壓鑄件的檢測,該來臺工業(yè)CT了!
2018-08-27 10:51:52· 來源:《蔡司工業(yè)測量》
結(jié)合壓鑄缺陷檢驗現(xiàn)狀及大趨勢探討在線與離線檢測相結(jié)合的鋁壓鑄件質(zhì)量控制技術(shù),基于工業(yè)CT 測量機(jī)離線對鋁壓鑄制品進(jìn)行高精度掃描測量分析,并與線邊或在線高速CT 檢測手段相結(jié)合,以有效阻斷質(zhì)保及生產(chǎn)全過程質(zhì)量異常并快速追溯缺陷信息,從而顯著改善壓鑄質(zhì)量,該方法可使異常壓鑄件于最短時間內(nèi)得到識別、剔除及隔離,從而達(dá)到精細(xì)質(zhì)量控制及提升企業(yè)市場競爭力之目的。
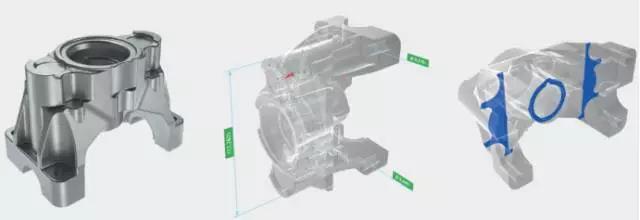
結(jié)合壓鑄缺陷檢驗現(xiàn)狀及大趨勢探討在線與離線檢測相結(jié)合的鋁壓鑄件質(zhì)量控制技術(shù),基于工業(yè)CT 測量機(jī)離線對鋁壓鑄制品進(jìn)行高精度掃描測量分析,并與線邊或在線高速CT 檢測手段相結(jié)合,以有效阻斷質(zhì)保及生產(chǎn)全過程質(zhì)量異常并快速追溯缺陷信息,從而顯著改善壓鑄質(zhì)量,該方法可使異常壓鑄件于最短時間內(nèi)得到識別、剔除及隔離,從而達(dá)到精細(xì)質(zhì)量控制及提升企業(yè)市場競爭力之目的。
1壓鑄件的缺陷檢驗現(xiàn)狀
壓鑄作為一種現(xiàn)代化的金屬鑄造工藝,其利用模具型腔對熔融狀態(tài)的金屬施加高壓成型,與其它鑄造技術(shù)相較,壓鑄的表面更為平整,并擁有更高的尺寸一致性,然而不規(guī)范的操作及參數(shù)不可避免產(chǎn)生種類眾多的鑄件缺陷,包括形狀及尺寸超差、氣孔、縮孔、夾雜、疏松及裂紋等,其原因涉及壓鑄機(jī)性能、壓鑄工藝參數(shù)設(shè)置、壓鑄模、壓鑄件設(shè)計及操作、材料等多樣化因素。
目前國內(nèi)鑄造生產(chǎn)車間多采用破壞性檢驗及人工目視檢測法,勞動強(qiáng)度大且作業(yè)效率低,檢測結(jié)果易受到操作人員的主觀影響。
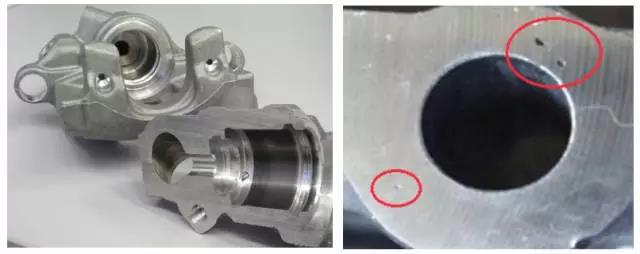
圖1: 傳統(tǒng)破壞性檢驗及目視檢測法
部分壓鑄廠家采用常規(guī)X射線照相技術(shù)對鋁壓鑄件進(jìn)行探傷,其具有檢測快速及操作簡單等特點,但通常僅提供二維平面投影信息,在射線透照方向上缺陷前后影像重疊,存在更高的缺陷誤判可能性,對于缺陷的深度、厚度及三維信息無法直接或準(zhǔn)確給出,然測定缺陷的尺寸及位置的重要性與確定產(chǎn)品安全性能卻有著千絲萬縷的直接聯(lián)系,缺陷的精確定量分析及三維尺寸測定于汽車等產(chǎn)業(yè)制造鏈中日益得到關(guān)注及應(yīng)用。
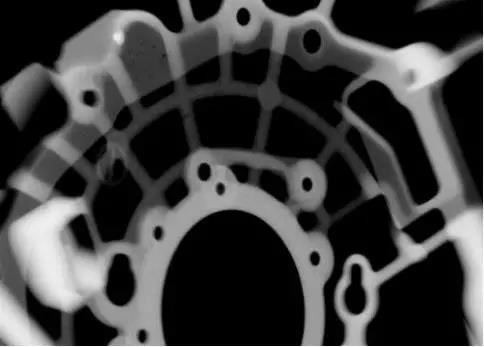
圖2: 工業(yè)X 光機(jī)檢測二維平面圖像
2大趨勢:高精度三維CT 掃描檢測
工業(yè)CT 是工業(yè)用計算機(jī)斷層掃描成像技術(shù)簡稱,以錐束CT 為例,其基本原理是錐束射線束穿過被測對象及衰減,通過平板探測器獲取大量無影像重疊的斷層掃描圖像,最終按照重建算法重構(gòu)得到完整的三維圖像。作為現(xiàn)今最佳的無損檢測手段之一,可獲取更全面的產(chǎn)品內(nèi)外質(zhì)量數(shù)據(jù),更有效反映內(nèi)部結(jié)構(gòu),缺陷形狀、尺寸及分布位置情況的直觀圖像,越趨廣泛地應(yīng)用于鋁壓鑄缺陷檢驗領(lǐng)域。
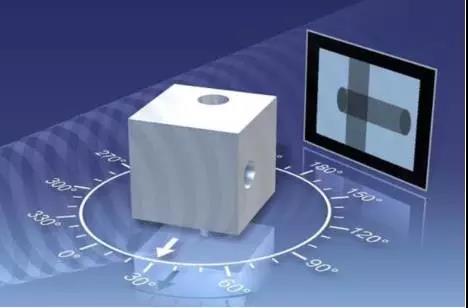
圖3: 錐束計算機(jī)斷層掃描成像
作為主要應(yīng)用之一,工業(yè)CT 可實現(xiàn)三維及二維缺陷的自動量測、分析及顯示,可將檢測到的缺陷大小以顏色編碼可視化顯示,獲取每個缺陷的各種參數(shù)(缺陷位置、尺寸及幾何形狀(體積、坐標(biāo)、投影面積)、最近缺陷間隔、每個缺陷到參考表面的距離,統(tǒng)計總體百分比或孔隙率及缺陷體積直方圖,可依據(jù)P201及VW 50097等標(biāo)準(zhǔn)對切片圖像進(jìn)行局部孔隙率分析,該方法淘汰了耗時的樣品制備及顯微拍照作業(yè)。分析過程可保存為模版,以實現(xiàn)快速及重復(fù)地分析所有樣品,減少人為干預(yù)。
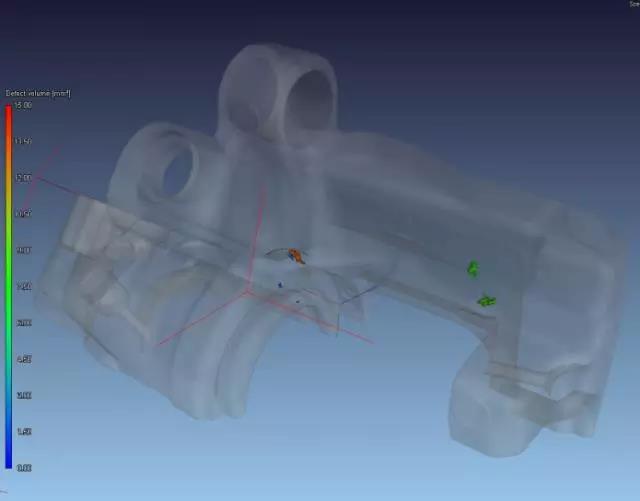
圖4:鋁鑄件整體缺陷定量可視化分析
伴隨工業(yè)CT 越趨多樣化的發(fā)展維度,兼具測量性能及可追溯性測量精度的工業(yè)CT 測量機(jī)于綜合性能方面具有更強(qiáng)的拓展性,特別體現(xiàn)于鋁鑄造毛坯件的尺寸及形位公差量測、厚度分析、數(shù)模比對/實際值比對及逆向工程等需精確量測應(yīng)用的領(lǐng)域。
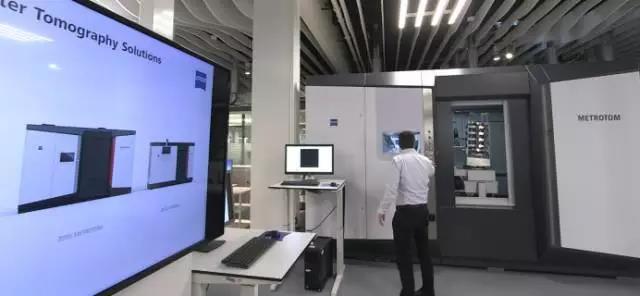
圖5:采用ZEISS METROTOM 工業(yè)CT 測量機(jī)
對大型鋁壓鑄件進(jìn)行CT掃描
以數(shù)模比對/實際值比對為例,可直接比對CT 三維體元數(shù)據(jù)和CAD 或其它CT 三維體元數(shù)據(jù),較之常規(guī)方法效率更高,并可以顏色標(biāo)識來顯示分析結(jié)果,可對整體對象或用戶指定的“感興趣區(qū)域”進(jìn)行分析,數(shù)模對比可直接在CT 三維體元數(shù)據(jù)上進(jìn)行,而無需將三維數(shù)據(jù)間接轉(zhuǎn)換成點云或STL 數(shù)據(jù),從而避免了增加間接測量的不確定性及有效信息的丟失。
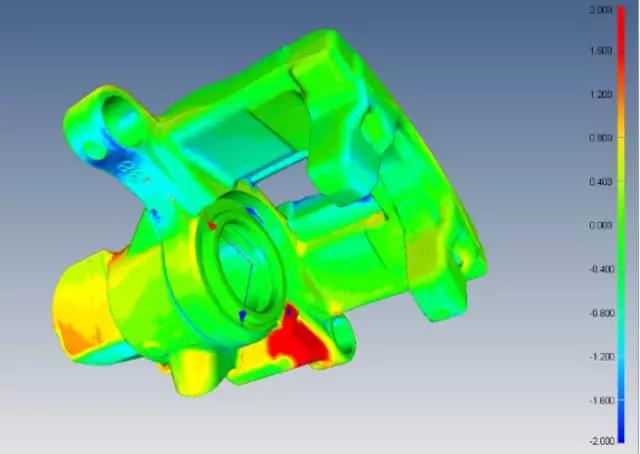
圖6:鋁鑄件整體色差數(shù)模比對
3大趨勢:離線、線邊或在線檢測相融合
近年來,隨著產(chǎn)品技術(shù)的快速發(fā)展及日益激烈的市場競爭,為了確保產(chǎn)品的質(zhì)量及經(jīng)濟(jì)效益,先進(jìn)及優(yōu)化控制廣泛應(yīng)用于壓鑄過程。然而,不管是在先進(jìn)控制策略的應(yīng)用過程中還是對產(chǎn)品質(zhì)量的直接控制過程中,一個最棘手的問題就是難以對壓鑄產(chǎn)品的質(zhì)量變量進(jìn)行在線實時測量。過往受工藝及技術(shù)的限制,部分重要的過程參數(shù)和產(chǎn)品內(nèi)部質(zhì)量指標(biāo)難以甚至無法通過硬件傳感器在線檢測,近期隨著先進(jìn)的高速CT 系統(tǒng)方案在國外知名企業(yè)陸續(xù)推行,此難題將得以有效解決。
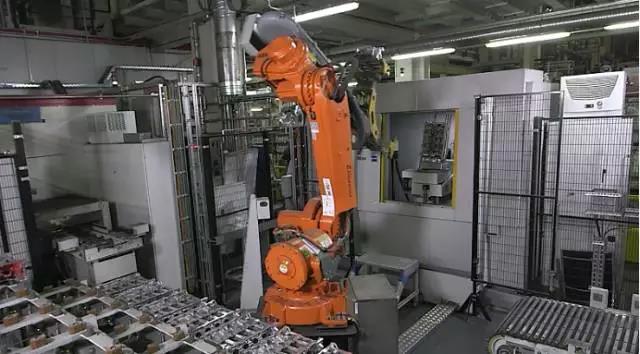
圖7: ZEISS VoluMax 在線高速CT
應(yīng)用于寶馬集團(tuán)德國鋁壓鑄工廠
通常,生產(chǎn)過程中需對每一部機(jī)臺進(jìn)行巡檢,對其正在生產(chǎn)的產(chǎn)品進(jìn)行離線分析抽檢,送計量實驗室進(jìn)行人工分析,以確認(rèn)產(chǎn)品即時的符合性,并根據(jù)分析值來指導(dǎo)生產(chǎn)。由于時間滯后大,因此遠(yuǎn)不能滿足在線過程控制的要求,于生產(chǎn)現(xiàn)場增加線邊或在線高速CT 存在一定的必然性。其正是為了解決質(zhì)量變量的實時測量及控制問題而逐漸發(fā)展起來的。在線檢測為過程控制、質(zhì)量控制、過程管理與決策等提供支持,亦為進(jìn)一步實現(xiàn)質(zhì)量控制及過程優(yōu)化奠定基礎(chǔ)。
在線連續(xù)檢測技術(shù)已是現(xiàn)代流程工業(yè)和過程控制領(lǐng)域關(guān)鍵技術(shù)之一,它的成功應(yīng)用將極大地推動在線質(zhì)量控制和各種先進(jìn)控制策略的實施,使生產(chǎn)過程控制得更加理想,例如孔隙率、形狀、尺寸、縮孔等質(zhì)量參數(shù)皆可以實現(xiàn)在線檢測,借助于核心圖像算法,快速識別缺陷及自動剔除偽缺陷的干擾。
壓鑄生產(chǎn)過程作為復(fù)雜及龐大的工業(yè)大系統(tǒng),其本身就存在大量的不確定性和非線性因素,通常伴隨著十分苛刻的生產(chǎn)條件或環(huán)境,如高溫、振動及高濕度,對于在線CT 系統(tǒng)的安全性要求較高;各生產(chǎn)裝置間存在復(fù)雜的耦合及制約關(guān)系,這即要求從全局協(xié)調(diào),以求整個生產(chǎn)裝置運(yùn)行平穩(wěn)、高效,作為在線CT系統(tǒng)工程的重要組成部分,質(zhì)量管理平臺同樣扮演著重要的角色,需有效對接各關(guān)鍵生產(chǎn)及管理單元,實時快速處理海量的質(zhì)量數(shù)據(jù)。
在線/線邊CT 系統(tǒng)解決方案具有自動化效能高、無人值守、批量化高速檢測、自動上下料、高效的自動缺陷識別、測量及評定等系列全過程采用計算機(jī)自動化控制,最大化避免人工干預(yù)等顯著特點。
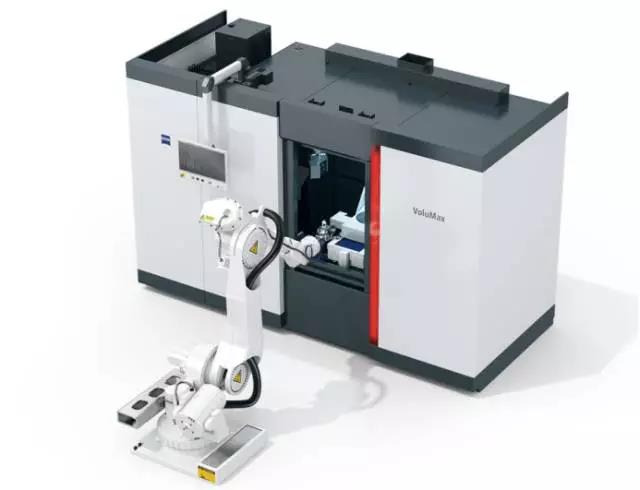
圖8: 全自動化高速CT 掃描檢測系統(tǒng)
離線、在線或線邊檢測系統(tǒng)的有機(jī)融合有利于確保涵蓋研發(fā)、生產(chǎn)及質(zhì)保等環(huán)節(jié)整體質(zhì)量數(shù)據(jù)流的透明化及實時性,其各有特點:高精度、高速,均采用CT 系統(tǒng)亦有利于確保數(shù)據(jù)的三維一致及可匹配性,以實現(xiàn)產(chǎn)品信息的可追溯性、完善的閉環(huán)反饋,加速產(chǎn)品開發(fā)周期、縮減生產(chǎn)成本及提升產(chǎn)品整體質(zhì)量。
編輯推薦
最新資訊
-
跨越速運(yùn)憑什么“圈粉”萬千客戶?“
2025-07-01 14:42
-
數(shù)智破局啟新篇?生態(tài)共生再啟程 —
2025-06-27 20:13
-
助力汽車零部件產(chǎn)線智能化升級,西門
2025-06-27 13:59
-
BBA集體轉(zhuǎn)向!放棄全面電動化
2025-06-26 17:32
-
比換柜省錢,比自研省心,西門子Xcel
2025-06-25 15:07