新能源汽車一體化鋁合金壓鑄結(jié)構(gòu)件成形工藝
汽車輕量化是要在保證汽車安全性和性能的基礎(chǔ)上,盡可能地降低整車質(zhì)量,以達(dá)到減少汽車燃油消耗、提高汽車整車動力性。特斯拉、蔚來等車企都大量采用鋁合金降低車身重量。一體化壓鑄是將車身較多的鋁合金零部件有效地整合為一個大結(jié)構(gòu)件,有效節(jié)省生產(chǎn)成本,同時也可實(shí)現(xiàn)汽車的輕量化目標(biāo)。
鋁合金一體化壓鑄成形結(jié)構(gòu)件因其質(zhì)量輕、成本低和性能好,在新能源汽車制造中所占比例越來越高。特斯拉公司在 Model Y 車型制造中,一體壓鑄成形了車身后底板,焊點(diǎn)由大約700~800個減少到50個,減少了焊接工序,大幅提升了車身結(jié)構(gòu)穩(wěn)定性。在一體化壓鑄工藝研究發(fā)展下,對一體化壓鑄質(zhì)量保證技術(shù)研究也不斷發(fā)展。材料、工藝和設(shè)計(jì)等方面的技術(shù)研究推進(jìn)一體化壓鑄加快發(fā)展。本文從一體化壓鑄需求的新型鋁合金材料、工藝參數(shù)控制、結(jié)構(gòu)設(shè)計(jì)等,提出了三個方面研究進(jìn)展,可以為一體化壓鑄技術(shù)研究提供參考。
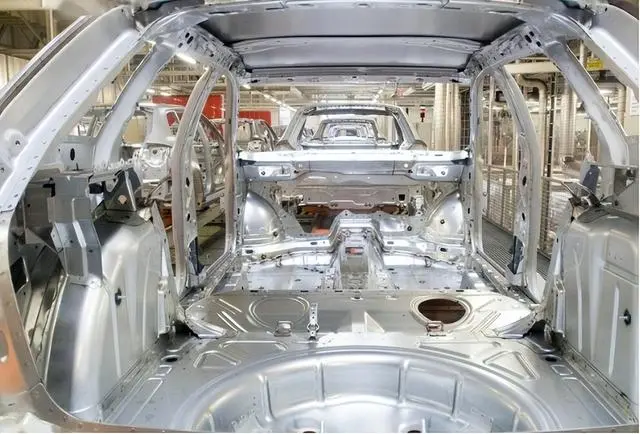
01 新能源汽車一體化壓鑄成型技術(shù)的產(chǎn)業(yè)化現(xiàn)狀及發(fā)展趨勢
隨著汽車輕量化發(fā)展,車身一體化成型將引領(lǐng)車身制造全新革命。特斯拉作為一體化壓鑄行業(yè)技術(shù)引領(lǐng)者,其壓鑄生產(chǎn)主要是 Model Y 后車身一體化壓鑄件。相較于傳統(tǒng)汽車零部件壓鑄,主要區(qū)別是使用大噸位壓鑄機(jī),將原來幾十個零部件整合為同一個鋁合金材料的大型件壓鑄。未來隨著壓鑄工藝的發(fā)展,其他車身結(jié)構(gòu)件也將逐漸采用一體化壓鑄生產(chǎn)。
隨著汽車減重的需求不斷增加,鋁、鎂合金等輕質(zhì)材料在新能源汽車全車占比不斷增加。特斯拉不斷研發(fā)免熱處理鋁合金壓鑄新材料,致力于開發(fā)具有更高強(qiáng)度和更好延展性的鋁合金材料,已經(jīng)用于實(shí)際生產(chǎn),在滿足強(qiáng)度要求條件下,生產(chǎn)過程中無需額外加工,進(jìn)一步降低成本。伴隨著汽車零部件一體化成型時代到來,一體化壓鑄主要向著以下方向發(fā)展。
1.1 高壓壓鑄工藝優(yōu)化
目前一體化壓鑄技術(shù)主要來源于高壓壓鑄技術(shù),在高壓壓鑄的基礎(chǔ)上采用真空輔助,以解決高壓壓鑄中由于高速高壓引起的卷氣和大孔隙等問題。隨著一體化壓鑄的不斷實(shí)踐,對于壓鑄工藝的完善優(yōu)化也在不斷地進(jìn)行,壓鑄過程中工藝、熱力學(xué)參數(shù)和動力學(xué)參數(shù)等的設(shè)置可以直接影響壓鑄成型結(jié)果,合理地設(shè)置這些參數(shù)能夠?qū)崿F(xiàn)優(yōu)化壓鑄結(jié)果,有效控制壓鑄件成型質(zhì)量。
1.2 高性能鋁合金材料探索
目前免熱處理鋁合金材料研發(fā)在國內(nèi)外掀起熱潮,其壓鑄后不需熱處理即可滿足車身性能。鑒于對鋁合金材料性能方面的要求,各廠商也正研發(fā)具有更高性能的鋁合金材料。
1.3 壓鑄件結(jié)構(gòu)設(shè)計(jì)及優(yōu)化
壓鑄件結(jié)構(gòu)設(shè)計(jì)主要針對新能源汽車關(guān)鍵零部件,如一體化汽車減震塔零件優(yōu)化設(shè)計(jì)。壓鑄件的結(jié)構(gòu)設(shè)計(jì)和壓鑄方案的設(shè)計(jì)能夠影響壓鑄件的成型質(zhì)量,而一體化壓鑄對于壓鑄件的質(zhì)量要求較高。特斯拉開發(fā)的汽車后車身一體化底板壓鑄結(jié)構(gòu)件包含了整車左右側(cè)的后輪罩內(nèi)板、后縱梁、底板連接板、梁內(nèi)加強(qiáng)板等零件,通過壓鑄件結(jié)構(gòu)優(yōu)化設(shè)計(jì)及壓鑄方案的設(shè)計(jì)實(shí)現(xiàn)對壓鑄件質(zhì)量的控制勢在必行。
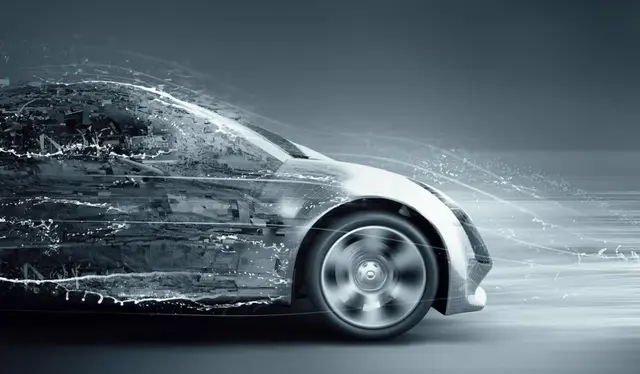
02 新能源汽車一體化壓鑄成型技術(shù)
研究進(jìn)展
2.1 免熱處理鋁合金材料研究現(xiàn)狀
與其他金屬相比,鋁合金作為輕質(zhì)合金滿足了汽車輕量化的需求,密度較低,強(qiáng)度較高。作為壓鑄材料,鋁合金線收縮小,填充性能好,在惡劣環(huán)境下工作,其力學(xué)性能依然能夠滿足多方面需求。鋁合金具有良好導(dǎo)熱性、導(dǎo)電性和切削性,因此對新型高性能鋁合金材料的研究一直是一體化壓鑄研究中的重點(diǎn)。
傳統(tǒng)的鋁合金壓鑄生產(chǎn)中,無法保證鋁合金壓鑄件的機(jī)械性能,為保障壓鑄后汽車零部件的機(jī)械性能,一般會對零部件進(jìn)行熱處理以滿足性能需求。然而,經(jīng)過熱處理工藝的汽車零部件,容易發(fā)生尺寸變形及表面缺陷。一體化壓鑄件一般由十幾個到數(shù)十個零部件集成為一兩個大型零部件,其投影面積較大,成形后熱處理同樣也會存在尺寸變形及表面缺陷問題。雖然通過矯正工藝可以改善一定尺寸精度,但容易導(dǎo)致廢品率增加,成本急劇上升。因此,免熱處理鋁合金材料成為一體化壓鑄的重要技術(shù)壁壘。
一體化壓鑄的零部件主要使用鋁合金材料,因此對鋁合金材料成型性能、機(jī)械性能等要求較高,具有更高性能的鋁合金材料的探索不斷持續(xù)發(fā)展。國際上,特斯拉、美國美鋁、德國萊茵菲爾德等均有免熱處理鋁合金開發(fā)計(jì)劃,國內(nèi)立中集團(tuán)、帥翼馳集團(tuán)、華人運(yùn)通與上海交大等均積極研發(fā)高性能免熱處理鋁合金材料。
為開發(fā)具有較高性能的新型鋁合金材料,LeiJiang根據(jù)高強(qiáng)度高韌性鋁合金的特性,整理了171套數(shù)據(jù)。然后建立了一個以性能導(dǎo)向?yàn)樵O(shè)計(jì)策略的機(jī)器學(xué)習(xí)設(shè)計(jì)系統(tǒng),快速發(fā)現(xiàn)具有高延展性和高韌性指數(shù)的新型鋁合金,并使用該系統(tǒng)快速設(shè)計(jì)了3組滿足性能要求的合金成分,極限抗拉強(qiáng)度為700~750MPa,伸長率為 8%~10%,斷裂韌性為33~35MPa·m。試驗(yàn)測得結(jié)果符合設(shè)計(jì)要求,該研究結(jié)果可為快速發(fā)現(xiàn)具有多靶向性能的復(fù)雜合金提供參考。
C. Mun?z-Iba?ez建立了鋁合金壓鑄工藝的半非參數(shù)模型,使用分層人工神經(jīng)網(wǎng)絡(luò)(HANN),Sn、Zn、Mn、Cu、Si、Ni 和 Mg等七種金屬含量與合金特性之間的關(guān)系決定了分層人工神經(jīng)網(wǎng)絡(luò)的結(jié)構(gòu)。使用兩種數(shù)據(jù)集分別對該模型進(jìn)行訓(xùn)練和實(shí)驗(yàn)驗(yàn)證。開發(fā)了兩種新合金來測試 HANN 預(yù)測能力,可得到建模誤差百分比為3.65%。
用于一體化壓鑄的鋁合金材料需要具有較高的強(qiáng)度和延展性,Xixi Dong研制了一種高強(qiáng)度和高延展性壓鑄鋁合金,其屈服強(qiáng)度≥320MPa,伸長率≥10%。采用高壓壓鑄法加工的 Al Si Cu Mg Mn合金,經(jīng) 510 ℃固溶處理30min,在170℃下老化12h 后,能達(dá)到屈服強(qiáng)度321MPa、極限抗拉強(qiáng)度425MPa 和延伸率11.3%等指標(biāo)。該鋁合金材料具備在實(shí)際生產(chǎn)中應(yīng)用的條件,可有效降低生產(chǎn)成本。
Ruizhang Hu制備免熱處理的壓鑄鋁合金樣品,熱處理前樣品的平均顯微硬度為 114HV0.1,熱處理后為121H0.1。樣品力學(xué)特性優(yōu)良,具有免熱處理等性能。熱處理前的抗拉強(qiáng)度達(dá)到310MPa,其強(qiáng)度大于具有類似成分的普通鑄造鋁合金強(qiáng)度,不經(jīng)過熱處理過程即可具備滿足要求的機(jī)械性能,減少了尺寸變形,改善壓鑄精度。
2.2 一體化壓鑄工藝優(yōu)化
一體化壓鑄技術(shù)來源于高壓壓鑄,高壓鑄造因效率高、零件壁厚小等特點(diǎn),在汽車車身中的運(yùn)用較多。然而,高壓壓鑄過程中充型速度較高,經(jīng)常會引起壓室及型腔內(nèi)存在的氣體未能完全排出到外部環(huán)境中,金屬液中會摻雜進(jìn)氣體,造成內(nèi)部氣孔或鑄件缺陷,使得鑄件質(zhì)量下降,其力學(xué)性能也一定程度降低。為減少鑄件中氣孔等缺陷形成,真空度、柱塞速度、合金澆注溫度、模具溫度等真空輔助高壓壓鑄的工藝參數(shù)實(shí)時調(diào)節(jié)是一體化壓鑄中關(guān)鍵技術(shù)。
Hanxue Cao研究了在 500 mbar、200 mbar和 100 mbar 的絕對壓力下通過真空輔助高壓壓鑄(HPDC)工藝制造的 AlSi9Cu3合金鑄件,確定了模腔內(nèi)絕對壓力對壓鑄件孔隙率、微觀組織和力學(xué)性能的影響。結(jié)果表明,隨著絕對壓力的降低,平均孔隙率和孔徑降低,拉伸強(qiáng)度和伸長率顯著提高。壓鑄件機(jī)械性能可通過提高真空度來進(jìn)一步提高。Hanxue Cao還研究了壓鑄金屬孔隙形成的動力學(xué)分析及絕對壓力對孔隙率的影響,傳統(tǒng)HPDC 壓鑄中速噴射下氣體的截留引起了氣體孔隙率的產(chǎn)生,孔隙率會降低鑄件質(zhì)量。真空壓鑄會在一定程度上阻礙分離流的產(chǎn)生,使得在鑄造過程中難以產(chǎn)生渦流。由于流場的作用,只能在很小的范圍內(nèi)流動并且不能擴(kuò)散出去的氣體將會減少。凝固前金屬液中摻雜的空氣量降低,鑄件的孔隙率也會同樣降低。Chen Hu研究了在不同真空度下 HPDC 工藝生產(chǎn)的 AlSi12Fe 合金壓鑄件。結(jié)果表明,隨著真空度增加,AlSi12Fe 鑄件中的殘余氣體含量降低,在真空度增加的情況下,鑄件孔隙率有了明顯的降低,而屈服強(qiáng)度也有了明顯的增大。表明在高真空度下增加真空度對極限抗拉強(qiáng)度沒有顯著影響。
M.??giewka研究真空輔助對高壓壓鑄鑄件質(zhì)量的影響,壓鑄機(jī)模腔內(nèi)負(fù)(相對)壓值的變化對壓力鑄件表面質(zhì)量的影響。選擇的參數(shù)為注入第二階段的柱塞速度、合金的澆注溫度、模具溫度等。通過比較隨機(jī)選擇的鑄件進(jìn)行表面粗糙度測量,評估鑄件的質(zhì)量。結(jié)果表明,正確選擇壓力壓鑄機(jī)的工作參數(shù)、金屬和模具的適當(dāng)溫度,以及模具中附加的負(fù)壓可以實(shí)現(xiàn)高質(zhì)量的鑄件。
B Budiarto探索真空系統(tǒng)對 ADC-12 鋁合金材料產(chǎn)品缺陷和微結(jié)構(gòu)影響。觀察孔隙率、捕獲氣壓、熱點(diǎn)水平、維氏硬度水平等參數(shù),開展 XRD 分析和光學(xué)顯微鏡(LOM)顯微結(jié)構(gòu)分析。真空系統(tǒng)在孔隙率和產(chǎn)品產(chǎn)率方面優(yōu)于溢出系統(tǒng),受到真空度和熱點(diǎn)水平的影響。具有真空系統(tǒng)的產(chǎn)品的硬度水平優(yōu)于溢出系統(tǒng),位錯密度增加,晶格應(yīng)變增加,產(chǎn)品的晶體尺寸水平減小。Xixi Dong設(shè)計(jì)了兩級真空系統(tǒng)的 4500 kN 冷室 HPDC 機(jī)器用于制造標(biāo)準(zhǔn)的 ASTM 拉伸樣品,真空輔助 HPDC提高了合金拉伸性能的可重復(fù)性。經(jīng)過數(shù)據(jù)和偏差分析驗(yàn)證,真空輔助 HPDC 在澆注狀態(tài)下顯著降低了合金延展性的不穩(wěn)定波動,同時提高了鑄造合金的極限抗拉強(qiáng)度和延展性。延展性和拉伸性能重復(fù)性的顯著提高源于真空輔助 HPDC 處理合金中孔隙率體積分?jǐn)?shù)和孔隙率尺寸的降低。缺陷尺寸的減小可以改善應(yīng)力分布,延緩鑄件的裂紋萌生。因此真空輔助 HPDC 加工壓鑄合金拉伸強(qiáng)度和延展性得到了增強(qiáng)。
Péter Szalva采用常壓排氣和真空輔助高壓壓鑄工藝生產(chǎn)了 AlSi9Cu3(Fe)鋁合金鑄件。在壓鑄流程中,分三級設(shè)置柱塞速度。研究了絕對空腔氣壓對鑄件孔隙率和力學(xué)性能的影響,并與傳統(tǒng)的 HPDC 鑄造方法進(jìn)行了比較。結(jié)果表明,鑄件的孔隙率和孔徑可以顯著降低,力學(xué)性能得到顯著改善。真空輔助壓鑄工藝減少了模腔內(nèi)夾帶空氣和其他氣體的量,提高了壓鑄件的拉伸強(qiáng)度和伸長率。他還研究了真空輔助高壓壓鑄 AlSi9Cu3(Fe)鋁合金壓鑄件疲勞壽命,與傳統(tǒng)的 HPDC 鑄造相比,在給定的負(fù)載水平下,真空輔助高壓壓鑄增加了斷裂的循環(huán)次數(shù),顯著降低了孔隙率尺寸和體積,減少了氧化物薄片出現(xiàn),從而提高循環(huán)疲勞實(shí)驗(yàn)次數(shù),改善鑄件應(yīng)力分布,同時延長疲勞壽命。
壓鑄工藝參數(shù)的設(shè)置會對壓鑄成品產(chǎn)生一定影響,合理地設(shè)置壓鑄工藝參數(shù),能夠改善壓鑄件質(zhì)量。
M. Koru研究了模具溫度、鑄造溫度和動態(tài)(壓力、速度和真空施加)注射參數(shù)對樣品力學(xué)性能和孔隙率的影響。結(jié)果表明,孔隙率因模具溫度的提高及真空環(huán)境的引入而降低。提高模具溫度并對模具型腔施加真空有助于增強(qiáng)機(jī)械性能。與提高模具溫度相比,提高鑄造溫度對機(jī)械性能的影響要小。增加注射速度會導(dǎo)致孔隙率增加和液態(tài)金屬表面的湍流,而增加壓力會降低孔隙率百分比。與非真空條件相比,因?yàn)樗鼤p少空氣混合到液態(tài)金屬中,壓力鑄造中的真空應(yīng)用可以提供更好的壓鑄結(jié)果。
Bekir Yal?in研究了注射參數(shù)和真空度對合金強(qiáng)度和孔隙率的影響,通過調(diào)整優(yōu)化澆注溫度、鑄造壓力、速度和模腔內(nèi)的真空度等參數(shù),分析鋁合金的機(jī)械和冶金性能的變化。結(jié)果表明,模腔內(nèi)的真空度改善了機(jī)械性能,例如拉伸強(qiáng)度、屈服強(qiáng)度和硬度,有助于形成細(xì)晶粒結(jié)構(gòu)。鋁合金的機(jī)械性能隨著注射壓力增加而增加。無真空的壓力噴射和低澆注溫度會形成較大孔隙和較高孔隙率,導(dǎo)致屈服強(qiáng)度、抗拉強(qiáng)度以及硬度值的降低。
Hong-mei YANG研究不同加工參數(shù)對高壓壓鑄工藝界面?zhèn)鳠嵝袨榈挠绊憽=饘?- 模具界面?zhèn)鳠嵝袨閷ψ罱K產(chǎn)品微觀結(jié)構(gòu)及其力學(xué)性能起重要作用,需要獲得可靠的 HPDC 界面?zhèn)鳠釋?shí)驗(yàn)值,而界面?zhèn)鳠嵝袨榭梢酝ㄟ^界面?zhèn)鳠嵯禂?shù)來表征。該研究通過汽車壓鑄件慢速度、高速度、澆注溫度和初始溫度等加工參數(shù)的設(shè)置,檢測金屬 - 模具界面的溫度,以反比法測定界面?zhèn)鳠嵯禂?shù)。結(jié)果表明真空輔助可以顯著提高鑄件 IHTC 值,降低鑄件粒徑。
上述文獻(xiàn)主要闡述了真空輔助對高壓壓鑄件的機(jī)械性能和疲勞壽命等方面的影響,此外,還探討了壓鑄中各方面加工參數(shù)對壓鑄結(jié)果的影響。不同模具溫度、鑄造溫度和動態(tài)(壓力、速度和真空施加) 注射參數(shù)等參數(shù)影響高壓壓鑄工藝界面?zhèn)鳠嵝袨?,對樣品力學(xué)性能和孔隙率參數(shù)有直接影響。
2.3 壓鑄零件結(jié)構(gòu)設(shè)計(jì)優(yōu)化
為減小壓鑄件的缺陷,提高壓鑄件的表面質(zhì)量及力學(xué)性能,對壓鑄零件進(jìn)行結(jié)構(gòu)優(yōu)化設(shè)計(jì)是關(guān)鍵技術(shù)之一。需要深入探究壓鑄件各部分結(jié)構(gòu)設(shè)計(jì)對壓鑄結(jié)果的影響及作用機(jī)理。
Hyuk-Jae Kwon通過 CAE 仿真,優(yōu)化汽車油底殼零件澆口和流道,開展填充流道系統(tǒng)分析,找出澆口大小和位置。通過對澆口和流道系統(tǒng)的修改以及溢流的配置,顯著減少了由空氣滯留引起的內(nèi)部孔隙率。通過凝固分析,預(yù)測了凝固收縮引起的內(nèi)部孔隙率。合理地設(shè)置內(nèi)澆口尺寸能夠有效改善壓鑄件的填充效果,提高壓鑄件的整體質(zhì)量。
Mohamad El Mehtedi通過有限元模擬對金屬板的 AlSi13Fe 鋁合金壓鑄工藝進(jìn)行了研究和分析。采用填料分析方法確定了澆口尺寸、流道和溢流系統(tǒng),減少了鑄造材料消耗和模具磨損。從結(jié)果中可以看出增加流道及溢流槽的數(shù)量,可以有效提高鑄件充填度,減小鑄件孔隙率和永久變形,確保鑄件質(zhì)量。
J. S. S. Babu報道了關(guān)于鋁合金蜘蛛臂部件制造的模具設(shè)計(jì)和澆注系統(tǒng)的仿真和試驗(yàn)研究。改進(jìn)澆注系統(tǒng),對模具型腔進(jìn)行了優(yōu)化,調(diào)節(jié)溢出和模具壓力,壓鑄過程中使熔融金屬平穩(wěn)流動,提高可鑄造性并減小孔隙率。
Seong Il Jeong模擬了汽車離合器殼體部件高壓壓鑄情況,重點(diǎn)對澆注系統(tǒng)進(jìn)行優(yōu)化設(shè)計(jì),分析了熔體填充模具時流動行為,通過改進(jìn)澆注系統(tǒng),鑄造缺陷得到顯著改善,而澆口變化對鑄件表面硬度不存在較大影響。
Jan Majernik研究了利用澆口幾何形狀提高鋁合金壓鑄件機(jī)械和結(jié)構(gòu)性能的可能性。在五組不同高度的內(nèi)澆口情況下生產(chǎn)了五套壓鑄件,并對每組鑄件進(jìn)行機(jī)械性能的檢查。結(jié)果表明,內(nèi)澆口高度是影響壓鑄件定性性能的基本結(jié)構(gòu)因素之一,決定了模腔填充速度和模腔填充方式,對表面硬度不存在較大的影響,但是會影響鑄件孔隙率。
B. D. Lee通過四腔體薄電子元件外殼的澆注系統(tǒng)設(shè)計(jì),研究了澆注系統(tǒng)結(jié)構(gòu)對該電子元件壓鑄成型后鑄件質(zhì)量的影響,提出外殼型腔最優(yōu)設(shè)計(jì)。結(jié)果表明,溢流槽末端排氣孔數(shù)量的增加有效降低了鑄件孔隙率,屈服強(qiáng)度及拉伸強(qiáng)度也因此增加。
上述研究表明,通過壓鑄件澆注系統(tǒng)、排溢系統(tǒng)和壓鑄件模具型腔等結(jié)構(gòu)設(shè)計(jì)影響壓鑄件成型質(zhì)量,在理清結(jié)構(gòu)變化與壓鑄件性能變化的對應(yīng)關(guān)系后,可以通過優(yōu)化結(jié)構(gòu)以實(shí)現(xiàn)對鑄件質(zhì)量的調(diào)控。以上研究結(jié)果同樣可適用于一體化壓鑄技術(shù),為一體化壓鑄件的結(jié)構(gòu)設(shè)計(jì)及優(yōu)化提供思路。
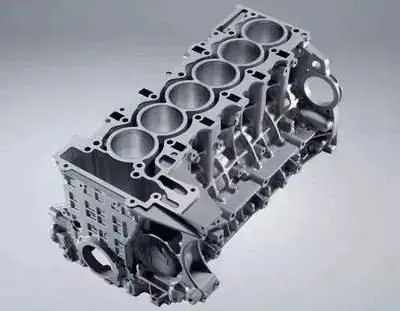
03 總結(jié)
本文介紹了一體化壓鑄工藝涉及的高性能鋁合金材料、高壓壓鑄工藝和壓鑄件結(jié)構(gòu)設(shè)計(jì)等關(guān)鍵技術(shù)新進(jìn)展,為一體化壓鑄技術(shù)發(fā)展提供參考。
一體化壓鑄技術(shù)發(fā)展需要高度重視免熱處理特性的新型鋁合金材料研發(fā),通過人工神經(jīng)網(wǎng)絡(luò)模型可以對鋁合金材料機(jī)械性能進(jìn)行預(yù)測,有助于新型鋁合金材料的探索,而要驗(yàn)證新型鋁合金材料的性能,則需要進(jìn)行實(shí)際試制并測試其性能。
除提高鋁合金材料綜合機(jī)械性能外,免熱處理性能也是當(dāng)前用于一體化壓鑄的鋁合金材料的關(guān)鍵研究方向。為避免成形后結(jié)構(gòu)件熱處理帶來的嚴(yán)重形變問題,需要通過理論和實(shí)踐相結(jié)合,多方面驗(yàn)證應(yīng)用免熱處理材料的壓鑄件的綜合機(jī)械性能。
一體化壓鑄技術(shù)來源于高壓壓鑄技術(shù)升級,真空系統(tǒng)的引入有效降低了高壓壓鑄固有的型腔內(nèi)氣體殘留問題。真空輔助的高壓壓鑄降低了壓鑄件孔隙率,壓鑄件機(jī)械性能也隨之改善。壓鑄過程中熱力學(xué)和動力學(xué)參數(shù)改變可以對壓鑄件質(zhì)量產(chǎn)生影響,正確配置加工參數(shù)可以保證壓鑄件性能。鑄造過程中,加工參數(shù)實(shí)時調(diào)節(jié)有利于提高一體化壓鑄件性能。
壓鑄件澆注系統(tǒng)、排溢系統(tǒng)和鑄件本身等結(jié)構(gòu)設(shè)計(jì)直接影響壓鑄件成型質(zhì)量,優(yōu)化設(shè)計(jì)關(guān)鍵環(huán)節(jié)可以控制壓鑄成型質(zhì)量。澆注系統(tǒng)中內(nèi)澆口的結(jié)構(gòu)和數(shù)量能影響鑄件孔隙率。而排溢系統(tǒng)中溢流槽及排氣孔位置的設(shè)計(jì),將影響鑄件的抗拉強(qiáng)度等機(jī)械性能。鑄件流道等結(jié)構(gòu)設(shè)計(jì)會影響到鑄件充填行為,對鑄件表面硬度等性能產(chǎn)生影響。
一體化壓鑄技術(shù)的發(fā)展要借助于壓鑄材料、壓鑄工藝和模具結(jié)構(gòu)等方面融合發(fā)展,為一體化壓鑄技術(shù)研究提供理論和技術(shù)基礎(chǔ)。由于能帶來顯著經(jīng)濟(jì)效益,目前新能源汽車輕量化領(lǐng)域中,車身一體化結(jié)構(gòu)壓鑄技術(shù)研究十分活躍,但仍有許多理論和實(shí)踐問題尚待解決,需要繼續(xù)深入此領(lǐng)域多項(xiàng)關(guān)鍵技術(shù)研究,以促進(jìn)一體化壓鑄技術(shù)更快發(fā)展和廣泛應(yīng)用。
-
乘用車金屬沖壓
2025-05-29 -
沖壓技術(shù)在電機(jī)疊片制造的應(yīng)用
2024-09-06 -
車身零部件包邊質(zhì)量控制要點(diǎn)
2024-09-05 -
輕量化技術(shù)——熱汽脹形工藝技術(shù)解析
2024-09-04
最新資訊
-
跨越速運(yùn)憑什么“圈粉”萬千客戶?“
2025-07-01 14:42
-
數(shù)智破局啟新篇?生態(tài)共生再啟程 —
2025-06-27 20:13
-
助力汽車零部件產(chǎn)線智能化升級,西門
2025-06-27 13:59
-
BBA集體轉(zhuǎn)向!放棄全面電動化
2025-06-26 17:32
-
比換柜省錢,比自研省心,西門子Xcel
2025-06-25 15:07