自動化立體庫在智能制造中的應用
2018-06-16 11:32:18· 來源:AI制造
近兩年,我國汽車產(chǎn)銷增速下降并放緩,汽車行業(yè)已進入了發(fā)展的拐點。汽車制造企業(yè)必須通過產(chǎn)品創(chuàng)新和管理變革,有效利用信息技術(shù)(如PDM、ERP、SCM、MES和移動互聯(lián)等相關(guān)技術(shù))、自動化技術(shù)(如自動識別、自動化控制、工業(yè)機器人、AGV、自動化倉庫及其輸送系統(tǒng))和智能化技術(shù)(如智能裝備、智能產(chǎn)線、智能車間和機器視覺等),建立差異化競爭優(yōu)勢,從而縮短產(chǎn)品上市周期、降低成本并提升產(chǎn)品質(zhì)量,滿足個性化需求,敏捷應對市場變化,實現(xiàn)可持續(xù)發(fā)展。
近兩年,我國汽車產(chǎn)銷增速下降并放緩,汽車行業(yè)已進入了發(fā)展的拐點。汽車制造企業(yè)必須通過產(chǎn)品創(chuàng)新和管理變革,有效利用信息技術(shù)(如PDM、ERP、SCM、MES和移動互聯(lián)等相關(guān)技術(shù))、自動化技術(shù)(如自動識別、自動化控制、工業(yè)機器人、AGV、自動化倉庫及其輸送系統(tǒng))和智能化技術(shù)(如智能裝備、智能產(chǎn)線、智能車間和機器視覺等),建立差異化競爭優(yōu)勢,從而縮短產(chǎn)品上市周期、降低成本并提升產(chǎn)品質(zhì)量,滿足個性化需求,敏捷應對市場變化,實現(xiàn)可持續(xù)發(fā)展。
隨著汽車市場競爭的日趨激烈,各大汽車制造商不斷加快新車型開發(fā)并不斷降低開發(fā)成本,開發(fā)成本的降低主要集中在共用平臺、動力總成和提高生產(chǎn)制造柔性等方面。一汽轎車現(xiàn)擁有多種平臺,每個平臺下還有多種車型,因而采用了多品種小批量的柔性化生產(chǎn)方式,并在智能制造系統(tǒng)中應用智能物流自動化倉庫及其輸送系統(tǒng)。
總裝底盤合裝線柔性化工藝分析
一汽轎車總裝底盤合裝線主要由RGV小車(含軌道)、裝配高架平臺和前托盤轉(zhuǎn)交站組成,按裝配內(nèi)容分為底盤合裝區(qū)、前機艙裝配區(qū)、托盤轉(zhuǎn)交區(qū)及外分裝配區(qū)。底盤合裝區(qū)設計了3個工位,其中2個操作工位、1個預留工位。底盤合裝區(qū)的主要工作內(nèi)容是完成前、后副車架與車身的裝配(見下圖)。第一步,RGV與車身自動找正,并與底盤線保持速度同步;第二步,人工控制RGV前、后舉升臺舉升,并將副車架孔位與車身焊接螺栓對正;第三步,人工使用擰緊工具將前、后副車架緊固至車身。
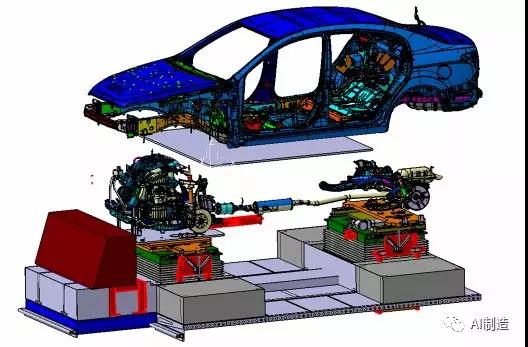
前后懸架總成底盤合裝
后導入的平臺車型懸架與車身采用螺栓連接固定,為保證合裝過程中懸架與車身的準確定位,一是需要增加導向來保證懸架與車身的準確定位,縮短作業(yè)調(diào)整時間;二是最大限度地保證車輛外傾合格。定位銷在合裝舉升過程中先與車身定位再裝配螺栓,對輔助定位的定位精度要求較高。由于前輪外傾值需通過調(diào)整前滑柱與轉(zhuǎn)向節(jié)連接螺栓實現(xiàn),因此該工作必須在舉升機上進行。在舉升機上調(diào)整后再到四輪定位進行檢測,每調(diào)整一次需要20~30min。后輪外傾值整車下線后均不可調(diào),故必須在底盤合裝時用專用托盤保證。如果前、后輪外傾值不合格將會導致整車跑偏、車輪偏磨等嚴重質(zhì)量問題,因此必須在底盤合裝工位保證前后輪外傾值。
本文對3種平臺的不同車型前、后懸架總成與車身合裝產(chǎn)品結(jié)構(gòu)進行了分析,確定底盤合裝工位需采用2種前懸架托盤和3種后懸架托盤,才可以滿足各平臺底盤合裝的精度要求。由于底盤合裝線面積有限,為保證承載多種托盤的生產(chǎn)線的柔性化生產(chǎn),需建立托盤立體庫用于托盤輸送、存儲和編組。
前、后懸架托盤立體庫方案選擇
立體庫設計要求:前、后懸架托盤能夠獨立運行并自動完成托盤進庫、出庫、編組和輸送,從而保證托盤先進、先出,防止個別托盤過度使用。同時通過查詢車身VIN碼可以追溯裝配托盤編號,從而為產(chǎn)品質(zhì)量追溯系統(tǒng)提供信息支持。
前、后托盤立體庫結(jié)構(gòu)種類很多,經(jīng)深入分析對比,初步選用了高位貨架立體庫和存儲線立體庫(見下圖)。根據(jù)總裝底盤線現(xiàn)有布局共制定3種前、后懸架托盤立體庫選擇方案。
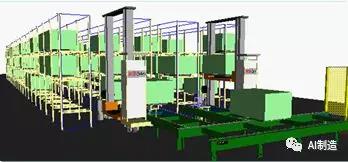
高位貨架立體庫
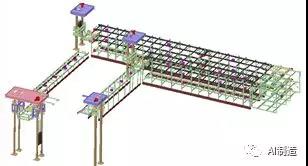
存儲線立體庫
1.方案一:地面高位貨架托盤立體庫
在地面建設高位貨架立體庫,通過有軌巷道車存取托盤。前、后懸架托盤存儲貨架通用,可提高托盤存儲量并滿足前、后懸架托盤柔性存儲。該方案設計存儲140個托盤。
2.方案二:空中存儲線托盤立體庫Ⅰ(5條存儲線)
在空中建設輸送線結(jié)構(gòu)托盤立體庫,該方式通過提升機自動轉(zhuǎn)運托盤進出庫。該方式需新增2條前懸架空中托盤存儲線及3條后懸架空中托盤存儲線。
3.方案三:空中存儲線托盤立體庫Ⅱ(4條存儲線)
在空中建設輸送線結(jié)構(gòu)托盤立體庫,該方式需新增1條前懸架空中托盤存儲線及3條后懸架空中托盤存儲線,原有平臺前懸架托盤仍用動分線返回轉(zhuǎn)運托盤。
3種方案綜合評價對比如表所示。
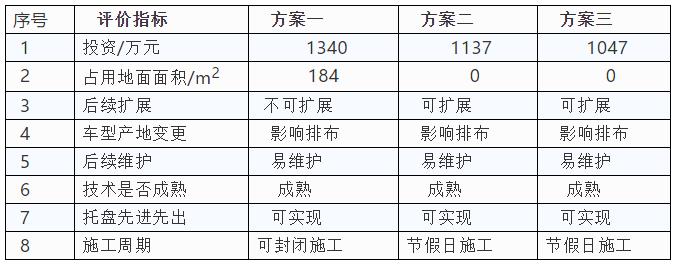
由于地面可用面積僅184m2,高位貨架立體庫后續(xù)貨架無增加空間;移動距離短,有軌巷道車發(fā)揮不了快速移動功能;高位貨架立體庫無價格優(yōu)勢等原因,故不建議采用方案一。
方案三雖比方案二設計、施工難度大,但方案三比方案二少建設一條前懸架托盤輸送線并能節(jié)省投資90萬元,故建議采用方案三。
前、后懸架托盤立體庫主要由前、后懸架托盤立體庫,生產(chǎn)聯(lián)網(wǎng)系統(tǒng),質(zhì)量追
溯系統(tǒng)和前、后懸架專用托盤組成,通過新增4臺提升機實現(xiàn)托盤自動進庫、出庫功能(見下圖)。
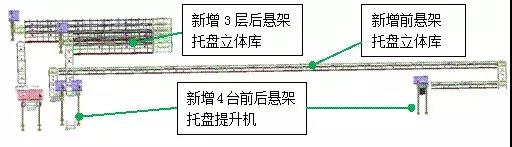
空中前后懸架托盤立體庫
托盤立體庫功能及實現(xiàn)方法
1.托盤出庫編組功能
托盤立體庫功能主要體現(xiàn)在提升機準確讀取車型信息后,托盤需立體出庫并自動編組。托盤立體庫與生產(chǎn)信息系統(tǒng)聯(lián)網(wǎng),實現(xiàn)自動讀取生產(chǎn)信息中的生產(chǎn)車序并將其轉(zhuǎn)換成托盤種類信號,提升機根據(jù)托盤信息到相應存儲線提取對應托盤。以前懸架托盤立體庫為例:如車型信息為新平臺車型,托盤提升機接收信號需到空中接取新平臺專用托盤;如車型信息為原有平臺車型,托盤提升機接收信號到地面動分線下層輸送線接取原有平臺托盤。
2.托盤入庫編組功能
以后懸架托盤入庫編組為例:后懸架托盤有3種平臺專用托盤,分別存儲到各自專用存儲線中;后懸架托盤在底盤線完成合裝裝配后并在進入托盤立體庫前,通過托盤上安裝的RFID電子標簽和線體上安裝的接近開關(guān)對托盤型號進行電子和物理雙重識別;如RFID讀寫頭與接近開關(guān)判斷的托盤型號一致,立體庫系統(tǒng)通知提升機將托盤轉(zhuǎn)運到托盤專用存儲線中,如RFID讀寫頭與接近開關(guān)判斷的托盤型號不一致,立體庫停止工作并報警,同時人工查找托盤出錯原因。托盤采用RFID和物理結(jié)構(gòu)雙重識別,提高了托盤的入庫準確率。
3.具備手動調(diào)整出庫托盤編組功能
總裝生產(chǎn)車序因突發(fā)情況變化時,需人工調(diào)整托盤出庫車序。
4.質(zhì)量追溯功能
我們搭建了立體庫質(zhì)量追溯系統(tǒng),在托盤上安裝RFID電子標簽,實現(xiàn)每個托盤編號與生產(chǎn)整車VIN碼綁定,并存儲到立體庫工控機中。由于托盤編號和整車VIN碼均具有唯一性,當檢測線檢測出前后輪外傾值不合格時,根據(jù)車身VIN碼可以在立體庫工控機中迅速查找到生產(chǎn)該車的托盤,鎖定托盤后用托盤檢具對托盤進行檢測,判斷是否是托盤問題。制作前、后懸架標準托盤并放至立體庫檢具架。當出現(xiàn)批量外傾不合格車輛時,用標準托盤進行裝配。如外傾值合格則為托盤問題,否則從產(chǎn)品質(zhì)量問題入手。
托盤立體庫方案虛擬評審
一汽轎車應用數(shù)字化仿真技術(shù)對總裝底盤柔性化生產(chǎn)準備方案進行了仿真分析,仿真過程中運動部件如果干涉,程序字體會自動變紅并提示干涉量。利用該功能,通過模擬前、后懸架托盤在立體庫中的實際工作軌跡,檢驗立體庫的通過性和干涉性,從而驗證方案的可行性。以新增托盤立體庫前懸架托盤工藝方案虛擬評審為例:在立體庫仿真環(huán)境中對設備關(guān)鍵生準點(20個關(guān)鍵評審點)進行極限參數(shù)設定。通過方案仿真評審,實現(xiàn)方案制定、交流、評審和校對可視化,提高生產(chǎn)準備的準確性和效率。
結(jié)語
一汽轎車前、后懸架托盤立體庫現(xiàn)已投入使用一年多,成功解決了多平臺車型的總裝底盤合裝柔性化生產(chǎn)的瓶頸問題,同時在裝配過程中保證了前束、外傾等關(guān)鍵參數(shù)精度,在質(zhì)量、進度和成本上也得到了有效的控制。
托盤立體庫在總裝領(lǐng)域的應用越來越成熟,也越來越廣泛,通過應用托盤立體庫技術(shù),一汽轎車積累了柔性化生產(chǎn)、底盤合裝、立體庫、虛擬仿真和質(zhì)量追溯等方面的經(jīng)驗,在現(xiàn)有工廠改造以及新工廠建設中,這些經(jīng)驗可以擴展應用到線束存儲線、車身存儲線、物料分揀和物料自動輸送等區(qū)域,可以實現(xiàn)減少人員和廠房面積、提高自動化程度和裝配質(zhì)量等方面的改善,同時達到公司降低成本、提高質(zhì)量和勞動生產(chǎn)率的目標。
隨著汽車市場競爭的日趨激烈,各大汽車制造商不斷加快新車型開發(fā)并不斷降低開發(fā)成本,開發(fā)成本的降低主要集中在共用平臺、動力總成和提高生產(chǎn)制造柔性等方面。一汽轎車現(xiàn)擁有多種平臺,每個平臺下還有多種車型,因而采用了多品種小批量的柔性化生產(chǎn)方式,并在智能制造系統(tǒng)中應用智能物流自動化倉庫及其輸送系統(tǒng)。
總裝底盤合裝線柔性化工藝分析
一汽轎車總裝底盤合裝線主要由RGV小車(含軌道)、裝配高架平臺和前托盤轉(zhuǎn)交站組成,按裝配內(nèi)容分為底盤合裝區(qū)、前機艙裝配區(qū)、托盤轉(zhuǎn)交區(qū)及外分裝配區(qū)。底盤合裝區(qū)設計了3個工位,其中2個操作工位、1個預留工位。底盤合裝區(qū)的主要工作內(nèi)容是完成前、后副車架與車身的裝配(見下圖)。第一步,RGV與車身自動找正,并與底盤線保持速度同步;第二步,人工控制RGV前、后舉升臺舉升,并將副車架孔位與車身焊接螺栓對正;第三步,人工使用擰緊工具將前、后副車架緊固至車身。
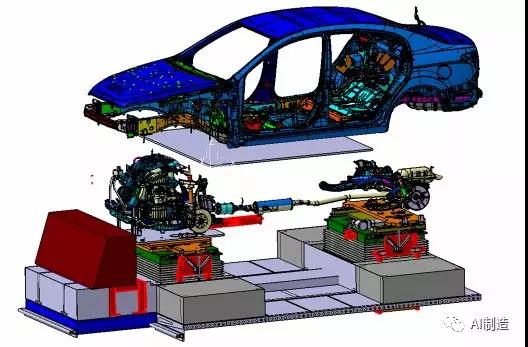
前后懸架總成底盤合裝
后導入的平臺車型懸架與車身采用螺栓連接固定,為保證合裝過程中懸架與車身的準確定位,一是需要增加導向來保證懸架與車身的準確定位,縮短作業(yè)調(diào)整時間;二是最大限度地保證車輛外傾合格。定位銷在合裝舉升過程中先與車身定位再裝配螺栓,對輔助定位的定位精度要求較高。由于前輪外傾值需通過調(diào)整前滑柱與轉(zhuǎn)向節(jié)連接螺栓實現(xiàn),因此該工作必須在舉升機上進行。在舉升機上調(diào)整后再到四輪定位進行檢測,每調(diào)整一次需要20~30min。后輪外傾值整車下線后均不可調(diào),故必須在底盤合裝時用專用托盤保證。如果前、后輪外傾值不合格將會導致整車跑偏、車輪偏磨等嚴重質(zhì)量問題,因此必須在底盤合裝工位保證前后輪外傾值。
本文對3種平臺的不同車型前、后懸架總成與車身合裝產(chǎn)品結(jié)構(gòu)進行了分析,確定底盤合裝工位需采用2種前懸架托盤和3種后懸架托盤,才可以滿足各平臺底盤合裝的精度要求。由于底盤合裝線面積有限,為保證承載多種托盤的生產(chǎn)線的柔性化生產(chǎn),需建立托盤立體庫用于托盤輸送、存儲和編組。
前、后懸架托盤立體庫方案選擇
立體庫設計要求:前、后懸架托盤能夠獨立運行并自動完成托盤進庫、出庫、編組和輸送,從而保證托盤先進、先出,防止個別托盤過度使用。同時通過查詢車身VIN碼可以追溯裝配托盤編號,從而為產(chǎn)品質(zhì)量追溯系統(tǒng)提供信息支持。
前、后托盤立體庫結(jié)構(gòu)種類很多,經(jīng)深入分析對比,初步選用了高位貨架立體庫和存儲線立體庫(見下圖)。根據(jù)總裝底盤線現(xiàn)有布局共制定3種前、后懸架托盤立體庫選擇方案。
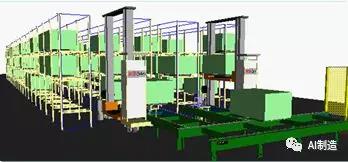
高位貨架立體庫
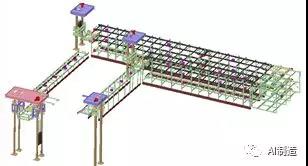
存儲線立體庫
1.方案一:地面高位貨架托盤立體庫
在地面建設高位貨架立體庫,通過有軌巷道車存取托盤。前、后懸架托盤存儲貨架通用,可提高托盤存儲量并滿足前、后懸架托盤柔性存儲。該方案設計存儲140個托盤。
2.方案二:空中存儲線托盤立體庫Ⅰ(5條存儲線)
在空中建設輸送線結(jié)構(gòu)托盤立體庫,該方式通過提升機自動轉(zhuǎn)運托盤進出庫。該方式需新增2條前懸架空中托盤存儲線及3條后懸架空中托盤存儲線。
3.方案三:空中存儲線托盤立體庫Ⅱ(4條存儲線)
在空中建設輸送線結(jié)構(gòu)托盤立體庫,該方式需新增1條前懸架空中托盤存儲線及3條后懸架空中托盤存儲線,原有平臺前懸架托盤仍用動分線返回轉(zhuǎn)運托盤。
3種方案綜合評價對比如表所示。
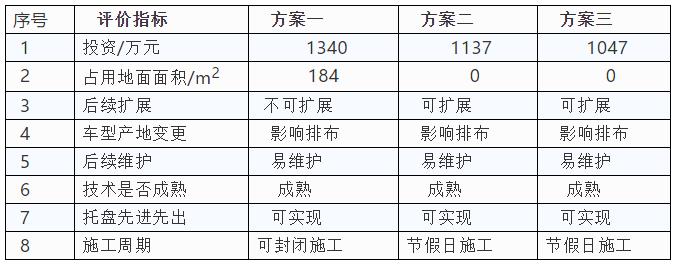
由于地面可用面積僅184m2,高位貨架立體庫后續(xù)貨架無增加空間;移動距離短,有軌巷道車發(fā)揮不了快速移動功能;高位貨架立體庫無價格優(yōu)勢等原因,故不建議采用方案一。
方案三雖比方案二設計、施工難度大,但方案三比方案二少建設一條前懸架托盤輸送線并能節(jié)省投資90萬元,故建議采用方案三。
前、后懸架托盤立體庫主要由前、后懸架托盤立體庫,生產(chǎn)聯(lián)網(wǎng)系統(tǒng),質(zhì)量追
溯系統(tǒng)和前、后懸架專用托盤組成,通過新增4臺提升機實現(xiàn)托盤自動進庫、出庫功能(見下圖)。
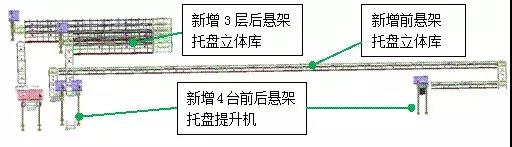
空中前后懸架托盤立體庫
托盤立體庫功能及實現(xiàn)方法
1.托盤出庫編組功能
托盤立體庫功能主要體現(xiàn)在提升機準確讀取車型信息后,托盤需立體出庫并自動編組。托盤立體庫與生產(chǎn)信息系統(tǒng)聯(lián)網(wǎng),實現(xiàn)自動讀取生產(chǎn)信息中的生產(chǎn)車序并將其轉(zhuǎn)換成托盤種類信號,提升機根據(jù)托盤信息到相應存儲線提取對應托盤。以前懸架托盤立體庫為例:如車型信息為新平臺車型,托盤提升機接收信號需到空中接取新平臺專用托盤;如車型信息為原有平臺車型,托盤提升機接收信號到地面動分線下層輸送線接取原有平臺托盤。
2.托盤入庫編組功能
以后懸架托盤入庫編組為例:后懸架托盤有3種平臺專用托盤,分別存儲到各自專用存儲線中;后懸架托盤在底盤線完成合裝裝配后并在進入托盤立體庫前,通過托盤上安裝的RFID電子標簽和線體上安裝的接近開關(guān)對托盤型號進行電子和物理雙重識別;如RFID讀寫頭與接近開關(guān)判斷的托盤型號一致,立體庫系統(tǒng)通知提升機將托盤轉(zhuǎn)運到托盤專用存儲線中,如RFID讀寫頭與接近開關(guān)判斷的托盤型號不一致,立體庫停止工作并報警,同時人工查找托盤出錯原因。托盤采用RFID和物理結(jié)構(gòu)雙重識別,提高了托盤的入庫準確率。
3.具備手動調(diào)整出庫托盤編組功能
總裝生產(chǎn)車序因突發(fā)情況變化時,需人工調(diào)整托盤出庫車序。
4.質(zhì)量追溯功能
我們搭建了立體庫質(zhì)量追溯系統(tǒng),在托盤上安裝RFID電子標簽,實現(xiàn)每個托盤編號與生產(chǎn)整車VIN碼綁定,并存儲到立體庫工控機中。由于托盤編號和整車VIN碼均具有唯一性,當檢測線檢測出前后輪外傾值不合格時,根據(jù)車身VIN碼可以在立體庫工控機中迅速查找到生產(chǎn)該車的托盤,鎖定托盤后用托盤檢具對托盤進行檢測,判斷是否是托盤問題。制作前、后懸架標準托盤并放至立體庫檢具架。當出現(xiàn)批量外傾不合格車輛時,用標準托盤進行裝配。如外傾值合格則為托盤問題,否則從產(chǎn)品質(zhì)量問題入手。
托盤立體庫方案虛擬評審
一汽轎車應用數(shù)字化仿真技術(shù)對總裝底盤柔性化生產(chǎn)準備方案進行了仿真分析,仿真過程中運動部件如果干涉,程序字體會自動變紅并提示干涉量。利用該功能,通過模擬前、后懸架托盤在立體庫中的實際工作軌跡,檢驗立體庫的通過性和干涉性,從而驗證方案的可行性。以新增托盤立體庫前懸架托盤工藝方案虛擬評審為例:在立體庫仿真環(huán)境中對設備關(guān)鍵生準點(20個關(guān)鍵評審點)進行極限參數(shù)設定。通過方案仿真評審,實現(xiàn)方案制定、交流、評審和校對可視化,提高生產(chǎn)準備的準確性和效率。
結(jié)語
一汽轎車前、后懸架托盤立體庫現(xiàn)已投入使用一年多,成功解決了多平臺車型的總裝底盤合裝柔性化生產(chǎn)的瓶頸問題,同時在裝配過程中保證了前束、外傾等關(guān)鍵參數(shù)精度,在質(zhì)量、進度和成本上也得到了有效的控制。
托盤立體庫在總裝領(lǐng)域的應用越來越成熟,也越來越廣泛,通過應用托盤立體庫技術(shù),一汽轎車積累了柔性化生產(chǎn)、底盤合裝、立體庫、虛擬仿真和質(zhì)量追溯等方面的經(jīng)驗,在現(xiàn)有工廠改造以及新工廠建設中,這些經(jīng)驗可以擴展應用到線束存儲線、車身存儲線、物料分揀和物料自動輸送等區(qū)域,可以實現(xiàn)減少人員和廠房面積、提高自動化程度和裝配質(zhì)量等方面的改善,同時達到公司降低成本、提高質(zhì)量和勞動生產(chǎn)率的目標。
- 下一篇:沃克斯豪爾展示新款概念車 采用全新設計風格
- 上一篇:汽車儀表盤UI設計
編輯推薦
最新資訊
-
跨越速運憑什么“圈粉”萬千客戶?“
2025-07-01 14:42
-
數(shù)智破局啟新篇?生態(tài)共生再啟程 —
2025-06-27 20:13
-
助力汽車零部件產(chǎn)線智能化升級,西門
2025-06-27 13:59
-
BBA集體轉(zhuǎn)向!放棄全面電動化
2025-06-26 17:32
-
比換柜省錢,比自研省心,西門子Xcel
2025-06-25 15:07