汽車信號(hào)輪旋壓增厚工藝研究及旋輪設(shè)計(jì)
2019-02-01 15:56:09· 來源:鍛造與沖壓 作者:周金良,黃彪
信號(hào)輪作為汽車發(fā)動(dòng)機(jī)里面重要的傳動(dòng)部件,信號(hào)輪外齒端厚度是板料厚度的2~3倍,對(duì)于其綜合性能有著很高的要求。傳統(tǒng)工藝主要是通過沖壓、拼焊或者鍛造后多次機(jī)加工獲得。采用傳統(tǒng)工藝獲得的信號(hào)輪存在著焊接影響區(qū)化學(xué)成分不均勻、精度
信號(hào)輪作為汽車發(fā)動(dòng)機(jī)里面重要的傳動(dòng)部件,信號(hào)輪外齒端厚度是板料厚度的2~3倍,對(duì)于其綜合性能有著很高的要求。傳統(tǒng)工藝主要是通過沖壓、拼焊或者鍛造后多次機(jī)加工獲得。采用傳統(tǒng)工藝獲得的信號(hào)輪存在著焊接影響區(qū)化學(xué)成分不均勻、精度較低、零件壽命短、材料利用率低等問題。而采用旋壓工藝成形信號(hào)輪有諸多優(yōu)點(diǎn),比如產(chǎn)品精度高、零件性能優(yōu)良、材料利用率高等。本文將設(shè)計(jì)一套信號(hào)輪旋壓成形模具,通過有限元分析軟件SIMUFACT對(duì)信號(hào)輪多道次旋壓增厚成形的過程進(jìn)行有限元模擬分析,分析成形過程中板坯變形情況、金屬流動(dòng)規(guī)律及旋壓增厚過程中載荷分布情況,驗(yàn)證所設(shè)計(jì)旋輪的合理性。
多楔輪旋壓成形工藝分析
信號(hào)輪的結(jié)構(gòu)特征如圖1所示,通過多道次旋壓增厚可使原始厚度為2.5mm的板料局部增厚到6mm。板料增厚部位并非兩邊對(duì)稱增厚,上半部板料厚度為0.75mm,下半部厚度為1.75mm,考慮后續(xù)加工余量兩邊各加0.5mm,總增厚厚度為6mm,增厚外徑加0.5mm,最終上半部板料厚度為1.25mm,下半部厚度為2.25mm。所以在旋輪定位時(shí),應(yīng)保證板料距旋槽上平面距離和下平面距離比值為5∶9。
圖2所示為增厚旋輪局部示意圖,旋輪側(cè)面有一個(gè)深度為n的旋輪槽,輪槽底端為一個(gè)半徑為r的圓底,圓底的設(shè)計(jì)有利于增厚過程中金屬的流動(dòng),輪槽寬度為m。
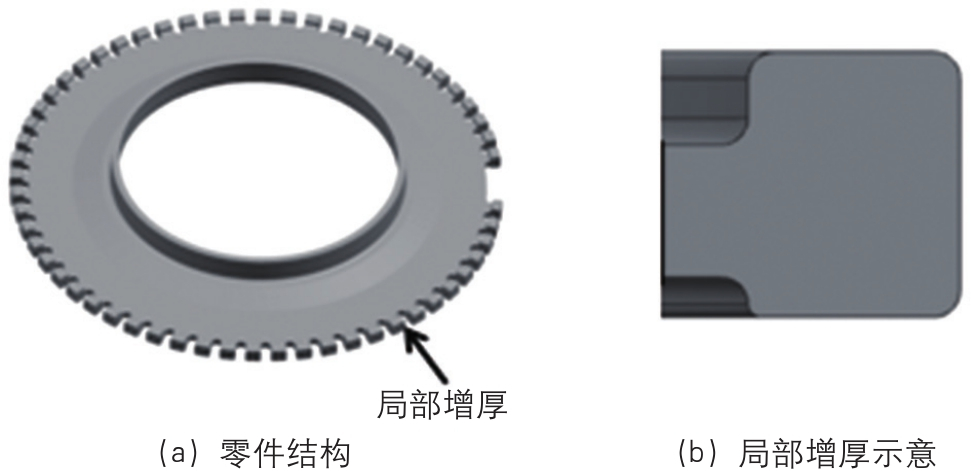
圖1 信號(hào)輪結(jié)構(gòu)特征示意圖
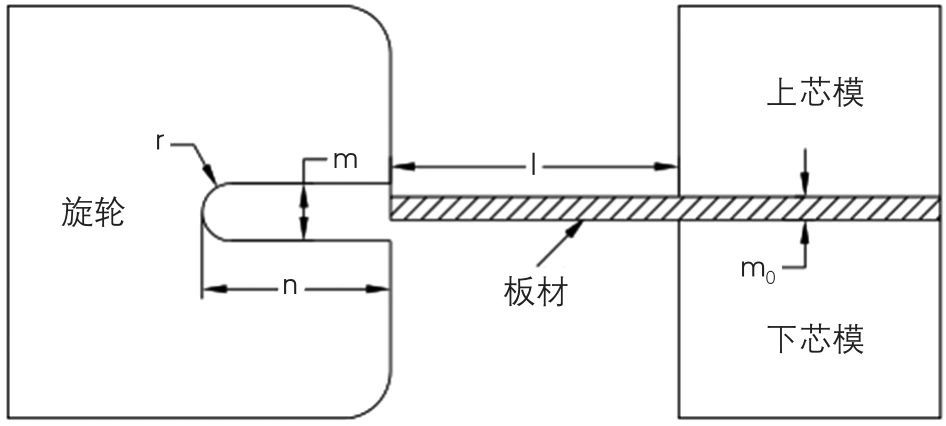
圖2 增厚旋輪局部示意圖
表1 旋壓增厚輪具體參數(shù)

根據(jù)旋壓手冊(cè)以及工業(yè)生產(chǎn)經(jīng)驗(yàn),從減少生產(chǎn)道次以及提高材料利用率和零件成品率的角度考慮,信號(hào)輪的旋壓增厚成形工藝采用三個(gè)增厚旋輪依次進(jìn)給成形,每道次進(jìn)給旋輪的具體參數(shù)如表1所示。
有限元模型建立
采用SIMUFACT有限元分析軟件建立如圖3所示的板材旋壓增厚模型,板材為厚度2.5mm、直徑191mm、DD13材料的圓形板材。模擬中定義板材和模具溫度為20℃,旋輪與板材之間的摩擦系數(shù)為0.05,芯模與板材之間的摩擦系數(shù)為0.3,上下芯軸轉(zhuǎn)速為300 r/min,旋輪的進(jìn)給速度為2mm/s。
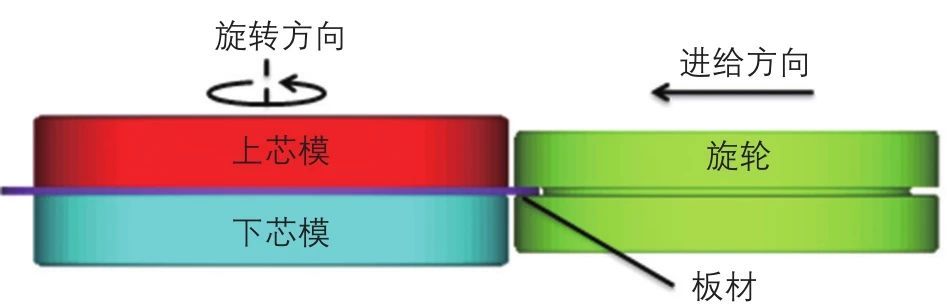
圖3 信號(hào)輪旋壓增厚模型
模擬過程分析
圖4 所示為一道次旋壓增厚成形過程,可以看出在旋輪與板材接觸處的應(yīng)力最大,應(yīng)力沿著徑向逐漸遞減,隨著旋輪的進(jìn)給,板材中的高應(yīng)力區(qū)范圍也越來越大。根據(jù)成形過程中板材在旋輪進(jìn)給作用下的變形情況,可以將一道次旋壓增厚工藝分為三個(gè)階段:第一階段是成形初期,板材與旋輪剛接觸時(shí)發(fā)生變形,如圖4(a)所示,這時(shí)板材的外緣發(fā)生塑性變形,板材外緣增厚程度明顯,同時(shí)板材發(fā)生微小的彈性變形;第二階段是成形中期,此時(shí)板材外緣已經(jīng)完全增厚,隨著旋輪的進(jìn)給,板材主要發(fā)生軸向變形,金屬逐漸充滿整個(gè)輪槽,如圖4(b)所示。等效應(yīng)力值隨著旋輪的進(jìn)給呈現(xiàn)增大的趨勢(shì),等效應(yīng)變隨著變形程度的增大逐漸累積;第三階段是成形末期,增厚旋輪達(dá)到預(yù)定位置,板坯完整成形,如圖4(c)所示,且沒有產(chǎn)生飛邊、卷邊等缺陷,整體成形效果良好。
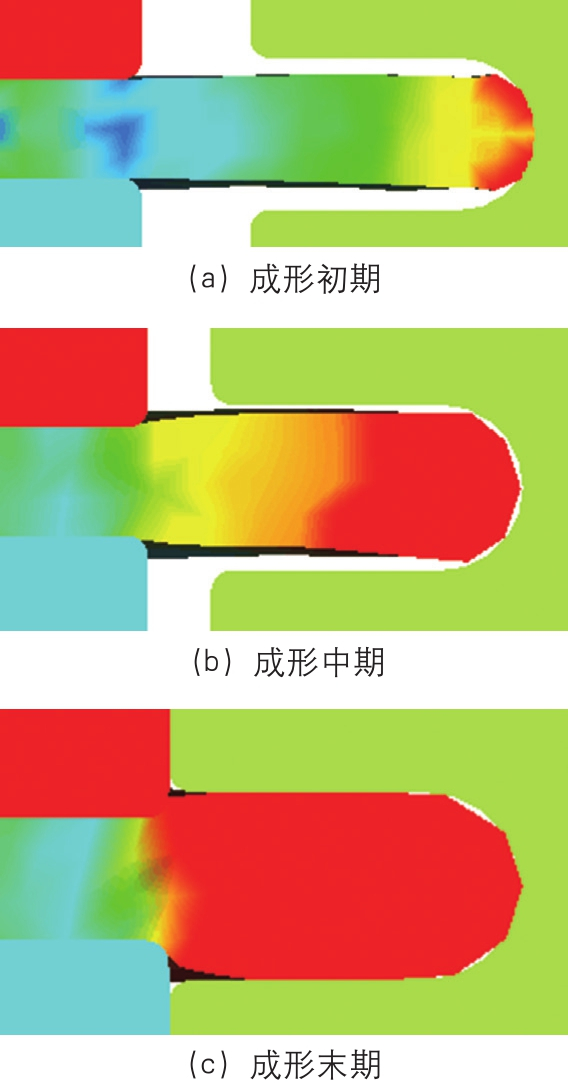
圖4 一道次旋壓增厚成形過程
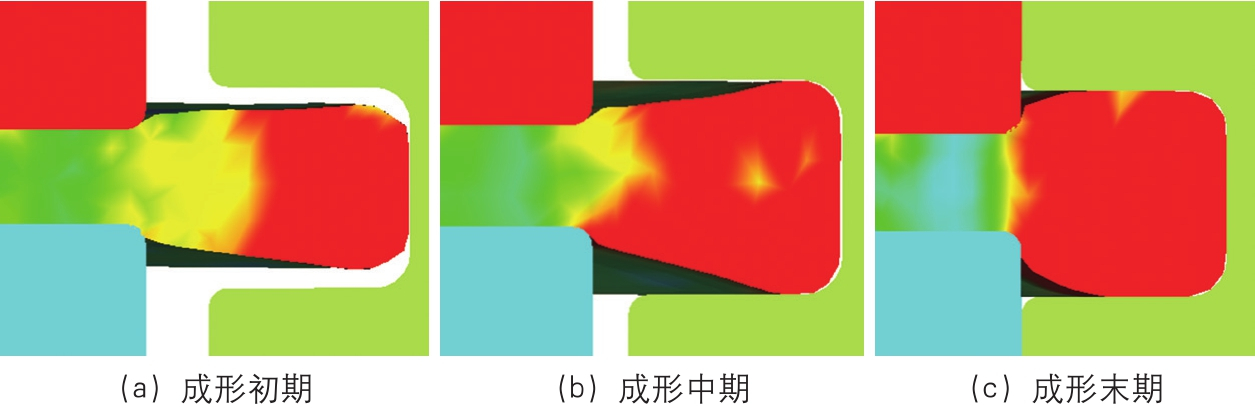
圖5 二道次旋壓增厚成形過程

圖6 三道次旋壓增厚成形過程
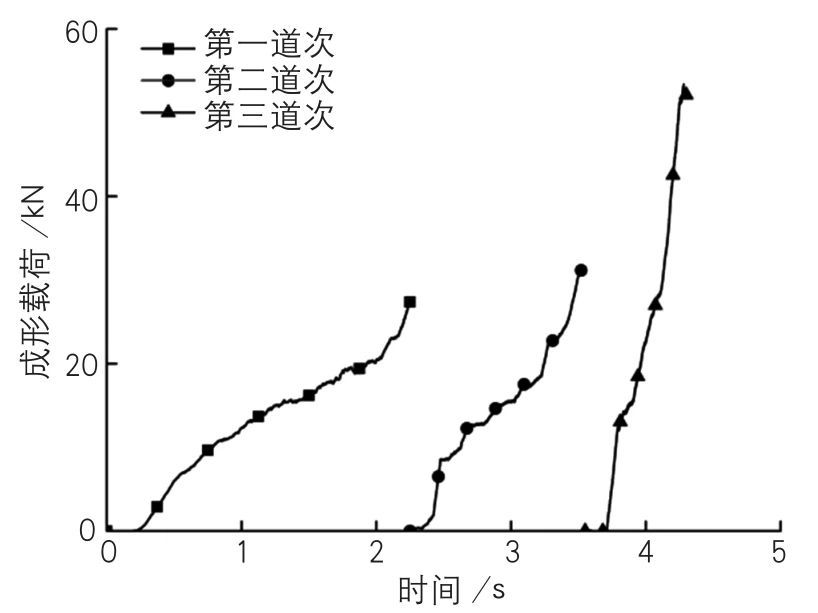
圖7 各道次旋壓成形過程徑向載荷變化
圖5所示為二道次旋壓增厚成形過程。一道次成形后,旋壓增厚輪輪槽相比一道次旋壓增厚輪寬度增大但深度減小,旋輪徑向進(jìn)給使板坯金屬進(jìn)一步變形增厚。金屬的流動(dòng)情況與一道次大致相同,板材外緣與旋輪接觸先發(fā)生增厚,隨著旋輪進(jìn)給,金屬主要向軸向流動(dòng),發(fā)生軸向增厚,并且金屬的變形抗力和等效應(yīng)力值隨之變大。從圖5(c)可以看出在成形末期時(shí)板材的成形效果良好,輪槽內(nèi)部幾乎完全被填充,沒有產(chǎn)生飛邊、卷邊等缺陷。
圖6所示為三道次旋壓增厚成形過程。整個(gè)變形過程與前兩個(gè)道次類似,圖6(c)中板材的成形效果良好,金屬填充滿旋輪槽,并且沒有明顯缺陷產(chǎn)生。
通過比較三道次旋壓增厚過程中的載荷變化(圖7),可以看出前兩道次的模具載荷大小幾乎一樣且明顯小于第三道次。0~2.25s為第一道次載荷變化,載荷整體變化趨勢(shì)均勻平緩,這是因?yàn)榈谝坏来纬尚芜^程中金屬變形程度較小,因此變形抗力較小,所以載荷均勻增大;2.25~3.6s為第二道次載荷變化,當(dāng)板材外緣完全增厚時(shí),旋輪繼續(xù)進(jìn)給且載荷急劇增大,這是因?yàn)樽冃瘟坷鄯e導(dǎo)致金屬的變形抗力增大;3.6~4.2s為第三道次載荷變化趨勢(shì),由于前兩道次的應(yīng)變累積,此時(shí)變形抗力更大,所以在旋輪進(jìn)給過程中,載荷急劇增加,最大載荷達(dá)到50.1kN。
試驗(yàn)驗(yàn)證
信號(hào)輪旋壓增厚試驗(yàn)是在CDC-4S80多工位旋壓機(jī)上進(jìn)行的,所用圓形板坯尺寸為191mm×2.5 mm、旋輪進(jìn)給速度為1mm/s、摩擦系數(shù)0.05、主軸轉(zhuǎn)速300 r/min,旋輪尺寸與表1完全一致。成形后的試驗(yàn)樣品成形效果良好,外緣端從2.5mm增厚到了6mm,再經(jīng)過表面精車外緣端,厚度變成了5mm,達(dá)到了模擬預(yù)期效果,試驗(yàn)與有限元模擬結(jié)果基本一致。
——本文節(jié)選自《鍛造與沖壓》2018年第22期。
舉報(bào) 0
收藏 0
分享 102
-
乘用車金屬?zèng)_壓
2025-05-29 -
沖壓技術(shù)在電機(jī)疊片制造的應(yīng)用
2024-09-06 -
車身零部件包邊質(zhì)量控制要點(diǎn)
2024-09-05 -
輕量化技術(shù)——熱汽脹形工藝技術(shù)解析
2024-09-04
最新資訊
-
跨越速運(yùn)憑什么“圈粉”萬千客戶?“
2025-07-01 14:42
-
數(shù)智破局啟新篇?生態(tài)共生再啟程 —
2025-06-27 20:13
-
助力汽車零部件產(chǎn)線智能化升級(jí),西門
2025-06-27 13:59
-
BBA集體轉(zhuǎn)向!放棄全面電動(dòng)化
2025-06-26 17:32
-
比換柜省錢,比自研省心,西門子Xcel
2025-06-25 15:07