汽車發(fā)動機齒圈飛輪盤板沖鍛制作新技術(shù)
2018-07-12 16:01:26· 來源:鍛造與沖壓
齒圈飛輪盤是自動擋汽車發(fā)動機上的一個重要功能部件,筆者在成功地實現(xiàn)了其結(jié)構(gòu)輕量化的同時,還研發(fā)出實現(xiàn)輕量化飛輪盤整體閉式溫沖鍛成形和旋壓增厚成形新技術(shù),應(yīng)用于生產(chǎn),產(chǎn)生了良好的經(jīng)濟與社會效益。
齒圈飛輪盤是自動擋汽車發(fā)動機上的一個重要功能部件,筆者在成功地實現(xiàn)了其結(jié)構(gòu)輕量化的同時,還研發(fā)出實現(xiàn)輕量化飛輪盤整體閉式溫沖鍛成形和旋壓增厚成形新技術(shù),應(yīng)用于生產(chǎn),產(chǎn)生了良好的經(jīng)濟與社會效益。
功能及結(jié)構(gòu)特點
齒圈飛輪盤總成是自動擋汽車發(fā)動機的一個重要零部件,自動變速箱的飛輪相對手動變速箱的飛輪較輕較薄,安裝在曲軸后面,外緣上的齒圈用來與起動機嚙合。飛輪用來平順做功行程之間的脈沖振動,并提供慣性以便發(fā)動機怠速平穩(wěn)。
齒圈飛輪盤的傳統(tǒng)結(jié)構(gòu)由飛輪盤、飛輪齒圈、三角支撐墊、變矩器緊固墊及曲軸法蘭襯墊所組成,如圖1 所示,飛輪盤有信號齒,用于傳遞轉(zhuǎn)速信號,墊片與發(fā)動機曲軸聯(lián)接,將力矩傳遞到三角支撐墊上,進而傳遞到液力變矩器。部件總體上屬于盤狀回轉(zhuǎn)體形狀,結(jié)構(gòu)復雜,尺寸精度要求高,制造難度大。
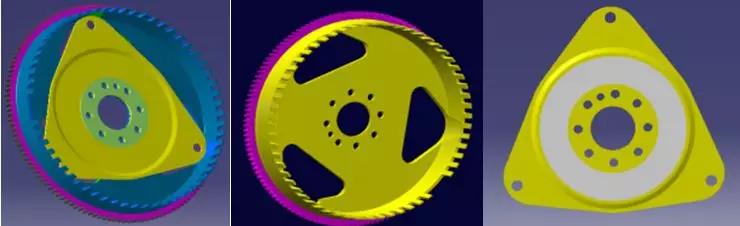
圖1 齒圈飛輪盤零件
改進后的結(jié)構(gòu)
柔性飛輪總成由齒圈(盤)、柔性托盤組成,如圖2 所示,齒圈(盤)與柔性托盤鉚接在一起,具有更好的柔性,零件形狀和結(jié)構(gòu)復雜,尺寸精度高,可靠性強。齒盤需要采用半閉式旋壓增厚特種成形工藝。
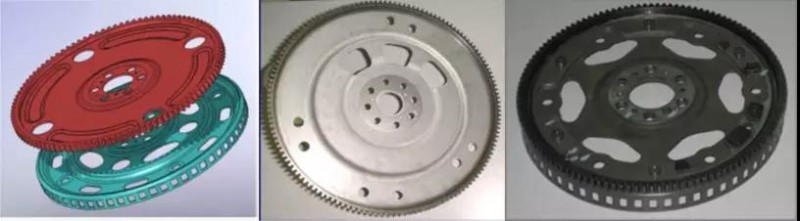
圖2 改進后的齒圈飛輪托盤零件
整體閉式溫沖鍛成形
工藝方案的確定
該飛輪盤屬于高度尺寸不大且壁厚比底厚大1mm 的盤形件,經(jīng)初步分析,可以采用如下兩種工藝方案:
⑴溫熱反擠壓成形。其工藝流程是下料→加熱→端面整平→反擠壓→底部沖孔→盤形口部車平。
⑵板鍛溫成形。以板料為原始毛坯,通過沖壓和鍛造復合成形方法得到所需精化毛坯或成品零件,其工藝流程是落料→加熱→拉深→鐓鍛成形,如圖3 所示。其中,鐓鍛的作用是使飛輪盤筒形壁厚由10mm增加至11mm,同時將內(nèi)圓角R20mm 減小至R5mm,外圓角由R30mm 減小至R2.5mm。
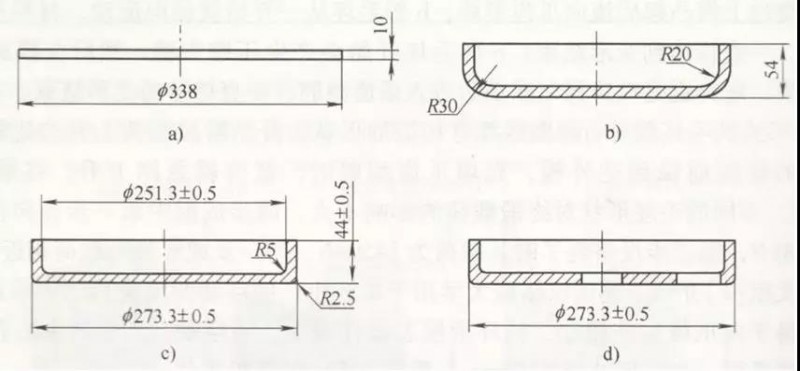
圖3 板鍛溫成形工序圖
模具設(shè)計
⑴拉深模。拉深模結(jié)構(gòu)如圖4 所示,該模采用導柱34 和導套35 導向,凹模采用預(yù)應(yīng)力組合結(jié)構(gòu)(凹模16、預(yù)應(yīng)力圈15),凹模下面設(shè)置有頂出機構(gòu)(小圓柱1、頂桿2、托板3、頂板13),凸模17 為橫向分層結(jié)構(gòu),凸模外圍設(shè)有環(huán)形頂出器18,環(huán)形頂出器上端通過頂桿30 同橫板31 接觸,下環(huán)形面通過螺栓25、彈簧24 與上模板22 相連的托板19 限位。該模具也是安裝在Y34KJII-800 型液壓機上使用,下模安裝在壓力機工作臺上,上模安裝在壓力機滑塊下面,橫板31 與安裝在滑塊內(nèi)的油缸活塞桿相連。工作時,將加熱至850℃左右的坯料(φ 338mm×10mm)放置在凹??谏希ㄟ^定位銷33 定位,開動壓力機,滑塊下行帶動凸模使坯料拉深成形,成形結(jié)束后,滑塊帶動凸?;爻?,滑塊內(nèi)頂出油缸通過環(huán)形頂出器,將套在凸模上的拉深工件從凸模上退下。
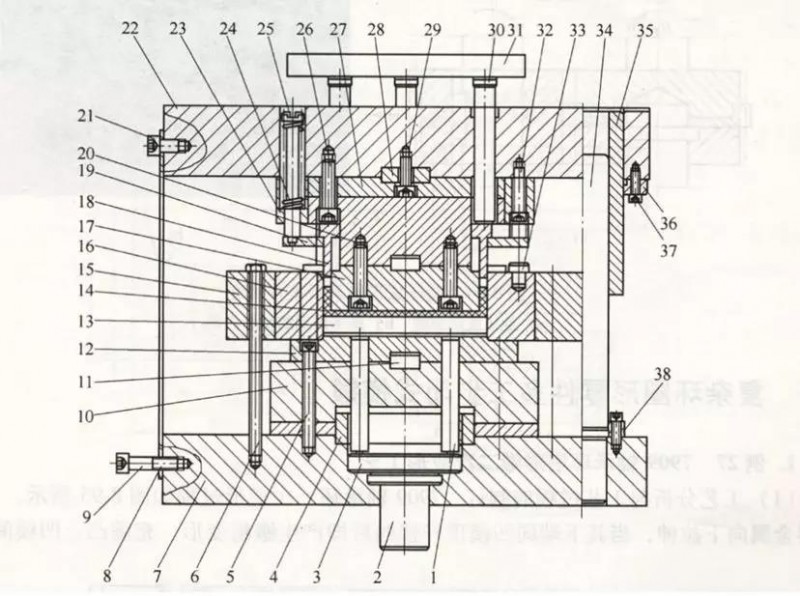
圖4 拉深模結(jié)構(gòu)
1-小圓柱;2-頂桿;3-托板;4-定位環(huán);5,6,9,20,21,26,29,32,37,38-螺釘;7-下模板;8-連接板(模具吊裝用);10-模座;11-定位塊;12-墊板;13-頂板;14-工件;15-預(yù)應(yīng)力圈;16-凹模;17-凸模;18-環(huán)形頂出器;19-托板;22-上模板;23-座圈;24-彈簧;25-螺栓;27-墊板;28-定位塊;30-頂桿;31-橫板;33-定位銷;34-導柱;35-導套;36-固定圈
⑵鐓鍛整形模。該模具結(jié)構(gòu)與圖4 所示拉深模幾乎相同,其不同之處:一是凸模17 的端部做成倒角或做成大于飛輪盤零件內(nèi)圓角R5mm 的圓角;二是凸、凹模的間隙為11mm,而拉深模具凸、凹模的間隙為10mm;三是環(huán)形頂出器在這副模具中是先作為環(huán)形鐓鍛與整形的凸模,然后作為頂出器使用。
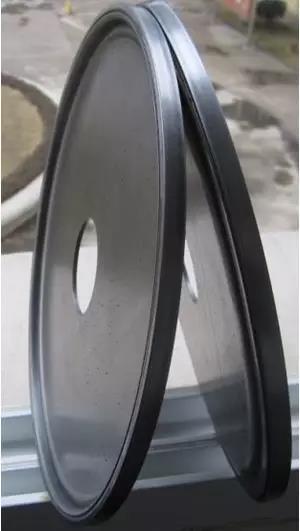
圖5 厚輪緣薄輻板旋壓毛坯
旋壓增厚成形原理
旋壓增厚以閉式溫沖鍛成形得到的精密盤形工件為毛坯(圖5)。旋壓增厚成形原理如圖6 所示,圓形板坯3 置于托盤4 上,壓盤2 被油缸柱塞1 壓緊,板坯和壓盤快速旋轉(zhuǎn),四個旋壓輪依次動作,首先旋壓輪6 沿徑向?qū)Π迮魇┘訅毫Γ拱逋馊υ龊?,達到徑向進給量后沿原路徑退回,然后,旋壓輪7、8 及9 依次執(zhí)行與旋壓輪6 相同的動作,直至板坯外圓形成與板坯垂直的輪緣且厚度達到所設(shè)計的厚度為止。
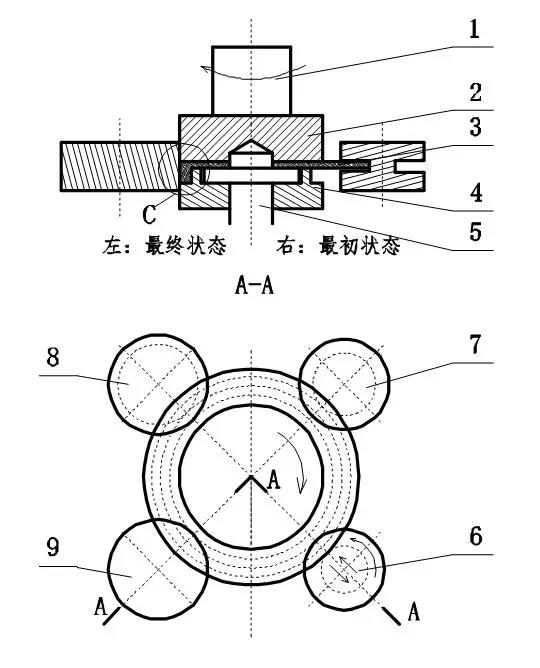
圖6 旋壓增厚成形原理
1-油缸柱塞;2-壓盤;3-板坯;4-托盤;5-旋轉(zhuǎn)軸;6,7,8,9-旋輪;
旋壓設(shè)備的研制
旋壓機由上主軸、下主軸、下頂出和旋輪進給系統(tǒng)組成,工作時先將環(huán)形坯料置于下主軸上,然后上主軸下行與下主軸一同將坯料夾緊并隨下主軸一同旋轉(zhuǎn),接著各旋輪依次進給,將環(huán)形毛坯輪緣增厚至所要求的厚度。圖7 所示為華中科技大學材料成形與模具技術(shù)國家重點實驗室與黃石華力鍛壓機床有限公司聯(lián)合開發(fā)的專用旋壓增厚機,由該機所生產(chǎn)出的齒圈飛輪盤精化毛坯如圖8 所示。
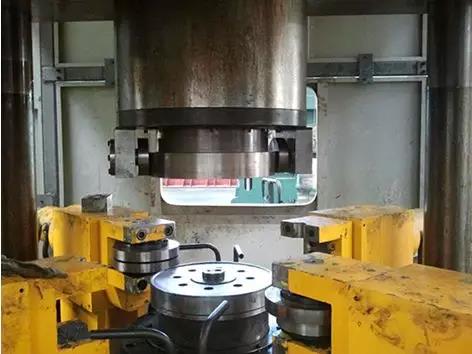
圖7 數(shù)控旋壓機
.jpg)
圖8 齒圈飛輪托盤精化毛坯
增厚輪緣外表面上的小模數(shù)直齒可采用兩種方法加工:一是旋壓成形,即將旋壓增厚的旋輪換成模數(shù)相等的旋輪,因模數(shù)一般為m=1mm,所以工件旋轉(zhuǎn)一圈即可;二是利用滾齒機加工。
應(yīng)用效果
采用所研究的齒圈飛輪盤閉式?jīng)_鍛成形和旋壓增厚成形技術(shù)成功生產(chǎn)出輕量化、一體化的齒圈飛輪盤零件(圖5、圖8),與原有生產(chǎn)技術(shù)比較:
⑴實現(xiàn)齒圈和連接盤整體制造后,材料用量由4.6kg 降至1.9kg,材料利用率由27% 提高到75%。
⑵加工工序由11 道減少至3 道,提高生產(chǎn)效率近4 倍。
⑶所研制的齒圈飛輪盤旋壓成形專用機床及工裝模具滿足工藝試驗要求,所加工的汽車齒圈飛輪盤樣件達到神龍公司EW10A 型主要技術(shù)指標要求。
⑷單件生產(chǎn)成本降低到原有成本的70%。
功能及結(jié)構(gòu)特點
齒圈飛輪盤總成是自動擋汽車發(fā)動機的一個重要零部件,自動變速箱的飛輪相對手動變速箱的飛輪較輕較薄,安裝在曲軸后面,外緣上的齒圈用來與起動機嚙合。飛輪用來平順做功行程之間的脈沖振動,并提供慣性以便發(fā)動機怠速平穩(wěn)。
齒圈飛輪盤的傳統(tǒng)結(jié)構(gòu)由飛輪盤、飛輪齒圈、三角支撐墊、變矩器緊固墊及曲軸法蘭襯墊所組成,如圖1 所示,飛輪盤有信號齒,用于傳遞轉(zhuǎn)速信號,墊片與發(fā)動機曲軸聯(lián)接,將力矩傳遞到三角支撐墊上,進而傳遞到液力變矩器。部件總體上屬于盤狀回轉(zhuǎn)體形狀,結(jié)構(gòu)復雜,尺寸精度要求高,制造難度大。
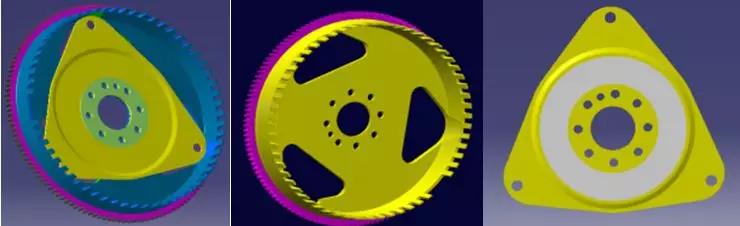
圖1 齒圈飛輪盤零件
改進后的結(jié)構(gòu)
柔性飛輪總成由齒圈(盤)、柔性托盤組成,如圖2 所示,齒圈(盤)與柔性托盤鉚接在一起,具有更好的柔性,零件形狀和結(jié)構(gòu)復雜,尺寸精度高,可靠性強。齒盤需要采用半閉式旋壓增厚特種成形工藝。
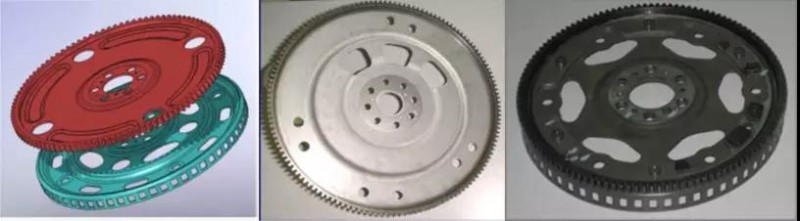
圖2 改進后的齒圈飛輪托盤零件
整體閉式溫沖鍛成形
工藝方案的確定
該飛輪盤屬于高度尺寸不大且壁厚比底厚大1mm 的盤形件,經(jīng)初步分析,可以采用如下兩種工藝方案:
⑴溫熱反擠壓成形。其工藝流程是下料→加熱→端面整平→反擠壓→底部沖孔→盤形口部車平。
⑵板鍛溫成形。以板料為原始毛坯,通過沖壓和鍛造復合成形方法得到所需精化毛坯或成品零件,其工藝流程是落料→加熱→拉深→鐓鍛成形,如圖3 所示。其中,鐓鍛的作用是使飛輪盤筒形壁厚由10mm增加至11mm,同時將內(nèi)圓角R20mm 減小至R5mm,外圓角由R30mm 減小至R2.5mm。
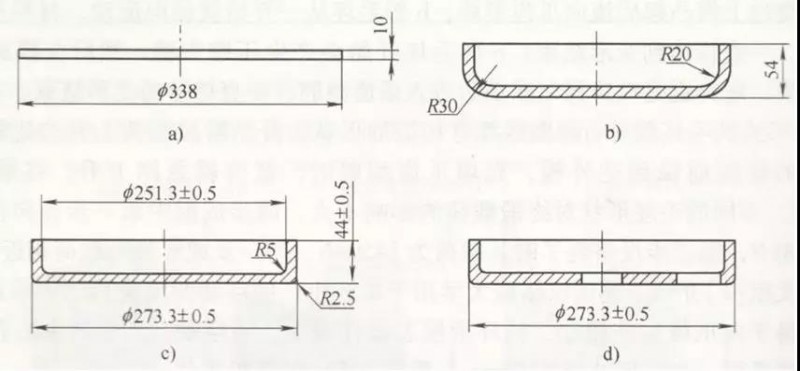
圖3 板鍛溫成形工序圖
模具設(shè)計
⑴拉深模。拉深模結(jié)構(gòu)如圖4 所示,該模采用導柱34 和導套35 導向,凹模采用預(yù)應(yīng)力組合結(jié)構(gòu)(凹模16、預(yù)應(yīng)力圈15),凹模下面設(shè)置有頂出機構(gòu)(小圓柱1、頂桿2、托板3、頂板13),凸模17 為橫向分層結(jié)構(gòu),凸模外圍設(shè)有環(huán)形頂出器18,環(huán)形頂出器上端通過頂桿30 同橫板31 接觸,下環(huán)形面通過螺栓25、彈簧24 與上模板22 相連的托板19 限位。該模具也是安裝在Y34KJII-800 型液壓機上使用,下模安裝在壓力機工作臺上,上模安裝在壓力機滑塊下面,橫板31 與安裝在滑塊內(nèi)的油缸活塞桿相連。工作時,將加熱至850℃左右的坯料(φ 338mm×10mm)放置在凹??谏希ㄟ^定位銷33 定位,開動壓力機,滑塊下行帶動凸模使坯料拉深成形,成形結(jié)束后,滑塊帶動凸?;爻?,滑塊內(nèi)頂出油缸通過環(huán)形頂出器,將套在凸模上的拉深工件從凸模上退下。
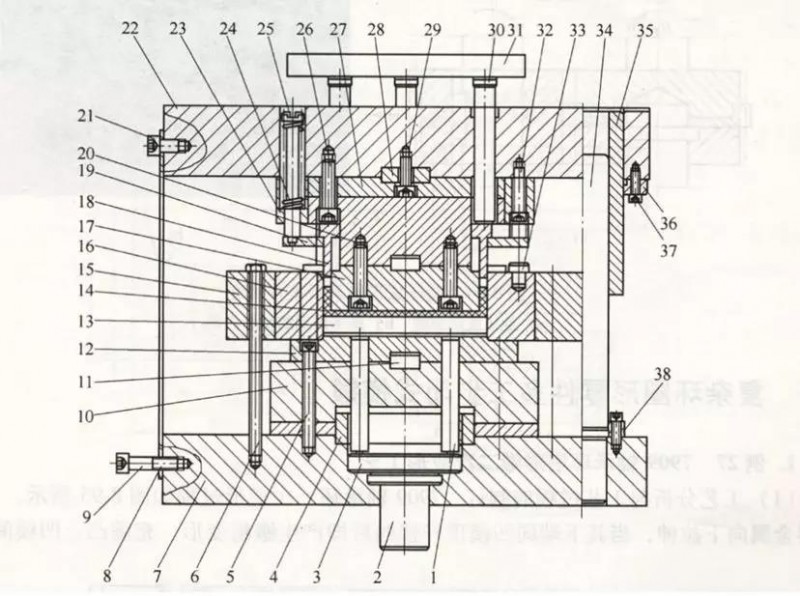
圖4 拉深模結(jié)構(gòu)
1-小圓柱;2-頂桿;3-托板;4-定位環(huán);5,6,9,20,21,26,29,32,37,38-螺釘;7-下模板;8-連接板(模具吊裝用);10-模座;11-定位塊;12-墊板;13-頂板;14-工件;15-預(yù)應(yīng)力圈;16-凹模;17-凸模;18-環(huán)形頂出器;19-托板;22-上模板;23-座圈;24-彈簧;25-螺栓;27-墊板;28-定位塊;30-頂桿;31-橫板;33-定位銷;34-導柱;35-導套;36-固定圈
⑵鐓鍛整形模。該模具結(jié)構(gòu)與圖4 所示拉深模幾乎相同,其不同之處:一是凸模17 的端部做成倒角或做成大于飛輪盤零件內(nèi)圓角R5mm 的圓角;二是凸、凹模的間隙為11mm,而拉深模具凸、凹模的間隙為10mm;三是環(huán)形頂出器在這副模具中是先作為環(huán)形鐓鍛與整形的凸模,然后作為頂出器使用。
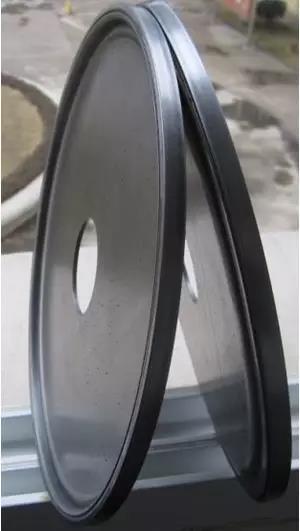
圖5 厚輪緣薄輻板旋壓毛坯
旋壓增厚成形原理
旋壓增厚以閉式溫沖鍛成形得到的精密盤形工件為毛坯(圖5)。旋壓增厚成形原理如圖6 所示,圓形板坯3 置于托盤4 上,壓盤2 被油缸柱塞1 壓緊,板坯和壓盤快速旋轉(zhuǎn),四個旋壓輪依次動作,首先旋壓輪6 沿徑向?qū)Π迮魇┘訅毫Γ拱逋馊υ龊?,達到徑向進給量后沿原路徑退回,然后,旋壓輪7、8 及9 依次執(zhí)行與旋壓輪6 相同的動作,直至板坯外圓形成與板坯垂直的輪緣且厚度達到所設(shè)計的厚度為止。
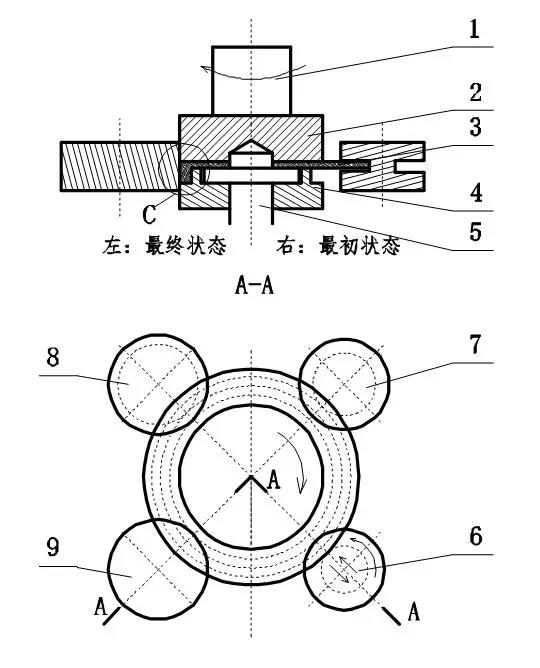
圖6 旋壓增厚成形原理
1-油缸柱塞;2-壓盤;3-板坯;4-托盤;5-旋轉(zhuǎn)軸;6,7,8,9-旋輪;
旋壓設(shè)備的研制
旋壓機由上主軸、下主軸、下頂出和旋輪進給系統(tǒng)組成,工作時先將環(huán)形坯料置于下主軸上,然后上主軸下行與下主軸一同將坯料夾緊并隨下主軸一同旋轉(zhuǎn),接著各旋輪依次進給,將環(huán)形毛坯輪緣增厚至所要求的厚度。圖7 所示為華中科技大學材料成形與模具技術(shù)國家重點實驗室與黃石華力鍛壓機床有限公司聯(lián)合開發(fā)的專用旋壓增厚機,由該機所生產(chǎn)出的齒圈飛輪盤精化毛坯如圖8 所示。
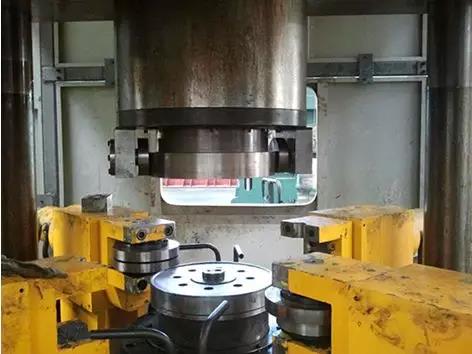
圖7 數(shù)控旋壓機
.jpg)
圖8 齒圈飛輪托盤精化毛坯
增厚輪緣外表面上的小模數(shù)直齒可采用兩種方法加工:一是旋壓成形,即將旋壓增厚的旋輪換成模數(shù)相等的旋輪,因模數(shù)一般為m=1mm,所以工件旋轉(zhuǎn)一圈即可;二是利用滾齒機加工。
應(yīng)用效果
采用所研究的齒圈飛輪盤閉式?jīng)_鍛成形和旋壓增厚成形技術(shù)成功生產(chǎn)出輕量化、一體化的齒圈飛輪盤零件(圖5、圖8),與原有生產(chǎn)技術(shù)比較:
⑴實現(xiàn)齒圈和連接盤整體制造后,材料用量由4.6kg 降至1.9kg,材料利用率由27% 提高到75%。
⑵加工工序由11 道減少至3 道,提高生產(chǎn)效率近4 倍。
⑶所研制的齒圈飛輪盤旋壓成形專用機床及工裝模具滿足工藝試驗要求,所加工的汽車齒圈飛輪盤樣件達到神龍公司EW10A 型主要技術(shù)指標要求。
⑷單件生產(chǎn)成本降低到原有成本的70%。
最新資訊
-
跨越速運憑什么“圈粉”萬千客戶?“
2025-07-01 14:42
-
數(shù)智破局啟新篇?生態(tài)共生再啟程 —
2025-06-27 20:13
-
助力汽車零部件產(chǎn)線智能化升級,西門
2025-06-27 13:59
-
BBA集體轉(zhuǎn)向!放棄全面電動化
2025-06-26 17:32
-
比換柜省錢,比自研省心,西門子Xcel
2025-06-25 15:07