機(jī)器人滾邊質(zhì)量缺陷的仿真分析與改善措施
2019-03-11 22:47:12· 來源:文/王強(qiáng) 鍛造與沖壓
根據(jù)某車型后背門總成零件在滾邊過程中出現(xiàn)的外觀質(zhì)量缺陷,應(yīng)用CAE仿真分析的方法對(duì)機(jī)器人滾邊工藝過程進(jìn)行模擬分析,提出了質(zhì)量改進(jìn)方案并驗(yàn)證有效,對(duì)后續(xù)車型機(jī)器人滾邊質(zhì)量的改進(jìn)過程提供了指導(dǎo)方法。機(jī)器人滾邊工藝主要指汽車門、
根據(jù)某車型后背門總成零件在滾邊過程中出現(xiàn)的外觀質(zhì)量缺陷,應(yīng)用CAE仿真分析的方法對(duì)機(jī)器人滾邊工藝過程進(jìn)行模擬分析,提出了質(zhì)量改進(jìn)方案并驗(yàn)證有效,對(duì)后續(xù)車型機(jī)器人滾邊質(zhì)量的改進(jìn)過程提供了指導(dǎo)方法。
機(jī)器人滾邊工藝主要指汽車門、蓋等開閉件的內(nèi)外板合裝采用的一種連接工藝,即應(yīng)用工業(yè)機(jī)器人持滾邊工具端將外板零件分序向內(nèi)折彎包裹內(nèi)板零件,以獲得一定的連接強(qiáng)度并保證總成制件的尺寸及外觀質(zhì)量,如圖1所示。本文主要結(jié)合一汽轎車某車型后背門總成制件在滾邊過程中產(chǎn)生的表面波浪缺陷,簡述了機(jī)器人滾邊的工藝過程,并利用有限元分析軟件對(duì)在不同滾邊角度下制件壓合邊彎曲變形情況進(jìn)行分析,最終獲得最優(yōu)的滾邊壓合角度,改進(jìn)產(chǎn)品外觀質(zhì)量。

圖1 機(jī)器人滾邊工位
缺陷描述
機(jī)器人滾邊過程中會(huì)產(chǎn)生各種類型缺陷,對(duì)此應(yīng)分析缺陷的具體類型,并針對(duì)不同類型缺陷找出解決問題的辦法。本文所述某車型后背門壓合總成,滾邊壓合后上邊緣邊存在嚴(yán)重的波浪缺陷,白車身AUDIT評(píng)審為B類缺陷,整車油漆后缺陷同樣可見,嚴(yán)重影響整車外觀質(zhì)量,如圖2所示。
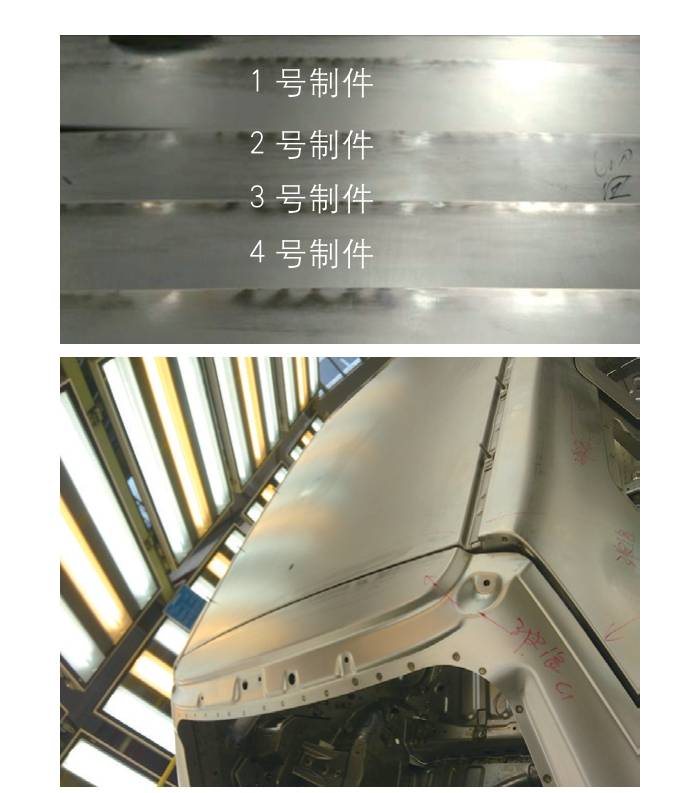
圖2 后背門總成上邊緣波浪缺陷及白車身評(píng)審結(jié)果
其評(píng)價(jià)方法為:⑴白車身評(píng)審者使用油石在制件表面沿固定方向反復(fù)輕摩擦,觀察表面即可看出缺陷;⑵觀察者在燈光隧道區(qū),觀察車門在燈帶下的反光情況即可看出缺陷。
滾邊工藝過程
根據(jù)后背門外板沖壓工藝規(guī)劃,外板上邊緣翻邊角度為120°,壓合采用三序滾邊成形工藝,后背門上邊緣具體滾邊序數(shù)及滾邊角度如表1所示,分別完成120°~65°第一序滾邊、65°~30°第二序滾邊、30°~0°第三序滾邊,通過三序滾邊,最終完成邊部壓實(shí)。其中,第一序滾邊和第二序滾邊為預(yù)翻邊,第三序滾邊為終翻邊。
在實(shí)際滾邊過程中發(fā)現(xiàn),預(yù)翻邊工序中外板翻邊波浪已經(jīng)產(chǎn)生,第一序及第二序滾邊后壓合邊波浪較大,如圖3所示。分析原因可能是預(yù)翻邊的角度過大(第一序滾邊角度大于50°),翻邊區(qū)域進(jìn)行大角度滾邊時(shí),較大變形量產(chǎn)生的內(nèi)應(yīng)力無法釋放,造成波浪起皺。此時(shí),應(yīng)考慮減小滾邊角度,合理分配每一序滾邊的變形量,減小滾邊波浪的產(chǎn)生。
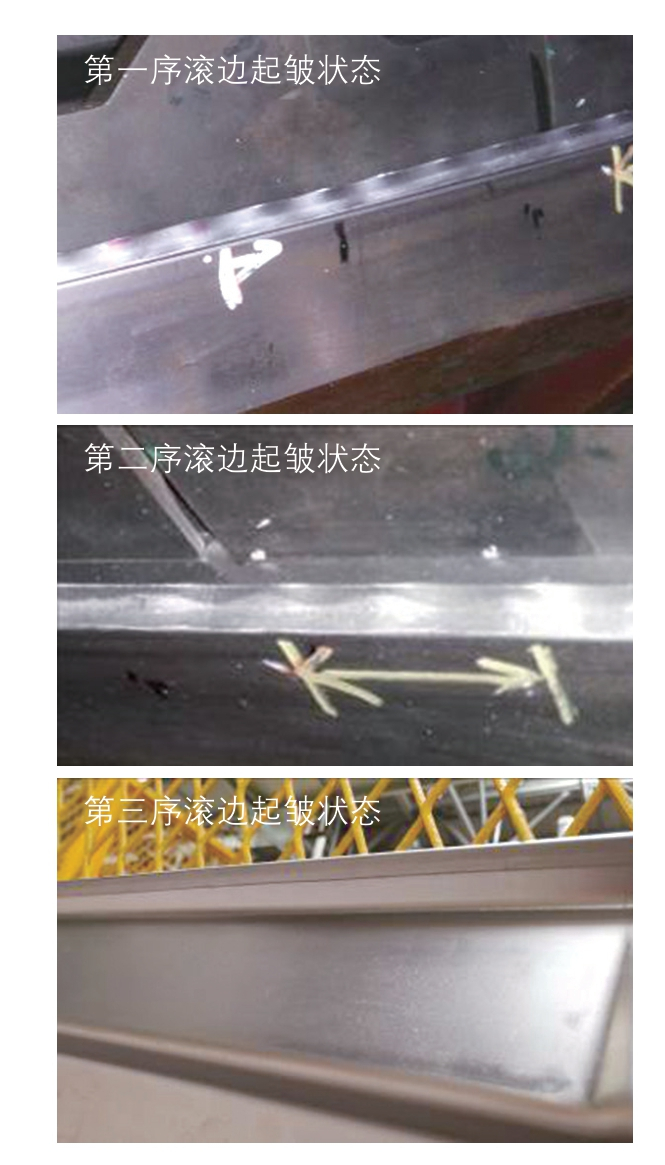
圖3 外板各工序翻邊波浪缺陷
滾邊仿真模型建立及角度優(yōu)化
滾邊CAE仿真模型建立
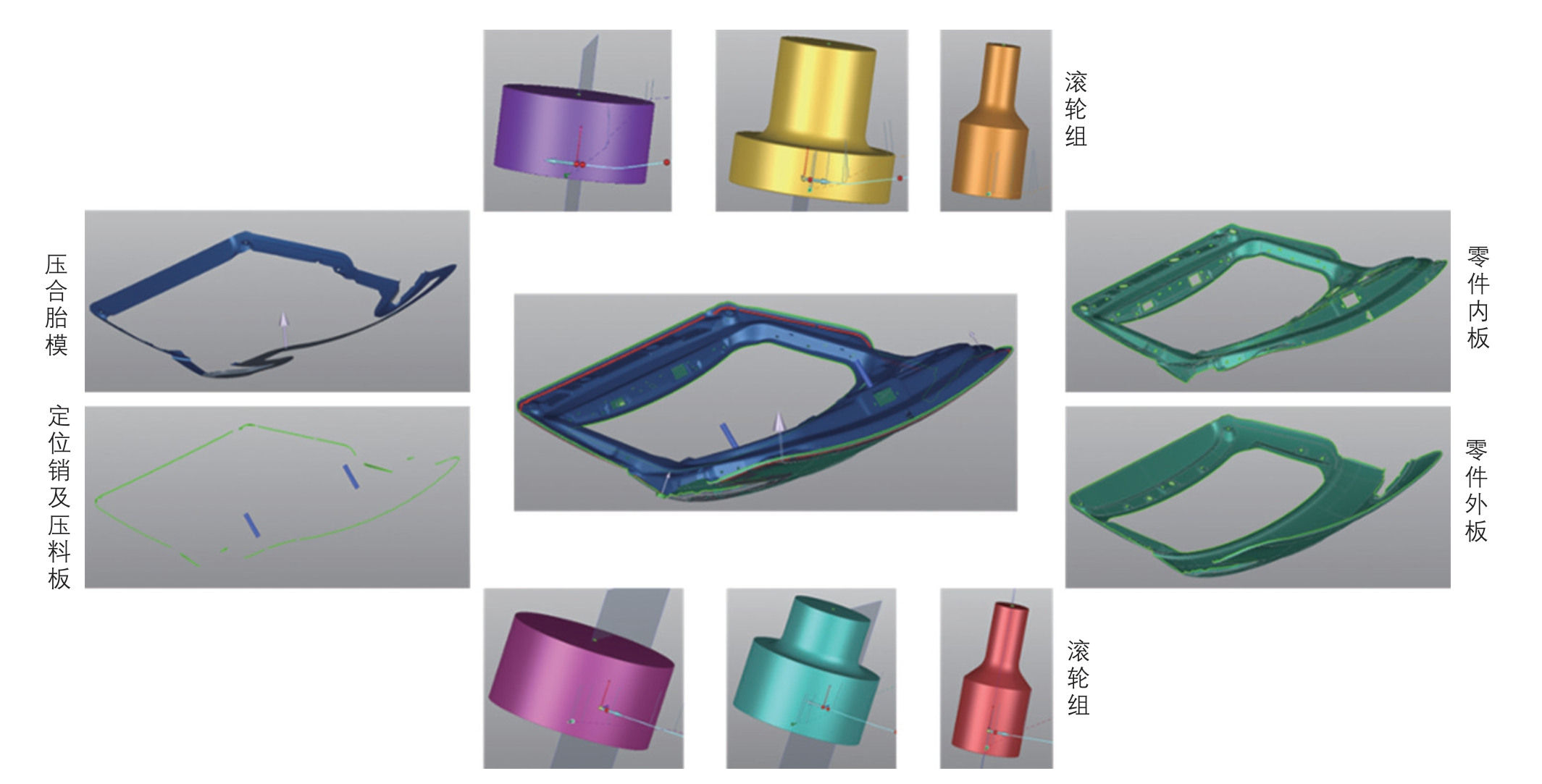
圖4 滾邊壓合仿真理論模型建立
Auto Form軟件廣泛應(yīng)用于金屬板材成形的工藝仿真優(yōu)化,Auto Form R6版本新加入了Hem Planner模塊,為滾邊成形仿真提供了一個(gè)很方便的工具。根據(jù)實(shí)際生產(chǎn)情況,使用Auto Form模擬軟件建立壓合仿真模型,如圖4所示。將后背門外板沖壓成形后產(chǎn)品數(shù)據(jù)導(dǎo)入軟件,材料設(shè)置為H180,材料厚度t=0.7mm,胎模型面在軟件中根據(jù)產(chǎn)品型面生成,胎模型面支撐寬度100mm,后背門內(nèi)板沖壓成形后產(chǎn)品數(shù)據(jù)導(dǎo)入軟件,材料設(shè)置為St16,材料厚度t=0.65mm,壓料板壓料型面從模具結(jié)構(gòu)圖中提取型面導(dǎo)入,總壓料力大小設(shè)置為2500N。內(nèi)板定位銷根據(jù)定位孔位置及直徑在軟件中生成,滾輪組根據(jù)實(shí)際滾輪尺寸在軟件中直接生成,采用三序滾邊成形工藝。本模型僅考慮滾邊壓合中翻邊成形的應(yīng)力應(yīng)變,不考慮沖壓成形后殘余應(yīng)力、應(yīng)變及零件回彈等。
滾邊CAE模擬分析及角度優(yōu)化
滾邊壓合仿真理論模型建立完成后,利用Auto Form軟件進(jìn)行滾邊壓合模擬分析,將三序壓合角度設(shè)置為表1所示的實(shí)際生產(chǎn)滾邊角度,分析結(jié)果如圖5所示。結(jié)果顯示第一序及第二序滾邊后翻邊波浪較大,與實(shí)際滾邊后翻邊狀態(tài)基本一致。第三序滾邊后壓合邊內(nèi)沿起皺較大,存在較大的殘余應(yīng)力,最終將導(dǎo)致零件外表面形成波浪,影響后背門總成及整車外觀質(zhì)量。
表1 后背門上邊緣各工序滾邊角度

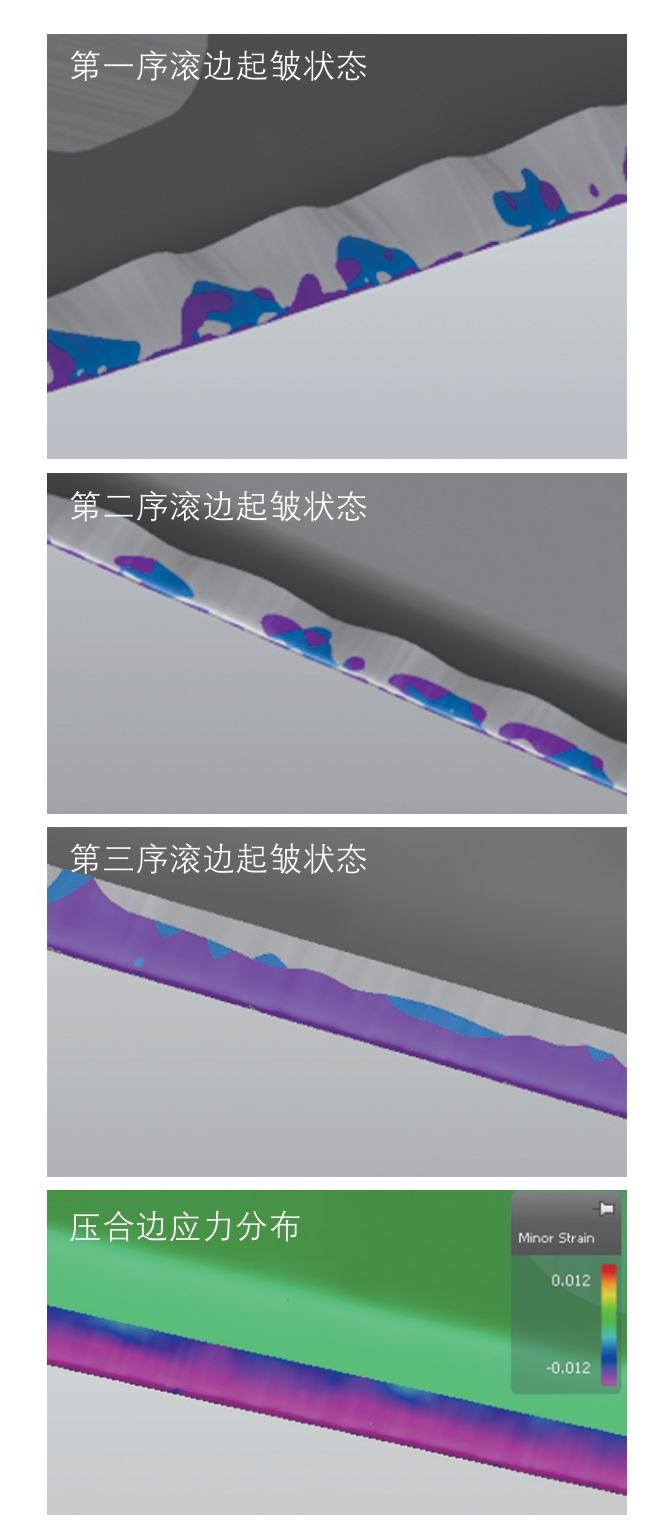
圖5 原始滾邊角度仿真分析結(jié)果
根據(jù)原始滾邊角度滾邊仿真分析結(jié)果,對(duì)后背門上邊緣滾邊角度進(jìn)行優(yōu)化,重新分配三序滾邊角度,具體角度分配如表2所示。利用Auto Form軟件建立滾邊壓合仿真模型,分別對(duì)10組滾邊角度分配進(jìn)行模擬分析。
表2 后背門上邊緣滾邊角度優(yōu)化
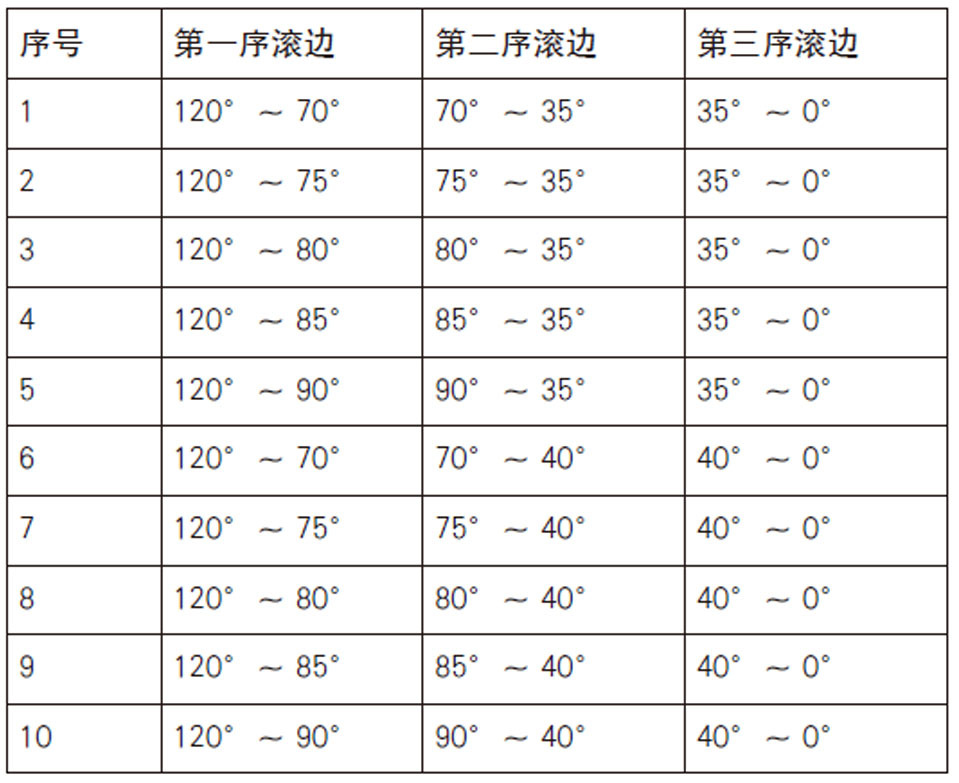
模擬分析結(jié)果表明,當(dāng)后背門上邊緣滾邊角度選取三序滾邊角度分別為120°~85°、85°~40°、40°~0°組合時(shí),每一序滾邊壓合后的翻邊波浪較小,翻邊質(zhì)量明顯優(yōu)于其他角度滾邊狀態(tài),最終滾邊后壓合邊起皺及殘余應(yīng)力都較原滾邊壓合角度明顯減輕,如圖6所示。
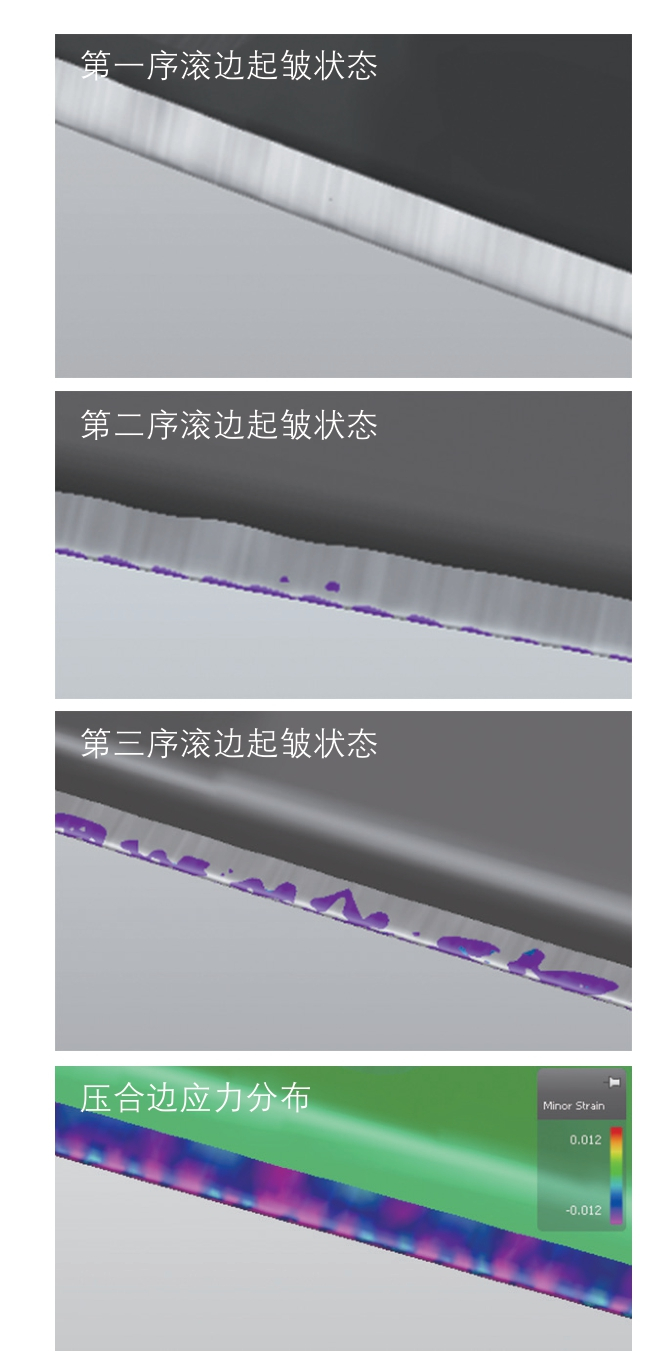
圖6 優(yōu)化滾邊角度后滾邊仿真分析結(jié)果
滾邊角度優(yōu)化結(jié)果驗(yàn)證
根據(jù)優(yōu)化滾邊角度模擬分析結(jié)果,通過調(diào)整機(jī)器人工具端角度,采用最優(yōu)的120°~85°、85°~40°、40°~0°滾邊壓合角度進(jìn)行滾邊壓合,生產(chǎn)結(jié)果表明:第一序、第二序滾邊后翻邊表面波浪明顯減輕,終壓合后制件總成表面波浪缺陷也得到大幅度優(yōu)化,實(shí)際生產(chǎn)結(jié)果如圖7、圖8所示。
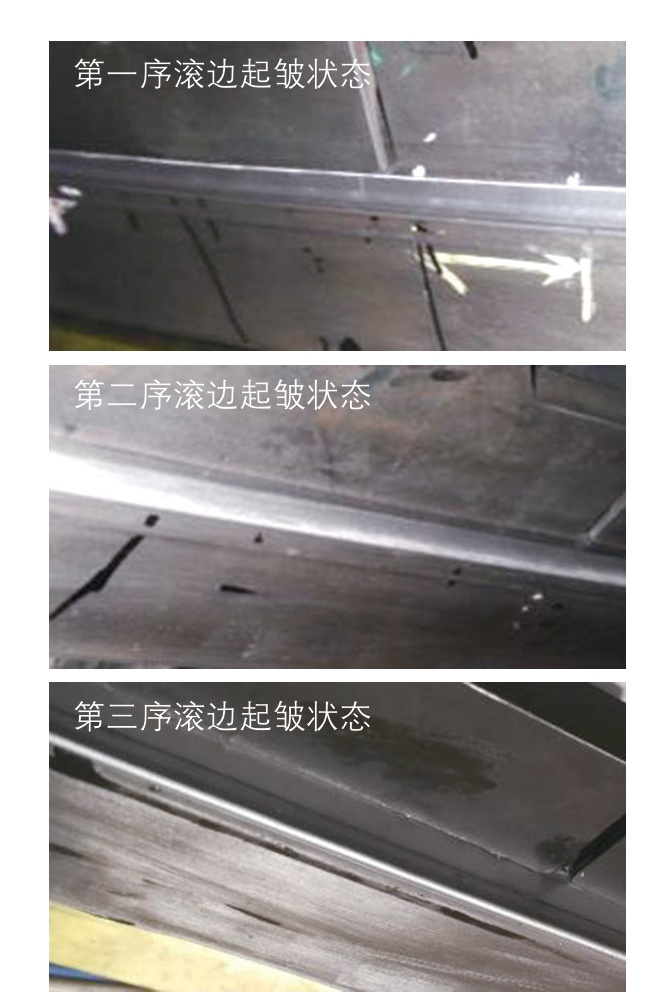
圖7 優(yōu)化滾邊角度后實(shí)際生產(chǎn)調(diào)試結(jié)果
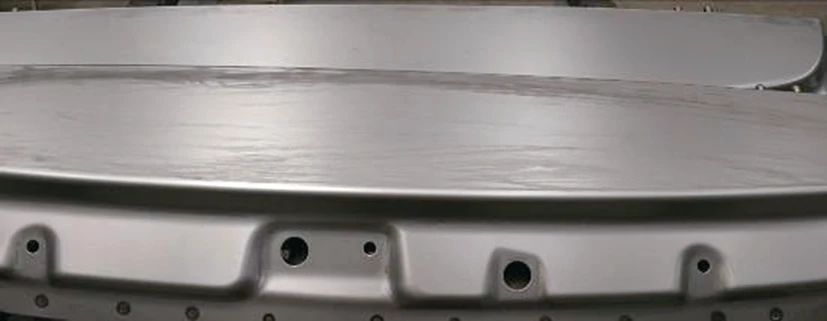
圖8 優(yōu)化滾邊角度后壓合總成狀態(tài)
最終后背門上邊緣表面波浪缺陷優(yōu)化至白車身AUDIT評(píng)審C類項(xiàng),漆后整車表面質(zhì)量不扣分,滿足整車評(píng)審質(zhì)量要求,整改效果明顯。
結(jié)束語
本文采用CAE仿真分析與現(xiàn)場(chǎng)實(shí)際生產(chǎn)相結(jié)合的方法,通過對(duì)機(jī)器人滾邊壓合典型質(zhì)量缺陷的案例研究表明,滾邊壓合角度對(duì)制件表面質(zhì)量的影響很大,合理分配每一序滾邊的角度,可以明顯優(yōu)化表面波浪缺陷,提升制件及整車外觀質(zhì)量,為今后生產(chǎn)中此一類問題的解決提供了參考方法。
——摘自《鍛造與沖壓》2019年第4期
舉報(bào) 0
收藏 0
分享 116
-
2024??禉C(jī)器人行業(yè)解決方案系列發(fā)布會(huì)
2024-10-14 -
2024年機(jī)器人行業(yè)5大發(fā)展趨勢(shì)
2024-07-29 -
AMTS | 以智馭新,協(xié)作創(chuàng)造汽車行業(yè)新質(zhì)生產(chǎn)力
2025-02-17 -
汽車制造新范式,AMR賦能汽車工業(yè)智造新藍(lán)圖
2024-06-20
編輯推薦
最新資訊
-
跨越速運(yùn)憑什么“圈粉”萬千客戶?“
2025-07-01 14:42
-
數(shù)智破局啟新篇?生態(tài)共生再啟程 —
2025-06-27 20:13
-
助力汽車零部件產(chǎn)線智能化升級(jí),西門
2025-06-27 13:59
-
BBA集體轉(zhuǎn)向!放棄全面電動(dòng)化
2025-06-26 17:32
-
比換柜省錢,比自研省心,西門子Xcel
2025-06-25 15:07