簡(jiǎn)單分析整體輪加工效率和程序的優(yōu)化
2018-03-23 16:15:14· 來(lái)源:《金屬加工》 作者:鄒毅
隨著鐵路運(yùn)輸需要,機(jī)車(chē)速度和牽引噸位不斷提高,要求機(jī)車(chē)整體輪生產(chǎn)能力提高2~3倍。整體輪生產(chǎn)按照原來(lái)的工藝已無(wú)法滿足生產(chǎn)需求。
隨著鐵路運(yùn)輸需要,機(jī)車(chē)速度和牽引噸位不斷提高,要求機(jī)車(chē)整體輪生產(chǎn)能力提高2~3倍。整體輪生產(chǎn)按照原來(lái)的工藝已無(wú)法滿足生產(chǎn)需求。德國(guó)進(jìn)口鍛件整體輪如圖1所示,毛坯質(zhì)量約為1 000kg,孔與外圓嚴(yán)重偏心,內(nèi)孔偏心和輪廓直徑加工余量大,且輪坯表面附著硬度很高的氧化層及鋼印號(hào),切削中費(fèi)時(shí)又費(fèi)刀,直接影響生產(chǎn)效率及產(chǎn)品的質(zhì)量,針對(duì)上述一系列加工難點(diǎn),合理選擇整體輪加工工藝路線,優(yōu)化程序,優(yōu)選刀具,有效保證質(zhì)量與加工效率成為生產(chǎn)中的當(dāng)務(wù)之急。
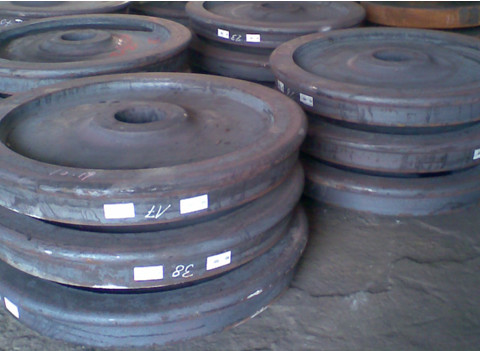
圖1 德國(guó)進(jìn)口整體輪毛坯實(shí)物
1.整體輪加工難點(diǎn)分析及應(yīng)對(duì)措施
在型號(hào)CK5116B-4A的數(shù)控立車(chē)上加工整體輪毛坯,其工藝難點(diǎn)表現(xiàn)為以下幾個(gè)方面:
原來(lái)是把內(nèi)側(cè)平面、孔(見(jiàn)圖2)放在C5116B普通立式車(chē)床上加工,外側(cè)面、內(nèi)弧面和踏面分別在數(shù)控車(chē)床上加工,因裝夾次數(shù)過(guò)多,定位基準(zhǔn)面位移產(chǎn)生0.5~1mm的定位誤差,定位精度不能保證。由于普通立車(chē)上加工內(nèi)側(cè)平面、孔,工序簡(jiǎn)單、加工速度快,造成占地面積大,且多一臺(tái)普通立車(chē)就要增加操作工人。
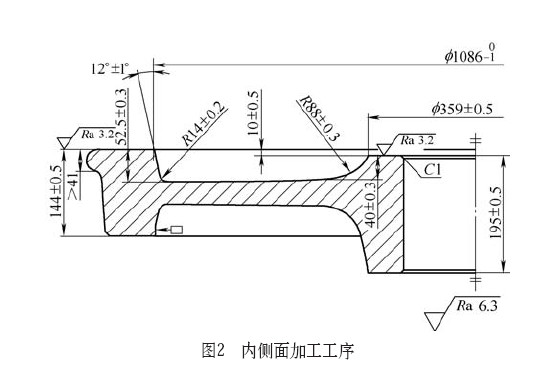
分析上述不利的因素,決定擬定一條合理的工藝加工路線,減少裝夾次數(shù),在普通立車(chē)上把外側(cè)面和孔在一次裝夾中加工出來(lái),利用如圖3所示的夾具,把內(nèi)側(cè)面和踏面(見(jiàn)圖4)一次加工出來(lái),把加工順序及走刀路線集中分配,不僅利于車(chē)削加工,還保證了尺寸精度,效率明顯提高。
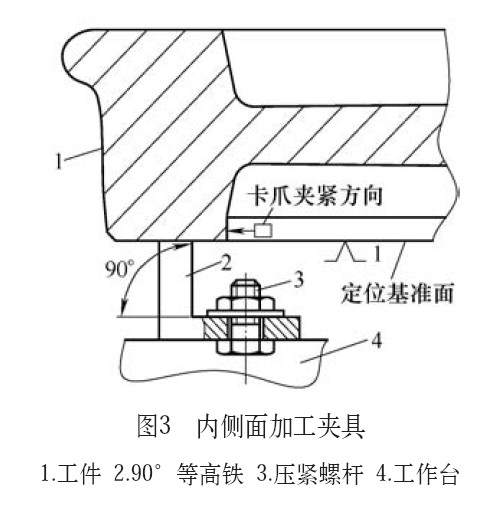
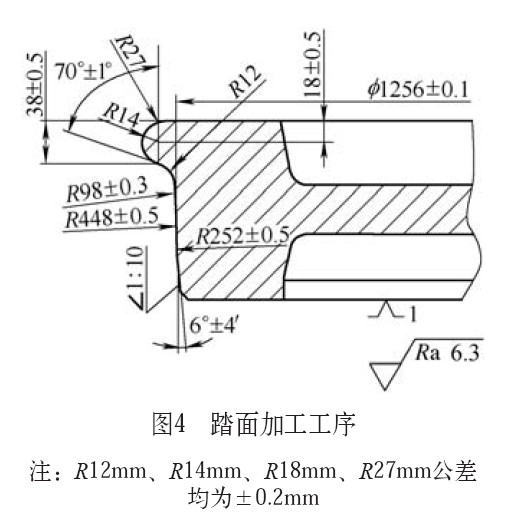
原編制加工程序利用G94恒轉(zhuǎn)速車(chē)削,加工時(shí)主軸轉(zhuǎn)速恒定,通過(guò)手動(dòng)調(diào)節(jié)進(jìn)給倍率開(kāi)關(guān)和主軸倍率開(kāi)關(guān),這樣加工費(fèi)時(shí)費(fèi)力。
經(jīng)過(guò)分析,考慮應(yīng)修改程序加工指令,用恒線速車(chē)削指令代替G94恒轉(zhuǎn)速,使整個(gè)工件加工時(shí)保證恒定的切削速度,減少了因切削速度變化引起工件表面結(jié)構(gòu)不一致的現(xiàn)象,充分發(fā)揮了數(shù)控機(jī)床的優(yōu)勢(shì)。
粗加工大型鍛件毛坯,由于毛坯偏心、加工量不均勻等因素,在編制加工程序方面應(yīng)考慮每道工序盡量減少空行程,按最短路線安排加工表面的加工順序。加工內(nèi)側(cè)圓弧和外側(cè)圓弧如圖5所示,原加工程序是利用“環(huán)繞法”加工編制,加工時(shí)的不利條件有:加工內(nèi)弧面和外側(cè)面,由于毛坯量集中在兩邊圓弧,中間平面加工余量偏少,粗加工過(guò)程造成空行程時(shí)間過(guò)長(zhǎng);空行程時(shí),刀片接觸毛坯表面氧化層,導(dǎo)致刀片磨損快,降低了刀具壽命。
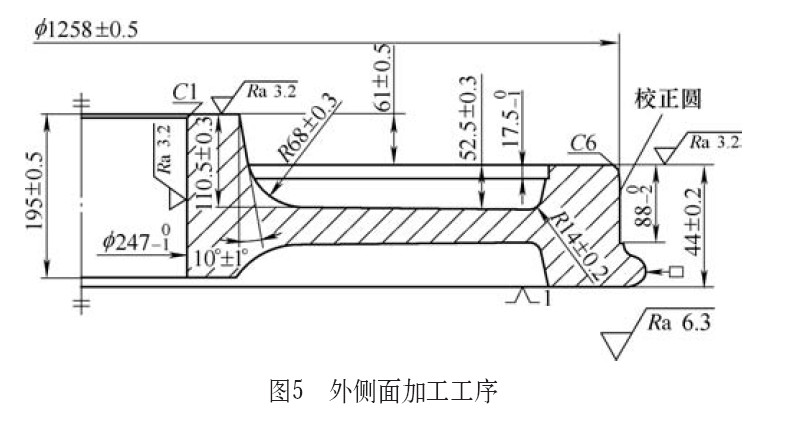
原工藝用φ28mm刀具加工,由于該刀具刀片接觸面積寬,切削抗力大,易引起振動(dòng),使切削不平穩(wěn),對(duì)機(jī)床精度有很大影響。
應(yīng)對(duì)措施是采用刀片直徑較小的涂層硬質(zhì)合金刀具取代現(xiàn)用刀具,這樣可減小切削抗力,使切削更平穩(wěn),涂層刀具具有承受高速切削和強(qiáng)力切削的性能,耐磨性更好,不僅有利于提高功效,而且降低了刀具消耗。
2.改進(jìn)加工工藝
(1)制定合理的工藝路線。原加工工藝路線:車(chē)內(nèi)側(cè)平面、車(chē)孔→車(chē)外側(cè)面→車(chē)內(nèi)側(cè)弧面、車(chē)踏面。
新工藝加工路線:車(chē)外側(cè)面、車(chē)孔→車(chē)內(nèi)側(cè)面、車(chē)內(nèi)平面、內(nèi)弧面、踏面,新的工藝路線體現(xiàn)了以下優(yōu)點(diǎn):①工序變得連貫,加工一個(gè)整體輪,兩道工序共耗時(shí)約2h,生產(chǎn)效率高。②減少了設(shè)備數(shù)量(兩臺(tái)數(shù)控加工)、操作工人人數(shù)和占地面積,節(jié)省人力物力。③減少了工件裝夾次數(shù),由原來(lái)的3次裝夾減少到2次裝夾,定位誤差大大減小,縮短了輔助時(shí)間,同時(shí)也為后繼工序(比如裝夾、吊運(yùn)和翻面)帶來(lái)了方便,生產(chǎn)效率顯著提高。
在新的工藝路線中,外側(cè)面和孔可以通過(guò)1次裝夾加工出來(lái),內(nèi)側(cè)面可以在1次裝夾中加工出來(lái)。新的工藝加工1個(gè)整體輪,兩道工序耗時(shí)僅僅2h左右,與原來(lái)的加工工藝相比,工效提高兩倍,充分達(dá)到了工藝創(chuàng)新的目的。
(2)優(yōu)化加工程序。①將G94恒轉(zhuǎn)速改用G96恒線速加工,使切削速度不因直徑大小的改變而改變,始終保持恒定的切削速度。②因毛坯加工量不均勻,毛坯偏心嚴(yán)重,原加工程序是用G41,現(xiàn)決定把原加工程序分兩段加工。加工程序如表1~表3所示(表1為主程序,表2、表3是分段程序)。
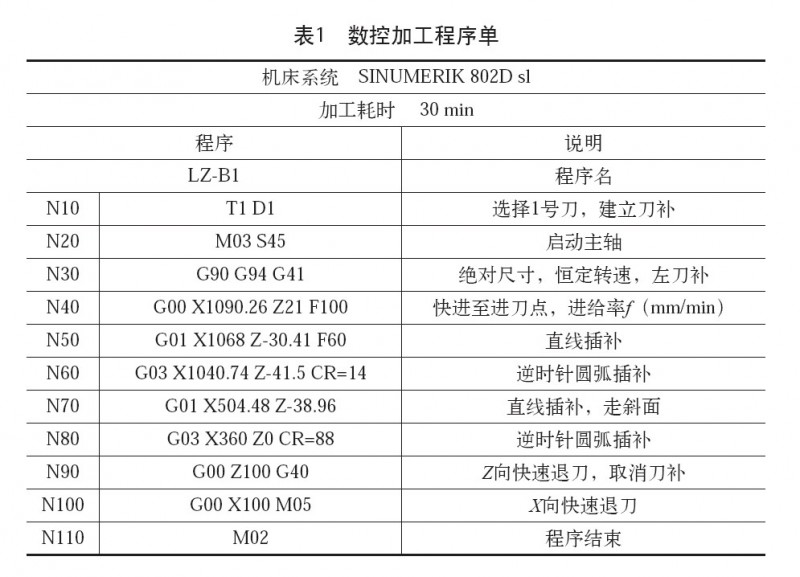
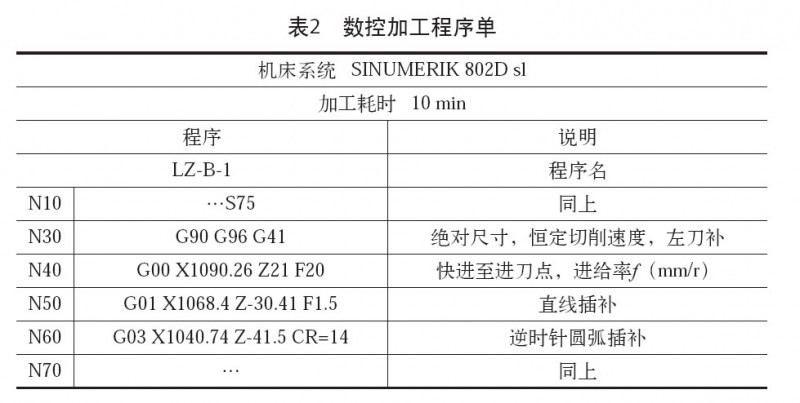
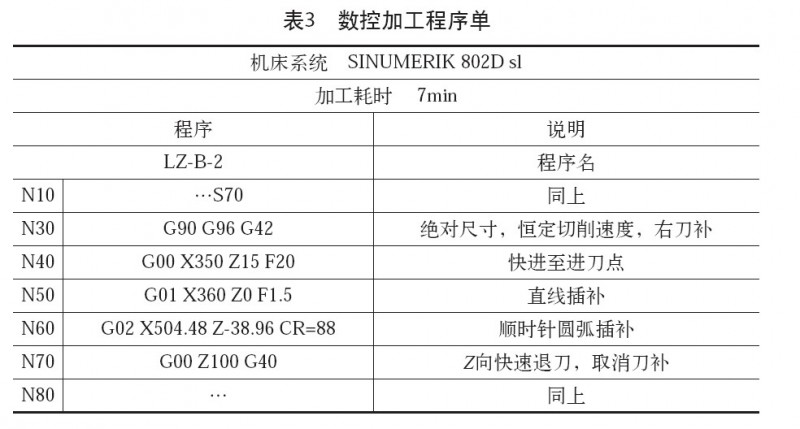
主程序LZ-B1分為:LZ-B-1補(bǔ)償G41刀具半徑,輪廓左邊,順時(shí)針車(chē)削加工;LZ-B-2補(bǔ)償G42刀具半徑,輪廓右邊,逆時(shí)針車(chē)削加工。
把主程序LZ-B1分兩段加工,既縮短了加工路線,減少了刀具空行程時(shí)間,提高了工作效率,僅加工內(nèi)側(cè)圓弧面就節(jié)約了13min左右的空行程走刀,又減少了一次換刀片的時(shí)間。通過(guò)計(jì)算,利用程序分段加工一個(gè)整體輪可以節(jié)約加工時(shí)間26min左右;由于弧板面中間斜面毛坯量只有一刀,采用分段加工避免了刀片直接接觸氧化層而磨損刀片,降低了刀具磨損,延長(zhǎng)刀具使用壽命;提高了工作效率,降低了刀具的消耗,體現(xiàn)了“提高生產(chǎn)率和降低成本”這個(gè)目的,從而實(shí)現(xiàn)精益生產(chǎn)。
(3)優(yōu)選加工刀具。整體輪材料分析如表4所示,通過(guò)了解整體輪材質(zhì)及硬度,粗加工較大的鍛件毛坯,首先考慮刀具材料應(yīng)具有較高的切削性能和刀具壽命,因此在六軸車(chē)整體輪粗加工中應(yīng)盡量使用優(yōu)質(zhì)高效刀具,充分把數(shù)控立車(chē)的效率發(fā)揮出來(lái)。
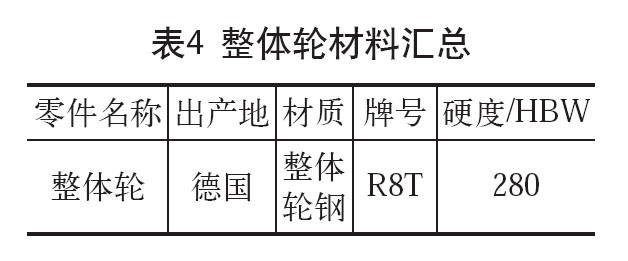
在刀具選擇方面進(jìn)行了分析、比較和試驗(yàn)等大量工作,最后優(yōu)化篩選出用φ20mm涂層硬質(zhì)合金刀具取代φ28mm的大直徑圓弧刀具。用φ20mm涂層硬質(zhì)合金的小直徑圓弧刀具加工,刀具實(shí)物如圖6所示。該刀具的優(yōu)點(diǎn)如下:①此刀具刀片直徑小,切削時(shí)刀片接觸面積小,降低了切削抗力,無(wú)振刀現(xiàn)象,并對(duì)機(jī)床損耗小。②刀片材料為涂層硬質(zhì)合金,具有表面硬度高、耐磨性好且能承受高速切削和強(qiáng)力切削等特性。③切削效率高,切削時(shí)比未涂層刀具壽命高3~4倍,切削速度高20%~70%,加工精度高0.5~1級(jí),刀具消耗費(fèi)用降低20%~50%。
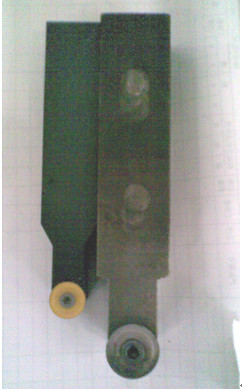
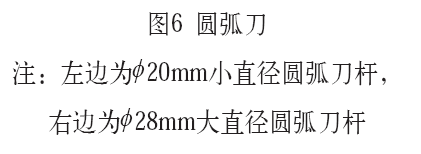
(4)使用φ20mm涂層硬質(zhì)合金刀具和使用φ28mm刀具比較如下:
在加工內(nèi)側(cè)面和踏面圓弧時(shí),用φ28mm大直徑圓弧刀桿切削,抗力大、切削速度慢、起刀距離遠(yuǎn)、走刀時(shí)間長(zhǎng),加工1個(gè)內(nèi)側(cè)圓弧面就要1片刀片,該刀片價(jià)值人民幣38.9~42元。用φ20mm的小直徑圓弧刀桿加工,加工4個(gè)內(nèi)側(cè)圓弧面才換1次刀片,每片刀片費(fèi)用約人民幣68~73.55元。
φ28mm刀具車(chē)削表面有振動(dòng)波紋,還需要再精車(chē),尺寸精度、表面結(jié)構(gòu)達(dá)不到圖樣要求;新刀片切削效率高,由原來(lái)的轉(zhuǎn)速n = 25r/min提高到n = 45r/min,進(jìn)給量f由原來(lái)的0.3~0.5mm/r提高到了0.5~1mm/r;可以一次加工到尺寸,可以有效地控制尺寸精度。
由于φ28mm刀具接觸面大而引起的機(jī)床振動(dòng),對(duì)機(jī)床損耗很大,機(jī)床故障率較高。 班組5臺(tái)數(shù)控立車(chē)維修工時(shí)多達(dá)150h左右,改用φ20mm刀具后,5臺(tái)數(shù)控立車(chē)每月維修工時(shí)最高70h。
加工內(nèi)側(cè)面里面平面時(shí),兩種刀具切削三要素的比較如表5所示。
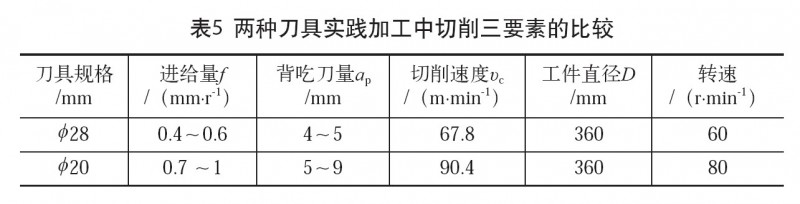
上述加工過(guò)程中可以看到,φ20mm的小直徑圓弧刀桿優(yōu)勢(shì)非常明顯,該刀具具有良好的耐磨性和耐熱性,特別適合高速切削;由于其耐用度高、通用性好,加工時(shí)可以有效減少換刀片次數(shù),提高加工效率,推動(dòng)了整體輪粗加工切削的進(jìn)步。
3.結(jié)語(yǔ)
更改整體輪加工工藝實(shí)現(xiàn)了工序的集中,大大提升了工作效率,節(jié)約了1次裝夾校正的輔助時(shí)間;對(duì)加工程序的優(yōu)化,從根本上消除了不必要的空行程走刀,減少了刀具的不必要磨損,大大提高了刀具壽命,從根本上提高了整體輪粗加工效率,由改進(jìn)前粗加工一個(gè)車(chē)輪要用4h,通過(guò)3道工序才能完工,現(xiàn)僅用2h,通過(guò)兩道工序加工完成一個(gè)車(chē)輪;由原來(lái)一個(gè)班只能加工3個(gè)車(chē)輪提高到每個(gè)班完成6個(gè)車(chē)輪,提高工效兩倍,產(chǎn)品的一次交檢合格率達(dá)到99.98%。
通過(guò)對(duì)刀具的優(yōu)選,用φ20mm的刀具取代φ28mm刀具,刀片可以節(jié)約60元/班,按11臺(tái)數(shù)控機(jī)床三班倒計(jì)算,每月可節(jié)約5 1480元,一年可節(jié)約刀具消耗成本約617 760元。產(chǎn)品質(zhì)量大幅提高,表面結(jié)構(gòu)完全符合圖樣要求。
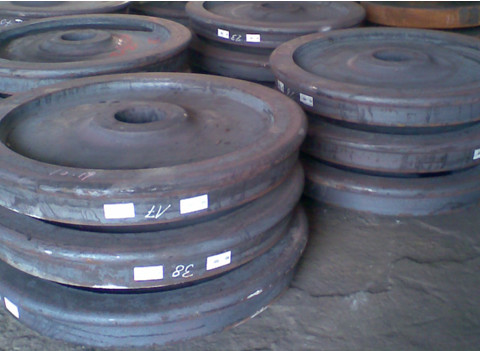
圖1 德國(guó)進(jìn)口整體輪毛坯實(shí)物
1.整體輪加工難點(diǎn)分析及應(yīng)對(duì)措施
在型號(hào)CK5116B-4A的數(shù)控立車(chē)上加工整體輪毛坯,其工藝難點(diǎn)表現(xiàn)為以下幾個(gè)方面:
原來(lái)是把內(nèi)側(cè)平面、孔(見(jiàn)圖2)放在C5116B普通立式車(chē)床上加工,外側(cè)面、內(nèi)弧面和踏面分別在數(shù)控車(chē)床上加工,因裝夾次數(shù)過(guò)多,定位基準(zhǔn)面位移產(chǎn)生0.5~1mm的定位誤差,定位精度不能保證。由于普通立車(chē)上加工內(nèi)側(cè)平面、孔,工序簡(jiǎn)單、加工速度快,造成占地面積大,且多一臺(tái)普通立車(chē)就要增加操作工人。
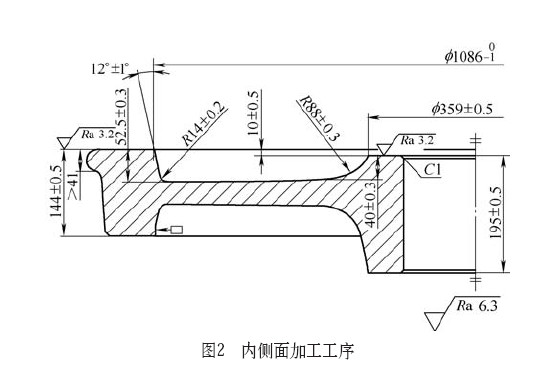
分析上述不利的因素,決定擬定一條合理的工藝加工路線,減少裝夾次數(shù),在普通立車(chē)上把外側(cè)面和孔在一次裝夾中加工出來(lái),利用如圖3所示的夾具,把內(nèi)側(cè)面和踏面(見(jiàn)圖4)一次加工出來(lái),把加工順序及走刀路線集中分配,不僅利于車(chē)削加工,還保證了尺寸精度,效率明顯提高。
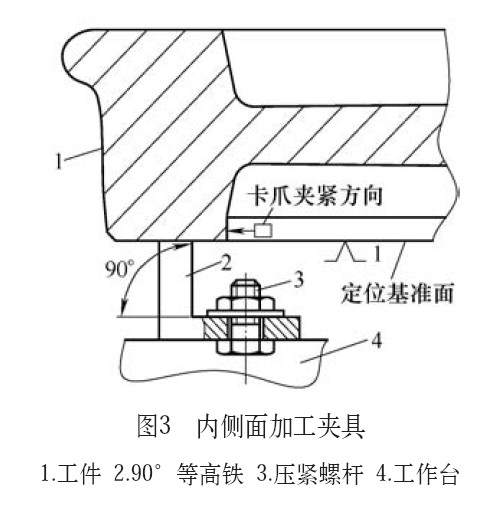
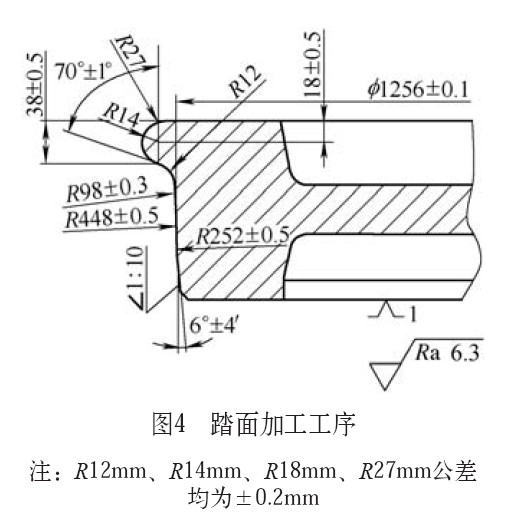
原編制加工程序利用G94恒轉(zhuǎn)速車(chē)削,加工時(shí)主軸轉(zhuǎn)速恒定,通過(guò)手動(dòng)調(diào)節(jié)進(jìn)給倍率開(kāi)關(guān)和主軸倍率開(kāi)關(guān),這樣加工費(fèi)時(shí)費(fèi)力。
經(jīng)過(guò)分析,考慮應(yīng)修改程序加工指令,用恒線速車(chē)削指令代替G94恒轉(zhuǎn)速,使整個(gè)工件加工時(shí)保證恒定的切削速度,減少了因切削速度變化引起工件表面結(jié)構(gòu)不一致的現(xiàn)象,充分發(fā)揮了數(shù)控機(jī)床的優(yōu)勢(shì)。
粗加工大型鍛件毛坯,由于毛坯偏心、加工量不均勻等因素,在編制加工程序方面應(yīng)考慮每道工序盡量減少空行程,按最短路線安排加工表面的加工順序。加工內(nèi)側(cè)圓弧和外側(cè)圓弧如圖5所示,原加工程序是利用“環(huán)繞法”加工編制,加工時(shí)的不利條件有:加工內(nèi)弧面和外側(cè)面,由于毛坯量集中在兩邊圓弧,中間平面加工余量偏少,粗加工過(guò)程造成空行程時(shí)間過(guò)長(zhǎng);空行程時(shí),刀片接觸毛坯表面氧化層,導(dǎo)致刀片磨損快,降低了刀具壽命。
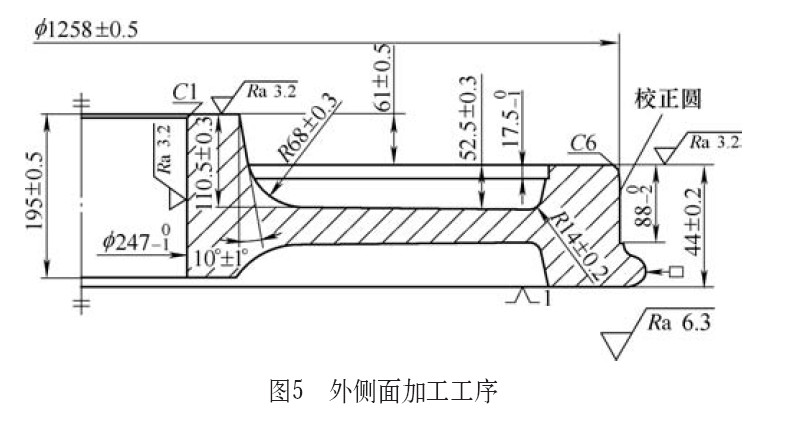
原工藝用φ28mm刀具加工,由于該刀具刀片接觸面積寬,切削抗力大,易引起振動(dòng),使切削不平穩(wěn),對(duì)機(jī)床精度有很大影響。
應(yīng)對(duì)措施是采用刀片直徑較小的涂層硬質(zhì)合金刀具取代現(xiàn)用刀具,這樣可減小切削抗力,使切削更平穩(wěn),涂層刀具具有承受高速切削和強(qiáng)力切削的性能,耐磨性更好,不僅有利于提高功效,而且降低了刀具消耗。
2.改進(jìn)加工工藝
(1)制定合理的工藝路線。原加工工藝路線:車(chē)內(nèi)側(cè)平面、車(chē)孔→車(chē)外側(cè)面→車(chē)內(nèi)側(cè)弧面、車(chē)踏面。
新工藝加工路線:車(chē)外側(cè)面、車(chē)孔→車(chē)內(nèi)側(cè)面、車(chē)內(nèi)平面、內(nèi)弧面、踏面,新的工藝路線體現(xiàn)了以下優(yōu)點(diǎn):①工序變得連貫,加工一個(gè)整體輪,兩道工序共耗時(shí)約2h,生產(chǎn)效率高。②減少了設(shè)備數(shù)量(兩臺(tái)數(shù)控加工)、操作工人人數(shù)和占地面積,節(jié)省人力物力。③減少了工件裝夾次數(shù),由原來(lái)的3次裝夾減少到2次裝夾,定位誤差大大減小,縮短了輔助時(shí)間,同時(shí)也為后繼工序(比如裝夾、吊運(yùn)和翻面)帶來(lái)了方便,生產(chǎn)效率顯著提高。
在新的工藝路線中,外側(cè)面和孔可以通過(guò)1次裝夾加工出來(lái),內(nèi)側(cè)面可以在1次裝夾中加工出來(lái)。新的工藝加工1個(gè)整體輪,兩道工序耗時(shí)僅僅2h左右,與原來(lái)的加工工藝相比,工效提高兩倍,充分達(dá)到了工藝創(chuàng)新的目的。
(2)優(yōu)化加工程序。①將G94恒轉(zhuǎn)速改用G96恒線速加工,使切削速度不因直徑大小的改變而改變,始終保持恒定的切削速度。②因毛坯加工量不均勻,毛坯偏心嚴(yán)重,原加工程序是用G41,現(xiàn)決定把原加工程序分兩段加工。加工程序如表1~表3所示(表1為主程序,表2、表3是分段程序)。
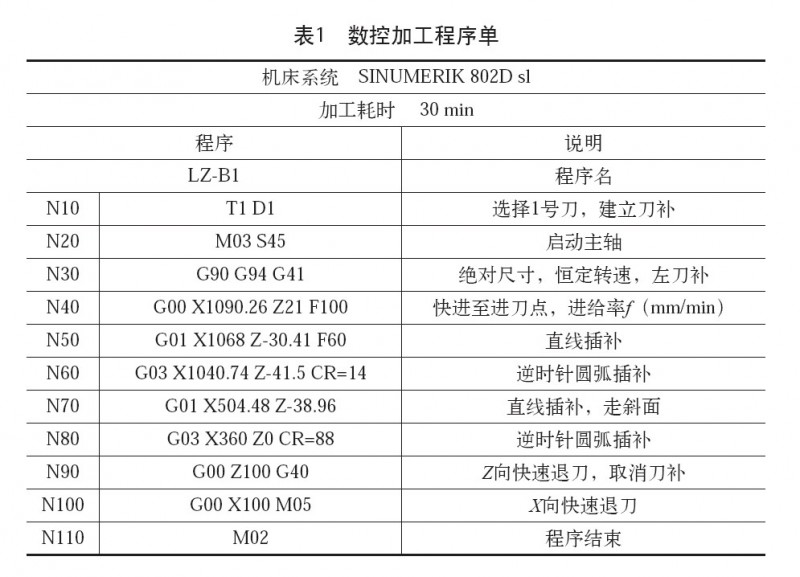
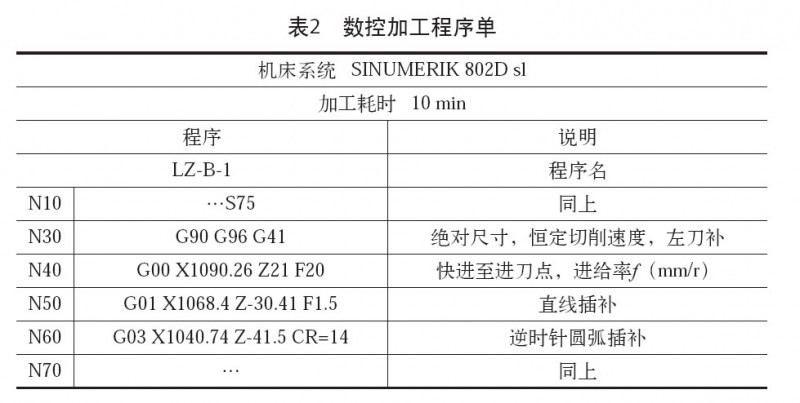
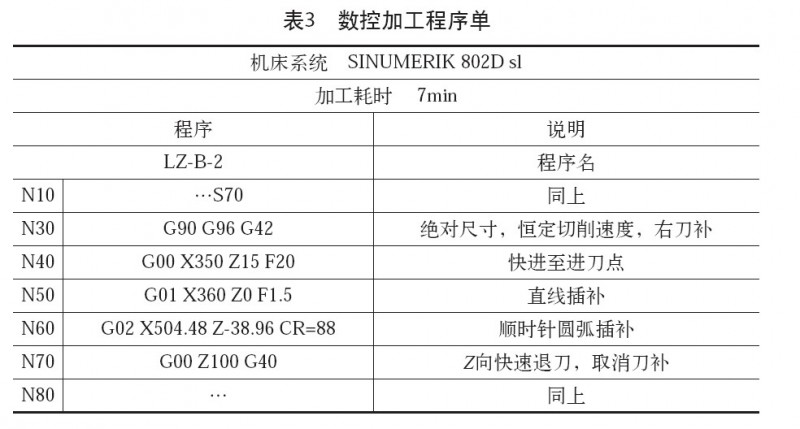
主程序LZ-B1分為:LZ-B-1補(bǔ)償G41刀具半徑,輪廓左邊,順時(shí)針車(chē)削加工;LZ-B-2補(bǔ)償G42刀具半徑,輪廓右邊,逆時(shí)針車(chē)削加工。
把主程序LZ-B1分兩段加工,既縮短了加工路線,減少了刀具空行程時(shí)間,提高了工作效率,僅加工內(nèi)側(cè)圓弧面就節(jié)約了13min左右的空行程走刀,又減少了一次換刀片的時(shí)間。通過(guò)計(jì)算,利用程序分段加工一個(gè)整體輪可以節(jié)約加工時(shí)間26min左右;由于弧板面中間斜面毛坯量只有一刀,采用分段加工避免了刀片直接接觸氧化層而磨損刀片,降低了刀具磨損,延長(zhǎng)刀具使用壽命;提高了工作效率,降低了刀具的消耗,體現(xiàn)了“提高生產(chǎn)率和降低成本”這個(gè)目的,從而實(shí)現(xiàn)精益生產(chǎn)。
(3)優(yōu)選加工刀具。整體輪材料分析如表4所示,通過(guò)了解整體輪材質(zhì)及硬度,粗加工較大的鍛件毛坯,首先考慮刀具材料應(yīng)具有較高的切削性能和刀具壽命,因此在六軸車(chē)整體輪粗加工中應(yīng)盡量使用優(yōu)質(zhì)高效刀具,充分把數(shù)控立車(chē)的效率發(fā)揮出來(lái)。
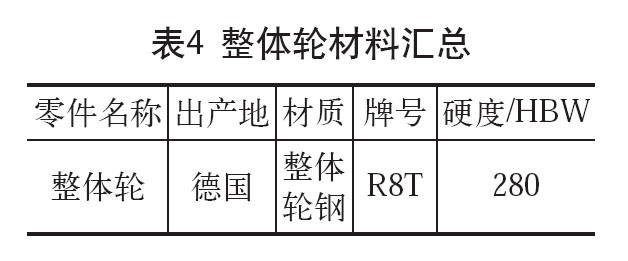
在刀具選擇方面進(jìn)行了分析、比較和試驗(yàn)等大量工作,最后優(yōu)化篩選出用φ20mm涂層硬質(zhì)合金刀具取代φ28mm的大直徑圓弧刀具。用φ20mm涂層硬質(zhì)合金的小直徑圓弧刀具加工,刀具實(shí)物如圖6所示。該刀具的優(yōu)點(diǎn)如下:①此刀具刀片直徑小,切削時(shí)刀片接觸面積小,降低了切削抗力,無(wú)振刀現(xiàn)象,并對(duì)機(jī)床損耗小。②刀片材料為涂層硬質(zhì)合金,具有表面硬度高、耐磨性好且能承受高速切削和強(qiáng)力切削等特性。③切削效率高,切削時(shí)比未涂層刀具壽命高3~4倍,切削速度高20%~70%,加工精度高0.5~1級(jí),刀具消耗費(fèi)用降低20%~50%。
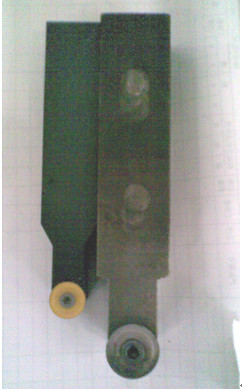
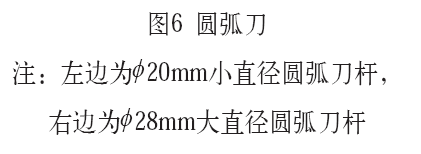
(4)使用φ20mm涂層硬質(zhì)合金刀具和使用φ28mm刀具比較如下:
在加工內(nèi)側(cè)面和踏面圓弧時(shí),用φ28mm大直徑圓弧刀桿切削,抗力大、切削速度慢、起刀距離遠(yuǎn)、走刀時(shí)間長(zhǎng),加工1個(gè)內(nèi)側(cè)圓弧面就要1片刀片,該刀片價(jià)值人民幣38.9~42元。用φ20mm的小直徑圓弧刀桿加工,加工4個(gè)內(nèi)側(cè)圓弧面才換1次刀片,每片刀片費(fèi)用約人民幣68~73.55元。
φ28mm刀具車(chē)削表面有振動(dòng)波紋,還需要再精車(chē),尺寸精度、表面結(jié)構(gòu)達(dá)不到圖樣要求;新刀片切削效率高,由原來(lái)的轉(zhuǎn)速n = 25r/min提高到n = 45r/min,進(jìn)給量f由原來(lái)的0.3~0.5mm/r提高到了0.5~1mm/r;可以一次加工到尺寸,可以有效地控制尺寸精度。
由于φ28mm刀具接觸面大而引起的機(jī)床振動(dòng),對(duì)機(jī)床損耗很大,機(jī)床故障率較高。 班組5臺(tái)數(shù)控立車(chē)維修工時(shí)多達(dá)150h左右,改用φ20mm刀具后,5臺(tái)數(shù)控立車(chē)每月維修工時(shí)最高70h。
加工內(nèi)側(cè)面里面平面時(shí),兩種刀具切削三要素的比較如表5所示。
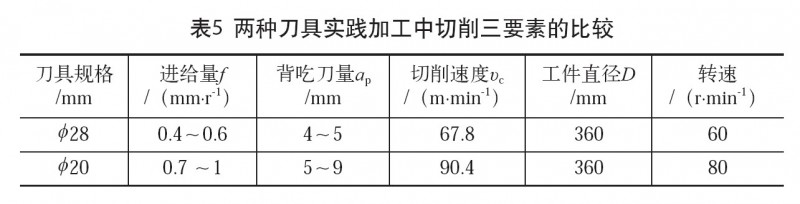
上述加工過(guò)程中可以看到,φ20mm的小直徑圓弧刀桿優(yōu)勢(shì)非常明顯,該刀具具有良好的耐磨性和耐熱性,特別適合高速切削;由于其耐用度高、通用性好,加工時(shí)可以有效減少換刀片次數(shù),提高加工效率,推動(dòng)了整體輪粗加工切削的進(jìn)步。
3.結(jié)語(yǔ)
更改整體輪加工工藝實(shí)現(xiàn)了工序的集中,大大提升了工作效率,節(jié)約了1次裝夾校正的輔助時(shí)間;對(duì)加工程序的優(yōu)化,從根本上消除了不必要的空行程走刀,減少了刀具的不必要磨損,大大提高了刀具壽命,從根本上提高了整體輪粗加工效率,由改進(jìn)前粗加工一個(gè)車(chē)輪要用4h,通過(guò)3道工序才能完工,現(xiàn)僅用2h,通過(guò)兩道工序加工完成一個(gè)車(chē)輪;由原來(lái)一個(gè)班只能加工3個(gè)車(chē)輪提高到每個(gè)班完成6個(gè)車(chē)輪,提高工效兩倍,產(chǎn)品的一次交檢合格率達(dá)到99.98%。
通過(guò)對(duì)刀具的優(yōu)選,用φ20mm的刀具取代φ28mm刀具,刀片可以節(jié)約60元/班,按11臺(tái)數(shù)控機(jī)床三班倒計(jì)算,每月可節(jié)約5 1480元,一年可節(jié)約刀具消耗成本約617 760元。產(chǎn)品質(zhì)量大幅提高,表面結(jié)構(gòu)完全符合圖樣要求。
編輯推薦
最新資訊
-
跨越速運(yùn)憑什么“圈粉”萬(wàn)千客戶(hù)?“
2025-07-01 14:42
-
數(shù)智破局啟新篇?生態(tài)共生再啟程 —
2025-06-27 20:13
-
助力汽車(chē)零部件產(chǎn)線智能化升級(jí),西門(mén)
2025-06-27 13:59
-
BBA集體轉(zhuǎn)向!放棄全面電動(dòng)化
2025-06-26 17:32
-
比換柜省錢(qián),比自研省心,西門(mén)子X(jué)cel
2025-06-25 15:07