鋁合金汽車頂蓋拉延成形優(yōu)化及回彈控制
2018-04-25 09:38:44· 來(lái)源:鍛造與沖壓
構(gòu)成汽車車身的零件一般分為三類:外覆蓋件、內(nèi)覆蓋件和骨架件,前兩者統(tǒng)稱為覆蓋件。汽車頂蓋作為一種典型的外覆蓋件,在質(zhì)量要求上被劃分為A類件,是消費(fèi)者最直觀接觸到的零件之一,這就要求汽車頂蓋在其表面上有著相對(duì)苛刻的要求。對(duì)于本文所述無(wú)天窗類頂蓋,其拉深程度小,表面圓弧大,沒(méi)有復(fù)雜的特征形狀,因此總體來(lái)說(shuō)其成形相對(duì)簡(jiǎn)單,但是仍不可避免存在圓角凹陷和破裂、法蘭部位起皺等缺陷,其中最難以解決的問(wèn)題是拉延后大面積回彈。
產(chǎn)品介紹及分析
構(gòu)成汽車車身的零件一般分為三類:外覆蓋件、內(nèi)覆蓋件和骨架件,前兩者統(tǒng)稱為覆蓋件。汽車頂蓋作為一種典型的外覆蓋件,在質(zhì)量要求上被劃分為A類件,是消費(fèi)者最直觀接觸到的零件之一,這就要求汽車頂蓋在其表面上有著相對(duì)苛刻的要求。對(duì)于本文所述無(wú)天窗類頂蓋,其拉深程度小,表面圓弧大,沒(méi)有復(fù)雜的特征形狀,因此總體來(lái)說(shuō)其成形相對(duì)簡(jiǎn)單,但是仍不可避免存在圓角凹陷和破裂、法蘭部位起皺等缺陷,其中最難以解決的問(wèn)題是拉延后大面積回彈。
在汽車輕量化的要求下,頂蓋常用5系及6系鋁合金進(jìn)行冷沖成形,且厚度較薄,一般在1mm左右。本文所述為江淮某型號(hào)汽車頂蓋,其材料指定為6016鋁合金,厚度為1mm。該材料強(qiáng)度較高,綜合性能較好,但是延伸率較低,屈強(qiáng)比大,在常溫下成形性能并不是很好,而且成形后回彈嚴(yán)重,因此需要設(shè)計(jì)更為有效的柔性成形工藝來(lái)提高表面質(zhì)量和制件精度。充液拉深工藝作為一種典型的柔性成形工藝,被廣泛應(yīng)用于汽車制造和航空航天領(lǐng)域。該工藝在成形階段通入高壓液體代替凹?;蛘咄鼓?,降低模具成本以及后期的修模時(shí)間,并能在模具之間形成良好的潤(rùn)滑作用,減小摩擦力。現(xiàn)針對(duì)該零件已經(jīng)設(shè)計(jì)完成一套完整的拉延模具,但在后續(xù)參數(shù)調(diào)整中發(fā)現(xiàn)仍然存在一定的問(wèn)題,主要是法蘭起皺和回彈量過(guò)大,本文在現(xiàn)有模具基礎(chǔ)上,基于大型商用有限元模擬軟件Dynaform對(duì)模具進(jìn)行調(diào)整和工藝改進(jìn),提高成形質(zhì)量并減小回彈。
初始模具成形效果
圖1為根據(jù)現(xiàn)有模具提取的有限元模擬當(dāng)中使用的模型示意圖。該零件成形過(guò)程中,其成形質(zhì)量主要受到壓邊力、拉延筋形狀和分布、以及液壓加載方式的影響?,F(xiàn)有模具中拉延筋的形狀和位置已經(jīng)固定,從俯視圖來(lái)看主要為四周直邊,圓角處無(wú)拉延筋,前階段模擬中主要調(diào)整壓邊力以及液壓加載曲線。通過(guò)模擬得到的最優(yōu)的壓邊力為40kN,液壓力在調(diào)整過(guò)程中主要采用如圖2所示的三種加載方式,得到的最優(yōu)路徑為c,該路徑可以保證成形過(guò)程中板料充分變形,減少起皺和拉裂缺陷。模擬得到的最佳結(jié)果如圖3(a)所示。
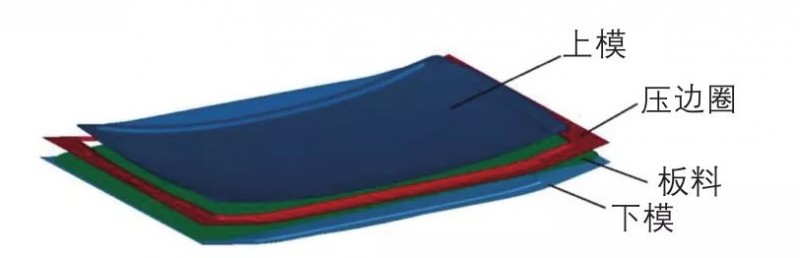
圖1 原始模面充液拉深有限元模型
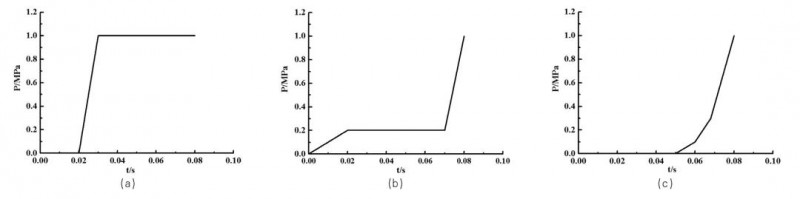
圖2 不同液壓加載路徑
由圖3(a)可以發(fā)現(xiàn)經(jīng)過(guò)優(yōu)化后四個(gè)圓角處仍然存在較為嚴(yán)重的起皺現(xiàn)象,這與現(xiàn)場(chǎng)實(shí)物出現(xiàn)的問(wèn)題一致,如圖3(b)所示。可以判斷,現(xiàn)有模具仍存在待改進(jìn)之處,因此設(shè)計(jì)兩種改進(jìn)方案如下文所述。

圖3 模擬結(jié)果與實(shí)物對(duì)照示意圖
改進(jìn)方案一(壓邊圈填補(bǔ)法)
進(jìn)一步分析起皺的原因可以發(fā)現(xiàn),凹???個(gè)交角區(qū)域在上模下行的過(guò)程中沒(méi)有模具限制,成形后出現(xiàn)嚴(yán)重的起皺缺陷,如圖4所示。因此對(duì)原模面進(jìn)行優(yōu)化設(shè)計(jì),如圖5所示,將上模4個(gè)交角區(qū)域(圖5(a)標(biāo)注區(qū)域)添加到壓邊圈上。通過(guò)補(bǔ)充壓邊圈內(nèi)圓角處,增大壓邊圈在下壓過(guò)程中對(duì)坯料的作用效果,減小坯料圓角成形過(guò)程中的失穩(wěn)現(xiàn)象,從而消除起皺。優(yōu)化后的模面得到圖6所示的結(jié)果,可以發(fā)現(xiàn)起皺現(xiàn)象得到明顯改善,減薄率為13.9%,符合制件減薄率<15%的要求。
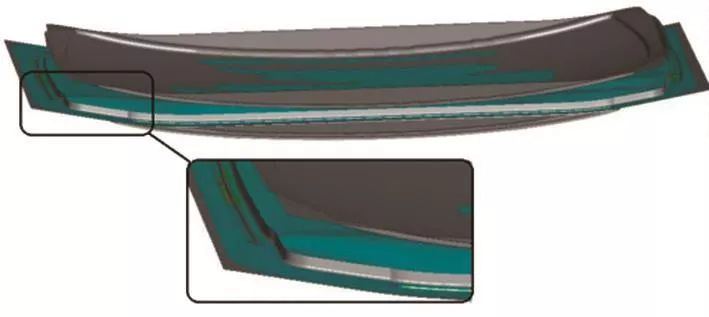
圖4 起皺原因示意圖
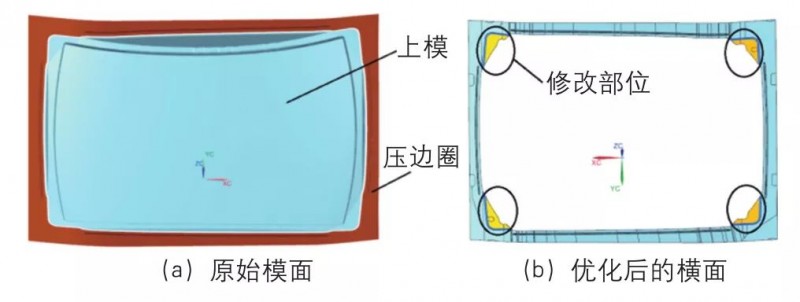
圖5 模具優(yōu)化示意圖
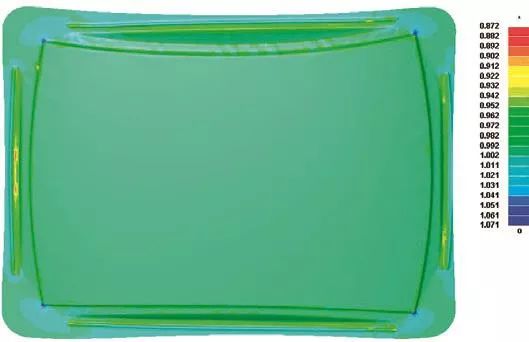
圖6 方案一優(yōu)化結(jié)果示意圖
分析上述結(jié)果可以判斷該修模方案可以很好的滿足對(duì)頂蓋成形質(zhì)量的要求,但是仍然存在一些問(wèn)題。如果按照上述方案進(jìn)行優(yōu)化,需要對(duì)壓邊圈及凸模進(jìn)行較大程度修改,這是一個(gè)相對(duì)來(lái)講很復(fù)雜的工作,會(huì)花費(fèi)大量的人力物力,這就要求找到更為簡(jiǎn)單的方法。
模擬過(guò)程中可以發(fā)現(xiàn)成形主要的影響參數(shù)為拉延筋形狀和位置、壓邊力以及液壓曲線,這幾個(gè)參數(shù)反復(fù)協(xié)調(diào)以后發(fā)現(xiàn)角部仍存在起皺以及拉裂情況,因此在較優(yōu)參數(shù)下又進(jìn)行了坯料形狀和大小的優(yōu)化,目的是應(yīng)用最小阻力原則改善金屬在角部的流動(dòng)情況。在設(shè)計(jì)的幾種板料形狀中選擇主要的三種如圖7所示,其圖7(a)方形板料尺寸為1700×1300mm2,圖7(b)和圖7(c)所示板料是在圖7(a)所示板料基礎(chǔ)上分別進(jìn)行了倒圓角和倒斜角處理,從模擬結(jié)果可知圖7(c)所示板料形狀為最優(yōu),如圖8(b)所示,無(wú)拉裂和起皺情況,減薄率符合要求。
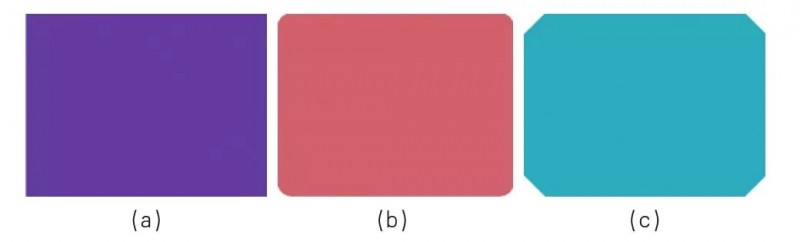
圖7 坯料形狀優(yōu)化示意圖
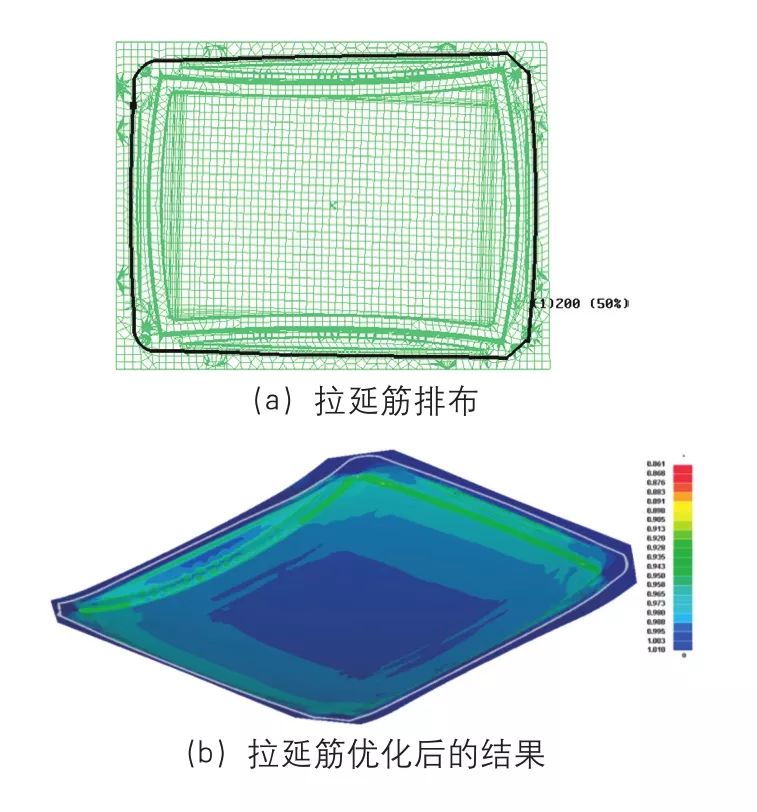
圖8 拉延筋優(yōu)化示意圖
回彈預(yù)測(cè)
通過(guò)前期對(duì)模面的修改工作,已經(jīng)可以很好的達(dá)到成形要求,但是仍需要對(duì)拉延結(jié)束后的回彈進(jìn)行預(yù)測(cè)和分析。圖9(a)為公司按照原有工藝生產(chǎn)的零件在拉延之后實(shí)際測(cè)得的回彈量,圖9(b)為基于Dynaform軟件的回彈模塊得到的回彈云圖,兩者整體趨勢(shì)基本相同,模擬的數(shù)值略大于實(shí)測(cè)值。由圖中可以看到,回彈最嚴(yán)重的的部位發(fā)生在兩側(cè)的工藝補(bǔ)充面上,一般認(rèn)為,只要實(shí)際的零件覆蓋范圍內(nèi)回彈值滿足要求即可,在此基礎(chǔ)上盡量控制補(bǔ)充面上的回彈,避免在修邊工序后應(yīng)力釋放導(dǎo)致回彈加劇。
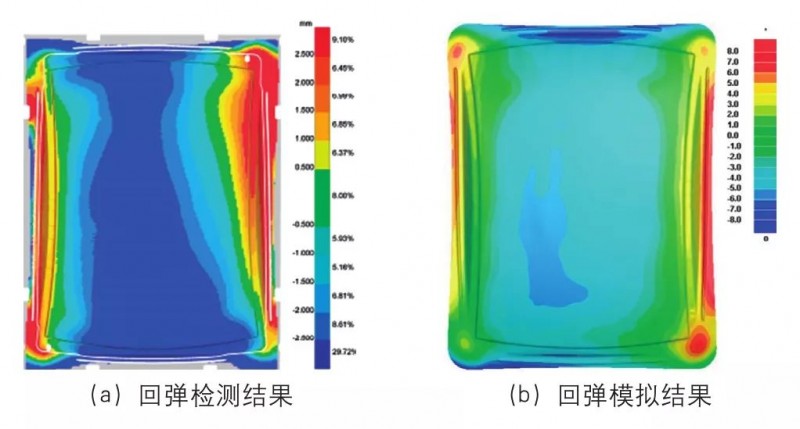
圖9 回彈檢測(cè)報(bào)告及模擬結(jié)果
在現(xiàn)有結(jié)果基礎(chǔ)上根據(jù)最終制定的拉延筋排布方式以及坯料的形狀,進(jìn)行拉延筋參數(shù)、壓邊力、模具間隙和液壓力這幾個(gè)影響回彈的主要參數(shù)進(jìn)行協(xié)調(diào)和優(yōu)化,得到的回彈優(yōu)化結(jié)果如圖10所示。從圖中可以知道,零件覆蓋的范圍內(nèi)回彈基本小于0.5mm,滿足生產(chǎn)要求,即使修邊之后應(yīng)力釋放使回彈增大,生產(chǎn)中可以通過(guò)后續(xù)整形工步實(shí)現(xiàn)回彈控制。
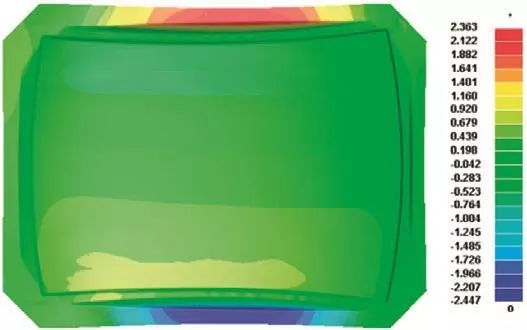
圖10 回彈優(yōu)化后回彈模擬結(jié)果
結(jié)論
最新資訊
-
跨越速運(yùn)憑什么“圈粉”萬(wàn)千客戶?“
2025-07-01 14:42
-
數(shù)智破局啟新篇?生態(tài)共生再啟程 —
2025-06-27 20:13
-
助力汽車零部件產(chǎn)線智能化升級(jí),西門(mén)
2025-06-27 13:59
-
BBA集體轉(zhuǎn)向!放棄全面電動(dòng)化
2025-06-26 17:32
-
比換柜省錢(qián),比自研省心,西門(mén)子X(jué)cel
2025-06-25 15:07