聚焦汽車輕量化技術(shù)全方位解析
2018-06-11 11:14:49· 來源:中汽創(chuàng)新創(chuàng)業(yè)中心
隨著新能源汽車發(fā)展,動力電池技術(shù)不斷飛躍,電動汽車續(xù)航持續(xù)提升,電池能量密度不斷攀升,同時,補貼下降又對動力電池成本要求更加嚴格。隨著后補貼時代能耗考核的不斷加嚴,新能源車行業(yè)不應(yīng)僅把眼光放在電池密度上,更該結(jié)合車身輕量化,將更多注意力放在減輕能耗方面,我們相信能耗將成為后補貼時代政策導(dǎo)向和整車企業(yè)最重視的關(guān)鍵指標。
隨著新能源汽車發(fā)展,動力電池技術(shù)不斷飛躍,電動汽車續(xù)航持續(xù)提升,電池能量密度不斷攀升,同時,補貼下降又對動力電池成本要求更加嚴格。隨著后補貼時代能耗考核的不斷加嚴,新能源車行業(yè)不應(yīng)僅把眼光放在電池密度上,更該結(jié)合車身輕量化,將更多注意力放在減輕能耗方面,我們相信能耗將成為后補貼時代政策導(dǎo)向和整車企業(yè)最重視的關(guān)鍵指標。本文將對汽車輕量化技術(shù)做個統(tǒng)攬:
汽車的輕量化的定義
就是在保證汽車的強度和安全性能的前提下,盡可能地降低汽車的整備質(zhì)量。汽車輕量化有以下優(yōu)點:
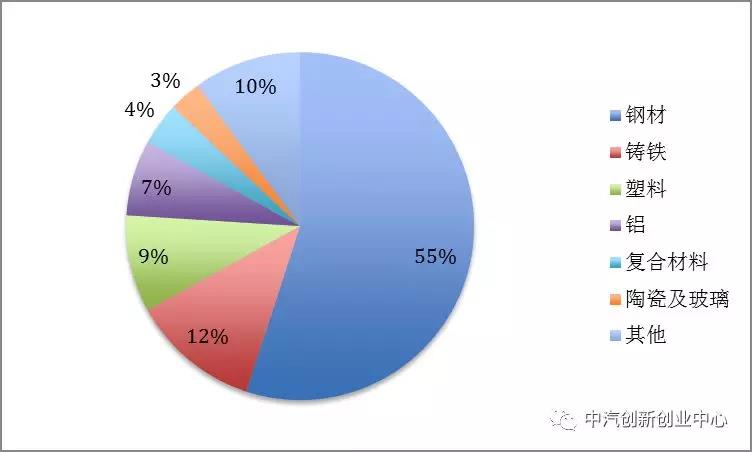
圖:汽車材料使用占比
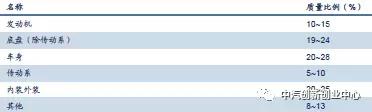
圖:汽車各部件重量占比
汽車輕量化作為一個系統(tǒng)化的工程,并不是簡單地針對某個零件的單獨減重,局部重量的變化在很大程度上會影響汽車的其他部位,因此汽車輕量化是指在汽車制造過程中集設(shè)計、制造、材料技術(shù)等一起的系統(tǒng)性工程。在對汽車進行輕量化設(shè)計時,主要有以下三個途徑:

一、材料輕量化
材料輕量化即通過使用輕量化材料來達到減輕新能源汽車質(zhì)量的目的。目前,應(yīng)用于新能源汽車的輕量化材料主要是有高強度鋼、鋁合金、鎂合金、碳纖維等。例如,奇瑞新能源公司推出的新一代純電動微型車小螞蟻(代號eQ1)采用了“全鋁空間結(jié)構(gòu)+全復(fù)合材料外覆蓋件”的組合形式,車身采用高強度鎂鋁合金應(yīng)用比高達93%以上,全鋁車身較傳統(tǒng)汽車減重40%的同時車身剛性提高了60%以上;大眾寶來通過更改材料減輕重量104.2kg,占總減重的41%。零件小型化后減輕重量144.1kg,占總減重的57%;
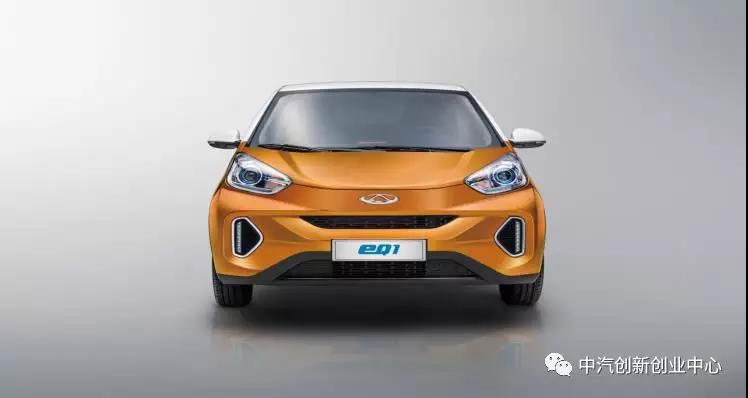
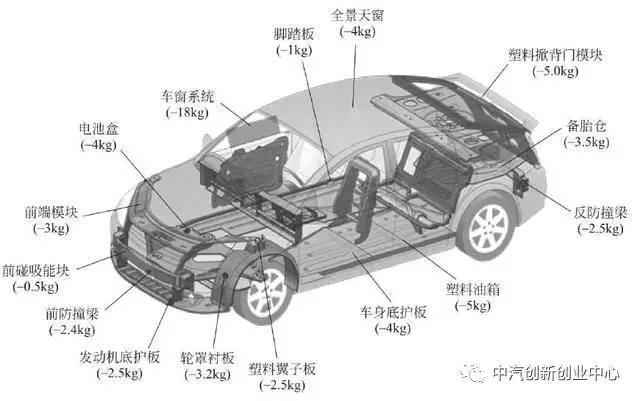
圖:汽車外飾件采用輕量化材料減重途徑

圖:寶來汽車減重途徑
二、結(jié)構(gòu)輕量化
輕量化的另一手段就是在汽車零部件概念設(shè)計、初始結(jié)構(gòu)設(shè)計、產(chǎn)品工程設(shè)計及樣車制造過程中做相關(guān)結(jié)構(gòu)的分析和優(yōu)化,或去除零部件的冗余部分、或減少搭接(如花邊形設(shè)計)、或改變結(jié)構(gòu),在不影響車身強度和安全性能的基礎(chǔ)下盡量減少對零件的使用,有用則保留,無用則放棄,使車內(nèi)布局達到最佳的效果,以實現(xiàn)對汽車零部件的精簡化、整體化和輕質(zhì)化。
結(jié)構(gòu)輕量化包括車身結(jié)構(gòu)優(yōu)化設(shè)計和汽車實體結(jié)構(gòu)布局設(shè)計這兩種方式,主要運用ANSYS、UG、CAD、CATIA等軟件,手段有形貌優(yōu)化、尺寸優(yōu)化、拓撲優(yōu)化(包括多種輕量化材料的匹配、零部件的優(yōu)化分塊)、有限元分析和模塊化集成設(shè)計等。
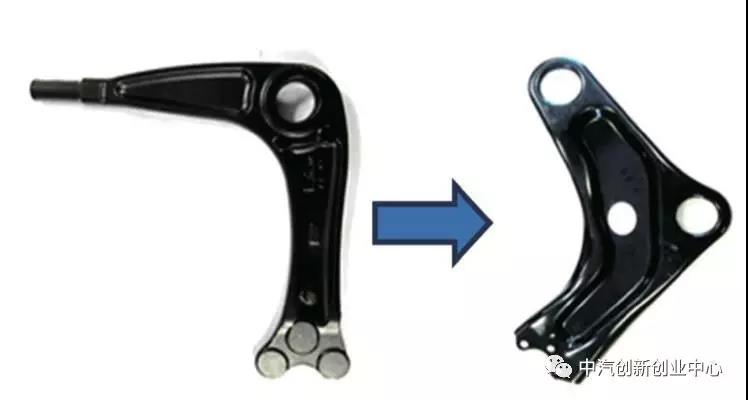
圖:三角臂結(jié)構(gòu)變更
例如神龍汽車公司將三角臂結(jié)構(gòu)變更之后(三角臂是在汽車行駛于不平路面時起平衡支撐作用的結(jié)構(gòu)件),質(zhì)量減輕近50%,制造能耗降低65%。
三、制造工藝輕量化
為進一步達到減重降本的目的,除了開發(fā)應(yīng)用輕量化材料外,一系列適應(yīng)這些新材料的先進工藝,如熱成型、激光焊接、液壓成型、差厚軋制、徑向鍛造、半固態(tài)成型等應(yīng)運而生。
例如,熱成型技術(shù)是基于高強鋼冷沖壓成型中普遍存在塑性范圍窄、易開裂、回彈大等問題而發(fā)展起來的板材成形新技術(shù),通常在900~950°C的奧氏體狀態(tài)下沖壓,并在模具內(nèi)淬火冷卻,汽車上應(yīng)用熱成型技術(shù)的典型鋼種是22MnB5,抗拉強度可達1500MPa。
激光拼焊是指將幾個小零件通過激光焊接集成到一個大的毛坯,進而沖壓成形成所需整體部件。使用激光拼焊板可使模具的數(shù)量和后續(xù)生產(chǎn)工序減少,從而降低了生產(chǎn)成本,并提高了零部件的質(zhì)量、優(yōu)化了零件結(jié)構(gòu),充分發(fā)揮了不同強度、不同厚度板材的特性,成為汽車輕化降低零件數(shù)量、保證汽車安全、優(yōu)化設(shè)計和改進制造技術(shù)的重要手段。
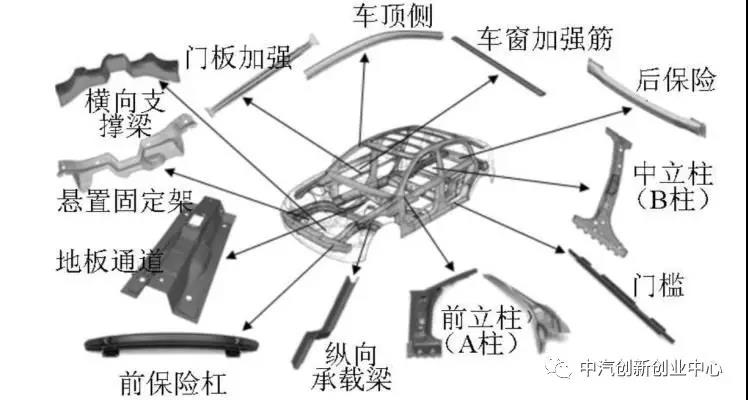
圖:熱成型在汽車零件上的典型應(yīng)用
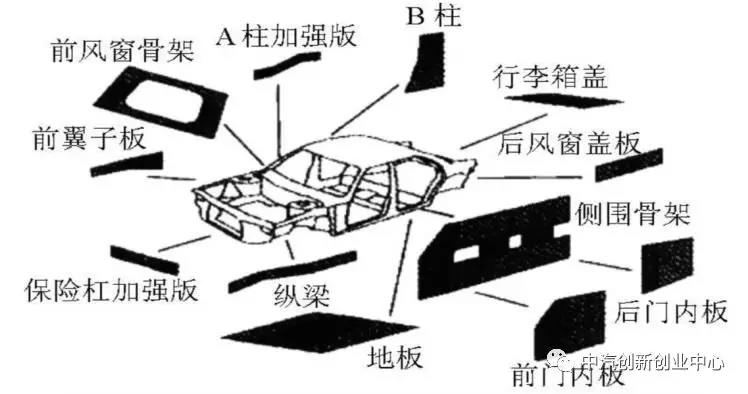
圖:激光拼焊應(yīng)用的典型零件
根據(jù)2017年新能源汽車目錄列表中的汽車續(xù)航里程情況計算,乘用車平均續(xù)航里程為192km,新能源客車平均續(xù)航里程為238km,專用車為219km??紤]到測試數(shù)據(jù)一般要優(yōu)于實際數(shù)據(jù),所以我們認為新能源乘用車的平均續(xù)航能力要小于192km,與中央希望達到的250km以上的續(xù)航能力相差很遠(根據(jù)補貼新政,中央將扶持250km以上乘用車,其中300km以上的將大力扶持)。對于那些續(xù)航能力在200km左右的車型來說,他們將寄希望于未來能夠短時間內(nèi)提升續(xù)航里程。那對于那些續(xù)航里程在200km左右的車型來說,用汽車輕量化的方法來達標是否可行呢?
答案是可行的。根據(jù)《論汽車輕量化》雜志報道,奇瑞汽車實車測試數(shù)據(jù)顯示,電動汽車減重10%,平均續(xù)航能力增加5%-8%。對于那些續(xù)航能力在200km的汽車來說,在不改變汽車設(shè)計以及電池性能的條件下,將車體重量減少20%左右就可以達標。
綜上所述,提升鋰電池性能目前處于一個瓶頸期,鋰電池性能在短時間內(nèi)突破瓶頸可能性不大;增加鋰電池數(shù)量也將增加汽車的重量以及成本,對于續(xù)航里程沒有明顯的提升;所以,最可行的、而且是最快速的方法就是汽車輕量化。
汽車輕量化材料市場前景廣闊
本報告主要關(guān)注新能源汽車補貼新政落地后,對輕量化材料市場的影響。在接下來的篇幅中將重點討論新材料在汽車輕量化的地位以及發(fā)展情況。
一、汽車輕量化材料之碳纖維
概述
碳纖維起源可以追溯到1860年,首先由英國人發(fā)明。由于其抗高溫能力不如鎢絲,所以無法成為電燈泡的發(fā)光材料,隨后碳纖維的研究進入低谷。直到20世紀50年代,碳纖維的研究被美國人在導(dǎo)彈研究領(lǐng)域再一次推上舞臺。碳纖維研究的里程碑發(fā)生在1959年,日本人近藤昭男發(fā)明了聚丙烯晴(PAN)基碳纖維。PAN碳纖維具有工藝成熟,性能良好和低成本等優(yōu)勢,在目前統(tǒng)計情況來看,PAN碳纖維占全部產(chǎn)量的90%以上。在今天的材料領(lǐng)域,如果不特指的話,碳纖維一般都是指PAN碳纖維。
碳纖維是有機纖維經(jīng)過碳化和石墨化處理得到的微晶石墨材料,其微觀結(jié)構(gòu)類似人造石墨,是亂層石墨結(jié)構(gòu)。其含碳量高于90%,如果含碳量高于99%則稱為石墨纖維。碳纖維軸向強度和模量高,耐疲勞性好,比熱和導(dǎo)電性質(zhì)介于金屬和非金屬之間,熱膨脹系數(shù)小,耐腐蝕,密度低。但是由于碳纖維耐沖擊性較弱,容易發(fā)生氧化,所以一般需要進行表面處理。
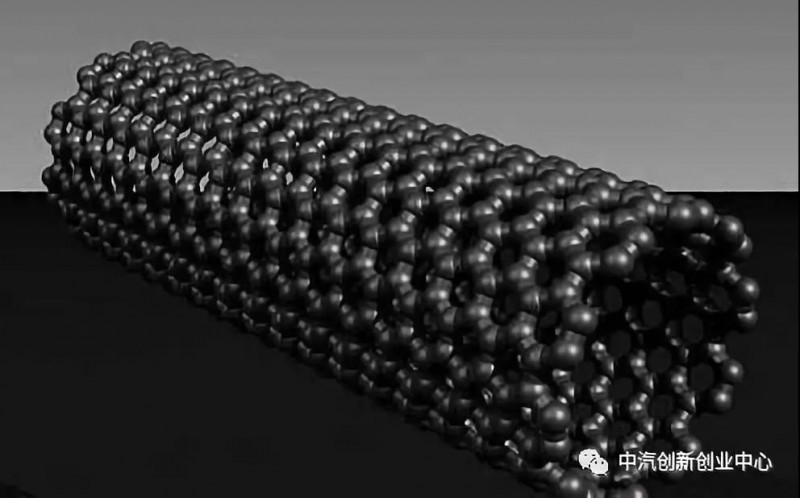
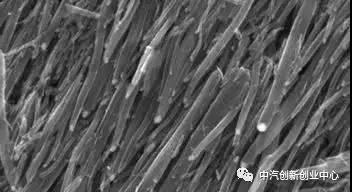
碳纖維的生產(chǎn)通常使用一些含碳的有機纖維(尼龍、腈綸、人造絲等)做原料,將有機纖維跟塑料樹脂結(jié)合一起,在惰性氣體環(huán)境中高壓高熱碳化而成。碳纖維可以通過高分子有機纖維碳化或者低分子烴類氣相熱解來制備。目前世界上生產(chǎn)銷售的碳纖維大部分是用PAN纖維固相碳化而來。
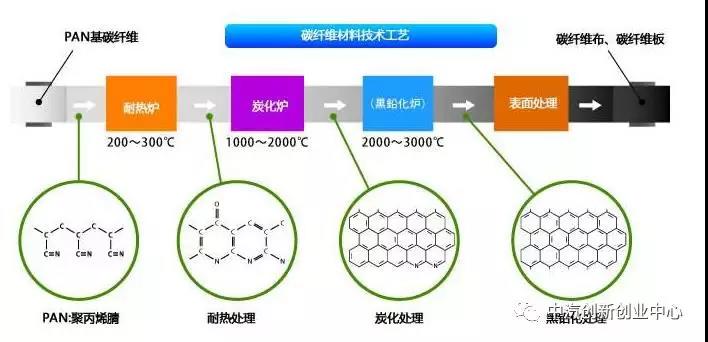
圖:碳纖維生產(chǎn)方式
目前,碳纖維的主要生產(chǎn)國家有美國、日本等。日本是世界上碳纖維產(chǎn)能最大的國家,并且控制了高端碳纖維的生產(chǎn)。日本東麗公里在PAN碳纖維研制生產(chǎn)中充當(dāng)急先鋒,美國的Hexcel公司緊隨其后。在小絲束碳纖維生產(chǎn)層面,除了東麗和Hexcel以外,日本東邦人造絲,日本三菱人造絲和美國Cytec公司都是在碳纖維生產(chǎn)制造上有一席之地,但是技術(shù)上還是與日本東麗有一定差距。在大絲束碳纖維生產(chǎn)層面,美國的Zoltek,Aldila,德國的SGLcarbon也有一定的話語權(quán)??偟膩碚f,美國在大絲束碳纖維上有一定優(yōu)勢,日本則在小絲束上領(lǐng)先。
優(yōu)缺點及應(yīng)用
碳纖維具有多種優(yōu)異的性質(zhì),具有密度小、強度高、熱膨脹系數(shù)小、導(dǎo)熱性好、耐腐蝕性好、耐磨性好等特性,使用碳纖維復(fù)合材料代替?zhèn)鹘y(tǒng)的汽車材料,有以下幾個優(yōu)點:
第一,碳纖維應(yīng)用于汽車后,有利于實現(xiàn)汽車輕量化,提升汽車的節(jié)能、加速、制動性能。
第二,車身輕量化可以使整車的重心下移,提升了汽車操縱穩(wěn)定性,車輛的運行將更加安全、穩(wěn)定。碳纖維復(fù)合材料具有極佳的能量吸收率,碰撞吸能能力是鋼的六到七倍、鋁的三到四倍,碰撞時產(chǎn)生的碎片較少,進一步保證了汽車的安全性。
第三,碳纖維復(fù)合材料具有更高的震動阻尼,輕合金需要9秒才能停止震動,碳纖維復(fù)合材料2秒就能停止,故碳纖維應(yīng)用在汽車上,對于整車NVH(噪聲、振動與聲振粗糙度)的提升貢獻同樣很大,會大幅增強汽車行駛的舒適性。
第四,碳纖維復(fù)合材料具有更高的疲勞強度,鋼和鋁的疲勞強度是抗拉強度的30-50%,而碳纖維復(fù)合材料可達70-80%,因此汽車上應(yīng)用碳纖維復(fù)合材料對于材料疲勞可靠性有較大提升。

目前,碳纖維目前已經(jīng)在高端車、超跑、賽車、改裝車以及少量的電動車上開始大量。在汽車零部件中的應(yīng)用,碳纖維主要分布在汽車車身、內(nèi)外飾、底盤系統(tǒng)、動力系統(tǒng)等。

碳纖維在汽車車身、汽車輪轂、汽車剎車、傳動系統(tǒng)以及汽車內(nèi)飾、門窗等多個汽車組件上都有應(yīng)用。
如寶馬在多個系列的車型中使用了碳纖維,例如,在全新寶馬7系的車體框架中,碳纖維被用于加固車頂橫梁結(jié)構(gòu)、B柱、C柱、底部側(cè)圍、中央通道和后部支撐,這些部件以往只能用高強度鋼材打造,換成鋼和碳纖維混合結(jié)構(gòu)后重量直接減輕50%以上,而且強度是鋼的5倍以上,最終7系比上一代減輕了130kg重量;寶馬i3/i8Life模塊由全碳纖維材質(zhì)打造,該結(jié)構(gòu)免去了中央通道對內(nèi)部空間的占用,讓乘客擁有更多空間,同時也抵消了高壓蓄電池給車身帶來的重量,還降低了汽車的重心;保時捷911Turbo采用碳纖維輪轂,比鋁合金減重20%,強度提高了20%,且減輕簧下重量,讓懸掛反應(yīng)靈敏度增加、減少轉(zhuǎn)動慣性以及縮短剎車距離。
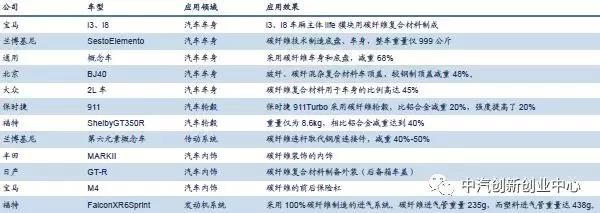
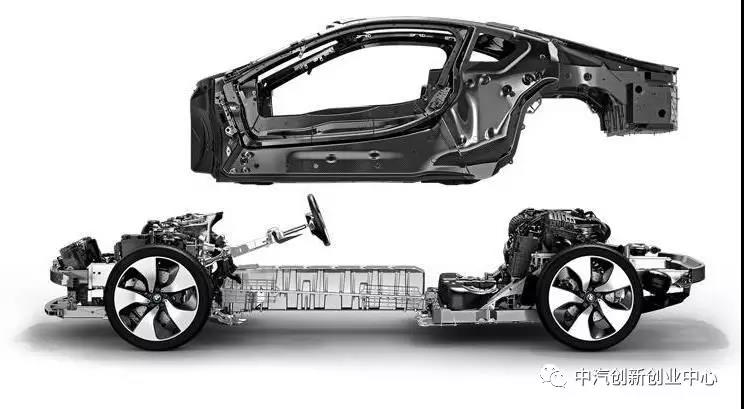
圖:寶馬i8碳纖維車身
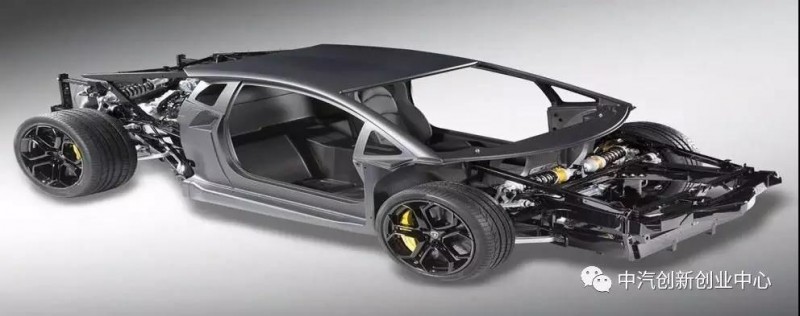
圖:蘭博基尼Aventador碳纖維車身
目前,碳纖維在民用領(lǐng)域的應(yīng)用依然不多,主要集中應(yīng)用在一些賽車和小批量高檔轎車上,制約我國碳纖維及其復(fù)合材料業(yè)發(fā)展的問題在于碳纖維原絲質(zhì)量差、價格高、應(yīng)用基礎(chǔ)研究薄弱等。
碳纖維是脆性材料,它的高強度只限于軸向,徑向強度較低。如果受力過大,碳纖維會直接斷裂。目前對于碳纖維材料在碰撞下的性能仍然了解不充分,損壞零部件的檢測與維修技術(shù)還不成熟,因此損壞后基本無法修復(fù)。國產(chǎn)原絲不僅強度低,而且CV(強度離散系數(shù))值大,很難生產(chǎn)出質(zhì)量穩(wěn)定的優(yōu)質(zhì)碳纖維。
另外,高昂的成本,使得碳纖維目前只能局限在部分超豪華車型上,難以普及。
例如,采用T300碳絲+環(huán)氧樹脂代替SMC+ABS制造的某車型車身頂蓋,質(zhì)量由9.7kg減到5kg,但單件產(chǎn)品成本從三百多元翻了近五番;寶馬i3電動車銷量不佳部分原因是過度使用了碳纖維使得車輛太貴,一輛寶馬i3價格大致為5.5萬歐元;雷克薩斯推出的全碳纖維車身和底盤的LFA,售價高達30萬-40萬英鎊。
因此,要促進碳纖維復(fù)合材料在汽車上的廣泛應(yīng)用,必須解決以下問題:
第一,降低碳纖維成本。每千克碳纖維耗費大概20美元,普通鋼只1美元左右。隨著生產(chǎn)工藝技術(shù)的重大突破,每千克碳纖維預(yù)計可以降到10美元左右,這將為碳纖維增強復(fù)合材料在汽車上的應(yīng)用開辟廣闊前景,碳纖維復(fù)合材料將大規(guī)模取代現(xiàn)用的工程材料。
第二,加強碳纖維及其復(fù)合材料的應(yīng)用技術(shù)研究。主要包括碳纖維及其復(fù)合材料結(jié)構(gòu)設(shè)計技術(shù)的研究、碳纖維及其復(fù)合材料成型工藝、性能表征和質(zhì)量控制與保證、碳纖維及其復(fù)合材料相應(yīng)標準的建立與完善、碳纖維復(fù)合材料的修補技術(shù)等。
二、汽車輕量化材料之玻璃纖維
概況
玻璃纖維(GFRP)是纖維狀的玻璃,化學(xué)組成主要是二氧化硅(SiO2)、三氧化二硼(B2O3)、氧化鈣(CaO)、三氧化二鋁(Al2O3)等。玻璃纖維作為一種性能優(yōu)異的無機非金屬材料,是復(fù)合材料中使用量最大的一種增強材料,有著機械強度高、吸收沖擊能亮大、耐熱性強等優(yōu)點,能提高基體材料機械強度、彈性模量等力學(xué)性能。
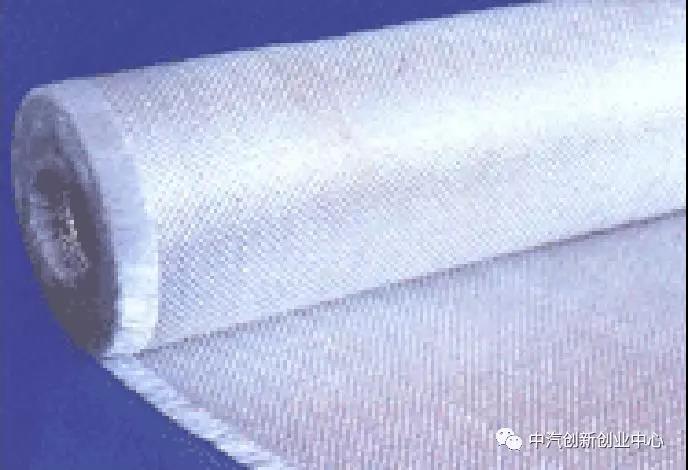
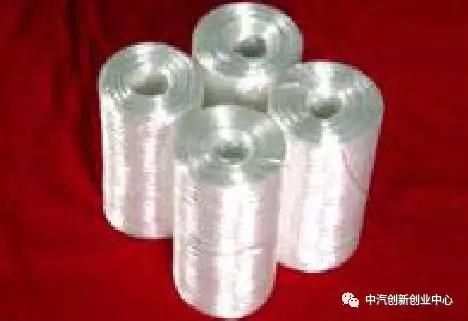
玻璃纖維分類方法很多,一般可以從成分,直徑,纖維外觀和纖維特性等方面分類。

玻璃纖維具有足夠的剛性,耐沖擊性能良好,能滿足車身安全的基本要求;且具有足夠的硬度及韌性,使得車身受到輕微碰撞時,能卸除部分沖擊力,或產(chǎn)生回彈,對比鐵質(zhì)來說其安全系數(shù)更高;其抗刮能力強,耐腐蝕,抗老化能力表現(xiàn)也非常優(yōu)秀。另外,玻璃纖維可塑性強,易成型;可后期拼接,也可與其他材質(zhì)的部件拼接。
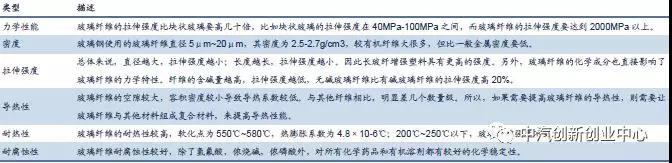
我國是一個玻璃纖維產(chǎn)業(yè)大國,2016年全球玻纖產(chǎn)量達到約625萬噸,我國玻纖產(chǎn)量約為363萬噸,占全球玻纖產(chǎn)量的58%,產(chǎn)量位居全球第一。但在生產(chǎn)技術(shù)、產(chǎn)品附加值、行業(yè)標準等方面,國內(nèi)玻纖產(chǎn)業(yè)與國外存在較明顯差距,尚未達到玻璃纖維強國的水平。

早在1955年,歐洲就開始在汽車上使用GFRP,曾在STM-Ⅲ型車上試用GFRP板。1970年,日本就用GFRP制造汽車車輪裝飾罩。1971年日本鈴木公司用GFRP制造發(fā)動機罩、翼子板、保險杠等。1974年英國厄夫公司試制成功了GFRP駕駛室。1979年美國克萊斯勒公司用GFRP制造轎車車身尾部零件。1980年美國通用公司用GFRP制造客貨兩用車車門,該公司用GFRP制造的駕駛室于1983年正式用于“將軍”型載貨車上。
此外,GFRP在國內(nèi)的汽車企業(yè)中也得到了廣泛的應(yīng)用。北京251廠的BJ121GFRP駕駛室的成功研制,為GFRP在國內(nèi)汽車應(yīng)用上奠定了堅實基礎(chǔ),隨后第一汽車制造廠成功研制GFRP發(fā)動機罩及平頭可翻式駕駛室。受國產(chǎn)汽車工業(yè)的影響,較多應(yīng)用在國內(nèi)汽車工業(yè)是在80年代后期。1986年山東武城旅行車廠成功研制了BWC-6440全GFRP車身旅行車,該廠研制的BWC6470、BWC6480全GFRP車身旅行車1992年通過了3萬公里可靠性定型試驗和碰撞試驗。2013年廣東省中山大學(xué)研究院與東莞雅日玻璃鋼有限公司成功研制了全GFRP車身電動巴士。
長玻纖增強材料
按照塑料粒子的長度和玻璃纖維的長度,有短玻纖增強塑料與長玻纖增強塑料之分。長玻纖一般指長度超過10mm的玻纖,與短玻纖相比,長玻纖纖維長度較長,力學(xué)性能更佳,且剛度和比強度高,抗沖擊性能好,耐疲勞性能優(yōu)良,特別適合汽車部件的應(yīng)用;另外,長玻纖耐蠕變性能提高,尺寸穩(wěn)定性好,部件成型精度高,成型過程中纖維可以在成型模具中相對移動,纖維損傷小。目前,LFT已在汽車防撞梁、前端模塊、儀表盤骨架、車門中間承載板、電瓶箱、座椅骨架板、備胎倉以及車底部護板等結(jié)構(gòu)件和半結(jié)構(gòu)件中得到廣泛應(yīng)用。
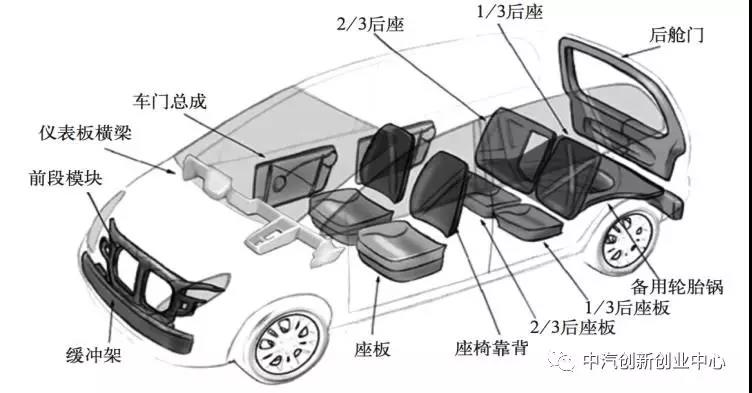
圖:長玻纖增強材料在汽車零部件中的應(yīng)用
玻璃纖維氈增強熱塑性復(fù)合材料
玻璃纖維氈增強熱塑性復(fù)合材料簡稱GMT,是目前國際上極為活躍的復(fù)合材料開發(fā)品種。這是一種以熱塑性樹脂為基體,以玻璃纖維氈為增強骨架的新穎、節(jié)能、輕質(zhì)的復(fù)合材料,一般可以生產(chǎn)出片材半成品,然后直接加工成所需形狀的產(chǎn)品,纖維可以是短切玻璃纖維或連續(xù)的玻璃纖維氈,熱塑性樹脂可以是通用塑料,工程塑料或高性能塑料。GMT產(chǎn)品具有很多優(yōu)異的性能,如耐化學(xué)性好,強度/重量比大,在高、低溫環(huán)境中的抗沖擊性能優(yōu)良。GMT工藝生產(chǎn)的輕質(zhì)高強度的GMT片材,通過結(jié)構(gòu)優(yōu)化設(shè)計,可取代部分金屬材料,獲得顯著的減重效果,而且節(jié)省模具費用,并有利于多種零件組合,形成模塊化生產(chǎn)方式。用GMT片材可較原金屬件減重30~80%,能耗僅為鋼制品的60~80%,鋁制品的35~50%。
GMT片材在汽車工業(yè)中的應(yīng)用,已達40多種,主要有座椅骨架、保險杠、儀表板、發(fā)動機罩、電池托架、腳踏板、前端、地板、護板、后牽門、車頂棚、行李托架、遮陽板、備用輪胎架等部件。國內(nèi)已經(jīng)投產(chǎn)的AuidA6以及A4車已采用GMT材料,但尚未實現(xiàn)國產(chǎn)化。
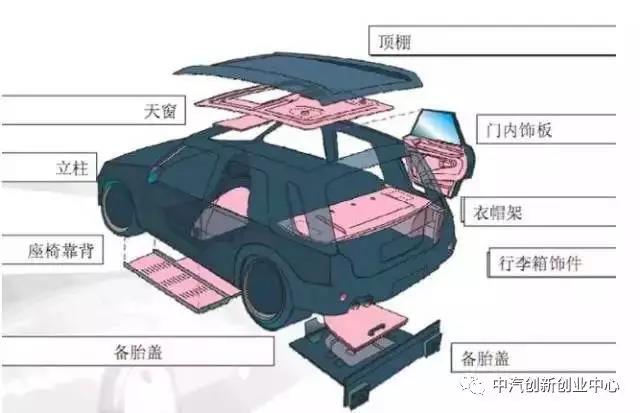
圖:GMT片材在在汽車零部件中的應(yīng)用
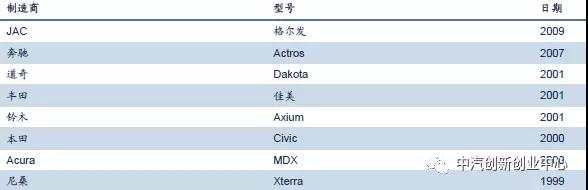
圖:GMT片材內(nèi)飾頂?shù)膽?yīng)用舉例
玻璃纖維增強復(fù)合材料具有優(yōu)異的綜合性能,是當(dāng)今塑料復(fù)合材料最重要的發(fā)展趨勢之一,在汽車上的應(yīng)用前景很可觀。玻璃纖維已開始在歐洲和美國的汽車制造業(yè)中廣泛使用,但在國產(chǎn)汽車上還未得到廣泛的應(yīng)用。
未來,車用玻纖材料需要著力從以下幾個方面進行改進:
第一,降低成本,擴大應(yīng)用領(lǐng)域。價格是制約汽車車身新材料應(yīng)用的重要因素,只有大幅度降低新材料的制造出成本,才可能使諸多新材料更容易被主機廠接受并加入批量生產(chǎn)。
第二,玻璃纖維具有很好的可設(shè)計性,但其與金屬制件的連接在國內(nèi)仍是制約其發(fā)展的瓶頸,未來需要著力提高玻纖與其他的材料的結(jié)合性。
第三,加快玻纖材料的開發(fā)和成型技術(shù)的研究,包括擴大增強纖維和基體的種類,開發(fā)先進的高效節(jié)能的成型技術(shù)和相應(yīng)的回收技術(shù),擴大器在汽車輕量化中的應(yīng)用,推動中國汽車輕量化的進展。
三、汽車輕量化材料之鎂合金
優(yōu)缺點
鎂合金是以鎂為原料的高性能輕型結(jié)構(gòu)材料,比重與塑料相近,剛度、強度不亞于鋁,具有較強的抗震、防電磁、導(dǎo)熱、導(dǎo)電等優(yōu)異性能,并且可以全回收無污染。具體來說,鎂合金在汽車生產(chǎn)中有以下幾個優(yōu)點:
第一,鎂合金密度小但強度高、剛性好。在現(xiàn)有工程用金屬中,鎂的密度最小,是鋼的1/5,鋅的1/4,鋁的2/3。普通鑄造鎂合金和鑄造鋁合金的剛度相同,因而其比強度明顯高于鋁合金。鎂合金的剛度隨厚度的增加而成立方比增加,故而鎂合金制造剛性好的性能對整體構(gòu)件的設(shè)計十分有利。
第二,鎂合金的韌性好、減震性強。鎂合金在受外力作用時,易產(chǎn)生較大的變形。但當(dāng)受沖擊載荷時,吸收的能量是鋁的1.5倍,因此,很適合應(yīng)于受沖擊的零件—車輪;鎂合金有很高的阻尼容量,是避免由于振動、噪音而引起工人疲勞等場合的理想材料。
第三,鎂合金的熱容量低、凝固速度快、壓鑄性能好。鎂合金是良好的壓鑄材料,它具有很好的流動性和快速凝固率,能生產(chǎn)表面精細、棱角清晰的零件,并能防止過量收縮以保證尺寸公差。由于鎂合金熱容量低,與生產(chǎn)同樣的鋁合金鑄件相比,其生產(chǎn)效率高40%~50%,且鑄件尺寸穩(wěn)定,精度高,表面光潔度好。
第四,鎂合金具有優(yōu)良的切削加工性。鎂合金是所有常用金屬中較容易加工的材料。加工時可采用較高的切削速度和廉價的切削刀具,工具消耗低。而且不需要磨削和拋光,用切削液就可以得到十分光潔的表面。
第五,鎂合金的儲量豐富,占地球地殼2.7%,開采壽命分別為鐵和鋁的20和4倍,我們國家占有世界70%的儲量。另外我國白云石儲備超過70億噸,而白云石是制造鎂合金的基礎(chǔ)原材料。
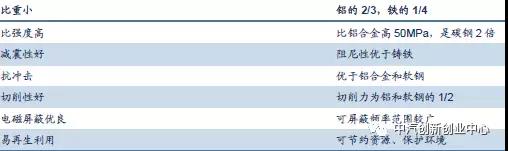
易燃燒和耐腐蝕性差是鎂合金普及的“攔路虎”。
鎂元素與氧元素具有極大的親和力,其在高溫下甚至還處于固態(tài)的情況下,就很容易與空氣中的氧氣發(fā)生反應(yīng),放出大量熱,且生成的氧化鎂導(dǎo)熱性能不好,熱量不能及時發(fā)散,繼而促進了氧化反應(yīng)的進一步進行,形成了惡性循環(huán),而且氧化鎂疏松多孔,不能有效阻隔空氣中氧的侵入。鎂合金加工過程中,容易發(fā)生燃燒和爆炸,存在安全生產(chǎn)問題,生產(chǎn)現(xiàn)場需要嚴格的管理來保證安全生產(chǎn)。
鎂合金高溫抗蠕變性和耐腐蝕性差等缺點也限制了其在汽車中的應(yīng)用。大部分鎂合金都是只有4個獨立滑移系的六方結(jié)構(gòu),塑性變形能力差。鎂合金的蠕變方式主要是位錯滑移和晶界滑移,AZ91系鎂合金高溫蠕變能力弱是由于晶界處β相(Mg17Al12)的熔點很低,容易高溫變形,無法穩(wěn)定晶界,晶界滑動進而引起蠕變的產(chǎn)生。鎂是活潑的化學(xué)元素,與其他金屬接觸時易發(fā)生電偶腐蝕現(xiàn)象,并充當(dāng)陽極。室溫下的鎂在空氣中形成致密系數(shù)僅為0.79的氧化鎂薄膜,體積縮小,導(dǎo)致耐蝕性很差。
應(yīng)用
國外鎂合金在汽車上的應(yīng)用十分廣泛。在美國、西歐、日本等汽車工業(yè)發(fā)達國家,輕質(zhì)鎂合金已經(jīng)廣泛應(yīng)用于汽車及零部件領(lǐng)域。在2007年,美國轎車95%的發(fā)動機缸蓋和50%缸體已經(jīng)采用鋁鑄件;歐洲的每車鋁鑄件,1990年已經(jīng)為55kg/輛,2006年為98kg/輛。而密度比鋁合金輕三分之一的鎂合金鑄件在轎車上的應(yīng)用更呈現(xiàn)大幅上升的趨勢。
美國通用汽車公司每車已經(jīng)采用45個鎂合金鑄件,每車已達100kg以上;美國福特公司每車已經(jīng)采用30個鎂合金鑄件,每車達到100kg;美國克萊斯勒每車已經(jīng)采用20個鎂合金鑄件,每車已達40kg。“通用”計劃鎂合金用量最高每輛達到150kg/輛;“福特”最高每車118kg/輛;“大眾”計劃10年內(nèi)每車最大達到178kg/輛。鎂合金推廣正向大型集成目標發(fā)展,美國三大汽車公司計劃開發(fā)超大型鎂合金集成件。近幾年,豐田、菲亞特等也已經(jīng)進入全力推廣階段。
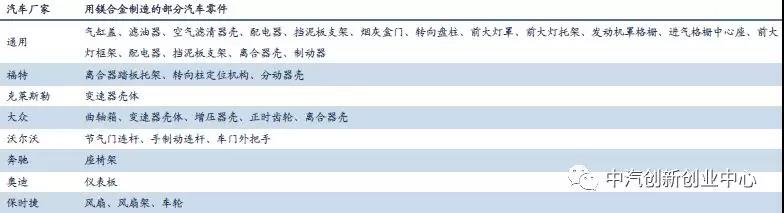
目前,我國鎂合金的應(yīng)用與國外有一定差距。20世紀末,隨著轎車工業(yè)的興起,汽車鎂合金件才起步。2004年全年510萬輛汽車使用鎂合金1.8萬t,2010年全國汽車達到1806萬輛時,鎂合金實用6.13萬t。目前,我國單車鎂合金用量僅在2-4kg左右,低于全球汽車平均每輛用鎂合金4~5kg,更低于日本為9.3kg/輛的鎂合金用量。國內(nèi)為汽車行業(yè)提供鎂合金件的供應(yīng)商大約60家,生產(chǎn)概況如下表:
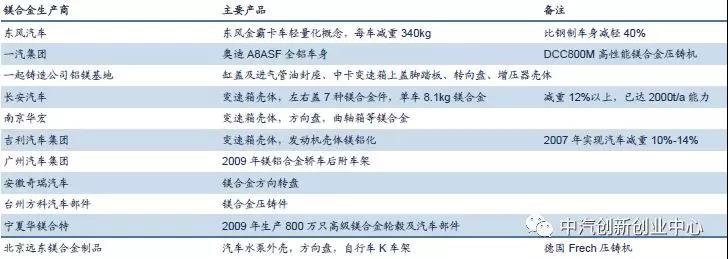
轎車上采用鎂合金的部件有座椅上一些部件、膝墊、轉(zhuǎn)向柱部件、轉(zhuǎn)向盤、制動與離合器踏板托架、安全氣囊限制裝臵、踏板托架、轎車音響小的散熱器框架、鏡托架以及可開式車頂?shù)囊恍┎考?;轎車發(fā)動機中的發(fā)動機機體、氣缸蓋、進氣管、油泵殼體、輔助裝臵的支架以及電器接線裝臵;還有變速箱、離合器殼體、轉(zhuǎn)向盤、柱、閥蓋、閥板、車窗、馬達殼體、油濾接頭、進氣歧管、鏡罩、大燈保持架、制動防抱死系統(tǒng)的托架、車輪、油箱門。未來的發(fā)展中,在一些大型壓鑄件上,也將拓展它的應(yīng)用,如車頂、發(fā)動機蓋、后艙蓋、內(nèi)門板框架、儀表板等。其它的如需要安全及高斷裂韌性的零部件,也將是鎂合金拓展應(yīng)用的領(lǐng)域,如座椅框架、轉(zhuǎn)向柱、車身保護板、發(fā)動機前的散熱器格柵加強板及一些車身結(jié)構(gòu)支撐件。
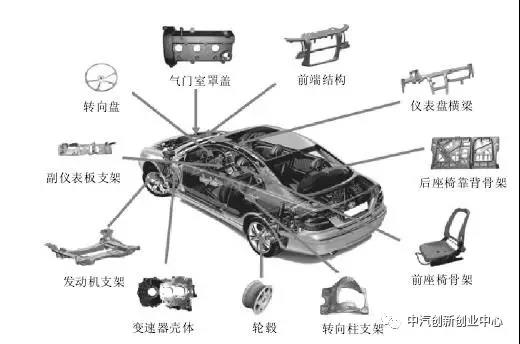
加速“鎂代鋁” 一直以來,高強度鋼、鋁合金等輕量化材料廣泛應(yīng)用于汽車及汽車零部件制造的各個方面,而鎂合金鑒于種種原因沒有得到大力推廣和使用。

鎂合金是最輕的金屬結(jié)構(gòu)材料,鎂的密度只有1.74g/cm3,是鋁的2/3,鋼的1/5。采用鎂合金能減輕整車重量,在車身、動力總成、底盤和內(nèi)飾等4個部分進行材料替換,被鎂和鎂合金替代后的汽車部件減重比例達到20%~70%。
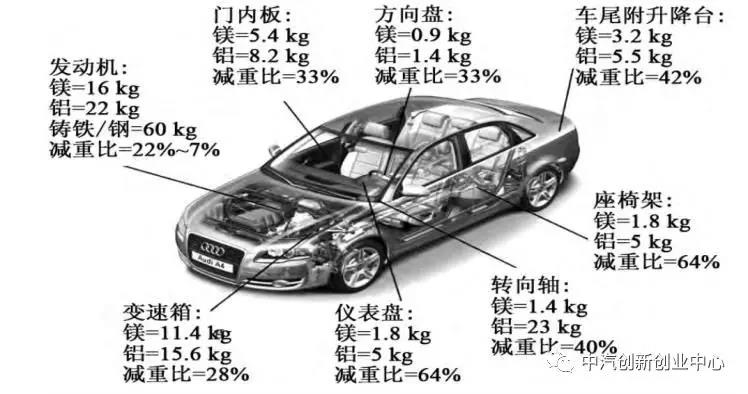
圖:采用鎂材料替換鋁和鋼后的汽車減重情況
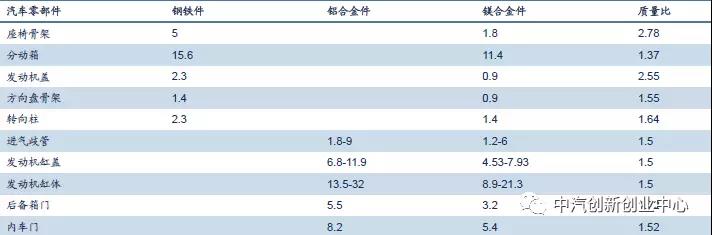
圖:不同金屬材料的汽車零部件質(zhì)量對比
相較于鋁合金,在成熟產(chǎn)品上鎂合金將具備更高的性價比:2018年3月26日,根據(jù)長江有色市場平均價,鎂的價格為16150元/噸,鋁的價格為13670元/噸,雖然鎂的價格比鋁要高大約18%,但是考慮到鎂合金比重較?。ㄦV比重約為1.7kg/m3,鋁比重約為2.7kg/m3),相同體積的鎂合金成本較鋁合金低約34%。
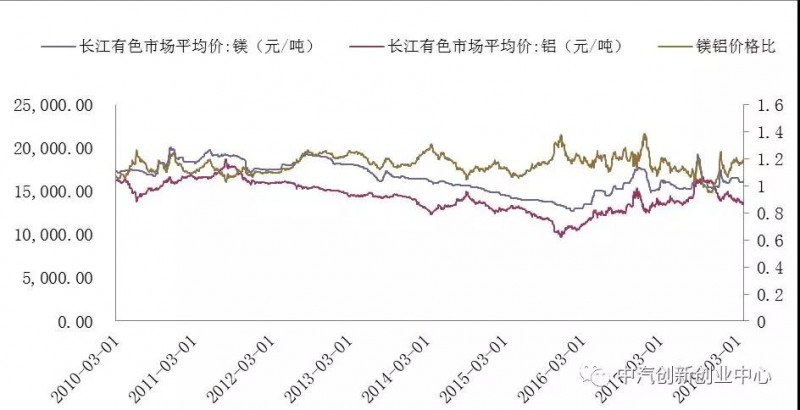
圖:鎂合金、鋁合金價格對比
汽車用鎂合金的技術(shù)不斷突破,應(yīng)用范圍已經(jīng)逐漸能夠與鋁合金相媲美,一方面隨著充氧壓鑄、真空鑄造和半固態(tài)壓鑄等工藝不斷發(fā)展,高性能鎂合金擠壓加工技術(shù)、鎂合金高效短流程成形技術(shù)等技術(shù)能有效提高鎂合金耐腐蝕性,提高鎂合金產(chǎn)品的性能及生產(chǎn)效率,降低生產(chǎn)成本;另一方面現(xiàn)有鎂合金壓鑄件應(yīng)用范圍與鋁合金的重合度日漸擴大,隨著鎂合金的壓鑄工藝進一步提升,鎂合金替代鋁合金產(chǎn)品將成為未來汽車輕量化的主要趨勢。
四、汽車輕量化材料之樹脂
優(yōu)缺點
樹脂基復(fù)合材料又稱纖維增強塑料(FRO),是以合成樹脂為基體,以纖維為增強材料的一種新型復(fù)合材料。樹脂基體包括熱固性樹脂和熱塑性樹脂;增強纖維材料常用的有玻璃纖維、碳纖維、芳綸纖維、高密度聚乙烯纖維等。樹脂基復(fù)合材料具有以下優(yōu)點:
第一,質(zhì)量輕,比強度高。樹脂基復(fù)合材料的相對密度較小,一般介于1.5-2.0g/cm3之間,只有普通碳鋼的1/4-1/5,但是比強度大,承載能力高。
第二,材料性能具有可設(shè)計性。樹脂基復(fù)合材料的物理性能、化學(xué)性能、力學(xué)性能都可以通過合理選擇原材料的種類、配比、加工方法、纖維含量和鋪層方式進行設(shè)計,由于樹脂基體材料的種類很多,故其選材設(shè)計的自由度很大。
第三,具有優(yōu)良的耐腐蝕性。樹脂具有優(yōu)良的耐腐蝕性,有針對性的選擇樹脂來生產(chǎn)復(fù)合材料,可以使樹脂基復(fù)合材料具有不同的耐腐蝕性能。
第四,減震性好。由于樹脂基復(fù)合材料震動衰減系數(shù)大,受沖擊時能夠吸收大量的沖擊能,當(dāng)汽車發(fā)生碰撞時,可以避免或減少對乘客的傷害,有利于提高行車的安全性。
第五,工藝成型簡單。樹脂基復(fù)合材料可以用磨具一次成型制造各種構(gòu)件,從而減少了零部件的數(shù)量及接頭等緊固件,節(jié)省原材料和工時,有效降低了生產(chǎn)成本。在中等批量生產(chǎn)的車型中,用樹脂基復(fù)合材料代替鋁材可以降低成本40%左右。此外,樹脂基復(fù)合材料對缺口、應(yīng)力集中敏感性小,而且纖維和集體潔面能夠阻止和改變裂紋擴展方向,因此具有較高的疲勞極限。

按樹脂基體分類,可以將樹脂基復(fù)合材料分為熱固性樹脂和熱塑性樹脂兩種。熱固性樹脂初加熱時軟化,可塑造成型,但固化后再加熱時將不再軟化,也不溶于溶劑。常用的熱固性樹脂有酚醛樹脂、環(huán)氧樹脂、不飽和聚醋樹脂和有機硅樹脂等。熱塑性樹脂加熱時會軟化和熔融,可塑造成型,冷卻后即成型并保持即得形狀,這一過程具有重復(fù)性。應(yīng)用較多的熱塑性樹脂是:尼龍、聚烯烴類、聚苯乙烯類、熱塑性聚醋和聚碳酸醋等。
車用復(fù)合材料的樹脂基體,目前仍以熱固性樹脂為主,但熱固性復(fù)合材料的缺點是廢棄物回收再利用困難。隨著國際社會對環(huán)境保護的要求越來越高,熱塑性樹脂基復(fù)合材料越來越受到人們的關(guān)注。與熱固性樹脂基復(fù)合材料相比,熱塑性樹脂基復(fù)合材料有許多優(yōu)點。例如斷裂韌性高、成型過程中無化學(xué)反應(yīng),因此成型速度快,成型周期短;預(yù)浸料可以無限期存放,且對存放無特殊要求,易于回收再利用,不環(huán)境污染;能夠?qū)崿F(xiàn)快速、無污染、自動化生產(chǎn)。所以近年來汽車用熱塑性復(fù)合材料的增長速度高于熱固性復(fù)合材料。
應(yīng)用
樹脂基復(fù)合材料在汽車上用途廣泛,可用于制造汽車外板、汽車結(jié)構(gòu)件、發(fā)動機及發(fā)動機周邊部件等。應(yīng)用范圍由內(nèi)飾件、覆蓋件向外裝件、結(jié)構(gòu)件和功能件發(fā)展。發(fā)動機及發(fā)動機周邊部件以往通常使用金屬材料制造,從1990年開始樹脂基復(fù)合材料被大量應(yīng)用于汽車發(fā)動機部件。美國通用汽車公司首先將它應(yīng)用于3.3/3.SLV6轎車發(fā)動機氣門罩殼上,用它代替金屬罩殼。
傳統(tǒng)的車身材料通常采用高強度薄鋼板,為了減輕汽車自重,采用樹脂基復(fù)合材料代替鋼材,已成為車身結(jié)構(gòu)發(fā)展的必然趨勢。通用公司早在1953年就推出克爾維特(Corvette)牌全塑車身的轎車,除翼子板用尼龍注射成型外,所有殼體都是用玻璃纖維增強塑料(FRP)壓鑄模塑成型的。到1980年已有65%的美國轎車采用玻璃鋼片狀模塑料作前臉和散熱器護柵板。目前樹脂基復(fù)合材料已被廣泛應(yīng)用于車身結(jié)構(gòu)件(如骨架、梁、柱等)、覆蓋件(如前臉面罩、前翼子板、發(fā)動機罩、頂蓋、車門、行李箱蓋、后側(cè)板等)以及保險杠、油箱等。
與鋼鐵材料、鋁合金等傳統(tǒng)材料相比,樹脂基復(fù)合材料具有重量輕、比強度高、耐腐蝕、減振性能好、可設(shè)計性強、易于加工等優(yōu)點。盡管樹脂基復(fù)合材料的許多優(yōu)點使其很好地適應(yīng)了汽車工業(yè)的發(fā)展要求,但其存在的一些缺點也是現(xiàn)代汽車工業(yè)所不能容忍的,如:原材料成本較高、彈性模量較低、材料特性分散性大、生產(chǎn)周期較長、可回收性差等。目前,樹脂基復(fù)合材料的加工方法仍不成熟,難以進行大規(guī)模商業(yè)化生產(chǎn)。作為汽車上重要的輕量化材料,樹脂基復(fù)合材料越來越多地取代了傳統(tǒng)的金屬材料,其應(yīng)用范圍由汽車內(nèi)裝飾件、覆蓋件向外裝件、結(jié)構(gòu)件方向發(fā)展,隨著生產(chǎn)工藝的進步,樹脂基復(fù)合材料在汽車工業(yè)中應(yīng)用前景十分廣闊。
市場容量測算
我們希望更加量化地測算出汽車輕量化的市場規(guī)模。由于汽車輕量化是一個系統(tǒng)性、復(fù)雜性的工程,所以我們只能推算出某種材料最大理論市場規(guī)模。具體方法如下:
1) 對比目前國內(nèi)外車重的差距,計算出替代材料單個車輛的需求。
2) 從單車需求推導(dǎo)出整體需求。
3) 根據(jù)材料價格推算出市場規(guī)模。
國內(nèi)外汽車輕量化的差距
汽車輕量化在發(fā)達國家已經(jīng)推廣了十幾年了,目前全球最大的輕量化市場在北美,歐洲為第二大市場。中國在汽車輕量化方面才剛剛起步,但是發(fā)展勢頭比較迅猛。
由于目前國內(nèi)政策并沒有把汽車輕量化的減重目標做量化規(guī)定,所以我們把最發(fā)達的美國減重目標作為對標標的。美國輕量化的汽車的發(fā)展目標:2020年要在13年的基礎(chǔ)上降重20%,2025年要降重30%。由此,我們假設(shè)未來中國汽車輕量化目標也在減重20%左右。
目前汽車車身主要材料還是以鋼為原材料,車身重量大約在1100kg左右。在下文中我們將對碳纖維、玻纖、鎂合金、樹脂等材料做定量分析,來計算出理論市場規(guī)模。
各種材料市場規(guī)模測算
鋼鐵的密度是7.8;碳纖維密度是1.8;玻纖密度是2.6;鎂合金密度是1.8;樹脂密度是1.4-2.2左右(為了保守預(yù)計,我們?nèi)?.2為樹脂密度)。
工信部苗圩部長接受采訪時提出,2020年中國新能源車藥占比達到10%。目前中國汽車產(chǎn)量在每年2600萬輛左右,預(yù)計到2020年這個數(shù)字將達到3000萬輛。保守起見,我們預(yù)計2020年新能源汽車生產(chǎn)數(shù)量為150萬輛。
由于輕量化目標是減重20%,所以1100kg的車身減重的重量理論上為220kg。從中我們可以計算出替代物的替代規(guī)模,推導(dǎo)出理論市場規(guī)模。計算結(jié)果見下表。

圖:2020年輕量化材料理論市場規(guī)模
根據(jù)中國產(chǎn)業(yè)信息網(wǎng)信息,目前碳纖維的價格在200元/kg;玻纖6元/kg;鎂合金30元/kg;樹脂10元/kg。如果在2020年新能源汽車規(guī)模能夠達到150萬輛,普通車規(guī)模能夠達到3000萬輛,則上述各材料對應(yīng)市場規(guī)模如下:碳纖維:200億/4000億;玻纖:10億/ 200億;鎂合金:30億/約600億;樹脂:13億/約260億。目前我國在這些產(chǎn)業(yè)的產(chǎn)能和市場規(guī)模分別是:碳纖維:約5000噸/約10億;玻纖:約400萬噸/約240億;鎂合金:約50萬噸/約150億;樹脂:約500萬噸/約500億。
從潛在市場規(guī)模對比現(xiàn)有市場規(guī)模來看,影響力從大到小排序分別為:碳纖維、鎂合金、樹脂、玻纖。
汽車的輕量化的定義
就是在保證汽車的強度和安全性能的前提下,盡可能地降低汽車的整備質(zhì)量。汽車輕量化有以下優(yōu)點:
- 輕量化可以通過減輕車輛的質(zhì)量來減少新能源汽車的慣性,使汽車的運動狀態(tài)更容易改變,進而提升汽車的加速性能、制動性能和操控性能,有利于應(yīng)對危急情況。
- 根據(jù)輕量化技術(shù)領(lǐng)域的相關(guān)研究,重量的減輕可以增加續(xù)航里程。如純電動汽車整車重量若降低10kg,續(xù)駛里程可增加2.5km。
- 在裝備等條件一致的情況下,只改變質(zhì)量,新能源汽車的能耗會隨著質(zhì)量的減輕而減少,可以在一定程度上達到節(jié)省電力、燃料等的結(jié)果。
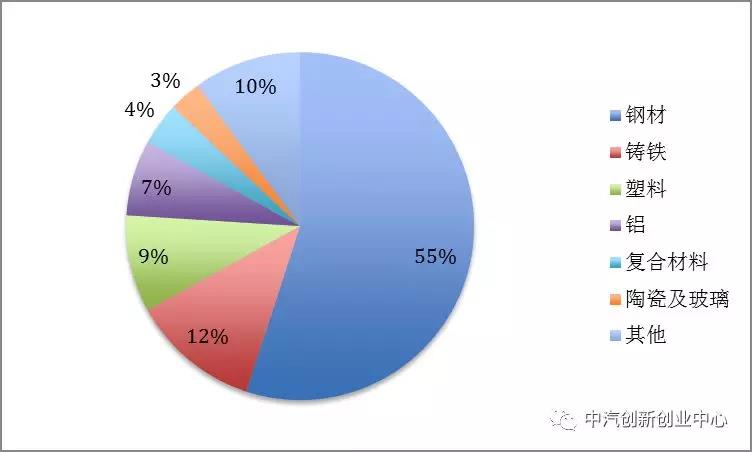
圖:汽車材料使用占比
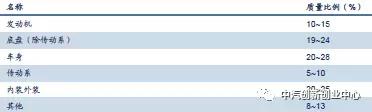
圖:汽車各部件重量占比
汽車輕量化作為一個系統(tǒng)化的工程,并不是簡單地針對某個零件的單獨減重,局部重量的變化在很大程度上會影響汽車的其他部位,因此汽車輕量化是指在汽車制造過程中集設(shè)計、制造、材料技術(shù)等一起的系統(tǒng)性工程。在對汽車進行輕量化設(shè)計時,主要有以下三個途徑:

一、材料輕量化
材料輕量化即通過使用輕量化材料來達到減輕新能源汽車質(zhì)量的目的。目前,應(yīng)用于新能源汽車的輕量化材料主要是有高強度鋼、鋁合金、鎂合金、碳纖維等。例如,奇瑞新能源公司推出的新一代純電動微型車小螞蟻(代號eQ1)采用了“全鋁空間結(jié)構(gòu)+全復(fù)合材料外覆蓋件”的組合形式,車身采用高強度鎂鋁合金應(yīng)用比高達93%以上,全鋁車身較傳統(tǒng)汽車減重40%的同時車身剛性提高了60%以上;大眾寶來通過更改材料減輕重量104.2kg,占總減重的41%。零件小型化后減輕重量144.1kg,占總減重的57%;
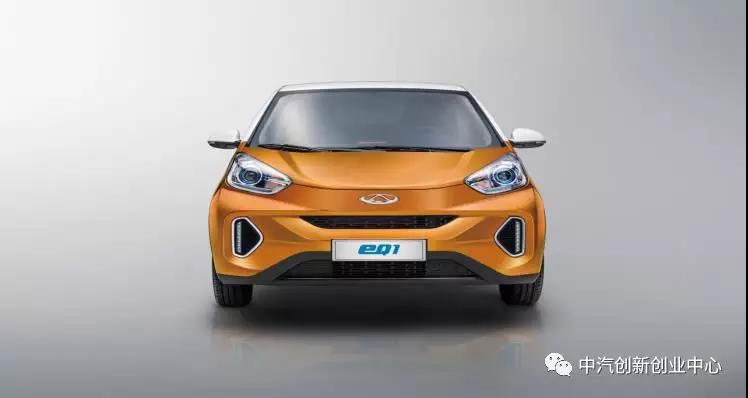
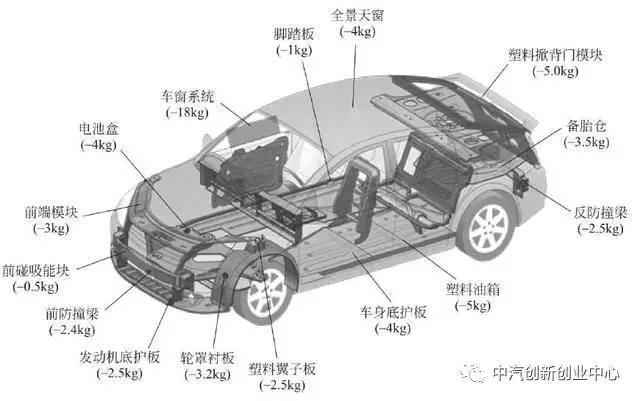
圖:汽車外飾件采用輕量化材料減重途徑

圖:寶來汽車減重途徑
二、結(jié)構(gòu)輕量化
輕量化的另一手段就是在汽車零部件概念設(shè)計、初始結(jié)構(gòu)設(shè)計、產(chǎn)品工程設(shè)計及樣車制造過程中做相關(guān)結(jié)構(gòu)的分析和優(yōu)化,或去除零部件的冗余部分、或減少搭接(如花邊形設(shè)計)、或改變結(jié)構(gòu),在不影響車身強度和安全性能的基礎(chǔ)下盡量減少對零件的使用,有用則保留,無用則放棄,使車內(nèi)布局達到最佳的效果,以實現(xiàn)對汽車零部件的精簡化、整體化和輕質(zhì)化。
結(jié)構(gòu)輕量化包括車身結(jié)構(gòu)優(yōu)化設(shè)計和汽車實體結(jié)構(gòu)布局設(shè)計這兩種方式,主要運用ANSYS、UG、CAD、CATIA等軟件,手段有形貌優(yōu)化、尺寸優(yōu)化、拓撲優(yōu)化(包括多種輕量化材料的匹配、零部件的優(yōu)化分塊)、有限元分析和模塊化集成設(shè)計等。
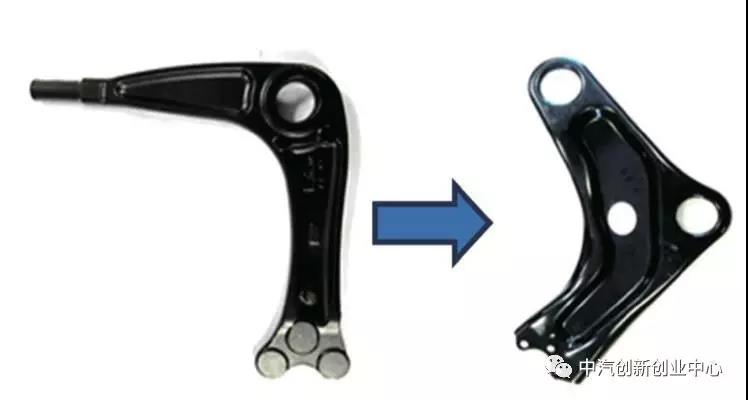
圖:三角臂結(jié)構(gòu)變更
例如神龍汽車公司將三角臂結(jié)構(gòu)變更之后(三角臂是在汽車行駛于不平路面時起平衡支撐作用的結(jié)構(gòu)件),質(zhì)量減輕近50%,制造能耗降低65%。
三、制造工藝輕量化
為進一步達到減重降本的目的,除了開發(fā)應(yīng)用輕量化材料外,一系列適應(yīng)這些新材料的先進工藝,如熱成型、激光焊接、液壓成型、差厚軋制、徑向鍛造、半固態(tài)成型等應(yīng)運而生。
例如,熱成型技術(shù)是基于高強鋼冷沖壓成型中普遍存在塑性范圍窄、易開裂、回彈大等問題而發(fā)展起來的板材成形新技術(shù),通常在900~950°C的奧氏體狀態(tài)下沖壓,并在模具內(nèi)淬火冷卻,汽車上應(yīng)用熱成型技術(shù)的典型鋼種是22MnB5,抗拉強度可達1500MPa。
激光拼焊是指將幾個小零件通過激光焊接集成到一個大的毛坯,進而沖壓成形成所需整體部件。使用激光拼焊板可使模具的數(shù)量和后續(xù)生產(chǎn)工序減少,從而降低了生產(chǎn)成本,并提高了零部件的質(zhì)量、優(yōu)化了零件結(jié)構(gòu),充分發(fā)揮了不同強度、不同厚度板材的特性,成為汽車輕化降低零件數(shù)量、保證汽車安全、優(yōu)化設(shè)計和改進制造技術(shù)的重要手段。
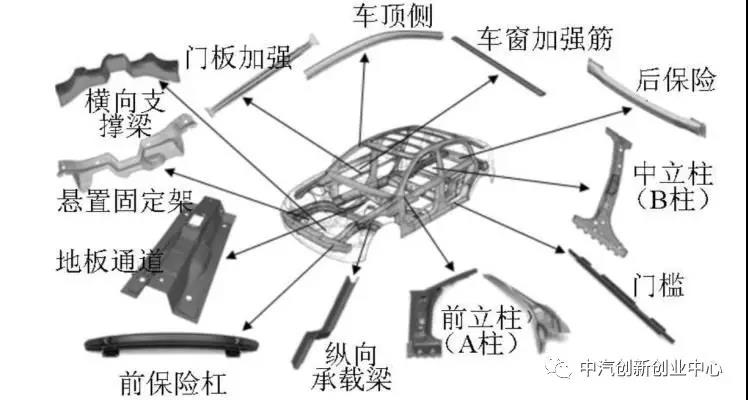
圖:熱成型在汽車零件上的典型應(yīng)用
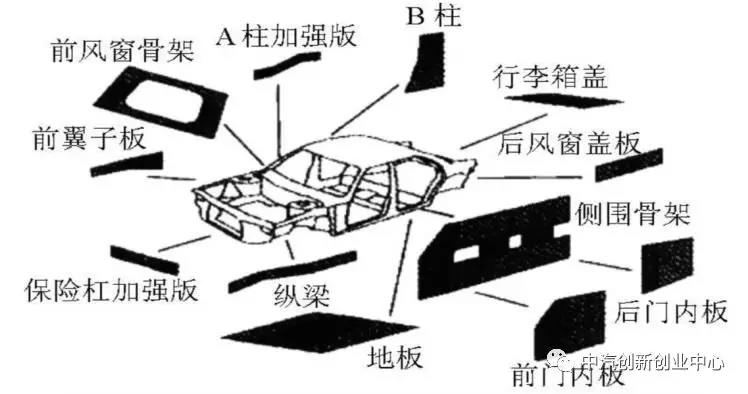
圖:激光拼焊應(yīng)用的典型零件
根據(jù)2017年新能源汽車目錄列表中的汽車續(xù)航里程情況計算,乘用車平均續(xù)航里程為192km,新能源客車平均續(xù)航里程為238km,專用車為219km??紤]到測試數(shù)據(jù)一般要優(yōu)于實際數(shù)據(jù),所以我們認為新能源乘用車的平均續(xù)航能力要小于192km,與中央希望達到的250km以上的續(xù)航能力相差很遠(根據(jù)補貼新政,中央將扶持250km以上乘用車,其中300km以上的將大力扶持)。對于那些續(xù)航能力在200km左右的車型來說,他們將寄希望于未來能夠短時間內(nèi)提升續(xù)航里程。那對于那些續(xù)航里程在200km左右的車型來說,用汽車輕量化的方法來達標是否可行呢?
答案是可行的。根據(jù)《論汽車輕量化》雜志報道,奇瑞汽車實車測試數(shù)據(jù)顯示,電動汽車減重10%,平均續(xù)航能力增加5%-8%。對于那些續(xù)航能力在200km的汽車來說,在不改變汽車設(shè)計以及電池性能的條件下,將車體重量減少20%左右就可以達標。
綜上所述,提升鋰電池性能目前處于一個瓶頸期,鋰電池性能在短時間內(nèi)突破瓶頸可能性不大;增加鋰電池數(shù)量也將增加汽車的重量以及成本,對于續(xù)航里程沒有明顯的提升;所以,最可行的、而且是最快速的方法就是汽車輕量化。
汽車輕量化材料市場前景廣闊
本報告主要關(guān)注新能源汽車補貼新政落地后,對輕量化材料市場的影響。在接下來的篇幅中將重點討論新材料在汽車輕量化的地位以及發(fā)展情況。
一、汽車輕量化材料之碳纖維
概述
碳纖維起源可以追溯到1860年,首先由英國人發(fā)明。由于其抗高溫能力不如鎢絲,所以無法成為電燈泡的發(fā)光材料,隨后碳纖維的研究進入低谷。直到20世紀50年代,碳纖維的研究被美國人在導(dǎo)彈研究領(lǐng)域再一次推上舞臺。碳纖維研究的里程碑發(fā)生在1959年,日本人近藤昭男發(fā)明了聚丙烯晴(PAN)基碳纖維。PAN碳纖維具有工藝成熟,性能良好和低成本等優(yōu)勢,在目前統(tǒng)計情況來看,PAN碳纖維占全部產(chǎn)量的90%以上。在今天的材料領(lǐng)域,如果不特指的話,碳纖維一般都是指PAN碳纖維。
碳纖維是有機纖維經(jīng)過碳化和石墨化處理得到的微晶石墨材料,其微觀結(jié)構(gòu)類似人造石墨,是亂層石墨結(jié)構(gòu)。其含碳量高于90%,如果含碳量高于99%則稱為石墨纖維。碳纖維軸向強度和模量高,耐疲勞性好,比熱和導(dǎo)電性質(zhì)介于金屬和非金屬之間,熱膨脹系數(shù)小,耐腐蝕,密度低。但是由于碳纖維耐沖擊性較弱,容易發(fā)生氧化,所以一般需要進行表面處理。
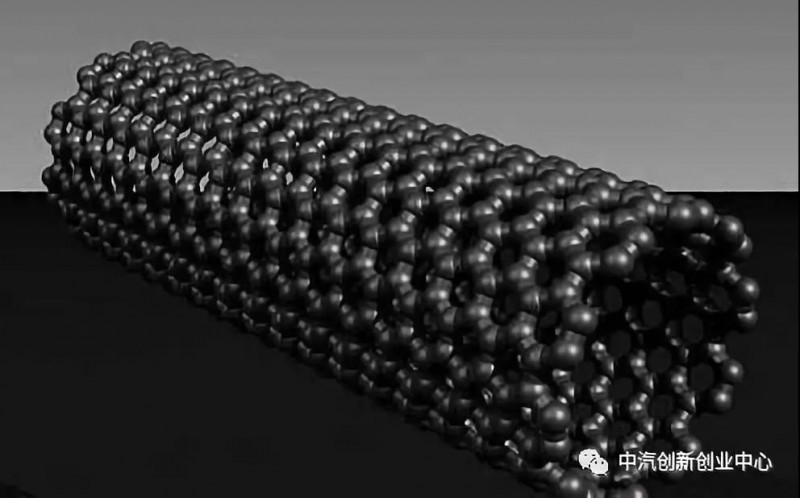
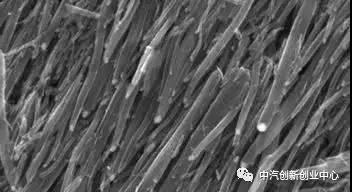
碳纖維的生產(chǎn)通常使用一些含碳的有機纖維(尼龍、腈綸、人造絲等)做原料,將有機纖維跟塑料樹脂結(jié)合一起,在惰性氣體環(huán)境中高壓高熱碳化而成。碳纖維可以通過高分子有機纖維碳化或者低分子烴類氣相熱解來制備。目前世界上生產(chǎn)銷售的碳纖維大部分是用PAN纖維固相碳化而來。
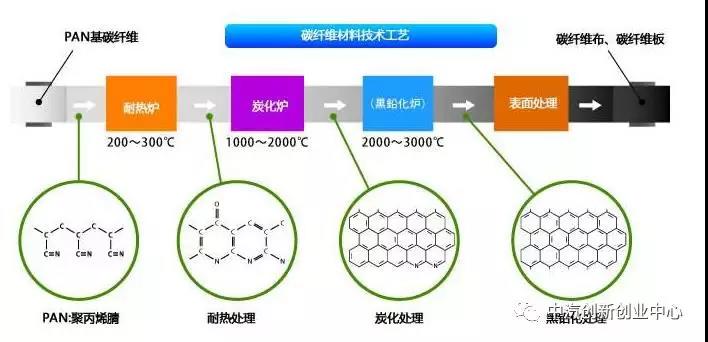
圖:碳纖維生產(chǎn)方式
目前,碳纖維的主要生產(chǎn)國家有美國、日本等。日本是世界上碳纖維產(chǎn)能最大的國家,并且控制了高端碳纖維的生產(chǎn)。日本東麗公里在PAN碳纖維研制生產(chǎn)中充當(dāng)急先鋒,美國的Hexcel公司緊隨其后。在小絲束碳纖維生產(chǎn)層面,除了東麗和Hexcel以外,日本東邦人造絲,日本三菱人造絲和美國Cytec公司都是在碳纖維生產(chǎn)制造上有一席之地,但是技術(shù)上還是與日本東麗有一定差距。在大絲束碳纖維生產(chǎn)層面,美國的Zoltek,Aldila,德國的SGLcarbon也有一定的話語權(quán)??偟膩碚f,美國在大絲束碳纖維上有一定優(yōu)勢,日本則在小絲束上領(lǐng)先。
優(yōu)缺點及應(yīng)用
碳纖維具有多種優(yōu)異的性質(zhì),具有密度小、強度高、熱膨脹系數(shù)小、導(dǎo)熱性好、耐腐蝕性好、耐磨性好等特性,使用碳纖維復(fù)合材料代替?zhèn)鹘y(tǒng)的汽車材料,有以下幾個優(yōu)點:
第一,碳纖維應(yīng)用于汽車后,有利于實現(xiàn)汽車輕量化,提升汽車的節(jié)能、加速、制動性能。
第二,車身輕量化可以使整車的重心下移,提升了汽車操縱穩(wěn)定性,車輛的運行將更加安全、穩(wěn)定。碳纖維復(fù)合材料具有極佳的能量吸收率,碰撞吸能能力是鋼的六到七倍、鋁的三到四倍,碰撞時產(chǎn)生的碎片較少,進一步保證了汽車的安全性。
第三,碳纖維復(fù)合材料具有更高的震動阻尼,輕合金需要9秒才能停止震動,碳纖維復(fù)合材料2秒就能停止,故碳纖維應(yīng)用在汽車上,對于整車NVH(噪聲、振動與聲振粗糙度)的提升貢獻同樣很大,會大幅增強汽車行駛的舒適性。
第四,碳纖維復(fù)合材料具有更高的疲勞強度,鋼和鋁的疲勞強度是抗拉強度的30-50%,而碳纖維復(fù)合材料可達70-80%,因此汽車上應(yīng)用碳纖維復(fù)合材料對于材料疲勞可靠性有較大提升。

目前,碳纖維目前已經(jīng)在高端車、超跑、賽車、改裝車以及少量的電動車上開始大量。在汽車零部件中的應(yīng)用,碳纖維主要分布在汽車車身、內(nèi)外飾、底盤系統(tǒng)、動力系統(tǒng)等。

碳纖維在汽車車身、汽車輪轂、汽車剎車、傳動系統(tǒng)以及汽車內(nèi)飾、門窗等多個汽車組件上都有應(yīng)用。
如寶馬在多個系列的車型中使用了碳纖維,例如,在全新寶馬7系的車體框架中,碳纖維被用于加固車頂橫梁結(jié)構(gòu)、B柱、C柱、底部側(cè)圍、中央通道和后部支撐,這些部件以往只能用高強度鋼材打造,換成鋼和碳纖維混合結(jié)構(gòu)后重量直接減輕50%以上,而且強度是鋼的5倍以上,最終7系比上一代減輕了130kg重量;寶馬i3/i8Life模塊由全碳纖維材質(zhì)打造,該結(jié)構(gòu)免去了中央通道對內(nèi)部空間的占用,讓乘客擁有更多空間,同時也抵消了高壓蓄電池給車身帶來的重量,還降低了汽車的重心;保時捷911Turbo采用碳纖維輪轂,比鋁合金減重20%,強度提高了20%,且減輕簧下重量,讓懸掛反應(yīng)靈敏度增加、減少轉(zhuǎn)動慣性以及縮短剎車距離。
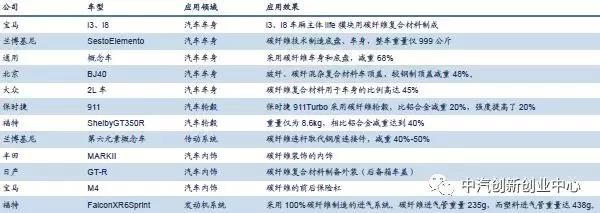
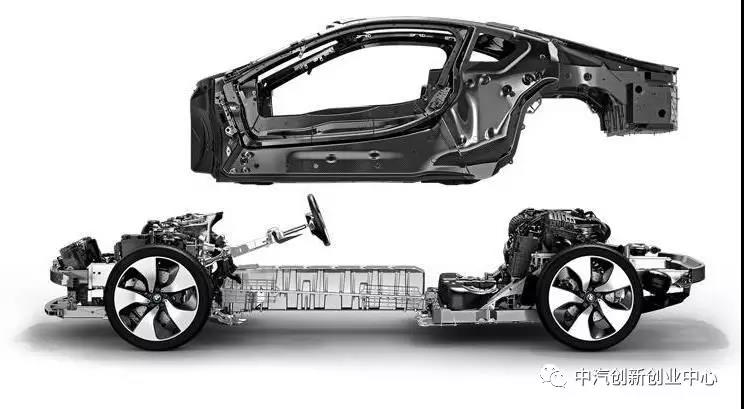
圖:寶馬i8碳纖維車身
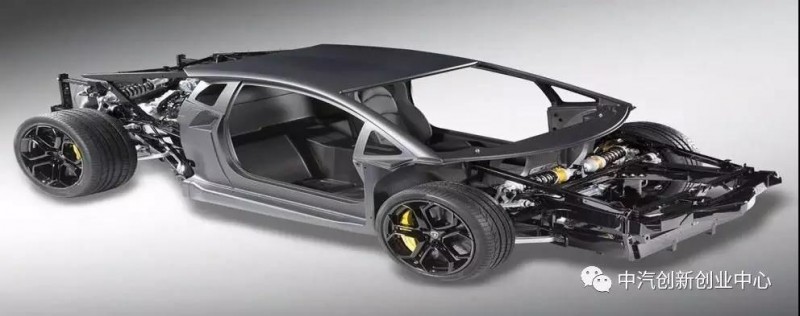
圖:蘭博基尼Aventador碳纖維車身
目前,碳纖維在民用領(lǐng)域的應(yīng)用依然不多,主要集中應(yīng)用在一些賽車和小批量高檔轎車上,制約我國碳纖維及其復(fù)合材料業(yè)發(fā)展的問題在于碳纖維原絲質(zhì)量差、價格高、應(yīng)用基礎(chǔ)研究薄弱等。
碳纖維是脆性材料,它的高強度只限于軸向,徑向強度較低。如果受力過大,碳纖維會直接斷裂。目前對于碳纖維材料在碰撞下的性能仍然了解不充分,損壞零部件的檢測與維修技術(shù)還不成熟,因此損壞后基本無法修復(fù)。國產(chǎn)原絲不僅強度低,而且CV(強度離散系數(shù))值大,很難生產(chǎn)出質(zhì)量穩(wěn)定的優(yōu)質(zhì)碳纖維。
另外,高昂的成本,使得碳纖維目前只能局限在部分超豪華車型上,難以普及。
例如,采用T300碳絲+環(huán)氧樹脂代替SMC+ABS制造的某車型車身頂蓋,質(zhì)量由9.7kg減到5kg,但單件產(chǎn)品成本從三百多元翻了近五番;寶馬i3電動車銷量不佳部分原因是過度使用了碳纖維使得車輛太貴,一輛寶馬i3價格大致為5.5萬歐元;雷克薩斯推出的全碳纖維車身和底盤的LFA,售價高達30萬-40萬英鎊。
因此,要促進碳纖維復(fù)合材料在汽車上的廣泛應(yīng)用,必須解決以下問題:
第一,降低碳纖維成本。每千克碳纖維耗費大概20美元,普通鋼只1美元左右。隨著生產(chǎn)工藝技術(shù)的重大突破,每千克碳纖維預(yù)計可以降到10美元左右,這將為碳纖維增強復(fù)合材料在汽車上的應(yīng)用開辟廣闊前景,碳纖維復(fù)合材料將大規(guī)模取代現(xiàn)用的工程材料。
第二,加強碳纖維及其復(fù)合材料的應(yīng)用技術(shù)研究。主要包括碳纖維及其復(fù)合材料結(jié)構(gòu)設(shè)計技術(shù)的研究、碳纖維及其復(fù)合材料成型工藝、性能表征和質(zhì)量控制與保證、碳纖維及其復(fù)合材料相應(yīng)標準的建立與完善、碳纖維復(fù)合材料的修補技術(shù)等。
二、汽車輕量化材料之玻璃纖維
概況
玻璃纖維(GFRP)是纖維狀的玻璃,化學(xué)組成主要是二氧化硅(SiO2)、三氧化二硼(B2O3)、氧化鈣(CaO)、三氧化二鋁(Al2O3)等。玻璃纖維作為一種性能優(yōu)異的無機非金屬材料,是復(fù)合材料中使用量最大的一種增強材料,有著機械強度高、吸收沖擊能亮大、耐熱性強等優(yōu)點,能提高基體材料機械強度、彈性模量等力學(xué)性能。
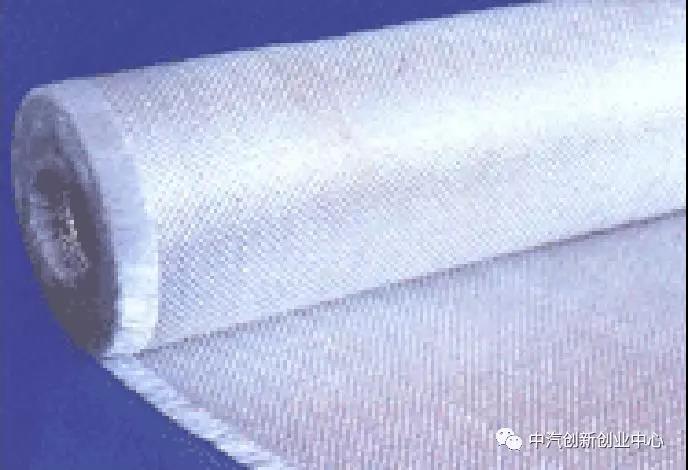
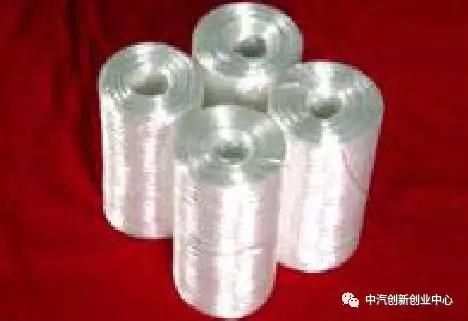
玻璃纖維分類方法很多,一般可以從成分,直徑,纖維外觀和纖維特性等方面分類。

玻璃纖維具有足夠的剛性,耐沖擊性能良好,能滿足車身安全的基本要求;且具有足夠的硬度及韌性,使得車身受到輕微碰撞時,能卸除部分沖擊力,或產(chǎn)生回彈,對比鐵質(zhì)來說其安全系數(shù)更高;其抗刮能力強,耐腐蝕,抗老化能力表現(xiàn)也非常優(yōu)秀。另外,玻璃纖維可塑性強,易成型;可后期拼接,也可與其他材質(zhì)的部件拼接。
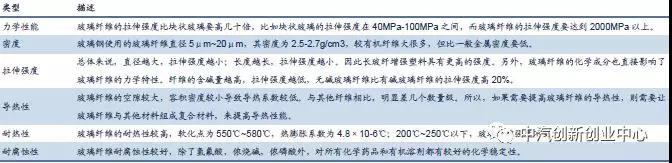
我國是一個玻璃纖維產(chǎn)業(yè)大國,2016年全球玻纖產(chǎn)量達到約625萬噸,我國玻纖產(chǎn)量約為363萬噸,占全球玻纖產(chǎn)量的58%,產(chǎn)量位居全球第一。但在生產(chǎn)技術(shù)、產(chǎn)品附加值、行業(yè)標準等方面,國內(nèi)玻纖產(chǎn)業(yè)與國外存在較明顯差距,尚未達到玻璃纖維強國的水平。

早在1955年,歐洲就開始在汽車上使用GFRP,曾在STM-Ⅲ型車上試用GFRP板。1970年,日本就用GFRP制造汽車車輪裝飾罩。1971年日本鈴木公司用GFRP制造發(fā)動機罩、翼子板、保險杠等。1974年英國厄夫公司試制成功了GFRP駕駛室。1979年美國克萊斯勒公司用GFRP制造轎車車身尾部零件。1980年美國通用公司用GFRP制造客貨兩用車車門,該公司用GFRP制造的駕駛室于1983年正式用于“將軍”型載貨車上。
此外,GFRP在國內(nèi)的汽車企業(yè)中也得到了廣泛的應(yīng)用。北京251廠的BJ121GFRP駕駛室的成功研制,為GFRP在國內(nèi)汽車應(yīng)用上奠定了堅實基礎(chǔ),隨后第一汽車制造廠成功研制GFRP發(fā)動機罩及平頭可翻式駕駛室。受國產(chǎn)汽車工業(yè)的影響,較多應(yīng)用在國內(nèi)汽車工業(yè)是在80年代后期。1986年山東武城旅行車廠成功研制了BWC-6440全GFRP車身旅行車,該廠研制的BWC6470、BWC6480全GFRP車身旅行車1992年通過了3萬公里可靠性定型試驗和碰撞試驗。2013年廣東省中山大學(xué)研究院與東莞雅日玻璃鋼有限公司成功研制了全GFRP車身電動巴士。
長玻纖增強材料
按照塑料粒子的長度和玻璃纖維的長度,有短玻纖增強塑料與長玻纖增強塑料之分。長玻纖一般指長度超過10mm的玻纖,與短玻纖相比,長玻纖纖維長度較長,力學(xué)性能更佳,且剛度和比強度高,抗沖擊性能好,耐疲勞性能優(yōu)良,特別適合汽車部件的應(yīng)用;另外,長玻纖耐蠕變性能提高,尺寸穩(wěn)定性好,部件成型精度高,成型過程中纖維可以在成型模具中相對移動,纖維損傷小。目前,LFT已在汽車防撞梁、前端模塊、儀表盤骨架、車門中間承載板、電瓶箱、座椅骨架板、備胎倉以及車底部護板等結(jié)構(gòu)件和半結(jié)構(gòu)件中得到廣泛應(yīng)用。
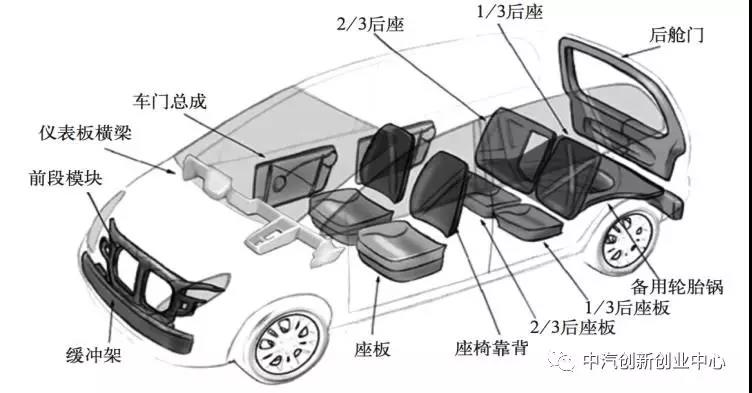
圖:長玻纖增強材料在汽車零部件中的應(yīng)用
玻璃纖維氈增強熱塑性復(fù)合材料
玻璃纖維氈增強熱塑性復(fù)合材料簡稱GMT,是目前國際上極為活躍的復(fù)合材料開發(fā)品種。這是一種以熱塑性樹脂為基體,以玻璃纖維氈為增強骨架的新穎、節(jié)能、輕質(zhì)的復(fù)合材料,一般可以生產(chǎn)出片材半成品,然后直接加工成所需形狀的產(chǎn)品,纖維可以是短切玻璃纖維或連續(xù)的玻璃纖維氈,熱塑性樹脂可以是通用塑料,工程塑料或高性能塑料。GMT產(chǎn)品具有很多優(yōu)異的性能,如耐化學(xué)性好,強度/重量比大,在高、低溫環(huán)境中的抗沖擊性能優(yōu)良。GMT工藝生產(chǎn)的輕質(zhì)高強度的GMT片材,通過結(jié)構(gòu)優(yōu)化設(shè)計,可取代部分金屬材料,獲得顯著的減重效果,而且節(jié)省模具費用,并有利于多種零件組合,形成模塊化生產(chǎn)方式。用GMT片材可較原金屬件減重30~80%,能耗僅為鋼制品的60~80%,鋁制品的35~50%。
GMT片材在汽車工業(yè)中的應(yīng)用,已達40多種,主要有座椅骨架、保險杠、儀表板、發(fā)動機罩、電池托架、腳踏板、前端、地板、護板、后牽門、車頂棚、行李托架、遮陽板、備用輪胎架等部件。國內(nèi)已經(jīng)投產(chǎn)的AuidA6以及A4車已采用GMT材料,但尚未實現(xiàn)國產(chǎn)化。
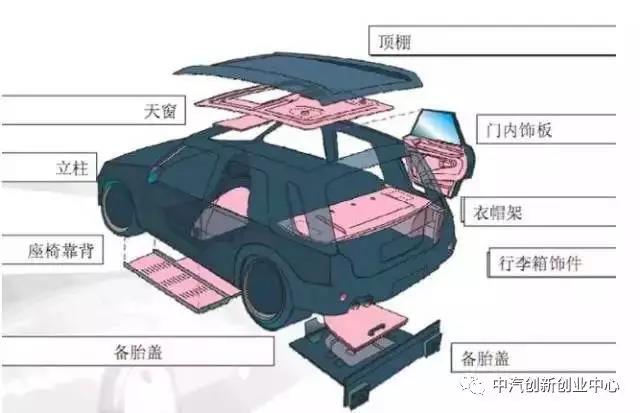
圖:GMT片材在在汽車零部件中的應(yīng)用
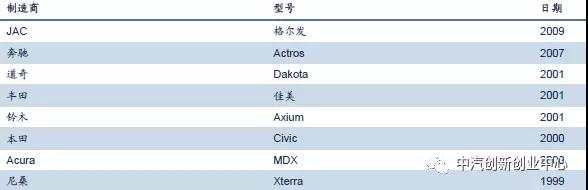
圖:GMT片材內(nèi)飾頂?shù)膽?yīng)用舉例
玻璃纖維增強復(fù)合材料具有優(yōu)異的綜合性能,是當(dāng)今塑料復(fù)合材料最重要的發(fā)展趨勢之一,在汽車上的應(yīng)用前景很可觀。玻璃纖維已開始在歐洲和美國的汽車制造業(yè)中廣泛使用,但在國產(chǎn)汽車上還未得到廣泛的應(yīng)用。
未來,車用玻纖材料需要著力從以下幾個方面進行改進:
第一,降低成本,擴大應(yīng)用領(lǐng)域。價格是制約汽車車身新材料應(yīng)用的重要因素,只有大幅度降低新材料的制造出成本,才可能使諸多新材料更容易被主機廠接受并加入批量生產(chǎn)。
第二,玻璃纖維具有很好的可設(shè)計性,但其與金屬制件的連接在國內(nèi)仍是制約其發(fā)展的瓶頸,未來需要著力提高玻纖與其他的材料的結(jié)合性。
第三,加快玻纖材料的開發(fā)和成型技術(shù)的研究,包括擴大增強纖維和基體的種類,開發(fā)先進的高效節(jié)能的成型技術(shù)和相應(yīng)的回收技術(shù),擴大器在汽車輕量化中的應(yīng)用,推動中國汽車輕量化的進展。
三、汽車輕量化材料之鎂合金
優(yōu)缺點
鎂合金是以鎂為原料的高性能輕型結(jié)構(gòu)材料,比重與塑料相近,剛度、強度不亞于鋁,具有較強的抗震、防電磁、導(dǎo)熱、導(dǎo)電等優(yōu)異性能,并且可以全回收無污染。具體來說,鎂合金在汽車生產(chǎn)中有以下幾個優(yōu)點:
第一,鎂合金密度小但強度高、剛性好。在現(xiàn)有工程用金屬中,鎂的密度最小,是鋼的1/5,鋅的1/4,鋁的2/3。普通鑄造鎂合金和鑄造鋁合金的剛度相同,因而其比強度明顯高于鋁合金。鎂合金的剛度隨厚度的增加而成立方比增加,故而鎂合金制造剛性好的性能對整體構(gòu)件的設(shè)計十分有利。
第二,鎂合金的韌性好、減震性強。鎂合金在受外力作用時,易產(chǎn)生較大的變形。但當(dāng)受沖擊載荷時,吸收的能量是鋁的1.5倍,因此,很適合應(yīng)于受沖擊的零件—車輪;鎂合金有很高的阻尼容量,是避免由于振動、噪音而引起工人疲勞等場合的理想材料。
第三,鎂合金的熱容量低、凝固速度快、壓鑄性能好。鎂合金是良好的壓鑄材料,它具有很好的流動性和快速凝固率,能生產(chǎn)表面精細、棱角清晰的零件,并能防止過量收縮以保證尺寸公差。由于鎂合金熱容量低,與生產(chǎn)同樣的鋁合金鑄件相比,其生產(chǎn)效率高40%~50%,且鑄件尺寸穩(wěn)定,精度高,表面光潔度好。
第四,鎂合金具有優(yōu)良的切削加工性。鎂合金是所有常用金屬中較容易加工的材料。加工時可采用較高的切削速度和廉價的切削刀具,工具消耗低。而且不需要磨削和拋光,用切削液就可以得到十分光潔的表面。
第五,鎂合金的儲量豐富,占地球地殼2.7%,開采壽命分別為鐵和鋁的20和4倍,我們國家占有世界70%的儲量。另外我國白云石儲備超過70億噸,而白云石是制造鎂合金的基礎(chǔ)原材料。
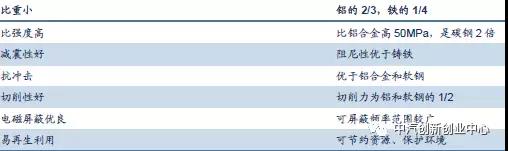
易燃燒和耐腐蝕性差是鎂合金普及的“攔路虎”。
鎂元素與氧元素具有極大的親和力,其在高溫下甚至還處于固態(tài)的情況下,就很容易與空氣中的氧氣發(fā)生反應(yīng),放出大量熱,且生成的氧化鎂導(dǎo)熱性能不好,熱量不能及時發(fā)散,繼而促進了氧化反應(yīng)的進一步進行,形成了惡性循環(huán),而且氧化鎂疏松多孔,不能有效阻隔空氣中氧的侵入。鎂合金加工過程中,容易發(fā)生燃燒和爆炸,存在安全生產(chǎn)問題,生產(chǎn)現(xiàn)場需要嚴格的管理來保證安全生產(chǎn)。
鎂合金高溫抗蠕變性和耐腐蝕性差等缺點也限制了其在汽車中的應(yīng)用。大部分鎂合金都是只有4個獨立滑移系的六方結(jié)構(gòu),塑性變形能力差。鎂合金的蠕變方式主要是位錯滑移和晶界滑移,AZ91系鎂合金高溫蠕變能力弱是由于晶界處β相(Mg17Al12)的熔點很低,容易高溫變形,無法穩(wěn)定晶界,晶界滑動進而引起蠕變的產(chǎn)生。鎂是活潑的化學(xué)元素,與其他金屬接觸時易發(fā)生電偶腐蝕現(xiàn)象,并充當(dāng)陽極。室溫下的鎂在空氣中形成致密系數(shù)僅為0.79的氧化鎂薄膜,體積縮小,導(dǎo)致耐蝕性很差。
應(yīng)用
國外鎂合金在汽車上的應(yīng)用十分廣泛。在美國、西歐、日本等汽車工業(yè)發(fā)達國家,輕質(zhì)鎂合金已經(jīng)廣泛應(yīng)用于汽車及零部件領(lǐng)域。在2007年,美國轎車95%的發(fā)動機缸蓋和50%缸體已經(jīng)采用鋁鑄件;歐洲的每車鋁鑄件,1990年已經(jīng)為55kg/輛,2006年為98kg/輛。而密度比鋁合金輕三分之一的鎂合金鑄件在轎車上的應(yīng)用更呈現(xiàn)大幅上升的趨勢。
美國通用汽車公司每車已經(jīng)采用45個鎂合金鑄件,每車已達100kg以上;美國福特公司每車已經(jīng)采用30個鎂合金鑄件,每車達到100kg;美國克萊斯勒每車已經(jīng)采用20個鎂合金鑄件,每車已達40kg。“通用”計劃鎂合金用量最高每輛達到150kg/輛;“福特”最高每車118kg/輛;“大眾”計劃10年內(nèi)每車最大達到178kg/輛。鎂合金推廣正向大型集成目標發(fā)展,美國三大汽車公司計劃開發(fā)超大型鎂合金集成件。近幾年,豐田、菲亞特等也已經(jīng)進入全力推廣階段。
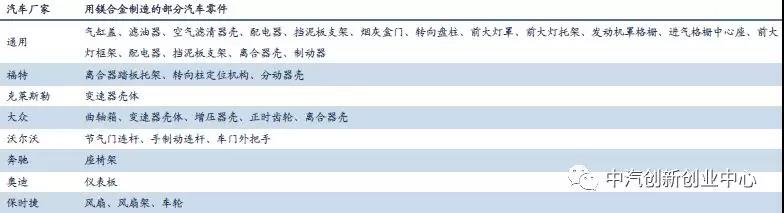
目前,我國鎂合金的應(yīng)用與國外有一定差距。20世紀末,隨著轎車工業(yè)的興起,汽車鎂合金件才起步。2004年全年510萬輛汽車使用鎂合金1.8萬t,2010年全國汽車達到1806萬輛時,鎂合金實用6.13萬t。目前,我國單車鎂合金用量僅在2-4kg左右,低于全球汽車平均每輛用鎂合金4~5kg,更低于日本為9.3kg/輛的鎂合金用量。國內(nèi)為汽車行業(yè)提供鎂合金件的供應(yīng)商大約60家,生產(chǎn)概況如下表:
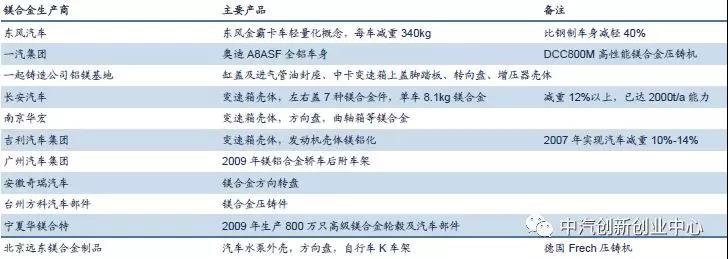
轎車上采用鎂合金的部件有座椅上一些部件、膝墊、轉(zhuǎn)向柱部件、轉(zhuǎn)向盤、制動與離合器踏板托架、安全氣囊限制裝臵、踏板托架、轎車音響小的散熱器框架、鏡托架以及可開式車頂?shù)囊恍┎考?;轎車發(fā)動機中的發(fā)動機機體、氣缸蓋、進氣管、油泵殼體、輔助裝臵的支架以及電器接線裝臵;還有變速箱、離合器殼體、轉(zhuǎn)向盤、柱、閥蓋、閥板、車窗、馬達殼體、油濾接頭、進氣歧管、鏡罩、大燈保持架、制動防抱死系統(tǒng)的托架、車輪、油箱門。未來的發(fā)展中,在一些大型壓鑄件上,也將拓展它的應(yīng)用,如車頂、發(fā)動機蓋、后艙蓋、內(nèi)門板框架、儀表板等。其它的如需要安全及高斷裂韌性的零部件,也將是鎂合金拓展應(yīng)用的領(lǐng)域,如座椅框架、轉(zhuǎn)向柱、車身保護板、發(fā)動機前的散熱器格柵加強板及一些車身結(jié)構(gòu)支撐件。
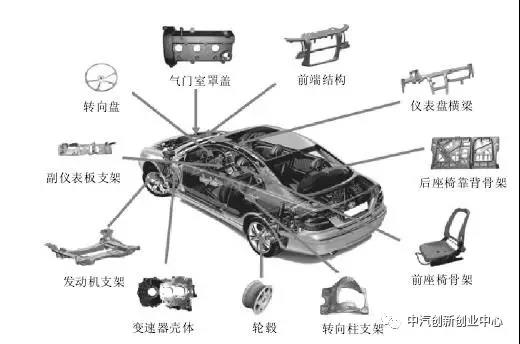
加速“鎂代鋁” 一直以來,高強度鋼、鋁合金等輕量化材料廣泛應(yīng)用于汽車及汽車零部件制造的各個方面,而鎂合金鑒于種種原因沒有得到大力推廣和使用。

鎂合金是最輕的金屬結(jié)構(gòu)材料,鎂的密度只有1.74g/cm3,是鋁的2/3,鋼的1/5。采用鎂合金能減輕整車重量,在車身、動力總成、底盤和內(nèi)飾等4個部分進行材料替換,被鎂和鎂合金替代后的汽車部件減重比例達到20%~70%。
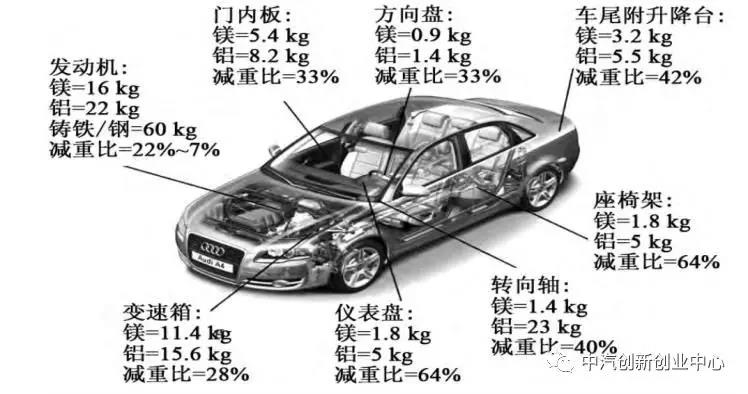
圖:采用鎂材料替換鋁和鋼后的汽車減重情況
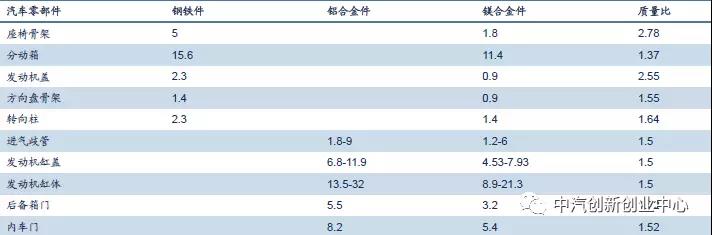
圖:不同金屬材料的汽車零部件質(zhì)量對比
相較于鋁合金,在成熟產(chǎn)品上鎂合金將具備更高的性價比:2018年3月26日,根據(jù)長江有色市場平均價,鎂的價格為16150元/噸,鋁的價格為13670元/噸,雖然鎂的價格比鋁要高大約18%,但是考慮到鎂合金比重較?。ㄦV比重約為1.7kg/m3,鋁比重約為2.7kg/m3),相同體積的鎂合金成本較鋁合金低約34%。
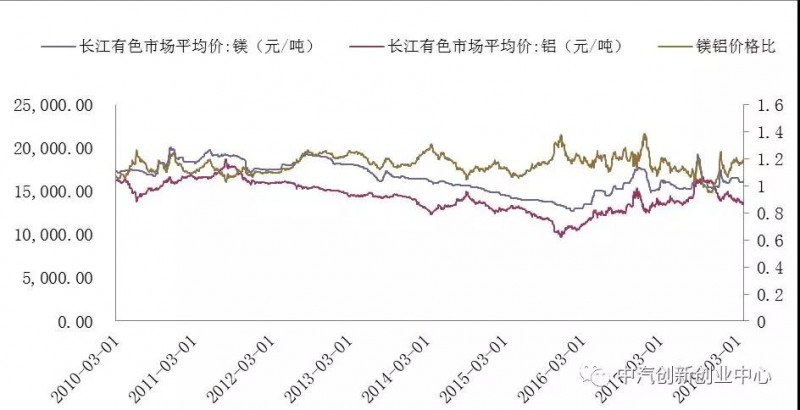
圖:鎂合金、鋁合金價格對比
汽車用鎂合金的技術(shù)不斷突破,應(yīng)用范圍已經(jīng)逐漸能夠與鋁合金相媲美,一方面隨著充氧壓鑄、真空鑄造和半固態(tài)壓鑄等工藝不斷發(fā)展,高性能鎂合金擠壓加工技術(shù)、鎂合金高效短流程成形技術(shù)等技術(shù)能有效提高鎂合金耐腐蝕性,提高鎂合金產(chǎn)品的性能及生產(chǎn)效率,降低生產(chǎn)成本;另一方面現(xiàn)有鎂合金壓鑄件應(yīng)用范圍與鋁合金的重合度日漸擴大,隨著鎂合金的壓鑄工藝進一步提升,鎂合金替代鋁合金產(chǎn)品將成為未來汽車輕量化的主要趨勢。
四、汽車輕量化材料之樹脂
優(yōu)缺點
樹脂基復(fù)合材料又稱纖維增強塑料(FRO),是以合成樹脂為基體,以纖維為增強材料的一種新型復(fù)合材料。樹脂基體包括熱固性樹脂和熱塑性樹脂;增強纖維材料常用的有玻璃纖維、碳纖維、芳綸纖維、高密度聚乙烯纖維等。樹脂基復(fù)合材料具有以下優(yōu)點:
第一,質(zhì)量輕,比強度高。樹脂基復(fù)合材料的相對密度較小,一般介于1.5-2.0g/cm3之間,只有普通碳鋼的1/4-1/5,但是比強度大,承載能力高。
第二,材料性能具有可設(shè)計性。樹脂基復(fù)合材料的物理性能、化學(xué)性能、力學(xué)性能都可以通過合理選擇原材料的種類、配比、加工方法、纖維含量和鋪層方式進行設(shè)計,由于樹脂基體材料的種類很多,故其選材設(shè)計的自由度很大。
第三,具有優(yōu)良的耐腐蝕性。樹脂具有優(yōu)良的耐腐蝕性,有針對性的選擇樹脂來生產(chǎn)復(fù)合材料,可以使樹脂基復(fù)合材料具有不同的耐腐蝕性能。
第四,減震性好。由于樹脂基復(fù)合材料震動衰減系數(shù)大,受沖擊時能夠吸收大量的沖擊能,當(dāng)汽車發(fā)生碰撞時,可以避免或減少對乘客的傷害,有利于提高行車的安全性。
第五,工藝成型簡單。樹脂基復(fù)合材料可以用磨具一次成型制造各種構(gòu)件,從而減少了零部件的數(shù)量及接頭等緊固件,節(jié)省原材料和工時,有效降低了生產(chǎn)成本。在中等批量生產(chǎn)的車型中,用樹脂基復(fù)合材料代替鋁材可以降低成本40%左右。此外,樹脂基復(fù)合材料對缺口、應(yīng)力集中敏感性小,而且纖維和集體潔面能夠阻止和改變裂紋擴展方向,因此具有較高的疲勞極限。

按樹脂基體分類,可以將樹脂基復(fù)合材料分為熱固性樹脂和熱塑性樹脂兩種。熱固性樹脂初加熱時軟化,可塑造成型,但固化后再加熱時將不再軟化,也不溶于溶劑。常用的熱固性樹脂有酚醛樹脂、環(huán)氧樹脂、不飽和聚醋樹脂和有機硅樹脂等。熱塑性樹脂加熱時會軟化和熔融,可塑造成型,冷卻后即成型并保持即得形狀,這一過程具有重復(fù)性。應(yīng)用較多的熱塑性樹脂是:尼龍、聚烯烴類、聚苯乙烯類、熱塑性聚醋和聚碳酸醋等。
車用復(fù)合材料的樹脂基體,目前仍以熱固性樹脂為主,但熱固性復(fù)合材料的缺點是廢棄物回收再利用困難。隨著國際社會對環(huán)境保護的要求越來越高,熱塑性樹脂基復(fù)合材料越來越受到人們的關(guān)注。與熱固性樹脂基復(fù)合材料相比,熱塑性樹脂基復(fù)合材料有許多優(yōu)點。例如斷裂韌性高、成型過程中無化學(xué)反應(yīng),因此成型速度快,成型周期短;預(yù)浸料可以無限期存放,且對存放無特殊要求,易于回收再利用,不環(huán)境污染;能夠?qū)崿F(xiàn)快速、無污染、自動化生產(chǎn)。所以近年來汽車用熱塑性復(fù)合材料的增長速度高于熱固性復(fù)合材料。
應(yīng)用
樹脂基復(fù)合材料在汽車上用途廣泛,可用于制造汽車外板、汽車結(jié)構(gòu)件、發(fā)動機及發(fā)動機周邊部件等。應(yīng)用范圍由內(nèi)飾件、覆蓋件向外裝件、結(jié)構(gòu)件和功能件發(fā)展。發(fā)動機及發(fā)動機周邊部件以往通常使用金屬材料制造,從1990年開始樹脂基復(fù)合材料被大量應(yīng)用于汽車發(fā)動機部件。美國通用汽車公司首先將它應(yīng)用于3.3/3.SLV6轎車發(fā)動機氣門罩殼上,用它代替金屬罩殼。
傳統(tǒng)的車身材料通常采用高強度薄鋼板,為了減輕汽車自重,采用樹脂基復(fù)合材料代替鋼材,已成為車身結(jié)構(gòu)發(fā)展的必然趨勢。通用公司早在1953年就推出克爾維特(Corvette)牌全塑車身的轎車,除翼子板用尼龍注射成型外,所有殼體都是用玻璃纖維增強塑料(FRP)壓鑄模塑成型的。到1980年已有65%的美國轎車采用玻璃鋼片狀模塑料作前臉和散熱器護柵板。目前樹脂基復(fù)合材料已被廣泛應(yīng)用于車身結(jié)構(gòu)件(如骨架、梁、柱等)、覆蓋件(如前臉面罩、前翼子板、發(fā)動機罩、頂蓋、車門、行李箱蓋、后側(cè)板等)以及保險杠、油箱等。
與鋼鐵材料、鋁合金等傳統(tǒng)材料相比,樹脂基復(fù)合材料具有重量輕、比強度高、耐腐蝕、減振性能好、可設(shè)計性強、易于加工等優(yōu)點。盡管樹脂基復(fù)合材料的許多優(yōu)點使其很好地適應(yīng)了汽車工業(yè)的發(fā)展要求,但其存在的一些缺點也是現(xiàn)代汽車工業(yè)所不能容忍的,如:原材料成本較高、彈性模量較低、材料特性分散性大、生產(chǎn)周期較長、可回收性差等。目前,樹脂基復(fù)合材料的加工方法仍不成熟,難以進行大規(guī)模商業(yè)化生產(chǎn)。作為汽車上重要的輕量化材料,樹脂基復(fù)合材料越來越多地取代了傳統(tǒng)的金屬材料,其應(yīng)用范圍由汽車內(nèi)裝飾件、覆蓋件向外裝件、結(jié)構(gòu)件方向發(fā)展,隨著生產(chǎn)工藝的進步,樹脂基復(fù)合材料在汽車工業(yè)中應(yīng)用前景十分廣闊。
市場容量測算
我們希望更加量化地測算出汽車輕量化的市場規(guī)模。由于汽車輕量化是一個系統(tǒng)性、復(fù)雜性的工程,所以我們只能推算出某種材料最大理論市場規(guī)模。具體方法如下:
1) 對比目前國內(nèi)外車重的差距,計算出替代材料單個車輛的需求。
2) 從單車需求推導(dǎo)出整體需求。
3) 根據(jù)材料價格推算出市場規(guī)模。
國內(nèi)外汽車輕量化的差距
汽車輕量化在發(fā)達國家已經(jīng)推廣了十幾年了,目前全球最大的輕量化市場在北美,歐洲為第二大市場。中國在汽車輕量化方面才剛剛起步,但是發(fā)展勢頭比較迅猛。
由于目前國內(nèi)政策并沒有把汽車輕量化的減重目標做量化規(guī)定,所以我們把最發(fā)達的美國減重目標作為對標標的。美國輕量化的汽車的發(fā)展目標:2020年要在13年的基礎(chǔ)上降重20%,2025年要降重30%。由此,我們假設(shè)未來中國汽車輕量化目標也在減重20%左右。
目前汽車車身主要材料還是以鋼為原材料,車身重量大約在1100kg左右。在下文中我們將對碳纖維、玻纖、鎂合金、樹脂等材料做定量分析,來計算出理論市場規(guī)模。
各種材料市場規(guī)模測算
鋼鐵的密度是7.8;碳纖維密度是1.8;玻纖密度是2.6;鎂合金密度是1.8;樹脂密度是1.4-2.2左右(為了保守預(yù)計,我們?nèi)?.2為樹脂密度)。
工信部苗圩部長接受采訪時提出,2020年中國新能源車藥占比達到10%。目前中國汽車產(chǎn)量在每年2600萬輛左右,預(yù)計到2020年這個數(shù)字將達到3000萬輛。保守起見,我們預(yù)計2020年新能源汽車生產(chǎn)數(shù)量為150萬輛。
由于輕量化目標是減重20%,所以1100kg的車身減重的重量理論上為220kg。從中我們可以計算出替代物的替代規(guī)模,推導(dǎo)出理論市場規(guī)模。計算結(jié)果見下表。

圖:2020年輕量化材料理論市場規(guī)模
根據(jù)中國產(chǎn)業(yè)信息網(wǎng)信息,目前碳纖維的價格在200元/kg;玻纖6元/kg;鎂合金30元/kg;樹脂10元/kg。如果在2020年新能源汽車規(guī)模能夠達到150萬輛,普通車規(guī)模能夠達到3000萬輛,則上述各材料對應(yīng)市場規(guī)模如下:碳纖維:200億/4000億;玻纖:10億/ 200億;鎂合金:30億/約600億;樹脂:13億/約260億。目前我國在這些產(chǎn)業(yè)的產(chǎn)能和市場規(guī)模分別是:碳纖維:約5000噸/約10億;玻纖:約400萬噸/約240億;鎂合金:約50萬噸/約150億;樹脂:約500萬噸/約500億。
從潛在市場規(guī)模對比現(xiàn)有市場規(guī)模來看,影響力從大到小排序分別為:碳纖維、鎂合金、樹脂、玻纖。
編輯推薦
最新資訊
-
跨越速運憑什么“圈粉”萬千客戶?“
2025-07-01 14:42
-
數(shù)智破局啟新篇?生態(tài)共生再啟程 —
2025-06-27 20:13
-
助力汽車零部件產(chǎn)線智能化升級,西門
2025-06-27 13:59
-
BBA集體轉(zhuǎn)向!放棄全面電動化
2025-06-26 17:32
-
比換柜省錢,比自研省心,西門子Xcel
2025-06-25 15:07