碳纖維復(fù)合材料汽車前地板的研制
2018-05-28 13:45:29· 來源:CST汽車輕量化
闡述了通過對碳纖維復(fù)合材料汽車前地板的研制,以金屬白車身為設(shè)計依據(jù)確定了碳纖維復(fù)合材料前地板的結(jié)構(gòu)。分析確定了材料及成型工藝,研究了預(yù)成型體制作,設(shè)計出了多點(diǎn)注射快速RTM模具,并成功制備了碳纖維增強(qiáng)熱固性環(huán)氧復(fù)合材料前地板。產(chǎn)品經(jīng)過剛度及模態(tài)測試,其結(jié)果滿足汽車整車廠提出的技術(shù)要求,而且減重效果明顯,說明碳纖維復(fù)合材料作為主受力結(jié)構(gòu)件在汽車上的應(yīng)用是可行的。
摘要:闡述了通過對碳纖維復(fù)合材料汽車前地板的研制,以金屬白車身為設(shè)計依據(jù)確定了碳纖維復(fù)合材料前地板的結(jié)構(gòu)。分析確定了材料及成型工藝,研究了預(yù)成型體制作,設(shè)計出了多點(diǎn)注射快速RTM模具,并成功制備了碳纖維增強(qiáng)熱固性環(huán)氧復(fù)合材料前地板。產(chǎn)品經(jīng)過剛度及模態(tài)測試,其結(jié)果滿足汽車整車廠提出的技術(shù)要求,而且減重效果明顯,說明碳纖維復(fù)合材料作為主受力結(jié)構(gòu)件在汽車上的應(yīng)用是可行的。
關(guān)鍵詞:復(fù)合材料;汽車前地板;RTM成型
1概 述
隨著汽車輕量化不斷發(fā)展,節(jié)能、環(huán)保、安全、舒適已成為當(dāng)今材料界和汽車界的研究熱點(diǎn)。研究顯示,車重每減少100kg,每百公里油耗可降低0.3~0.5L,二氧化碳的排放可以減少12g左右。車重減輕,可以提高車輛的加速度和制動效果。傳統(tǒng)汽車鋼鐵材料約占車體總重的3/4,用碳纖維增強(qiáng)復(fù)合材料(CFRP)制造的車身和底盤在等剛度、等強(qiáng)度下可以減重40%~60%,相當(dāng)于鋼結(jié)構(gòu)的1/3~1/6。因此,CFRP正日益成為汽車輕量化的首選材料,逐漸得到汽車行業(yè)越來越廣泛的認(rèn)可和應(yīng)用。
2015年國內(nèi)碳纖維需求總量為1.3萬噸左右,如果保持平穩(wěn)增長態(tài)勢,預(yù)計2020年將達(dá)到2.5萬噸。目前,我國復(fù)合材料在汽車工業(yè)中年用量比例還很小,因此,開發(fā)碳纖維復(fù)合材料在汽車上的應(yīng)用研究具有很大的發(fā)展空間和應(yīng)用前景。本文以碳纖維復(fù)合材料汽車前地板的研制為例,對其結(jié)構(gòu)方案設(shè)計、纖維預(yù)成型體制作、成型工藝及性能測試進(jìn)行了研究。
2結(jié)構(gòu)設(shè)計方案
2. 1 結(jié)構(gòu)設(shè)計依據(jù)
目標(biāo)產(chǎn)品以金屬白車身為設(shè)計依據(jù),原金屬汽車前地板橫截面呈“幾”字形,外形尺寸為1.7m×1.3m,重量為27.7kg,金屬板厚為0.8mm左右,由21個板金沖壓件組裝焊接而成,如圖1所示。
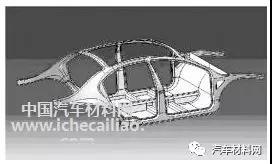
圖 1 汽車白車身
2. 2 性能要求
減重:與金屬鋼制地板相比,減重不低于40%;
彎曲剛度:在1kN載荷下,中心點(diǎn)垂直撓度應(yīng)小于2mm;
扭轉(zhuǎn)剛度:≥104N·m2/rad;
一階模態(tài):≥20Hz。
2. 3 碳纖維復(fù)合材料地板設(shè)計過程
由于原金屬汽車前地板零部件比較多,在復(fù)合材料成型中采用一體成型比較困難,為了充分發(fā)揮碳纖維復(fù)合材料性能及適應(yīng)復(fù)合材料成型工藝特點(diǎn),需要將原鋼制地板結(jié)構(gòu)進(jìn)行局部的設(shè)計修改,修改內(nèi)容主要有如下幾個方面:
(1)取消加強(qiáng)筋板及多余的復(fù)雜筋條:充分發(fā)揮碳纖維復(fù)合材料的比強(qiáng)度、比模量高和可設(shè)計性強(qiáng)等的優(yōu)點(diǎn),根據(jù)等剛度設(shè)計原則,在前地板不同受力部位設(shè)計不同厚度CFRP,盡量取消加強(qiáng)筋板及多余的復(fù)雜筋條;
(2)取消工藝漏液孔:碳纖維復(fù)合材料前地板不同于鋼制地板,產(chǎn)品焊接組裝完成后無需在涂裝車間進(jìn)行電泳工序,所以可以取消各工藝漏液孔;
(3)在碳纖維零部件設(shè)計時,對于影響鋪設(shè)成型的小圓角要盡量避免,原則上內(nèi)角R≥3mm,以利于在模具上鋪設(shè)成型,個別特殊部位可以將內(nèi)角設(shè)計成R≥2mm,但會降低量產(chǎn)效率,應(yīng)盡量避免;
(4)在碳纖維零部件壁厚不同的部位,應(yīng)逐漸過渡,以免在成型固化過程中,因固化收縮不同而產(chǎn)生較大變形。
根據(jù)以上設(shè)計原則,重新修改設(shè)計后的前地板數(shù)模如圖2所示。根據(jù)預(yù)先的有限元模擬,為了能夠達(dá)到與原金屬汽車前地板相同的剛度值,復(fù)合材料汽車前地板主板厚度為2.5mm,中央通道部分厚度為3.0mm。
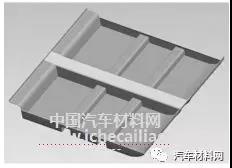
圖 2 碳纖維復(fù)合材料前地板數(shù)模
3成型工藝及試制
3. 1 原材料
對于汽車前地板這種主受力結(jié)構(gòu)件,一般需要首選快速成型的碳纖維復(fù)合材料。本項(xiàng)目設(shè)計選用性能較好的日本東麗碳纖維T700CS-12K織物,面密度分別為480g/m2和200g/m2;單軸向布為200g/m2。樹脂體系選用快速固化的環(huán)氧樹脂體系EpoTech167A/167B(廣州博匯)。
3. 2 成型工藝
復(fù)合材料成本已成為制約復(fù)合材料規(guī)?;瘧?yīng)用的瓶頸,以快速RTM成型技術(shù)為代表的低成本復(fù)合材料技術(shù)已成為目前復(fù)合材料領(lǐng)域的研究熱點(diǎn)之一。RTM工藝具有一系列的優(yōu)點(diǎn),可以一次性快速成型大型、復(fù)雜(包括帶夾芯或插件)的構(gòu)件;無需膠衣涂層即可為構(gòu)件提供光滑表面,后處理工作量??;預(yù)成型體尺寸易控,可設(shè)計性強(qiáng);生產(chǎn)周期適中,可實(shí)現(xiàn)半自動或自動化生產(chǎn),效率高;纖維含量較高;能夠應(yīng)用計算機(jī)輔助設(shè)計進(jìn)行模具和產(chǎn)品設(shè)計,可實(shí)現(xiàn)充模過程的模擬;無需二次粘接。鑒于以上技術(shù)優(yōu)點(diǎn),本項(xiàng)目選用了快速RTM成型工藝試制地板。
3. 3 纖維預(yù)成型體制作
纖維預(yù)成型技術(shù)是RTM工藝的一個重要環(huán)節(jié)。對質(zhì)量要求高、性能穩(wěn)定、結(jié)構(gòu)復(fù)雜、自動化程度要求高的制品來說,這項(xiàng)技術(shù)顯得尤為重要。其原理是采用增粘劑/定型劑或編織/縫紉等技術(shù)將增強(qiáng)材料固結(jié)成與制品相同形狀的半成品。纖維預(yù)成型技術(shù)在保證產(chǎn)品質(zhì)量、生產(chǎn)工藝快速及自動化方面具有重要意義,是實(shí)施RTM低成本化的重要途徑及手段。
根據(jù)汽車前地板結(jié)構(gòu)特點(diǎn),將其設(shè)計為由5個單獨(dú)的預(yù)成型件縫合組裝成一個整體。該預(yù)成型件采用了美國Airtech公司研制生產(chǎn)的Airtac 2增粘劑,通過研究確定最佳工藝參數(shù)為:增粘劑噴涂量為3%~5%、定型加熱溫度為90~100℃、定型時間為20~25min。
3. 4 基于多點(diǎn)注射的快速RTM模具設(shè)計技術(shù)
根據(jù)碳纖維復(fù)合材料前地板的結(jié)構(gòu)特征以及RTM模具與合模液壓機(jī)配合使用考慮,模具的結(jié)構(gòu)類型可以采用多點(diǎn)澆口的三板式注射模具。對于該汽車前地板制件而言,產(chǎn)品需要裝車驗(yàn)證,尺寸精度要求較;因產(chǎn)品結(jié)構(gòu)復(fù)雜、尺寸大,所以注膠過程中的壓力也較高;生產(chǎn)效率較高,要求快速成型,所以材料的導(dǎo)熱性能要好。另外,該模具需采用現(xiàn)有的100t合模液壓機(jī)作為啟模、閉模的機(jī)構(gòu),模具重量不易過大。經(jīng)初步設(shè)計分析,如果采用鋼模,模具重量達(dá)12t左右,而采用鋁模,其重量僅5t左右。綜合以上考慮,該汽車地板RTM模具采用了高強(qiáng)度鋁合金材料。
考慮到鋁合金比鋼材的硬度小,在設(shè)計鋁合金模具時還應(yīng)在一些細(xì)節(jié)上進(jìn)行如下考慮:①如果在鋁合金模具上加工螺紋孔,為了防止螺牙被螺栓磨損,需要安裝鋼絲螺套;②模具上設(shè)置的頂出點(diǎn)需要安裝鋼墊塊;③導(dǎo)柱采用軸承套導(dǎo)柱,減少導(dǎo)柱的摩擦力。圖3為該模具總體設(shè)計結(jié)構(gòu)。
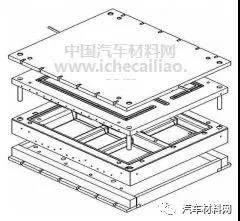
圖3總體結(jié)構(gòu)爆炸圖
3. 5 碳纖維增強(qiáng)熱固性環(huán)氧樹脂復(fù)合材料前地板試制
主要工藝參數(shù): 膠液溫度為50℃,模具溫度為55℃,注膠流量為10~20mL/s,固化溫度為90℃,保溫時間為20min,為了預(yù)防在注膠過程中發(fā)生爆模,注膠壓力不得超過1MPa。產(chǎn)品從注膠到脫模,成型周期在30min以下,基本達(dá)到了RTM快速成型的要求。
4試驗(yàn)結(jié)果
4. 1 重 量
產(chǎn)品重量為16.0kg,與鋼制地板相比減重42%,滿足設(shè)計指標(biāo)要求。
4. 2 靜態(tài)彎曲剛度測試
將樣件安裝及固定在彎曲剛度測試臺上,調(diào)平。樣件的固定位置如圖4所示。
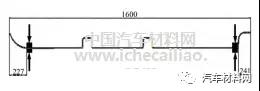
圖4 樣件彎曲剛度測試夾持位置圖
在樣件中心位置分別按照50.10kg、(50.10kg+30.45kg)、(50.10kg+30.45kg+20.30kg)三個加載塊順序加載,并記錄各測點(diǎn)的變形量。彎曲剛度測試數(shù)據(jù)見表1。
表1彎曲剛度測試數(shù)據(jù)表
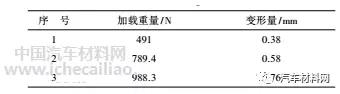
注:加載點(diǎn)和測量點(diǎn)均在樣件中心位置。
根據(jù)圖5所示地板彎曲剛度加載-變形圖可知:碳纖維復(fù)合材料地板中心在1kN載荷下,中心點(diǎn)垂直撓度為0.76mm,滿足設(shè)計指標(biāo)小于2mm的要求。
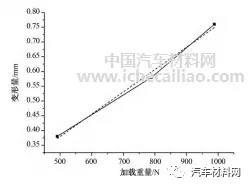
圖5地板彎曲剛度加載-變形圖
4. 3 扭轉(zhuǎn)剛度測試
將樣件安裝固定在扭轉(zhuǎn)剛度測試臺上,調(diào)平。在樣件扭轉(zhuǎn)夾持桿上對應(yīng)安裝布置千分表,并測量記錄各對應(yīng)點(diǎn)千分表距中心軸的距離。扭轉(zhuǎn)加載按表2加載重量依次加載測試。
表2扭轉(zhuǎn)剛度測試數(shù)據(jù)表
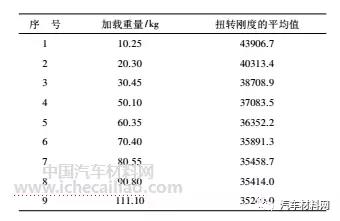
由圖6所示地板加載-扭轉(zhuǎn)剛度圖可知:碳纖維復(fù)合材料地板扭轉(zhuǎn)剛度大于3.5×104Nm2/rad,滿足設(shè)計指標(biāo)大于104Nm2/rad的要求。
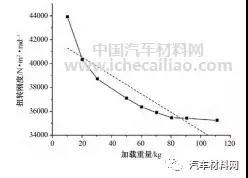
圖6地板加載-扭轉(zhuǎn)剛度圖
4. 4 模態(tài)測試
將產(chǎn)品安裝在振動試驗(yàn)臺上,測試設(shè)備型號為V8-440(英國LDS)。設(shè)定振動加速度為0.3g(1g=9.8m/s2);掃頻范圍為10~500Hz;掃頻速度為10ct/min。振動掃頻測試結(jié)果見表3。
表3地板振動掃頻測試結(jié)果
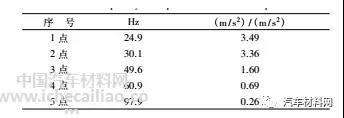
由表3可知,該碳纖維復(fù)合材料地板的階模態(tài)頻率均大于24.9Hz,滿足設(shè)計指標(biāo)大于20Hz的要求。
5結(jié) 語
通過對白車身汽車地板的結(jié)構(gòu)設(shè)計確定碳纖維復(fù)合材料作為汽車前地板材料,選擇RTM為成型工藝,采用多點(diǎn)注射的快速RTM模具,成功制備了碳纖維增強(qiáng)熱固性環(huán)氧樹脂復(fù)合材料前地板。通過靜態(tài)彎曲剛度、扭轉(zhuǎn)剛度及模態(tài)試驗(yàn)測試,結(jié)果滿足汽車整車廠提出的技術(shù)要求,在保證與金屬前地板互換性的基礎(chǔ)上,重量減輕效果明顯,證明復(fù)合材料在汽車領(lǐng)域使用的可行性,為未來汽車輕減化技術(shù)提供了一條可行的途徑。
文章來源:期刊——玻璃鋼/復(fù)合材料
作者:陳 剛,涂麗艷,陳明達(dá),劉東
關(guān)鍵詞:復(fù)合材料;汽車前地板;RTM成型
1概 述
隨著汽車輕量化不斷發(fā)展,節(jié)能、環(huán)保、安全、舒適已成為當(dāng)今材料界和汽車界的研究熱點(diǎn)。研究顯示,車重每減少100kg,每百公里油耗可降低0.3~0.5L,二氧化碳的排放可以減少12g左右。車重減輕,可以提高車輛的加速度和制動效果。傳統(tǒng)汽車鋼鐵材料約占車體總重的3/4,用碳纖維增強(qiáng)復(fù)合材料(CFRP)制造的車身和底盤在等剛度、等強(qiáng)度下可以減重40%~60%,相當(dāng)于鋼結(jié)構(gòu)的1/3~1/6。因此,CFRP正日益成為汽車輕量化的首選材料,逐漸得到汽車行業(yè)越來越廣泛的認(rèn)可和應(yīng)用。
2015年國內(nèi)碳纖維需求總量為1.3萬噸左右,如果保持平穩(wěn)增長態(tài)勢,預(yù)計2020年將達(dá)到2.5萬噸。目前,我國復(fù)合材料在汽車工業(yè)中年用量比例還很小,因此,開發(fā)碳纖維復(fù)合材料在汽車上的應(yīng)用研究具有很大的發(fā)展空間和應(yīng)用前景。本文以碳纖維復(fù)合材料汽車前地板的研制為例,對其結(jié)構(gòu)方案設(shè)計、纖維預(yù)成型體制作、成型工藝及性能測試進(jìn)行了研究。
2結(jié)構(gòu)設(shè)計方案
2. 1 結(jié)構(gòu)設(shè)計依據(jù)
目標(biāo)產(chǎn)品以金屬白車身為設(shè)計依據(jù),原金屬汽車前地板橫截面呈“幾”字形,外形尺寸為1.7m×1.3m,重量為27.7kg,金屬板厚為0.8mm左右,由21個板金沖壓件組裝焊接而成,如圖1所示。
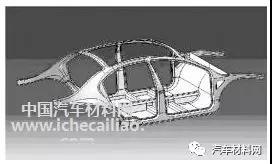
圖 1 汽車白車身
2. 2 性能要求
減重:與金屬鋼制地板相比,減重不低于40%;
彎曲剛度:在1kN載荷下,中心點(diǎn)垂直撓度應(yīng)小于2mm;
扭轉(zhuǎn)剛度:≥104N·m2/rad;
一階模態(tài):≥20Hz。
2. 3 碳纖維復(fù)合材料地板設(shè)計過程
由于原金屬汽車前地板零部件比較多,在復(fù)合材料成型中采用一體成型比較困難,為了充分發(fā)揮碳纖維復(fù)合材料性能及適應(yīng)復(fù)合材料成型工藝特點(diǎn),需要將原鋼制地板結(jié)構(gòu)進(jìn)行局部的設(shè)計修改,修改內(nèi)容主要有如下幾個方面:
(1)取消加強(qiáng)筋板及多余的復(fù)雜筋條:充分發(fā)揮碳纖維復(fù)合材料的比強(qiáng)度、比模量高和可設(shè)計性強(qiáng)等的優(yōu)點(diǎn),根據(jù)等剛度設(shè)計原則,在前地板不同受力部位設(shè)計不同厚度CFRP,盡量取消加強(qiáng)筋板及多余的復(fù)雜筋條;
(2)取消工藝漏液孔:碳纖維復(fù)合材料前地板不同于鋼制地板,產(chǎn)品焊接組裝完成后無需在涂裝車間進(jìn)行電泳工序,所以可以取消各工藝漏液孔;
(3)在碳纖維零部件設(shè)計時,對于影響鋪設(shè)成型的小圓角要盡量避免,原則上內(nèi)角R≥3mm,以利于在模具上鋪設(shè)成型,個別特殊部位可以將內(nèi)角設(shè)計成R≥2mm,但會降低量產(chǎn)效率,應(yīng)盡量避免;
(4)在碳纖維零部件壁厚不同的部位,應(yīng)逐漸過渡,以免在成型固化過程中,因固化收縮不同而產(chǎn)生較大變形。
根據(jù)以上設(shè)計原則,重新修改設(shè)計后的前地板數(shù)模如圖2所示。根據(jù)預(yù)先的有限元模擬,為了能夠達(dá)到與原金屬汽車前地板相同的剛度值,復(fù)合材料汽車前地板主板厚度為2.5mm,中央通道部分厚度為3.0mm。
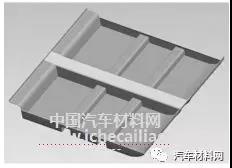
圖 2 碳纖維復(fù)合材料前地板數(shù)模
3成型工藝及試制
3. 1 原材料
對于汽車前地板這種主受力結(jié)構(gòu)件,一般需要首選快速成型的碳纖維復(fù)合材料。本項(xiàng)目設(shè)計選用性能較好的日本東麗碳纖維T700CS-12K織物,面密度分別為480g/m2和200g/m2;單軸向布為200g/m2。樹脂體系選用快速固化的環(huán)氧樹脂體系EpoTech167A/167B(廣州博匯)。
3. 2 成型工藝
復(fù)合材料成本已成為制約復(fù)合材料規(guī)?;瘧?yīng)用的瓶頸,以快速RTM成型技術(shù)為代表的低成本復(fù)合材料技術(shù)已成為目前復(fù)合材料領(lǐng)域的研究熱點(diǎn)之一。RTM工藝具有一系列的優(yōu)點(diǎn),可以一次性快速成型大型、復(fù)雜(包括帶夾芯或插件)的構(gòu)件;無需膠衣涂層即可為構(gòu)件提供光滑表面,后處理工作量??;預(yù)成型體尺寸易控,可設(shè)計性強(qiáng);生產(chǎn)周期適中,可實(shí)現(xiàn)半自動或自動化生產(chǎn),效率高;纖維含量較高;能夠應(yīng)用計算機(jī)輔助設(shè)計進(jìn)行模具和產(chǎn)品設(shè)計,可實(shí)現(xiàn)充模過程的模擬;無需二次粘接。鑒于以上技術(shù)優(yōu)點(diǎn),本項(xiàng)目選用了快速RTM成型工藝試制地板。
3. 3 纖維預(yù)成型體制作
纖維預(yù)成型技術(shù)是RTM工藝的一個重要環(huán)節(jié)。對質(zhì)量要求高、性能穩(wěn)定、結(jié)構(gòu)復(fù)雜、自動化程度要求高的制品來說,這項(xiàng)技術(shù)顯得尤為重要。其原理是采用增粘劑/定型劑或編織/縫紉等技術(shù)將增強(qiáng)材料固結(jié)成與制品相同形狀的半成品。纖維預(yù)成型技術(shù)在保證產(chǎn)品質(zhì)量、生產(chǎn)工藝快速及自動化方面具有重要意義,是實(shí)施RTM低成本化的重要途徑及手段。
根據(jù)汽車前地板結(jié)構(gòu)特點(diǎn),將其設(shè)計為由5個單獨(dú)的預(yù)成型件縫合組裝成一個整體。該預(yù)成型件采用了美國Airtech公司研制生產(chǎn)的Airtac 2增粘劑,通過研究確定最佳工藝參數(shù)為:增粘劑噴涂量為3%~5%、定型加熱溫度為90~100℃、定型時間為20~25min。
3. 4 基于多點(diǎn)注射的快速RTM模具設(shè)計技術(shù)
根據(jù)碳纖維復(fù)合材料前地板的結(jié)構(gòu)特征以及RTM模具與合模液壓機(jī)配合使用考慮,模具的結(jié)構(gòu)類型可以采用多點(diǎn)澆口的三板式注射模具。對于該汽車前地板制件而言,產(chǎn)品需要裝車驗(yàn)證,尺寸精度要求較;因產(chǎn)品結(jié)構(gòu)復(fù)雜、尺寸大,所以注膠過程中的壓力也較高;生產(chǎn)效率較高,要求快速成型,所以材料的導(dǎo)熱性能要好。另外,該模具需采用現(xiàn)有的100t合模液壓機(jī)作為啟模、閉模的機(jī)構(gòu),模具重量不易過大。經(jīng)初步設(shè)計分析,如果采用鋼模,模具重量達(dá)12t左右,而采用鋁模,其重量僅5t左右。綜合以上考慮,該汽車地板RTM模具采用了高強(qiáng)度鋁合金材料。
考慮到鋁合金比鋼材的硬度小,在設(shè)計鋁合金模具時還應(yīng)在一些細(xì)節(jié)上進(jìn)行如下考慮:①如果在鋁合金模具上加工螺紋孔,為了防止螺牙被螺栓磨損,需要安裝鋼絲螺套;②模具上設(shè)置的頂出點(diǎn)需要安裝鋼墊塊;③導(dǎo)柱采用軸承套導(dǎo)柱,減少導(dǎo)柱的摩擦力。圖3為該模具總體設(shè)計結(jié)構(gòu)。
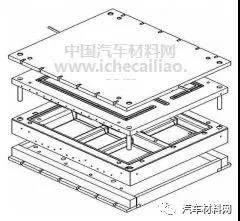
圖3總體結(jié)構(gòu)爆炸圖
3. 5 碳纖維增強(qiáng)熱固性環(huán)氧樹脂復(fù)合材料前地板試制
主要工藝參數(shù): 膠液溫度為50℃,模具溫度為55℃,注膠流量為10~20mL/s,固化溫度為90℃,保溫時間為20min,為了預(yù)防在注膠過程中發(fā)生爆模,注膠壓力不得超過1MPa。產(chǎn)品從注膠到脫模,成型周期在30min以下,基本達(dá)到了RTM快速成型的要求。
4試驗(yàn)結(jié)果
4. 1 重 量
產(chǎn)品重量為16.0kg,與鋼制地板相比減重42%,滿足設(shè)計指標(biāo)要求。
4. 2 靜態(tài)彎曲剛度測試
將樣件安裝及固定在彎曲剛度測試臺上,調(diào)平。樣件的固定位置如圖4所示。
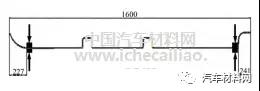
圖4 樣件彎曲剛度測試夾持位置圖
在樣件中心位置分別按照50.10kg、(50.10kg+30.45kg)、(50.10kg+30.45kg+20.30kg)三個加載塊順序加載,并記錄各測點(diǎn)的變形量。彎曲剛度測試數(shù)據(jù)見表1。
表1彎曲剛度測試數(shù)據(jù)表
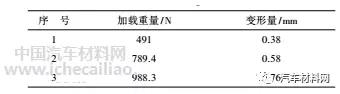
注:加載點(diǎn)和測量點(diǎn)均在樣件中心位置。
根據(jù)圖5所示地板彎曲剛度加載-變形圖可知:碳纖維復(fù)合材料地板中心在1kN載荷下,中心點(diǎn)垂直撓度為0.76mm,滿足設(shè)計指標(biāo)小于2mm的要求。
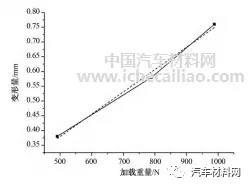
圖5地板彎曲剛度加載-變形圖
4. 3 扭轉(zhuǎn)剛度測試
將樣件安裝固定在扭轉(zhuǎn)剛度測試臺上,調(diào)平。在樣件扭轉(zhuǎn)夾持桿上對應(yīng)安裝布置千分表,并測量記錄各對應(yīng)點(diǎn)千分表距中心軸的距離。扭轉(zhuǎn)加載按表2加載重量依次加載測試。
表2扭轉(zhuǎn)剛度測試數(shù)據(jù)表
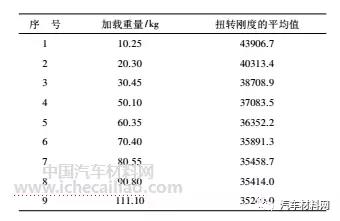
由圖6所示地板加載-扭轉(zhuǎn)剛度圖可知:碳纖維復(fù)合材料地板扭轉(zhuǎn)剛度大于3.5×104Nm2/rad,滿足設(shè)計指標(biāo)大于104Nm2/rad的要求。
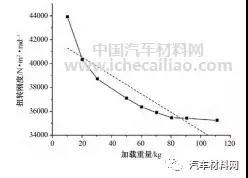
圖6地板加載-扭轉(zhuǎn)剛度圖
4. 4 模態(tài)測試
將產(chǎn)品安裝在振動試驗(yàn)臺上,測試設(shè)備型號為V8-440(英國LDS)。設(shè)定振動加速度為0.3g(1g=9.8m/s2);掃頻范圍為10~500Hz;掃頻速度為10ct/min。振動掃頻測試結(jié)果見表3。
表3地板振動掃頻測試結(jié)果
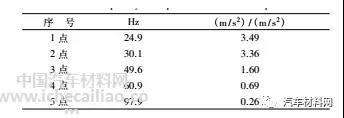
由表3可知,該碳纖維復(fù)合材料地板的階模態(tài)頻率均大于24.9Hz,滿足設(shè)計指標(biāo)大于20Hz的要求。
5結(jié) 語
通過對白車身汽車地板的結(jié)構(gòu)設(shè)計確定碳纖維復(fù)合材料作為汽車前地板材料,選擇RTM為成型工藝,采用多點(diǎn)注射的快速RTM模具,成功制備了碳纖維增強(qiáng)熱固性環(huán)氧樹脂復(fù)合材料前地板。通過靜態(tài)彎曲剛度、扭轉(zhuǎn)剛度及模態(tài)試驗(yàn)測試,結(jié)果滿足汽車整車廠提出的技術(shù)要求,在保證與金屬前地板互換性的基礎(chǔ)上,重量減輕效果明顯,證明復(fù)合材料在汽車領(lǐng)域使用的可行性,為未來汽車輕減化技術(shù)提供了一條可行的途徑。
文章來源:期刊——玻璃鋼/復(fù)合材料
作者:陳 剛,涂麗艷,陳明達(dá),劉東
編輯推薦
最新資訊
-
跨越速運(yùn)憑什么“圈粉”萬千客戶?“
2025-07-01 14:42
-
數(shù)智破局啟新篇?生態(tài)共生再啟程 —
2025-06-27 20:13
-
助力汽車零部件產(chǎn)線智能化升級,西門
2025-06-27 13:59
-
BBA集體轉(zhuǎn)向!放棄全面電動化
2025-06-26 17:32
-
比換柜省錢,比自研省心,西門子Xcel
2025-06-25 15:07