自動(dòng)化技術(shù)在沖壓生產(chǎn)線建設(shè)中的應(yīng)用
2018-06-06 09:43:37· 來(lái)源:文/孫逸仙 鍛造與沖壓
沖壓自動(dòng)化生產(chǎn)線是汽車(chē)覆蓋件沖壓生產(chǎn)的重要組成部分,在新建沖壓生產(chǎn)線的前期規(guī)劃中,要結(jié)合汽車(chē)覆蓋件的生產(chǎn)特點(diǎn),合理規(guī)劃生產(chǎn)線的功能與主要設(shè)備。自動(dòng)化生產(chǎn)線的優(yōu)勢(shì)主要體現(xiàn)在生產(chǎn)節(jié)拍的提升、沖壓件成本的降低以及沖壓件品質(zhì)的提
沖壓自動(dòng)化生產(chǎn)線是汽車(chē)覆蓋件沖壓生產(chǎn)的重要組成部分,在新建沖壓生產(chǎn)線的前期規(guī)劃中,要結(jié)合汽車(chē)覆蓋件的生產(chǎn)特點(diǎn),合理規(guī)劃生產(chǎn)線的功能與主要設(shè)備。自動(dòng)化生產(chǎn)線的優(yōu)勢(shì)主要體現(xiàn)在生產(chǎn)節(jié)拍的提升、沖壓件成本的降低以及沖壓件品質(zhì)的提高等。本文結(jié)合我廠沖壓生產(chǎn)線的建設(shè),闡述了自動(dòng)化技術(shù)的應(yīng)用對(duì)于效率提升、質(zhì)量提升以及成本降低方面的貢獻(xiàn),供工藝設(shè)計(jì)人員參考。
生產(chǎn)線規(guī)劃和設(shè)備選型
自動(dòng)化生產(chǎn)線規(guī)劃的背景
為適應(yīng)產(chǎn)品設(shè)計(jì)大型化、集成化特點(diǎn),滿足高標(biāo)準(zhǔn)產(chǎn)品質(zhì)量、制造成本降低、安全環(huán)保及職業(yè)健康等多方面要求,工廠原有手工生產(chǎn)線無(wú)法應(yīng)對(duì),需新建大型自動(dòng)化沖壓生產(chǎn)線來(lái)適應(yīng)公司的發(fā)展需求。為此,規(guī)劃建設(shè)了一條應(yīng)對(duì)大型零件生產(chǎn)的沖壓自動(dòng)化生產(chǎn)線。
自動(dòng)化生產(chǎn)線設(shè)備選型
沖壓車(chē)間的生產(chǎn)工藝主要有沖壓毛坯的生產(chǎn)和沖壓覆蓋件的生產(chǎn),其他還有試模、模具維修、沖壓件返修、廢料輸送等輔助工作。
壓機(jī)設(shè)備的參數(shù)根據(jù)各車(chē)型零件的生產(chǎn)工藝確定,零件均在4序內(nèi)完成沖壓,A、B、C各車(chē)型最大零件的沖壓力如表1所示。
根據(jù)上表沖裁力需求,為保障壓力機(jī)設(shè)備能力持有約10%的成形余裕度,首臺(tái)壓力機(jī)選型2400t,后續(xù)三臺(tái)壓力機(jī)選型1000t。考慮車(chē)型零件品種數(shù)量較多,為了適應(yīng)多規(guī)格品種零件的生產(chǎn),增加生產(chǎn)線柔性,生產(chǎn)線搬運(yùn)設(shè)備選用機(jī)器人,線首拆跺、上料及線尾下料采用6軸機(jī)器人,線間傳輸采用直線7軸機(jī)器人。全自動(dòng)沖壓生產(chǎn)線如圖1所示。
表1 零件沖壓成形/沖裁力需求分析表
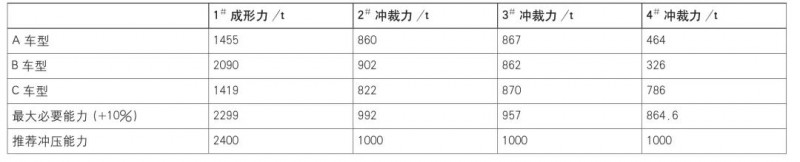
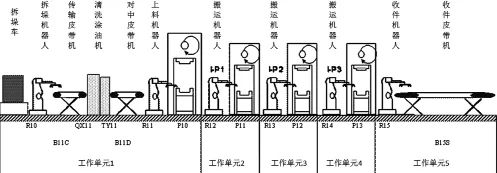
圖1 1×2400t+3×1000t全自動(dòng)沖壓生產(chǎn)線
生產(chǎn)線自動(dòng)化技術(shù)應(yīng)用亮點(diǎn)
伺服液壓拉深技術(shù)應(yīng)用
傳統(tǒng)生產(chǎn)方式采取氣動(dòng)拉深墊進(jìn)行拉延平衡,無(wú)法實(shí)現(xiàn)靈活的設(shè)定和壓力的精確穩(wěn)定,無(wú)法保證大型、深拉延件的穩(wěn)定生產(chǎn),經(jīng)常會(huì)發(fā)生零件質(zhì)量波動(dòng),開(kāi)裂等現(xiàn)象,需要大量涂抹拉延油以維持生產(chǎn),帶來(lái)了環(huán)境污染、涂裝后處理困難、零件起皺等一系列問(wèn)題,部分零件只能通過(guò)氮?dú)飧讖椈蓧毫?、雙動(dòng)結(jié)構(gòu)等模具設(shè)計(jì)來(lái)應(yīng)對(duì),但效果仍難以保證。
為滿足我廠A、B、C等車(chē)型超大型深拉延件穩(wěn)定生產(chǎn),根據(jù)工廠多年技術(shù)經(jīng)驗(yàn)的積累,尤其從A項(xiàng)目至C項(xiàng)目的工藝分析工作、同步工程工作形成的經(jīng)驗(yàn)積累,對(duì)深拉延件的成形過(guò)程,條件需求形成了一定的規(guī)范,最終經(jīng)過(guò)技術(shù)研討,確定采用伺服液壓拉深技術(shù)配置新建設(shè)的沖壓自動(dòng)化生產(chǎn)線。
首臺(tái)2400t多連桿機(jī)械壓力機(jī),配置伺服液壓拉深墊;后序3臺(tái)為偏心式機(jī)械壓力機(jī),具備全線自動(dòng)換模功能,伺服液壓墊結(jié)構(gòu)示意圖如圖2所示。
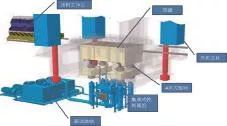
圖2 伺服液壓墊結(jié)構(gòu)示意圖
.jpg)
圖3 前圍擋板拉延模擬成形圖
⑴驅(qū)動(dòng)結(jié)構(gòu)。驅(qū)動(dòng)結(jié)構(gòu)由四個(gè)活塞缸驅(qū)動(dòng)布置在拉深墊頂罐的四角,通過(guò)獨(dú)立PLC編程控制各點(diǎn)的壓力值。從圖3車(chē)型前圍擋板CAE模擬結(jié)果可見(jiàn),在零件基本對(duì)稱設(shè)計(jì)的情況下,4點(diǎn)式壓力輸出已可以滿足產(chǎn)品生產(chǎn)需要,不需中間輸出點(diǎn),這一原則基本可滿足商用車(chē)大型覆蓋件生產(chǎn)。
⑵伺服液壓拉深技術(shù)的功能。
1)拉深壓力靈活設(shè)定。液壓拉深墊四點(diǎn)壓力單獨(dú)設(shè)定,數(shù)據(jù)可以存入壓力機(jī)控制系統(tǒng)的模具參數(shù)數(shù)據(jù)庫(kù),在自動(dòng)換模過(guò)程中與其他模具參數(shù)一起調(diào)出。
2)帶預(yù)加速的拉深。伺服液壓墊配置有預(yù)加速功能,在啟動(dòng)預(yù)加速功能時(shí),拉深墊在滑塊下降時(shí)不停留在上限位置,而是先于滑塊向下移動(dòng)。在運(yùn)行30mm后,滑塊趕上了拉深墊,繼續(xù)運(yùn)行,形成反力,拉深過(guò)程開(kāi)始。拉深墊的返回運(yùn)動(dòng)與滑塊同步或延遲回程,避免零件碰撞,方便取料,也可實(shí)現(xiàn)滑塊下死點(diǎn)保壓。液壓拉深墊在不使用預(yù)加速功能的情況下,部分區(qū)域板料變形率不足如圖4所示。在拉深過(guò)程中增加預(yù)加速功能后,板料變形變得相對(duì)均勻如圖5所示。
預(yù)加速功能目前無(wú)法使用CAE方式進(jìn)行模擬,我們通過(guò)參數(shù)置換等方式粗略模擬這種情況,該功能會(huì)提高生產(chǎn)的穩(wěn)定性,拉延變形效果更均勻,最終根據(jù)壓力機(jī)參數(shù)曲線完成預(yù)加速參數(shù)設(shè)計(jì)。
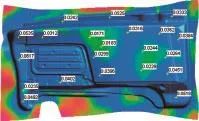
圖4 未使用預(yù)加速功能的零件成形情況
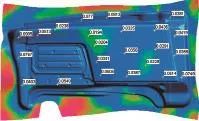
圖5 使用預(yù)加速功能的零件成形情況
3)生產(chǎn)參數(shù)數(shù)字化控制。液壓驅(qū)動(dòng)系統(tǒng)狀態(tài)與壓力機(jī)PLC連接,可實(shí)現(xiàn)設(shè)定、狀態(tài)監(jiān)控、故障報(bào)警、數(shù)據(jù)實(shí)時(shí)反饋以及設(shè)定的生產(chǎn)參數(shù)調(diào)用等。采用伺服液壓拉深技術(shù)可提高拉延件穩(wěn)定性,返修率降低10%,廢品率降低2%。對(duì)C車(chē)型部分零件而言,采用單動(dòng)拉延設(shè)計(jì)、取消氮?dú)鈴椈?,可?jié)約模具投入約100萬(wàn)元。
自動(dòng)化生產(chǎn)中板料上料對(duì)中系統(tǒng)
整線自動(dòng)化包含線首、線間、線尾三個(gè)部分。線首通過(guò)采用視覺(jué)加機(jī)械對(duì)中系統(tǒng),可有效提升可靠性和生產(chǎn)線柔性。線間配置的直線七軸機(jī)器人可大幅提升生產(chǎn)線節(jié)拍。線尾配置六軸機(jī)器人下料,在滿足下料需求的前提下,可降低投資成本。
⑴柔性化對(duì)中系統(tǒng)組成。
1)一套獨(dú)立安裝的拍攝和照明系統(tǒng)(圖6)。燈架安裝在防護(hù)罩上與壓力機(jī)等運(yùn)動(dòng)機(jī)構(gòu)軟連接,落地支撐在車(chē)間地坪上,避免振動(dòng)。燈具選用LED節(jié)能燈,拍攝區(qū)域照度800Lux以上,廣角高清攝像頭拍攝范圍2.5m×3m。
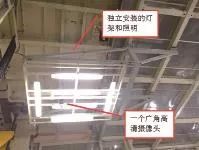
圖6 照明系統(tǒng)示意圖

圖7 對(duì)中平臺(tái)示意圖
2)多條同步帶組合限位檢測(cè)的對(duì)中平臺(tái)。圖7所示對(duì)中皮帶采用10條圓形同步帶,單條獨(dú)立變頻驅(qū)動(dòng)電機(jī)驅(qū)動(dòng),確保同步及到位準(zhǔn)確,皮帶間隔300mm,間隔區(qū)域內(nèi)安裝2組檢測(cè)開(kāi)關(guān),控制皮帶緩沖速度、停止。最前端設(shè)置翻轉(zhuǎn)擋塊,料寬大于300mm時(shí),可防止板料送進(jìn)過(guò)程意外飛出,主要用于調(diào)試階段工人的安全保護(hù)。底色采用黑色整塊2.5m×3m底板,與材料顏色形成對(duì)比,利于成像。
3)過(guò)渡工位。圖8所示過(guò)渡工位布置在前段清洗涂油機(jī)和對(duì)中工位中間,用于承接前段板料處理,此時(shí)運(yùn)行速度與清洗機(jī)速度匹配,同時(shí)用于給對(duì)中工位及時(shí)送料,此時(shí)速度與對(duì)中工位匹配,確保及時(shí)送料和控制板料初速度,速度指令有整線PLC根據(jù)送料邏輯發(fā)送,一次示教后自動(dòng)調(diào)用。
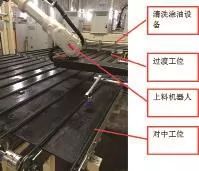
圖8 過(guò)渡工位示意圖
⑵柔性化對(duì)中系統(tǒng)優(yōu)勢(shì)。
該系統(tǒng)采用組合式的對(duì)中平臺(tái)設(shè)計(jì),確保板料到位精度,并適應(yīng)任何形狀的板料。雙工位的對(duì)中設(shè)計(jì),能有效確保整線上料節(jié)拍要求。圓形條式對(duì)中皮帶組合機(jī)械式檢測(cè)及可調(diào)式限位設(shè)計(jì)可準(zhǔn)確保障板料的對(duì)中效果。
該系統(tǒng)與傳統(tǒng)機(jī)械式對(duì)中系統(tǒng)相比,減少了20組可調(diào)式限位機(jī)構(gòu),節(jié)約投資成本約20萬(wàn)元。由于該系統(tǒng)的柔性化程度較高,可有效避免后期產(chǎn)品拓展時(shí)的設(shè)備改造和報(bào)廢。
零件柔性搬運(yùn)系統(tǒng)
零件在壓力機(jī)之間的搬運(yùn)采用直線7軸機(jī)器人,其技術(shù)優(yōu)點(diǎn)總結(jié)如下:
⑴工件在生產(chǎn)過(guò)程中始終保持平行移動(dòng),無(wú)須旋轉(zhuǎn)。這有益于提高工件在上下工序壓力機(jī)之間的傳遞速度,進(jìn)而提高生產(chǎn)線的效率,尤其是在生產(chǎn)“整體頂蓋”等大型覆蓋件時(shí),優(yōu)勢(shì)更明顯。
⑵工件在上下工序壓力機(jī)之間傳遞時(shí)保持平行移動(dòng)方式,可以使大型工件在較小的空間內(nèi)傳遞,減小壓力機(jī)之間的間距,也就減少整條沖壓線在廠房?jī)?nèi)的占地面積,從而降低廠房的建設(shè)成本。
⑶采用直線七軸技術(shù)的機(jī)器人搬運(yùn)系統(tǒng)適應(yīng)性強(qiáng),柔性化高。在該沖壓自動(dòng)線上,小至“側(cè)圍內(nèi)板”,大至“整體頂蓋”等沖壓件均可以全自動(dòng)化高效生產(chǎn)。
⑷配合大型機(jī)器人,直線七軸裝置的有效負(fù)載能力強(qiáng)。在該沖壓自動(dòng)線上,配置直線七軸技術(shù)的機(jī)器人選用的是ABB IRB7600 325/3.1型機(jī)器人,直線七軸裝置端部的負(fù)載能力可以達(dá)到90kg。減去端拾器和剛朵拉的重量,可以提供60kg的負(fù)載能力給沖壓件,這已經(jīng)足夠滿足商用車(chē)覆蓋件的重量。
結(jié)束語(yǔ)
自動(dòng)化技術(shù)在沖壓生產(chǎn)線中的應(yīng)用已非常成熟廣泛,選擇適應(yīng)公司產(chǎn)品規(guī)劃要求的工藝設(shè)備是首要考量的關(guān)注點(diǎn),在選擇生產(chǎn)線設(shè)備及功能配置時(shí),如何運(yùn)用自動(dòng)化技術(shù)減少投資費(fèi)用、降低后期設(shè)備維護(hù)費(fèi)用、降低產(chǎn)品廢品率,從而達(dá)到降低制造成本提升產(chǎn)品競(jìng)爭(zhēng)力的目的,是我們應(yīng)該重點(diǎn)考慮的問(wèn)題。
——節(jié)選自《鍛造與沖壓》2018年第6期
生產(chǎn)線規(guī)劃和設(shè)備選型
自動(dòng)化生產(chǎn)線規(guī)劃的背景
為適應(yīng)產(chǎn)品設(shè)計(jì)大型化、集成化特點(diǎn),滿足高標(biāo)準(zhǔn)產(chǎn)品質(zhì)量、制造成本降低、安全環(huán)保及職業(yè)健康等多方面要求,工廠原有手工生產(chǎn)線無(wú)法應(yīng)對(duì),需新建大型自動(dòng)化沖壓生產(chǎn)線來(lái)適應(yīng)公司的發(fā)展需求。為此,規(guī)劃建設(shè)了一條應(yīng)對(duì)大型零件生產(chǎn)的沖壓自動(dòng)化生產(chǎn)線。
自動(dòng)化生產(chǎn)線設(shè)備選型
沖壓車(chē)間的生產(chǎn)工藝主要有沖壓毛坯的生產(chǎn)和沖壓覆蓋件的生產(chǎn),其他還有試模、模具維修、沖壓件返修、廢料輸送等輔助工作。
壓機(jī)設(shè)備的參數(shù)根據(jù)各車(chē)型零件的生產(chǎn)工藝確定,零件均在4序內(nèi)完成沖壓,A、B、C各車(chē)型最大零件的沖壓力如表1所示。
根據(jù)上表沖裁力需求,為保障壓力機(jī)設(shè)備能力持有約10%的成形余裕度,首臺(tái)壓力機(jī)選型2400t,后續(xù)三臺(tái)壓力機(jī)選型1000t。考慮車(chē)型零件品種數(shù)量較多,為了適應(yīng)多規(guī)格品種零件的生產(chǎn),增加生產(chǎn)線柔性,生產(chǎn)線搬運(yùn)設(shè)備選用機(jī)器人,線首拆跺、上料及線尾下料采用6軸機(jī)器人,線間傳輸采用直線7軸機(jī)器人。全自動(dòng)沖壓生產(chǎn)線如圖1所示。
表1 零件沖壓成形/沖裁力需求分析表
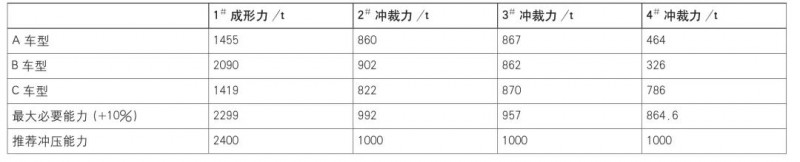
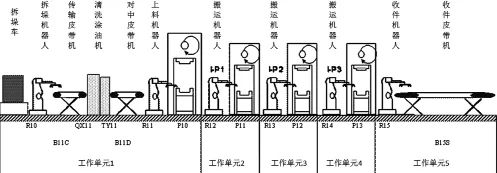
圖1 1×2400t+3×1000t全自動(dòng)沖壓生產(chǎn)線
生產(chǎn)線自動(dòng)化技術(shù)應(yīng)用亮點(diǎn)
伺服液壓拉深技術(shù)應(yīng)用
傳統(tǒng)生產(chǎn)方式采取氣動(dòng)拉深墊進(jìn)行拉延平衡,無(wú)法實(shí)現(xiàn)靈活的設(shè)定和壓力的精確穩(wěn)定,無(wú)法保證大型、深拉延件的穩(wěn)定生產(chǎn),經(jīng)常會(huì)發(fā)生零件質(zhì)量波動(dòng),開(kāi)裂等現(xiàn)象,需要大量涂抹拉延油以維持生產(chǎn),帶來(lái)了環(huán)境污染、涂裝后處理困難、零件起皺等一系列問(wèn)題,部分零件只能通過(guò)氮?dú)飧讖椈蓧毫?、雙動(dòng)結(jié)構(gòu)等模具設(shè)計(jì)來(lái)應(yīng)對(duì),但效果仍難以保證。
為滿足我廠A、B、C等車(chē)型超大型深拉延件穩(wěn)定生產(chǎn),根據(jù)工廠多年技術(shù)經(jīng)驗(yàn)的積累,尤其從A項(xiàng)目至C項(xiàng)目的工藝分析工作、同步工程工作形成的經(jīng)驗(yàn)積累,對(duì)深拉延件的成形過(guò)程,條件需求形成了一定的規(guī)范,最終經(jīng)過(guò)技術(shù)研討,確定采用伺服液壓拉深技術(shù)配置新建設(shè)的沖壓自動(dòng)化生產(chǎn)線。
首臺(tái)2400t多連桿機(jī)械壓力機(jī),配置伺服液壓拉深墊;后序3臺(tái)為偏心式機(jī)械壓力機(jī),具備全線自動(dòng)換模功能,伺服液壓墊結(jié)構(gòu)示意圖如圖2所示。
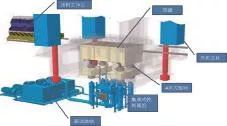
圖2 伺服液壓墊結(jié)構(gòu)示意圖
.jpg)
圖3 前圍擋板拉延模擬成形圖
⑴驅(qū)動(dòng)結(jié)構(gòu)。驅(qū)動(dòng)結(jié)構(gòu)由四個(gè)活塞缸驅(qū)動(dòng)布置在拉深墊頂罐的四角,通過(guò)獨(dú)立PLC編程控制各點(diǎn)的壓力值。從圖3車(chē)型前圍擋板CAE模擬結(jié)果可見(jiàn),在零件基本對(duì)稱設(shè)計(jì)的情況下,4點(diǎn)式壓力輸出已可以滿足產(chǎn)品生產(chǎn)需要,不需中間輸出點(diǎn),這一原則基本可滿足商用車(chē)大型覆蓋件生產(chǎn)。
⑵伺服液壓拉深技術(shù)的功能。
1)拉深壓力靈活設(shè)定。液壓拉深墊四點(diǎn)壓力單獨(dú)設(shè)定,數(shù)據(jù)可以存入壓力機(jī)控制系統(tǒng)的模具參數(shù)數(shù)據(jù)庫(kù),在自動(dòng)換模過(guò)程中與其他模具參數(shù)一起調(diào)出。
2)帶預(yù)加速的拉深。伺服液壓墊配置有預(yù)加速功能,在啟動(dòng)預(yù)加速功能時(shí),拉深墊在滑塊下降時(shí)不停留在上限位置,而是先于滑塊向下移動(dòng)。在運(yùn)行30mm后,滑塊趕上了拉深墊,繼續(xù)運(yùn)行,形成反力,拉深過(guò)程開(kāi)始。拉深墊的返回運(yùn)動(dòng)與滑塊同步或延遲回程,避免零件碰撞,方便取料,也可實(shí)現(xiàn)滑塊下死點(diǎn)保壓。液壓拉深墊在不使用預(yù)加速功能的情況下,部分區(qū)域板料變形率不足如圖4所示。在拉深過(guò)程中增加預(yù)加速功能后,板料變形變得相對(duì)均勻如圖5所示。
預(yù)加速功能目前無(wú)法使用CAE方式進(jìn)行模擬,我們通過(guò)參數(shù)置換等方式粗略模擬這種情況,該功能會(huì)提高生產(chǎn)的穩(wěn)定性,拉延變形效果更均勻,最終根據(jù)壓力機(jī)參數(shù)曲線完成預(yù)加速參數(shù)設(shè)計(jì)。
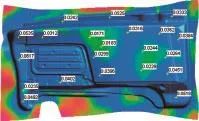
圖4 未使用預(yù)加速功能的零件成形情況
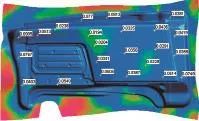
圖5 使用預(yù)加速功能的零件成形情況
3)生產(chǎn)參數(shù)數(shù)字化控制。液壓驅(qū)動(dòng)系統(tǒng)狀態(tài)與壓力機(jī)PLC連接,可實(shí)現(xiàn)設(shè)定、狀態(tài)監(jiān)控、故障報(bào)警、數(shù)據(jù)實(shí)時(shí)反饋以及設(shè)定的生產(chǎn)參數(shù)調(diào)用等。采用伺服液壓拉深技術(shù)可提高拉延件穩(wěn)定性,返修率降低10%,廢品率降低2%。對(duì)C車(chē)型部分零件而言,采用單動(dòng)拉延設(shè)計(jì)、取消氮?dú)鈴椈?,可?jié)約模具投入約100萬(wàn)元。
自動(dòng)化生產(chǎn)中板料上料對(duì)中系統(tǒng)
整線自動(dòng)化包含線首、線間、線尾三個(gè)部分。線首通過(guò)采用視覺(jué)加機(jī)械對(duì)中系統(tǒng),可有效提升可靠性和生產(chǎn)線柔性。線間配置的直線七軸機(jī)器人可大幅提升生產(chǎn)線節(jié)拍。線尾配置六軸機(jī)器人下料,在滿足下料需求的前提下,可降低投資成本。
⑴柔性化對(duì)中系統(tǒng)組成。
1)一套獨(dú)立安裝的拍攝和照明系統(tǒng)(圖6)。燈架安裝在防護(hù)罩上與壓力機(jī)等運(yùn)動(dòng)機(jī)構(gòu)軟連接,落地支撐在車(chē)間地坪上,避免振動(dòng)。燈具選用LED節(jié)能燈,拍攝區(qū)域照度800Lux以上,廣角高清攝像頭拍攝范圍2.5m×3m。
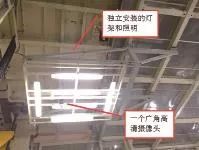
圖6 照明系統(tǒng)示意圖

圖7 對(duì)中平臺(tái)示意圖
2)多條同步帶組合限位檢測(cè)的對(duì)中平臺(tái)。圖7所示對(duì)中皮帶采用10條圓形同步帶,單條獨(dú)立變頻驅(qū)動(dòng)電機(jī)驅(qū)動(dòng),確保同步及到位準(zhǔn)確,皮帶間隔300mm,間隔區(qū)域內(nèi)安裝2組檢測(cè)開(kāi)關(guān),控制皮帶緩沖速度、停止。最前端設(shè)置翻轉(zhuǎn)擋塊,料寬大于300mm時(shí),可防止板料送進(jìn)過(guò)程意外飛出,主要用于調(diào)試階段工人的安全保護(hù)。底色采用黑色整塊2.5m×3m底板,與材料顏色形成對(duì)比,利于成像。
3)過(guò)渡工位。圖8所示過(guò)渡工位布置在前段清洗涂油機(jī)和對(duì)中工位中間,用于承接前段板料處理,此時(shí)運(yùn)行速度與清洗機(jī)速度匹配,同時(shí)用于給對(duì)中工位及時(shí)送料,此時(shí)速度與對(duì)中工位匹配,確保及時(shí)送料和控制板料初速度,速度指令有整線PLC根據(jù)送料邏輯發(fā)送,一次示教后自動(dòng)調(diào)用。
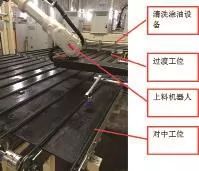
圖8 過(guò)渡工位示意圖
⑵柔性化對(duì)中系統(tǒng)優(yōu)勢(shì)。
該系統(tǒng)采用組合式的對(duì)中平臺(tái)設(shè)計(jì),確保板料到位精度,并適應(yīng)任何形狀的板料。雙工位的對(duì)中設(shè)計(jì),能有效確保整線上料節(jié)拍要求。圓形條式對(duì)中皮帶組合機(jī)械式檢測(cè)及可調(diào)式限位設(shè)計(jì)可準(zhǔn)確保障板料的對(duì)中效果。
該系統(tǒng)與傳統(tǒng)機(jī)械式對(duì)中系統(tǒng)相比,減少了20組可調(diào)式限位機(jī)構(gòu),節(jié)約投資成本約20萬(wàn)元。由于該系統(tǒng)的柔性化程度較高,可有效避免后期產(chǎn)品拓展時(shí)的設(shè)備改造和報(bào)廢。
零件柔性搬運(yùn)系統(tǒng)
零件在壓力機(jī)之間的搬運(yùn)采用直線7軸機(jī)器人,其技術(shù)優(yōu)點(diǎn)總結(jié)如下:
⑴工件在生產(chǎn)過(guò)程中始終保持平行移動(dòng),無(wú)須旋轉(zhuǎn)。這有益于提高工件在上下工序壓力機(jī)之間的傳遞速度,進(jìn)而提高生產(chǎn)線的效率,尤其是在生產(chǎn)“整體頂蓋”等大型覆蓋件時(shí),優(yōu)勢(shì)更明顯。
⑵工件在上下工序壓力機(jī)之間傳遞時(shí)保持平行移動(dòng)方式,可以使大型工件在較小的空間內(nèi)傳遞,減小壓力機(jī)之間的間距,也就減少整條沖壓線在廠房?jī)?nèi)的占地面積,從而降低廠房的建設(shè)成本。
⑶采用直線七軸技術(shù)的機(jī)器人搬運(yùn)系統(tǒng)適應(yīng)性強(qiáng),柔性化高。在該沖壓自動(dòng)線上,小至“側(cè)圍內(nèi)板”,大至“整體頂蓋”等沖壓件均可以全自動(dòng)化高效生產(chǎn)。
⑷配合大型機(jī)器人,直線七軸裝置的有效負(fù)載能力強(qiáng)。在該沖壓自動(dòng)線上,配置直線七軸技術(shù)的機(jī)器人選用的是ABB IRB7600 325/3.1型機(jī)器人,直線七軸裝置端部的負(fù)載能力可以達(dá)到90kg。減去端拾器和剛朵拉的重量,可以提供60kg的負(fù)載能力給沖壓件,這已經(jīng)足夠滿足商用車(chē)覆蓋件的重量。
結(jié)束語(yǔ)
自動(dòng)化技術(shù)在沖壓生產(chǎn)線中的應(yīng)用已非常成熟廣泛,選擇適應(yīng)公司產(chǎn)品規(guī)劃要求的工藝設(shè)備是首要考量的關(guān)注點(diǎn),在選擇生產(chǎn)線設(shè)備及功能配置時(shí),如何運(yùn)用自動(dòng)化技術(shù)減少投資費(fèi)用、降低后期設(shè)備維護(hù)費(fèi)用、降低產(chǎn)品廢品率,從而達(dá)到降低制造成本提升產(chǎn)品競(jìng)爭(zhēng)力的目的,是我們應(yīng)該重點(diǎn)考慮的問(wèn)題。
——節(jié)選自《鍛造與沖壓》2018年第6期
舉報(bào) 0
收藏 0
分享 122
-
乘用車(chē)金屬?zèng)_壓
2025-05-29 -
沖壓技術(shù)在電機(jī)疊片制造的應(yīng)用
2024-09-06 -
車(chē)身零部件包邊質(zhì)量控制要點(diǎn)
2024-09-05 -
輕量化技術(shù)——熱汽脹形工藝技術(shù)解析
2024-09-04
最新資訊
-
跨越速運(yùn)憑什么“圈粉”萬(wàn)千客戶?“
2025-07-01 14:42
-
數(shù)智破局啟新篇?生態(tài)共生再啟程 —
2025-06-27 20:13
-
助力汽車(chē)零部件產(chǎn)線智能化升級(jí),西門(mén)
2025-06-27 13:59
-
BBA集體轉(zhuǎn)向!放棄全面電動(dòng)化
2025-06-26 17:32
-
比換柜省錢(qián),比自研省心,西門(mén)子X(jué)cel
2025-06-25 15:07