車(chē)身覆蓋件實(shí)施并模沖壓的工藝總結(jié)
2019-03-04 16:11:28· 來(lái)源:鍛造與沖壓 作者:漆世澤
汽車(chē)覆蓋件和大型內(nèi)觀件的整個(gè)生產(chǎn)過(guò)程占據(jù)了優(yōu)質(zhì)的沖壓生產(chǎn)設(shè)備和配套人員,并消耗了巨大的能源。如何提高該沖壓生產(chǎn)的產(chǎn)出率,展開(kāi)效率提升、節(jié)能減排,實(shí)現(xiàn)成本優(yōu)化,很多沖壓工廠進(jìn)行了不懈的努力。一方面是導(dǎo)入先進(jìn)的生產(chǎn)設(shè)備,例如
汽車(chē)覆蓋件和大型內(nèi)觀件的整個(gè)生產(chǎn)過(guò)程占據(jù)了優(yōu)質(zhì)的沖壓生產(chǎn)設(shè)備和配套人員,并消耗了巨大的能源。如何提高該沖壓生產(chǎn)的產(chǎn)出率,展開(kāi)效率提升、節(jié)能減排,實(shí)現(xiàn)成本優(yōu)化,很多沖壓工廠進(jìn)行了不懈的努力。一方面是導(dǎo)入先進(jìn)的生產(chǎn)設(shè)備,例如將傳統(tǒng)的機(jī)械式壓力機(jī)生產(chǎn)線轉(zhuǎn)變?yōu)槿欧a(chǎn)線;另一方面是充分發(fā)揮現(xiàn)有設(shè)備的能效,例如消減換模時(shí)間、壓縮單沖次循環(huán)時(shí)間。除此以外,在模具設(shè)計(jì)上下功夫,實(shí)施模具并列式加工,讓一個(gè)沖壓循環(huán)內(nèi)做出盡量多的零件,這也是模具行業(yè)一個(gè)長(zhǎng)期堅(jiān)持的方向。以下就對(duì)我們過(guò)往模具并列式方案在新模具導(dǎo)入方面的一些現(xiàn)場(chǎng)實(shí)踐經(jīng)驗(yàn)進(jìn)行總結(jié)和歸納。
模具并列方案
所謂模具并列式?jīng)_壓工藝,就是在滿足整體設(shè)備能力范圍內(nèi)(含沖壓負(fù)荷、壓機(jī)尺寸)將至少2個(gè)沖壓件的模具實(shí)現(xiàn)并列式加工的生產(chǎn)工藝。目前模具并列的方式按照有無(wú)墊板可分為三種情況:(1)一體式1套模具;(2)帶墊板式2套模具;(3)無(wú)墊板式2套模具。這三種情況各有特點(diǎn),在我們的過(guò)往實(shí)績(jī)中都有廣泛的應(yīng)用。
對(duì)于第(1)種一體式模具常用于形狀對(duì)稱或相似的兩個(gè)零件(圖1),例如左/右翼子板、前/后門(mén)外板。這種并列方式在模具調(diào)試方面有較好的對(duì)稱性,在生產(chǎn)方面也有很好的穩(wěn)定性。但是相比第(2)和(3)種,單個(gè)模具的鑄件尺寸有大幅增加,所以在鑄造、調(diào)試上有較高的難度,同時(shí)從加工、調(diào)試到生產(chǎn)各環(huán)節(jié)的設(shè)備規(guī)格上都有較高的要求。
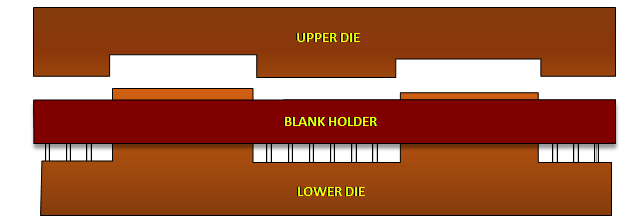
圖1 一體式1套模具
對(duì)于第(2)種帶墊板式2套模具并列的方式常用于形狀和材料差異較大的兩個(gè)零件(圖2),例如發(fā)罩內(nèi)/外板、行李箱內(nèi)/外板。這種并列方式在調(diào)試、生產(chǎn)上都具有較好的柔性,可以拆開(kāi)實(shí)現(xiàn)單模。同時(shí)在鑄造、加工、調(diào)試、生產(chǎn)等方面都有較好的靈活性,可以先做單模調(diào)試然后再合并一起調(diào)試,這樣分步進(jìn)行。但是,由于模具鑄件本體是分體的,所以從單模合成到并列式的時(shí)候會(huì)存在壓料力不平衡,特別是壓力機(jī)滑塊的剛性撓曲對(duì)模具的壓料力存在較大影響,導(dǎo)致零件品質(zhì)存在較大差異。
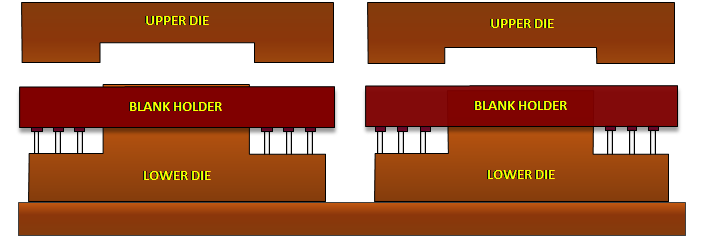
圖2 帶墊板式2套模具
對(duì)于第(3)種無(wú)墊板式2套模具并列的方式常用于生產(chǎn)量差異較大的零件(圖3),例如不同車(chē)型的兩個(gè)發(fā)罩外板零件。由于兩款車(chē)型產(chǎn)量不一樣,需要使用這種更具柔性的模具并列方式,可以隨時(shí)拆開(kāi)和合并生產(chǎn)。由于這種并模方式?jīng)]有了墊板,相比第(2)種方式在生產(chǎn)準(zhǔn)備時(shí)間(例如在模具吊裝)會(huì)有大幅增加。
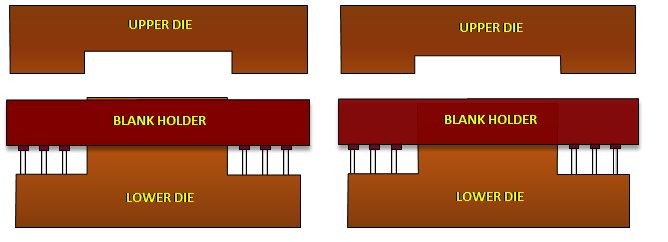
圖3 無(wú)墊板式2套模具
綜上,由于每種并列都有各自的優(yōu)點(diǎn),所以在模具設(shè)計(jì)之初要提前明確采用哪種并列方式、在哪條生產(chǎn)線生產(chǎn)、生產(chǎn)班組的人員配置能否對(duì)應(yīng)等。
并模經(jīng)驗(yàn)總結(jié)
對(duì)比上述三種并列加工方式,由于第(2)種方式相比其他兩種在過(guò)往模具調(diào)試上發(fā)生了較多的課題,所以這里主要就第(2)種方式的過(guò)往課題和對(duì)策經(jīng)驗(yàn)進(jìn)行總結(jié)和歸納。
模具吊運(yùn)準(zhǔn)備
將模具安裝到壓力機(jī)時(shí),最主要的是進(jìn)行起吊平衡的檢證,如圖4所示。所謂起吊平衡性檢證,就是模擬并列狀態(tài)下在起吊時(shí),檢證墊板底部懸空的最大高度差,確保其在合理的基準(zhǔn)范圍內(nèi)(參考基準(zhǔn)60mm),最終確保模具能夠順利快速的定置到壓力機(jī)工作臺(tái)上。
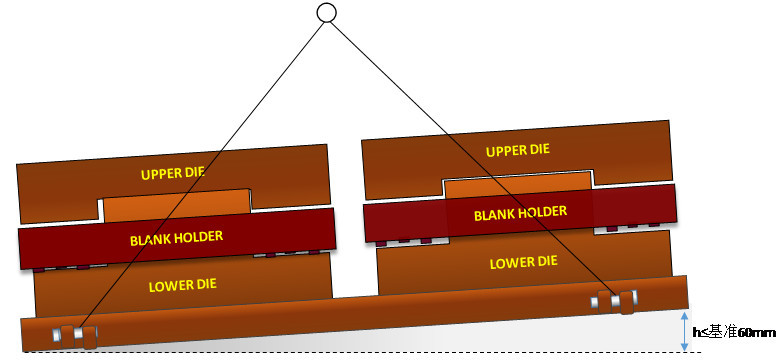
圖4 起吊平衡性檢證
為了保證整體的起吊平衡性,優(yōu)先考慮在墊板結(jié)構(gòu)設(shè)計(jì)時(shí)進(jìn)行合理的吊耳位置設(shè)定,將墊板的吊耳位置均勻?qū)ΨQ的設(shè)定在3套模具(含2套單模和1套墊板)的重心兩邊(圖5)。如果有特殊要求,墊板的吊耳必須與墊板中心進(jìn)行對(duì)稱設(shè)定,這時(shí)可以考慮追加配重塊來(lái)平衡(圖6)。
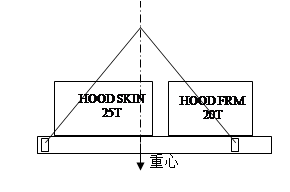
圖5 吊耳對(duì)稱設(shè)定在重心兩側(cè)
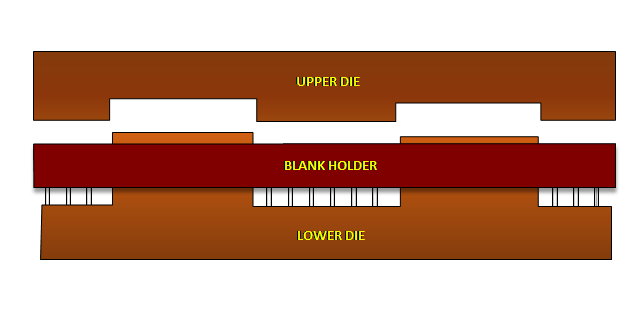
圖6 使用配重塊來(lái)平衡
模具在線安裝
模具并列加工方式在生產(chǎn)線調(diào)試安裝時(shí),需要確認(rèn)的項(xiàng)目很多,包括了人員布崗、設(shè)備規(guī)格、材料準(zhǔn)備、工藝標(biāo)準(zhǔn)、安全管理等各領(lǐng)域的分類檢討。單就設(shè)備規(guī)格按照生產(chǎn)流程,就要確認(rèn)坯料分張、對(duì)中上料、模具定位、沖壓成型、廢料排出等。以上檢證項(xiàng)目大多與以往的非并列式?jīng)]有特別的差異之處。根據(jù)我們之前的經(jīng)驗(yàn)總結(jié),這里著重強(qiáng)調(diào)的是以下方面兩個(gè)方面。一是充分檢證并列方式對(duì)壓力機(jī)的影響,確保不超過(guò)壓力機(jī)本身的能力和不損壞壓力機(jī)的精度及壽命;二是檢證并列方式對(duì)產(chǎn)品的影響,模具安裝和運(yùn)轉(zhuǎn)能否確保穩(wěn)定生產(chǎn)出合格的沖壓產(chǎn)品,如表1所示。
表1 并列加工方式的可行性檢討
主要重點(diǎn)檢證項(xiàng)目
參考基準(zhǔn)
壓力機(jī)能力
壓力機(jī)最大載荷
參考生產(chǎn)線壓力機(jī)最大載荷能力×安全系數(shù)
壓力機(jī)做功載荷
參考?jí)毫C(jī)的最大做功能力
壓力機(jī)偏載檢證
參考?jí)毫C(jī)一級(jí)精度要求范圍
模具安裝參數(shù)
頂桿分布
頂桿布滿時(shí),與模具沒(méi)有干涉
頂桿行程
保證并列的2套模具頂桿行程一致,且同時(shí)與上模的壓料器發(fā)生接觸
閉合高度
保證并列的2套模具閉合高度保持一致,且確保在下死點(diǎn)時(shí)兩套上下模同時(shí)到達(dá)合模要求
氣墊壓力
滿足設(shè)備氣墊最大能力范圍
在線調(diào)試難點(diǎn)
在單套模具調(diào)試到一定程度后需要將其并列起來(lái)調(diào)試,在這個(gè)單模轉(zhuǎn)并模的過(guò)程中會(huì)出現(xiàn)很多課題和風(fēng)險(xiǎn)。
(1)閉合高度的確定。
為了保證兩套模具并列起來(lái)后同時(shí)達(dá)到合模狀態(tài),這是一個(gè)需要經(jīng)驗(yàn)積累的難點(diǎn)。首先需要強(qiáng)調(diào)的是,兩套在施加設(shè)定載荷和達(dá)成合?;鶞?zhǔn)后閉合高度保持一致。這里要求的是在動(dòng)態(tài)工作狀態(tài)下的閉合高度一致,而不是靜態(tài)的非工作狀態(tài)下的一致。過(guò)往經(jīng)驗(yàn)證明:將兩個(gè)模具的上下模用螺絲鎖緊后的靜態(tài)高度差異量,跟施加載荷后工作狀態(tài)下的動(dòng)態(tài)閉合高度差異量,存在很大的變化。過(guò)往實(shí)績(jī)顯示兩者之間的變化量可達(dá)到4mm左右。
所以正確的方法是使用同一臺(tái)能夠精確顯示閉合高度的壓力機(jī),將兩套模具都調(diào)試到設(shè)定的載荷和所需的合模狀態(tài),再分別記錄下這臺(tái)壓力機(jī)顯示的兩套模具的閉合高度,最終得到兩個(gè)閉合高度的差異量ΔH=|H1-H2|作為模具底面切削的參考調(diào)整量,如圖7所示。
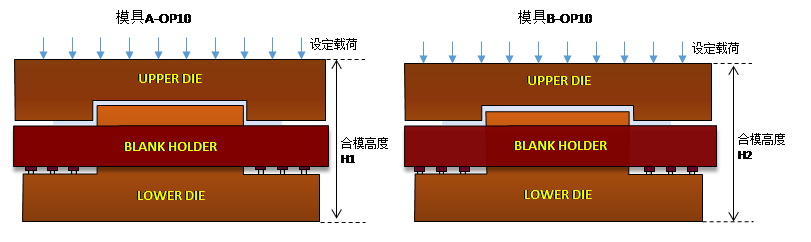
圖7 帶載荷的情況下進(jìn)行閉合高度測(cè)定
(2)頂桿行程的確定。
對(duì)于拉延工序模具,坯料的壓邊力直接影響到產(chǎn)品的開(kāi)裂和起皺。模具并列后兩套壓料板共同使用一個(gè)壓力機(jī)氣墊,這就導(dǎo)致一套模具的壓邊力調(diào)整時(shí)會(huì)影響到另一套模具,所以壓邊力的調(diào)整是主要難點(diǎn)之一。
另外對(duì)于圖8所示的模具結(jié)構(gòu),一方面模具的上模與壓料板配合把坯料周邊壓緊提供脹型的張力;另一方面上模與下模配合在下死點(diǎn)時(shí)發(fā)揮合模壓力。所以上?;娴那邢骷庸?huì)同時(shí)影響到壓料間隙和閉合高度。這也是單模轉(zhuǎn)并模的一個(gè)主要難點(diǎn)。
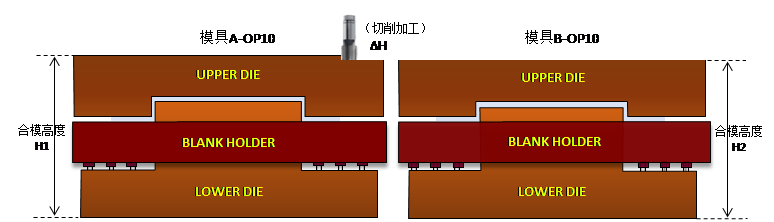
圖8 模具底面切削加工確保閉合高度一致
(3)制作過(guò)程的控制。
首先在模具一次加工時(shí)就將兩套模具的上?;婧穸榷碱A(yù)留多3mm的加工余量,同時(shí)確保上模、下模、壓料板的基體高度都在嚴(yán)格的公差范圍內(nèi)。在此以前,模具基體的高度尺寸在±1mm或更大公差內(nèi),由于其影響的只是最終的閉合高度,而對(duì)沖壓生產(chǎn)沒(méi)有特別大的影響,所以沒(méi)有嚴(yán)格要求和管理。但是在模具并列的情況下,這個(gè)會(huì)造成兩套模具的壓料接觸時(shí)點(diǎn)、閉合高度都差異很大,鉗工后續(xù)的調(diào)試工作量也會(huì)加大。
其次,將單模調(diào)試所得到的ΔH差異量,先用加墊片補(bǔ)償?shù)姆绞皆诓⒘姓{(diào)試時(shí)進(jìn)行上機(jī)試沖驗(yàn)證。主要是驗(yàn)證兩套模具的壓料面接觸是否均勻、上下模面的合模狀態(tài)。通過(guò)試沖檢證來(lái)修正ΔH差異量,從而作為上?;娴那邢髁?,減少后續(xù)的鉗工調(diào)整量。
在模具并列準(zhǔn)備就緒進(jìn)行In-Line調(diào)試時(shí),還會(huì)出現(xiàn)壓力機(jī)滑塊面的撓曲的現(xiàn)象,出現(xiàn)兩端壓力重、中間壓力輕的現(xiàn)象,如圖9所示。這時(shí)可以根據(jù)撓曲程度適當(dāng)追加墊片給予校正,根據(jù)過(guò)往經(jīng)驗(yàn)一般機(jī)械式壓力機(jī)追加0.5mm左右墊片予以校正。
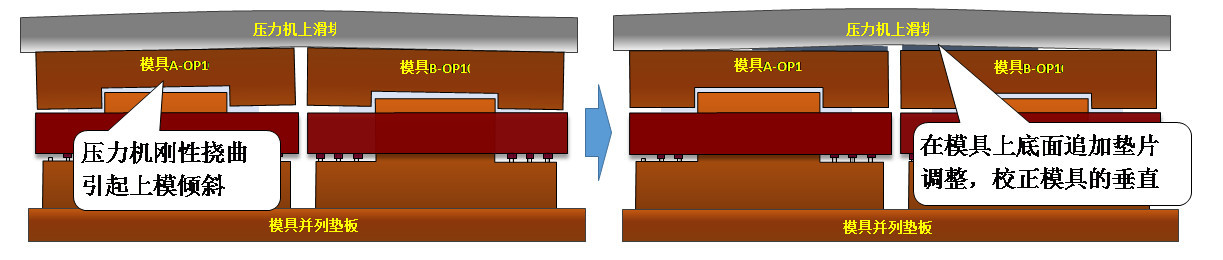
圖9 壓力機(jī)撓曲引起的模具壓力不均及對(duì)策
結(jié)束語(yǔ)
模具并列式?jīng)_壓工藝是發(fā)揮現(xiàn)有沖壓設(shè)備能力,提高生產(chǎn)效率的一項(xiàng)重要措施。從模具設(shè)計(jì)、加工到調(diào)試的整個(gè)導(dǎo)入過(guò)程都會(huì)存在一些需要注意的事項(xiàng),本文進(jìn)行了概要說(shuō)明。后續(xù)還會(huì)通過(guò)不斷的實(shí)踐總結(jié)和經(jīng)驗(yàn)反饋,繼續(xù)為沖壓領(lǐng)域的效率提升做出更大貢獻(xiàn)。
—— 來(lái)源:《鍛造與沖壓》2019年第4期
舉報(bào) 0
收藏 0
分享 120
-
乘用車(chē)金屬?zèng)_壓
2025-05-29 -
沖壓技術(shù)在電機(jī)疊片制造的應(yīng)用
2024-09-06 -
車(chē)身零部件包邊質(zhì)量控制要點(diǎn)
2024-09-05 -
輕量化技術(shù)——熱汽脹形工藝技術(shù)解析
2024-09-04
最新資訊
-
跨越速運(yùn)憑什么“圈粉”萬(wàn)千客戶?“
2025-07-01 14:42
-
數(shù)智破局啟新篇?生態(tài)共生再啟程 —
2025-06-27 20:13
-
助力汽車(chē)零部件產(chǎn)線智能化升級(jí),西門(mén)
2025-06-27 13:59
-
BBA集體轉(zhuǎn)向!放棄全面電動(dòng)化
2025-06-26 17:32
-
比換柜省錢(qián),比自研省心,西門(mén)子X(jué)cel
2025-06-25 15:07