弧齒錐齒輪熱后硬齒面刮削工藝試驗
2018-04-10 08:50:42· 來源:齒輪傳動
汽車驅動橋作為汽車的重要傳動部件,對整車的承載能力和舒適性有很大影響,其中主被動錐齒輪是驅動橋中最重要的零件。傳統(tǒng)的弧齒錐齒輪加工流程為制坯—軟齒面切削(干切或濕切)—熱處理—熱后研齒或磨齒。
汽車驅動橋作為汽車的重要傳動部件,對整車的承載能力和舒適性有很大影響,其中主被動錐齒輪是驅動橋中最重要的零件。傳統(tǒng)的弧齒錐齒輪加工流程為制坯—軟齒面切削(干切或濕切)—熱處理—熱后研齒或磨齒。
常規(guī)的加工工藝過程中,在熱前將齒面接觸區(qū)修正完成后,由于材料或其他方面的原因,熱處理變形的存在,導致熱處理后齒面接觸區(qū)形狀與位置發(fā)生很大變化。為此,熱后對齒面接觸區(qū)修正成為必不可少的工序,目前國內(nèi)應用較普遍的是研齒或磨齒工藝。
磨齒工藝的開展需要花費巨資引進弧齒磨齒機,與弧齒銑齒機相比較,弧齒磨齒機工藝復雜,機床調(diào)整繁瑣,修要經(jīng)常對砂輪進行修正。并且由于磨削過程中切削液的存在,不可避免會對環(huán)境產(chǎn)生影響。研齒工藝的開展,也需要引進研齒設備,并且機床調(diào)整較為復雜,由于研齒工藝無法修正變形較大的齒面接觸區(qū),只能對其做小部分修正。因此,研齒后的齒輪副其本身幾何精度并無太大提高。
基于以上原因,需求更經(jīng)濟、環(huán)保有效的熱后加工工藝成為必然選擇。隨著刀具材料技術和淬硬切削技術的進步,淬硬工件的加工已得到大規(guī)模推廣應用。為此,決定嘗試在弧齒錐齒輪銑齒機上,利用新型切削刀具,進行硬切削試驗。
1.熱后硬切削應用的可行性分析
本次工藝試驗決定使用PCBN復合焊接刀具進行試驗。PCBN即聚晶立方氮化硼(Polycrystalline Cubic Boron Nitride)作為利用人工方法合成的硬度僅次于天然金剛石的新型刀具材料,是目前高速切削鐵系金屬最合適的刀具材料。
根據(jù)相關資料介紹,用PCBN刀具加工淬硬鋼時,要求工件淬火硬度高于60~65HRC,加工硬鑄鐵時,只要硬度達到中等硬度水平(45HRC),就會取得良好的加工效果。目前公司內(nèi)被動錐齒輪熱后內(nèi)孔精加工即使用CBN刀片,切削余量為0.3mm,使用效果良好。而目前我公司內(nèi)錐齒輪副熱處理后硬度范圍為58~62HRC,完全滿足該類型刀具的使用條件,對其進行工藝試驗完全可行。
PCBN刀具的制造主要通過CBN粉末和結合劑經(jīng)超高壓高溫燒結而成.大致步驟有;混合粉末--模壓成型/與硬質(zhì)合金底層組裝成整體--超高壓高溫燒結--深加工。在CBN聚晶體中也可以不加粘結劑直接燒結而成聚晶立方氮化硼。CBN在燒結時發(fā)生再結晶和晶粒長大過程,燒結后的CBN多晶體的晶粒已不是原來的CBN單晶體顆粒。這種PCBN刀具耐磨性好,壽命長,但較脆且溫度條件苛刻,難以制成高韌性及大尺寸的刀片。 故本次試驗中采用焊接式結構,將刀齒做成三部分結構。
本次工藝試驗采用AC16被動錐齒輪進行,使用12英寸銑刀盤,其刀齒參數(shù)主要借鑒目前所使用的熱前精切刀齒參數(shù)。刀齒由三部分組成:高速鋼刀具基體、硬質(zhì)合金基體、PCBN切削刃。各部分間焊接成型。
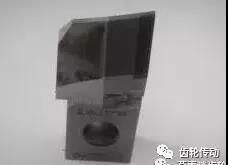
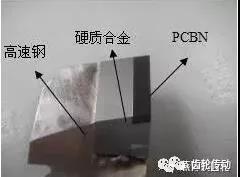
圖1 復合式焊接刀具
2.熱后硬切削切削參數(shù)的確定
根據(jù)相關資料介紹,PCBN刀具適合的切削速度為80-120m/min,結合刀具直徑,算出的刀具轉速應為:
n=1000*V/(3.14*d)=104r/min-125r/min
本次試驗在格里森NO.26機床上進行,所選取的速度掛輪為:20/70*28/62,刀具主軸轉速為114r/min。
PCBN刀具的吃刀量范圍為0.15-0.25mm,本次切削試驗中所采用的切削余量為0.2mm左右。進給量選擇在0.03r/min。
3.熱后硬切削工裝設計
由于熱處理前后的重復裝夾,不可避免會在熱后加工時出現(xiàn)亂齒現(xiàn)象,為此,對切齒工裝更改了設計,增加一套對齒機構。此外,將定位碟簧尺寸進行了更改,使用了熱后研配用碟簧,提高了工裝整體的剛性。
4.熱后硬切削加工情況
在本次工藝試驗中,采用大輪雙精刀盤進行加工,通過對齒機構的調(diào)整,實現(xiàn)了凹面與凸面的單獨切削。切削過程中,機床無明顯震動,刀具無損壞,加工中出現(xiàn)明顯火花。由于切削熱大部分被切屑帶走,切屑顏色為微藍色,因此,切削后工件僅有微熱感。
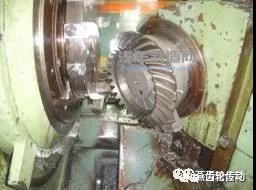
圖2 切削情況
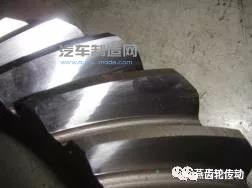
圖3 切削后齒輪齒面
切削后工件表面發(fā)亮,粗糙度達到Ra0.5左右,高于外圓磨粗糙度。
5.熱后硬加工質(zhì)量情況
經(jīng)過熱后硬加工的零部件進行檢測,齒圈跳動可達0.05,遠低于產(chǎn)品圖紙成品要求。與小輪研配后的齒面接觸區(qū)如下:

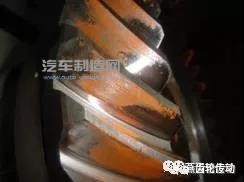
圖4 成品接觸區(qū)圖片
距離嚙合點0.5米時,檢測噪音結果如下:
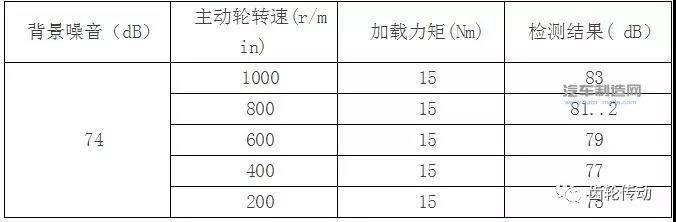
按常規(guī)工藝加工的齒輪副檢測結果為:
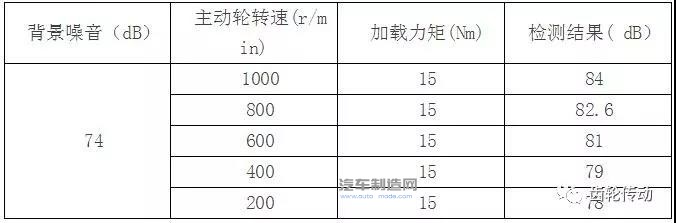
由此可以看出,熱后切削加工的齒輪副其質(zhì)量水平較正常加工零件質(zhì)量要高。
6.結論
1.目前在國內(nèi),對于硬度超過HRC50的錐齒輪產(chǎn)品,大部分采取的為熱后磨削工藝或者研齒工藝,熱后硬切削加工方法和裝備在中國重卡制造領域屬于空白。對于我公司,此次為首次引進熱后硬切削技術,屬于公司內(nèi)首創(chuàng),且在國內(nèi)重卡行業(yè)處于領先地位。
2.通過進行工藝試驗,驗證了熱后弧齒錐齒輪硬齒面刮削工藝的可行性,為以后生產(chǎn)高精度齒輪副奠定了基礎,加工后的齒輪副質(zhì)量狀況完全滿足要求,從根本上消除了熱處理變形對接觸區(qū)的影響。
常規(guī)的加工工藝過程中,在熱前將齒面接觸區(qū)修正完成后,由于材料或其他方面的原因,熱處理變形的存在,導致熱處理后齒面接觸區(qū)形狀與位置發(fā)生很大變化。為此,熱后對齒面接觸區(qū)修正成為必不可少的工序,目前國內(nèi)應用較普遍的是研齒或磨齒工藝。
磨齒工藝的開展需要花費巨資引進弧齒磨齒機,與弧齒銑齒機相比較,弧齒磨齒機工藝復雜,機床調(diào)整繁瑣,修要經(jīng)常對砂輪進行修正。并且由于磨削過程中切削液的存在,不可避免會對環(huán)境產(chǎn)生影響。研齒工藝的開展,也需要引進研齒設備,并且機床調(diào)整較為復雜,由于研齒工藝無法修正變形較大的齒面接觸區(qū),只能對其做小部分修正。因此,研齒后的齒輪副其本身幾何精度并無太大提高。
基于以上原因,需求更經(jīng)濟、環(huán)保有效的熱后加工工藝成為必然選擇。隨著刀具材料技術和淬硬切削技術的進步,淬硬工件的加工已得到大規(guī)模推廣應用。為此,決定嘗試在弧齒錐齒輪銑齒機上,利用新型切削刀具,進行硬切削試驗。
1.熱后硬切削應用的可行性分析
本次工藝試驗決定使用PCBN復合焊接刀具進行試驗。PCBN即聚晶立方氮化硼(Polycrystalline Cubic Boron Nitride)作為利用人工方法合成的硬度僅次于天然金剛石的新型刀具材料,是目前高速切削鐵系金屬最合適的刀具材料。
根據(jù)相關資料介紹,用PCBN刀具加工淬硬鋼時,要求工件淬火硬度高于60~65HRC,加工硬鑄鐵時,只要硬度達到中等硬度水平(45HRC),就會取得良好的加工效果。目前公司內(nèi)被動錐齒輪熱后內(nèi)孔精加工即使用CBN刀片,切削余量為0.3mm,使用效果良好。而目前我公司內(nèi)錐齒輪副熱處理后硬度范圍為58~62HRC,完全滿足該類型刀具的使用條件,對其進行工藝試驗完全可行。
PCBN刀具的制造主要通過CBN粉末和結合劑經(jīng)超高壓高溫燒結而成.大致步驟有;混合粉末--模壓成型/與硬質(zhì)合金底層組裝成整體--超高壓高溫燒結--深加工。在CBN聚晶體中也可以不加粘結劑直接燒結而成聚晶立方氮化硼。CBN在燒結時發(fā)生再結晶和晶粒長大過程,燒結后的CBN多晶體的晶粒已不是原來的CBN單晶體顆粒。這種PCBN刀具耐磨性好,壽命長,但較脆且溫度條件苛刻,難以制成高韌性及大尺寸的刀片。 故本次試驗中采用焊接式結構,將刀齒做成三部分結構。
本次工藝試驗采用AC16被動錐齒輪進行,使用12英寸銑刀盤,其刀齒參數(shù)主要借鑒目前所使用的熱前精切刀齒參數(shù)。刀齒由三部分組成:高速鋼刀具基體、硬質(zhì)合金基體、PCBN切削刃。各部分間焊接成型。
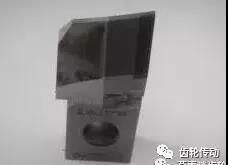
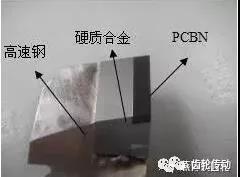
圖1 復合式焊接刀具
2.熱后硬切削切削參數(shù)的確定
根據(jù)相關資料介紹,PCBN刀具適合的切削速度為80-120m/min,結合刀具直徑,算出的刀具轉速應為:
n=1000*V/(3.14*d)=104r/min-125r/min
本次試驗在格里森NO.26機床上進行,所選取的速度掛輪為:20/70*28/62,刀具主軸轉速為114r/min。
PCBN刀具的吃刀量范圍為0.15-0.25mm,本次切削試驗中所采用的切削余量為0.2mm左右。進給量選擇在0.03r/min。
3.熱后硬切削工裝設計
由于熱處理前后的重復裝夾,不可避免會在熱后加工時出現(xiàn)亂齒現(xiàn)象,為此,對切齒工裝更改了設計,增加一套對齒機構。此外,將定位碟簧尺寸進行了更改,使用了熱后研配用碟簧,提高了工裝整體的剛性。
4.熱后硬切削加工情況
在本次工藝試驗中,采用大輪雙精刀盤進行加工,通過對齒機構的調(diào)整,實現(xiàn)了凹面與凸面的單獨切削。切削過程中,機床無明顯震動,刀具無損壞,加工中出現(xiàn)明顯火花。由于切削熱大部分被切屑帶走,切屑顏色為微藍色,因此,切削后工件僅有微熱感。
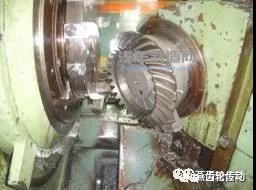
圖2 切削情況
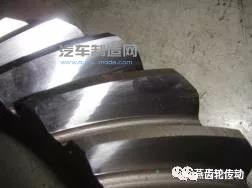
圖3 切削后齒輪齒面
切削后工件表面發(fā)亮,粗糙度達到Ra0.5左右,高于外圓磨粗糙度。
5.熱后硬加工質(zhì)量情況
經(jīng)過熱后硬加工的零部件進行檢測,齒圈跳動可達0.05,遠低于產(chǎn)品圖紙成品要求。與小輪研配后的齒面接觸區(qū)如下:

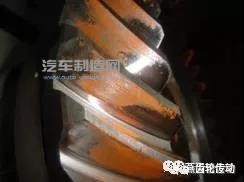
圖4 成品接觸區(qū)圖片
距離嚙合點0.5米時,檢測噪音結果如下:
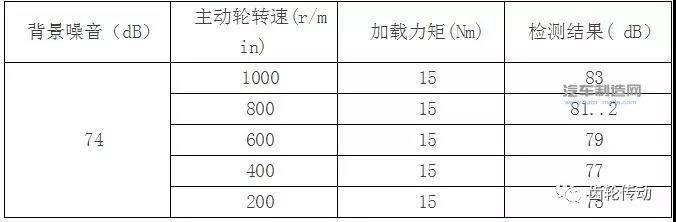
按常規(guī)工藝加工的齒輪副檢測結果為:
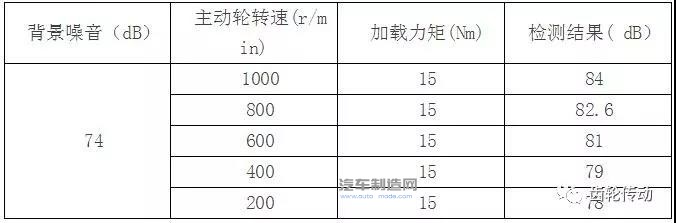
由此可以看出,熱后切削加工的齒輪副其質(zhì)量水平較正常加工零件質(zhì)量要高。
6.結論
1.目前在國內(nèi),對于硬度超過HRC50的錐齒輪產(chǎn)品,大部分采取的為熱后磨削工藝或者研齒工藝,熱后硬切削加工方法和裝備在中國重卡制造領域屬于空白。對于我公司,此次為首次引進熱后硬切削技術,屬于公司內(nèi)首創(chuàng),且在國內(nèi)重卡行業(yè)處于領先地位。
2.通過進行工藝試驗,驗證了熱后弧齒錐齒輪硬齒面刮削工藝的可行性,為以后生產(chǎn)高精度齒輪副奠定了基礎,加工后的齒輪副質(zhì)量狀況完全滿足要求,從根本上消除了熱處理變形對接觸區(qū)的影響。
編輯推薦
最新資訊
-
跨越速運憑什么“圈粉”萬千客戶?“
2025-07-01 14:42
-
數(shù)智破局啟新篇?生態(tài)共生再啟程 —
2025-06-27 20:13
-
助力汽車零部件產(chǎn)線智能化升級,西門
2025-06-27 13:59
-
BBA集體轉向!放棄全面電動化
2025-06-26 17:32
-
比換柜省錢,比自研省心,西門子Xcel
2025-06-25 15:07