淺談汽車凸輪塊精密鍛造技術(shù)與裝備
2018-12-27 22:21:06· 來源:高崇暉 鍛造與沖壓
凸輪軸是汽車發(fā)動(dòng)機(jī)的關(guān)鍵部件之一,其作用是按照發(fā)動(dòng)機(jī)的工作循環(huán)精確控制氣門的開啟和閉合動(dòng)作,使得進(jìn)氣、排氣都比較充分,由于氣門運(yùn)動(dòng)規(guī)律直接影響著發(fā)動(dòng)機(jī)的動(dòng)力和運(yùn)轉(zhuǎn)特性,因此凸輪軸在發(fā)動(dòng)機(jī)部件中有著十分重要的地位。在工作狀
凸輪軸是汽車發(fā)動(dòng)機(jī)的關(guān)鍵部件之一,其作用是按照發(fā)動(dòng)機(jī)的工作循環(huán)精確控制氣門的開啟和閉合動(dòng)作,使得進(jìn)氣、排氣都比較充分,由于氣門運(yùn)動(dòng)規(guī)律直接影響著發(fā)動(dòng)機(jī)的動(dòng)力和運(yùn)轉(zhuǎn)特性,因此凸輪軸在發(fā)動(dòng)機(jī)部件中有著十分重要的地位。在工作狀態(tài)下,凸輪軸的轉(zhuǎn)速很高且需承受周期性的沖擊載荷,因此對(duì)凸輪軸的精度、強(qiáng)度、耐磨性和支撐方面的要求很高。
裝配式凸輪軸的優(yōu)勢(shì)
凸輪軸的傳統(tǒng)制造方法主要由整體鑄造、鍛造或軋制生產(chǎn)毛坯,后續(xù)采用繁瑣的機(jī)加工工序去除多余的材料達(dá)到精度要求,整套工序耗時(shí)耗力,且材料利用率較低,也無法滿足各工作部位的不同性能要求。
裝配式凸輪軸設(shè)計(jì)采用“化整為零”的方法,將凸輪塊、芯軸等部件分開制造,如凸輪塊毛坯一般以精密塑性成形方法制造,芯軸用無縫鋼管冷拔,最后采用熱裝、冷裝或滾花等方式進(jìn)行組裝后再進(jìn)行精加工,這種裝配式制造方法在凸輪軸整體重量降低(20% ~ 40%)、提高材料利用率、縮短機(jī)加工工時(shí)、實(shí)現(xiàn)生產(chǎn)自動(dòng)化和提升發(fā)動(dòng)機(jī)性能等方面有著顯著的優(yōu)勢(shì)。因此,裝配式凸輪軸符合汽車輕量化和節(jié)能環(huán)保的發(fā)展趨勢(shì)。
裝配式凸輪軸主要應(yīng)用于高性能發(fā)動(dòng)機(jī),目前,世界上許多發(fā)動(dòng)機(jī)制造商越來越多使用裝配式凸輪軸制造新技術(shù)。同時(shí),隨著國(guó)內(nèi)自主研發(fā)水平的提高,裝配式凸輪軸已廣泛應(yīng)用于合資和自主品牌汽車,已展現(xiàn)出廣闊的應(yīng)用前景。
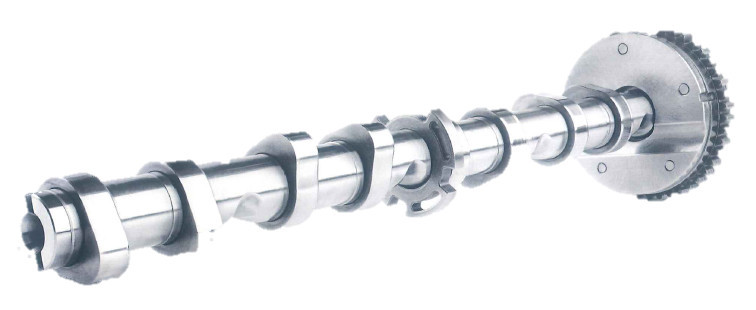
圖1 裝配式凸輪軸
凸輪塊鍛件要求
凸輪塊鍛件是精鍛件,其尺寸和形位公差及表面質(zhì)量要求很高,圖2 為凸輪塊的鍛件圖。一般來說,端面為非機(jī)加工面或留少量磨削余量,凸輪輪廓面只留幾十絲的磨削加工余量,內(nèi)孔有少量機(jī)加工余量,鍛造圓角要求在R1 以內(nèi),凸輪輪廓度在0.2mm,兩端面平行度在0.25mm,表面磕碰痕跡深度在0.3mm以內(nèi),局部脫碳層深度需控制在0.1mm 以內(nèi)。此外,每根凸輪軸大約配有8 ~ 10 片凸輪塊,凸輪塊的用量很大,如何按時(shí)保質(zhì)保量地交貨也成為鍛件生產(chǎn)中的一大難題。
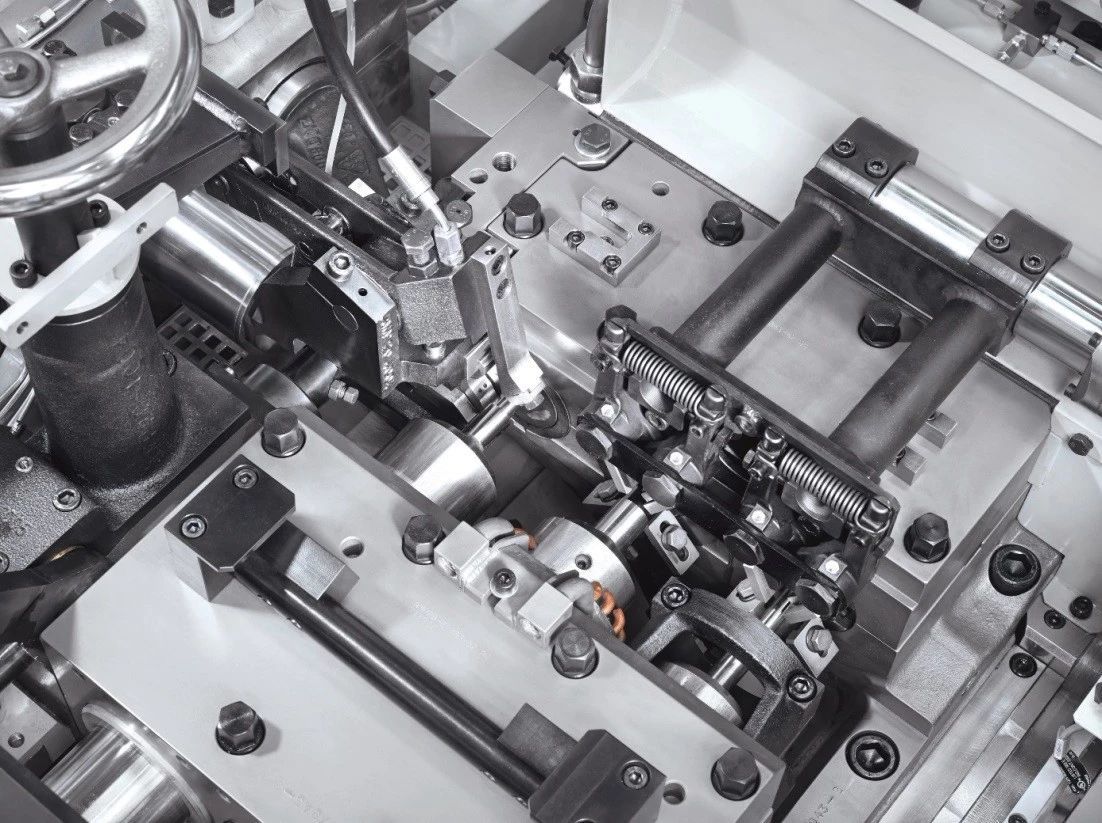
凸輪塊鍛件生產(chǎn)設(shè)備
凸輪塊鍛件采用“近凈成形”鍛造技術(shù)生產(chǎn),這就需要使用專業(yè)化和自動(dòng)化程度很高的設(shè)備。高速熱鐓機(jī)是一種高速、精密成形和全自動(dòng)化的鍛造設(shè)備,是凸輪塊這類鍛件的生產(chǎn)利器。以瑞士哈特貝爾熱鐓機(jī)AMP20N(圖3)為例,配合自動(dòng)上料和中頻感應(yīng)加熱,棒料加熱后進(jìn)行剪切下料,經(jīng)過三個(gè)工位成形(含沖孔),生產(chǎn)節(jié)拍最高可達(dá)每分鐘200 件。而且,生產(chǎn)過程全部實(shí)現(xiàn)自動(dòng)化,基本排除人為因素對(duì)鍛件質(zhì)量產(chǎn)生影響。主要技術(shù)參數(shù)如表1 所示。
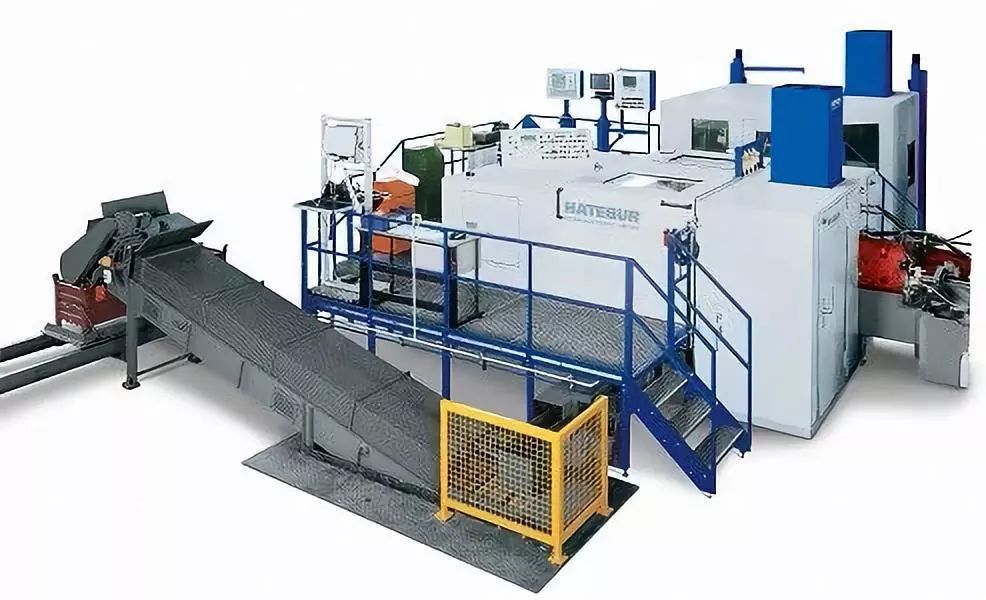
圖3 AMP20N 高速熱鐓機(jī)
表1 AMP20N 的技術(shù)參數(shù)
技術(shù)參數(shù)
AMP20N
成形工位數(shù)
3
生產(chǎn)節(jié)拍
140-200 spm
總成形噸位
1500 kN
第一、三工位最大成形力
400 kN
第二工位最大成形力
1300 kN
圓形鍛件最大外徑
41 mm
棒料直徑
14~28 mm
下料重量
24~217 g
下料長(zhǎng)度
20~45 mm
工藝與模具設(shè)計(jì)
凸輪塊毛坯的外輪廓為凸輪形狀,為異形非回轉(zhuǎn)體類鍛件,鍛件需沖孔。第一工位的預(yù)成形體積分配成為工藝設(shè)計(jì)的關(guān)鍵,需要根據(jù)設(shè)計(jì)經(jīng)驗(yàn)進(jìn)行初始設(shè)計(jì),主要目的是向凸輪桃尖區(qū)域聚集材料,在終鍛時(shí)可以同時(shí)充滿不同的區(qū)域,合理的體積分配才能保證不產(chǎn)生毛刺或大的圓角,成形力也可以控制在合理的范圍。CAE 軟件模擬可優(yōu)化預(yù)成形的形狀,得到合理的工藝,圖4 和圖5 為兩個(gè)工位的模擬情況。
模具采用組合式設(shè)計(jì),根據(jù)部件的功能選擇適合的材料及相應(yīng)的熱處理和表面處理工藝。特別是非回轉(zhuǎn)體類的易損件模具,可以顯著降低模具成本。
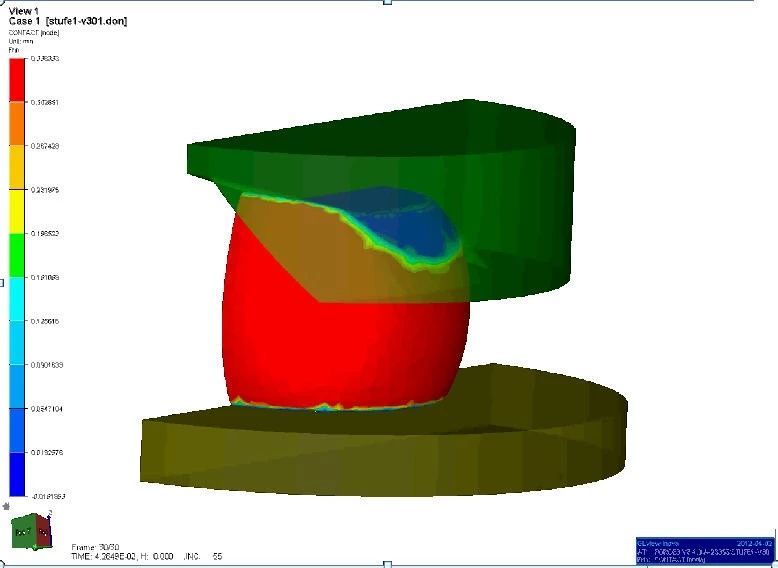
圖4 第一工位預(yù)成形
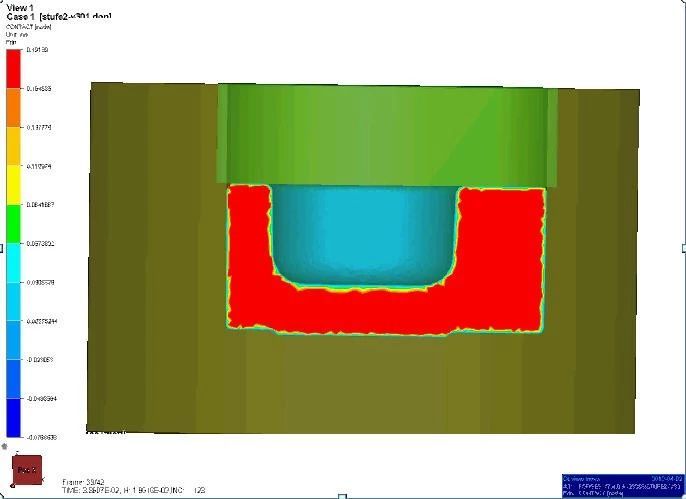
圖5 第二工位終鍛成形
根據(jù)高速熱鐓機(jī)的工藝特點(diǎn),使用的原材料為圓鋼,熱剪切下料,第一工位進(jìn)行預(yù)成形,第二工位終鍛成形,第三工位進(jìn)行沖孔。模具的三維模型設(shè)計(jì)如圖6 所示。高速熱鐓機(jī)的模具布局為水平布置,剪切下料后的料段由剪切頭傳送至第一工位成形,同時(shí),二三工位成形的工件由機(jī)械手傳送至下一工位。長(zhǎng)棒料的料頭料尾部位由設(shè)備ESA 電子剔料系統(tǒng)自動(dòng)識(shí)別及丟料。模具工作區(qū)域及機(jī)械手的結(jié)構(gòu)如圖7 所示。
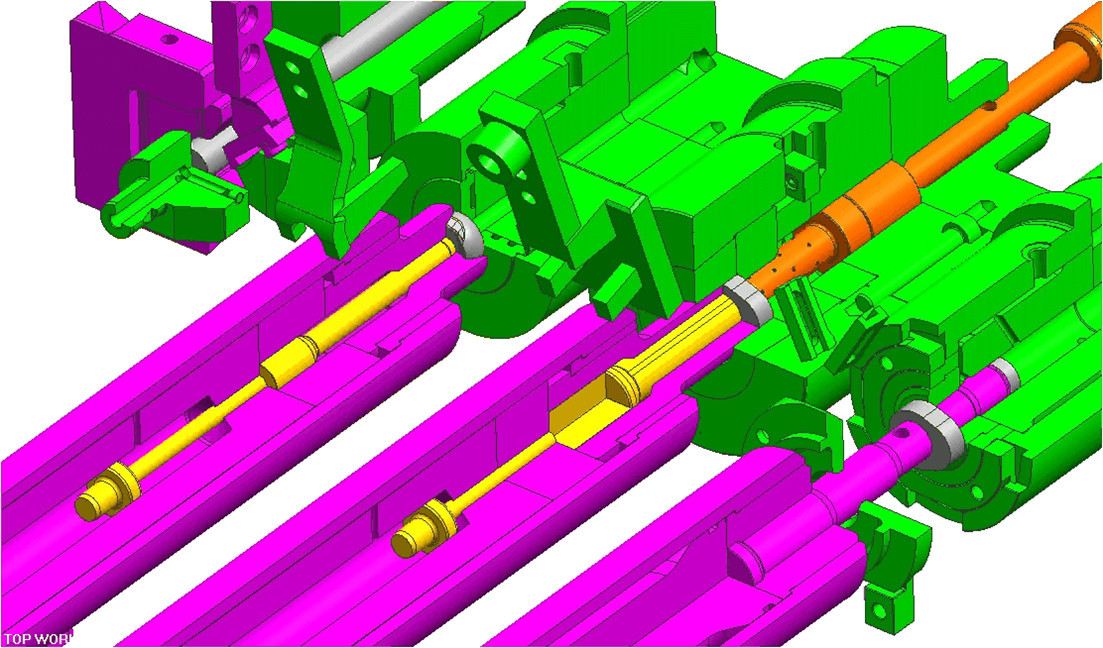
圖6 模具三維模型
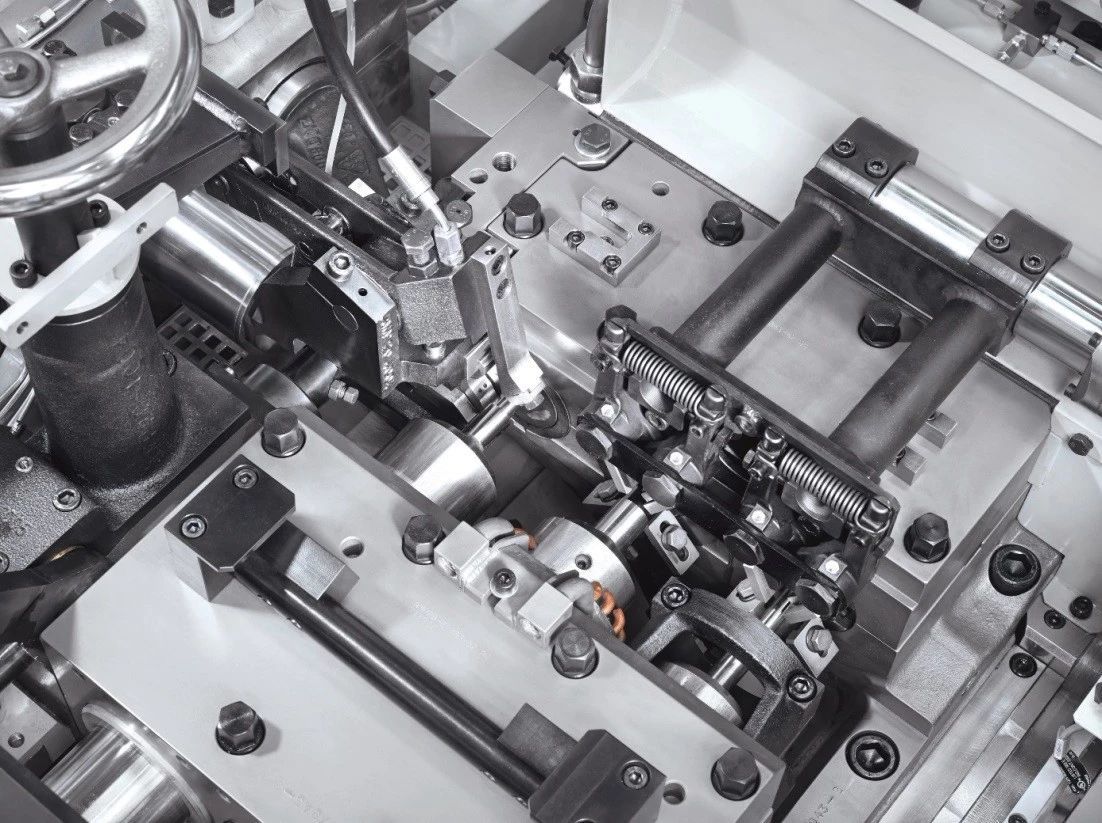
圖7 模具工作區(qū)域
大批量生產(chǎn)
高速熱鐓機(jī)生產(chǎn)線(圖8)主要由上料架⑤、中頻感應(yīng)加熱爐②、熱鐓機(jī)③和傳送帶④組成,模具冷卻直接采用水冷,需要配套相應(yīng)的冷卻水回收循環(huán)系統(tǒng)①。此外,凸輪塊鍛件原材料一般為軸承鋼,需特別注意鍛后鍛件與冷卻水的接觸時(shí)間,避免產(chǎn)生水淬裂紋。
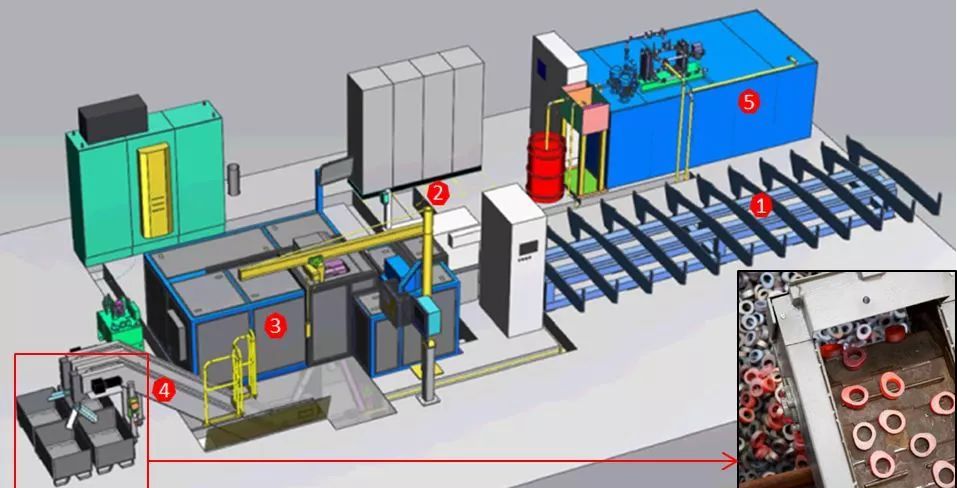
圖8 高速熱鐓機(jī)生產(chǎn)線
圖9 為批量生產(chǎn)的凸輪塊鍛件,經(jīng)過優(yōu)化預(yù)成形體積分配,終鍛成形后的凸輪塊端面邊緣充填飽滿,尤其是桃尖部位的鍛造圓角很小,凸輪輪廓度及端面平面度均達(dá)到圖紙要求。凸輪塊鍛件經(jīng)過退火、拋丸處理后進(jìn)行內(nèi)孔機(jī)加工,裝配至芯軸后再進(jìn)行輪廓磨削及表面淬火。
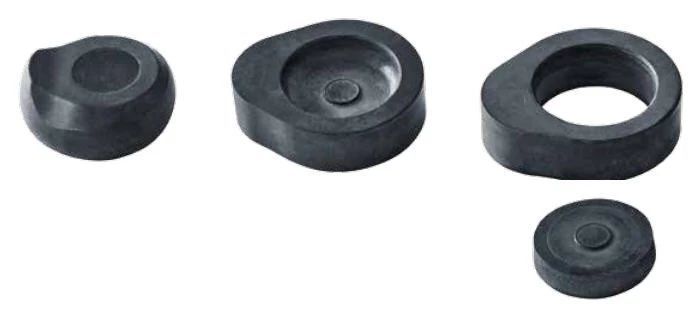
圖9 凸輪塊鍛件
結(jié)論
在汽車輕量化的發(fā)展趨勢(shì)下,裝配式凸輪軸的市場(chǎng)需求越來越大,相應(yīng)凸輪塊鍛件的市場(chǎng)需求量也越來越大。凸輪塊毛坯作為非回轉(zhuǎn)體類鍛件,尺寸公差小、本身質(zhì)量及一致性要求高。應(yīng)用多工位精密鍛造技術(shù),優(yōu)化凸輪塊鍛件的預(yù)成形形狀,實(shí)現(xiàn)合理的體積分配,使得圓角填充度滿足圖紙要求。分析高速熱鐓機(jī)的工藝特點(diǎn),驗(yàn)證了其是凸輪塊鍛件的高效大批量生產(chǎn)的適合設(shè)備。
——本文選自《鍛造與沖壓》2018年第23期
舉報(bào) 0
收藏 0
分享 124
-
乘用車金屬?zèng)_壓
2025-05-29 -
沖壓技術(shù)在電機(jī)疊片制造的應(yīng)用
2024-09-06 -
車身零部件包邊質(zhì)量控制要點(diǎn)
2024-09-05 -
輕量化技術(shù)——熱汽脹形工藝技術(shù)解析
2024-09-04
最新資訊
-
跨越速運(yùn)憑什么“圈粉”萬千客戶?“
2025-07-01 14:42
-
數(shù)智破局啟新篇?生態(tài)共生再啟程 —
2025-06-27 20:13
-
助力汽車零部件產(chǎn)線智能化升級(jí),西門
2025-06-27 13:59
-
BBA集體轉(zhuǎn)向!放棄全面電動(dòng)化
2025-06-26 17:32
-
比換柜省錢,比自研省心,西門子Xcel
2025-06-25 15:07