塑料在汽車領(lǐng)域的最新成功應(yīng)用
2018-05-28 09:39:20· 來源:SAEInternational
近年來涌現(xiàn)出了一批新型工程塑料,憑借結(jié)構(gòu)強、重量輕、外觀美等多種優(yōu)點,得以在新型汽車應(yīng)用中大展拳腳。
近年來涌現(xiàn)出了一批新型工程塑料,憑借結(jié)構(gòu)強、重量輕、外觀美等多種優(yōu)點,得以在新型汽車應(yīng)用中大展拳腳。
- Lindsay Brooke
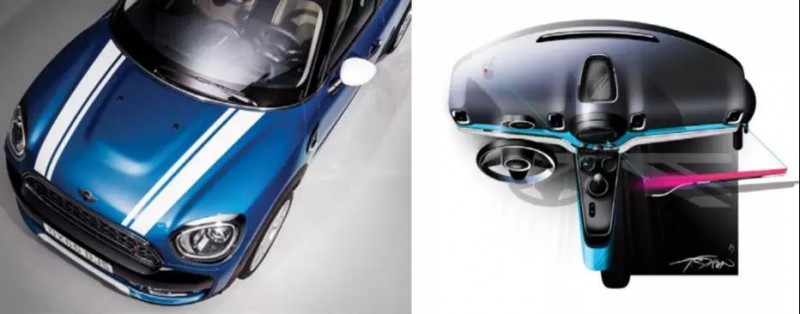
寶馬最新款Mini Countryman采用了IAC的輕量化儀表板解決方案。
選鋼還是選鋁,這是一個全球汽車研發(fā)人員一直爭論不下的問題。然而鋼鋁之爭尚未塵埃落定,塑料和復(fù)合材料領(lǐng)域已取得了同樣驚人的創(chuàng)新成果,無論是汽車還是卡車,無論是車內(nèi)還是車外,都能見到這些新材料的身影。
寶馬原本打算在總結(jié)i3和i8的寶貴裝配經(jīng)驗后,建立一個從華盛頓摩西湖市到德國的“閉環(huán)式”碳纖維供應(yīng)鏈,但最近這個雄心勃勃的項目被叫停了。不過,這并沒有影響先進(jìn)復(fù)合輕量化材料對以金屬為核心的汽車行業(yè)的沖擊。本文將著重介紹塑料在汽車領(lǐng)域的最新成功應(yīng)用,并從CFRP(碳纖維增強塑料)的主要特性之一出發(fā),探討CFRP的未來。
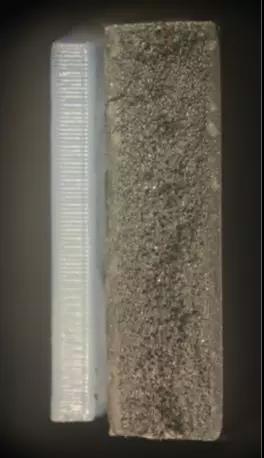
一個由Coreback工藝制成的零件的剖面圖,整體厚度為2.8mm。白色物體是厚度為1mm的參照物。
寶馬選擇了Coreback
儀表板骨架和交叉結(jié)構(gòu),一直是材料創(chuàng)新的焦點,種類繁多的金屬和金屬復(fù)合材料與新型復(fù)合材料在該領(lǐng)域展開競爭。為了減輕2017版Mini Countryman的儀表板架構(gòu)的重量,寶馬工程師選擇了IAC(國際汽車零部件集團(tuán))的Coreback全新注塑工藝。
據(jù)介紹,和“PP(聚丙烯)+ 滑石粉填料”的傳統(tǒng)注塑件相比,長玻纖維增強聚丙烯輕量化塑料泡沫制成的Mini 儀表板骨架的重量減輕了15%,而且剛性重量比卓越。通過改進(jìn)這樣的傳統(tǒng)工藝,寶馬實現(xiàn)了4%-5%的車身減重。
“Coreback 工藝是先在全壓下注入樹脂和CFA(化學(xué)發(fā)泡劑),完全填滿模腔。接著再開模。零件內(nèi)部的泡沫會順著開模拉伸的方向,均勻完美地膨脹,”IAC高級研發(fā)部總監(jiān)Marc Hayes解釋道。
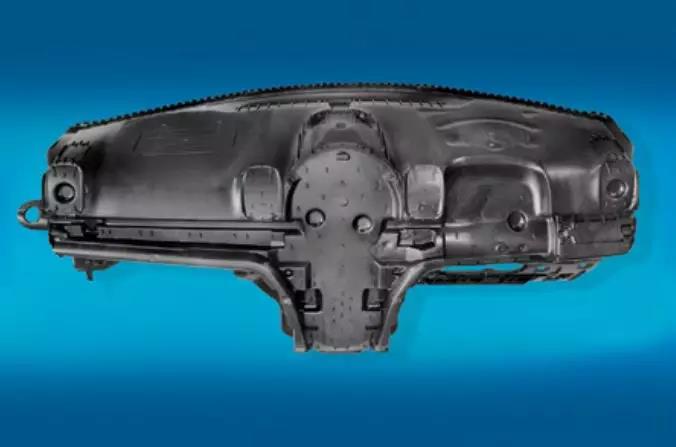
Mini的Coreback儀表板骨架展現(xiàn)了該工藝有助于整合零部件的優(yōu)點。
Hayes表示,在使用Coreback工藝制造儀表板骨架或車門內(nèi)飾板等大件時,注塑厚度為1.8mm,然后在開模時將制件拉伸到2.8mm。“模腔內(nèi)的真實樹脂注塑厚度是1.8mm,而不是2.8mm。這就是減重15-20%的秘密所在。橫截面的其它部分都是氣穴。”該工藝最多可將制件拉伸到4mm(0.157英寸)。
Mini 儀表板骨架項目是IAC Coreback工藝的首例量產(chǎn)應(yīng)用。該項目由IAC、寶馬、模具制造商Siebenwust、化學(xué)品供應(yīng)商SABIC(沙特基礎(chǔ)工業(yè)公司)共同合作完成。
Hayes 表示,“為了確保凹坑或升降桿的運動,標(biāo)準(zhǔn)的筋與壁厚之比通常為60%,而通過使用Coreback,我們可以打破這個局限。發(fā)泡劑也有助于增加這一比例。”
IAC和SABIC的工程師使用CAE(計算機(jī)輔助工程技術(shù))探索出了如何在現(xiàn)有的注塑機(jī)中使用特制的CFA,并預(yù)測泡沫塑件的翹曲。這一全面的分析法使工程師得以提前修改工具,避免可能出現(xiàn)的生產(chǎn)問題,確保生產(chǎn)順利展開。
數(shù)十年來,結(jié)構(gòu)性泡沫已經(jīng)成為了船只儀表板、建筑外飾和門板的主體材料。福特早在上世紀(jì)80年代就嘗試過使用結(jié)構(gòu)性泡沫制造儀表板。
繼Mini儀表板項目大獲成功后,IAC將繼續(xù)在外部內(nèi)飾件和內(nèi)部結(jié)構(gòu)件上應(yīng)用Coreback工藝。Hayes表示,未來需要進(jìn)一步改進(jìn)CFA。
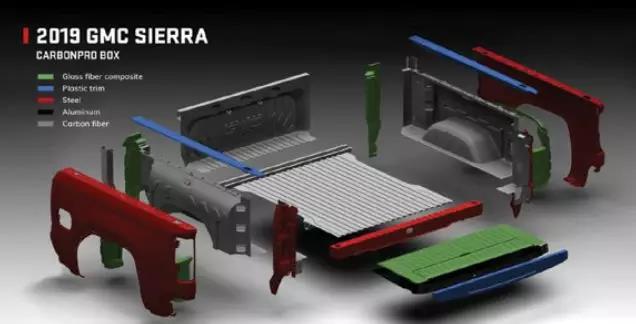
2019GMC Sierra Denali的全新碳纖維復(fù)合型車廂采用了多種材料,上圖是各類材料的分解圖。
Denali的碳纖維車廂
通用汽車的2019版Sierra Denali是業(yè)內(nèi)首次采用碳復(fù)合材車廂的皮卡,這也標(biāo)志著包括連續(xù)纖維增強材料在內(nèi)的輕量化材料離主流應(yīng)用更近了一步,且其在車內(nèi)的應(yīng)用比例也在提升。
值得一提的是,通用對復(fù)合材料的應(yīng)用最早可追溯到1953版Corvette的車身。隨后,通用又在1955年和1958年的雪佛蘭Cameo Carrier上率先使用了片狀模壓部分復(fù)合材料車廂。這次由通用、CSP(大陸結(jié)構(gòu)塑料公司)和CSP母公司帝人公司共同研發(fā)的Denali碳復(fù)合車身正是這一技術(shù)沿革的最新成果。
Sierra首席工程師Tim Herrick在接受《汽車工程》雜志的采訪時表示,全新Sierra車廂抗凹陷、抗刮痕、抗腐蝕,這讓通用的工程師很滿意。Sierra碳纖維熱塑性尼龍6車廂比標(biāo)準(zhǔn)鐵制的減輕了62磅(28kg)。
新材料選用了短切纖維,而非編織纖維。短切纖維可塑性強,使得設(shè)計師可以拓寬車廂,車廂容積增加了一立方英尺。Herrick表示,為防止剝落,雙層粘接工藝一開始就使用了結(jié)構(gòu)性粘合劑和一個機(jī)械緊固件。
Herrick還告訴《汽車工程》雜志,新款Sierra車廂的兩個部分—左前和右前插槽加強件—采用了100%后處理可再生材料。碳纖維車廂將先在位于印第安納州惠靈頓市的CSP工廠注塑成型,然后在通用的韋恩堡裝配工廠修平。
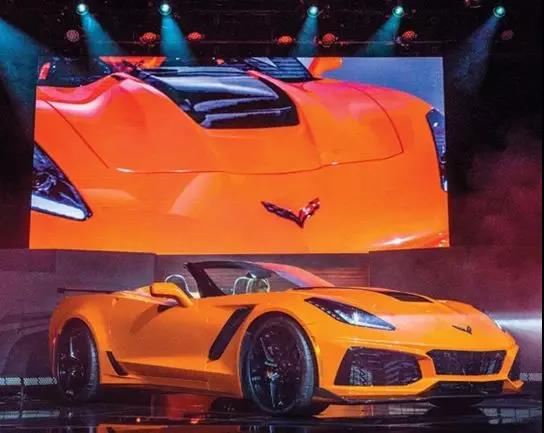
圖上展示的是2019款ZR1 兩門跑車。現(xiàn)有Corvette系列所采用的PCC創(chuàng)新型材料展現(xiàn)了頂級奢華感和一流質(zhì)量水準(zhǔn)。C8會有新的突破嗎?
Plasan帶來CFRP先進(jìn)分析技術(shù)
2019款Sierra Denali將于2018年秋季亮相,但是讓工程師們更翹首以盼的,是通用C8 Corvette。通用此前在2014款Corvette上大膽采用了以PCC(Plasan復(fù)合材料公司)的非高壓釜(out-of-autoclave)沖壓技術(shù)制作而成的A級車身板,在定于2019年年初發(fā)布的下一代Corvette上,不知道通用是否會增加CFRP的比例。
“無可奉告,這個問題我們無法回答!”,PCC工程副總裁Dan Hartzler和PCC總工程師Robert Murch這樣說道。兩人在最近接受《汽車工程》雜志的采訪時表示,目前CFRP材料和工藝技術(shù)的研發(fā)目標(biāo)是加快加工周期、擴(kuò)大生產(chǎn)量,同時大大縮短注塑后的拋光環(huán)節(jié)。
“十年前我們的工藝就已經(jīng)在趕超那些預(yù)浸料化工巨頭了,”Murch解釋道,“但是所有主要的樹脂供應(yīng)商都意識到了市場需求。過去3年,預(yù)浸料工藝取得了令人驚嘆的進(jìn)步。像Solvay、Toray這樣的公司還在航空航天領(lǐng)域一爭高下。但是他們?nèi)狈ο裎覀冞@樣的先進(jìn)工藝。我們的預(yù)浸料工藝只需要2分鐘,甚至更短。”
Hartzler表示,PCC也在研發(fā)沖壓模具。“我們正在努力將生產(chǎn)周期從15到17分鐘縮短到10到12分鐘。現(xiàn)在的關(guān)鍵是攻破瓶頸,但是瓶頸總在變化。我們的模具能否達(dá)到新型樹脂的生產(chǎn)周期標(biāo)準(zhǔn)?”他還表示,為了縮短生產(chǎn)周期,PCC可能會探索其它成型工藝。
“現(xiàn)在,整車企業(yè)終于準(zhǔn)備好要研究怎么樣才能在新領(lǐng)域發(fā)揮新材料和成型工藝的最大價值,”Hartzler說道。下一波技術(shù)將助力CFRP在結(jié)構(gòu)件上得到更大規(guī)模的應(yīng)用。
PCC已經(jīng)宣布將在汽車技術(shù)上投資4000萬美元,以支持結(jié)構(gòu)性碳纖維在車門防撞梁、保險桿等零部件上的應(yīng)用,并縮短生產(chǎn)周期,降低制造成本。
Murch表示,“我們越來越多地使用了動態(tài)建模,這將幫助我們將材料的應(yīng)用范圍拓展到B柱和發(fā)動機(jī)機(jī)艙內(nèi)的零部件。PPC正在將母公司(Plasan Sasa)的彈道技術(shù)轉(zhuǎn)移到汽車領(lǐng)域,這不是我在說大話。我們可以為整車企業(yè)提供分析在內(nèi)的完整解決方案。”
展望2020年,隨著自動駕駛汽車的興起和完全自動駕駛的到來,Hartzler和Murch相信CFRP將會有更多的發(fā)展機(jī)遇。
Hartzler說,“整車企業(yè)已經(jīng)達(dá)成了新的共識:新型復(fù)合材料不是金屬板的替代件,而是綜合性的零部件解決方案。”
- Lindsay Brooke
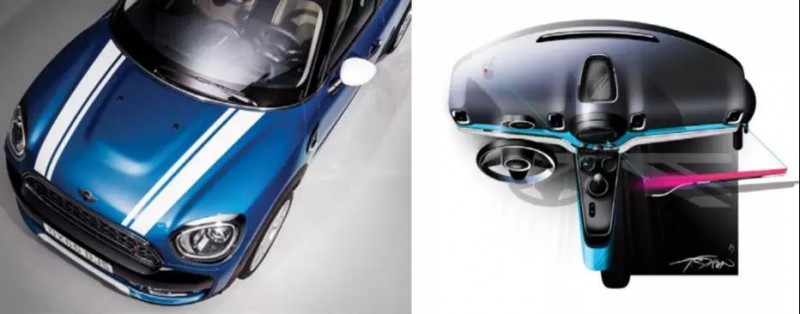
寶馬最新款Mini Countryman采用了IAC的輕量化儀表板解決方案。
選鋼還是選鋁,這是一個全球汽車研發(fā)人員一直爭論不下的問題。然而鋼鋁之爭尚未塵埃落定,塑料和復(fù)合材料領(lǐng)域已取得了同樣驚人的創(chuàng)新成果,無論是汽車還是卡車,無論是車內(nèi)還是車外,都能見到這些新材料的身影。
寶馬原本打算在總結(jié)i3和i8的寶貴裝配經(jīng)驗后,建立一個從華盛頓摩西湖市到德國的“閉環(huán)式”碳纖維供應(yīng)鏈,但最近這個雄心勃勃的項目被叫停了。不過,這并沒有影響先進(jìn)復(fù)合輕量化材料對以金屬為核心的汽車行業(yè)的沖擊。本文將著重介紹塑料在汽車領(lǐng)域的最新成功應(yīng)用,并從CFRP(碳纖維增強塑料)的主要特性之一出發(fā),探討CFRP的未來。
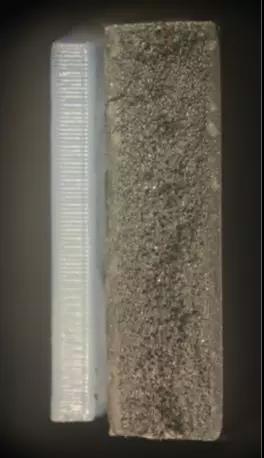
一個由Coreback工藝制成的零件的剖面圖,整體厚度為2.8mm。白色物體是厚度為1mm的參照物。
寶馬選擇了Coreback
儀表板骨架和交叉結(jié)構(gòu),一直是材料創(chuàng)新的焦點,種類繁多的金屬和金屬復(fù)合材料與新型復(fù)合材料在該領(lǐng)域展開競爭。為了減輕2017版Mini Countryman的儀表板架構(gòu)的重量,寶馬工程師選擇了IAC(國際汽車零部件集團(tuán))的Coreback全新注塑工藝。
據(jù)介紹,和“PP(聚丙烯)+ 滑石粉填料”的傳統(tǒng)注塑件相比,長玻纖維增強聚丙烯輕量化塑料泡沫制成的Mini 儀表板骨架的重量減輕了15%,而且剛性重量比卓越。通過改進(jìn)這樣的傳統(tǒng)工藝,寶馬實現(xiàn)了4%-5%的車身減重。
“Coreback 工藝是先在全壓下注入樹脂和CFA(化學(xué)發(fā)泡劑),完全填滿模腔。接著再開模。零件內(nèi)部的泡沫會順著開模拉伸的方向,均勻完美地膨脹,”IAC高級研發(fā)部總監(jiān)Marc Hayes解釋道。
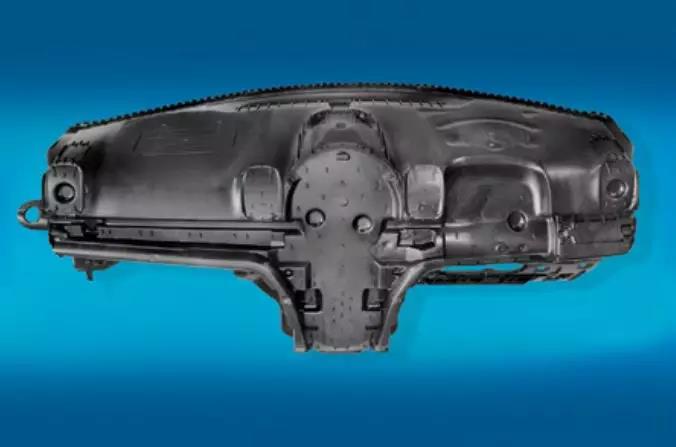
Mini的Coreback儀表板骨架展現(xiàn)了該工藝有助于整合零部件的優(yōu)點。
Hayes表示,在使用Coreback工藝制造儀表板骨架或車門內(nèi)飾板等大件時,注塑厚度為1.8mm,然后在開模時將制件拉伸到2.8mm。“模腔內(nèi)的真實樹脂注塑厚度是1.8mm,而不是2.8mm。這就是減重15-20%的秘密所在。橫截面的其它部分都是氣穴。”該工藝最多可將制件拉伸到4mm(0.157英寸)。
Mini 儀表板骨架項目是IAC Coreback工藝的首例量產(chǎn)應(yīng)用。該項目由IAC、寶馬、模具制造商Siebenwust、化學(xué)品供應(yīng)商SABIC(沙特基礎(chǔ)工業(yè)公司)共同合作完成。
Hayes 表示,“為了確保凹坑或升降桿的運動,標(biāo)準(zhǔn)的筋與壁厚之比通常為60%,而通過使用Coreback,我們可以打破這個局限。發(fā)泡劑也有助于增加這一比例。”
IAC和SABIC的工程師使用CAE(計算機(jī)輔助工程技術(shù))探索出了如何在現(xiàn)有的注塑機(jī)中使用特制的CFA,并預(yù)測泡沫塑件的翹曲。這一全面的分析法使工程師得以提前修改工具,避免可能出現(xiàn)的生產(chǎn)問題,確保生產(chǎn)順利展開。
數(shù)十年來,結(jié)構(gòu)性泡沫已經(jīng)成為了船只儀表板、建筑外飾和門板的主體材料。福特早在上世紀(jì)80年代就嘗試過使用結(jié)構(gòu)性泡沫制造儀表板。
繼Mini儀表板項目大獲成功后,IAC將繼續(xù)在外部內(nèi)飾件和內(nèi)部結(jié)構(gòu)件上應(yīng)用Coreback工藝。Hayes表示,未來需要進(jìn)一步改進(jìn)CFA。
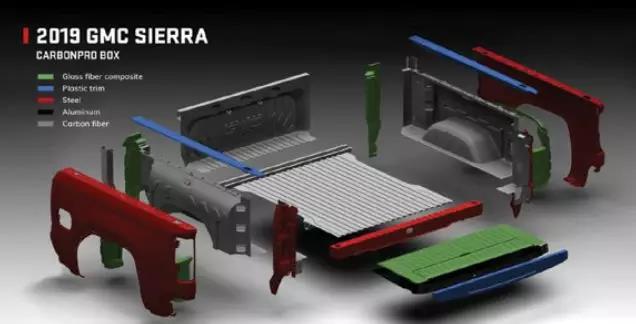
2019GMC Sierra Denali的全新碳纖維復(fù)合型車廂采用了多種材料,上圖是各類材料的分解圖。
Denali的碳纖維車廂
通用汽車的2019版Sierra Denali是業(yè)內(nèi)首次采用碳復(fù)合材車廂的皮卡,這也標(biāo)志著包括連續(xù)纖維增強材料在內(nèi)的輕量化材料離主流應(yīng)用更近了一步,且其在車內(nèi)的應(yīng)用比例也在提升。
值得一提的是,通用對復(fù)合材料的應(yīng)用最早可追溯到1953版Corvette的車身。隨后,通用又在1955年和1958年的雪佛蘭Cameo Carrier上率先使用了片狀模壓部分復(fù)合材料車廂。這次由通用、CSP(大陸結(jié)構(gòu)塑料公司)和CSP母公司帝人公司共同研發(fā)的Denali碳復(fù)合車身正是這一技術(shù)沿革的最新成果。
Sierra首席工程師Tim Herrick在接受《汽車工程》雜志的采訪時表示,全新Sierra車廂抗凹陷、抗刮痕、抗腐蝕,這讓通用的工程師很滿意。Sierra碳纖維熱塑性尼龍6車廂比標(biāo)準(zhǔn)鐵制的減輕了62磅(28kg)。
新材料選用了短切纖維,而非編織纖維。短切纖維可塑性強,使得設(shè)計師可以拓寬車廂,車廂容積增加了一立方英尺。Herrick表示,為防止剝落,雙層粘接工藝一開始就使用了結(jié)構(gòu)性粘合劑和一個機(jī)械緊固件。
Herrick還告訴《汽車工程》雜志,新款Sierra車廂的兩個部分—左前和右前插槽加強件—采用了100%后處理可再生材料。碳纖維車廂將先在位于印第安納州惠靈頓市的CSP工廠注塑成型,然后在通用的韋恩堡裝配工廠修平。
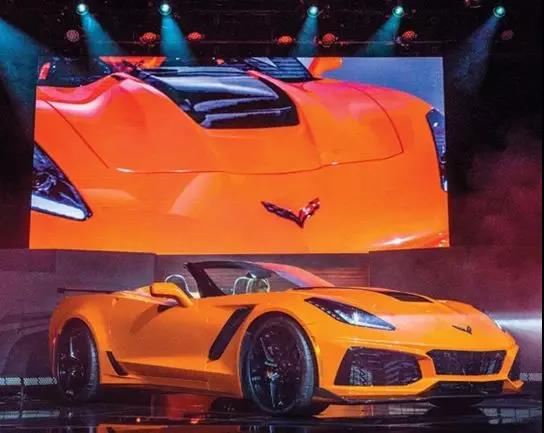
圖上展示的是2019款ZR1 兩門跑車。現(xiàn)有Corvette系列所采用的PCC創(chuàng)新型材料展現(xiàn)了頂級奢華感和一流質(zhì)量水準(zhǔn)。C8會有新的突破嗎?
Plasan帶來CFRP先進(jìn)分析技術(shù)
2019款Sierra Denali將于2018年秋季亮相,但是讓工程師們更翹首以盼的,是通用C8 Corvette。通用此前在2014款Corvette上大膽采用了以PCC(Plasan復(fù)合材料公司)的非高壓釜(out-of-autoclave)沖壓技術(shù)制作而成的A級車身板,在定于2019年年初發(fā)布的下一代Corvette上,不知道通用是否會增加CFRP的比例。
“無可奉告,這個問題我們無法回答!”,PCC工程副總裁Dan Hartzler和PCC總工程師Robert Murch這樣說道。兩人在最近接受《汽車工程》雜志的采訪時表示,目前CFRP材料和工藝技術(shù)的研發(fā)目標(biāo)是加快加工周期、擴(kuò)大生產(chǎn)量,同時大大縮短注塑后的拋光環(huán)節(jié)。
“十年前我們的工藝就已經(jīng)在趕超那些預(yù)浸料化工巨頭了,”Murch解釋道,“但是所有主要的樹脂供應(yīng)商都意識到了市場需求。過去3年,預(yù)浸料工藝取得了令人驚嘆的進(jìn)步。像Solvay、Toray這樣的公司還在航空航天領(lǐng)域一爭高下。但是他們?nèi)狈ο裎覀冞@樣的先進(jìn)工藝。我們的預(yù)浸料工藝只需要2分鐘,甚至更短。”
Hartzler表示,PCC也在研發(fā)沖壓模具。“我們正在努力將生產(chǎn)周期從15到17分鐘縮短到10到12分鐘。現(xiàn)在的關(guān)鍵是攻破瓶頸,但是瓶頸總在變化。我們的模具能否達(dá)到新型樹脂的生產(chǎn)周期標(biāo)準(zhǔn)?”他還表示,為了縮短生產(chǎn)周期,PCC可能會探索其它成型工藝。
“現(xiàn)在,整車企業(yè)終于準(zhǔn)備好要研究怎么樣才能在新領(lǐng)域發(fā)揮新材料和成型工藝的最大價值,”Hartzler說道。下一波技術(shù)將助力CFRP在結(jié)構(gòu)件上得到更大規(guī)模的應(yīng)用。
PCC已經(jīng)宣布將在汽車技術(shù)上投資4000萬美元,以支持結(jié)構(gòu)性碳纖維在車門防撞梁、保險桿等零部件上的應(yīng)用,并縮短生產(chǎn)周期,降低制造成本。
Murch表示,“我們越來越多地使用了動態(tài)建模,這將幫助我們將材料的應(yīng)用范圍拓展到B柱和發(fā)動機(jī)機(jī)艙內(nèi)的零部件。PPC正在將母公司(Plasan Sasa)的彈道技術(shù)轉(zhuǎn)移到汽車領(lǐng)域,這不是我在說大話。我們可以為整車企業(yè)提供分析在內(nèi)的完整解決方案。”
展望2020年,隨著自動駕駛汽車的興起和完全自動駕駛的到來,Hartzler和Murch相信CFRP將會有更多的發(fā)展機(jī)遇。
Hartzler說,“整車企業(yè)已經(jīng)達(dá)成了新的共識:新型復(fù)合材料不是金屬板的替代件,而是綜合性的零部件解決方案。”
編輯推薦
最新資訊
-
跨越速運憑什么“圈粉”萬千客戶?“
2025-07-01 14:42
-
數(shù)智破局啟新篇?生態(tài)共生再啟程 —
2025-06-27 20:13
-
助力汽車零部件產(chǎn)線智能化升級,西門
2025-06-27 13:59
-
BBA集體轉(zhuǎn)向!放棄全面電動化
2025-06-26 17:32
-
比換柜省錢,比自研省心,西門子Xcel
2025-06-25 15:07