專家解讀江淮汽車涂裝生產(chǎn)線
2018-08-10 10:04:00· 來源:AI汽車制造業(yè)
江淮汽車在涂裝工藝方面一直緊跟時代發(fā)展的步伐,圍繞“綠色環(huán)保、節(jié)能低碳”的精益制造理念開展工作。今天,小編帶大家真正了解一下江淮汽車的涂裝生產(chǎn)線,更有江淮汽車技術(shù)中心工藝研究院涂裝工藝部技術(shù)總監(jiān)邢汶平女士的詳盡分享。
江淮汽車在涂裝工藝方面一直緊跟時代發(fā)展的步伐,圍繞“綠色環(huán)保、節(jié)能低碳”的精益制造理念開展工作。今天,小編帶大家真正了解一下江淮汽車的涂裝生產(chǎn)線,更有江淮汽車技術(shù)中心工藝研究院涂裝工藝部技術(shù)總監(jiān)邢汶平女士的詳盡分享。
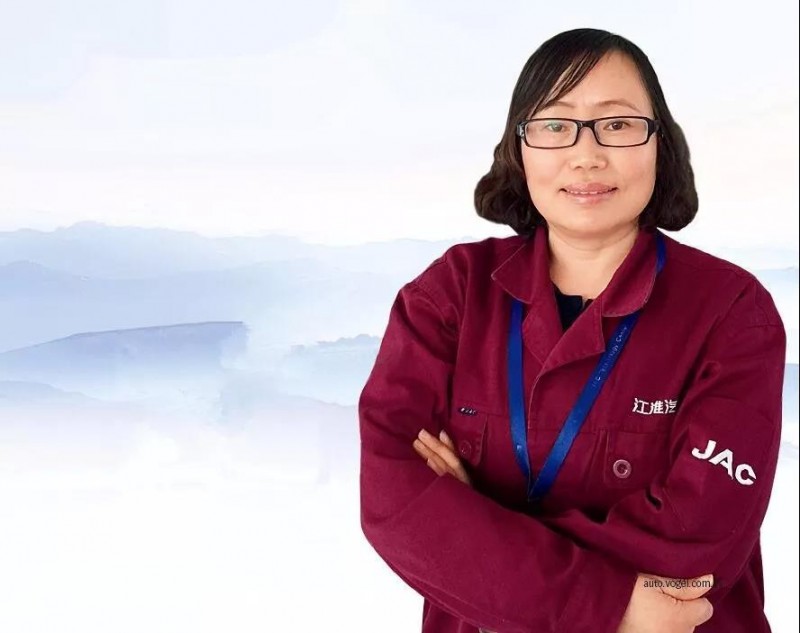
——江淮汽車技術(shù)中心工藝研究院涂裝工藝部技術(shù)總監(jiān)邢汶平女士
邢汶平女士擔(dān)任安徽江淮汽車集團股份有限公司技術(shù)中心工藝研究院涂裝工藝部技術(shù)總監(jiān)一職,主要負責(zé)江淮汽車涂裝生產(chǎn)線新建和改造項目的規(guī)劃設(shè)計、建設(shè)和工藝調(diào)試工作及新產(chǎn)品的涂裝工藝SE分析、生產(chǎn)線適應(yīng)性改造、工藝調(diào)試和量產(chǎn)拉動等工作。
新技術(shù)、新設(shè)備
邢汶平女士:江淮汽車在涂裝工藝方面按照安進董事長提出的“六化”要求,圍繞技術(shù)領(lǐng)先化、制造精益化的理念,通過采用新工藝、新技術(shù)和新設(shè)備,打造“綠色環(huán)保、節(jié)能低碳”的世界先進涂裝生產(chǎn)線。
在新工藝應(yīng)用方面,江淮汽車具有敢為天下先的勇氣,近幾年不斷引入新工藝、新技術(shù)。2012年,其率先在乘用車上采用當(dāng)時國際先進的水性免中涂涂裝工藝,在保證產(chǎn)品質(zhì)量的同時,實現(xiàn)了能源消耗、VOC排放及生產(chǎn)成本的大幅下降,成為我國首條應(yīng)用該技術(shù)的典范。2014年,江淮汽車采用的粉末涂料具有品質(zhì)更加優(yōu)良、廢水/廢氣/廢渣等零排放、涂料回收利用率高達95%以及生產(chǎn)成本更低等明顯優(yōu)勢,被成功應(yīng)用于商用車車廂涂裝線,這也是國內(nèi)首條車廂粉末生產(chǎn)線。
2015年,江淮汽車從歐洲引進了先進的水性單涂層工藝技術(shù)(工藝更加緊湊、VOC排放更低),用于江淮汽車遂寧工廠的素色漆生產(chǎn),為國內(nèi)商用車涂裝線水性化改造建立了一個新的樣板工廠。通過采用水性免中涂工藝取代原有3C2B溶劑型,采用水性單涂層工藝以及粉末涂料取代溶劑型單涂層技術(shù)等舉措,江淮汽車實現(xiàn)了涂裝技術(shù)在品質(zhì)、綠色、精益等方面的不斷升級。
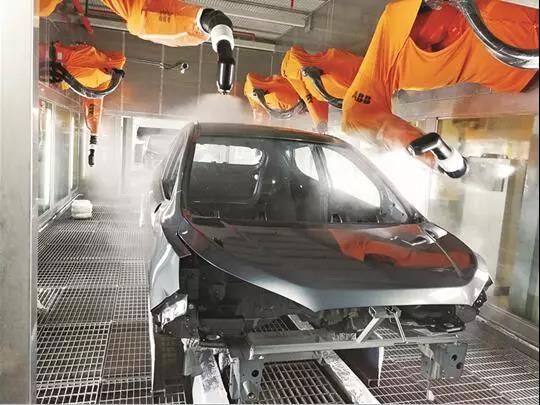
在涂裝設(shè)備選型方面,江淮汽車以智能、低碳為原則,選用最先進、最節(jié)能且最環(huán)保的工藝裝備。以江淮汽車新港生產(chǎn)基地為例,該項目車身內(nèi)外表面均采用機器人噴涂,機器人數(shù)量達48臺,實現(xiàn)了噴涂區(qū)域無人化,在保證產(chǎn)品一致性的同時,有效減少了人工并提高了涂料利用率。噴漆室采用最新的“空調(diào)循環(huán)風(fēng)+熱泵機組”節(jié)能技術(shù),實現(xiàn)了單臺涂裝能耗下降15%。烘干系統(tǒng)采用TAR集中供熱系統(tǒng),在滿足烘干加熱需求的同時,實現(xiàn)了烘干廢氣焚燒達標(biāo),同時為最大程度地降低烘干能耗,設(shè)置了煙氣余熱回收裝置,可實現(xiàn)年回收熱量折合天然氣26.2萬立方米,減少碳年排放1?458.03?t。下地板涂膠采用“機器人+3D膠槍涂膠系統(tǒng)”,實現(xiàn)了地板涂膠和PVC全自動噴涂,確保地板優(yōu)良防護性能,該項目建成后將是國內(nèi)最先進的商用車生產(chǎn)線。
在環(huán)保措施方面,江淮汽車涂裝線在全面采用水性涂料的同時,對于溶劑型清漆噴漆廢氣采用沸石轉(zhuǎn)輪+RTO焚燒技術(shù),將VOC排放量降至最低水平,可控制在?15?g/m2以下,滿足國內(nèi)最嚴(yán)格的排放限制要求,實現(xiàn)了真正意義上的綠色環(huán)保。
精益生產(chǎn)與技術(shù)先進性之間的平衡
邢汶平女士:精益生產(chǎn)體現(xiàn)在采用最合理的工藝方法和選用最適合的制造設(shè)備,而不一定是最先進的設(shè)備或技術(shù)。這需要通過對各類設(shè)備的技術(shù)特點及相關(guān)配套資源進行詳細調(diào)研,在設(shè)備的投入費用、日常運行費用、廢棄物處置費用以及設(shè)備維護保養(yǎng)費用等整個生命周期內(nèi)進行系統(tǒng)分析,才能做出最佳選擇。
我來舉一個例子說明我們公司在這方面所做的工作。
設(shè)備方面,以噴漆室采用空調(diào)循環(huán)風(fēng)技術(shù)為例,近幾年國內(nèi)外大多數(shù)汽車企業(yè)開始采用“干式噴漆室+循環(huán)風(fēng)”技術(shù)實現(xiàn)噴涂系統(tǒng)的節(jié)能降耗,經(jīng)過分析,我們發(fā)現(xiàn)該技術(shù)比較先進,也很節(jié)能,但設(shè)備投入及維護較高,且廢漆渣處置費用也相對較高。
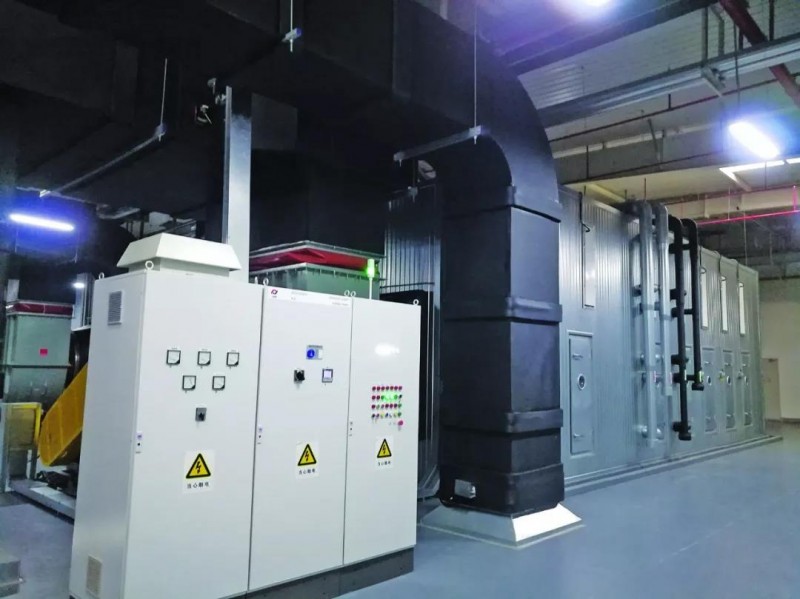
經(jīng)過詳細分析后,我們認(rèn)為噴涂系統(tǒng)實現(xiàn)節(jié)能的根本在于采用了循環(huán)風(fēng)技術(shù),而不是取決于是否為干式噴漆室,同時文丘里形式的濕式噴漆室對噴漆漆霧的捕捉能力可以達到99%,優(yōu)于目前使用的干式噴漆室,可以減輕循環(huán)風(fēng)空調(diào)進口處過濾系統(tǒng)的壓力。在漆渣處理方面,濕式噴漆室主要通過添加微量的漆霧凝聚劑進行漆渣處理,同時打撈出的漆渣經(jīng)瀝水干燥后,重量不會增加。
另外,濕式噴漆室技術(shù)比較成熟,已經(jīng)應(yīng)用了20年以上,設(shè)備已經(jīng)完全國產(chǎn)化,同時設(shè)備運行較為穩(wěn)定,基本沒有設(shè)備維修費用。因此,我們最終選用了“濕式噴漆室+循環(huán)風(fēng)空調(diào)+熱泵”的組合方式,在同樣實現(xiàn)節(jié)能降耗的同時,有效降低了前期的設(shè)備投入和后期的設(shè)備維護費用,經(jīng)對半年的實際運行數(shù)據(jù)統(tǒng)計分析,可實現(xiàn)噴漆室區(qū)域能耗下降50%以上,整車能耗下降15%以上,這個例子僅供大家參考,適合的才是最好的。
節(jié)能環(huán)保方面的努力
邢汶平女士:我們圍繞涂裝生產(chǎn)如何實現(xiàn)節(jié)能降耗和綠色環(huán)保,采用具體項目具體分析的方法,根據(jù)我們的產(chǎn)品目標(biāo)和生產(chǎn)線定位,設(shè)計和開發(fā)最為適合的生產(chǎn)工藝和涂裝設(shè)備。
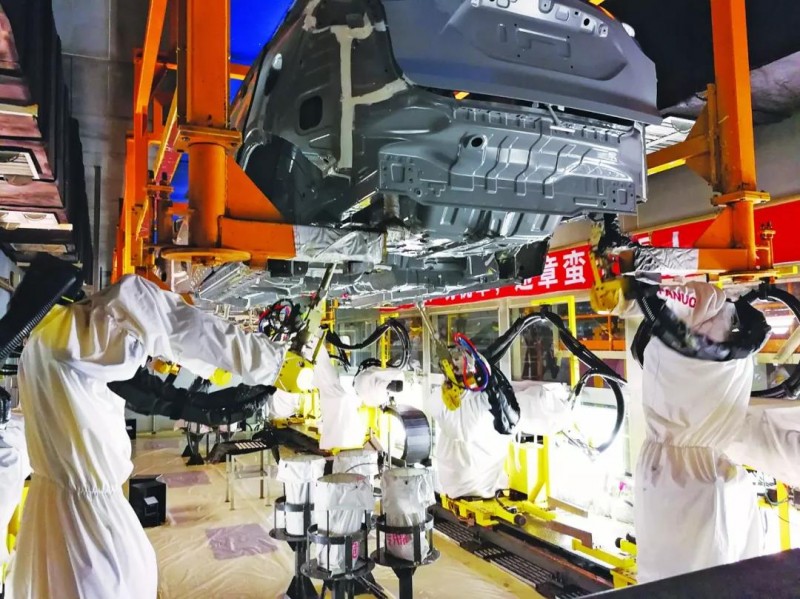
這里有一個典型例子可以說明,在我們公司大車廂涂裝生產(chǎn)線設(shè)計過程中,經(jīng)過對車廂產(chǎn)品特點和各類涂裝工藝的優(yōu)缺點進行詳細分析,車廂產(chǎn)品需與車身的顏色相匹配,因此其顏色主要有白色、藍色(素色漆)和藍色、紅色等金屬漆為主,其中白色占比為50%以上。而粉末涂料素色漆噴涂可采用2C1B工藝,涂料利用率達到95%以上,生產(chǎn)成本更低,且可實現(xiàn)“三廢”零排放,環(huán)保性能優(yōu)良。
但粉末涂料的金屬漆需要2C2B工藝,即金屬面漆噴涂后需要在高溫下固化方可進行罩光清漆的噴涂,罩光清漆噴涂后仍需要再次高溫烘干,能耗更高,液體金屬漆噴涂工藝則可以實現(xiàn)2C1B工藝,能耗相對較低。因此為滿足車廂生產(chǎn)多顏色的需求,我們設(shè)計了液體涂料和粉末涂料共線生產(chǎn)工藝,充分利用這兩種工藝的優(yōu)點,采用粉末涂料生產(chǎn)素色漆車廂,采用液體涂料生產(chǎn)金屬漆車廂,從而最大限度地實現(xiàn)節(jié)能降耗和綠色環(huán)保。
“自主創(chuàng)新”的生產(chǎn)實踐
邢汶平女士:我們的自主創(chuàng)新主要分為原始創(chuàng)新、消化吸收創(chuàng)新和集成創(chuàng)新三類,而自主創(chuàng)新課題的來源分為兩種,一種是滿足現(xiàn)有生產(chǎn)線在實現(xiàn)新產(chǎn)品上線及省人省力自動化方面的需求而做的技術(shù)創(chuàng)新工作;另一種是圍繞新工藝、新技術(shù)和新材料等應(yīng)用方面所做的技術(shù)創(chuàng)新工作,如為滿足水性免中涂新工藝的應(yīng)用,需要根據(jù)該工藝特有的技術(shù)特點開發(fā)配套的工藝裝備及方法,如我們開發(fā)的水性免中涂預(yù)烘干系統(tǒng)等。
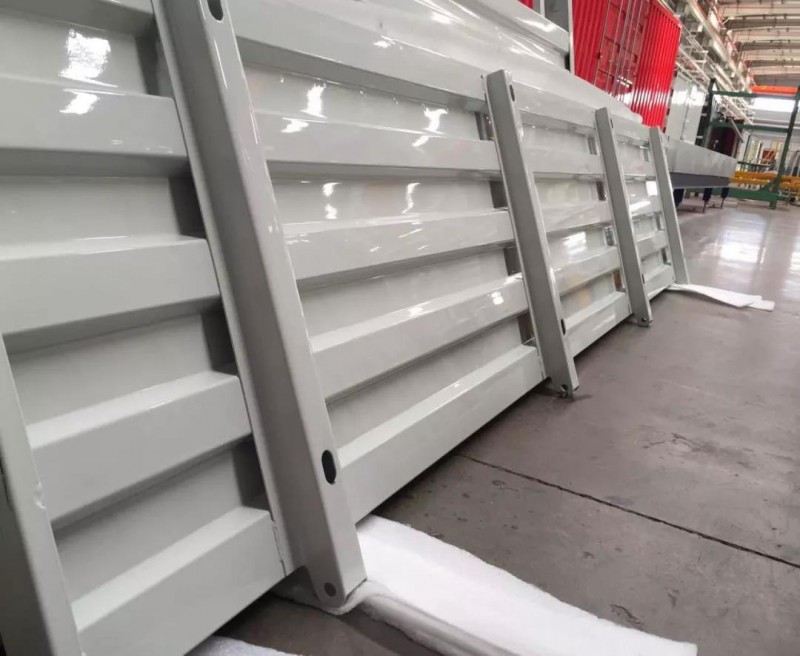
截至2017年,我們部門已獲得20多項發(fā)明專利證書和100多項實用新型專利證書,上面提到的液體涂料與粉末涂料共線生產(chǎn)工藝就是工藝上實現(xiàn)集成創(chuàng)新的典型例子,另外,我部門還為M6新車型開發(fā)了一種裙邊膠自動噴涂系統(tǒng),該系統(tǒng)可實現(xiàn)車身自動識別、自動噴涂和自動完成遮蔽,同時還可實現(xiàn)殘膠的回收利用,系統(tǒng)投資僅40萬元,還有許許多多的專利覆蓋涂裝新工藝、新設(shè)備和新方法等各個方面的改進和創(chuàng)新,主要是圍繞產(chǎn)品質(zhì)量提升、減少人工、精益生產(chǎn)和投資等方面的優(yōu)化和改進。
智能制造取得哪些成績
邢汶平女士:智能制造方面,我們主要從生產(chǎn)線仿真分析、自動化(即用自動設(shè)備或機器人等取代人工)、柔性化、數(shù)字化和網(wǎng)絡(luò)化方面開展工作。
在仿真分析方面,我們面向產(chǎn)品開發(fā)和工程開發(fā)兩個方面開展工作。圍繞產(chǎn)品開發(fā),我們通過引入VPS電泳仿真分析軟件,在產(chǎn)品處于數(shù)模階段就完成了涂裝質(zhì)量方面的分析工作,確保產(chǎn)品涂裝質(zhì)量達標(biāo);圍繞工程開發(fā),我們通過三維設(shè)計軟件實現(xiàn)生產(chǎn)線的三維設(shè)計,并開展產(chǎn)品3D模擬通過性分析及與廠房、公用管線的干涉檢查。在自動化方面,如我們最新的新港基地涂裝線,除必須由人工操作的工位(如打磨、目視檢查、精修和車身內(nèi)表面涂膠等工位),其他工位已全部實現(xiàn)自動化。
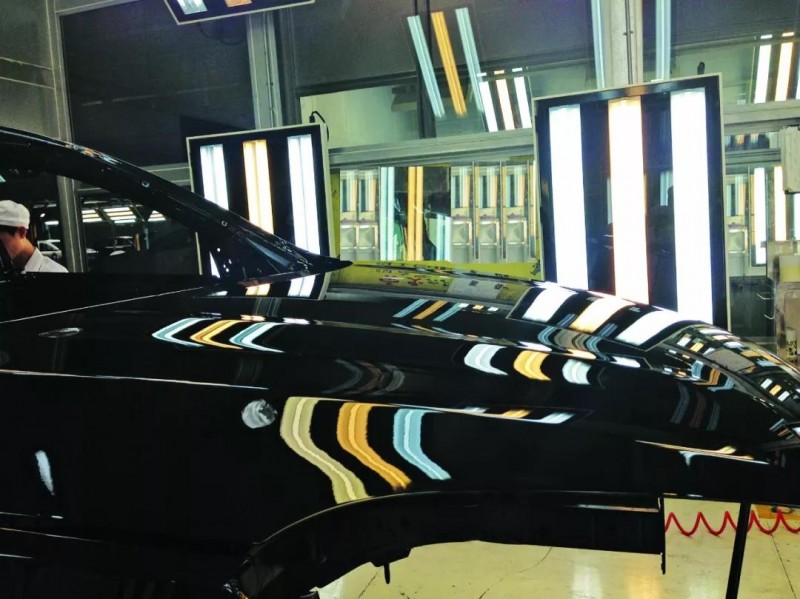
在柔性化方面,我們已實現(xiàn)了17種車型的混線生產(chǎn),通過自動識別車型實現(xiàn)自動切換車型對應(yīng)的橇體、調(diào)用對應(yīng)的工藝參數(shù)及自動分流等功能,同時設(shè)置AVI系統(tǒng)實現(xiàn)車身的實時位置跟蹤。
在數(shù)字化方面,生產(chǎn)線已基本實現(xiàn)設(shè)備運行數(shù)據(jù)、工藝參數(shù)數(shù)據(jù)、外觀質(zhì)量數(shù)據(jù)、能耗數(shù)據(jù)等采集、分析及報警。在網(wǎng)絡(luò)化方面,我們也實施了全生產(chǎn)環(huán)節(jié)的FAS系統(tǒng),即通過網(wǎng)絡(luò)實現(xiàn)全生產(chǎn)環(huán)節(jié)的信息化和生產(chǎn)指令下發(fā)等,但尚不能實現(xiàn)訂單化生產(chǎn)。
邢汶平眼中的工業(yè)4.0時代的汽車涂裝車間?
工業(yè)4.0時代的汽車涂裝車間
邢汶平
邢汶平女士:工業(yè)4.0時代的汽車涂裝車間應(yīng)該是涂裝生產(chǎn)能耗更低,大氣VOC、CO2和污水等排放量更小,智能化程度更高,同時在配有大量傳感器和大數(shù)據(jù)基礎(chǔ)上實現(xiàn)各類設(shè)備運行數(shù)據(jù)、工藝參數(shù)及質(zhì)量數(shù)據(jù)的自動分析、自動糾偏的數(shù)字化,和可實現(xiàn)訂單式生產(chǎn)、設(shè)備遠程監(jiān)控、遠程診斷的網(wǎng)絡(luò)化方面更加深入,最終實現(xiàn)客戶個性化定制的柔性化生產(chǎn)。
最后,借用涂裝界泰斗王錫春先生的一句話作為補充:“‘互聯(lián)網(wǎng)+綠色涂裝’是將汽車涂裝行業(yè)做大做強的必經(jīng)之路。它需從第三次工業(yè)革命的軟件嵌入模式發(fā)展到以網(wǎng)絡(luò)化、智能化為動力,是工業(yè)化和信息化的深度融合。”
未來發(fā)展計劃和目標(biāo)
在未來幾年,邢汶平女士將帶領(lǐng)涂裝工藝部技術(shù)團隊重點開展如下工作:
1)根據(jù)國家政策和公司規(guī)劃,新能源汽車都將是后期發(fā)展的重心,而新能源汽車車身將會采用鋁合金、塑料件及碳纖維等新型材料。涂裝工藝部將緊跟這一趨勢,圍繞這些新材料的涂裝技術(shù)開展研究。
2)涂裝工藝作為汽車制造領(lǐng)域中的污染和能耗大戶,涂裝工藝部仍將會在滿足和提升產(chǎn)品質(zhì)量的情況下,對可以實現(xiàn)節(jié)能降耗、更加綠色環(huán)保的涂裝新工藝、新材料、新技術(shù)和新設(shè)備等開展技術(shù)研究工作。
3)為實現(xiàn)“中國制造2025”的落地,涂裝工藝部將會繼續(xù)深化在智能化、數(shù)字化及網(wǎng)絡(luò)化方面的研究,以一條生產(chǎn)線為試點,通過生產(chǎn)運行收集大量的數(shù)據(jù)形成大數(shù)據(jù)庫,探索數(shù)字化工廠的建設(shè)。
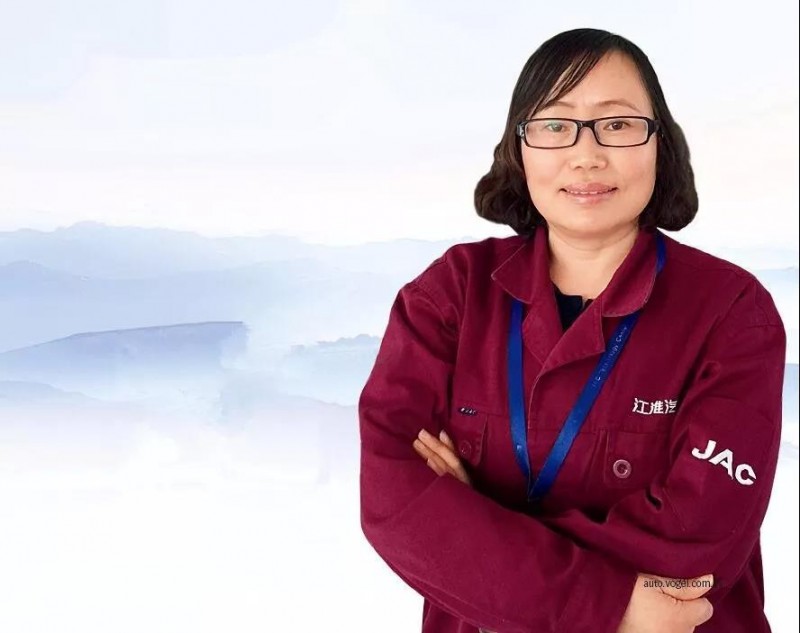
——江淮汽車技術(shù)中心工藝研究院涂裝工藝部技術(shù)總監(jiān)邢汶平女士
邢汶平女士擔(dān)任安徽江淮汽車集團股份有限公司技術(shù)中心工藝研究院涂裝工藝部技術(shù)總監(jiān)一職,主要負責(zé)江淮汽車涂裝生產(chǎn)線新建和改造項目的規(guī)劃設(shè)計、建設(shè)和工藝調(diào)試工作及新產(chǎn)品的涂裝工藝SE分析、生產(chǎn)線適應(yīng)性改造、工藝調(diào)試和量產(chǎn)拉動等工作。
新技術(shù)、新設(shè)備
邢汶平女士:江淮汽車在涂裝工藝方面按照安進董事長提出的“六化”要求,圍繞技術(shù)領(lǐng)先化、制造精益化的理念,通過采用新工藝、新技術(shù)和新設(shè)備,打造“綠色環(huán)保、節(jié)能低碳”的世界先進涂裝生產(chǎn)線。
在新工藝應(yīng)用方面,江淮汽車具有敢為天下先的勇氣,近幾年不斷引入新工藝、新技術(shù)。2012年,其率先在乘用車上采用當(dāng)時國際先進的水性免中涂涂裝工藝,在保證產(chǎn)品質(zhì)量的同時,實現(xiàn)了能源消耗、VOC排放及生產(chǎn)成本的大幅下降,成為我國首條應(yīng)用該技術(shù)的典范。2014年,江淮汽車采用的粉末涂料具有品質(zhì)更加優(yōu)良、廢水/廢氣/廢渣等零排放、涂料回收利用率高達95%以及生產(chǎn)成本更低等明顯優(yōu)勢,被成功應(yīng)用于商用車車廂涂裝線,這也是國內(nèi)首條車廂粉末生產(chǎn)線。
2015年,江淮汽車從歐洲引進了先進的水性單涂層工藝技術(shù)(工藝更加緊湊、VOC排放更低),用于江淮汽車遂寧工廠的素色漆生產(chǎn),為國內(nèi)商用車涂裝線水性化改造建立了一個新的樣板工廠。通過采用水性免中涂工藝取代原有3C2B溶劑型,采用水性單涂層工藝以及粉末涂料取代溶劑型單涂層技術(shù)等舉措,江淮汽車實現(xiàn)了涂裝技術(shù)在品質(zhì)、綠色、精益等方面的不斷升級。
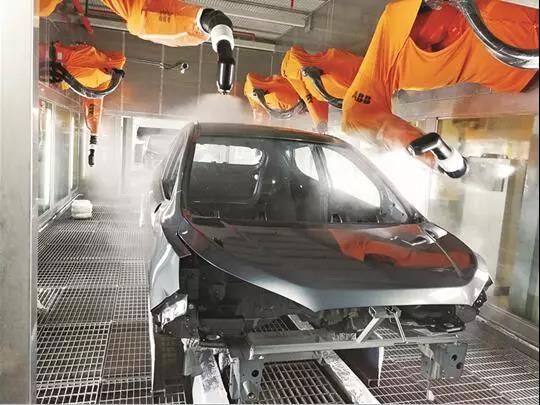
在涂裝設(shè)備選型方面,江淮汽車以智能、低碳為原則,選用最先進、最節(jié)能且最環(huán)保的工藝裝備。以江淮汽車新港生產(chǎn)基地為例,該項目車身內(nèi)外表面均采用機器人噴涂,機器人數(shù)量達48臺,實現(xiàn)了噴涂區(qū)域無人化,在保證產(chǎn)品一致性的同時,有效減少了人工并提高了涂料利用率。噴漆室采用最新的“空調(diào)循環(huán)風(fēng)+熱泵機組”節(jié)能技術(shù),實現(xiàn)了單臺涂裝能耗下降15%。烘干系統(tǒng)采用TAR集中供熱系統(tǒng),在滿足烘干加熱需求的同時,實現(xiàn)了烘干廢氣焚燒達標(biāo),同時為最大程度地降低烘干能耗,設(shè)置了煙氣余熱回收裝置,可實現(xiàn)年回收熱量折合天然氣26.2萬立方米,減少碳年排放1?458.03?t。下地板涂膠采用“機器人+3D膠槍涂膠系統(tǒng)”,實現(xiàn)了地板涂膠和PVC全自動噴涂,確保地板優(yōu)良防護性能,該項目建成后將是國內(nèi)最先進的商用車生產(chǎn)線。
在環(huán)保措施方面,江淮汽車涂裝線在全面采用水性涂料的同時,對于溶劑型清漆噴漆廢氣采用沸石轉(zhuǎn)輪+RTO焚燒技術(shù),將VOC排放量降至最低水平,可控制在?15?g/m2以下,滿足國內(nèi)最嚴(yán)格的排放限制要求,實現(xiàn)了真正意義上的綠色環(huán)保。
精益生產(chǎn)與技術(shù)先進性之間的平衡
邢汶平女士:精益生產(chǎn)體現(xiàn)在采用最合理的工藝方法和選用最適合的制造設(shè)備,而不一定是最先進的設(shè)備或技術(shù)。這需要通過對各類設(shè)備的技術(shù)特點及相關(guān)配套資源進行詳細調(diào)研,在設(shè)備的投入費用、日常運行費用、廢棄物處置費用以及設(shè)備維護保養(yǎng)費用等整個生命周期內(nèi)進行系統(tǒng)分析,才能做出最佳選擇。
我來舉一個例子說明我們公司在這方面所做的工作。
設(shè)備方面,以噴漆室采用空調(diào)循環(huán)風(fēng)技術(shù)為例,近幾年國內(nèi)外大多數(shù)汽車企業(yè)開始采用“干式噴漆室+循環(huán)風(fēng)”技術(shù)實現(xiàn)噴涂系統(tǒng)的節(jié)能降耗,經(jīng)過分析,我們發(fā)現(xiàn)該技術(shù)比較先進,也很節(jié)能,但設(shè)備投入及維護較高,且廢漆渣處置費用也相對較高。
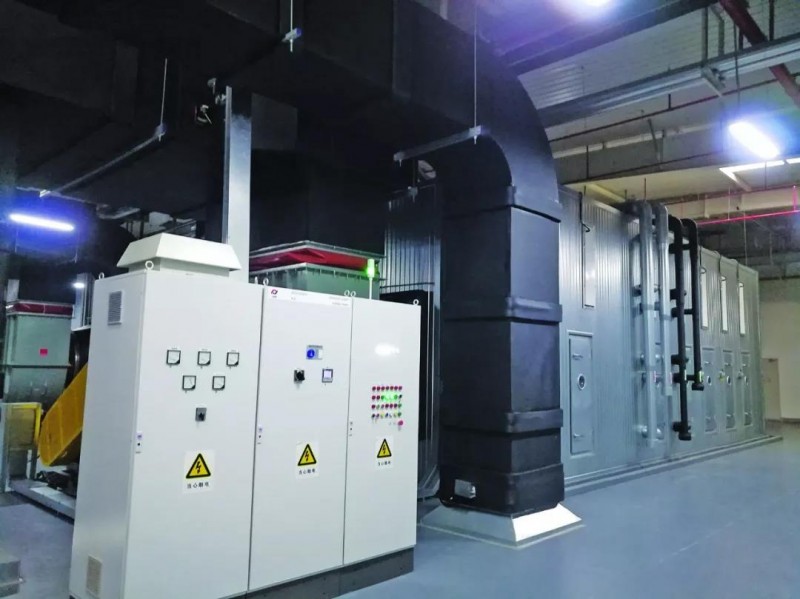
經(jīng)過詳細分析后,我們認(rèn)為噴涂系統(tǒng)實現(xiàn)節(jié)能的根本在于采用了循環(huán)風(fēng)技術(shù),而不是取決于是否為干式噴漆室,同時文丘里形式的濕式噴漆室對噴漆漆霧的捕捉能力可以達到99%,優(yōu)于目前使用的干式噴漆室,可以減輕循環(huán)風(fēng)空調(diào)進口處過濾系統(tǒng)的壓力。在漆渣處理方面,濕式噴漆室主要通過添加微量的漆霧凝聚劑進行漆渣處理,同時打撈出的漆渣經(jīng)瀝水干燥后,重量不會增加。
另外,濕式噴漆室技術(shù)比較成熟,已經(jīng)應(yīng)用了20年以上,設(shè)備已經(jīng)完全國產(chǎn)化,同時設(shè)備運行較為穩(wěn)定,基本沒有設(shè)備維修費用。因此,我們最終選用了“濕式噴漆室+循環(huán)風(fēng)空調(diào)+熱泵”的組合方式,在同樣實現(xiàn)節(jié)能降耗的同時,有效降低了前期的設(shè)備投入和后期的設(shè)備維護費用,經(jīng)對半年的實際運行數(shù)據(jù)統(tǒng)計分析,可實現(xiàn)噴漆室區(qū)域能耗下降50%以上,整車能耗下降15%以上,這個例子僅供大家參考,適合的才是最好的。
節(jié)能環(huán)保方面的努力
邢汶平女士:我們圍繞涂裝生產(chǎn)如何實現(xiàn)節(jié)能降耗和綠色環(huán)保,采用具體項目具體分析的方法,根據(jù)我們的產(chǎn)品目標(biāo)和生產(chǎn)線定位,設(shè)計和開發(fā)最為適合的生產(chǎn)工藝和涂裝設(shè)備。
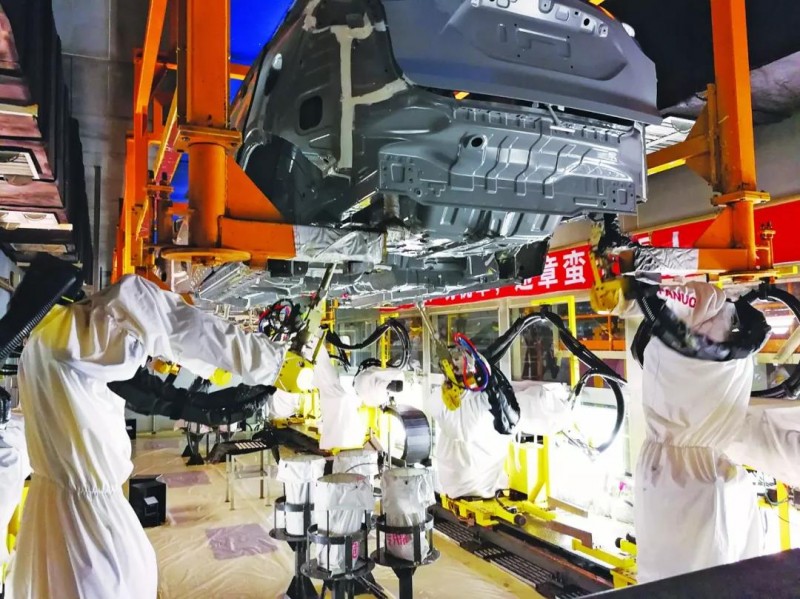
這里有一個典型例子可以說明,在我們公司大車廂涂裝生產(chǎn)線設(shè)計過程中,經(jīng)過對車廂產(chǎn)品特點和各類涂裝工藝的優(yōu)缺點進行詳細分析,車廂產(chǎn)品需與車身的顏色相匹配,因此其顏色主要有白色、藍色(素色漆)和藍色、紅色等金屬漆為主,其中白色占比為50%以上。而粉末涂料素色漆噴涂可采用2C1B工藝,涂料利用率達到95%以上,生產(chǎn)成本更低,且可實現(xiàn)“三廢”零排放,環(huán)保性能優(yōu)良。
但粉末涂料的金屬漆需要2C2B工藝,即金屬面漆噴涂后需要在高溫下固化方可進行罩光清漆的噴涂,罩光清漆噴涂后仍需要再次高溫烘干,能耗更高,液體金屬漆噴涂工藝則可以實現(xiàn)2C1B工藝,能耗相對較低。因此為滿足車廂生產(chǎn)多顏色的需求,我們設(shè)計了液體涂料和粉末涂料共線生產(chǎn)工藝,充分利用這兩種工藝的優(yōu)點,采用粉末涂料生產(chǎn)素色漆車廂,采用液體涂料生產(chǎn)金屬漆車廂,從而最大限度地實現(xiàn)節(jié)能降耗和綠色環(huán)保。
“自主創(chuàng)新”的生產(chǎn)實踐
邢汶平女士:我們的自主創(chuàng)新主要分為原始創(chuàng)新、消化吸收創(chuàng)新和集成創(chuàng)新三類,而自主創(chuàng)新課題的來源分為兩種,一種是滿足現(xiàn)有生產(chǎn)線在實現(xiàn)新產(chǎn)品上線及省人省力自動化方面的需求而做的技術(shù)創(chuàng)新工作;另一種是圍繞新工藝、新技術(shù)和新材料等應(yīng)用方面所做的技術(shù)創(chuàng)新工作,如為滿足水性免中涂新工藝的應(yīng)用,需要根據(jù)該工藝特有的技術(shù)特點開發(fā)配套的工藝裝備及方法,如我們開發(fā)的水性免中涂預(yù)烘干系統(tǒng)等。
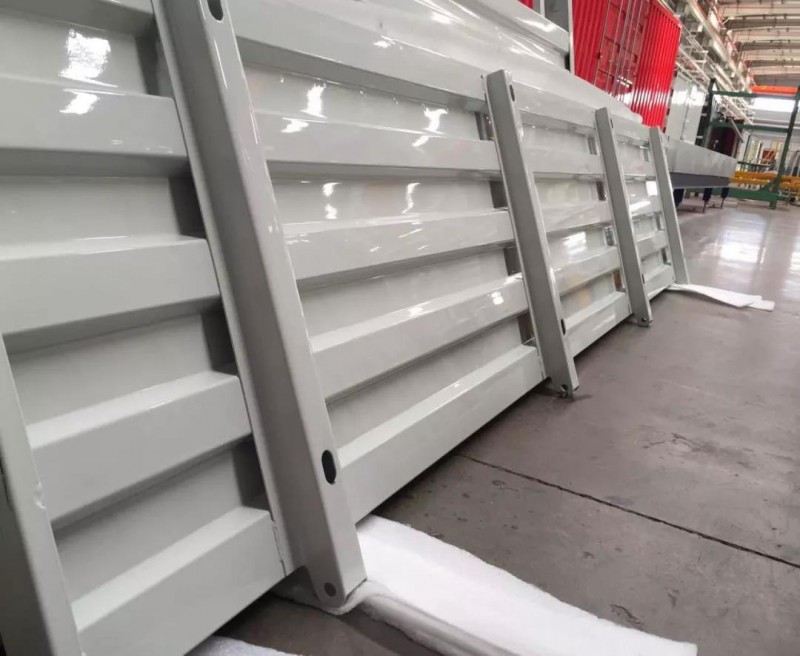
截至2017年,我們部門已獲得20多項發(fā)明專利證書和100多項實用新型專利證書,上面提到的液體涂料與粉末涂料共線生產(chǎn)工藝就是工藝上實現(xiàn)集成創(chuàng)新的典型例子,另外,我部門還為M6新車型開發(fā)了一種裙邊膠自動噴涂系統(tǒng),該系統(tǒng)可實現(xiàn)車身自動識別、自動噴涂和自動完成遮蔽,同時還可實現(xiàn)殘膠的回收利用,系統(tǒng)投資僅40萬元,還有許許多多的專利覆蓋涂裝新工藝、新設(shè)備和新方法等各個方面的改進和創(chuàng)新,主要是圍繞產(chǎn)品質(zhì)量提升、減少人工、精益生產(chǎn)和投資等方面的優(yōu)化和改進。
智能制造取得哪些成績
邢汶平女士:智能制造方面,我們主要從生產(chǎn)線仿真分析、自動化(即用自動設(shè)備或機器人等取代人工)、柔性化、數(shù)字化和網(wǎng)絡(luò)化方面開展工作。
在仿真分析方面,我們面向產(chǎn)品開發(fā)和工程開發(fā)兩個方面開展工作。圍繞產(chǎn)品開發(fā),我們通過引入VPS電泳仿真分析軟件,在產(chǎn)品處于數(shù)模階段就完成了涂裝質(zhì)量方面的分析工作,確保產(chǎn)品涂裝質(zhì)量達標(biāo);圍繞工程開發(fā),我們通過三維設(shè)計軟件實現(xiàn)生產(chǎn)線的三維設(shè)計,并開展產(chǎn)品3D模擬通過性分析及與廠房、公用管線的干涉檢查。在自動化方面,如我們最新的新港基地涂裝線,除必須由人工操作的工位(如打磨、目視檢查、精修和車身內(nèi)表面涂膠等工位),其他工位已全部實現(xiàn)自動化。
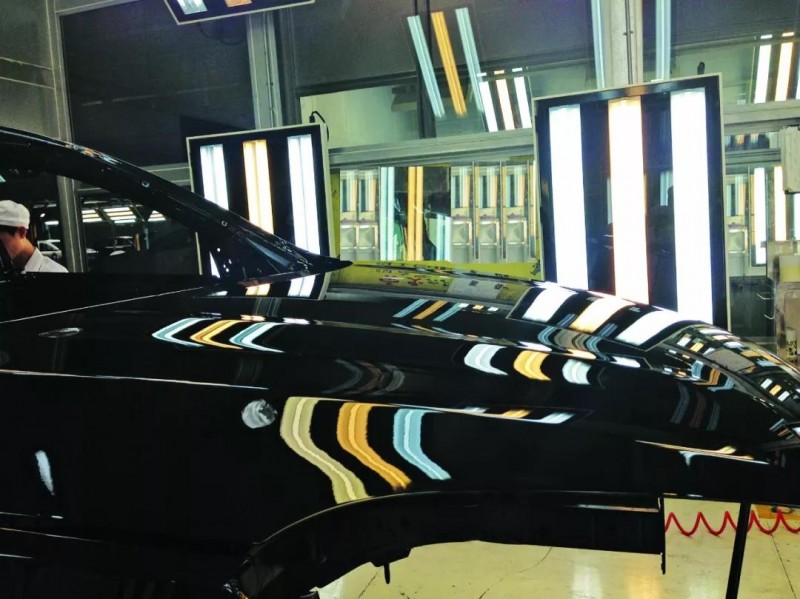
在柔性化方面,我們已實現(xiàn)了17種車型的混線生產(chǎn),通過自動識別車型實現(xiàn)自動切換車型對應(yīng)的橇體、調(diào)用對應(yīng)的工藝參數(shù)及自動分流等功能,同時設(shè)置AVI系統(tǒng)實現(xiàn)車身的實時位置跟蹤。
在數(shù)字化方面,生產(chǎn)線已基本實現(xiàn)設(shè)備運行數(shù)據(jù)、工藝參數(shù)數(shù)據(jù)、外觀質(zhì)量數(shù)據(jù)、能耗數(shù)據(jù)等采集、分析及報警。在網(wǎng)絡(luò)化方面,我們也實施了全生產(chǎn)環(huán)節(jié)的FAS系統(tǒng),即通過網(wǎng)絡(luò)實現(xiàn)全生產(chǎn)環(huán)節(jié)的信息化和生產(chǎn)指令下發(fā)等,但尚不能實現(xiàn)訂單化生產(chǎn)。
邢汶平眼中的工業(yè)4.0時代的汽車涂裝車間?
工業(yè)4.0時代的汽車涂裝車間
邢汶平
邢汶平女士:工業(yè)4.0時代的汽車涂裝車間應(yīng)該是涂裝生產(chǎn)能耗更低,大氣VOC、CO2和污水等排放量更小,智能化程度更高,同時在配有大量傳感器和大數(shù)據(jù)基礎(chǔ)上實現(xiàn)各類設(shè)備運行數(shù)據(jù)、工藝參數(shù)及質(zhì)量數(shù)據(jù)的自動分析、自動糾偏的數(shù)字化,和可實現(xiàn)訂單式生產(chǎn)、設(shè)備遠程監(jiān)控、遠程診斷的網(wǎng)絡(luò)化方面更加深入,最終實現(xiàn)客戶個性化定制的柔性化生產(chǎn)。
最后,借用涂裝界泰斗王錫春先生的一句話作為補充:“‘互聯(lián)網(wǎng)+綠色涂裝’是將汽車涂裝行業(yè)做大做強的必經(jīng)之路。它需從第三次工業(yè)革命的軟件嵌入模式發(fā)展到以網(wǎng)絡(luò)化、智能化為動力,是工業(yè)化和信息化的深度融合。”
未來發(fā)展計劃和目標(biāo)
在未來幾年,邢汶平女士將帶領(lǐng)涂裝工藝部技術(shù)團隊重點開展如下工作:
1)根據(jù)國家政策和公司規(guī)劃,新能源汽車都將是后期發(fā)展的重心,而新能源汽車車身將會采用鋁合金、塑料件及碳纖維等新型材料。涂裝工藝部將緊跟這一趨勢,圍繞這些新材料的涂裝技術(shù)開展研究。
2)涂裝工藝作為汽車制造領(lǐng)域中的污染和能耗大戶,涂裝工藝部仍將會在滿足和提升產(chǎn)品質(zhì)量的情況下,對可以實現(xiàn)節(jié)能降耗、更加綠色環(huán)保的涂裝新工藝、新材料、新技術(shù)和新設(shè)備等開展技術(shù)研究工作。
3)為實現(xiàn)“中國制造2025”的落地,涂裝工藝部將會繼續(xù)深化在智能化、數(shù)字化及網(wǎng)絡(luò)化方面的研究,以一條生產(chǎn)線為試點,通過生產(chǎn)運行收集大量的數(shù)據(jù)形成大數(shù)據(jù)庫,探索數(shù)字化工廠的建設(shè)。
- 下一篇:瓦爾特渦輪罩精密刀具
- 上一篇:工業(yè)的大門已為協(xié)作機器人敞開
編輯推薦
最新資訊
-
跨越速運憑什么“圈粉”萬千客戶?“
2025-07-01 14:42
-
數(shù)智破局啟新篇?生態(tài)共生再啟程 —
2025-06-27 20:13
-
助力汽車零部件產(chǎn)線智能化升級,西門
2025-06-27 13:59
-
BBA集體轉(zhuǎn)向!放棄全面電動化
2025-06-26 17:32
-
比換柜省錢,比自研省心,西門子Xcel
2025-06-25 15:07