汽車總裝工藝內(nèi)部物流模式的突破
2018-12-25 20:17:43· 來源:汽車供應(yīng)鏈物流規(guī)劃與改善
本文對中國汽車制造業(yè)總裝車間的內(nèi)部物流進(jìn)行了深入分析,目前汽車制造業(yè)普遍推行精益生產(chǎn)方式,該方式的主要特點(diǎn)是:多品種小批次隨機(jī)混流生產(chǎn)。隨著品種的增加,批次的減小,汽車零件按車型種類供給的不斷增多與線邊零件存放面積不足的
本文對中國汽車制造業(yè)總裝車間的內(nèi)部物流進(jìn)行了深入分析,目前汽車制造業(yè)普遍推行精益生產(chǎn)方式,該方式的主要特點(diǎn)是:多品種小批次隨機(jī)混流生產(chǎn)。隨著品種的增加,批次的減小,汽車零件按車型種類供給的不斷增多與線邊零件存放面積不足的矛盾日益凸顯。以往采用的解決方案是通過增大線邊零件存放面積來緩和該種矛盾,但目前可增加的空間已趨于飽和而且此種方案還會(huì)帶來庫存增加,作業(yè)取料損失加劇,內(nèi)部物流復(fù)雜混亂等一系列負(fù)面影響。因此我們借助現(xiàn)代IE技術(shù),對此種問題進(jìn)行革新性的改善,同時(shí)也為IE技術(shù)在汽車制造業(yè)的發(fā)展運(yùn)用方向進(jìn)行探索,本次將以某公司總裝底盤線綜合物流改善為例,對于上述觀點(diǎn)進(jìn)行說明。
一、某公司IE推進(jìn)現(xiàn)狀
早在80年代末,此公司就引進(jìn)了日產(chǎn)柴“一個(gè)流”的生產(chǎn)方式,經(jīng)過7個(gè)月的推進(jìn),在當(dāng)時(shí)此公司生產(chǎn)能力最薄弱的環(huán)節(jié)上獲得了成功:當(dāng)年轉(zhuǎn)向節(jié)生產(chǎn)線產(chǎn)量增長了29.8%,人員減少28%,廢品率下降68%,在制品減少79.9%,設(shè)備故障停工率下降了84%。而合資方日產(chǎn)汽車公司在推進(jìn)工業(yè)工程方面也形成了一套完整的推進(jìn)方法??梢哉f在合資公司成立之前在IE推進(jìn)方面就已經(jīng)打下了較好的基礎(chǔ)。
合資后此公司非常重視IE部門的建設(shè),在成立之初就在某工廠建立了IE/GK科(GK是日語中現(xiàn)場管理的縮寫)。目前IE/GK科有工程師11人,改善員11人,改善中心裝配場一處,負(fù)責(zé)工廠的中期方針規(guī)劃、工廠及各科室關(guān)鍵績效指標(biāo)的設(shè)定、日產(chǎn)生產(chǎn)方式的推進(jìn)、制造成本的管理、勞動(dòng)生產(chǎn)力的提升和現(xiàn)場改善活動(dòng)的推進(jìn)等重要工作。從職能上看,包括了IE的三個(gè)技術(shù)群:分析型技術(shù)群、規(guī)劃與設(shè)計(jì)型技術(shù)群和管理與控制型技術(shù)群,而且還成立了一個(gè)專職進(jìn)行低成本自動(dòng)化技術(shù)應(yīng)用的改善中心。
此公司還非常重視IE學(xué)科的建設(shè),近幾年一直保持與清華大學(xué)工業(yè)工程系的良好合作關(guān)系,每年接收清華實(shí)習(xí)生進(jìn)行工廠實(shí)習(xí)。公司還關(guān)注IE學(xué)科新興技術(shù)的發(fā)展,定期派員參加國內(nèi)外的學(xué)習(xí)進(jìn)修,并于2007年購置專業(yè)仿真軟件EXTEND,投入力量進(jìn)行應(yīng)用研究,并取得顯著的效果。
二、此工廠總裝底盤線物流綜合改善案例
1.工廠背景介紹
此工廠是此公司主要的成品車生產(chǎn)廠,產(chǎn)量達(dá)到此公司全部產(chǎn)量的80%左右,截至2008年10月,累計(jì)生產(chǎn)820,688臺(tái)。工廠采用模擬訂單化生產(chǎn),完全混流模式,工廠產(chǎn)能設(shè)計(jì)為年產(chǎn)36萬臺(tái)。
2.總裝車間背景介紹與案例總體介紹
總裝車間是此工廠占地最大、人員最多、產(chǎn)能最大的車間。2004年5月建成,占地58500平方米,共有兩條裝配線,最大設(shè)計(jì)產(chǎn)能45萬臺(tái)/年。目前生產(chǎn)車型為8種,無規(guī)則混流上線??傃b車間總?cè)藬?shù)為932人。
此案例是通過對底盤線線邊物流現(xiàn)狀與需求矛盾的分析,依次展開供料模式、運(yùn)輸模式和布局優(yōu)化等方面,揭示總裝工藝內(nèi)部物流的變化趨勢,探尋IE 新興技術(shù)與現(xiàn)場改善的結(jié)合點(diǎn)。
在此案例中,可以看到線邊供貨模式從“One Pitch”(單品供給)模式到“Strike Zone”(單品同步供給)模式最終發(fā)展到“Block & KIT”(KIT同步供給)模式。線邊供貨模式不斷向更高的柔性化程度和更簡便的作業(yè)方式發(fā)展。
“One Pitch”(單品供給)------在線邊設(shè)定固定料位,專職物流人員通過牽引車將零件批量供給到線邊。
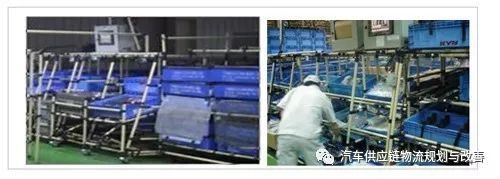
單品供給相對于最原始的料箱直送有一定的提升,解決了零件先進(jìn)先出和空料箱切換的問題,供給范圍廣,空間利用率高。但存在取料距離遠(yuǎn),取料動(dòng)作幅度大等問題,對于作業(yè)人員的體力和零件識(shí)別要求較高。
“Strike Zone”(單品同步供給)------對部分體大件,顏色件,以件為單位,在集配區(qū)將零件按照車輛生產(chǎn)順序進(jìn)行排列,在適當(dāng)?shù)臅r(shí)間供給到線邊。
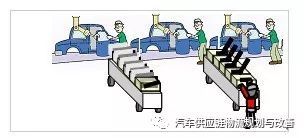
單品同步供給解決部分大零件和零件模塊的料位面積問題,改善了取料動(dòng)作,削減了零件辨識(shí)作業(yè)。但取料步行依然存在,集配區(qū)開始出現(xiàn),增加了集配人員。在這個(gè)階段沒有取得生產(chǎn)效率的有效提升,但為后續(xù)的改善指出了方向。
“Block & KIT”(KIT同步供給)------對整車生產(chǎn)用的零件,以一段生產(chǎn)線需求的所有零件為單位,在集中的集配區(qū)將零件按照車輛生產(chǎn)計(jì)劃排列放置在KIT BOX(臺(tái)套料箱)中,在適當(dāng)?shù)臅r(shí)間供給到線邊。
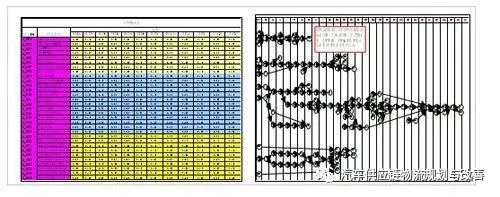
KIT同步供給削減了取料步行和辨識(shí)作業(yè)、減輕了取料作業(yè)負(fù)荷,為模塊化作業(yè)編成提供了條件。同時(shí)將線上取料作業(yè)損失集中并轉(zhuǎn)移到了集配區(qū),為實(shí)施第三方物流或物流自動(dòng)化創(chuàng)造了條件。KIT同步供給是線邊供貨模式的最高形態(tài)。
3.現(xiàn)狀與損失把握
底盤線目前生產(chǎn)車型為4種,生產(chǎn)所需各種物料達(dá)到446種,主要的大件有儀表臺(tái)、發(fā)動(dòng)機(jī)艙、后背門飾板和保險(xiǎn)杠等,車型間零件差異非常大。
整個(gè)底盤線只有約60米長,10個(gè)工位,446種零件供貨模式大部分采用“One Pitch”模式,少量大零件采用了“Strike Zone”模式,線邊面積已基本用完。但后續(xù)將再增加一種X車型,預(yù)計(jì)又會(huì)增加零件約100種。這種情況下延續(xù)原有的供貨模式則有較大的難度,而且不利于生產(chǎn)效率的進(jìn)一步提升。
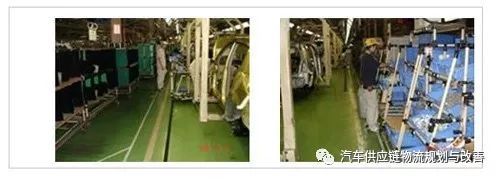
由于地板鏈的安全性要求,所以斜坡料架距離工位約1.5米,往返一次需4-6步,且每個(gè)工位都有裝配作業(yè),所以大量的取料作業(yè)分散在各個(gè)工位,形成各工位損失分散,不易改善的局面。
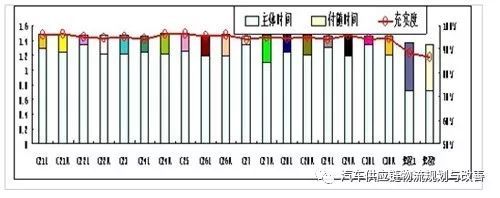
4.改善思路
要解決線邊料位不足的問題,就要從供料方式著手考慮。對于任何一種供料方式來說,在正確的時(shí)間將正確的零件送到正確的工位是終極的目標(biāo)。
傳統(tǒng)的“One Pitch”是完全建立在物流作業(yè)和裝配作業(yè)分離的角度進(jìn)行設(shè)計(jì),將物流系統(tǒng)和作業(yè)系統(tǒng)割裂開來,只考慮了物流作業(yè)本身的順暢和批量運(yùn)輸效率,但對整個(gè)系統(tǒng)的生產(chǎn)效率來說是不利的。
“Strike Zone”是從人機(jī)工程的角度出發(fā)進(jìn)行設(shè)計(jì),初衷是削減大零件的辨識(shí)作業(yè)和降低取料作業(yè)負(fù)荷。改善的效果分散在多個(gè)工位,難以形成規(guī)模效果,并且由于集配區(qū)的出現(xiàn)更降低了整個(gè)系統(tǒng)的生產(chǎn)效率,是典型的以效率換取空間、品質(zhì)、安全的形式,但提供了一種將損失從作業(yè)工位剝離并集中化的思想,為后續(xù)改善指出了方向。
“Block & KIT”是綜合了物流設(shè)計(jì)、人機(jī)工程和作業(yè)平衡多方面考慮的理想模式。損失的集中化和轉(zhuǎn)移同時(shí)為后續(xù)的低成本自動(dòng)化搬運(yùn)系統(tǒng)提供了改善空間。
所以此案例采用“Block & KIT”作為目標(biāo)姿態(tài),從線上損失集中化開始,逐步實(shí)現(xiàn)損失的集中和削減,最終達(dá)成改善效果。
5.KIT集配系統(tǒng)
基于“為每一臺(tái)車僅提供這一臺(tái)車所需的零件”思想,導(dǎo)入了同步配套供貨系統(tǒng),簡稱KIT系統(tǒng)。
· KIT系統(tǒng)通過在生產(chǎn)線設(shè)立集配區(qū),將每一臺(tái)份的物料放置在一臺(tái)物料小車中,按照生產(chǎn)順序投放上線,跟隨生產(chǎn)線前進(jìn),起到流動(dòng)料位的作用,而且取消了作業(yè)人員選取物料和拆包裝的作業(yè)。
KIT的構(gòu)思是比較簡單的,困難的部分在于小車如何跟隨生產(chǎn)線前進(jìn),如何實(shí)現(xiàn)小車與工位的相對靜止,如何保證小車、零件和產(chǎn)品車的匹配以及如何避免小車對作業(yè)的干涉。
在小車的前進(jìn)動(dòng)力和定位部分,發(fā)揮低成本自動(dòng)化思想中“充分發(fā)揮現(xiàn)有制造設(shè)備動(dòng)力余量”的要求,通過巧妙的小機(jī)關(guān)設(shè)計(jì),利用一個(gè)簡單的聯(lián)動(dòng)支桿,將小車與主線聯(lián)結(jié),借助主線的動(dòng)力前進(jìn)并保持相對固定的位置。既可以降低整個(gè)項(xiàng)目投資和技術(shù)難度,又提高了可靠性和可維護(hù)性。
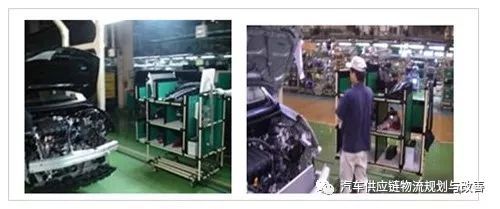
在保證小車、零件和產(chǎn)品車的匹配部分,選擇通過集配區(qū)的集配指示系統(tǒng)實(shí)現(xiàn)。在物料集配區(qū)接入生產(chǎn)系統(tǒng)終端,接受生產(chǎn)管理系統(tǒng)的后續(xù)生產(chǎn)計(jì)劃;在每種零件的料箱上方設(shè)置指示燈和計(jì)數(shù)器;中央處理器將生產(chǎn)計(jì)劃分解為所需零件指示,則對應(yīng)的零件料箱上指示燈亮起,集配人員取料后按下計(jì)數(shù)器,則指示燈熄滅;待一臺(tái)車所需全部零件取料完成后給出集配結(jié)束指示,同時(shí)系統(tǒng)進(jìn)行下一臺(tái)份的集配指示。
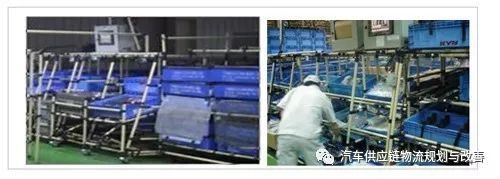
通過集配指示系統(tǒng),不僅最終削減了零件辨識(shí)作業(yè),更將原有體系中信息流的終點(diǎn)由裝配人員向集配人員轉(zhuǎn)移。將信息流的傳遞方式由紙版的作業(yè)指示單,提升為集成化的數(shù)據(jù)系統(tǒng),保持了物流和信息流的匹配,提升了整個(gè)生產(chǎn)流的體系水平。
避免小車對作業(yè)的干涉部分需要在料車的設(shè)計(jì)中體現(xiàn),設(shè)計(jì)時(shí)充分考慮了人機(jī)工效學(xué)以進(jìn)一步消減取料損失。小車的尺寸充分考慮了作業(yè)工位和周邊設(shè)備的要求,高度考慮了作業(yè)者的作業(yè)便利區(qū)域,并在零件位置的設(shè)計(jì)中考慮了諸如零件的相關(guān)就近原則、空間利用原則等一系列人機(jī)工程原則。
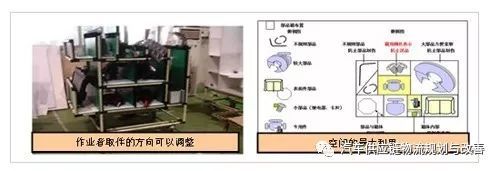
6.線平衡軟件
KIT系統(tǒng)導(dǎo)入后線上作業(yè)人員的取料動(dòng)作已經(jīng)集中至集配區(qū),這就需要增加集配的人員。為保證整個(gè)項(xiàng)目的收益性,需要對整個(gè)生產(chǎn)線的作業(yè)平衡進(jìn)行調(diào)整。
傳統(tǒng)的作業(yè)線平衡采用手動(dòng)調(diào)整的方法,調(diào)整的依據(jù)有:
生產(chǎn)節(jié)拍和總體作業(yè)工時(shí);
零件裝配順序和各零件裝配工時(shí);
調(diào)整的方法是手動(dòng)繪制作業(yè)堆積圖(又稱“山積表”),通過手動(dòng)調(diào)整達(dá)成理想的作業(yè)平衡。
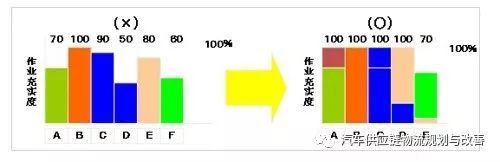
但對于汽車這種復(fù)雜工業(yè)產(chǎn)品來說,巨大的零件種類和復(fù)雜的安裝邏輯使手動(dòng)調(diào)整線平衡成為十分困難的作業(yè),而且對于柔性化生產(chǎn)體系,多種車型的零件差異和裝配差異特別是此公司采用的4車型混流生產(chǎn),一個(gè)工位可能面臨4種完全不同的車種數(shù)十種不同配置的情況,對于作業(yè)線平衡分析人員來說無疑是天文數(shù)字級(jí)的工作量。
針對這種情況,導(dǎo)入了專業(yè)線平衡軟件進(jìn)行輔助作業(yè)是非常必要的。經(jīng)過多方對比,采用的是ALINE系列軟件。該軟件具有多產(chǎn)品復(fù)合線平衡模式,且可以設(shè)定作業(yè)模塊,符合模塊化作業(yè)編成的需要。
線平衡軟件的制約因素是基本數(shù)據(jù)的準(zhǔn)確性,這就需要企業(yè)有較高的作業(yè)標(biāo)準(zhǔn)化水平和完善的基本作業(yè)工時(shí)數(shù)據(jù)庫。在軟件導(dǎo)入前,需要進(jìn)行大量的作業(yè)測量工作和作業(yè)標(biāo)準(zhǔn)固化作業(yè)。
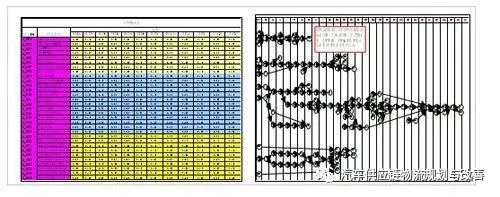
將基本作業(yè)工時(shí)數(shù)據(jù)庫和安裝邏輯輸入軟件,并設(shè)定生產(chǎn)所需的節(jié)拍和車型比例,則可以自動(dòng)生產(chǎn)作業(yè)編成,大大減輕了IE工程師的作業(yè)負(fù)荷,使得IE工程師可以將主要精力投入制造系統(tǒng)的整體設(shè)計(jì)中。
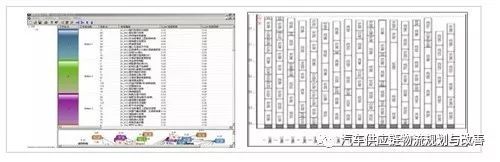
7.AGV自動(dòng)搬運(yùn)系統(tǒng)
導(dǎo)入KIT系統(tǒng)后,線上作業(yè)和集配作業(yè)都得到削減,但由于生產(chǎn)現(xiàn)場的局限性,集配區(qū)與生產(chǎn)區(qū)有一段較長的距離,又增加了物流的搬運(yùn)損失,所以又提出了削減物流損失的要求。
· · 如果采用人工或牽引車搬運(yùn),可以以第三方物流的形式實(shí)現(xiàn)物流成本的削減,但對于整個(gè)系統(tǒng)的生產(chǎn)效率是沒有幫助的。在這里考慮的是徹底的物流損失削減,用低成本自動(dòng)化搬運(yùn)系統(tǒng)進(jìn)行物流作業(yè)。
在充分理解AGV工作原理的基礎(chǔ)上,采用了散件進(jìn)口,自行組裝的模式,極大地降低了AGV的成本,保證了項(xiàng)目整體收益性。
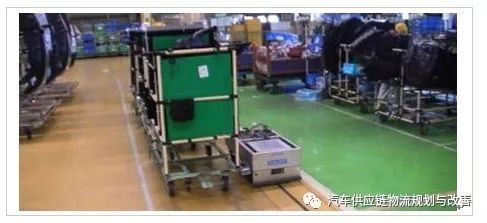
僅有運(yùn)輸工具是無法完全實(shí)現(xiàn)物流自動(dòng)化的,還需要在裝卸端進(jìn)行自動(dòng)化設(shè)計(jì)。所以在低成本AGV小車技術(shù)實(shí)現(xiàn)突破后,巧妙構(gòu)思設(shè)計(jì)了簡易自動(dòng)脫鉤系統(tǒng)。利用機(jī)械連桿和主線地板鏈的動(dòng)力,實(shí)現(xiàn)了無動(dòng)力自動(dòng)化順序裝卸。這樣AGV可以在完全自動(dòng)的情況下,依次卸下所托運(yùn)的全部KIT料車,實(shí)現(xiàn)了AGV能力的最大利用化,而且脫鉤系統(tǒng)完全是機(jī)械結(jié)構(gòu),可靠性高且維護(hù)簡單。
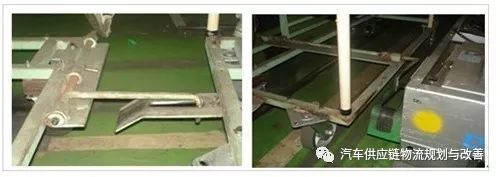
然在AGV小車的成本上實(shí)現(xiàn)了突破,但也要對AGV的運(yùn)輸效率進(jìn)行研究,所以在AGV小車導(dǎo)入前,我們使用仿真技術(shù)結(jié)合現(xiàn)場物流狀況對AGV的運(yùn)輸效率進(jìn)行分析,得到計(jì)算AGV的最經(jīng)濟(jì)投入量的運(yùn)算模型,可快速對應(yīng)不同生產(chǎn)節(jié)拍下的AGV需求核算。
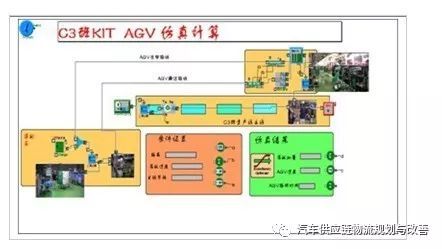
8.物流模式變更引發(fā)的布局優(yōu)化
AGV自動(dòng)搬運(yùn)系統(tǒng)的投入極大削減了物流搬運(yùn)損失,為進(jìn)一步提升集配效率,優(yōu)化了集配區(qū)布局。為保證車間內(nèi)多個(gè)AGV系統(tǒng)的運(yùn)行又進(jìn)行了物流路線的優(yōu)化。
集配區(qū)布局優(yōu)化的過程中針對零件種類多的特點(diǎn)采用了SLP的方法,根據(jù)物流強(qiáng)度重排了物料布置。
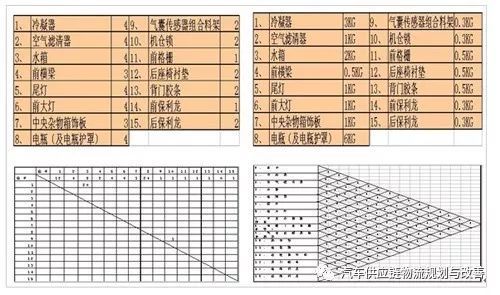
集配區(qū)布局優(yōu)化的過程中除采用SLP的方法外,還根據(jù)設(shè)施規(guī)劃思想進(jìn)行了布局設(shè)計(jì),并做出兩種方案,二字型與U字型布局模式集配區(qū)布局優(yōu)化的過程中,我們運(yùn)用了仿真技術(shù)對兩個(gè)方案進(jìn)行模擬,得到結(jié)果二字型的效率更高。
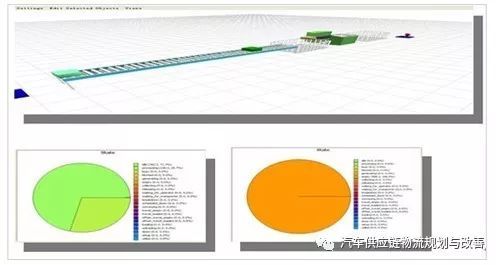
最終我們根據(jù)線邊的局限性和設(shè)備因素綜合考慮,將集配區(qū)布局成U型的二字型。
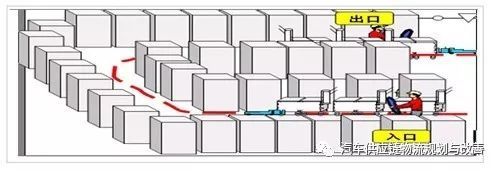
三、總結(jié)與思考
1.思路總結(jié)—改善著眼點(diǎn)的推移
在整個(gè)改善過程中,從線邊取料出發(fā),到車間整體的布局優(yōu)化,從作業(yè)指示單到信息指示系統(tǒng),改善的著眼點(diǎn)不斷向生產(chǎn)流程前端移動(dòng),構(gòu)成了兩條相對的平行線,揭示了物流類改善的切入點(diǎn)和改善方向。
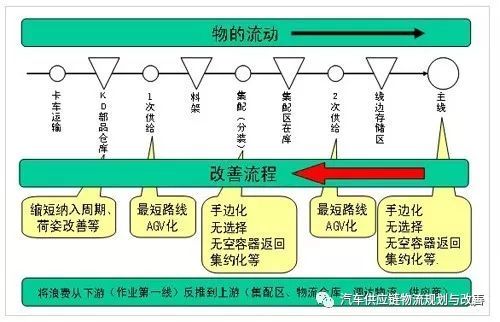
改善的方法是將損失集中化,再通過合適的低成本自動(dòng)化取代人工作業(yè)。
2.探索創(chuàng)新—IE新興技術(shù)與現(xiàn)場改善結(jié)合的切入點(diǎn)
在整個(gè)改善中,大量運(yùn)用了IE新興技術(shù):在重組線平衡的過程中使用了專業(yè)線平衡軟件;在AGV導(dǎo)入前使用仿真軟件進(jìn)行AGV的運(yùn)輸效率模擬;在集配區(qū)的優(yōu)化過程中使用SLP方法評(píng)定零件的物流等級(jí);對集配區(qū)變更后的作業(yè)情況進(jìn)行模擬以驗(yàn)證改善的效果;可以說貫穿整個(gè)過程。這證明最新的IE技術(shù)在現(xiàn)場都可以找到直接的切入點(diǎn)。
對于IE功底比較扎實(shí),即現(xiàn)場作業(yè)工時(shí)測定準(zhǔn)確完整、作業(yè)標(biāo)準(zhǔn)化程度高的成熟企業(yè),完全可以導(dǎo)入成熟的專業(yè)線平衡軟件和輔助作業(yè)分析軟件來減少IE工程師的工作負(fù)擔(dān),IE工程師可以專注于工廠制造體系的整體改善,在系統(tǒng)設(shè)計(jì)的過程中可以廣泛使用仿真技術(shù)驗(yàn)證設(shè)計(jì)效果,降低改善風(fēng)險(xiǎn)。
汽車總裝工藝內(nèi)部物流模式借助供貨模式的思維突破和低成本自動(dòng)化搬運(yùn)系統(tǒng)實(shí)用化而發(fā)生了革命性的突破,不僅突破了傳統(tǒng)的物流觀念和物流技術(shù),更是在物流系統(tǒng)設(shè)計(jì)思想的突破。這種突破是應(yīng)汽車工業(yè)的多品種柔性化生產(chǎn)模式的要求誕生的,但這種思想、這種方法必將擴(kuò)展至其他工業(yè)領(lǐng)域,對中國工業(yè)未來發(fā)展做出積極的貢獻(xiàn)!
舉報(bào) 0
收藏 0
分享 142
-
推動(dòng)汽車行業(yè)轉(zhuǎn)型的引領(lǐng)者——面向未來的總裝NE
2024-12-03 -
總裝工藝成本優(yōu)化實(shí)踐案例
2024-08-05 -
如何提高螺栓連接的強(qiáng)度?
2024-07-30 -
案例分析:螺栓“跑丟了”!
2024-07-29
編輯推薦
最新資訊
-
跨越速運(yùn)憑什么“圈粉”萬千客戶?“
2025-07-01 14:42
-
數(shù)智破局啟新篇?生態(tài)共生再啟程 —
2025-06-27 20:13
-
助力汽車零部件產(chǎn)線智能化升級(jí),西門
2025-06-27 13:59
-
BBA集體轉(zhuǎn)向!放棄全面電動(dòng)化
2025-06-26 17:32
-
比換柜省錢,比自研省心,西門子Xcel
2025-06-25 15:07