汽車齒輪的精密鍛造技術(shù)
2018-05-03 10:17:21· 來源:齒輪傳動
本文介紹了精密鍛造成形在汽車齒輪制造中的應(yīng)用,總結(jié)了各種齒形精密鍛造的關(guān)鍵技術(shù),特別提到分流鍛造在齒形成形方面的應(yīng)用。
本文介紹了精密鍛造成形在汽車齒輪制造中的應(yīng)用,總結(jié)了各種齒形精密鍛造的關(guān)鍵技術(shù),特別提到分流鍛造在齒形成形方面的應(yīng)用。
前言
齒輪精密鍛造成形是一種優(yōu)質(zhì)、高效、低消耗的先進制造技術(shù),被廣泛地用于汽車齒形零件的大批量生產(chǎn)中。隨著精密鍛造工藝和精密模具制造技術(shù)的進步,汽車齒輪和齒形類零件的生產(chǎn)已越來越多地采用精密鍛造成形。當前國外一臺普通轎車采用的精鍛件總質(zhì)量已達到(40—45)Kg,其中齒形類零件總質(zhì)量達10Kg以上。精鍛成形的齒輪單件質(zhì)量可達1Kg以上、齒形精度達到(DIN) 7級。隨著汽車的輕量化要求和人們環(huán)保意識的增強,汽車齒輪制造業(yè)將更多地應(yīng)用精鍛成形技術(shù)。
一.傘齒輪的精鍛成形
1. 傘齒輪(錐齒輪)的熱精鍛成形
(1)早期的傘齒輪精密鍛造
傘齒輪的精密鍛造最早見于50年代德國的拜爾工廠,并在蒂森等公司得到廣泛的應(yīng)用。我國上海汽車齒輪廠等在70年代采用熱精鍛技術(shù),成功進行了傘齒輪的精密鍛造生產(chǎn)。在當時社會主義大協(xié)作的環(huán)境下,傘齒輪的精鍛技術(shù)很快在齒輪行業(yè)得到推廣應(yīng)用。
該技術(shù)的應(yīng)用和發(fā)展得益于2項當時先進的技術(shù):模具的放電加工技術(shù)和毛坯感應(yīng)加熱技術(shù)。先淬火后加工的放電加工避免了模具淬火變形帶來的齒廓誤差;快速加熱的中頻感應(yīng)加熱解決了齒輪毛坯在加熱過程中的氧化和脫碳問題,以上2項技術(shù)的應(yīng)用使鍛造成形的傘齒輪齒面達到無切削加工要求(圖1、圖2)。
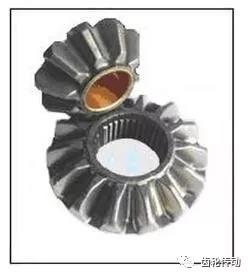
圖1.精鍛成形的行星和半軸齒輪
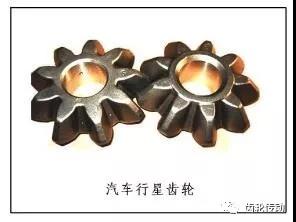
圖2.精鍛成形的汽車行星齒輪
(2)鍛造設(shè)備
傘齒輪的鍛造設(shè)備在國外一般使用熱模鍛壓力機。但在60-70年代的中國,熱模鍛壓力機是非常昂貴的設(shè)備。因此,國內(nèi)企業(yè)普遍使用的鍛造設(shè)備是雙盤摩擦壓力機(圖3)。該設(shè)備結(jié)構(gòu)簡單,價格便宜,很快成為齒輪精鍛的主力設(shè)備。但摩擦壓力機技術(shù)陳舊、難以控制打擊精度、而且能源利用率較低。隨著高能螺旋壓力機和電動螺旋壓力機的出現(xiàn)(圖4),落后的摩擦壓力機有被取代的趨勢。
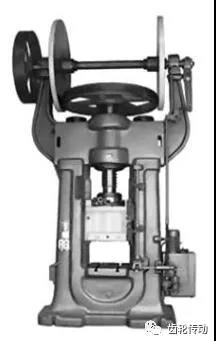
圖3.雙盤摩擦壓力機
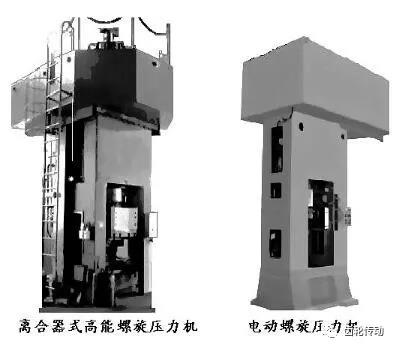
圖4.高能螺旋壓力機和電動螺旋壓力機
(3)熱精鍛造工藝
對于大量生產(chǎn)的汽車行星和差速齒輪,成熟的精鍛成形技術(shù)是號稱“一火兩鍛” 的熱精鍛工藝技術(shù)。即齒輪在熱鍛成形和切邊后利用鍛件余熱進行熱精整。通常的設(shè)計原則是將成形模和精整模設(shè)計為完全相同的尺寸,使精整模用到接近換模極限時充當成形模使用,使齒輪模具的使用壽命得到最大限度的利用。
當時,齒輪行業(yè)的骨干企業(yè)已擁有引進的高精度刨齒機,可以刨出較高精度的齒輪電極,但齒輪模腔的加工手段是早期的放電加工機床。這一類放電加工機床加工速度慢、電極損耗大、加工表面質(zhì)量差。因此,當時的熱精鍛齒輪精度在9級左右,主要應(yīng)用于卡車和拖拉機工業(yè)。
改革開放初期,隨著高精度刨齒機和精密數(shù)控電加工機床的引進,模具的制造精度得到成級的提高。傘齒輪的制造精度隨之提高到8-9級,達到了卡車和輕型車的使用要求。
2.先進的閉塞鍛造技術(shù)
(1)成形原理
閉塞鍛造是一種先進的無飛邊精密成形技術(shù)。70年代,國外在閉塞冷鍛應(yīng)用技術(shù)得到突破后,很快用于傘齒輪的精密成形。閉塞冷鍛成形的齒輪精度相比熱精鍛成形可提高半級至一級;閉塞冷鍛還有無飛邊鍛造的特征,使材料利用率得到較大提高。在80—90年代,轎車、輕型車和微型車的行星、半軸齒輪已廣泛采用閉塞冷鍛工藝生產(chǎn)(圖5)。
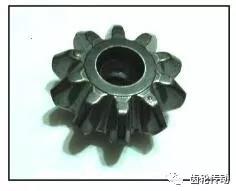
圖5.閉塞冷鍛的汽車行星齒輪
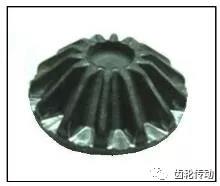
圖6.閉塞冷鍛的傘齒輪
圖6所示的傘齒輪大端面具有較厚的連皮。齒端連皮的存在提高了齒輪的抗彎力矩,使輪齒可承受更大的載荷,這樣的齒輪用機加工是難以加工出來的。
傘齒輪閉塞冷鍛成形原理見圖(7)。由圖可見,毛坯是在封閉的模腔里,被擠壓沖頭推入齒輪型腔充填成形。齒輪的成形精度主要決定于型腔的加工精度,并受到模具彈性變形的影響。但在一般精度條件下,模具的彈性變形可忽視不計。
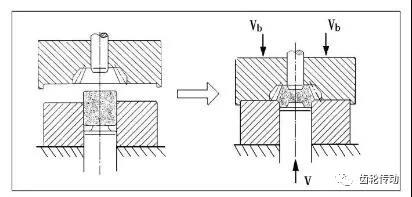
圖7.傘齒輪閉塞成形原理
(2)設(shè)備
通常,較大規(guī)格的傘齒輪在專用的大噸位液壓閉塞壓力機上成形(圖8),而較小規(guī)格的傘齒輪更多采用在普通冷鍛壓力機上以專用閉塞模架(圖9)成形的方法。后一種方法具有生產(chǎn)效率高和成本低的特點。唯鍛件規(guī)格受制于模架的閉塞壓力,不能完成大尺寸傘齒輪的成形。
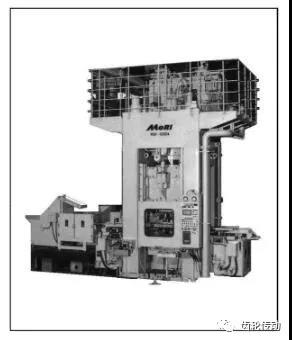
圖8.閉塞鍛造專用壓力機
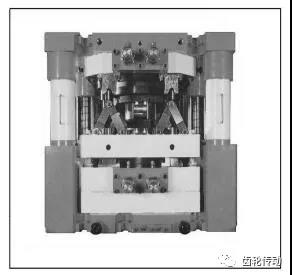
圖9.閉塞鍛造專用模架
國內(nèi)汽車齒輪的骨干企業(yè)如江蘇飛船齒輪和江蘇太平洋精鍛等企業(yè)在90年代初及時引進了傘齒輪的閉塞成形技術(shù)和設(shè)備,經(jīng)過多年的消化吸收,傘齒輪閉塞成形技術(shù)已日臻成熟。在近幾年汽車工業(yè)的飛躍發(fā)展中,傘齒輪的閉塞成形技術(shù)對國內(nèi)汽車差速器的生產(chǎn)發(fā)揮了重要的作用。
(3)等溫正火和齒輪精整的應(yīng)用
閉塞冷鍛成形的齒形精度能滿足一般汽車的使用要求。對精度有更高要求時,在齒輪閉塞成形后進行等溫退火,然后在精密模具內(nèi)作一次冷精整,可穩(wěn)定地獲得DIN 7級或更高的齒形精度。由于冷精整變形量小,齒坯精整前只要少量油霧潤滑,無須作磷、皂化處理,精整后的齒面粗糙度有很大的改善。由于齒坯進行了等溫正火,后續(xù)滲碳淬火時齒形變形量較小而且規(guī)律性好,因此可根據(jù)淬火變形規(guī)律對鍛造齒形進行修正,達到熱處理后精度不降低的目標。
由于傘齒輪精整毛坯有無氧化、無脫碳的要求,因此對等溫正火設(shè)備的技術(shù)要求很高,除采用密封爐體的結(jié)構(gòu)和抽真空—充氮氣保護的措施外,通常還要充入少量氫氣等還原性氣體。充入氫氣后正火的毛坯表面光潔并呈銀亮色澤,精整后齒輪表面質(zhì)量特別好。但這樣的正火設(shè)備,世界上只有少數(shù)廠家能提供,而且價格非常昂貴。圖10為國外某企業(yè)制造的連續(xù)式等溫正火自動線。
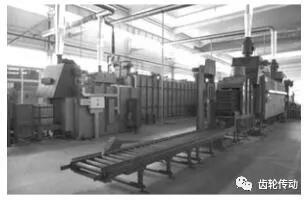
圖10.等溫正火自動線
3.傘齒輪鍛造工藝的發(fā)展趨勢
隨著汽車行星-半軸齒輪規(guī)格越來越大的趨勢和低成本生產(chǎn)的需要,傘齒輪的生產(chǎn)技術(shù)又發(fā)展到溫鍛成形—冷鍛精整和熱鍛成形—冷鍛精整。傘齒輪的溫—冷聯(lián)合成形和熱—冷聯(lián)合成形技術(shù)解決了傘齒輪熱精鍛成形精度不高和閉塞冷鍛齒輪的尺寸規(guī)格做不大的問題,使傘齒輪的成形發(fā)展到一個新的階段。
聯(lián)合成形技術(shù)中,溫鍛成形一般采用閉塞溫鍛工藝,主要于中等規(guī)格的汽車傘齒輪大批量生產(chǎn)。對于大規(guī)格的傘齒輪,推薦采用熱—冷聯(lián)合成形的方案。熱精鍛可采用閉塞鍛造的方案,但更多采用普通熱精鍛方案。因為對于大規(guī)格的傘齒輪,閉塞鍛造的閉塞力已大到難以實現(xiàn)的程度。因此,普通熱精鍛成為熱—冷聯(lián)合成形的主流。圖11為一個用于農(nóng)業(yè)機械上的大規(guī)格傘齒輪,成形工藝為熱鍛成形—冷鍛精整工藝。當前,國內(nèi)用于冷鍛精整的壓力機噸位已達到40MN,可完成外徑300mm的傘齒輪的精整成形。
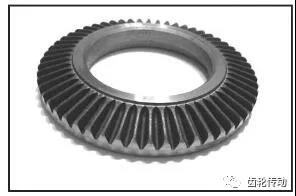
圖11.熱—冷聯(lián)合成形的傘齒輪
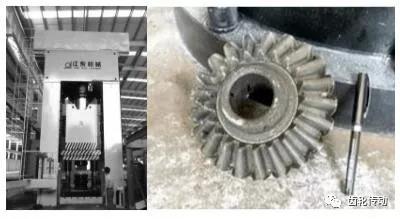
圖12.用于傘齒輪精整的40MN液壓冷鍛壓力機
4.傘齒輪模具加工的技術(shù)進步
在90年代及以前,放電加工是傘齒輪成形模具齒廓加工的主要手段,而齒輪電極主要用精密刨齒機刨出。刨齒加工是一種齒輪的展成成形加工,因此,刨出的齒輪電極是一個符合標準的漸開線齒輪,而電蝕加工出的齒輪模忠實拷貝了電極的形狀,因此是一個標準的齒輪型腔。這對于一般精度的傘齒輪成形并沒有什么問題,但對于噪聲和傳動平穩(wěn)性要求很高的轎車齒輪,一個符合標準齒廓的傘齒輪有時并不能獲得最好的傳動效果。為了改善傳動平穩(wěn)性并減小傳動噪聲,一般要對錐齒輪的齒形和齒向作修鼓處理(見圖13;圖14)。
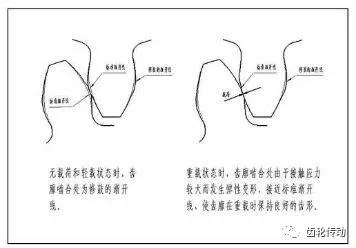
圖13.齒形修鼓原理
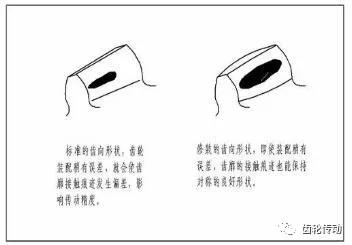
圖14.齒向修鼓原理
由于齒輪的展成加工很難制作出齒形和齒向修鼓的齒輪電極,所以,電極的修鼓成為高精度錐齒輪精鍛成形的技術(shù)難題。國內(nèi)某大學(xué)曾提出利用金屬物體尖角處腐蝕速度大于平坦處的原理,對標準齒輪電極進行化學(xué)腐蝕,從而獲得齒形和齒向得到修鼓的傘齒輪電極。但這種方法因缺少腐蝕量的控制手段,腐蝕的一致性差,因此很難應(yīng)用在傘齒輪的批量生產(chǎn)中。
90年代后期,高速銑的出現(xiàn)解決了齒形電極的修鼓問題。現(xiàn)代的高精度數(shù)控高速銑加工銅電極時精度達到μ米級(圖15),只要建模正確,完全有可能加工出任意修鼓量的齒形電極。在當今,應(yīng)用高性能的復(fù)合涂層刀具和CBN刀具,甚至能將淬硬到洛氏60度以上的高合金模具鋼直接銑加工成齒輪模具(圖16)。
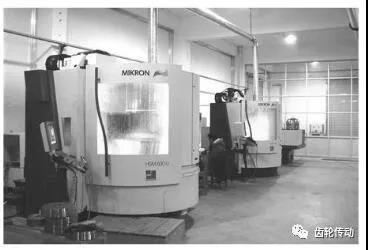
圖15.精密數(shù)控高速銑加工中心
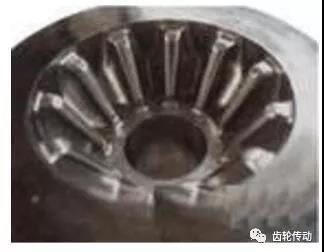
圖16.高速銑削加工的傘齒輪成形模
考慮到齒輪模具制造的經(jīng)濟性,特別是對于硬質(zhì)合金齒輪模,目前齒輪精鍛行業(yè)主要的制模工藝仍然是放電加工,但齒形電極的展成加工已有被高速銑數(shù)控加工全面取代的趨勢。對于淬火硬度在洛氏50度左右的溫鍛和熱鍛成形模,高速銑在加工速度和精度方面已遠遠超過放電加工,在模具的使用壽命方面也體現(xiàn)出明顯的優(yōu)勢。只要解決刀具的使用成本,高速銑加工在溫鍛和熱鍛齒輪模方面可完全取代放電加工。
二.園柱齒輪的精密鍛造成形
1.園柱齒輪的滾軋成形
早在50年代,國內(nèi)的教科書和文獻資料上就介紹了園柱齒輪的熱滾軋和冷滾軋工藝(2)。典型的齒輪滾軋原理如(圖17)。按毛坯滾軋溫度可分為冷滾軋和熱滾軋;按滾輪和齒坯是否強制按一定速比可分為自由滾軋和強制滾軋;按滾輪數(shù)量可分為單輪滾軋、雙輪滾軋和三輪滾軋和搓齒成形等等。
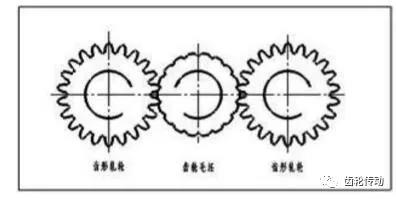
圖17.兩滾式齒輪滾軋成形
由于大模數(shù)的園柱齒輪很難通過滾軋加工得到較高精度,因此,在園柱齒輪精密鍛造方法出現(xiàn)后,人們已很少使用滾軋齒輪的方法。只有在小規(guī)格的漸開線花鍵成形方面,還在大量使用滾軋成形和搓齒成形的方法(圖18)。
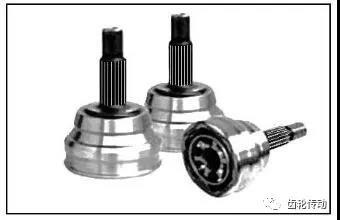
圖18.冷滾軋或搓齒成形的漸開線花鍵
2.園柱齒輪的正擠壓成形
(1)齒輪和花鍵的正擠壓成形
園柱齒輪的正擠壓成形是較早得到應(yīng)用的齒輪成形工藝。典型零件是汽車起動電機小齒輪,及齒輪正擠壓模具結(jié)構(gòu)。圖20.是起動齒輪的工藝過程。
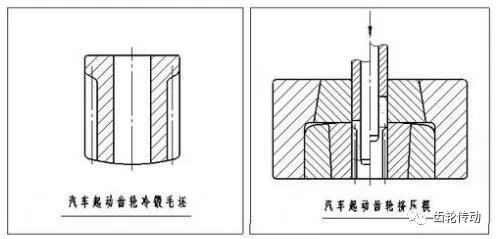
圖19.汽車起動齒輪和齒輪正擠壓模具結(jié)構(gòu)
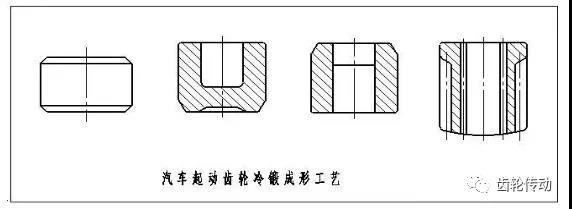
圖20.起動齒輪的冷鍛成形工藝
由于冷鍛過程是金屬在高應(yīng)力下的塑性變形,因此,冷鍛成形的起動齒輪組織致密,金屬纖維連續(xù),疲勞強度和耐磨性比切削加工的齒輪要高出許多。特別是冷擠成形的起動齒輪結(jié)構(gòu)上一端封閉,為輪齒提供了額外的抗彎強度,最適合于汽車起動機頻繁沖擊和高載荷工況下工作。
齒輪正擠壓成形時,齒形凹??梢杂酶呔染€切割機床加工。當齒形擠壓模具采用高速鋼材料,模具齒形制造精度達到(DIN)6級,在批量生產(chǎn)條件下,齒輪成形精度穩(wěn)定達到(DIN) 8—9級??紤]到模具的彈性變形和磨損,在大批量生產(chǎn)時改用硬質(zhì)合金模具并合理設(shè)計冷鍛變形率,可使正擠壓齒輪的齒形精度進一步達到(DIN)7—7.5級。
成形模的齒形設(shè)計要考慮冷鍛過程中模具的彈性變形和模具磨損的影響,對模具齒形加以必要的修正。由于在擠壓過程中模具曲率大的部分磨損速率大于曲率小的部分,因此,采用標準齒形的齒輪擠壓模齒頂處的磨損明顯大于齒面和齒根處的磨損。如果對齒形作適當修正(圖21),可使模具齒形獲得均勻磨損的效果,從而得到較長的模具壽命。
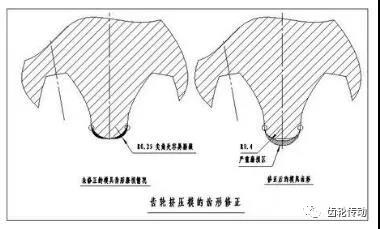
圖21.正擠壓模具的齒形修正
正擠壓成形工藝的另一特出優(yōu)點是模具齒形由數(shù)控線切割加工得到,在少齒數(shù)齒輪加工時通過編程即可獲得理想齒形而不必擔心根切。在加工特殊齒形或修正齒形場合,采用數(shù)控線切割加工齒形比齒輪的展成加工或仿形加工更方便、更快捷、更正確。
花鍵冷鍛成形是齒輪正擠壓成形的一個特例。漸開線花鍵的成形相當于擠壓一個較長的正齒輪,矩形花鍵的擠壓與漸開線花鍵的擠壓相似。從另一方面考慮,小模數(shù)正齒輪可采用分割漸開線花鍵軸的方法來得到(圖22)。
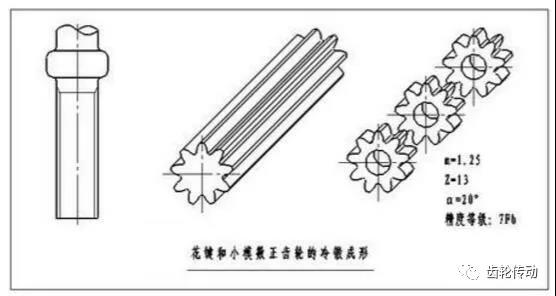
圖22. 花鍵的正擠壓成形和小齒輪的切割成形
從70年代起,國內(nèi)外汽車起動齒輪絕大部分用冷鍛方法生產(chǎn)(3)、(4)。某公司用冷擠壓工藝生產(chǎn)摩托車花鍵軸,并用分割漸開線花鍵軸的方法生產(chǎn)小模數(shù)正齒輪。分割的小齒輪主要用于轎車起動電機行星減速系統(tǒng)。
(2)非園齒輪的正擠壓成形
齒輪正擠壓成形的另一個案例是非園齒輪的精密成形(圖23)。
該齒輪采用正擠壓成形后分割加工,比數(shù)控滾齒加工的生產(chǎn)效率提高幾十倍。正擠壓的難度與園柱齒輪沒有什么不同。只是當外形與正園異較大時,毛坯最好要用冷拔或其他方法做成與非園齒輪外形相同的形狀。
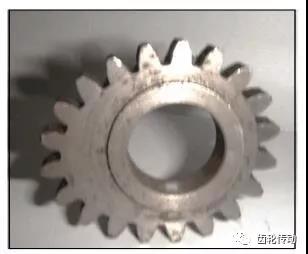
圖23.正擠壓—分割成形的非園齒輪
齒輪正擠壓成形的缺點是成形齒坯的頭、尾有較大的塌角和過渡圓弧,因此齒輪兩端面切削余量大,材料利用率不高,也影響了生產(chǎn)效率的進一步提高。另外齒輪端面切削后容易殘留毛刺,而去毛刺是機加工中最傷腦筋的問題。受擠壓變形率的限制,并考慮到模具制造尺寸和冷鍛壓力機能力等因素,齒輪正擠壓成形目前只應(yīng)用于小規(guī)格園柱齒輪的制造。比起切齒加工,齒輪擠壓成形無論是在質(zhì)量、效率和效益方面,都是一個飛躍。
對于內(nèi)齒輪的制造,可用齒形沖頭反擠壓成形。用該工藝可制造貫通的內(nèi)齒輪(圖24),也可制造底部不通的內(nèi)齒輪(圖25)。在后一種場合,齒輪冷鍛成形不需要預(yù)加工退刀槽,因而在有限尺寸內(nèi)可保證制出最大限度的有效齒形,從而可優(yōu)化零部件結(jié)構(gòu),減小齒輪傳動系統(tǒng)的尺寸并提高齒輪強度。
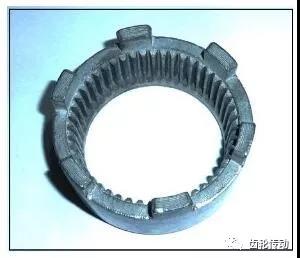
圖24.通孔的內(nèi)齒輪毛坯
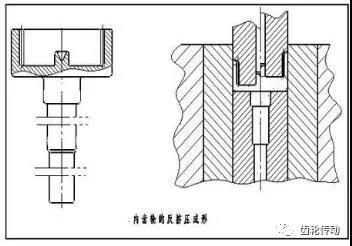
圖25.盲孔的內(nèi)齒輪毛坯和模具結(jié)構(gòu)圖
(3)螺旋齒輪的擠壓成形
當代,齒輪的擠壓成形技術(shù)已從正齒輪成形發(fā)展到了斜齒園柱齒輪和螺旋花鍵軸的擠壓成形(圖26),齒形精度已接近和達到(DIN)7級,能充分滿足大部分汽車齒形零件的要求。冷擠壓成形的齒形零件應(yīng)用已從汽車起動電機、汽車搖窗機等外圍部件發(fā)展到汽車轉(zhuǎn)向機、汽車變速箱等關(guān)鍵總成上。
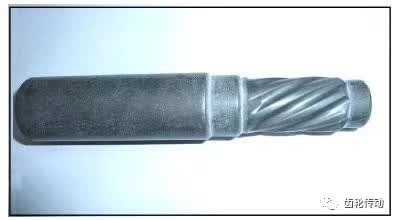
圖26.正擠壓成形的漸開線花鍵軸
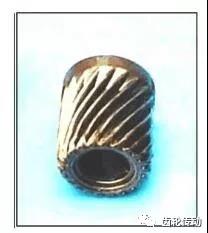
圖27.正擠壓成形的園柱螺旋齒輪
螺旋齒輪的擠壓成形關(guān)鍵技術(shù)是螺旋齒形模具的制作。在使用帶數(shù)控旋轉(zhuǎn)軸的放電加工設(shè)備后,螺旋齒形模具的制造已不太困難。螺旋齒輪擠壓能否成功的另一關(guān)鍵是螺旋齒輪的擠壓的限制。根據(jù)經(jīng)驗,螺旋升角小于27度的齒輪能夠順利擠壓成形。對于貫通式擠壓,螺旋升角還可以加大。
3.園柱齒輪的的分流鍛造
(1)園柱齒輪的閉式冷鐓鍛成形
對于齒寬較窄和直徑較大的園柱齒輪,可用的成形工藝有閉式冷鐓鍛成形(圖28)
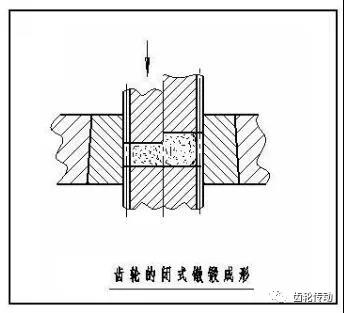
圖28.園柱齒輪的閉式冷鐓鍛成形
由于齒輪冷鐓鍛成形時在齒頂?shù)募饨遣拷饘倭鲃訔l件不好,單用加大鍛造力的方法不能有效地改善齒尖部的充填效果。而加大鍛造力的負面效應(yīng)是使模具壽命大幅度下降。鍛造應(yīng)力的加大還使模具彈性變形增加,使鍛件的齒形精度下降。由于閉模鍛造的特點,當齒坯的下料精度較低時,毛坯體積少量超標就會引起鍛造應(yīng)力的急劇上升,最終造成模具的破損失效。
(2)園柱齒輪的分流鍛造成形
80年代以來,國內(nèi)外精密鍛造專家開始將分流鍛造理論應(yīng)用于正齒輪和螺旋齒輪的冷鍛成形(3)、(4)、(5)。分流鍛造的原理是在毛坯或模具的成形部分建立一個材料的分流腔或分流通道(圖29)。鍛造過程中,材料在充滿型腔的同時,部分材料流向分流腔或分流通道。分流腔或分流通道能容納少量體積超標的材料,而不致于造成鍛造應(yīng)力急劇增加的后果。更主要的是,通過對分流路徑的合理設(shè)計,使鍛造過程中金屬的流動有利于齒形尖角處的充填,從而可在較小的成形應(yīng)力下得到充滿程度較好的齒形。分流鍛造技術(shù)的應(yīng)用,使較高精度齒輪的少、無切削加工迅速達到了產(chǎn)業(yè)化規(guī)模。

圖29.倒擋齒輪的分流成形
另外,以多工位溫鍛或熱精鍛成形作為倒擋齒輪的預(yù)成形,以冷鍛精整來獲得最終的齒形精度,已成為當前大批量生產(chǎn)汽車倒擋齒輪的經(jīng)濟方案。但在小批量生產(chǎn)場合,也可采用全冷鍛成形的方案(圖30)。全冷鍛成形時,可在一臺設(shè)備上通過更換模具完成多道工序,設(shè)備投資較小,適合于多品種中、小批量生產(chǎn)。
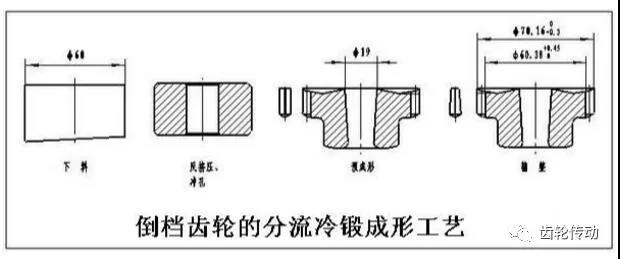
圖30. 倒擋齒輪的分流成形
(3)齒輪分流鍛造的應(yīng)用
與擠壓齒輪相比,分流鍛造的齒輪容易獲得較大的尺寸。齒輪分流鍛造成形后如追加一次冷精整,同樣獲得較好的精度,可完全滿足汽車變速箱齒輪的精度要求。另外,分流鍛造的齒輪端面余量小,材料利用率高。某些情況下,齒形端面可不加工,避免了車削毛刺的發(fā)生。
分流鍛造技術(shù)主要應(yīng)用于汽車變速箱齒輪。除倒擋齒輪外,變速齒坯接合齒的成形和接合齒環(huán)等齒形零件等都有了冷鍛成形的工藝和大批量生產(chǎn)的經(jīng)驗。在國外,變速箱螺旋齒輪與接合齒的整體精鍛(7)也有了成功的經(jīng)驗(圖31;32)。
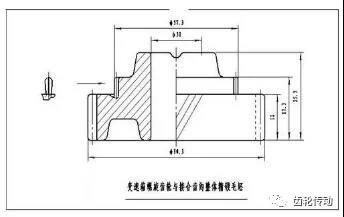
圖31. 變速箱接合齒整體精鍛毛坯
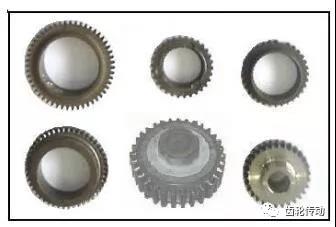
圖32.汽車變速箱結(jié)合齒和倒擋齒輪
(4)園柱齒輪的冷精整技術(shù)
無論是熱鍛、溫鍛或冷鍛狀態(tài)的分流鍛造,都能夠完成園柱齒輪的齒形成形。但由于溫度和模具在大應(yīng)力下工作的影響,分流成形的齒輪精度不會太高,不能滿足汽車齒輪的使用要求。因此,大部分園柱齒輪在分流成形后都必需對齒廓進行精整。為了保證齒輪的精整效果,并使后續(xù)的滲碳熱處理變形小,在分流成形后有必要對齒輪毛坯進行
一次軟化退火或等溫正火。由于園柱齒輪的精整一般是貫通式擠壓,即使預(yù)成形齒坯在壓力下擠過一個精密的齒輪模具(圖33),使毛坯齒廓精度得到提高的方法。在這種精整模式下,齒輪毛坯表面的金屬將與精整模具表面發(fā)生相對流動。為了保證毛坯在模具表面較長距離的流動中不因摩擦而產(chǎn)生粘著燒傷,必需對齒坯實施精細的拋丸和磷化-潤滑處理。潤滑處理可以是皂化處理,也可以滾涂二硫化鉬微粉。

圖33. 園柱齒輪的精整凹模
3.園柱齒輪精密鍛造的技術(shù)瓶頸
目前,窄齒園柱齒輪通過溫鍛或熱鍛、或冷鍛分流成形,并經(jīng)熱處理和磷、皂化處理后實施冷鍛精整,其齒形精度已完全能滿足汽車齒輪的要求。大部份汽車倒擋齒輪和結(jié)合齒環(huán)就是這樣生產(chǎn)的。但對于寬齒園柱齒輪,由于在齒向有修鼓要求,即齒向精度呈“K”線分布,對齒輪精整提出了一個特別的難題(圖34)。
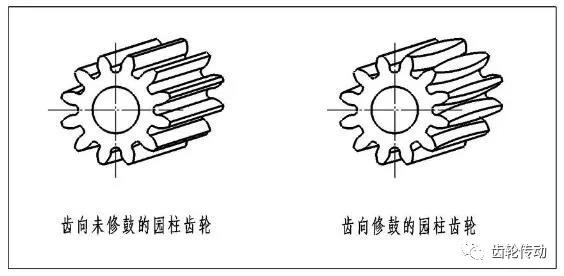
圖34.寬齒園柱齒輪的齒向修鼓
目前,人們提出了種種方法,卻沒有得到一個可靠的結(jié)果。所以,當前寬齒園柱齒輪的精密鍛造成形,只能局限于低精度齒輪制造,或是為磨齒加工提供磨前毛坯。
在當前,探索一個可靠的齒向修鼓方法,突破園柱齒輪精密鍛造的技術(shù)瓶頸,是擺在鍛造和齒輪工作者面前的重大課題。
體現(xiàn)優(yōu)質(zhì)、高效、低成本的汽車齒形零件精鍛成形技術(shù)一定會在汽車零部件生產(chǎn)中得到推廣應(yīng)用。
前言
齒輪精密鍛造成形是一種優(yōu)質(zhì)、高效、低消耗的先進制造技術(shù),被廣泛地用于汽車齒形零件的大批量生產(chǎn)中。隨著精密鍛造工藝和精密模具制造技術(shù)的進步,汽車齒輪和齒形類零件的生產(chǎn)已越來越多地采用精密鍛造成形。當前國外一臺普通轎車采用的精鍛件總質(zhì)量已達到(40—45)Kg,其中齒形類零件總質(zhì)量達10Kg以上。精鍛成形的齒輪單件質(zhì)量可達1Kg以上、齒形精度達到(DIN) 7級。隨著汽車的輕量化要求和人們環(huán)保意識的增強,汽車齒輪制造業(yè)將更多地應(yīng)用精鍛成形技術(shù)。
一.傘齒輪的精鍛成形
1. 傘齒輪(錐齒輪)的熱精鍛成形
(1)早期的傘齒輪精密鍛造
傘齒輪的精密鍛造最早見于50年代德國的拜爾工廠,并在蒂森等公司得到廣泛的應(yīng)用。我國上海汽車齒輪廠等在70年代采用熱精鍛技術(shù),成功進行了傘齒輪的精密鍛造生產(chǎn)。在當時社會主義大協(xié)作的環(huán)境下,傘齒輪的精鍛技術(shù)很快在齒輪行業(yè)得到推廣應(yīng)用。
該技術(shù)的應(yīng)用和發(fā)展得益于2項當時先進的技術(shù):模具的放電加工技術(shù)和毛坯感應(yīng)加熱技術(shù)。先淬火后加工的放電加工避免了模具淬火變形帶來的齒廓誤差;快速加熱的中頻感應(yīng)加熱解決了齒輪毛坯在加熱過程中的氧化和脫碳問題,以上2項技術(shù)的應(yīng)用使鍛造成形的傘齒輪齒面達到無切削加工要求(圖1、圖2)。
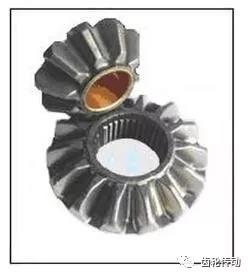
圖1.精鍛成形的行星和半軸齒輪
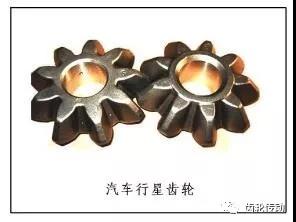
圖2.精鍛成形的汽車行星齒輪
(2)鍛造設(shè)備
傘齒輪的鍛造設(shè)備在國外一般使用熱模鍛壓力機。但在60-70年代的中國,熱模鍛壓力機是非常昂貴的設(shè)備。因此,國內(nèi)企業(yè)普遍使用的鍛造設(shè)備是雙盤摩擦壓力機(圖3)。該設(shè)備結(jié)構(gòu)簡單,價格便宜,很快成為齒輪精鍛的主力設(shè)備。但摩擦壓力機技術(shù)陳舊、難以控制打擊精度、而且能源利用率較低。隨著高能螺旋壓力機和電動螺旋壓力機的出現(xiàn)(圖4),落后的摩擦壓力機有被取代的趨勢。
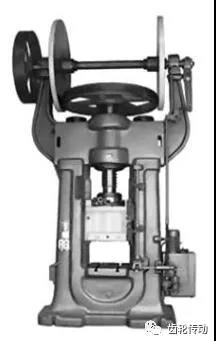
圖3.雙盤摩擦壓力機
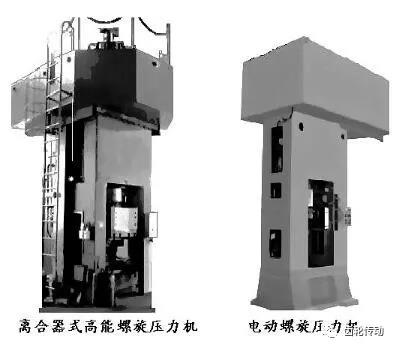
圖4.高能螺旋壓力機和電動螺旋壓力機
(3)熱精鍛造工藝
對于大量生產(chǎn)的汽車行星和差速齒輪,成熟的精鍛成形技術(shù)是號稱“一火兩鍛” 的熱精鍛工藝技術(shù)。即齒輪在熱鍛成形和切邊后利用鍛件余熱進行熱精整。通常的設(shè)計原則是將成形模和精整模設(shè)計為完全相同的尺寸,使精整模用到接近換模極限時充當成形模使用,使齒輪模具的使用壽命得到最大限度的利用。
當時,齒輪行業(yè)的骨干企業(yè)已擁有引進的高精度刨齒機,可以刨出較高精度的齒輪電極,但齒輪模腔的加工手段是早期的放電加工機床。這一類放電加工機床加工速度慢、電極損耗大、加工表面質(zhì)量差。因此,當時的熱精鍛齒輪精度在9級左右,主要應(yīng)用于卡車和拖拉機工業(yè)。
改革開放初期,隨著高精度刨齒機和精密數(shù)控電加工機床的引進,模具的制造精度得到成級的提高。傘齒輪的制造精度隨之提高到8-9級,達到了卡車和輕型車的使用要求。
2.先進的閉塞鍛造技術(shù)
(1)成形原理
閉塞鍛造是一種先進的無飛邊精密成形技術(shù)。70年代,國外在閉塞冷鍛應(yīng)用技術(shù)得到突破后,很快用于傘齒輪的精密成形。閉塞冷鍛成形的齒輪精度相比熱精鍛成形可提高半級至一級;閉塞冷鍛還有無飛邊鍛造的特征,使材料利用率得到較大提高。在80—90年代,轎車、輕型車和微型車的行星、半軸齒輪已廣泛采用閉塞冷鍛工藝生產(chǎn)(圖5)。
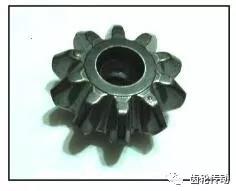
圖5.閉塞冷鍛的汽車行星齒輪
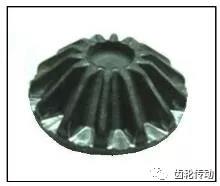
圖6.閉塞冷鍛的傘齒輪
圖6所示的傘齒輪大端面具有較厚的連皮。齒端連皮的存在提高了齒輪的抗彎力矩,使輪齒可承受更大的載荷,這樣的齒輪用機加工是難以加工出來的。
傘齒輪閉塞冷鍛成形原理見圖(7)。由圖可見,毛坯是在封閉的模腔里,被擠壓沖頭推入齒輪型腔充填成形。齒輪的成形精度主要決定于型腔的加工精度,并受到模具彈性變形的影響。但在一般精度條件下,模具的彈性變形可忽視不計。
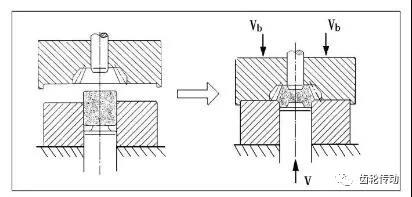
圖7.傘齒輪閉塞成形原理
(2)設(shè)備
通常,較大規(guī)格的傘齒輪在專用的大噸位液壓閉塞壓力機上成形(圖8),而較小規(guī)格的傘齒輪更多采用在普通冷鍛壓力機上以專用閉塞模架(圖9)成形的方法。后一種方法具有生產(chǎn)效率高和成本低的特點。唯鍛件規(guī)格受制于模架的閉塞壓力,不能完成大尺寸傘齒輪的成形。
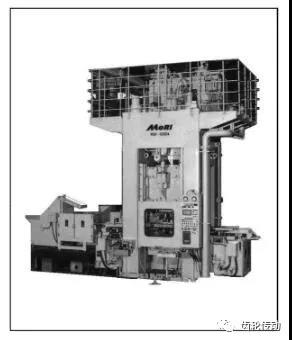
圖8.閉塞鍛造專用壓力機
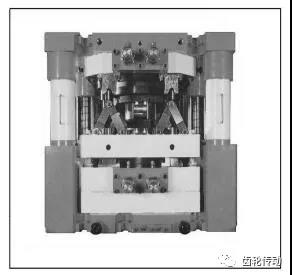
圖9.閉塞鍛造專用模架
國內(nèi)汽車齒輪的骨干企業(yè)如江蘇飛船齒輪和江蘇太平洋精鍛等企業(yè)在90年代初及時引進了傘齒輪的閉塞成形技術(shù)和設(shè)備,經(jīng)過多年的消化吸收,傘齒輪閉塞成形技術(shù)已日臻成熟。在近幾年汽車工業(yè)的飛躍發(fā)展中,傘齒輪的閉塞成形技術(shù)對國內(nèi)汽車差速器的生產(chǎn)發(fā)揮了重要的作用。
(3)等溫正火和齒輪精整的應(yīng)用
閉塞冷鍛成形的齒形精度能滿足一般汽車的使用要求。對精度有更高要求時,在齒輪閉塞成形后進行等溫退火,然后在精密模具內(nèi)作一次冷精整,可穩(wěn)定地獲得DIN 7級或更高的齒形精度。由于冷精整變形量小,齒坯精整前只要少量油霧潤滑,無須作磷、皂化處理,精整后的齒面粗糙度有很大的改善。由于齒坯進行了等溫正火,后續(xù)滲碳淬火時齒形變形量較小而且規(guī)律性好,因此可根據(jù)淬火變形規(guī)律對鍛造齒形進行修正,達到熱處理后精度不降低的目標。
由于傘齒輪精整毛坯有無氧化、無脫碳的要求,因此對等溫正火設(shè)備的技術(shù)要求很高,除采用密封爐體的結(jié)構(gòu)和抽真空—充氮氣保護的措施外,通常還要充入少量氫氣等還原性氣體。充入氫氣后正火的毛坯表面光潔并呈銀亮色澤,精整后齒輪表面質(zhì)量特別好。但這樣的正火設(shè)備,世界上只有少數(shù)廠家能提供,而且價格非常昂貴。圖10為國外某企業(yè)制造的連續(xù)式等溫正火自動線。
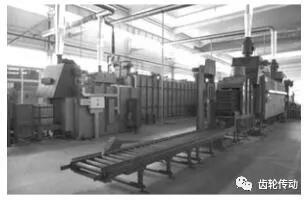
圖10.等溫正火自動線
3.傘齒輪鍛造工藝的發(fā)展趨勢
隨著汽車行星-半軸齒輪規(guī)格越來越大的趨勢和低成本生產(chǎn)的需要,傘齒輪的生產(chǎn)技術(shù)又發(fā)展到溫鍛成形—冷鍛精整和熱鍛成形—冷鍛精整。傘齒輪的溫—冷聯(lián)合成形和熱—冷聯(lián)合成形技術(shù)解決了傘齒輪熱精鍛成形精度不高和閉塞冷鍛齒輪的尺寸規(guī)格做不大的問題,使傘齒輪的成形發(fā)展到一個新的階段。
聯(lián)合成形技術(shù)中,溫鍛成形一般采用閉塞溫鍛工藝,主要于中等規(guī)格的汽車傘齒輪大批量生產(chǎn)。對于大規(guī)格的傘齒輪,推薦采用熱—冷聯(lián)合成形的方案。熱精鍛可采用閉塞鍛造的方案,但更多采用普通熱精鍛方案。因為對于大規(guī)格的傘齒輪,閉塞鍛造的閉塞力已大到難以實現(xiàn)的程度。因此,普通熱精鍛成為熱—冷聯(lián)合成形的主流。圖11為一個用于農(nóng)業(yè)機械上的大規(guī)格傘齒輪,成形工藝為熱鍛成形—冷鍛精整工藝。當前,國內(nèi)用于冷鍛精整的壓力機噸位已達到40MN,可完成外徑300mm的傘齒輪的精整成形。
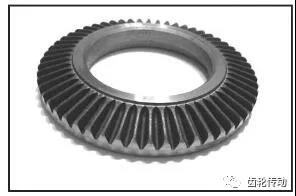
圖11.熱—冷聯(lián)合成形的傘齒輪
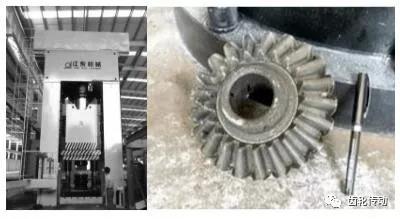
圖12.用于傘齒輪精整的40MN液壓冷鍛壓力機
4.傘齒輪模具加工的技術(shù)進步
在90年代及以前,放電加工是傘齒輪成形模具齒廓加工的主要手段,而齒輪電極主要用精密刨齒機刨出。刨齒加工是一種齒輪的展成成形加工,因此,刨出的齒輪電極是一個符合標準的漸開線齒輪,而電蝕加工出的齒輪模忠實拷貝了電極的形狀,因此是一個標準的齒輪型腔。這對于一般精度的傘齒輪成形并沒有什么問題,但對于噪聲和傳動平穩(wěn)性要求很高的轎車齒輪,一個符合標準齒廓的傘齒輪有時并不能獲得最好的傳動效果。為了改善傳動平穩(wěn)性并減小傳動噪聲,一般要對錐齒輪的齒形和齒向作修鼓處理(見圖13;圖14)。
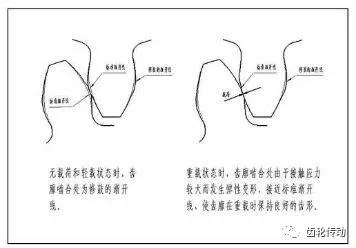
圖13.齒形修鼓原理
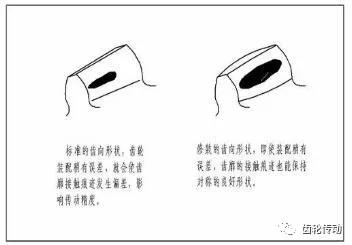
圖14.齒向修鼓原理
由于齒輪的展成加工很難制作出齒形和齒向修鼓的齒輪電極,所以,電極的修鼓成為高精度錐齒輪精鍛成形的技術(shù)難題。國內(nèi)某大學(xué)曾提出利用金屬物體尖角處腐蝕速度大于平坦處的原理,對標準齒輪電極進行化學(xué)腐蝕,從而獲得齒形和齒向得到修鼓的傘齒輪電極。但這種方法因缺少腐蝕量的控制手段,腐蝕的一致性差,因此很難應(yīng)用在傘齒輪的批量生產(chǎn)中。
90年代后期,高速銑的出現(xiàn)解決了齒形電極的修鼓問題。現(xiàn)代的高精度數(shù)控高速銑加工銅電極時精度達到μ米級(圖15),只要建模正確,完全有可能加工出任意修鼓量的齒形電極。在當今,應(yīng)用高性能的復(fù)合涂層刀具和CBN刀具,甚至能將淬硬到洛氏60度以上的高合金模具鋼直接銑加工成齒輪模具(圖16)。
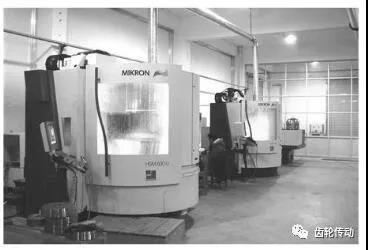
圖15.精密數(shù)控高速銑加工中心
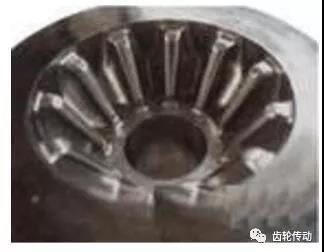
圖16.高速銑削加工的傘齒輪成形模
考慮到齒輪模具制造的經(jīng)濟性,特別是對于硬質(zhì)合金齒輪模,目前齒輪精鍛行業(yè)主要的制模工藝仍然是放電加工,但齒形電極的展成加工已有被高速銑數(shù)控加工全面取代的趨勢。對于淬火硬度在洛氏50度左右的溫鍛和熱鍛成形模,高速銑在加工速度和精度方面已遠遠超過放電加工,在模具的使用壽命方面也體現(xiàn)出明顯的優(yōu)勢。只要解決刀具的使用成本,高速銑加工在溫鍛和熱鍛齒輪模方面可完全取代放電加工。
二.園柱齒輪的精密鍛造成形
1.園柱齒輪的滾軋成形
早在50年代,國內(nèi)的教科書和文獻資料上就介紹了園柱齒輪的熱滾軋和冷滾軋工藝(2)。典型的齒輪滾軋原理如(圖17)。按毛坯滾軋溫度可分為冷滾軋和熱滾軋;按滾輪和齒坯是否強制按一定速比可分為自由滾軋和強制滾軋;按滾輪數(shù)量可分為單輪滾軋、雙輪滾軋和三輪滾軋和搓齒成形等等。
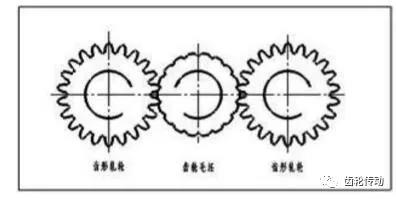
圖17.兩滾式齒輪滾軋成形
由于大模數(shù)的園柱齒輪很難通過滾軋加工得到較高精度,因此,在園柱齒輪精密鍛造方法出現(xiàn)后,人們已很少使用滾軋齒輪的方法。只有在小規(guī)格的漸開線花鍵成形方面,還在大量使用滾軋成形和搓齒成形的方法(圖18)。
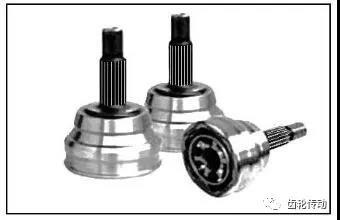
圖18.冷滾軋或搓齒成形的漸開線花鍵
2.園柱齒輪的正擠壓成形
(1)齒輪和花鍵的正擠壓成形
園柱齒輪的正擠壓成形是較早得到應(yīng)用的齒輪成形工藝。典型零件是汽車起動電機小齒輪,及齒輪正擠壓模具結(jié)構(gòu)。圖20.是起動齒輪的工藝過程。
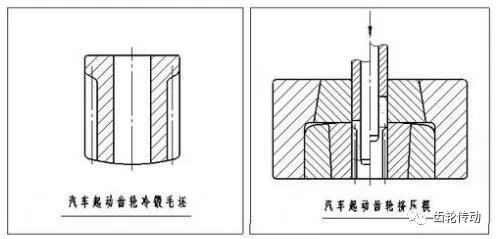
圖19.汽車起動齒輪和齒輪正擠壓模具結(jié)構(gòu)
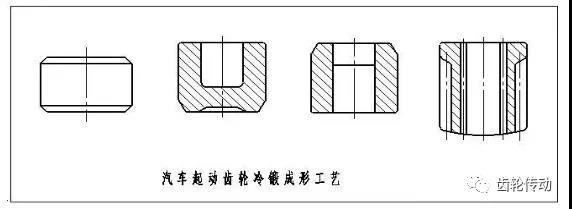
圖20.起動齒輪的冷鍛成形工藝
由于冷鍛過程是金屬在高應(yīng)力下的塑性變形,因此,冷鍛成形的起動齒輪組織致密,金屬纖維連續(xù),疲勞強度和耐磨性比切削加工的齒輪要高出許多。特別是冷擠成形的起動齒輪結(jié)構(gòu)上一端封閉,為輪齒提供了額外的抗彎強度,最適合于汽車起動機頻繁沖擊和高載荷工況下工作。
齒輪正擠壓成形時,齒形凹??梢杂酶呔染€切割機床加工。當齒形擠壓模具采用高速鋼材料,模具齒形制造精度達到(DIN)6級,在批量生產(chǎn)條件下,齒輪成形精度穩(wěn)定達到(DIN) 8—9級??紤]到模具的彈性變形和磨損,在大批量生產(chǎn)時改用硬質(zhì)合金模具并合理設(shè)計冷鍛變形率,可使正擠壓齒輪的齒形精度進一步達到(DIN)7—7.5級。
成形模的齒形設(shè)計要考慮冷鍛過程中模具的彈性變形和模具磨損的影響,對模具齒形加以必要的修正。由于在擠壓過程中模具曲率大的部分磨損速率大于曲率小的部分,因此,采用標準齒形的齒輪擠壓模齒頂處的磨損明顯大于齒面和齒根處的磨損。如果對齒形作適當修正(圖21),可使模具齒形獲得均勻磨損的效果,從而得到較長的模具壽命。
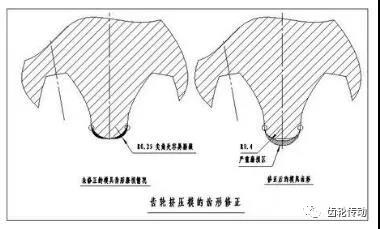
圖21.正擠壓模具的齒形修正
正擠壓成形工藝的另一特出優(yōu)點是模具齒形由數(shù)控線切割加工得到,在少齒數(shù)齒輪加工時通過編程即可獲得理想齒形而不必擔心根切。在加工特殊齒形或修正齒形場合,采用數(shù)控線切割加工齒形比齒輪的展成加工或仿形加工更方便、更快捷、更正確。
花鍵冷鍛成形是齒輪正擠壓成形的一個特例。漸開線花鍵的成形相當于擠壓一個較長的正齒輪,矩形花鍵的擠壓與漸開線花鍵的擠壓相似。從另一方面考慮,小模數(shù)正齒輪可采用分割漸開線花鍵軸的方法來得到(圖22)。
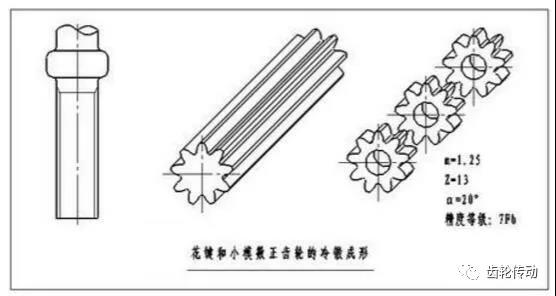
圖22. 花鍵的正擠壓成形和小齒輪的切割成形
從70年代起,國內(nèi)外汽車起動齒輪絕大部分用冷鍛方法生產(chǎn)(3)、(4)。某公司用冷擠壓工藝生產(chǎn)摩托車花鍵軸,并用分割漸開線花鍵軸的方法生產(chǎn)小模數(shù)正齒輪。分割的小齒輪主要用于轎車起動電機行星減速系統(tǒng)。
(2)非園齒輪的正擠壓成形
齒輪正擠壓成形的另一個案例是非園齒輪的精密成形(圖23)。
該齒輪采用正擠壓成形后分割加工,比數(shù)控滾齒加工的生產(chǎn)效率提高幾十倍。正擠壓的難度與園柱齒輪沒有什么不同。只是當外形與正園異較大時,毛坯最好要用冷拔或其他方法做成與非園齒輪外形相同的形狀。
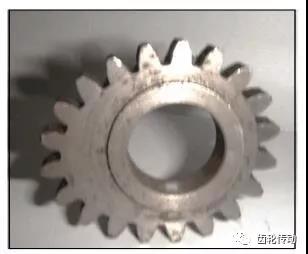
圖23.正擠壓—分割成形的非園齒輪
齒輪正擠壓成形的缺點是成形齒坯的頭、尾有較大的塌角和過渡圓弧,因此齒輪兩端面切削余量大,材料利用率不高,也影響了生產(chǎn)效率的進一步提高。另外齒輪端面切削后容易殘留毛刺,而去毛刺是機加工中最傷腦筋的問題。受擠壓變形率的限制,并考慮到模具制造尺寸和冷鍛壓力機能力等因素,齒輪正擠壓成形目前只應(yīng)用于小規(guī)格園柱齒輪的制造。比起切齒加工,齒輪擠壓成形無論是在質(zhì)量、效率和效益方面,都是一個飛躍。
對于內(nèi)齒輪的制造,可用齒形沖頭反擠壓成形。用該工藝可制造貫通的內(nèi)齒輪(圖24),也可制造底部不通的內(nèi)齒輪(圖25)。在后一種場合,齒輪冷鍛成形不需要預(yù)加工退刀槽,因而在有限尺寸內(nèi)可保證制出最大限度的有效齒形,從而可優(yōu)化零部件結(jié)構(gòu),減小齒輪傳動系統(tǒng)的尺寸并提高齒輪強度。
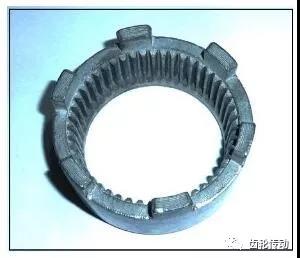
圖24.通孔的內(nèi)齒輪毛坯
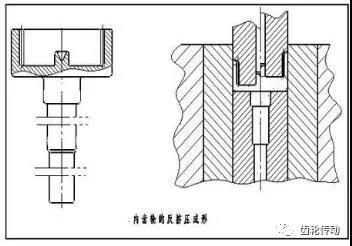
圖25.盲孔的內(nèi)齒輪毛坯和模具結(jié)構(gòu)圖
(3)螺旋齒輪的擠壓成形
當代,齒輪的擠壓成形技術(shù)已從正齒輪成形發(fā)展到了斜齒園柱齒輪和螺旋花鍵軸的擠壓成形(圖26),齒形精度已接近和達到(DIN)7級,能充分滿足大部分汽車齒形零件的要求。冷擠壓成形的齒形零件應(yīng)用已從汽車起動電機、汽車搖窗機等外圍部件發(fā)展到汽車轉(zhuǎn)向機、汽車變速箱等關(guān)鍵總成上。
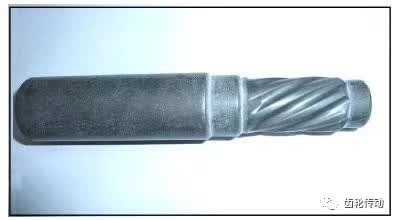
圖26.正擠壓成形的漸開線花鍵軸
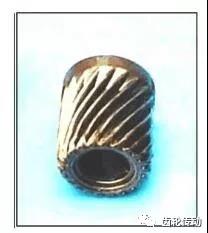
圖27.正擠壓成形的園柱螺旋齒輪
螺旋齒輪的擠壓成形關(guān)鍵技術(shù)是螺旋齒形模具的制作。在使用帶數(shù)控旋轉(zhuǎn)軸的放電加工設(shè)備后,螺旋齒形模具的制造已不太困難。螺旋齒輪擠壓能否成功的另一關(guān)鍵是螺旋齒輪的擠壓的限制。根據(jù)經(jīng)驗,螺旋升角小于27度的齒輪能夠順利擠壓成形。對于貫通式擠壓,螺旋升角還可以加大。
3.園柱齒輪的的分流鍛造
(1)園柱齒輪的閉式冷鐓鍛成形
對于齒寬較窄和直徑較大的園柱齒輪,可用的成形工藝有閉式冷鐓鍛成形(圖28)
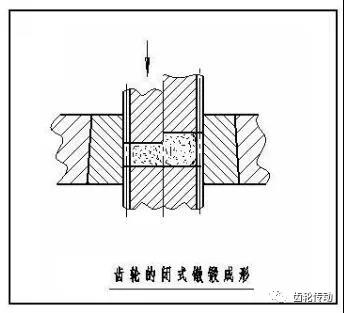
圖28.園柱齒輪的閉式冷鐓鍛成形
由于齒輪冷鐓鍛成形時在齒頂?shù)募饨遣拷饘倭鲃訔l件不好,單用加大鍛造力的方法不能有效地改善齒尖部的充填效果。而加大鍛造力的負面效應(yīng)是使模具壽命大幅度下降。鍛造應(yīng)力的加大還使模具彈性變形增加,使鍛件的齒形精度下降。由于閉模鍛造的特點,當齒坯的下料精度較低時,毛坯體積少量超標就會引起鍛造應(yīng)力的急劇上升,最終造成模具的破損失效。
(2)園柱齒輪的分流鍛造成形
80年代以來,國內(nèi)外精密鍛造專家開始將分流鍛造理論應(yīng)用于正齒輪和螺旋齒輪的冷鍛成形(3)、(4)、(5)。分流鍛造的原理是在毛坯或模具的成形部分建立一個材料的分流腔或分流通道(圖29)。鍛造過程中,材料在充滿型腔的同時,部分材料流向分流腔或分流通道。分流腔或分流通道能容納少量體積超標的材料,而不致于造成鍛造應(yīng)力急劇增加的后果。更主要的是,通過對分流路徑的合理設(shè)計,使鍛造過程中金屬的流動有利于齒形尖角處的充填,從而可在較小的成形應(yīng)力下得到充滿程度較好的齒形。分流鍛造技術(shù)的應(yīng)用,使較高精度齒輪的少、無切削加工迅速達到了產(chǎn)業(yè)化規(guī)模。

圖29.倒擋齒輪的分流成形
另外,以多工位溫鍛或熱精鍛成形作為倒擋齒輪的預(yù)成形,以冷鍛精整來獲得最終的齒形精度,已成為當前大批量生產(chǎn)汽車倒擋齒輪的經(jīng)濟方案。但在小批量生產(chǎn)場合,也可采用全冷鍛成形的方案(圖30)。全冷鍛成形時,可在一臺設(shè)備上通過更換模具完成多道工序,設(shè)備投資較小,適合于多品種中、小批量生產(chǎn)。
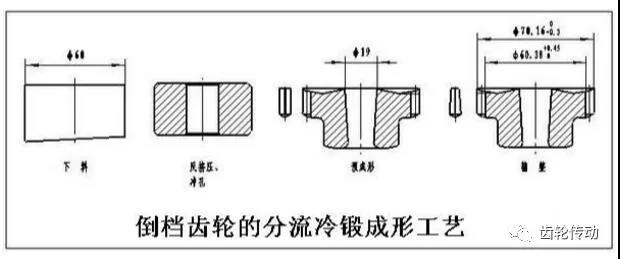
圖30. 倒擋齒輪的分流成形
(3)齒輪分流鍛造的應(yīng)用
與擠壓齒輪相比,分流鍛造的齒輪容易獲得較大的尺寸。齒輪分流鍛造成形后如追加一次冷精整,同樣獲得較好的精度,可完全滿足汽車變速箱齒輪的精度要求。另外,分流鍛造的齒輪端面余量小,材料利用率高。某些情況下,齒形端面可不加工,避免了車削毛刺的發(fā)生。
分流鍛造技術(shù)主要應(yīng)用于汽車變速箱齒輪。除倒擋齒輪外,變速齒坯接合齒的成形和接合齒環(huán)等齒形零件等都有了冷鍛成形的工藝和大批量生產(chǎn)的經(jīng)驗。在國外,變速箱螺旋齒輪與接合齒的整體精鍛(7)也有了成功的經(jīng)驗(圖31;32)。
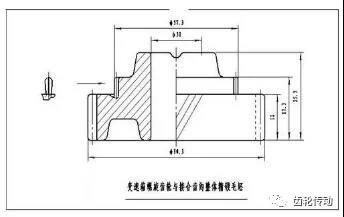
圖31. 變速箱接合齒整體精鍛毛坯
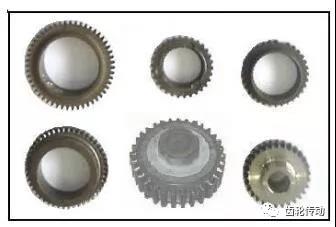
圖32.汽車變速箱結(jié)合齒和倒擋齒輪
(4)園柱齒輪的冷精整技術(shù)
無論是熱鍛、溫鍛或冷鍛狀態(tài)的分流鍛造,都能夠完成園柱齒輪的齒形成形。但由于溫度和模具在大應(yīng)力下工作的影響,分流成形的齒輪精度不會太高,不能滿足汽車齒輪的使用要求。因此,大部分園柱齒輪在分流成形后都必需對齒廓進行精整。為了保證齒輪的精整效果,并使后續(xù)的滲碳熱處理變形小,在分流成形后有必要對齒輪毛坯進行
一次軟化退火或等溫正火。由于園柱齒輪的精整一般是貫通式擠壓,即使預(yù)成形齒坯在壓力下擠過一個精密的齒輪模具(圖33),使毛坯齒廓精度得到提高的方法。在這種精整模式下,齒輪毛坯表面的金屬將與精整模具表面發(fā)生相對流動。為了保證毛坯在模具表面較長距離的流動中不因摩擦而產(chǎn)生粘著燒傷,必需對齒坯實施精細的拋丸和磷化-潤滑處理。潤滑處理可以是皂化處理,也可以滾涂二硫化鉬微粉。

圖33. 園柱齒輪的精整凹模
3.園柱齒輪精密鍛造的技術(shù)瓶頸
目前,窄齒園柱齒輪通過溫鍛或熱鍛、或冷鍛分流成形,并經(jīng)熱處理和磷、皂化處理后實施冷鍛精整,其齒形精度已完全能滿足汽車齒輪的要求。大部份汽車倒擋齒輪和結(jié)合齒環(huán)就是這樣生產(chǎn)的。但對于寬齒園柱齒輪,由于在齒向有修鼓要求,即齒向精度呈“K”線分布,對齒輪精整提出了一個特別的難題(圖34)。
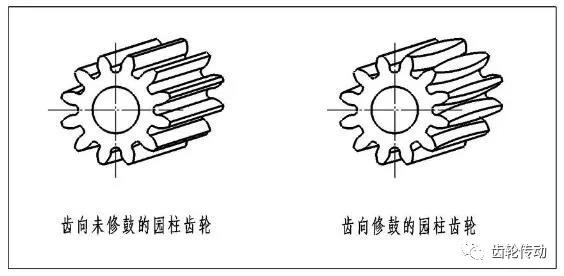
圖34.寬齒園柱齒輪的齒向修鼓
目前,人們提出了種種方法,卻沒有得到一個可靠的結(jié)果。所以,當前寬齒園柱齒輪的精密鍛造成形,只能局限于低精度齒輪制造,或是為磨齒加工提供磨前毛坯。
在當前,探索一個可靠的齒向修鼓方法,突破園柱齒輪精密鍛造的技術(shù)瓶頸,是擺在鍛造和齒輪工作者面前的重大課題。
體現(xiàn)優(yōu)質(zhì)、高效、低成本的汽車齒形零件精鍛成形技術(shù)一定會在汽車零部件生產(chǎn)中得到推廣應(yīng)用。
最新資訊
-
跨越速運憑什么“圈粉”萬千客戶?“
2025-07-01 14:42
-
數(shù)智破局啟新篇?生態(tài)共生再啟程 —
2025-06-27 20:13
-
助力汽車零部件產(chǎn)線智能化升級,西門
2025-06-27 13:59
-
BBA集體轉(zhuǎn)向!放棄全面電動化
2025-06-26 17:32
-
比換柜省錢,比自研省心,西門子Xcel
2025-06-25 15:07