齒輪冷鍛成形在汽車齒形零件制造中的應用
2019-04-26 20:33:56· 來源:齒輪傳動
本文介紹了冷鍛成形技術(shù)在汽車齒形類零件制造中的應用,總結(jié)了各種齒形精密成形方法的關鍵 技術(shù),特別提到分流鍛造在齒形成形方面越來越廣泛的應用。前言冷鍛成形是一種優(yōu)質(zhì)、高效、低消耗的先進制造技術(shù),被廣泛地用于汽車零部件的大批量
本文介紹了冷鍛成形技術(shù)在汽車齒形類零件制造中的應用,總結(jié)了各種齒形精密成形方法的關鍵 技術(shù),特別提到分流鍛造在齒形成形方面越來越廣泛的應用。
前言
冷鍛成形是一種優(yōu)質(zhì)、高效、低消耗的先進制造技術(shù),被廣泛地用于汽車零部件的大批量生產(chǎn)中。隨著冷鍛工藝技術(shù)和精密模具制造技術(shù)的發(fā)展,汽車齒輪和齒形類零件的生產(chǎn)已越來越多地采用冷鍛成形。當前國外一臺普通轎車采用的冷鍛件總質(zhì)量(40—45)Kg,其中齒形類零件總質(zhì)量達10Kg以上。冷鍛成形的齒輪單件質(zhì)量可達1Kg以上、齒形精度可達(DIN) 7級。隨著汽車的輕量化和人們對環(huán)境保護越來越嚴格的要求,汽車齒輪制造業(yè)將更多地應用冷鍛成形技術(shù)。
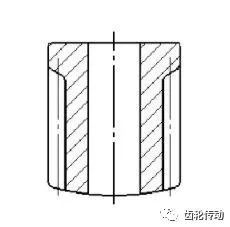
圖1:汽車起動齒輪冷鍛毛坯
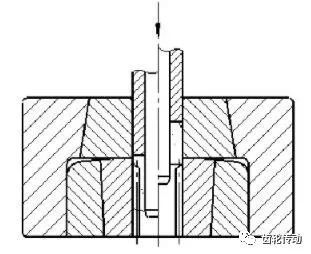
圖2:汽車起動齒輪擠壓模
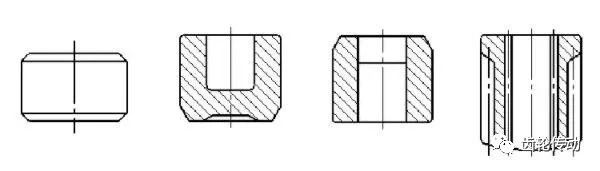
圖3:汽車起動齒輪冷鍛成形工藝
2.圓柱齒輪的擠壓成形
圓柱齒輪的正擠壓成形是應用最早的齒形成形工藝。典型零件是汽車起動電機起動齒輪(圖1)和汽車傳動軸花鍵。起動齒輪的模具結(jié)構(gòu)和工藝過程見(圖2、圖3)。由于冷擠壓過程是金屬在高應力下的塑性變形,因此,冷擠壓成形的起動齒輪組織致密,金屬纖維連續(xù),疲勞強度和耐磨性比切削加工的齒輪要高出許多。特別是冷擠成形的起動齒輪結(jié)構(gòu)上一端封閉,為輪齒提供了額外的抗彎強度,最適合于汽車起動機頻繁沖擊和高載荷工況下工作。齒輪正擠壓成形時,齒形凹??梢杂酶呔染€切割機床加工。當齒形擠壓模具采用高速鋼材料,模具齒形制造精度達到(DIN)6級,在批量生產(chǎn)條件下,齒輪成形精度穩(wěn)定達到(DIN) 8—9級??紤]到模具的彈性變形和磨損,在大批量生產(chǎn)時改用硬質(zhì)合金模具并合理設計冷鍛變形率,可使正擠壓齒輪的齒形精度進一步達到(DIN)7—7.5級。成形模的齒形設計要考慮冷鍛過程中模具的彈性變形和模具磨損的影響,對模具齒形加以必要的修正。由于在擠壓過程中模具曲率大的部分磨損速率大于曲率小的部分,因此,采用標準齒形的齒輪擠壓模齒頂處的磨損明顯大于齒面和齒根處的磨損。如果對齒形作適當修正(圖4),可使模具齒形獲得均勻磨損的效果,從而得到較長的模具壽命。正擠壓成形工藝的另一特出優(yōu)點是模具齒形由數(shù)控線切割加工得到,在少齒數(shù)齒輪加工時通過編程即可獲得理想齒形而不必擔心根切。在加工特殊齒形或修正齒形場合,采用數(shù)控線切割加工齒形比齒輪的展成加工或仿形加工更方便、更快捷、更正確。
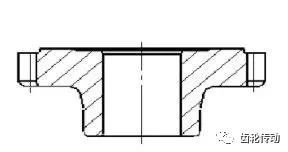
圖4:齒輪擠壓模的齒形修正
花鍵冷鍛成形是齒輪正擠壓成形的一個特例。漸開線花鍵的成形相當于擠壓一個較長的正齒輪,矩形花鍵的擠壓與漸開線花鍵的擠壓相似。從另一方面考慮,小模數(shù)正齒輪可采用分割漸開線花鍵軸的方法來得到(圖5)。
圖5:花鍵和小模數(shù)正齒輪的冷鍛成形
國內(nèi)外汽車起動齒輪絕大部分用冷鍛方法生產(chǎn)。本公司用冷擠壓工藝生產(chǎn)摩托車花鍵軸,并用分割漸開線花鍵軸的方法生產(chǎn)小模數(shù)正齒輪。小齒輪每月產(chǎn)量達數(shù)萬件,精度可達(DIN)7.5級,主要用于轎車起動電機行星減速系統(tǒng)。
齒輪正擠壓成形的缺點是成形齒坯的頭、尾有較大的塌角和過渡圓弧,因此齒輪兩端面切削余量大,材料利用率不高,也影響了生產(chǎn)效率的進一步提高。另外齒輪端面切削后容易殘留毛刺,而去毛刺是機加工中最傷腦筋的問題。另外,受擠壓變形率的限制,并考慮到模具制造尺寸和冷鍛壓力機能力等因素,齒輪正擠壓成形目前只應用于小規(guī)格小模數(shù)齒輪的制造。當然,比起切齒加工,齒輪擠壓成形無論是在質(zhì)量、效率和效益方面,都是一個飛躍。
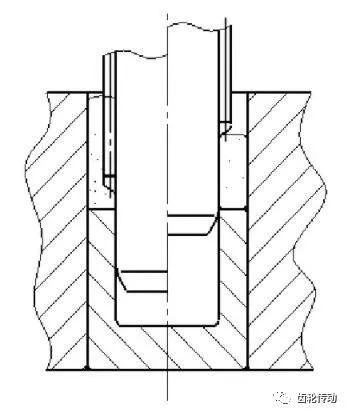
圖6:貫通內(nèi)齒輪的反擠壓成形
對于內(nèi)齒輪的制造,可用齒形沖頭反擠壓成形。用該工藝可制造貫通的內(nèi)齒輪(圖6),也可制造底部不通的內(nèi)齒輪(圖7)。在后一種場合,齒輪冷鍛成形不需要預加工退刀槽,因而在有限尺寸內(nèi)可保證制出最大限度的有效齒形,從而可優(yōu)化零部件結(jié)構(gòu),減小齒輪傳動系統(tǒng)的尺寸并提高齒輪強度。
當代,齒輪的擠壓成形技術(shù)已從正齒輪成形發(fā)展到了斜齒園柱齒輪和螺旋花鍵軸的擠壓成形,齒形精度已達到(DIN)7級,能充分滿足大部分汽車齒形零件的要求。冷擠壓成形的齒形零件應用已從汽車起動電機、汽車搖窗機等外圍部件發(fā)展到汽車轉(zhuǎn)向機、汽車變速箱等關鍵總成上。
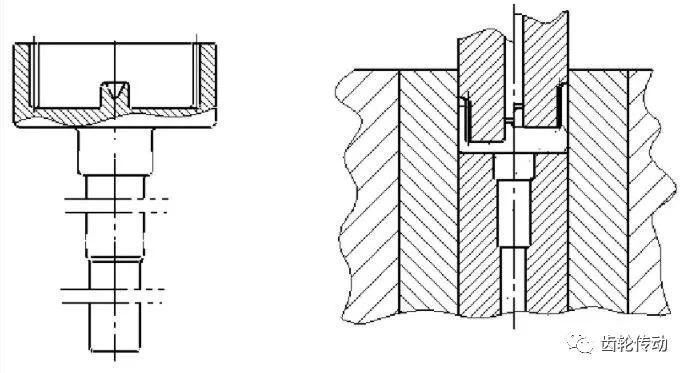
圖7:內(nèi)齒輪的反擠壓成形
3.傘齒輪閉塞冷鍛成形
傘齒輪的精密鍛造最早見于50年代德國的拜爾工廠,并在蒂森、B.L.W等公司得到廣泛的應用。上海汽車齒輪廠等在70年代就成功進行齒輪精密鍛造生產(chǎn)。但當時采用的是熱精鍛技術(shù),齒輪鍛造精度8—9級,主要應用于卡車和拖拉機工業(yè)。
在冷鍛和閉塞鍛造技術(shù)得到突破和發(fā)展后,傘齒輪的鍛造精度得到較大提高,已能滿足當代轎車工業(yè)的要求。目前,汽車工業(yè)發(fā)達國家的轎車、輕型車和微型車的行星齒輪、半軸齒輪(差速器齒輪總成)等直齒傘齒輪已廣泛采用冷鍛和閉塞冷鍛工藝生產(chǎn),螺傘齒輪的精密鍛造也在開發(fā)中。江蘇飛船齒輪股份有限公司和太平洋精密鍛造公司等引進國外先進的專用冷鍛壓力機,并引進國外傘齒輪閉塞冷鍛成形技術(shù),完成了轎車、輕型車行星和半軸齒輪的開發(fā)。精鍛齒輪產(chǎn)品已得到多個汽車廠的確認并投入了批量生產(chǎn)。傘齒輪閉塞冷鍛成形原理見圖(8)。
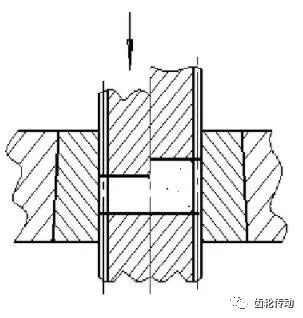
圖8:錐齒輪的閉塞冷鍛成形
通常,傘齒輪的切削成形往往采用刨齒機等作展成加工,而傘齒輪精鍛成形模的成形電極可用數(shù)控加工和展成加工二種方法制造。二種不同方法加工出的齒輪相互嚙合時有可能會有接觸面不好的負面影響,因而,精鍛傘齒輪推薦成對使用。
閉塞冷鍛成形的齒形精度可滿足一般汽車的使用要求。對精度有較高要求時,在齒輪閉塞成形后進行等溫退火,再在精密成形模具作一次冷精整,可穩(wěn)定地獲得DIN 7級的齒形成形精度。由于冷精整變形量小,并為了提高齒面質(zhì)量,齒坯精整前用少量稀油噴霧潤滑,無須作磷、皂化處理。由于齒坯進行了等溫退火,后續(xù)滲碳淬火時齒形變形量較小而且規(guī)律性好,因此可根據(jù)淬火變形規(guī)律對鍛造齒形進行修正,最終使熱處理后精度不下降。
4.汽車齒輪的分流鍛造
圓柱齒輪的成形工藝還有閉式冷鐓鍛成形等(圖9)。
由于齒輪冷鐓鍛成形時在齒頂?shù)募饨遣拷饘倭鲃訔l件不好,單用加大鍛造力的方法不能有效地改善齒尖部的充填效果。而加大鍛造力的負面效應是使模具壽命大幅度下降。鍛造應力的加大還使模具彈性變形增加,最終使鍛件的齒形精度下降。由于閉模鍛造的特點,當齒坯的下料精度較低時,毛坯體積少量超標就會引起鍛造應力的急劇上升,最終造成模具的破損失效。
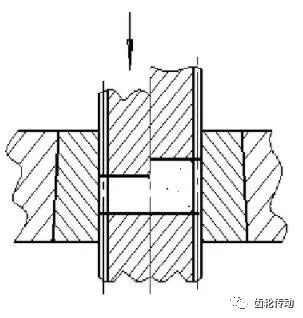
圖9:齒輪的閉式鐓鍛成形
國內(nèi)外精密鍛造專家開始將分流鍛造理論應用于正齒輪和螺旋齒輪的冷鍛成形(4)(5)(6)。分流鍛造的主要原理是在毛坯或模具的成形部分建立一個材料的分流腔或分流通道(圖10)。鍛造過程中,材料在充滿型腔的同時,部分材料流向分流腔或分流通道。分流腔或分流通道能容納少量體積超標的材料,而不致于造成鍛造應力急劇增加的后果。更主要的是,通過對分流路徑的合理設計,使鍛造過程中金屬的流動有利于齒形尖角處的充填,從而可在較小的成形應力下得到充滿程度較好的齒形。分流鍛造技術(shù)的應用,使較高精度齒輪的少、無切削加工迅速達到了產(chǎn)業(yè)化規(guī)模。
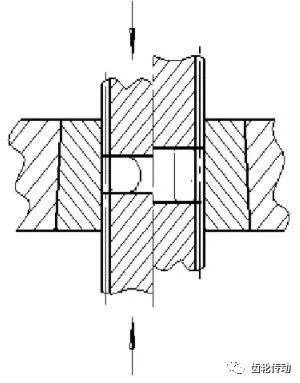
圖10:齒輪的分流鍛造成形
本公司從日本Nichidai公司引進齒輪分流鍛造工藝技術(shù)和模具技術(shù),開發(fā)轎車手動變速箱倒擋齒輪零件(圖11)。該齒輪的成形原理見(圖12),產(chǎn)品冷鍛工藝過程見(圖13)。由于倒擋齒輪的齒面有一定的錐度要求,因此,齒形成形后要對齒面進行一次錐度整形。該齒輪成形和整形工序在日本小松L1C —6300KN冷鍛壓力機上完成。
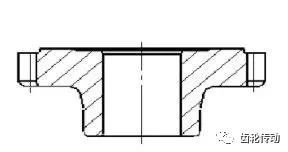
圖11:倒擋齒輪零件圖
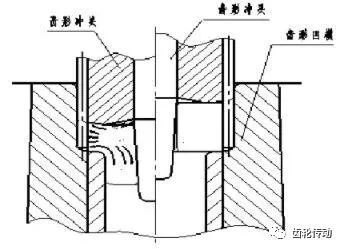
圖12:倒擋齒輪的分流成形
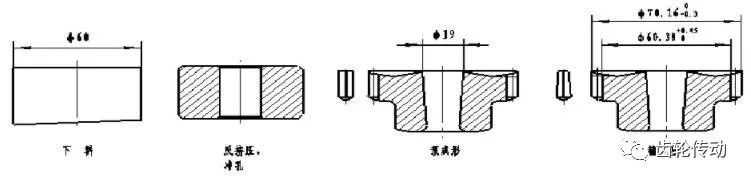
圖13:倒擋齒輪冷鍛成形工藝
試制的倒擋齒輪的齒形和齒向精度見表1—表3。
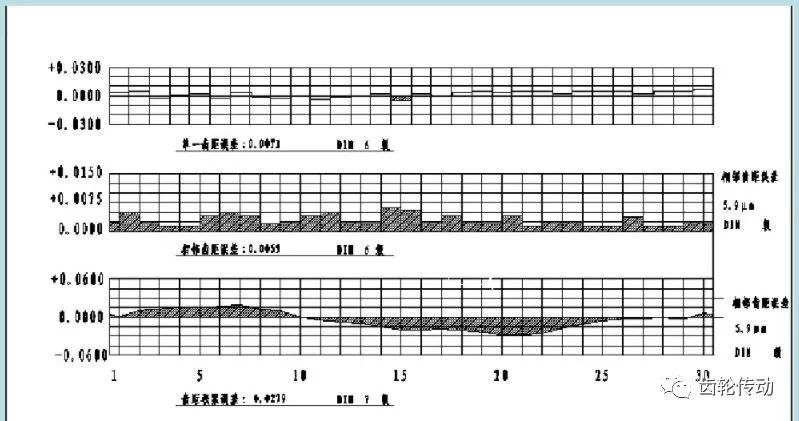
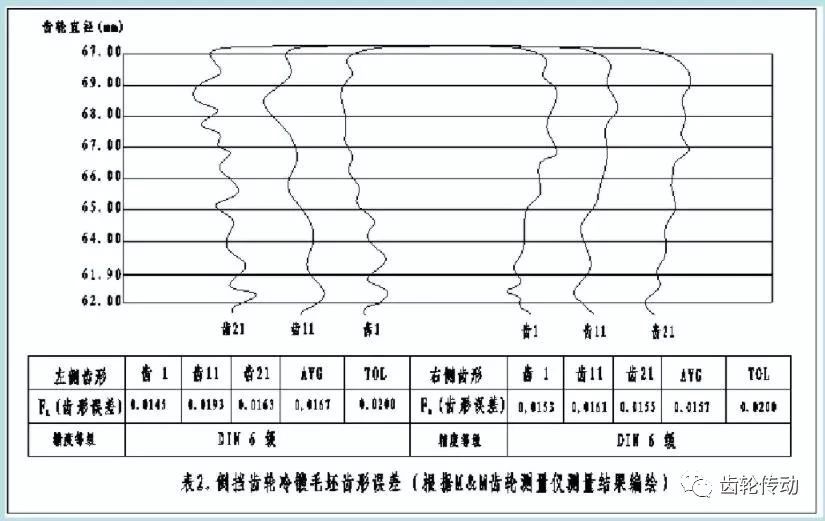
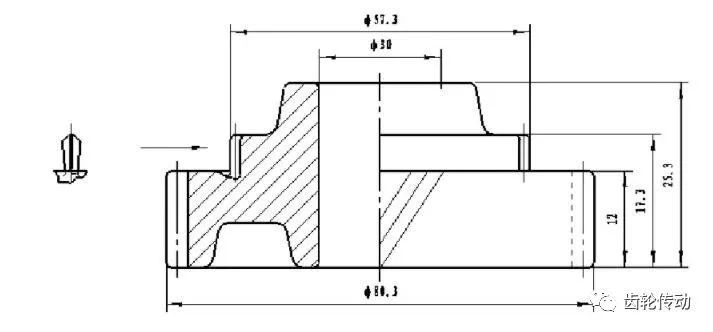
通過倒擋齒輪的分流鍛造試驗,我們認識到分流路徑的設計是齒輪分流鍛造成形的關鍵。對于每一個具體的齒輪,可有不同的設計方案,但基本原理是要使材料在鍛造時盡量沿齒向有一定的滑動,才能在盡量小的成形應力下得到充滿的齒形。
另外,采用多工位溫鍛或熱精鍛成形作為倒擋齒輪的預成形,而以冷鍛精整來獲得最終的齒形精度,已成為當前大批量生產(chǎn)汽車倒擋齒輪的最經(jīng)濟的方案。但溫—冷聯(lián)合成形工藝的設備投資相當大,投資后如得不到幾百萬件鍛件訂單的支持,則將陷入虧損的窘境。相比之下倒擋齒輪的全冷鍛成形,可在一臺設備上通過更換模具完成多道工序,設備投資較小,生產(chǎn)成本低于切削加工,適合于多品種中、小批量生產(chǎn)。
與擠壓齒輪相比,分流鍛造的齒輪容易獲得較大的尺寸。齒輪分流鍛造成形后如追加一次冷精整,同樣獲得較好的精度,可完全滿足汽車變速箱齒輪的精度要求。另外,分流鍛造的齒輪端面余量小,材料利用率高。某些情況下,齒形端面可不加工,避免了車削毛刺的發(fā)生。
分流鍛造技術(shù)主要應用于汽車變速箱齒輪。除倒擋齒輪和行星齒輪外,變速齒坯接合齒的成形和接合齒環(huán)等齒形零件等都有了冷鍛成形的工藝和大批量生產(chǎn)的經(jīng)驗。在國外,變速箱螺旋齒輪與接合齒的整體精鍛也有了成功的經(jīng)驗(圖14)。
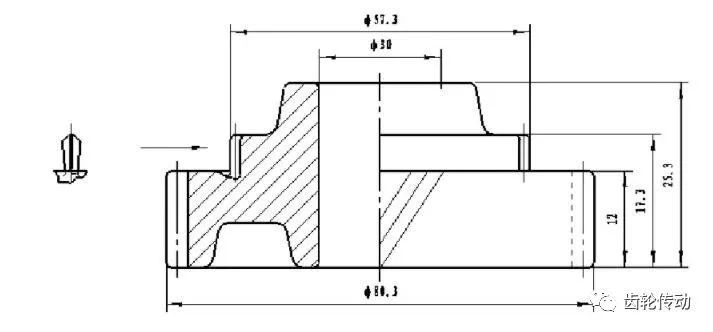
圖14:變速箱螺旋齒輪與結(jié)合齒的整體精鍛毛坯
5.其它齒輪鍛造技術(shù)
除閉塞成形外,冷擺輾技術(shù)也可應用于汽車傘齒輪的精密成形,并用于鋼質(zhì)同步器齒環(huán)的齒形成形。冷擺輾在汽車齒形零件制造方面最成功的應用當屬汽車轉(zhuǎn)向器變速比齒條的精密擺輾成形。由于變速比齒條的齒形模數(shù)和壓力角是變動的,用傳統(tǒng)的切齒方法加工極其困難而且不經(jīng)濟。冷鍛模具由于齒形用數(shù)控方法加工,所以變速比齒形對模具加工沒有加工理論和加工成本上的難題。但普通冷鍛對于較長的齒條成形須要增加預成形工序,并且有齒頂難以充滿和模具壽命低的缺點。擺輾機通過調(diào)整擺頭可獲得沿齒條長度方向擺動的軌跡,有利于齒條的逐次成形。該技術(shù)為瑞士Schmid公司和德國ZF公司合作開發(fā)并應用至今。精密冷擺輾的齒條尺寸精度不超過0.04mm,模具壽命超過1.5萬件。目前,冷擺輾工藝仍是是轉(zhuǎn)向器變速比齒條最經(jīng)濟的制造方法。
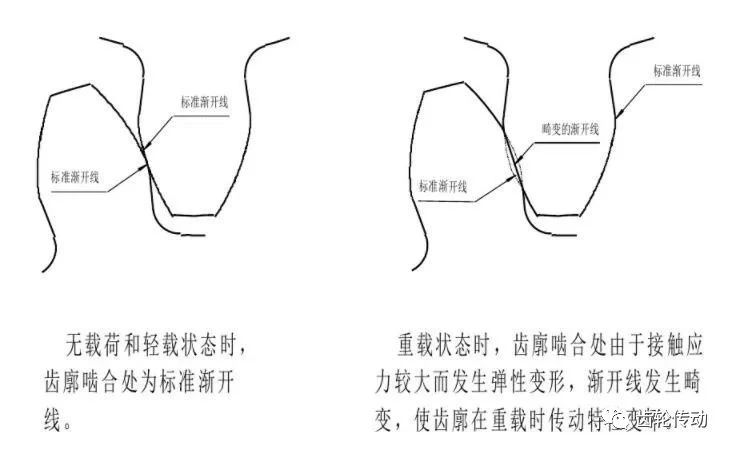
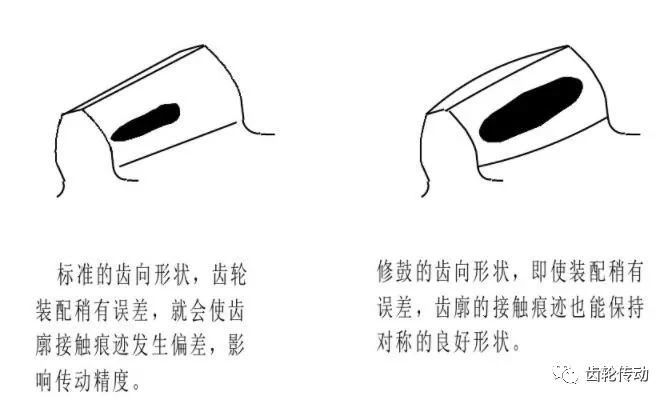
6.結(jié)論
過去,由于國內(nèi)汽車零部件工廠生產(chǎn)規(guī)模小而分散,齒形零件的生產(chǎn)達不到冷鍛生產(chǎn)的經(jīng)濟規(guī)模,因此,汽車工業(yè)中大部分齒輪和齒形零件停留在傳統(tǒng)的切齒加工落后狀態(tài)。隨著我國汽車工業(yè)的飛躍發(fā)展,汽車零部件制造面臨全球采購的競爭,提高產(chǎn)品質(zhì)量和降低制造成本將被提到最重要位置考慮。體現(xiàn)優(yōu)質(zhì)、高效、低成本的齒形零件冷鍛成形技術(shù)一定會在汽車零部件生產(chǎn)中得到推廣應用。
舉報 0
收藏 0
分享 110
-
乘用車金屬沖壓
2025-05-29 -
沖壓技術(shù)在電機疊片制造的應用
2024-09-06 -
車身零部件包邊質(zhì)量控制要點
2024-09-05 -
輕量化技術(shù)——熱汽脹形工藝技術(shù)解析
2024-09-04
最新資訊
-
跨越速運憑什么“圈粉”萬千客戶?“
2025-07-01 14:42
-
數(shù)智破局啟新篇?生態(tài)共生再啟程 —
2025-06-27 20:13
-
助力汽車零部件產(chǎn)線智能化升級,西門
2025-06-27 13:59
-
BBA集體轉(zhuǎn)向!放棄全面電動化
2025-06-26 17:32
-
比換柜省錢,比自研省心,西門子Xcel
2025-06-25 15:07