汽車左右前地板多工位生產(chǎn)工藝研究
2019-01-15 21:18:45· 來源:《鍛造與沖壓》
通過優(yōu)化某汽車左右前地板的多工位生產(chǎn)工藝及模具結(jié)構(gòu)設(shè)計(jì),將左右件對接生產(chǎn),即一模兩件(傳輸方向)生產(chǎn)。有效降低了模具開發(fā)成本,將原來的八套模具減少至四套模具,減少了投資費(fèi)用,提高了材料利用率和生產(chǎn)效率,降低生產(chǎn)成本,節(jié)省
通過優(yōu)化某汽車左右前地板的多工位生產(chǎn)工藝及模具結(jié)構(gòu)設(shè)計(jì),將左右件對接生產(chǎn),即一模兩件(傳輸方向)生產(chǎn)。有效降低了模具開發(fā)成本,將原來的八套模具減少至四套模具,減少了投資費(fèi)用,提高了材料利用率和生產(chǎn)效率,降低生產(chǎn)成本,節(jié)省了模具存放空間。
目前汽車行業(yè)節(jié)奏越來越快,新車型的生準(zhǔn)周期越來越短,多工位的高柔性和高效率備受行業(yè)青睞,而為了充分發(fā)揮多工位的高生產(chǎn)效率,需要在零件的生產(chǎn)工藝上進(jìn)行充分研究。本文通過對多工位左右前地板的生產(chǎn)工藝進(jìn)行研究,得到一模雙件(傳輸方向)的新生產(chǎn)方式,希望給國內(nèi)采用大型多工位生產(chǎn)線生產(chǎn)的同行提供新的思路。
傳統(tǒng)生產(chǎn)工藝

圖1 汽車左右前地板零件
圖1為某車型左右前地板零件。左右前地板零件尺寸較大,單件尺寸(1250mm×600mm×160mm),拉延深度較深,局部起伏較大。受多工位對料片最大尺寸限制(圖2),考慮拉延工藝補(bǔ)充部分以及模具結(jié)構(gòu)布置要求,因此傳統(tǒng)生產(chǎn)方式采用單件生產(chǎn)。
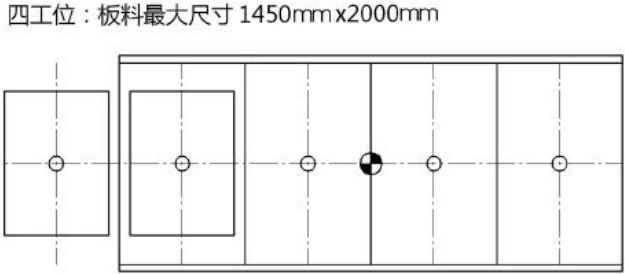
圖2 多工位板料最大尺寸要求
單件生產(chǎn)時(shí)需要對兩側(cè)進(jìn)行工藝補(bǔ)充,經(jīng)分析可以達(dá)到成形要求。確認(rèn)4工序內(nèi)容為:拉延、修邊(側(cè)修邊)、翻邊(側(cè)翻邊、側(cè)沖孔),如圖3所示。因需要考慮四角夾件,因此需要在四角留有至少30mm×30mm的夾持平面。經(jīng)分析確認(rèn),板料采用(1400mm×750mm)長方料,材料利用率=(零件凈重)4.2877kg÷(板料重量 )5.769kg =74.3%。
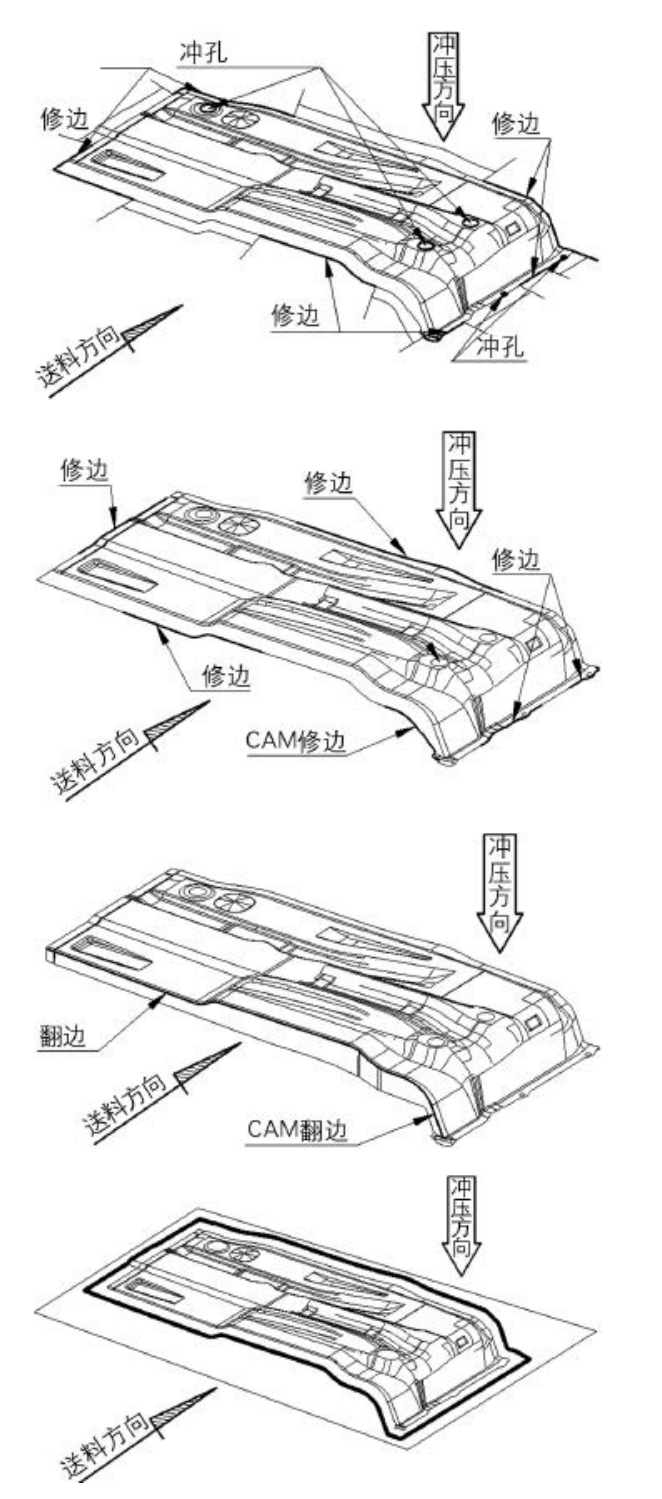
圖3 單件工藝分布圖
新型生產(chǎn)工藝
成形性分析
為了提升生產(chǎn)效率,左右前地板在多工位上采用一模兩件(傳輸方向)的生產(chǎn)方式,如要采用這種形式,就必須對整體尺寸進(jìn)行充分優(yōu)化,首先選擇在平面部分對接,中間連接最小間隙選擇20mm,翻邊補(bǔ)充部分取消,以板料法蘭邊和翻邊平面作為壓料面,充分減少工藝補(bǔ)充。經(jīng)分析對比,板料局部起皺趨勢較單件基本一致,減薄率有所增加但在可接受的范圍內(nèi),成形充分,可以達(dá)到成形要求。對比分析結(jié)果如圖4所示。
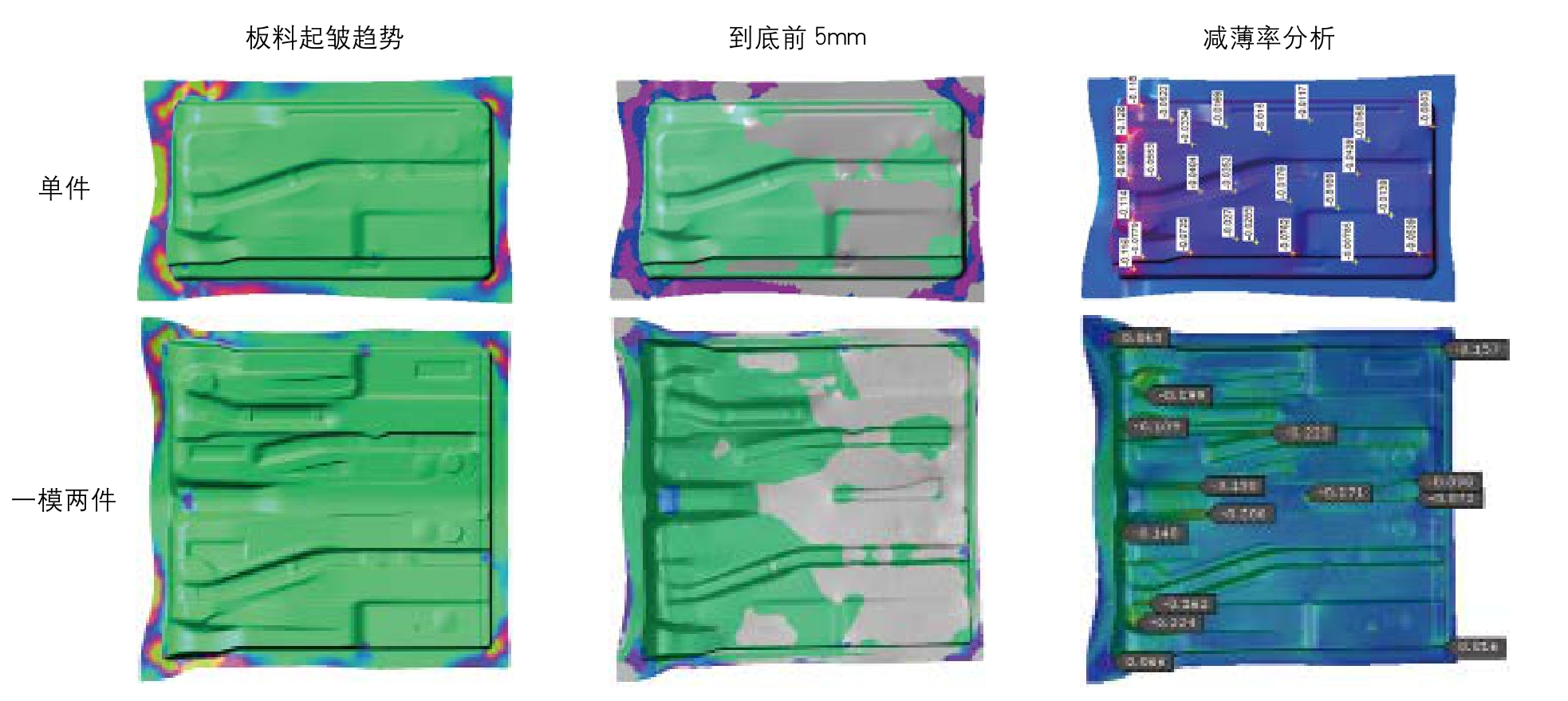
圖4 兩種工藝方式對比圖
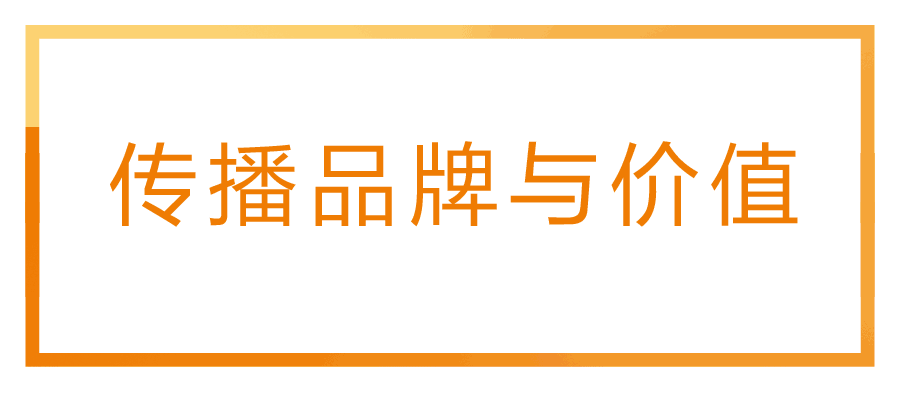
工序分布
結(jié)合零件特點(diǎn)和工藝分析結(jié)果,確認(rèn)4工序內(nèi)容為:拉延、修邊沖孔、翻邊整形、修邊分離沖孔側(cè)沖孔,如圖5所示。經(jīng)分析,板料采用(1380mm×138mm×1240mm)梯形料,材料利用率=(零件凈重)4.2877kg×2÷(板料重量)9.93kg=86.3%。
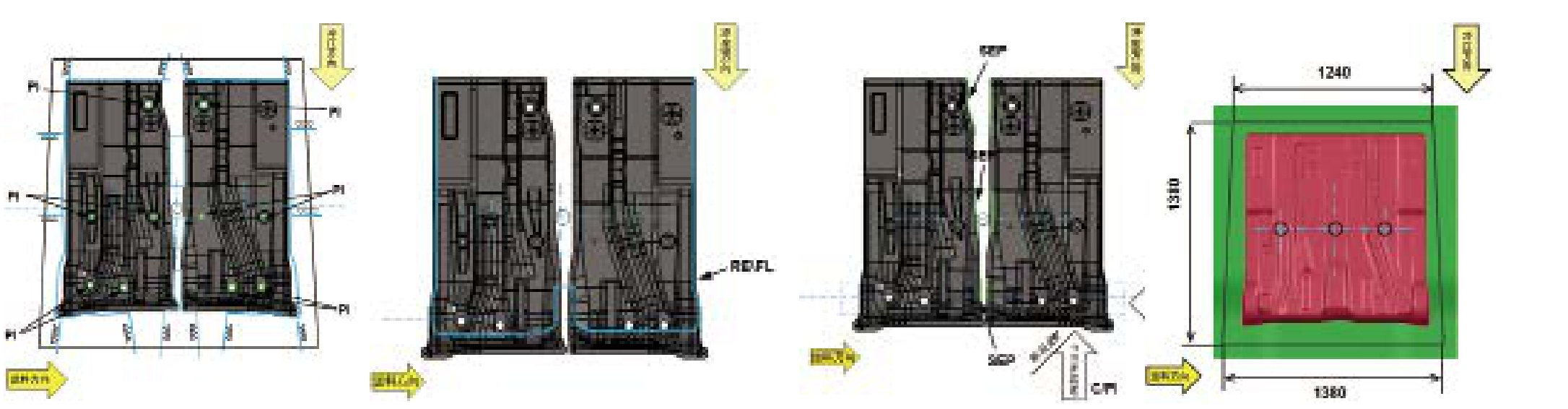
圖5 一模兩件工藝分布圖
模具結(jié)構(gòu)
因模具尺寸要求限制,一模兩件生產(chǎn)結(jié)構(gòu)需要采用特殊布置。這里主要是拉延結(jié)構(gòu)的選取,因板料最大尺寸為1380mm,而模具最大允許寬度為1750mm,因此單邊距離剩余185mm,因此需要謹(jǐn)慎布置,如圖6所示。采用插入式導(dǎo)板,壓邊圈局部深度較深處做鑲塊,上模也同樣做成鑲塊式,布置四處托起塊,每個(gè)托起塊都增加磁鐵,防止托起后零件不穩(wěn)定,局部模擬起皺區(qū)域增加刺破,增加翻轉(zhuǎn)托料定位架,保證板料不翹曲。
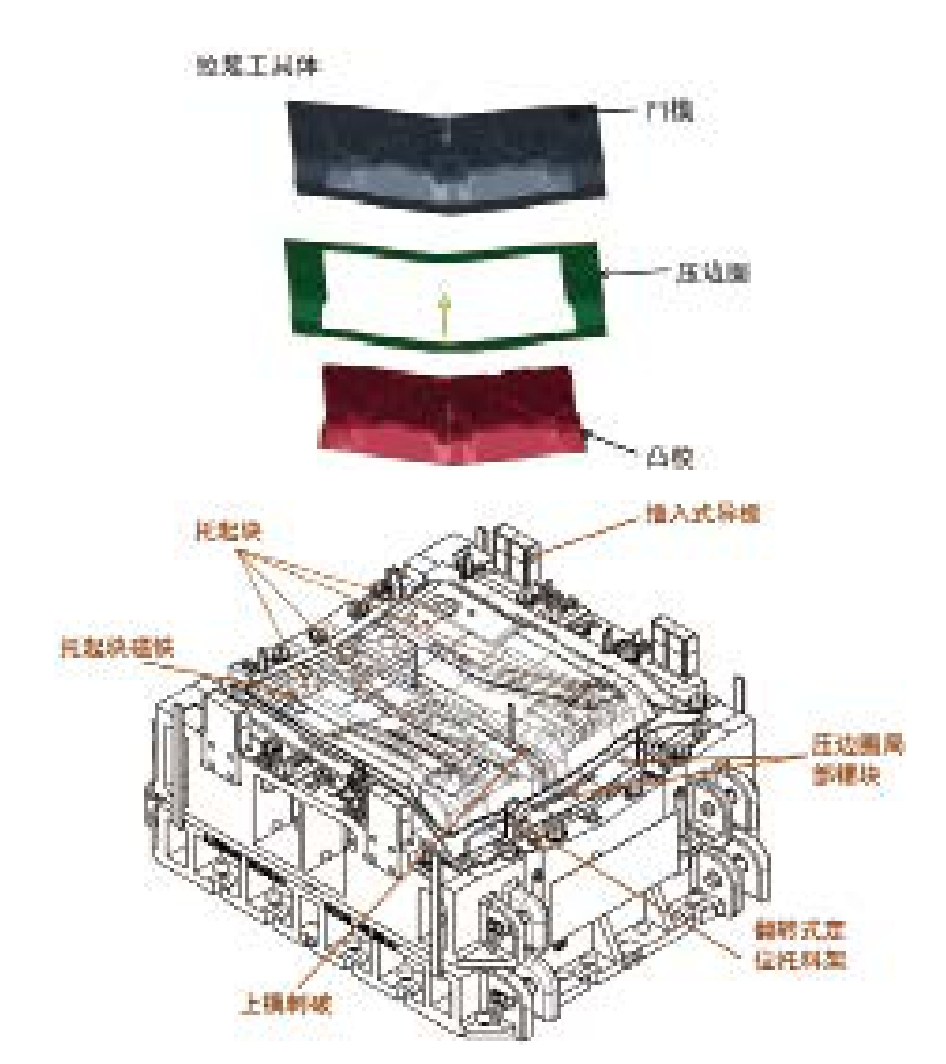
圖6 OP10拉延模具結(jié)構(gòu)示意圖
夾鉗傳輸
左右前地板因尺寸較大,板料和零件在傳輸過程中容易塌腰,為了提高零件傳輸穩(wěn)定性,每序上必須對單個(gè)零件進(jìn)行雙夾鉗夾持。最后一序分離工位,模具傳感器和夾鉗傳感器也必須分開布置,以保證兩個(gè)零件的傳輸,如圖7所示。
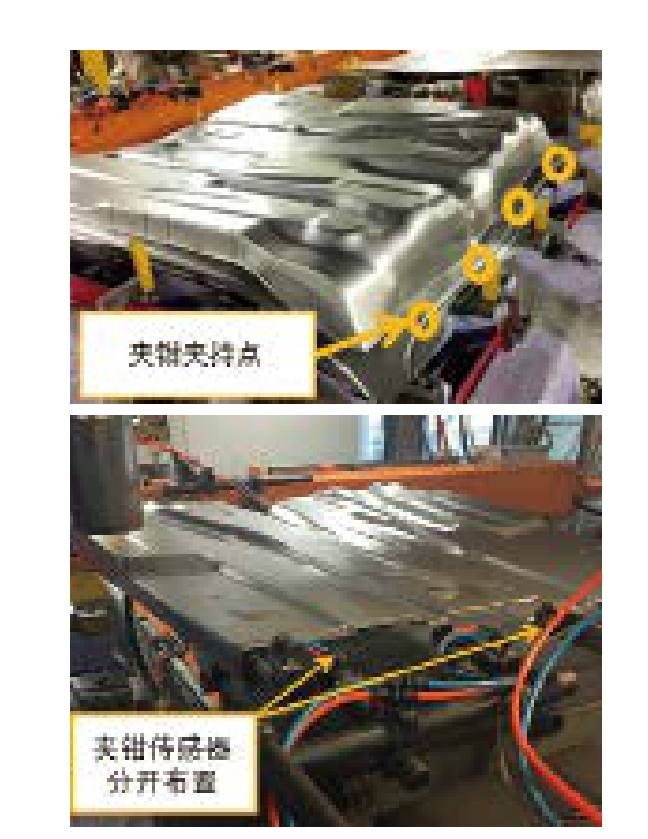
圖7 夾鉗夾持點(diǎn)和最后一序分離夾件
結(jié)束語
多工位生產(chǎn)工藝是汽車產(chǎn)業(yè)為滿足飛速發(fā)展產(chǎn)生的新工藝技術(shù),此技術(shù)已成為車身沖壓件快速制造的保證。多工位生產(chǎn)可以大大提高車身工藝裝備產(chǎn)品的質(zhì)量,縮短工期,降低成本。本文通過對左右前地板生產(chǎn)工藝的研究,提供了新型一模雙件(傳輸方向)的生產(chǎn)方式,左右前地板材料利用率提升了12%,生產(chǎn)效率提升了一倍,減少了30%的模具投資,節(jié)省了存放面積,縮短了換模時(shí)間和停機(jī)時(shí)間。
舉報(bào) 0
收藏 0
分享 121
-
乘用車金屬沖壓
2025-05-29 -
沖壓技術(shù)在電機(jī)疊片制造的應(yīng)用
2024-09-06 -
車身零部件包邊質(zhì)量控制要點(diǎn)
2024-09-05 -
輕量化技術(shù)——熱汽脹形工藝技術(shù)解析
2024-09-04
最新資訊
-
跨越速運(yùn)憑什么“圈粉”萬千客戶?“
2025-07-01 14:42
-
數(shù)智破局啟新篇?生態(tài)共生再啟程 —
2025-06-27 20:13
-
助力汽車零部件產(chǎn)線智能化升級,西門
2025-06-27 13:59
-
BBA集體轉(zhuǎn)向!放棄全面電動化
2025-06-26 17:32
-
比換柜省錢,比自研省心,西門子Xcel
2025-06-25 15:07