鋁合金汽車發(fā)動機罩外板沖壓成形規(guī)律研究
2018-12-02 17:18:57· 來源:鍛造與沖壓 作者:余萬銓,胡志力
伴隨著日益嚴峻的環(huán)境資源壓力以及嚴苛的節(jié)能減排法律法規(guī),輕量化已成為汽車產業(yè)發(fā)展不容忽視的主題。輕質材料的使用是實現汽車輕量化的重要途經,而鋁合金材料以其比強度高、良好的耐腐蝕性及焊接性等優(yōu)點,在汽車生產中的應用越來越廣
伴隨著日益嚴峻的環(huán)境資源壓力以及嚴苛的節(jié)能減排法律法規(guī),輕量化已成為汽車產業(yè)發(fā)展不容忽視的主題。輕質材料的使用是實現汽車輕量化的重要途經,而鋁合金材料以其比強度高、良好的耐腐蝕性及焊接性等優(yōu)點,在汽車生產中的應用越來越廣泛。但鋁合金彈性模量小、室溫條件下成形性較差,因此在沖壓成形過程中極易出現起皺、開裂、回彈等缺陷,特別是對于結構復雜、相對厚度小、表面質量要求高的大型外覆蓋件(如頂蓋外板、發(fā)動機罩外板等),鋁合金材料在成形性上的劣勢就更為突出。如何克服鋁合金板材在成形性能上的不足,促進鋁合金材料在汽車輕量化中的應用,已成為業(yè)內關注的熱點問題。
通常來說,影響汽車零部件成形性能的主要因素包括零件結構、材料性能、成形工藝以及模具設計等。在車身外覆蓋件沖壓成形過程中,對沖壓工藝參數及模具結構的優(yōu)化是提高制件成形質量的主要方式。國內外已經有眾多學者對鋁合金板材在沖壓成形過程中出現的開裂、回彈、起皺等缺陷及其影響因素進行了研究,分析了材料性能、模具結構及工藝參數等對沖壓成形性能的影響,極大推動了鋁合金材料在汽車輕量化中的應用。
本文通過AutoForm軟件平臺對鋁合金汽車發(fā)動機罩外板的沖壓成形過程仿真分析,研究了模具型面結構優(yōu)化及相關沖壓工藝參數對鋁合金板材成形性的影響,同時采用型面補償的方法有效減小了發(fā)動機罩外板的回彈。最終通過沖壓試驗實現了沖壓件的試制,試驗結果與仿真優(yōu)化結果保持了一致性。
模具型面設計與優(yōu)化
利用三維建模軟件CATIA對鋁合金汽車機罩外板進行型面優(yōu)化,其后基于AutoForm軟件平臺對板料的成形過程進行數值模擬,討論型面結構優(yōu)化對板材成形性的影響,主要集中在可成形性與回彈兩方面進行研究。
初始型面設計
根據外板的尺寸大小,取坯料尺寸為1850mm×1245mm×1mm,型面結構如圖1所示。
利用AutoForm軟件平臺進行成形分析。材料選用6016-T4鋁合金,本構模型采用Ludwik公式:σ=Kεn,其中σ為真應力,ε為對數塑性應變,n和K為材料常數。模擬單元為彈塑性殼單元,設置壓邊力為850kN,摩擦系數設為0.15,模具間隙設為t(即板料厚度),沖壓速度為1mm/s。分析結果如圖2 所示,從中可見產品開裂嚴重,在翼子板與玻璃交接處的圓角、機罩前端都出現了破裂,故該結果不滿足成形要求,需對型面進行進一步改進。
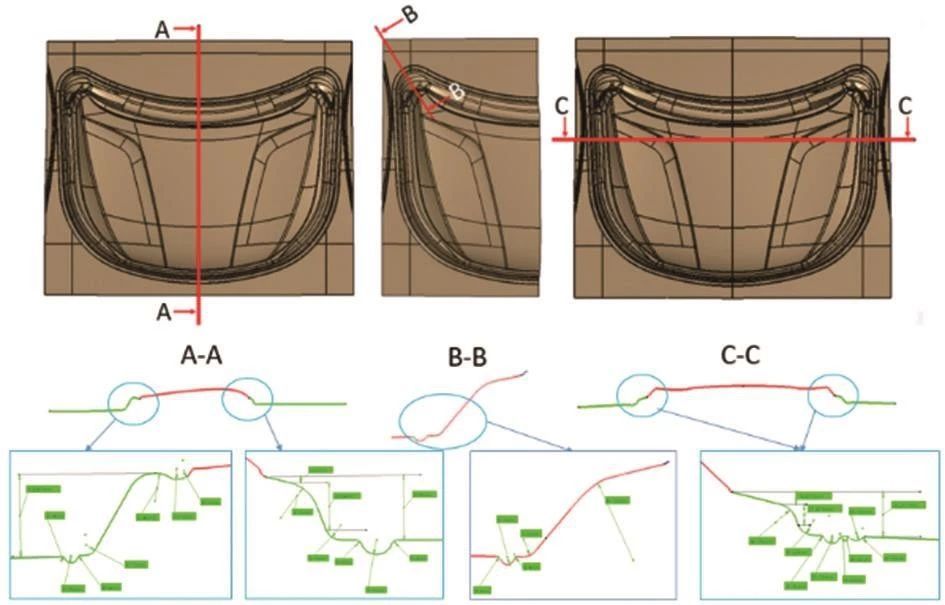
圖1 初始型面結構
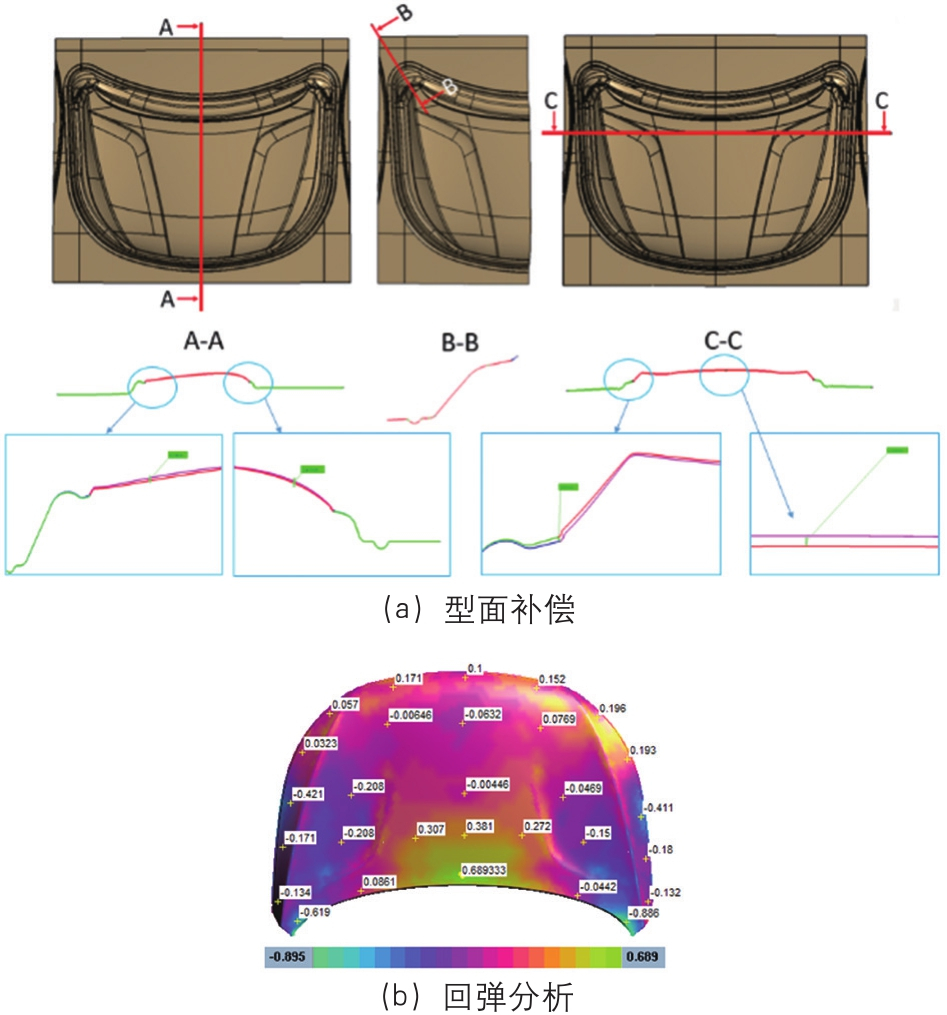
圖2 初始型面成形性分析
第一次型面優(yōu)化
坯料尺寸不變,在初始型面的基礎上,在型面兩側增加拉延筋,并將拉延筋半徑從8mm增加至10mm,其他較初始型面無改變,型面結構如圖3所示。
圖4為成形仿真分析結果,雖然開裂問題有所改善,但是擋風玻璃與翼子板交界側的圓角處仍出現明顯破裂問題,需對型面進行進一步改進。
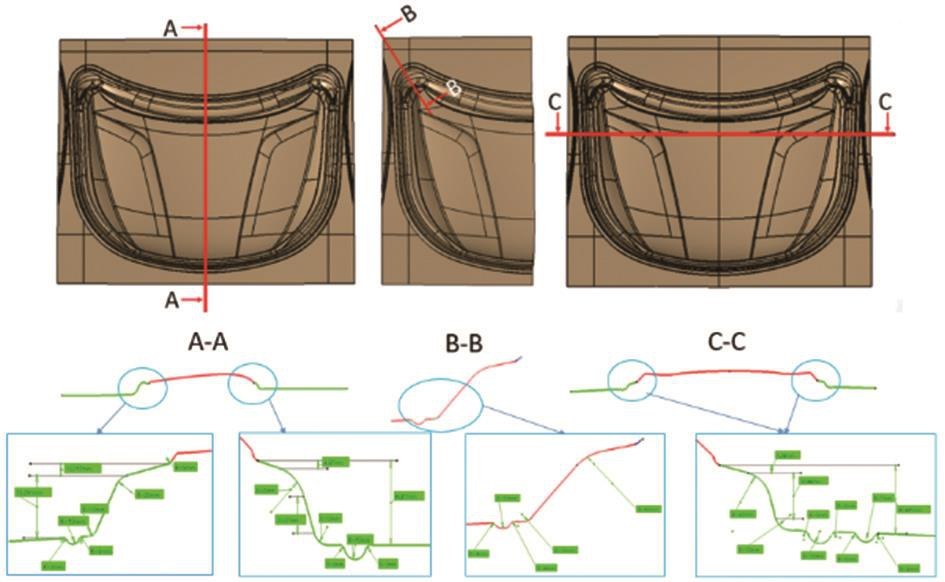
圖3 第一次型面優(yōu)化結構
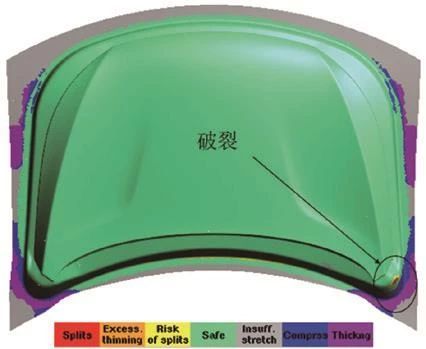
圖4 第一次型面優(yōu)化成形性分析
第二次型面優(yōu)化
設定坯料尺寸為1929mm×1320mm×1mm,型面結構在第一次優(yōu)化的基礎上在玻璃側增加余肉造型,增大圓角改善材料流動,并將分模線向外偏移15mm,對圓弧進行適當的優(yōu)化,其型面結構如圖5所示。
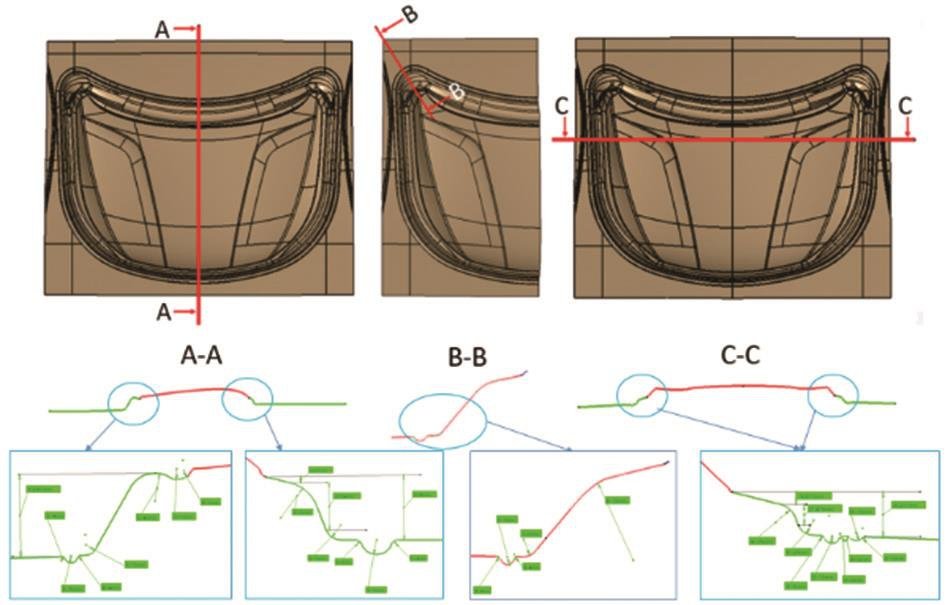
圖5 第二次型面優(yōu)化結構
第二次型面優(yōu)化結構成形仿真結果如圖6所示,圖中可見增加的余肉有效地解決了零件破裂問題,優(yōu)化后的圓弧尺寸及圓角半徑使得零件成形充分,減薄率、應變分布均勻,保證了零件的剛度。成形后板料的減薄率最大為0.04%,最小為-21.50%;回彈最大值為5.98mm,最小值為-4.97mm,出現在零件中部靠近擋風玻璃的局部負向回彈區(qū)域,回彈量仍然較大。
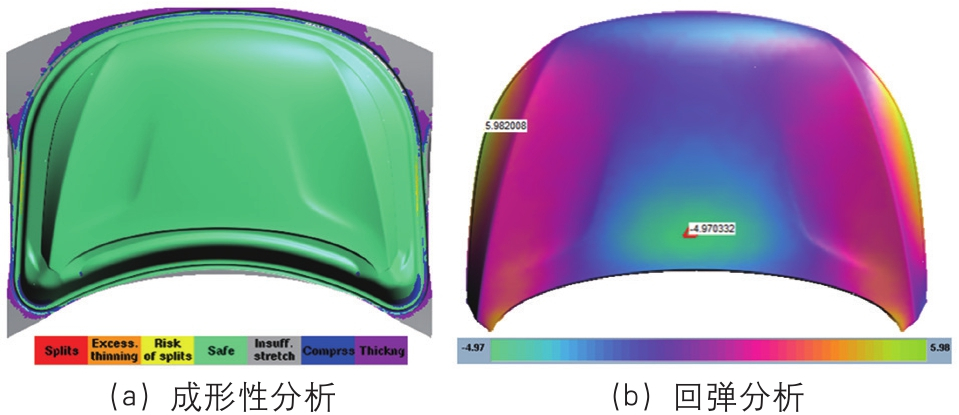
圖6 第二次型面優(yōu)化分析
工藝參數的影響
工藝參數對零件成形質量有顯著影響,通??紤]的工藝因素有壓邊力、模具間隙、沖壓速度等。在室溫條件下,材料性能隨應變速率的變化不明顯,因此沖壓速度對成形性的影響幾乎可以忽略。本文重點關注壓邊力和模具間隙對成形質量的影響。
壓邊力的影響
壓邊力在板材的沖壓成形中起到非常重要的作用,通常過小的壓邊力難以控制材料的流動從而使起皺趨勢增大,而過大的壓邊力則會使材料流動變得困難,破裂趨勢增大。同時壓邊力會影響板料塑性變形中的應力狀態(tài),對其成形質量產生影響。采用不同壓邊力對零件沖壓過程進行分析,結果表明隨著壓邊力的增大,外板起皺趨勢減小,零件的整體回彈有所減小,但變化不明顯,局部區(qū)域的負向回彈則出現增大。零件的減薄率與最大回彈量隨壓邊力的變化規(guī)律如圖7所示。由分析結果可見,外板的起皺趨勢隨著壓邊力的增大而減小,減薄率隨著壓邊力的增大而增大,最大回彈都隨著壓邊力的增大而增大。
模具間隙的影響
模具間隙是沖壓成形中的重要參數,直接影響模具與板料之間的接觸情況,進而影響板料在變形過程中的應力-應變狀態(tài),對零件的成形質量影響顯著。模具間隙分別設為t,1.05t和1.1t(t為板料厚度),并對零件減薄率和回彈進行了分析(圖8)。由分析結果可見,外板的起皺趨勢隨著模具間隙的增大而增大,減薄率隨著模具間隙的增大而減小,最大正回彈隨著模具間隙的增大而增大。
回彈控制
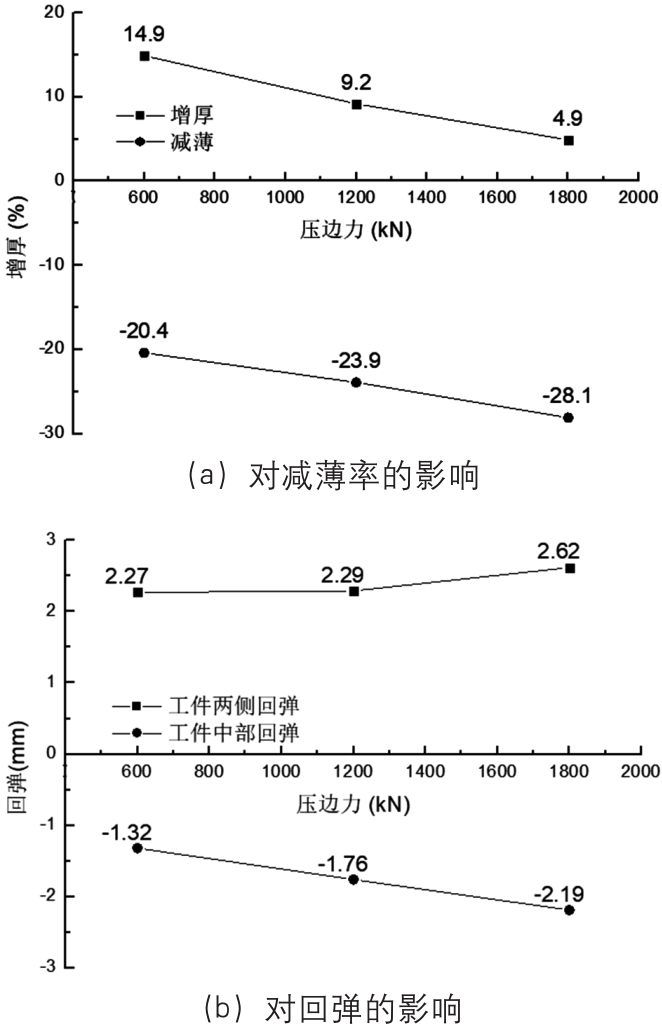
圖7 壓邊力對板料減薄率和回彈的影響
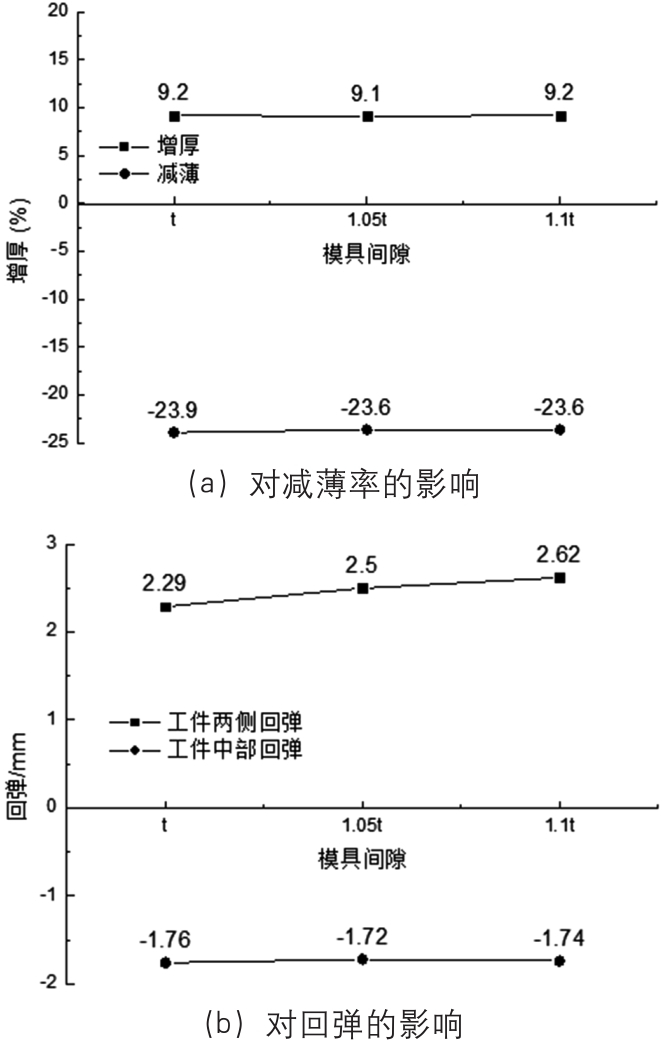
圖8 模具間隙對板料減薄率和回彈的影響
如前所述,通過初步的型面優(yōu)化,零件的可成形性問題得到了解決,但零件的回彈量仍然較大,精度無法保證。在沖壓生產過程中,工藝參數的調整對回彈的改善效果有限,型面補償是解決回彈問題的主要方法,因此在第二次型面優(yōu)化的基礎上,以回彈量為依據,進一步對型面進行補償優(yōu)化。同時根據工藝參數對回彈和成形性的影響對其進行調整,達到減小回彈的目的。圖9中經型面補償后零件的回彈可以控制在±1mm以內。
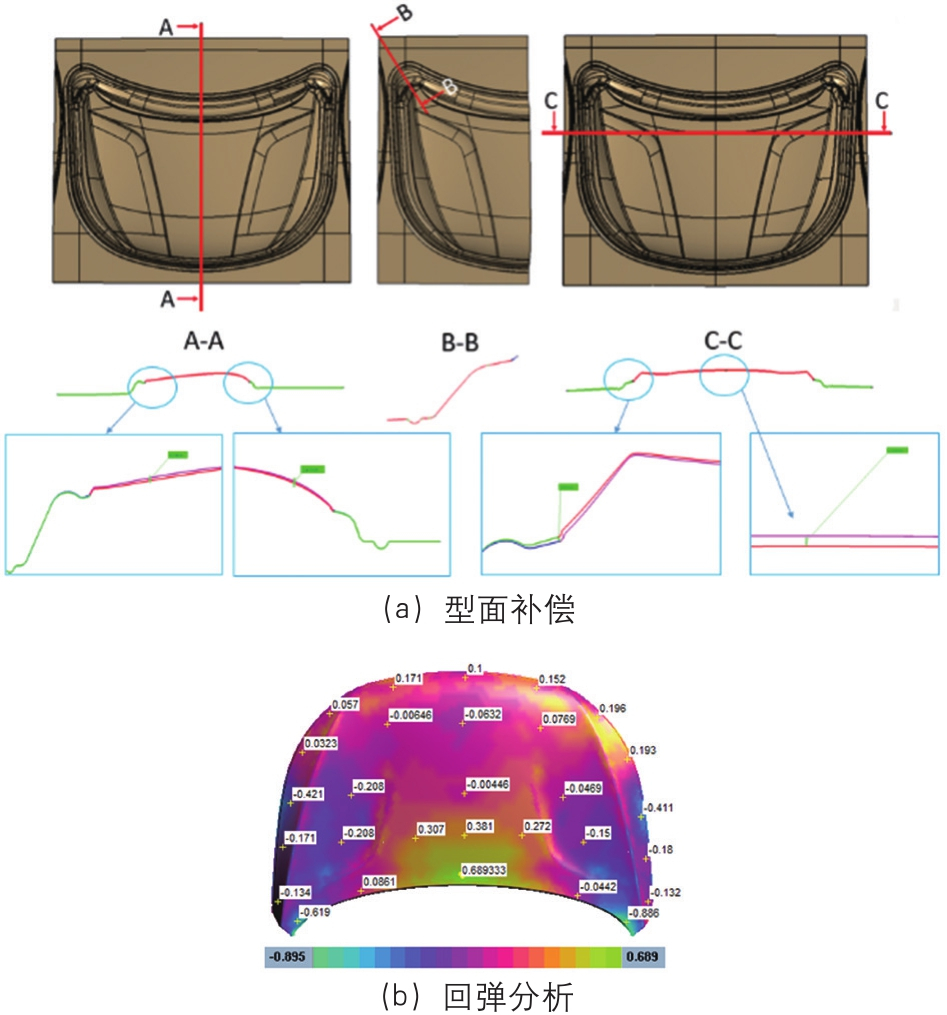
圖9 型面補償及回彈分析
試驗驗證
基于以上分析和優(yōu)化,進行模具試制和調試,并對鋁合金汽車機罩外板進行沖壓試驗。試驗設備采用800t液壓機(圖10),所得制件如圖11b所示。由仿真結果可見,零件大部分區(qū)域的減薄率分布在2%~5%范圍內,板料的減薄均勻,保證了零件的剛度,同時最大減薄率為20.59%,避免了過度減?。▓D11a),制件易發(fā)生破裂的區(qū)域(擋風玻璃與翼子板交界側的圓角處)未出現破裂。另外通過對零件進行精度測試,測得零件的總體回彈量能夠控制在±1mm以內(圖11b),與仿真結果較為接近,說明實際沖壓結果與仿真優(yōu)化結果取得了較好的一致性。
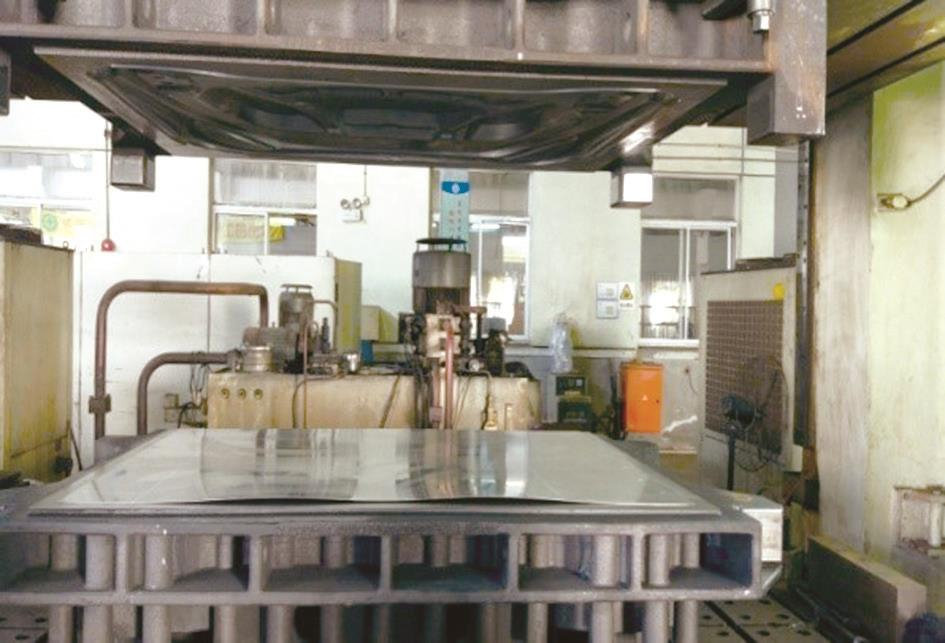
圖10 沖壓試驗設備
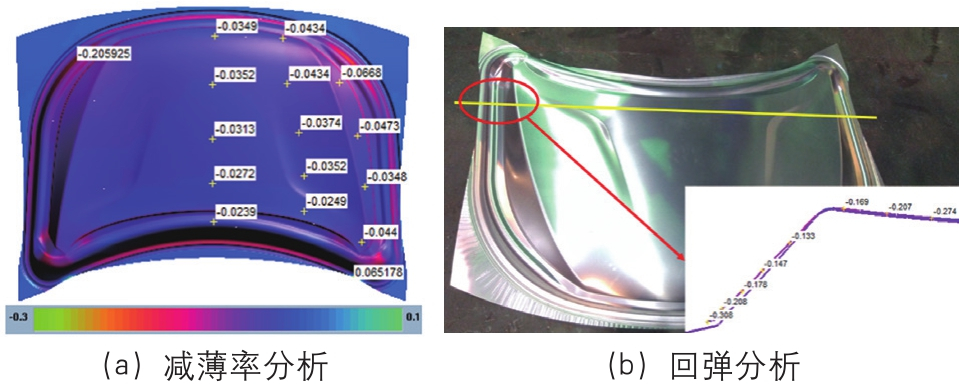
圖11 零件減薄率與回彈分析
結束語
通過對鋁合金汽車發(fā)動機罩外板沖壓成形過程仿真分析,優(yōu)化了模具型面結構,改善了板料流動,進而減少了由局部結構引起的成形缺陷,提高了外板的成形質量。此外還研究了工藝參數對板料減薄及回彈的影響。在600~1800kN范圍內,選用600kN壓邊力和適當的模具間隙有利于緩解板料減薄,提高了零件的精度和強度。我們最終采用了面補償配合工藝參數調整,使得零件的最大正回彈減小至0.69mm,最大負回彈減小至0.89mm。對鋁合金板料成形質量的影響規(guī)律研究與模具型面優(yōu)化,可以作為實際生產的理論基礎和重要參考。模具的制造和調試及對發(fā)動機罩外板的沖壓成形進行試驗驗證,試驗結果與仿真優(yōu)化結果保持了一致性。
舉報 0
收藏 0
分享 116
-
專家訪談:埃馬克 OCTG 加工的技術密鑰與生產之
2025-06-25 -
Know-How系列 | 石油鉆機核心技術揭秘:埃馬克
2025-06-19 -
聚焦機床 | 埃馬克USC 850數控萬能車床:突破大
2025-06-11 -
DMC中國國際模具裝備展今日開幕,600+展商齊聚
2025-06-05
編輯推薦
最新資訊
-
跨越速運憑什么“圈粉”萬千客戶?“
2025-07-01 14:42
-
數智破局啟新篇?生態(tài)共生再啟程 —
2025-06-27 20:13
-
助力汽車零部件產線智能化升級,西門
2025-06-27 13:59
-
BBA集體轉向!放棄全面電動化
2025-06-26 17:32
-
比換柜省錢,比自研省心,西門子Xcel
2025-06-25 15:07