汽車發(fā)動機缸體擴缸前后靜強度和模態(tài)分析(二)
2017-05-15 23:18:59·
本文利用HyperWorks軟件對此發(fā)動機缸體原方案與新方案的缸體靜態(tài)強度和模態(tài)進行分析。
4 缸體靜力分析
4.1 靜力分析結果
如圖5所示,其最大主應力發(fā)生在三缸上緣,大小為169.8Mpa。應力較大的地方有兩處,第一處在缸體上表面,第三缸周圍,主要由于此時第三剛爆發(fā),有19Mpa壓力作用在三缸上緣部分;第二處在第三、第四軸承座連接部分周圍的缸體部分,由于三缸爆發(fā),第三第四軸承座提供的支撐力十分大導致。
如圖6所示,此時原方案缸體最大位移為0.054mm。缸體變形區(qū)域與缸體所受應力較大區(qū)域類似。
如圖7所示,此時原方案缸套最大Mises應力為236.3Mpa。應力較大q區(qū)域為三缸套上緣及第二第四缸套靠近第三缸缸套的部分。三缸爆發(fā)時,其他缸內(nèi)壓力及活塞側(cè)推力都較小,所以缸套應力主要受第三缸爆發(fā)影響。
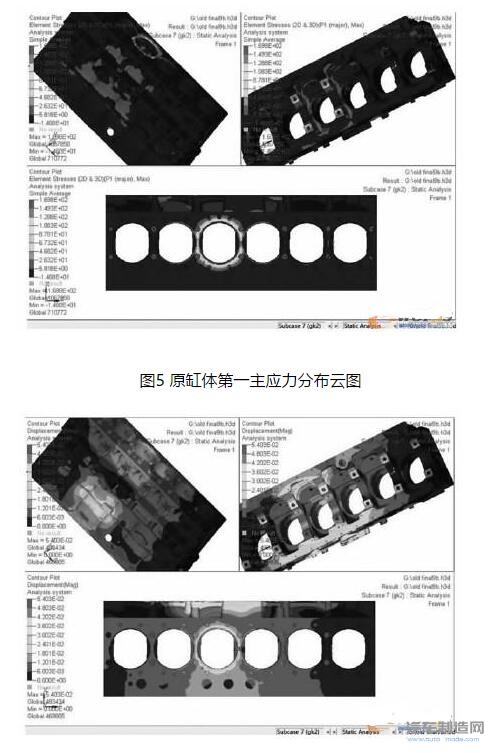
如圖8所示,此時原方案缸套最大位移量為0.02777mm。位處第三缸上緣部分。整體位移分布十分具有規(guī)律性,以三缸套上緣為起點向下和向兩側(cè)逐步減小。
如圖9所示,原方案軸承座最大Mises應力值為235.8Mpa,發(fā)生在螺栓預緊處。此處出現(xiàn)較大應力原因應該是施加螺栓預緊力時以集中力方式施加,出現(xiàn)應力集中所致。而除螺栓預緊處外,較大1、2、5、6、7號所受載荷較小的軸承座,應力從與缸體接觸面其逐步向下和中間部分減小。而3、4號軸承座,應力值在載荷施加處較大向其他區(qū)域逐步減小。
如圖10所示,此時原方案動機軸承座最大位移為0.09081mm。較大處為3、4號軸承座受載部分。
擴缸后發(fā)動機缸體靜力分析模型的受載形式與原方案一致,僅是載荷大小略有變化,因此應力分布及位移情況類似,以下結果不再描述。
如圖11所示,128mm缸徑新方案的缸體最大平均第一主應力值為165Mpa。如圖12所示,新方案缸體最大位移為0.07938mm。
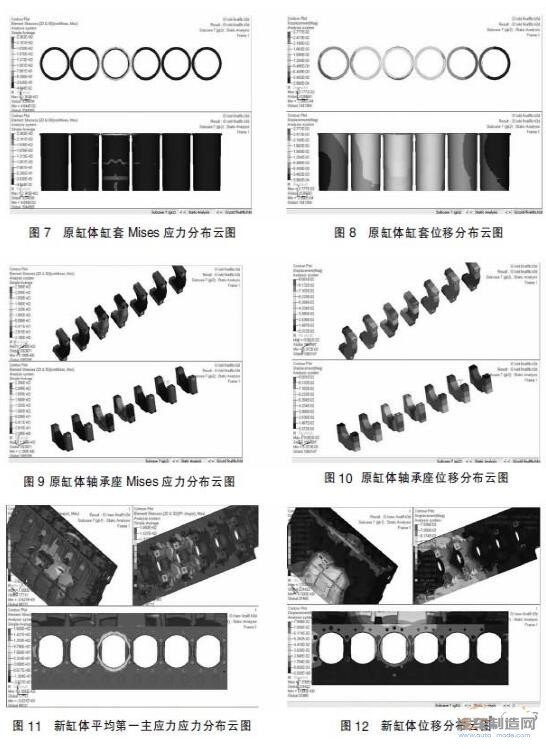
如圖13所示,新方案缸套最大Mises應力值為215.9Mpa。如圖14所示,新方案缸套最大位移為0.02477mm。
如圖15所示,新方案軸承座最大Mises應力為222.4Mpa。如圖16所示,新方案軸承座最大位移為0.125mm。
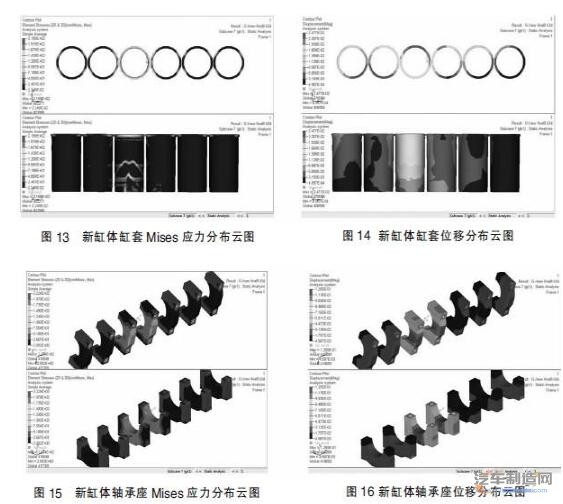
4.2 靜力分析匯總與分析
上述對123mm缸徑和128mm缸徑兩種發(fā)動機缸體進行了在第三缸爆發(fā)壓力最大這一極限工況的靜力分析求解。結果匯總?cè)绫?所示:
表5 靜力分析結果匯總
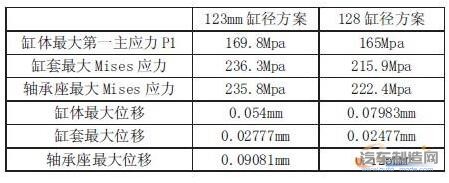
對于所關心的缸體最大第一主應力值,均為160Mpa以上。此值小于HT250的抗拉強度250Mpa,但引入安全系數(shù)的概念后,此值偏大。但考慮到新方案是在原缸體基礎上改進得到的,且新方案最大主應力值變化不大,且略有減小。故說明新缸體靜力分析強度符合要求。
從表中清晰可得,在同一發(fā)動機缸內(nèi)壓力變化曲線數(shù)據(jù)下,擴缸后發(fā)動機缸體、缸套最大應力值略微變小。缸體、軸承座最大位移略微變大。且最大應力均小于材料強度極限。但由于擴缸后,缸內(nèi)壓力曲線數(shù)據(jù)會發(fā)生變化,所以實際中略有差異。但是整體的分布形式應該變化不大,主要的危險區(qū)域,和較大位移區(qū)域不會發(fā)生改變。所得結果有一定參考價值。
在建立分析模型時,缸蓋部分由4層2.5mm的三棱柱單元代替,其材料選用較大的彈性模量。通過多次嘗試求解對比結果發(fā)現(xiàn),此彈性模量大小會導致缸體最大第一主應力值。具體規(guī)律是缸蓋部分單元彈性模量越大,缸體最大應力值越小。所以在缸體靜力分析中,缸蓋部分影響十分大。所以為得到更好結果,需要建立較為準確的缸蓋模型。
5 缸體模態(tài)分析
5.1 缸體模態(tài)分析的有限元模型
缸體模態(tài)分析的有限元模型,與靜力分析相比只選擇缸體部分,去掉缸套、缸蓋、等連接部分。
對于發(fā)動機缸體這種具有復雜幾何的模型,在Hypermesh網(wǎng)格劃分中,一般選用四面體單元。網(wǎng)格劃分思路一般為先生成高質(zhì)量2D網(wǎng)格單元,再向內(nèi)填充生成3D網(wǎng)格單元模型。
4.1 靜力分析結果
如圖5所示,其最大主應力發(fā)生在三缸上緣,大小為169.8Mpa。應力較大的地方有兩處,第一處在缸體上表面,第三缸周圍,主要由于此時第三剛爆發(fā),有19Mpa壓力作用在三缸上緣部分;第二處在第三、第四軸承座連接部分周圍的缸體部分,由于三缸爆發(fā),第三第四軸承座提供的支撐力十分大導致。
如圖6所示,此時原方案缸體最大位移為0.054mm。缸體變形區(qū)域與缸體所受應力較大區(qū)域類似。
如圖7所示,此時原方案缸套最大Mises應力為236.3Mpa。應力較大q區(qū)域為三缸套上緣及第二第四缸套靠近第三缸缸套的部分。三缸爆發(fā)時,其他缸內(nèi)壓力及活塞側(cè)推力都較小,所以缸套應力主要受第三缸爆發(fā)影響。
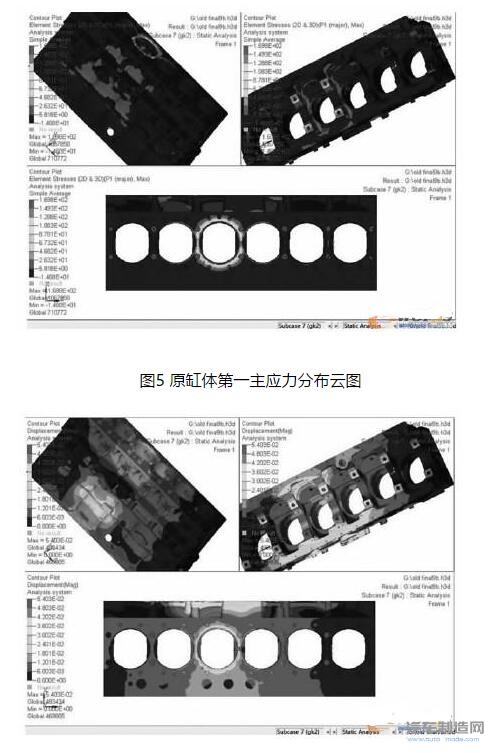
如圖8所示,此時原方案缸套最大位移量為0.02777mm。位處第三缸上緣部分。整體位移分布十分具有規(guī)律性,以三缸套上緣為起點向下和向兩側(cè)逐步減小。
如圖9所示,原方案軸承座最大Mises應力值為235.8Mpa,發(fā)生在螺栓預緊處。此處出現(xiàn)較大應力原因應該是施加螺栓預緊力時以集中力方式施加,出現(xiàn)應力集中所致。而除螺栓預緊處外,較大1、2、5、6、7號所受載荷較小的軸承座,應力從與缸體接觸面其逐步向下和中間部分減小。而3、4號軸承座,應力值在載荷施加處較大向其他區(qū)域逐步減小。
如圖10所示,此時原方案動機軸承座最大位移為0.09081mm。較大處為3、4號軸承座受載部分。
擴缸后發(fā)動機缸體靜力分析模型的受載形式與原方案一致,僅是載荷大小略有變化,因此應力分布及位移情況類似,以下結果不再描述。
如圖11所示,128mm缸徑新方案的缸體最大平均第一主應力值為165Mpa。如圖12所示,新方案缸體最大位移為0.07938mm。
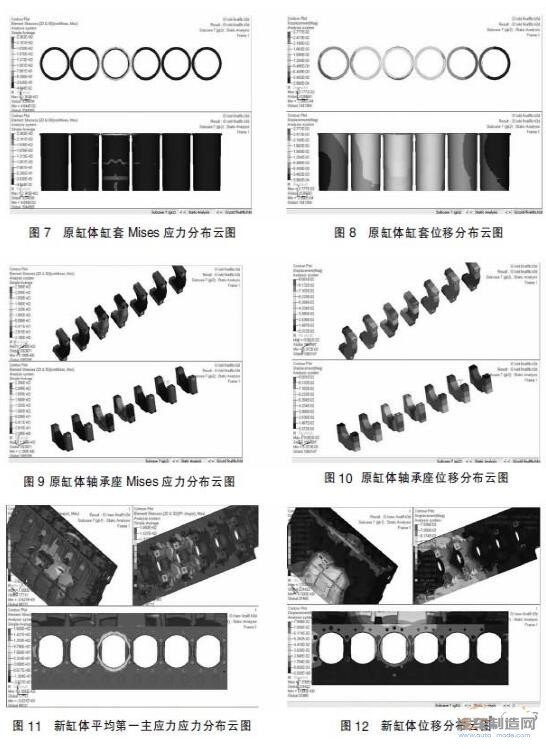
如圖13所示,新方案缸套最大Mises應力值為215.9Mpa。如圖14所示,新方案缸套最大位移為0.02477mm。
如圖15所示,新方案軸承座最大Mises應力為222.4Mpa。如圖16所示,新方案軸承座最大位移為0.125mm。
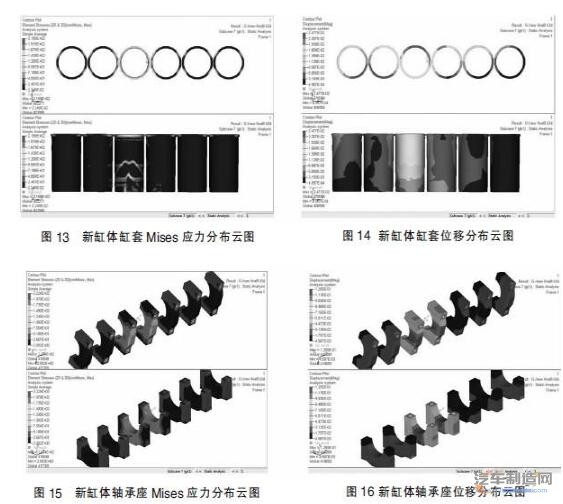
4.2 靜力分析匯總與分析
上述對123mm缸徑和128mm缸徑兩種發(fā)動機缸體進行了在第三缸爆發(fā)壓力最大這一極限工況的靜力分析求解。結果匯總?cè)绫?所示:
表5 靜力分析結果匯總
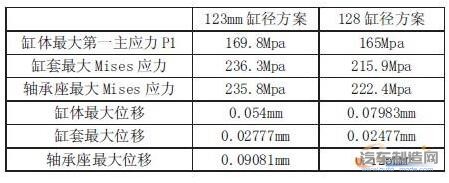
對于所關心的缸體最大第一主應力值,均為160Mpa以上。此值小于HT250的抗拉強度250Mpa,但引入安全系數(shù)的概念后,此值偏大。但考慮到新方案是在原缸體基礎上改進得到的,且新方案最大主應力值變化不大,且略有減小。故說明新缸體靜力分析強度符合要求。
從表中清晰可得,在同一發(fā)動機缸內(nèi)壓力變化曲線數(shù)據(jù)下,擴缸后發(fā)動機缸體、缸套最大應力值略微變小。缸體、軸承座最大位移略微變大。且最大應力均小于材料強度極限。但由于擴缸后,缸內(nèi)壓力曲線數(shù)據(jù)會發(fā)生變化,所以實際中略有差異。但是整體的分布形式應該變化不大,主要的危險區(qū)域,和較大位移區(qū)域不會發(fā)生改變。所得結果有一定參考價值。
在建立分析模型時,缸蓋部分由4層2.5mm的三棱柱單元代替,其材料選用較大的彈性模量。通過多次嘗試求解對比結果發(fā)現(xiàn),此彈性模量大小會導致缸體最大第一主應力值。具體規(guī)律是缸蓋部分單元彈性模量越大,缸體最大應力值越小。所以在缸體靜力分析中,缸蓋部分影響十分大。所以為得到更好結果,需要建立較為準確的缸蓋模型。
5 缸體模態(tài)分析
5.1 缸體模態(tài)分析的有限元模型
缸體模態(tài)分析的有限元模型,與靜力分析相比只選擇缸體部分,去掉缸套、缸蓋、等連接部分。
對于發(fā)動機缸體這種具有復雜幾何的模型,在Hypermesh網(wǎng)格劃分中,一般選用四面體單元。網(wǎng)格劃分思路一般為先生成高質(zhì)量2D網(wǎng)格單元,再向內(nèi)填充生成3D網(wǎng)格單元模型。
編輯推薦
最新資訊
-
跨越速運憑什么“圈粉”萬千客戶?“
2025-07-01 14:42
-
數(shù)智破局啟新篇?生態(tài)共生再啟程 —
2025-06-27 20:13
-
助力汽車零部件產(chǎn)線智能化升級,西門
2025-06-27 13:59
-
BBA集體轉(zhuǎn)向!放棄全面電動化
2025-06-26 17:32
-
比換柜省錢,比自研省心,西門子Xcel
2025-06-25 15:07