基于達索系統(tǒng)SIMULIA Isight的汽車扭轉(zhuǎn)梁參數(shù)化設(shè)計方法
2019-03-14 16:02:55· 來源:達索系統(tǒng)
許諾,曹露芬,李華斌,翁洋,王光耀,孫成智上海汽車集團股份有限公司乘用車技術(shù)中心摘要:本文提出基于Isight的參數(shù)化設(shè)計方法,優(yōu)化得到的扭轉(zhuǎn)梁滿足操穩(wěn)性能和耐久性能的要求,同時方案具備較好的輕量化意義。利用Isight軟件,集成SF
許諾,曹露芬,李華斌,翁洋,王光耀,孫成智
上海汽車集團股份有限公司乘用車技術(shù)中心
摘要:本文提出基于Isight的參數(shù)化設(shè)計方法,優(yōu)化得到的扭轉(zhuǎn)梁滿足操穩(wěn)性能和耐久性能的要求,同時方案具備較好的輕量化意義。利用Isight軟件,集成SFE、Nastran、ncode、Abaqus,完成剛度、耐久及強度多目標自動化優(yōu)化,縮短了90%的優(yōu)化周期。
關(guān)鍵字:扭轉(zhuǎn)梁;參數(shù)化;多目標自動化優(yōu)化
0 前言
當(dāng)前,汽車行業(yè)競爭愈發(fā)激烈,如何縮短汽車產(chǎn)品的設(shè)計周期,提高設(shè)計效率,成為所有汽車企業(yè)研究的重點[1]。王平等[2]運用多目標遺傳算法結(jié)合多學(xué)科協(xié)同優(yōu)化對車身吸能部件板厚及車門屈服應(yīng)力作為變量,進行多目標優(yōu)化設(shè)計;李錦等[3]基于靈敏度分析方法,以副車架部件厚度作為優(yōu)化變量,進行強度和模態(tài)多目標優(yōu)化;蔣榮超等[4]基于網(wǎng)格變形技術(shù),對開口梁進行了形狀變量和厚度變量設(shè)計,以質(zhì)量、疲勞、剛度為優(yōu)化目標進行了優(yōu)化設(shè)計。而對于結(jié)構(gòu)較復(fù)雜的汽車扭轉(zhuǎn)梁結(jié)構(gòu),國內(nèi)外關(guān)于其選型及形狀參數(shù)化設(shè)計的研究則少見報道[1-5]。
扭轉(zhuǎn)剛度是扭轉(zhuǎn)梁重要的固有性能之一,決定了扭轉(zhuǎn)梁在輪心反向跳動時抗扭轉(zhuǎn)能力。反映到整車車輛特性上,扭轉(zhuǎn)梁自身的扭轉(zhuǎn)可以有效降低車身側(cè)傾,扭轉(zhuǎn)剛度越大,對車身側(cè)傾減小程度越大;但是扭轉(zhuǎn)剛度過大,會影響整車平順性。在不同車型開發(fā)過程中,整車操穩(wěn)性能要求的側(cè)傾剛度隨軸荷不同而要求不同。對于高軸荷車,因為側(cè)傾剛度要求較高,帶來扭轉(zhuǎn)剛度和彈簧剛度要求較大。扭轉(zhuǎn)剛度增大的方法從扭梁結(jié)構(gòu)方面,主要包括形狀和尺寸變量,變量提升都會帶來質(zhì)量及成本的提升。因此,滿足輕量化要求的扭轉(zhuǎn)梁后橋需要具備在質(zhì)量較輕的同時具備較大的扭轉(zhuǎn)剛度。
1 扭轉(zhuǎn)梁截面參數(shù)化模型建立
由扭轉(zhuǎn)梁剛度公式可得到關(guān)鍵因子為外闊尺寸、尺寸變量及形狀變量。
如圖1所示閉口梁參數(shù)化模型,可實現(xiàn)形狀一定范圍內(nèi)快速變化。
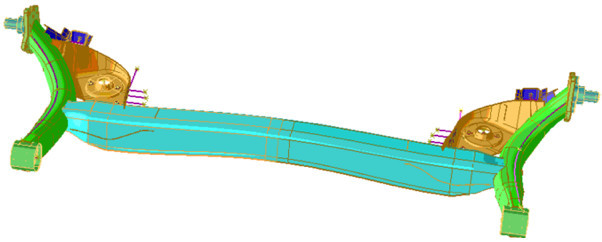
圖1 參數(shù)化模型
Fig.1 Parametric model
如圖2,3所示,開口梁參數(shù)化變量主要包括外闊尺寸、形狀變量、尺寸變量。形狀變量包括三個截面的高度和寬度,第二截面和第三截面的位置,以及開口方向(開口向下到開口向前連續(xù)變化),這些變量共同決定了橫梁應(yīng)力的趨勢及剛度大小。尺寸變量包括橫梁和縱臂厚度,橫梁厚度直接影響扭梁剛度及耐久性能;而縱臂厚度直接影響濫用性能。
圖2 截面選取定義
Fig.2 Section Selection Definition
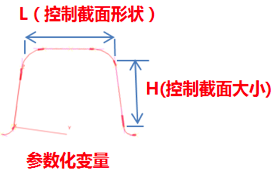
圖3 截面參數(shù)化示意圖
Fig.3 Section parametric diagram
扭轉(zhuǎn)梁參數(shù)化模型需覆蓋車型的輪距范圍,并滿足現(xiàn)有車身連接點與輪心相對位置的要求。如表1,對輪距和縱臂長度實現(xiàn)范圍選擇。輪距范圍為1400-1800mm。縱臂長度,范圍為400-500mm。
表1 參數(shù)化變量取值范圍
Table.1 Parametric value range
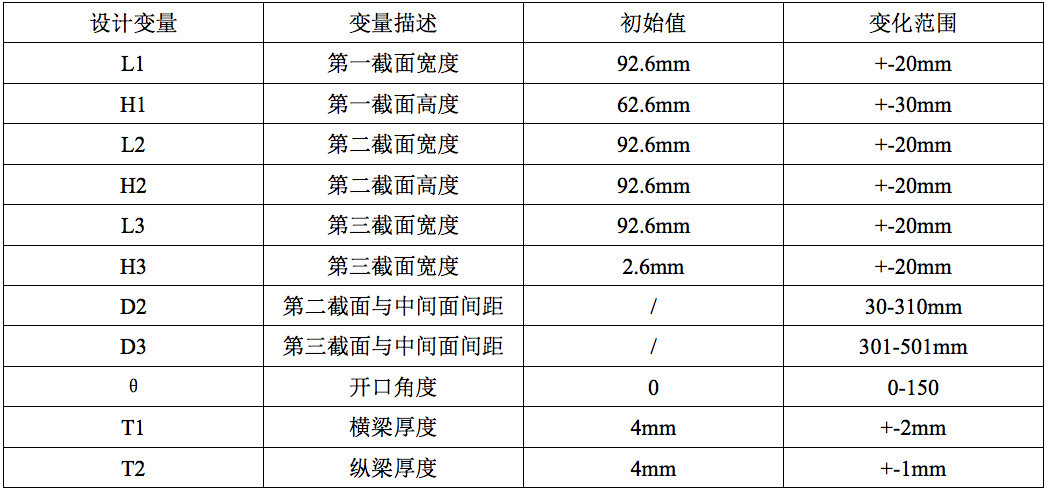
2 基于Isight設(shè)計流程
DOE設(shè)計方法選擇優(yōu)化超拉丁方方法。拉丁方試驗設(shè)計將因素按水平豎排一個隨機矩陣,即拉丁方矩陣,在同一列中任何因素的水平均無重復(fù)。如圖4所示,優(yōu)化拉丁方試驗設(shè)計方法采用正交性較好的初始解,綜合考慮拉丁方矩陣的正交性和均勻性。
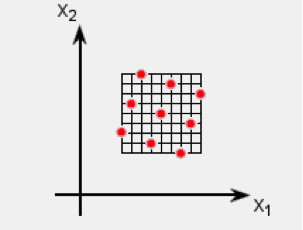
圖4 優(yōu)化超拉丁方方法選點方法
Fig.4 Optimal Latin Hypercube sampling method
分別對9個形狀變量及2個尺寸變量按照優(yōu)化超拉丁采樣試驗,共1000個試驗以求得最優(yōu)解。優(yōu)化工況為剛度要、耐久、濫用變形性能要求,優(yōu)化目標為質(zhì)量最小。優(yōu)化方法如下:
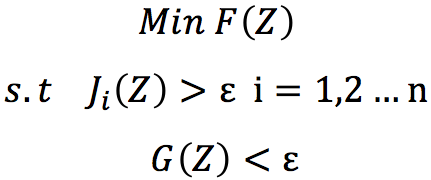
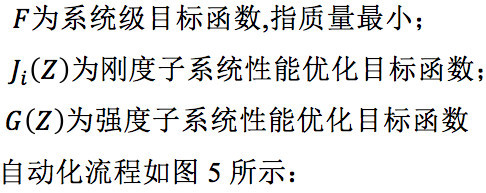

圖5 自動化優(yōu)化流程
Fig.5 Automatic optimization flow
3 扭轉(zhuǎn)梁優(yōu)化最優(yōu)結(jié)構(gòu)
通過DOE優(yōu)化,得到了形狀和尺寸變量最優(yōu)解,其結(jié)果如表2所示:
表2 參數(shù)最優(yōu)解
Table.2 Parametric optimized value
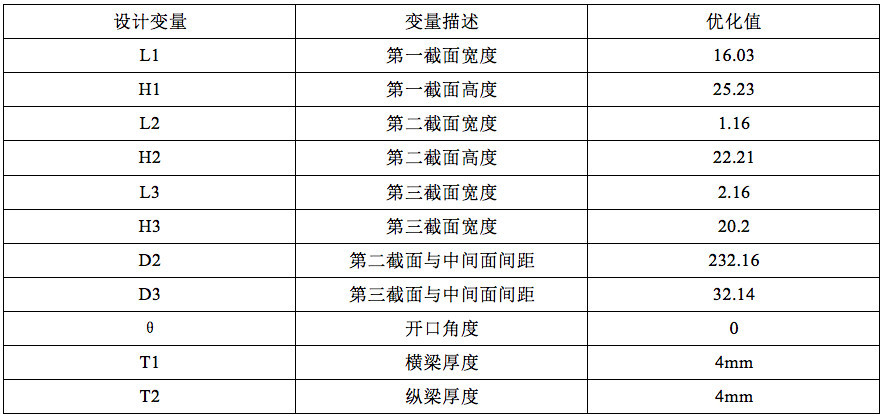
如圖6中原結(jié)構(gòu)與優(yōu)化結(jié)構(gòu)對比圖所示,紅色部分為優(yōu)化結(jié)構(gòu),藍色部分為原結(jié)構(gòu),可以發(fā)現(xiàn)優(yōu)化的結(jié)構(gòu)橫梁兩端抬高,更強的抗扭能力有效降低橫梁應(yīng)力,耐久性能更優(yōu)。相較于傳統(tǒng)的扭轉(zhuǎn)梁優(yōu)化設(shè)計流程,設(shè)計周期從3周減少為2天,縮短了90%的優(yōu)化周期,極大地提升了扭轉(zhuǎn)梁設(shè)計的周期與效率。
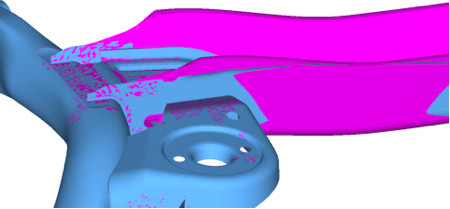
圖6 優(yōu)化結(jié)構(gòu)對比圖
Fig.6 base and optimized structure diagram
4 最優(yōu)參數(shù)性能驗證
扭轉(zhuǎn)梁性能要求主要包括操穩(wěn)及耐久性能。其中操穩(wěn)對扭轉(zhuǎn)梁結(jié)構(gòu)件的要求可以分解到剛度要求上,剛度主要包括扭轉(zhuǎn)剛度、縱向剛度、側(cè)向剛度、垂向剛度、彈簧安裝點剛度、減震器安裝點剛度。而扭梁扭轉(zhuǎn)剛度和彈簧剛度決定了扭轉(zhuǎn)梁后懸架的側(cè)傾剛度,側(cè)向剛度決定了后懸架的橫向剛度。
從表3中性能結(jié)果表可見,包括扭轉(zhuǎn)剛度、側(cè)向剛度、垂向剛度、彈簧安裝點剛度、減震器安裝點剛度全部滿足目標值。
表3 性能結(jié)果表
Table.3 Function result
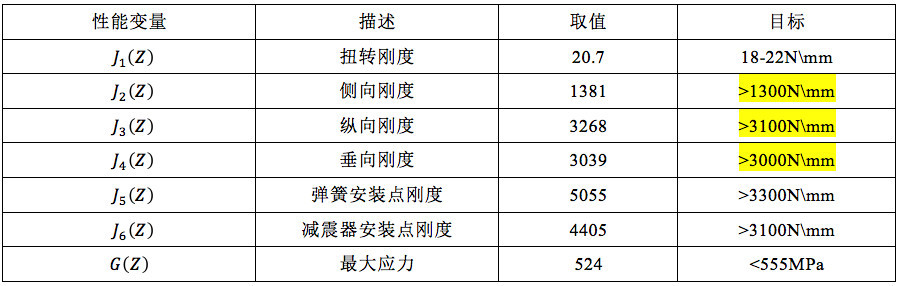
優(yōu)化方案的試制樣件,經(jīng)過臺架考核后,可以看到試驗結(jié)果均滿足20萬次的目標值,如表4和圖7所示。因此,該優(yōu)化方案可以同時滿足低頻扭轉(zhuǎn)耐久壽命要求。
表4 臺架試驗結(jié)果
Table.3 Rig-test result
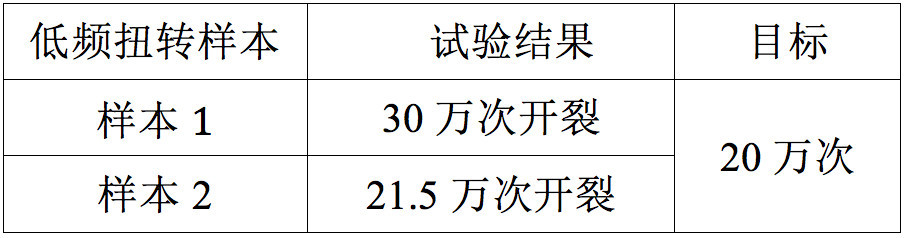
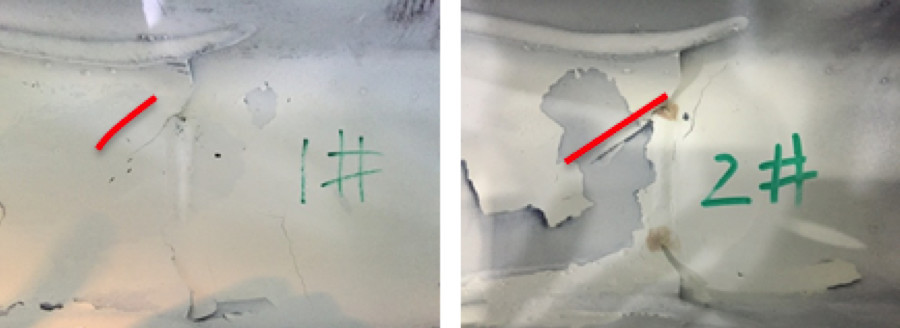
圖7 臺架驗證
Fig.7 Rig-test validation
綜上所述,基于Isight的參數(shù)化設(shè)計而得的汽車扭轉(zhuǎn)梁優(yōu)化結(jié)構(gòu),其操穩(wěn)及耐久性能都得到優(yōu)化的同時,輕量化意義也得到了進一步提升。
5 結(jié)論
(1)基于Isight的參數(shù)化設(shè)計方法優(yōu)化得到的扭轉(zhuǎn)梁,經(jīng)過臺架驗證,發(fā)現(xiàn)扭轉(zhuǎn)剛度、側(cè)向剛度、垂向剛度、彈簧安裝點剛度、減震器安裝點剛度,以及耐久性能全部滿足要求,同時方案具備較好的輕量化意義。
(2)基于Isight的汽車扭轉(zhuǎn)梁參數(shù)化設(shè)計方法,相較于傳統(tǒng)的扭轉(zhuǎn)梁優(yōu)化設(shè)計流程,縮短了90%的優(yōu)化周期,極大地提升了扭轉(zhuǎn)梁設(shè)計的周期與效率。
參考文獻
[1] 宋凱,段利斌,陳濤,陳艾國.全參數(shù)化概念車身協(xié)同開發(fā)與快速化結(jié)構(gòu)設(shè)計研究[J].中國機械工程,2014,3(25):6
Song Kai, Duan Libin, Chen Tao, Chen Aiguo. Collaborative Development and Rapid Structure Design based on Full Parametric Concept Car Body[J].China Mechanical Engineering,2014,3(25):6
[2] 王平,鄭松林,吳光強.基于協(xié)同優(yōu)化和多目標遺傳算法的車身結(jié)構(gòu)多學(xué)科優(yōu)化設(shè)計[J].機械工程學(xué)報,2011,1(47):2
Wang Ping, Zheng Songlin,Wu Guangqiang. Multidisciplinary Design Optimization of Vehicle Body Structure based on.Collaborative Optimization and Multi-objective Genetic Algorithm[J]. Journalof China Mechanical Engineering,2011,1(47):2
[3] 李錦,蘇小平,王宏楠,陳宇暉,張才偉.基于靈敏度分析的轎車副車架輕量化研究[J].機械科學(xué)與技術(shù),2013,11(32):11
Li Jin,Su Xiaoping,Wang Hongnan,Chen Yuhui,Zhang Caiwei.Study on the Lightweight of Car Subframe based on the Sentivity Analysis Method[J].Mechanical Science and Technology for Aerospace Engineering,2013,11(32):11
[4] 蔣榮超,王登峰,秦民,蔣永峰.基于疲勞壽命的轎車后懸架扭轉(zhuǎn)梁輕量化設(shè)計[J].吉林大學(xué)學(xué)報(工學(xué)版),2016,1(46):1
Jiang Rongchao, Wang Dengfeng, Qing Ming, Jiang Yongfeng.Lightweight design of twist beam of rear suspension of passenger carbased on fatigue life. Journal of Jilin University (Engineering and Technology Edition) [J],2016,1(46):1
[5] Georgios Papaioannou, Dimitrios Koulocheris. An approach for minimizing the number of objectivefunctions in the optimization of vehicle suspension systems. Journal of Soundand Vibration[J]. 2018,435:149-169
[6] 李劍如.扭轉(zhuǎn)梁扭轉(zhuǎn)剛度的理論計算方法研究[J]. 機械強度, 2015,2.215-225
Li jianru. Research on the method of torsion stiffness calculation in theory for twist beam [J]. Journal of Mechanical Strength, 2015, 2.215-225
舉報 0
收藏 0
分享 144
-
助力汽車零部件產(chǎn)線智能化升級,西門子Xcelerat
2025-06-27 -
BBA集體轉(zhuǎn)向!放棄全面電動化
2025-06-26 -
西門子SiePA斬獲麒麟認證,服務(wù)能力再升級!
2025-06-24 -
Geega產(chǎn)品圖譜 | Geega OS 工業(yè)操作系統(tǒng)
2025-06-23
編輯推薦
最新資訊
-
跨越速運憑什么“圈粉”萬千客戶?“
2025-07-01 14:42
-
數(shù)智破局啟新篇?生態(tài)共生再啟程 —
2025-06-27 20:13
-
助力汽車零部件產(chǎn)線智能化升級,西門
2025-06-27 13:59
-
BBA集體轉(zhuǎn)向!放棄全面電動化
2025-06-26 17:32
-
比換柜省錢,比自研省心,西門子Xcel
2025-06-25 15:07