熱塑性復(fù)合材料在汽車車身面板中的應(yīng)用與創(chuàng)新
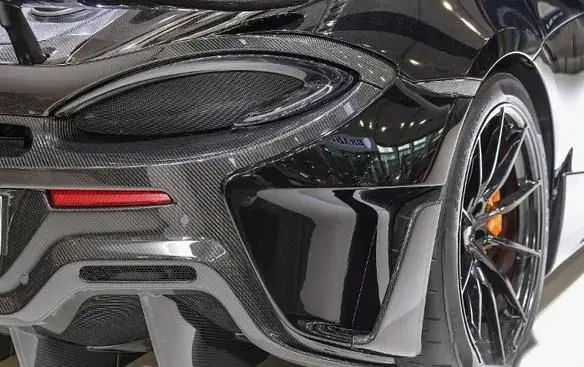
至少五十多年來,全球汽車復(fù)合材料供應(yīng)鏈的重要工作都集中在努力使熱塑性復(fù)合材料成為A級飾面水平車身面板的可行選擇,包括發(fā)動機(jī)罩、車頂和艙蓋(行李箱蓋)。從20世紀(jì)50年代開始,熱固性復(fù)合材料取代了半結(jié)構(gòu)/垂直和全結(jié)構(gòu)/水平車身面板上的金屬。自20世紀(jì)80年代起,熱塑性復(fù)合材料開始間歇性地應(yīng)用于垂直車身面板,如保險杠面板和擋泥板;自20世紀(jì)90年代起,熱塑性復(fù)合材料開始應(yīng)用于門板和其他飾件;自21世紀(jì)初,熱塑性復(fù)合材料開始應(yīng)用于舉升門。然而,事實證明,在水平面板上使用這一類材料很難滿足汽車行業(yè)對性能、成本和美觀的要求。
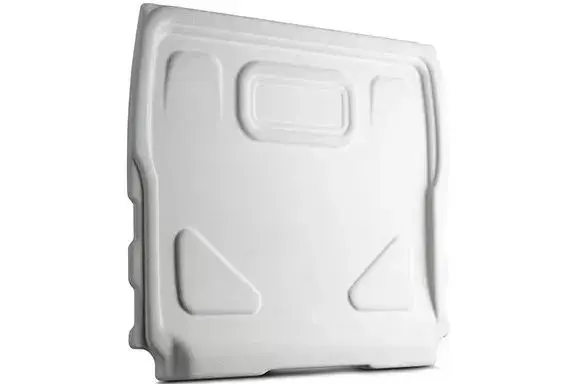
RLE國際開發(fā)了一種創(chuàng)新的低成本/低壓壓縮成型變體和熱塑性夾芯板技術(shù),該技術(shù)自2019年以來一直用于商用車的內(nèi)部隔板(上圖)。目前正在研究將該技術(shù)用于生產(chǎn)車頂外板和引擎蓋。
這種情況可能正在發(fā)生變化,這要?dú)w功于英國的一種低壓壓縮成型和熱塑性夾芯板技術(shù)。4年來,該技術(shù)一直在為一輛額定載重2噸的輕型商用車生產(chǎn)大型隔板。本文討論的最新工作表明,該技術(shù)可將設(shè)計靈活性、機(jī)械性能、經(jīng)濟(jì)快速的加工和表面美學(xué)完美地結(jié)合在一起,最終可用于水平外板。
汽車復(fù)合車身板簡史
熱固性復(fù)合材料在乘用車上的應(yīng)用歷史悠久,可用于半結(jié)構(gòu)垂直和全結(jié)構(gòu)水平車身外板以及底盤/單體部件。玻璃纖維增強(qiáng)塑料(GFRP)于1953年首次出現(xiàn)在當(dāng)時的通用汽車公司(現(xiàn)為通用汽車公司,GM,美國密歇根州底特律市)生產(chǎn)的新型雪佛蘭克爾維特跑車的所有車身外板上。20世紀(jì)60年代,在科爾維特跑車上,手糊玻璃鋼被循環(huán)速度更快、更穩(wěn)定的壓縮模塑片狀模塑料(SMC)所取代。從那時起,SMC的使用范圍已經(jīng)超出了車身面板,包括結(jié)構(gòu)拾取盒、底盤部件以及最近的電動汽車電池組的大型保護(hù)罩。此外,碳纖維/熱固性基復(fù)合材料從20世紀(jì)90年代的一級方程式和二級方程式賽車的重要部件,過渡到車身面板,后來又從2000年代初開始過渡到街車(包括克爾維特)的整個整體車身。
注塑成型的短玻璃纖維增強(qiáng)熱塑性塑料于20世紀(jì)80年代初首次應(yīng)用于非結(jié)構(gòu)性保險杠面板,到20世紀(jì)80年代中期,開始向擋泥板等其他垂直面板過渡。1990年,通用汽車的土星汽車首次亮相,所有垂直車身面板均采用注塑熱塑性復(fù)合材料。不過,發(fā)動機(jī)罩、擋泥板和車頂仍采用沖壓鋼板,最終在2010年停產(chǎn)之前,整個車身外部都過渡到了鋼板。
這十年間,通用汽車的其他幾款車型也采用了熱塑性垂直面板,例如德國慕尼黑寶馬汽車公司(BMW AG)限量版(1989-1991年)Z1跑車,以及后來戴姆勒股份公司梅賽德斯-奔馳分部(現(xiàn)為德國斯圖加特梅賽德斯-奔馳股份公司)于1997年推出的小巧的smart fortwo微型車。smart是第一款采用全熱塑車身面板的汽車,盡管引擎蓋和車頂面板確實非常小。2007年,smart成為第一款從玻璃纖維增強(qiáng)聚碳酸酯/聚對苯二甲酸丁二醇酯(GR/PC-PBT)轉(zhuǎn)向滑石粉填充熱塑性聚烯烴(TPO)的乘用車。
在過去的15年中,滑石粉填充熱塑性聚烯烴在垂直車身面板上慢慢取代了 GR/PC-PBT和GR/改性聚苯醚-聚酰胺(GR/MPPE-PA)等工程熱塑性塑料。2014年,日產(chǎn)Rogue跨界多功能車(CUV)首次采用全熱塑性舉升門(滑石粉/熱塑性聚烯烴外板與長纖維熱塑性聚丙烯(LFT-PP)內(nèi)板粘合),這是另一個歷時10年的重要里程碑。此后,其他越野車和CUV也紛紛效仿。
減重方法
故事開始于2015年左右,一家汽車制造商的工程團(tuán)隊找到RLE國際公司(德國科?。┯k事處,尋求幫助降低商用車的成本和質(zhì)量。RLE因其汽車設(shè)計和工程工作而聞名全球,尤其是在主要車身結(jié)構(gòu)和內(nèi)飾方面。因此,該公司提供全面的CAE、工程設(shè)計、造型可行性和發(fā)布支持。RLE團(tuán)隊提出了幾種金屬到復(fù)合材料的轉(zhuǎn)換方案,以降低成本和質(zhì)量,其中包括全結(jié)構(gòu)/水平式外部頂板和客艙與貨艙之間的半結(jié)構(gòu)/垂直式內(nèi)部隔板。
聯(lián)合小組首先解決了技術(shù)上較為容易的艙壁問題。在接下來的幾年中,艙壁設(shè)計不斷發(fā)展,最終使該技術(shù)通過了所有原始設(shè)備制造商的性能要求。為滿足原始設(shè)備制造商的最大12千牛頓沖擊力要求,最終的艙壁采用了單層輕質(zhì)增強(qiáng)熱塑性塑料 (LWRT) 面板,包括聚丙烯 (PP) 浸漬的可懸浮、短玻璃、低克/平方米 (GSM) 形式的玻璃氈熱塑性塑料 (GMT) 復(fù)合材料,夾心為0°/90°單向 (UD) 玻璃纖維帶(也可使用織物編織)。選擇LWRT蒙皮材料是為了提供良好的未涂漆表面效果。
設(shè)計結(jié)果
◆與鋼材和SMC相比,結(jié)構(gòu)面板的質(zhì)量減少了≥50%,半結(jié)構(gòu)/美觀面板的質(zhì)量減少了≥60%,同時與碳纖維增強(qiáng)塑料 (CFRP) 外面板的質(zhì)量相匹配。
◆單件成本降低10%,但零件數(shù)量減少,耐久性更強(qiáng),模具成本大大降低,噪音/振動/震動(NVH)明顯優(yōu)于金屬?!舫尚椭芷诙蹋?0-120 秒),具有出色的低溫抗沖擊性,可選擇模內(nèi)著色和100%報廢回收。
隔倉板是在室溫下通過低成本/低壓(3.4-4.5巴)“熱壓/凝固”變體在匹配的金屬模具中壓縮成型,成型時間小于90秒。模具既不加熱也不冷卻,但夾層結(jié)構(gòu)中使用的材料在成型前要預(yù)熱。由于模具沒有剪切邊緣,因此在脫模后需要進(jìn)行水刀修整,以清理零件邊緣并切割所需的孔洞。一體式面板取代了多件式鋼/聚氨酯泡沫襯墊組件,重量減輕了5.2千克,降低了單件成本,模具投資減少了80%。此外,這種全玻璃纖維/烯烴夾層結(jié)構(gòu)在部件壽命結(jié)束時可完全回收利用。該獲獎艙壁自2019年起投入商業(yè)使用,年產(chǎn)量為60,000至70,000件,但據(jù)報道,該工藝的單個工具年產(chǎn)量可達(dá)90,000件。
獨(dú)辟蹊徑
RLE的團(tuán)隊(由內(nèi)飾/外飾開發(fā)主管Mark Grix領(lǐng)導(dǎo))相信同樣的技術(shù)也適用于車頂外板,因此選擇獨(dú)自開發(fā)A級水平車頂板。Grix自20世紀(jì)90年代在通用電氣塑料公司工作以來,一直從事熱塑性車身外板的開發(fā)工作。
由于團(tuán)隊預(yù)算有限,因此需要采取巧妙的方法。其中一種方法是獲得三塊免費(fèi)的鋼制車頂外板--打算在裝有隔板的商用車上用作焊接車頂板的外層/表層。這些鋼板身兼兩職。其中一塊被掃描并用于創(chuàng)建模板,以快速設(shè)計面板的外表皮,從而大大縮短了CAE時間。由于車頂面板的內(nèi)部(B面)不是概念驗證的一部分,因此團(tuán)隊只關(guān)注外部(A面)的幾何形狀和表面光潔度。
另外兩塊鋼板被用來制作低成本的成型工具,其中一塊作為核心,另一塊作為模腔,用于成型相對平整的復(fù)合屋面板的A面和B面。該車頂工具隨后被用于在開發(fā)項目中成型復(fù)合材料面板,Grix稱它從一開始就生產(chǎn)出了出色的部件。
從與商用艙壁類似的夾層結(jié)構(gòu)開始,鋪設(shè)、成型和評估了許多不同的表皮和芯材組合(總厚度從3毫米到5毫米不等),以開發(fā)車頂板概念。在對各種材料進(jìn)行預(yù)熱后(不同的層受熱時間可能不同),在裝有上述工具(保持室溫)的壓縮壓力機(jī)中手動鋪設(shè),并通過熱壓成型。研究人員再次將有效循環(huán)時間設(shè)定為90秒。
屋面板是在Airborne公司(荷蘭海牙)在英國擁有的一家工廠進(jìn)行模壓成型的,目的是進(jìn)一步發(fā)展這一概念,并為夾芯板結(jié)構(gòu)實現(xiàn)表皮和芯材的正確組合。Airborne公司的設(shè)備非常理想,因為它配備了一個可以加熱整個1.75×2.0米頂板的超大烤箱,可以將材料加熱到240°C。具有諷刺意味的是,這個烤箱實際上對面板來說太大了,因此我們將烤箱的一部分隔開,這樣材料的停留時間就不會太長,而且材料可以從烤箱的側(cè)面而不是末端送入。
隨后,對各種面板材料組合進(jìn)行了小規(guī)模的實驗室測試。最終,最有希望的候選材料通過西卡股份公司(瑞士巴爾)生產(chǎn)的1K結(jié)構(gòu)聚氨酯粘合劑粘合到了測試車輛的車頂環(huán)/弓上,并接受了額外的車輛級測試。
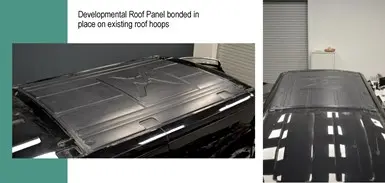
RLE在沒有原始設(shè)備制造商關(guān)于開發(fā)車頂面板規(guī)格的情況下,將工作重點(diǎn)放在外部表皮上,目的是將車頂箍/弓保持在原位,并將復(fù)合材料解決方案粘接到當(dāng)前金屬車頂使用的現(xiàn)有焊接法蘭上。之所以能做到這一點(diǎn),是因為復(fù)合材料結(jié)構(gòu)的線性熱膨脹系數(shù)(CLTE)較低。隨后的測試表明,目標(biāo)熱塑板的線性熱膨脹系數(shù)接近鋁的線性熱膨脹系數(shù)。
由于最終的復(fù)合材料是在加固和成型之前在壓力機(jī)中組裝的,因此根據(jù)應(yīng)用所需的性能和表面處理要求,RLE的技術(shù)在材料類型方面具有極大的通用性,可以組合成最終面板的表皮、內(nèi)核和外表面處理。幾乎可以使用任何類型的片狀熱塑性復(fù)合材料(如膠帶、GMT、有機(jī)片、LWRT)。唯一的要求是聚合物基體必須具有化學(xué)相容性(以實現(xiàn)良好的材料流動性,確保成分均勻),并且具有相似的玻璃化轉(zhuǎn)變溫度(Tg),以便在同一烘箱中加熱,而不必?fù)?dān)心溫度較高的材料會在固結(jié)/成型完成之前熔化溫度較低的材料。
Grix解釋說:“每個應(yīng)用的要求都是不同的,所以我們可以靈活地使用纖維體積分?jǐn)?shù)從20%到50%不等的材料,盡管我們通常喜歡在30-40%左右。測試表明,使用更高的FVFs并沒有任何好處。事實上,如果我們有太多的樹脂,那么沖擊強(qiáng)度和層之間的附著力就會受到影響。為了獲得良好的表面,有足夠的樹脂是絕對必要的”。
對于控制表面光潔度的最上層美觀層,候選材料包括啞光或亮光熱塑性薄膜、紡織品、無紡布/織物組合,甚至是抗劃痕/抗紫外線硬涂層或柔軟觸感熱塑性聚氨酯(TPU)涂層。同樣,這項技術(shù)的優(yōu)點(diǎn)在于它可以很容易地進(jìn)行即時修改,以滿足許多行業(yè)的應(yīng)用需求。
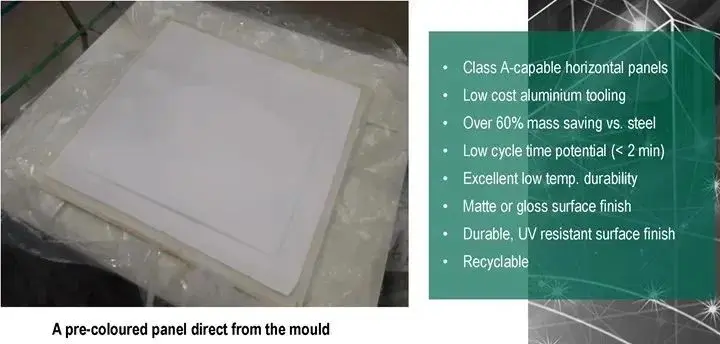
迄今為止,RLE已經(jīng)使用預(yù)著色薄膜和低成本鋁制工具直接從模具中生產(chǎn)出具有耐用且抗紫外線光澤或啞光表面的汽車A級面板,周期時間為<2分鐘。與鋼板相比,復(fù)合材料為結(jié)構(gòu)板提供了50%的潛在質(zhì)量節(jié)省,為外部/半結(jié)構(gòu)板提供了60%的潛在質(zhì)量節(jié)省。即使在低溫下,它們也具有出色的沖擊強(qiáng)度和完全的報廢可回收性。這種熱塑性夾芯板技術(shù)不僅引起了汽車行業(yè)參與者的興趣,也引起了其他地面運(yùn)輸領(lǐng)域參與者的興趣。
該團(tuán)隊研究了熱塑性樹脂系統(tǒng)(主要在烯烴和聚酰胺系列中)和增強(qiáng)材料(包括短切、UD和機(jī)織織物)的不同組合,用于屋頂夾芯板的表皮和芯材。由于其較高的位置,開發(fā)中的屋頂板不需要A級飾面。最初,使用預(yù)著色的黑色材料,并嘗試了啞光白色面板。最近,Grix和他的團(tuán)隊通過在工具中涂上一層薄膜以及嘗試硬涂層,提高了紫外線穩(wěn)定性和耐刮擦性。面板可以使用對比色,也可以與身體的其余部分相匹配。開發(fā)中的車頂板或商用艙壁都不需要金屬加固。如果將整個鋼屋頂(而不僅僅是一塊面板)轉(zhuǎn)換為熱塑性夾層技術(shù),Grix估計可以節(jié)省24.5公斤的重量。
準(zhǔn)備好迎接黃金時段了嗎?
汽車制造商喜歡問的一個大問題是,概念車目前處于什么技術(shù)準(zhǔn)備水平(TRL),而Grix的回答是,車頂板概念還很遙遠(yuǎn)。
他解釋道:“你仍然需要做一些特定于OEM的測試,例如環(huán)境穩(wěn)定性、NVH等等,但出于所有意圖和目的,車頂板使用與隔板相同的材料系列和相同加工方法的變體,隔板在過去四年中一直在進(jìn)行相當(dāng)大的商業(yè)生產(chǎn),這項技術(shù)的靈活性意味著,如果您需要提高紫外線性能或耐刮擦性,甚至使面板更厚、更薄或更堅硬,那么我們可以做到這一點(diǎn)。我們花了很多時間來真正了解這項技術(shù),以及用工具制作漂亮的面板需要什么”。
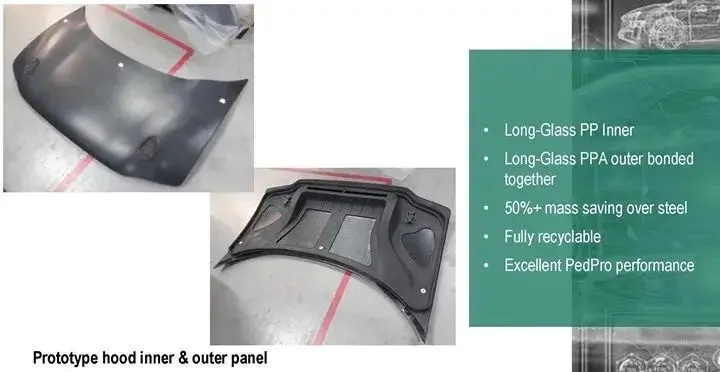
據(jù)報道,RLE正在與汽車一級供應(yīng)商和農(nóng)業(yè)設(shè)備和高爾夫球車等其他地面運(yùn)輸領(lǐng)域的OEM進(jìn)行討論,以實現(xiàn)內(nèi)部和外部應(yīng)用的商業(yè)化。
這項技術(shù)的下一步是什么?Grix說:“沒有理由(使用正確的配方)這項技術(shù)也不能用于符合PedPro(行人保護(hù))標(biāo)準(zhǔn)的引擎蓋,我們已經(jīng)生產(chǎn)了開發(fā)罩,小規(guī)模測試表明,我們比熱固性塑料或鋼具有更好的能量吸收和消散能力。此外,我們還探索了將這項技術(shù)不僅用于相對簡單的面板,還用于幾何復(fù)雜度明顯更高的汽車內(nèi)飾的高拉伸面板。結(jié)合工具的A級預(yù)著色飾面,與鋼相比節(jié)省50-60%的質(zhì)量,以及使用壽命結(jié)束時完全可回收的部件,我們認(rèn)為這對在多個行業(yè)尋求輕質(zhì)面板技術(shù)的OEM來說是一個成功的組合。我們很樂意與任何有興趣進(jìn)一步探索的人合作”。
熱塑性復(fù)合材料車身面板:優(yōu)勢和挑戰(zhàn)
與熱固性復(fù)合材料或金屬相比,熱塑性復(fù)合材料是車身外板的理想材料,原因有很多。首先,它們往往更輕(比重更低),具有更好的耐損傷性(抗沖擊強(qiáng)度)--這是滿足PedPro要求的一個優(yōu)勢,而且它們能提供更好的出模表面,減少模后加工。
與熱固性材料不同,熱塑性復(fù)合材料可回收(可熔融再加工),因此更容易重復(fù)使用廢料,并從報廢零件中回收可用材料--這對于向歐盟銷售汽車的企業(yè)來說是一個重要的特點(diǎn),而且熱塑性復(fù)合材料在供貨時已完全聚合,這意味著成型周期更短,可重復(fù)性和再現(xiàn)性(R&R)更好,因此更適合大批量生產(chǎn),并有助于抵消通常較高的原材料和模具成本。與金屬相比,熱塑性塑料還提供了更大的設(shè)計自由度,并為零件集成(減少零件數(shù)量)、插入硬件(便于連接)和簡化模后裝配提供了大量機(jī)會。
盡管熱塑性復(fù)合材料具有諸多優(yōu)點(diǎn),但與所有材料一樣,它們也面臨著必須克服的挑戰(zhàn)。例如,與鋼或鋁相比,早期的整體式熱塑性復(fù)合材料車身面板具有更高的熱膨脹系數(shù)(CLTE),不連續(xù)的纖維加固要求復(fù)合材料與金屬面板之間留有大于理想的間隙,以適應(yīng)溫度循環(huán)過程中的尺寸變化。如果沒有這種美學(xué)上的權(quán)衡,車門等可移動面板有時就無法打開或關(guān)閉。這一問題在很大程度上是通過以下方法解決的:將整體面板改成成對的粘合內(nèi)/外面板--帶或不帶芯--以及在片狀復(fù)合材料(如GMT/organosheet)和熱塑性塑料帶中使用較長的短切/非連續(xù)纖維增強(qiáng)材料以及連續(xù)纖維無紡布、單向和編織增強(qiáng)材料。
另一個問題是,汽車行業(yè)青睞的熱塑性塑料牌號(主要是聚丙烯、聚酰胺6或6/6,以及聚酰胺或熱塑性聚酯與PC或MPPE的混合物)缺乏熱穩(wěn)定性,無法在白車身(BIW)電泳涂裝(e-coat)和噴漆后承受烘烤爐的溫度。這增加了裝配的復(fù)雜性和成本,因為面板必須離線噴涂,并在汽車裝配流程的后期階段添加。雖然熱塑性塑料板的噴漆仍需離線完成,但在改善模塑著色(MIC)板的紫外線穩(wěn)定性、色彩深度和金屬特效方面已做了大量工作,之后只需清漆即可完成。此外,薄膜技術(shù)也取得了長足進(jìn)步,它提供了比油漆更耐用的表面,符合汽車制造商降低油漆成本和環(huán)境負(fù)擔(dān)的努力。
另一個配方問題是在剛度和沖擊力之間取得適當(dāng)?shù)钠胶猓员苊馐褂么笮徒饘僦Ъ軐⒋怪泵姘鍛覓煸谲囕v上。與此相關(guān)的一個問題是,由于剛度和強(qiáng)度通常低于金屬的數(shù)值,因此通常需要采用幾何形狀(如肋條)來實現(xiàn)面板的可比機(jī)械性能。然而,這往往會導(dǎo)致名義壁較厚,從而引起包裝問題。面對必須重新設(shè)計現(xiàn)有車輛的車身結(jié)構(gòu)以適應(yīng)更厚的復(fù)合材料面板的前景,大多數(shù)原始設(shè)備制造商都會選擇放棄。對于熱塑性烯烴(TPO)材料來說,將非連續(xù)纖維增強(qiáng)材料與礦物填料相結(jié)合的精心配方工作,已使這些材料在外部垂直面板的表皮上占據(jù)了主導(dǎo)地位。此外,通過從整體面板設(shè)計轉(zhuǎn)變?yōu)檎澈蟽?nèi)/外面板,無法滿足 A級要求的結(jié)構(gòu)性內(nèi)面板與無法單獨(dú)滿足機(jī)械要求的A級外皮相輔相成。
數(shù)十年來,熱塑性水平面板之所以無法使用,最大的挑戰(zhàn)可能就是在高溫下的下垂和長期蠕變問題。這有幾個原因。首先,熱塑性塑料在接近其Tg的溫度范圍內(nèi)會軟化,從而導(dǎo)致機(jī)械性能的逐漸喪失,包括承載負(fù)荷和自支撐的能力。這種特性使熱塑性塑料更容易回收利用,但也會損害其在高溫下的長期機(jī)械完整性。在某種程度上,從短纖維/非連續(xù)纖維加固改成連續(xù)纖維加固,以及從整體板材改成帶或不帶芯材的粘合板材,都有助于解決這一問題。
與此相關(guān)的一個問題是如何獲得足夠高的FVF或 FWF,以改善高溫期間的機(jī)械性能。熱塑性聚合物在供應(yīng)時已預(yù)聚(成型前分子鏈很長),這意味著即使在熔融溫度下,它們與許多液態(tài)熱固性體系相比也相當(dāng)粘稠。這就很難實現(xiàn)高水平的纖維浸潤和浸漬。因此,即使在今天,F(xiàn)WF值超過40%的注塑成型產(chǎn)品也很有限,而許多熱固性技術(shù)允許達(dá)到高達(dá)70%的FVF值。在某種程度上,解決這一問題的方法包括:謹(jǐn)慎選擇樹脂(例如,使用支鏈型聚丙烯而非線型聚丙烯,后者的粘度較低),修改熱塑性膠帶和GMT/organosheet生產(chǎn)的層壓工藝,以及最近使用低粘度己內(nèi)酰胺單體進(jìn)行浸漬,然后反應(yīng)聚合成PA6。其代價是較長的循環(huán)時間(更像熱固性塑料)和專業(yè)設(shè)備。不過,隨著時間的推移,在熱塑性復(fù)合材料中加入更多纖維,特別是更長的連續(xù)纖維的能力不斷提高,這極大地促進(jìn)了熱塑性復(fù)合材料在越來越多的結(jié)構(gòu)性應(yīng)用中的使用。這里需要權(quán)衡的一點(diǎn)是,對于外觀美觀的表面來說,較高的FVF/FWF可能會導(dǎo)致纖維穿透。解決這一問題的部分方法是使用薄膜、對面板進(jìn)行噴漆或紋理處理,或在夾芯板組合的最外層美觀層中使用較低的纖維增強(qiáng)層。
最后但并非最不重要的一點(diǎn)是,在高產(chǎn)量/低利潤的汽車行業(yè)中,直接和間接成本始終是一個敏感點(diǎn)。當(dāng)復(fù)合材料行業(yè)致力于改進(jìn)材料和工藝以應(yīng)對一個又一個車身面板挑戰(zhàn)時,鋁和鋼鐵行業(yè)的同行們也在不斷改進(jìn)他們的材料和工藝。即使在今天,除非改用復(fù)合材料能使汽車減輕大量重量、帶來重要的制造優(yōu)勢或使安全性或功能性達(dá)到新的水平,否則大多數(shù)汽車制造商都會拒絕使用復(fù)合材料,除非使用復(fù)合材料的成本至少與傳統(tǒng)材料持平或更低。
-
助力汽車零部件產(chǎn)線智能化升級,西門子Xcelerat
2025-06-27 -
BBA集體轉(zhuǎn)向!放棄全面電動化
2025-06-26 -
西門子SiePA斬獲麒麟認(rèn)證,服務(wù)能力再升級!
2025-06-24 -
Geega產(chǎn)品圖譜 | Geega OS 工業(yè)操作系統(tǒng)
2025-06-23
編輯推薦
最新資訊
-
數(shù)智破局啟新篇?生態(tài)共生再啟程 —
2025-06-27 20:13
-
助力汽車零部件產(chǎn)線智能化升級,西門
2025-06-27 13:59
-
BBA集體轉(zhuǎn)向!放棄全面電動化
2025-06-26 17:32
-
比換柜省錢,比自研省心,西門子Xcel
2025-06-25 15:07
-
采埃孚售后再制造中心喬遷臨港 領(lǐng)航
2025-06-25 14:44