁焊合件與前圍板焊合總成搭接)為研究對(duì)象,為五菱宏光S車型的不同搭接方式電阻點(diǎn)焊工藝參數(shù)優(yōu)化選擇提供新的思路和方法。
1試驗(yàn)材料和方法
采用小原品牌一體式電阻點(diǎn)焊機(jī)(型號(hào)ST21)額定功率180kV A,配套X型手工焊槍 (型號(hào)UXH-C9625) 進(jìn)行焊接,如圖1所示。
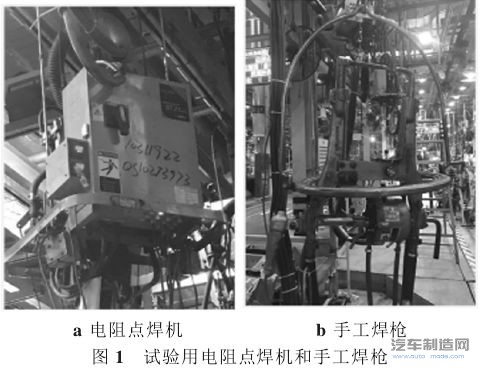
左前大梁和前圍板零件材料均為寶鋼牌號(hào)BLD低碳鋼板,試驗(yàn)用鋼板的化學(xué)成分如表1所示。
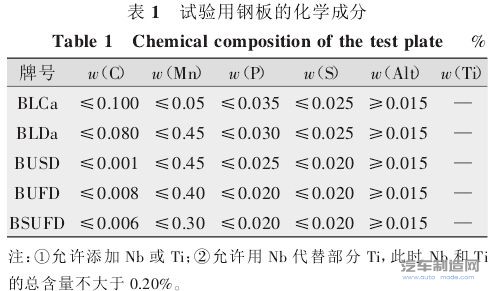
前大梁與前圍板搭接共11個(gè)焊點(diǎn),其中:兩層板搭接焊點(diǎn)10個(gè),板厚0.8mm+1.2mm;三層板搭接焊點(diǎn)1個(gè),板厚0.8mm+1.4mm+1.8mm。
首先選擇同樣汽車用鋼、厚度的試片模擬三層板搭接,使用不同的焊接工藝參數(shù)在三層板試片上進(jìn)行測(cè)試,獲取不同板厚下的工藝參數(shù),以確定符合技術(shù)要求的焊接工藝參數(shù)。
然后在左前大梁和前圍板連接區(qū)域進(jìn)行驗(yàn)證,獲得最終的工藝參數(shù)。根據(jù)搭接零件的主導(dǎo)板厚,參照《上汽通用五菱電阻點(diǎn)焊焊接參數(shù)推薦值》選擇試驗(yàn)用電阻點(diǎn)焊工藝參數(shù)。電阻點(diǎn)焊初始工藝參數(shù)如表2所示。
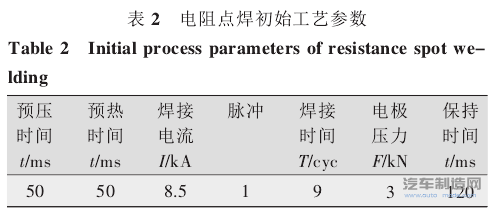
2 試驗(yàn)結(jié)果分析
2.1初始焊接工藝參數(shù)對(duì)焊接的影響
使用板材、厚度、工藝一致的3塊試片(0.8mm+1.4mm+1.8mm),根據(jù)表2的焊接工藝參數(shù),選擇電流8.5kA、電極壓力3kN、焊接時(shí)間9cyc進(jìn)行電阻點(diǎn)焊測(cè)試。焊點(diǎn)熔核尺寸如圖2所示。
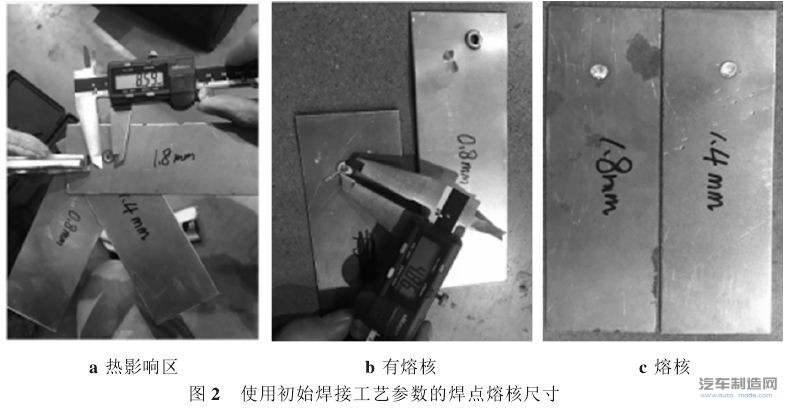
用游標(biāo)卡尺測(cè)量焊點(diǎn)熱影響區(qū)大小為8.59mm(見(jiàn)圖2a);將焊接試片撕裂后,0.8mm+1.4mm板材搭接處存在焊接熔核,熔核尺寸為4.86mm(見(jiàn)圖2b);但1.4mm+1.8mm板材搭接處未形成熔核,撕裂后焊點(diǎn)脆斷表面呈顆粒狀態(tài)(見(jiàn)圖2c).
試驗(yàn)結(jié)果表明,初始焊接工藝參數(shù)不適用于現(xiàn)場(chǎng)實(shí)際搭接狀態(tài),需要逐一調(diào)整焊接工藝參數(shù),使三層板材焊接均有符合要求的焊點(diǎn)熔核。
2.2左前大梁和前圍板連接區(qū)域點(diǎn)焊試驗(yàn)
影響試片焊點(diǎn)熔核尺寸的主要因素有焊接電流、焊接時(shí)間、電極壓力和脈沖,其他參數(shù)保持不變。本試驗(yàn)電極采用球形電極帽,端面尺寸Φ7mm,采取逐一對(duì)比方式進(jìn)行試驗(yàn),焊接工藝參數(shù)見(jiàn)表3.
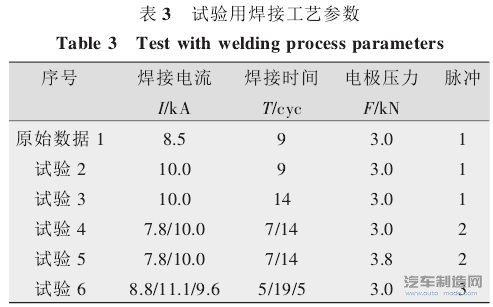
(1) 試驗(yàn)2。保持焊接時(shí)間和電極壓力不變,增加焊接電流至10.0kA(見(jiàn)表3)。試驗(yàn)2的熔核尺寸如圖3所示,將焊接試片撕裂后,0.8mm+1.4mm板材搭接處存在焊接熔核,尺寸Φ5.69mm,如圖3a所示;但1.4mm+1.8mm板材搭接處未形成熔核,撕裂后焊點(diǎn)脆斷表面呈顆粒狀態(tài)如圖3b所示。
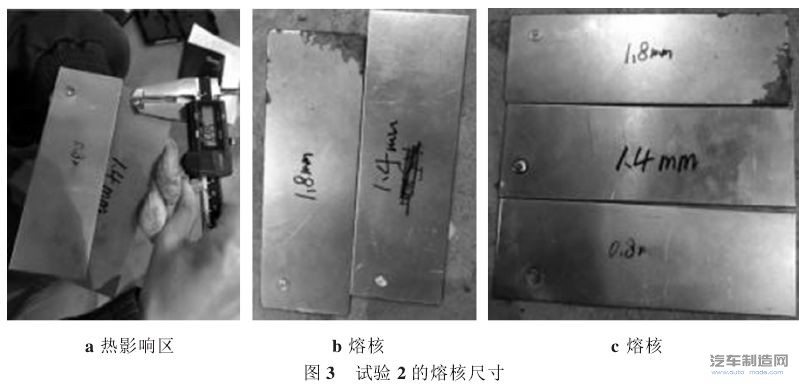
(2) 試驗(yàn)3。保持焊接電流為10.0kA,增加焊接時(shí)間到14cyc,電極壓力保持3.0kN(見(jiàn)表3)。試驗(yàn)3的熔核尺寸如圖4所示,將焊接試片撕裂后,0.8mm+1.4mm板材搭接處存在熔核,但1.4mm+1.8mm板材搭接處仍未形成熔核,且焊點(diǎn)脆斷表明呈顆粒狀態(tài),如圖4c所示。由于該板材三層板材厚度差異較大,焊接參數(shù)單項(xiàng)逐步增加已無(wú)法得到符合標(biāo)準(zhǔn)的焊點(diǎn)熔核,考慮選用2個(gè)焊接脈沖來(lái)增加焊接前的預(yù)熱焊接。
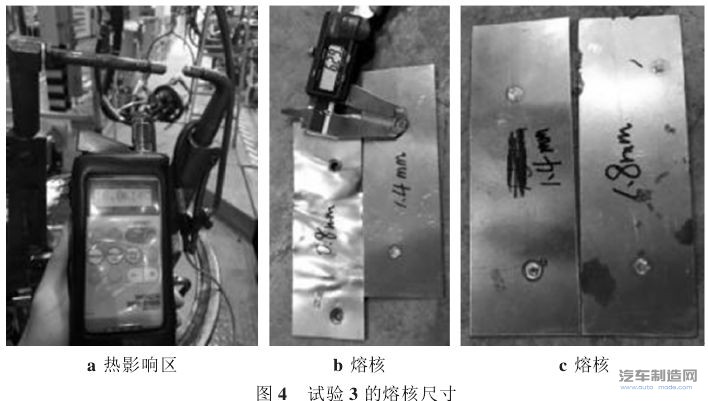
(3) 試驗(yàn)4。在前3個(gè)試驗(yàn)驗(yàn)證結(jié)果的基礎(chǔ)上,選用雙脈沖進(jìn)行試驗(yàn)。第一脈沖:焊接電流7.8kA焊接時(shí)間7cyc;第二脈沖:焊接電流10.0kA,焊接時(shí)間14cyc,電極壓力3.0kN保持不變(見(jiàn)表3)。焊接完成后,焊點(diǎn)熱影響區(qū)明顯變大,直徑為Φ9.6mm,如圖Sa所示;將焊接試片撕裂后,0.8mm+1.4mm板材搭接處存在焊接熔核,熔核尺寸為6.05mm,如圖5b所示;1.4mm+1.8mm板材搭接處未形成熔核,焊點(diǎn)脆斷表明呈顆粒狀態(tài),但承受剪切應(yīng)力明顯大
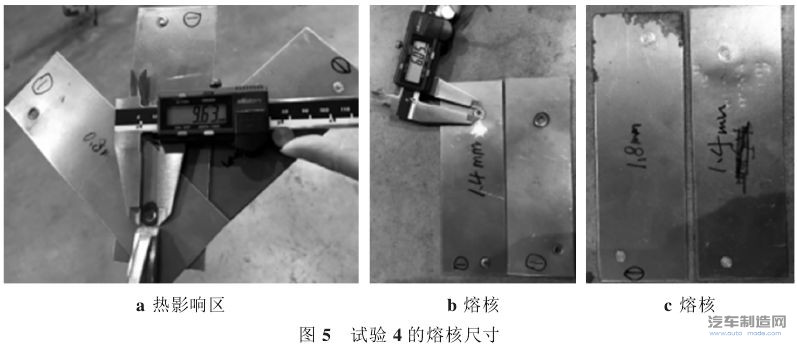
(4) 試驗(yàn)5。在試驗(yàn)4的基礎(chǔ)上,焊接電流、焊接時(shí)間保持不變,增加電極壓力至3.8kN進(jìn)行焊接試片驗(yàn)證(見(jiàn)表3)。焊點(diǎn)熱影響區(qū)尺寸Φ10.75mm已達(dá)到標(biāo)準(zhǔn)上限值,如圖6a所示;撕裂焊點(diǎn)后,0.8mm+1.4mm板材搭接處存在熔核且增大至Φ6.13mm,如圖5b所示;但1.4mm+1.8mm板材搭接處仍未形成明顯熔核,如圖5b所示;如果再單獨(dú)增加焊接電流、焊接時(shí)間或電極壓力,很難再產(chǎn)生明顯效果,且焊點(diǎn)熱影響區(qū)存在過(guò)燒風(fēng)險(xiǎn)。

(5)試驗(yàn)6。在試驗(yàn)5的基礎(chǔ)上,考慮到本工位焊點(diǎn)數(shù)量及生產(chǎn)節(jié)拍要求,選擇焊接參數(shù)中常用的軟規(guī)范,增大為三脈沖焊接參數(shù),增加了主焊接前的預(yù)熱過(guò)程和主焊接后的熔核保持過(guò)程(見(jiàn)表3)第1脈沖:焊接電流8.8kA,焊接時(shí)間5cyc;第2脈沖:焊接電流11.1kA,焊接時(shí)間19cyc;第3脈沖:焊接電流9.6kA,焊接時(shí)間5cyc;電極壓力保持為3.0kN。撕裂焊點(diǎn)后,0.8mm+1.4mm板材搭接存在焊接熔核,測(cè)量熔核尺寸為Φ6.19mm,如圖7a所示;
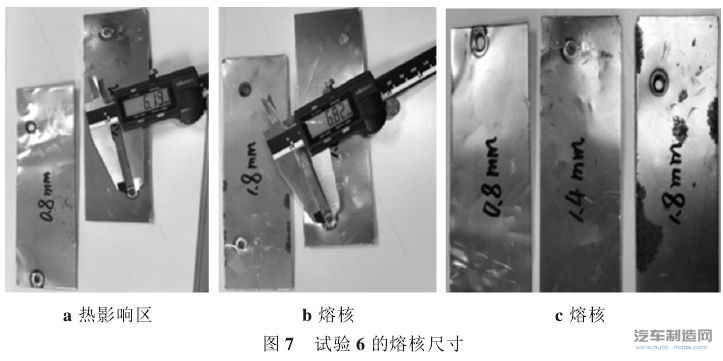
1.4mm+1.8mm板材搭接處存在明顯焊接熔核,熔核尺寸為Φ6.82mm,如圖7b,所示;在中間Φ側(cè)板材(1.4mm厚度)兩側(cè)均有明顯熔核,兩側(cè)板材(0.8mm和1.8mm厚度)存在明顯焊點(diǎn)撕裂的孔洞,如圖7c所示。板材焊點(diǎn)熔核質(zhì)量合格。
所有零件搭接實(shí)際工況均比焊接試片情況復(fù)雜,采取試驗(yàn)6數(shù)據(jù)在實(shí)車上進(jìn)行焊接實(shí)驗(yàn),用鐵錘和鑿子在三層板焊點(diǎn)處(0.8mm+1.4mm+1.8mm)進(jìn)行非破壞實(shí)驗(yàn),上下扳動(dòng)鑿子30°,焊點(diǎn)位置未發(fā)現(xiàn)虛焊,飯金表面無(wú)毛刺和裂紋,實(shí)車非破壞焊點(diǎn)質(zhì)量合格,如圖8所示。
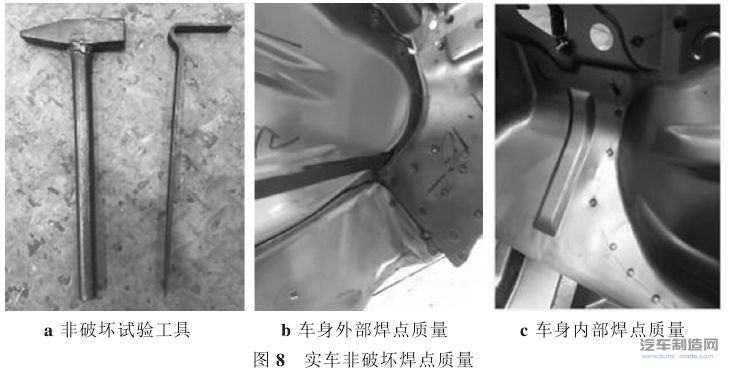
根據(jù)上汽通用五菱公司電阻點(diǎn)焊質(zhì)量要求,定期對(duì)該車型前車體區(qū)域焊點(diǎn)進(jìn)行全破壞實(shí)驗(yàn),大梁焊點(diǎn)兩側(cè)均有焊點(diǎn)熔核,兩側(cè)板材出現(xiàn)拉裂孔洞,焊點(diǎn)質(zhì)量合格,如圖9所示。
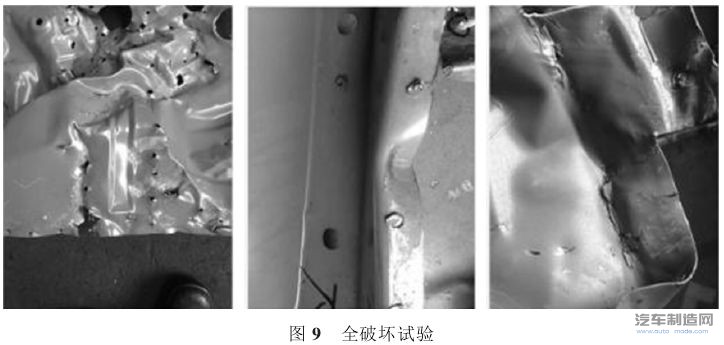
總 結(jié)
(1)獲得脈沖為1,2,3的電阻點(diǎn)焊熔核尺寸情況,綜合考慮三脈沖焊接參數(shù)為:焊接電流8.8/11.1/9.6kA、焊接時(shí)間5/19/5cyc、電極壓力3kN,獲得的各層搭接板之間熔核直徑大于等于6mm,適用于0.8mm+1.4mm+1.8mm厚度差異大的板材搭接點(diǎn)焊。
(二)以左前大梁和前圍板搭接為例,闡述了在兩層板與三層板搭接時(shí),應(yīng)優(yōu)先選擇適用于三層板搭接的焊接工藝參數(shù),解決了板材搭接的焊點(diǎn)熔核問(wèn)題,為其他汽車生產(chǎn)企業(yè)提供一種新的思路及方法。
編輯推薦
最新資訊
-
跨越速運(yùn)憑什么“圈粉”萬(wàn)千客戶?“
2025-07-01 14:42
-
數(shù)智破局啟新篇?生態(tài)共生再啟程 —
2025-06-27 20:13
-
助力汽車零部件產(chǎn)線智能化升級(jí),西門(mén)
2025-06-27 13:59
-
BBA集體轉(zhuǎn)向!放棄全面電動(dòng)化
2025-06-26 17:32
-
比換柜省錢(qián),比自研省心,西門(mén)子X(jué)cel
2025-06-25 15:07