鋁合金車身及連接技術
2019-01-25 15:48:02· 來源:中國汽車材料網(wǎng) 作者:東風柳州汽車有限公司 李武泉
摘要:以某車型鈑金沖壓后副車架作為優(yōu)化對象,通過拓撲、形貌和性能等多目標方法優(yōu)化,設計成采用液壓成形管件與鈑金沖壓件拼焊成的后副車架,在通過臺架試驗和可靠性道路試驗驗證后進行了量產?! £P鍵詞:副車架;拓撲優(yōu)化;多目標;
摘要:以某車型鈑金沖壓后副車架作為優(yōu)化對象,通過拓撲、形貌和性能等多目標方法優(yōu)化,設計成采用液壓成形管件與鈑金沖壓件拼焊成的后副車架,在通過臺架試驗和可靠性道路試驗驗證后進行了量產。
關鍵詞:副車架;拓撲優(yōu)化;多目標;輕量化;液壓成形;內高壓成形
液壓成形技術最早廣泛應用于航空航天領域,目前已成為汽車產業(yè)主流制造技術之一。圖1 為液壓成形技術在汽車上的應用概覽。液壓成形與傳統(tǒng)成形工藝最大的不同是采用水或者油作為傳力介質,從而取代凸模或凹模,通過增加壓力使得待加工工件發(fā)生適當?shù)乃苄宰冃危瑥亩_到設計要求。液壓成形技術的產品具有重量輕、形狀可塑性強、剛度高、精度高等特點。在生產過程中可減少零部件種類,焊縫長度、機械加工工序、產品組裝工序等,有降低生產成本、縮短加工周期等優(yōu)點。
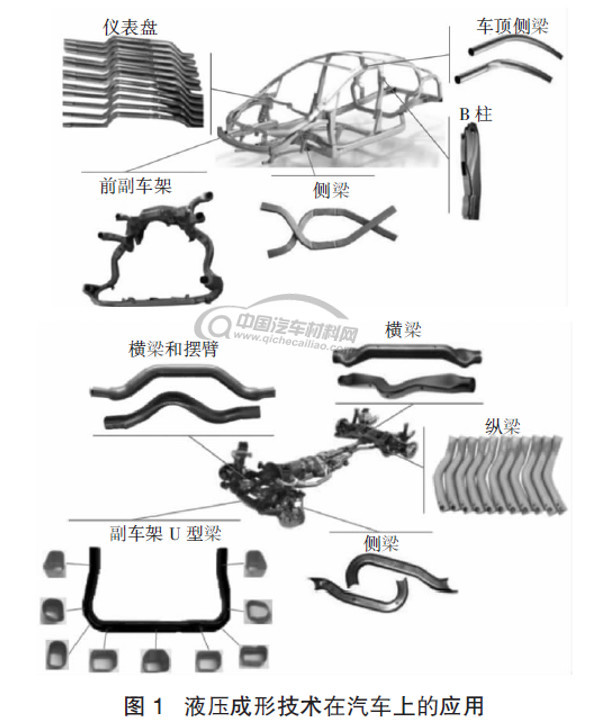
本文以乘用車某車型鈑金沖壓后副車架作為優(yōu)化對象,通過拓撲、形貌和性能等多目標方法優(yōu)化后,設計成采用液壓成形管件與鈑金沖壓件拼焊成的后副車架,將原型后副車架由原來的18.2 kg 降低到14.6 kg,實現(xiàn)減重3.6 kg(19.7%),性能保持不變,最大應力降低,同時,零部件采購成本降低25%,給企業(yè)帶來了非??捎^的經濟效益。
1 概述
本文所介紹的副車架原型為大型沖壓焊接件。該原型副車架的主要結構是由前后、上下鈑金沖壓件以及一些加強板、附屬支架通過焊接構成,焊接方式為二氧化碳和氬氣混合氣體保護電弧焊。
該原型副車架性能冗余、結構臃腫、材料利用率低、零部件采購成本高,故而產生輕量化的需求。通過分析對比副車架發(fā)展趨勢和該原型副車架結構特點,進行靜動態(tài)多目標拓撲優(yōu)化,通過多目標優(yōu)化,將其優(yōu)化成液壓成形管件和鈑金沖壓件拼焊結構副車架,優(yōu)化前后的對比如圖2 所示。最后的分析結果表明優(yōu)化后的副車架整體剛度性能、強度性能和模態(tài)固有頻率均有提高,減重效果明顯,實現(xiàn)了性能不變、結構簡化、材料利用率提高、零部件采購成本降低的目標。
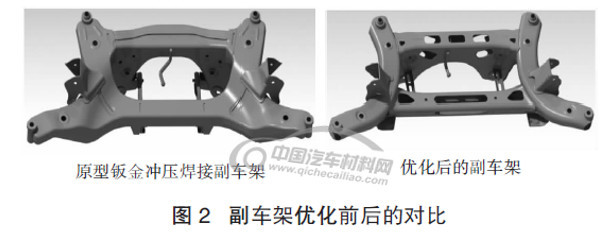
2 設計優(yōu)化
副車架是汽車上的重要總成之一,它把懸架系統(tǒng)與車身連接起來。其主要作用是傳遞車輪和車身之間的力和力矩,緩和不平路面?zhèn)鹘o車身的沖擊,衰減由此引起的系統(tǒng)振動,確保汽車的行駛平順性,同時副車架可以提高汽車的操縱穩(wěn)定性,加強承載式車身在載荷集中位置處的剛度與強度。為此,副車架應有足夠的彎曲剛度,以使裝載在其上的有關機構之間的相對運動位置在汽車行駛過程中保持不變并使車身變形??;副車架應有足夠強度,以保證其有足夠的可靠性與壽命,在使用期內不應有嚴重變形、開裂與脫焊。車架的剛度不足會引起振動與噪音,也使汽車乘坐舒適性和操縱穩(wěn)定性。
2.1 拓撲優(yōu)化
(1)根據(jù)整車參數(shù),在Adams/car 中建立汽車懸架動力學模型,根據(jù)整車載荷以及載荷分布情況,在動力學模型中對整車11 種典型工況進行仿真分析,得到懸架在相應工況下的載荷。
(2)建立拓撲優(yōu)化模型,其中包括拓撲優(yōu)化空間的包絡、邊界條件的定義和拓撲優(yōu)化參數(shù)的設置等,它們會對優(yōu)化結果產生重要的影響。
(3)根據(jù)建立好拓撲優(yōu)化模型,輸入相應工況下的載荷進行拓撲優(yōu)化計算并得到拓撲優(yōu)化結果。
(4)參照撲優(yōu)化結果進行三維實體建模。拓撲優(yōu)化流程如圖3 所示。
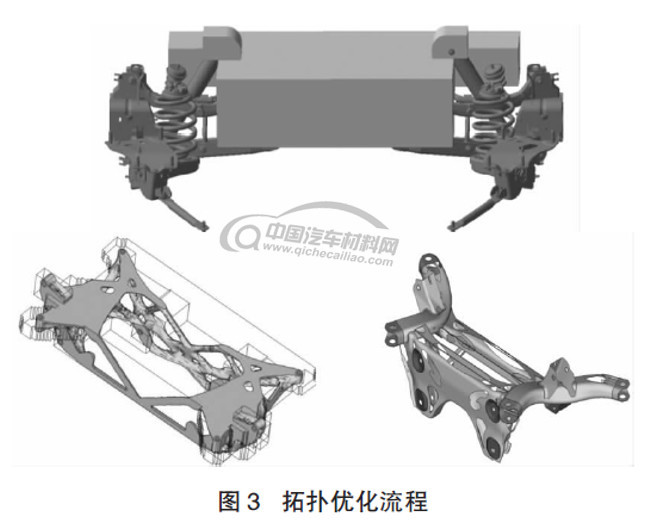
2.2 強度和模態(tài)分析
(1)如圖4 所示對優(yōu)化結果進行強度分析,單元尺寸為3 mm,單元類型以四邊形為主;螺栓連接采用RBE2 單元模擬;焊縫連接殼單元之間采用共節(jié)點模擬;楊氏模量:2.1E5 MPa;泊松比:0.3;密度:7.9E-9 t/mm3,優(yōu)化結果對比見表1.
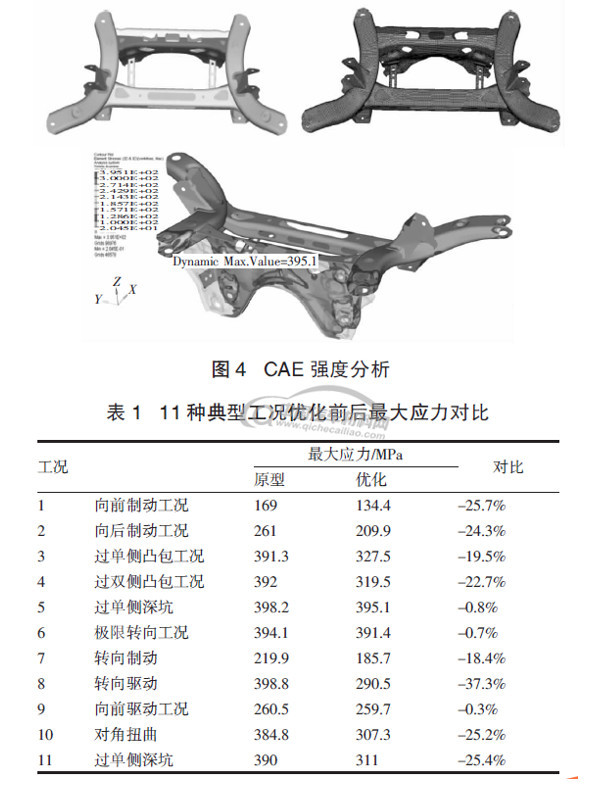
(2)副車架模態(tài)要求一階彎曲模態(tài)在160 ~ 200Hz 之間,400 Hz 以下不超過8 階彎曲模態(tài)模態(tài)間隔最好不小于20 Hz,優(yōu)化前后對比見表2.
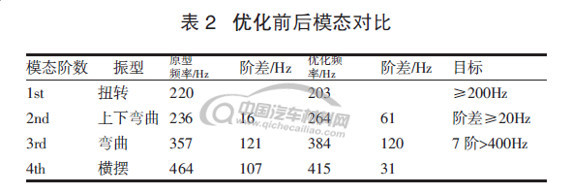
3 液壓成形工藝分析
副車架的液壓成形管件整個成形過程進行有限元模擬,其中包括:彎曲、預成形、內高壓成形三個主要工序,并根據(jù)相應的評定標準進行評定,彎曲工序中,對于彎曲半徑、彎曲步驟進行合理的調整以適應實際加工,預成形工序中根據(jù)副車架不同位置的截面設計預成形模具,并根據(jù)成形模擬結果進行修改以達到最優(yōu)成形效果,內高壓成形工序中對于重要的參數(shù)如進給量、成形壓力、整形壓力、初始壓力以及加載方式分別進行模擬,對不同參數(shù)下的壁厚分布以及成形極限圖進行分析,并對不同參數(shù)對于成形結果的影響進行總結,綜合以上模擬結果得出最優(yōu)成形結果。副車架的液壓成形管成形工藝可以分為彎曲、預成形和內高壓成形三道工序。
3.1 彎曲
如圖5 所示,由于管坯是一根直管,因此需要預彎工序,將直管彎曲成與液壓成形管件最終形狀相近的U 形管,現(xiàn)實生產中使用數(shù)控機床來進行彎曲,并加裝多節(jié)活芯、防皺塊等組件,這是為了保證管件彎曲工序的精確程度。但是在彎曲過程中,可能會出現(xiàn)一些問題,常見的問題有:(1)內側管壁的起皺;(2)外側管壁的過度減?。唬?)回彈。
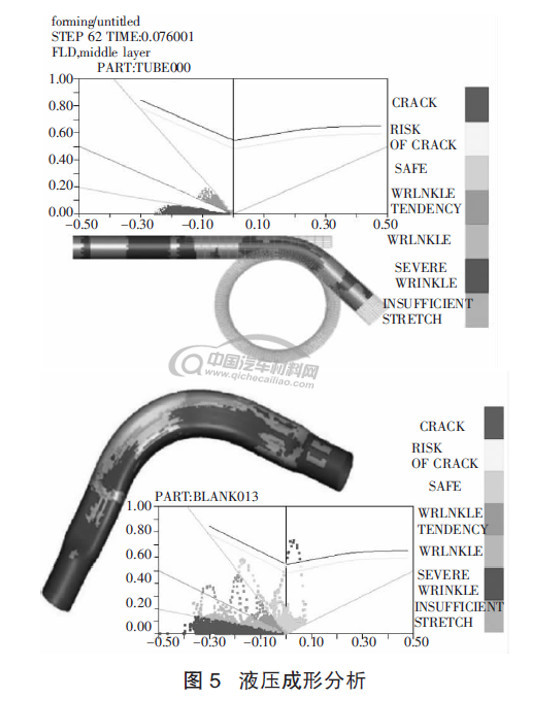
3.2 預成形
由于液壓成形管件的截面形狀復雜,考慮到最終成形質量和放入內高壓模具的可行性需要對于彎曲之后的管件進行預成形,使其成形過程具有更好的連續(xù)性和可行性,并且通過優(yōu)化預成形模具型面形狀,可以減小成形壓力和控制壁厚分布。所以預成形工序在副車架液壓成形管件整個成形工藝過程中至關重要。
3.3 內高壓成形
內高壓成形作為副車架液壓成形管件的最后一道工序,對于零件最終的質量有著至關重要的作用,要注意初始壓力、成形壓力、整形壓力的大小,并要對加載路徑進行優(yōu)化,避免出現(xiàn)破裂、起皺以及屈曲等缺陷。
4 臺架試驗
4.1 副車架要求
試驗樣件需正式得到認可的試驗報告必須在量產達到抽樣基數(shù)后進行符合設計圖樣要求,試驗樣件不得少于4 件,試驗樣件必須為隨機抽取,抽樣基數(shù)不少于200 件。前期試制驗證階段的樣件每批都要抽樣進行試驗,試制階段的抽樣基數(shù)不能少于10件,每次試驗的樣品不能少于2 件。在試驗過程中,視試驗部件的破壞或失效程度決定何時終止試驗,在試驗中若發(fā)現(xiàn)橡膠襯套或其他陪試零件提前損壞或失效,應及時更換該零件,并記錄疲勞試驗次數(shù)及相關零件的破壞程度。使副車架樣件以及對手件(副車架安裝墊片、緩沖塊、上下擺臂、后穩(wěn)定桿、螺旋彈簧、減振器、后懸縱臂、后懸縱臂安裝支架、穩(wěn)定桿拉桿、橡膠件等)在試驗臺上按照設計空載狀態(tài)位置進行裝配,如圖6 所示。
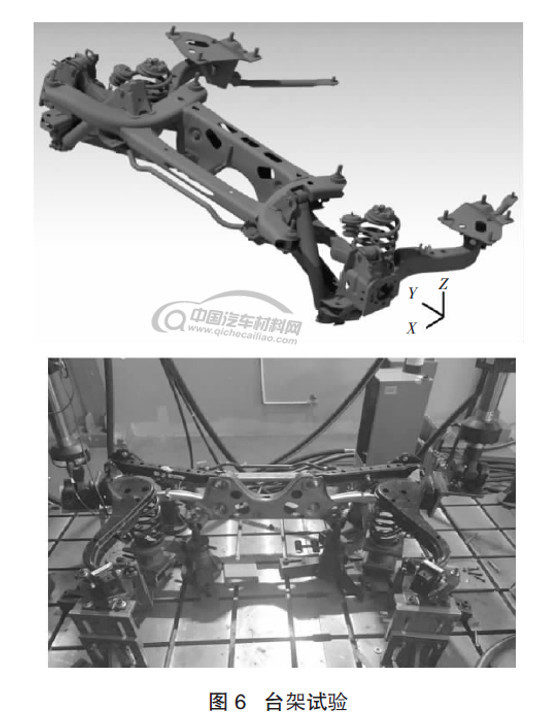
4.2 側向力疲勞試驗
側向力加載點為左右輪心點處,左右兩邊同步加載,加載頻率為1~3 Hz,兩端側向力加載-FY(向車輛外側)、+FY(向車輛內側),加載力+FY = 15 000 N,加載力-FY = 4 000 N.
4.3 縱向力疲勞試驗
縱向力加載點為左右輪心點處,左右兩邊同步加載,加載頻率為1~3 Hz,兩端側向力加載-FX(向車輛前方)、+FX(向車輛后方),加載力±FX = 3 500 N.
4.4 垂向力疲勞試驗
垂向加載點為左右輪心點處,加載方向±Fz,以擺臂球頭空載位置為基準,+Fz 距離為車輪上跳行程+125 mm,-Fz距離為車輪下跳行程-95 mm,左右兩邊相位相差180°,頻率為1~3 Hz.
4.5 試驗判斷
副車架在進行40 萬次循環(huán)內不允許產生明顯的永久變形或出現(xiàn)裂紋,每2000 次循環(huán)檢查一次。
5 可靠性道路試驗
路況分配如表3 所列。
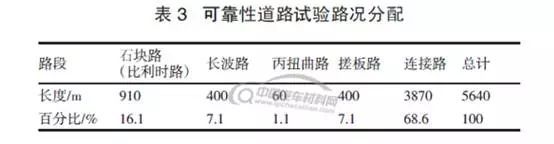
試驗路線:起點→石塊路→長波路→扭曲路(丙)→外部噪聲測試路→帶角度搓板路→錯位搓板路→長波路→扭曲路(丙)→外部噪聲測試路→石塊路。其中壞路占31.4%,連接路面占68.6%.
整車可靠性試驗場路面綜合強化系數(shù)20,試驗車按7 座滿載加載進行可靠性試驗,滿載狀態(tài)為:整車油水加滿(或用重物擬合),隨車工具齊全、安裝備胎,乘員按以下方式加載:整車布置方式:前排乘坐兩個人,后中間乘坐三個人,第三排乘坐兩個人,按標準每人重量(每人75 kg)進行加載,其余載荷按行李箱行李布置加載,循環(huán)試驗要求里程30 000 km,在試驗過程中要檢查試驗零部件是否有開裂、變形、異響等不良現(xiàn)象,并如實記錄和反饋,若有金屬失效件斷裂等故障,需將斷口用塑料材料封裝纏繞與空氣隔絕,防止生銹影響后續(xù)的斷面分析。試驗結果無永久變形或出現(xiàn)裂紋,通過可靠性道路試驗驗證。
6 結束語
有研究表明,若汽車整車重量降低10%,燃油效率可提高6% ~ 8%;汽車整備質量每減少100 kg,百公里油耗可降低0.51 L. 這使得輕量化被廣大汽車生產企業(yè)所重視。本文通過拓撲、形貌和性能等多目標優(yōu)化方法并結合液壓成形技術實現(xiàn)了輕量化目標,將某車型后副車架由原來的18.2 kg 降低到14.6kg,實現(xiàn)減重3.6 kg(19.7%),并通過試驗驗證和實現(xiàn)量產。
來源:《裝備制造技術》
作者:李武泉
(東風柳州汽車有限公司)
舉報 0
收藏 0
分享 108
-
乘用車金屬沖壓
2025-05-29 -
沖壓技術在電機疊片制造的應用
2024-09-06 -
車身零部件包邊質量控制要點
2024-09-05 -
輕量化技術——熱汽脹形工藝技術解析
2024-09-04
最新資訊
-
跨越速運憑什么“圈粉”萬千客戶?“
2025-07-01 14:42
-
數(shù)智破局啟新篇?生態(tài)共生再啟程 —
2025-06-27 20:13
-
助力汽車零部件產線智能化升級,西門
2025-06-27 13:59
-
BBA集體轉向!放棄全面電動化
2025-06-26 17:32
-
比換柜省錢,比自研省心,西門子Xcel
2025-06-25 15:07