輕量化白車身及多材料連接技術(shù)的發(fā)展
2018-01-11 13:06:28· 來源:AI制造
汽車輕量化是節(jié)能減排的一個有效途徑,而汽車輕量化最有效的手段就是輕質(zhì)合金材料的應(yīng)用,目前國外已開發(fā)出多種多材料應(yīng)用的輕量化白車身,但其連接問題成為瓶頸,目前通用的點(diǎn)焊連接技術(shù)已無法滿足要求,各種新晉的連接技術(shù)層出不窮。
汽車輕量化
汽車輕量化是節(jié)能減排的一個有效途徑,而汽車輕量化最有效的手段就是輕質(zhì)合金材料的應(yīng)用,目前國外已開發(fā)出多種多材料應(yīng)用的輕量化白車身,但其連接問題成為瓶頸,目前通用的點(diǎn)焊連接技術(shù)已無法滿足要求,各種新晉的連接技術(shù)層出不窮。
隨著國外輕量化白車身的發(fā)展,白車身的用材由鋼板應(yīng)用階段逐步發(fā)展到多材料混合應(yīng)用階段。本文以奧迪品牌的白車身發(fā)展進(jìn)程為例,歸納了其白車身用材演化的四個階段,分析了典型歐系、美系和日系車型白車身用材發(fā)展現(xiàn)狀及用材趨勢。
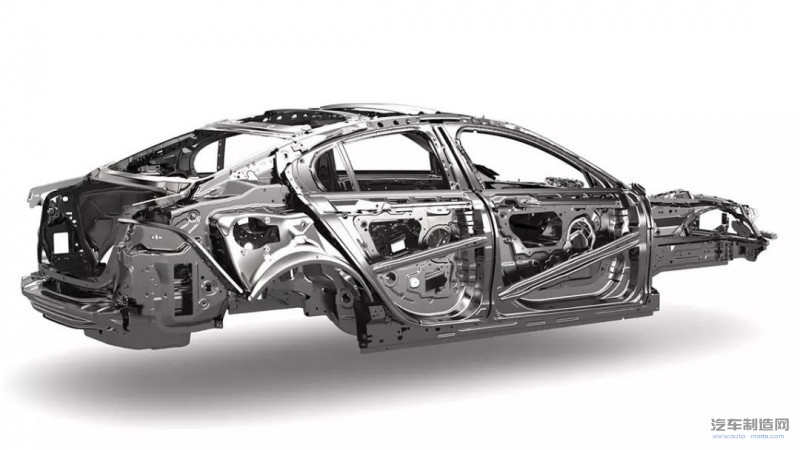
伴隨著輕量化白車身的發(fā)展,其相應(yīng)的多材料連接技術(shù)也隨之發(fā)展迅速。針對四個白車身發(fā)展階段,列舉了目前9種常用的多材料連接技術(shù),也對應(yīng)規(guī)劃為4個不同階段,分析了每個階段進(jìn)程的多材料連接技術(shù)的適用范圍與優(yōu)劣勢。
國外輕量化車身發(fā)展過程
縱觀國外白車身的發(fā)展趨勢,奧迪公司的白車身發(fā)展趨勢極具代表性,到目前為止,其白車身的發(fā)展過程可分為四個階段:
第一階段:鋁合金覆蓋件開發(fā)階段
這個階段主要是為了增加材料強(qiáng)度級別,熱成形鋼逐步用于車身,還有少量鋁合金覆蓋件的應(yīng)用。典型的車型代表為奧迪A3車型(見圖1)。
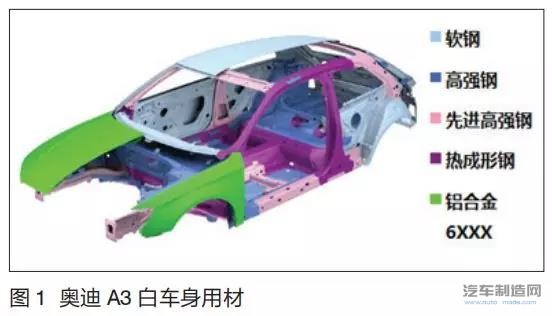
零部件用材方面,機(jī)蓋、翼子板使用鋁合金材質(zhì)(3.2%),后座椅橫梁、中通道、A柱、B柱、機(jī)艙縱梁后段、前圍下板、后地板橫梁和后地板縱梁等位置采用熱成形鋼(21.7%)。
第二階段:鋁合金外覆蓋件成熟應(yīng)用階段
這一階段,外覆蓋件大量采用鋁合金,鋁合金覆蓋件比重顯著增加,熱成形鋼比重相對減少,典型的車型代表是奧迪A6車型(見圖2)。
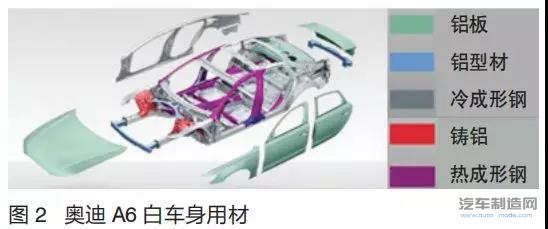
零部件用材方面,機(jī)蓋、前后車門、翼子板、行李箱蓋板、頂蓋和前后防撞梁(鋁型材)應(yīng)用鋁合金。鋁合金用量較第一階段增加至18%,中通道、座椅橫梁、A柱和B柱等位置保留熱成形鋼,熱成形鋼的用量比例減少至11.3%。
第三階段:全鋁車身開發(fā)應(yīng)用階段
這個階段,車身外覆蓋件全部應(yīng)用鋁合金(鋁板材)、鋁型材和鑄鋁開始應(yīng)用到車身結(jié)構(gòu)件,輕量化效果顯著,與此同時,高強(qiáng)鋼和軟鋼板的用量急劇減少,典型的車型代表是奧迪TT車型(見圖3)。
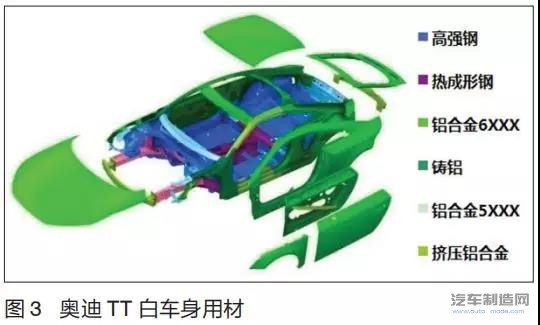
零部件用材方面,增加了A柱、C柱、側(cè)圍和頂蓋橫梁等位置的鋁合金,鋁合金用量由18%增加到35.8%,中通道、座椅橫梁采用熱成形鋼,軟鋼應(yīng)用量由35.2%下降到5.3%。
第四階段:多材料混合應(yīng)用階段
這一階段以鋁合金為主要車身材料,鋁型材和鑄鋁件大量應(yīng)用到車身結(jié)構(gòu)件。高強(qiáng)鋼、軟鋼和碳纖維為輔助用材,典型的車型代表是奧迪Q7車型(見圖4)。

零部件用材方面,地板、前縱梁等位置應(yīng)用鋁合金,鋁合金用量較上一階段由35.8%增加到49.9%,中通道采用的是鋁板和熱成形鋼的混合結(jié)構(gòu),熱成形鋼的用量減少至9.2%。
車身用材比較及發(fā)展趨勢
以上四款車型的白車身用材比例如表1所示。
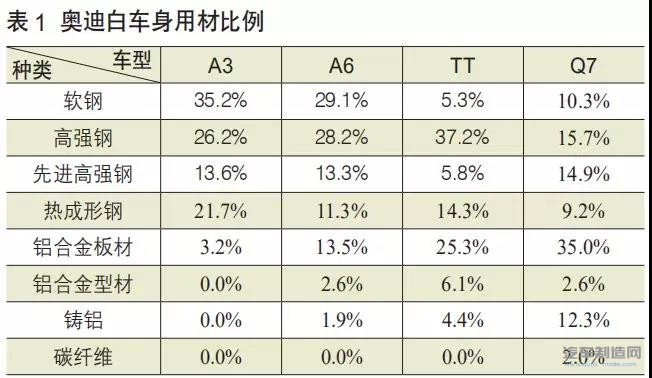
分析奧迪用材趨勢如下:
鋁合金用量上升趨勢明顯(3.2%→18.0%→35.8%→49.9%);
熱成形鋼整體用量呈下降趨勢(21.7%→11.3%→14.3%→9.2%);
軟鋼用量下降趨勢明顯(35.2%→29.1%→5.3%→10.3%)。
除歐系的奧迪車型外,美系福特和日系車的用材比例如表2、表3所示。
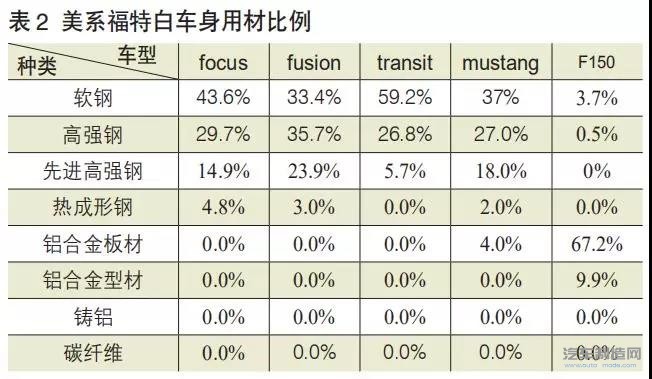
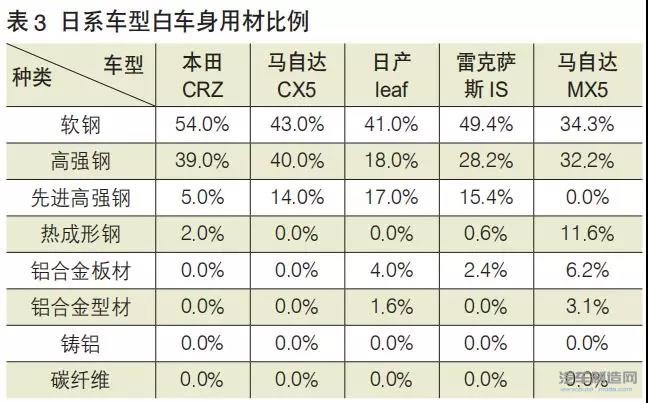
表2中,福特focus、福特fusion、福特transit和福特mustang處于奧迪輕量化白車身第一階段用材水平,且只有福特mustang的機(jī)蓋、翼子板應(yīng)用鋁合金(4%),福特F150處于奧迪輕量化白車身第三階段用材水平,車身結(jié)構(gòu)件和覆蓋件大量應(yīng)用鋁合金。
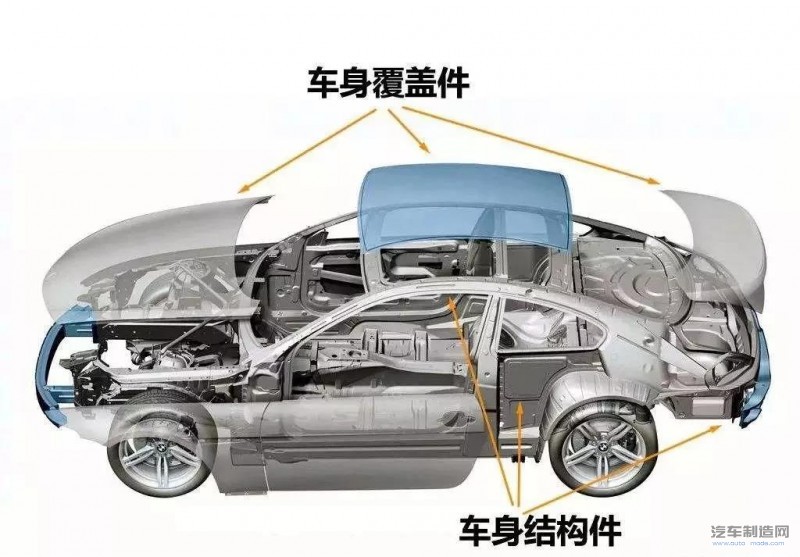
表3中的5款日系車型均處于奧迪輕量化白車身第一階段用材水平。在日系車型中,只有對輕量化要求較高的跑車、電動車及部分高端車中少量應(yīng)用鋁合金(2%~10%),主要應(yīng)用在防撞梁、機(jī)蓋和翼子板三個部位。
車身多材料連接技術(shù)
四個白車身發(fā)展階段,每個階段都有與之相應(yīng)的多材料連接技術(shù),表4列舉了不同的白車身發(fā)展階段與之對應(yīng)的多材料連接技術(shù)與主要應(yīng)用部位。
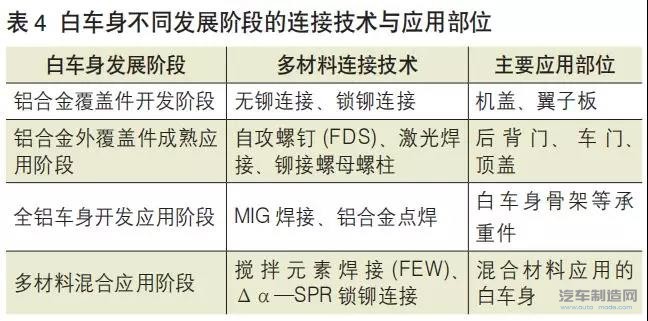
針對四個階段輕量化白車身的用材,圖5共歸納了目前最流行的9種白車身多材料連接技術(shù)。
根據(jù)奧迪車身發(fā)展的四個階段,所對應(yīng)的四個多材料連接技術(shù)發(fā)展階段如下:
第一階段應(yīng)用的連接技術(shù)主要是無鉚連接和鎖鉚連接(SPR)。無鉚連接適合于不同金屬材料及不同厚度連接,過程簡單,一步完成且不需要預(yù)先打孔,能耗低,但連接強(qiáng)度略低。鎖鉚連接(SPR)具有很高的動態(tài)疲勞強(qiáng)度(約為焊點(diǎn)的2倍),碰撞吸收的能量較焊點(diǎn)高,鉚接材料組合廣泛,不過鉚釘增加了車身自重。
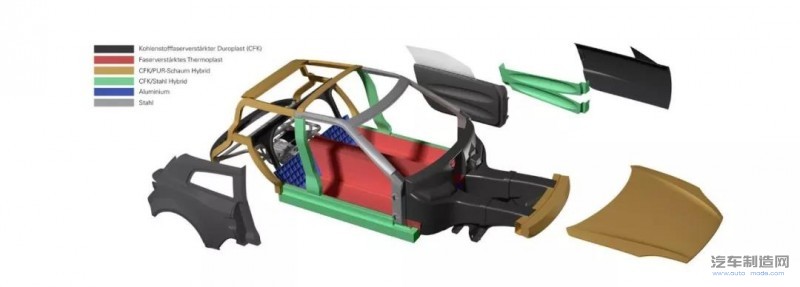
第二階段應(yīng)用的連接技術(shù)主要是自攻螺絲(FDS)、激光焊接和鉚接螺母螺柱。自攻螺絲(FDS)機(jī)械強(qiáng)度高,動態(tài)連接強(qiáng)度高,單面連接,可與折邊膠結(jié)合使用,拆卸更換螺絲方便;劣勢是防腐蝕能力降低,增加了車身自重,可能會產(chǎn)生金屬飛屑誤傷工人。激光焊接速度快,焊點(diǎn)排布方式更靈活,焊點(diǎn)寬深比大,變形??;缺點(diǎn)是異種材料不可直接焊接,需焊部位務(wù)必非常精確,需在激光束的聚焦范圍內(nèi)。鉚接螺母螺柱可集成在沖壓模具中,減少工序,靜態(tài)和動態(tài)載荷高,對涂層無損傷,適用板材范圍廣,鉚點(diǎn)可以防液、防氣,防止腐蝕,成品也容易檢驗(yàn);劣勢是一次性投資大,連接高強(qiáng)度鋼板時需預(yù)先開孔,工藝繁瑣。
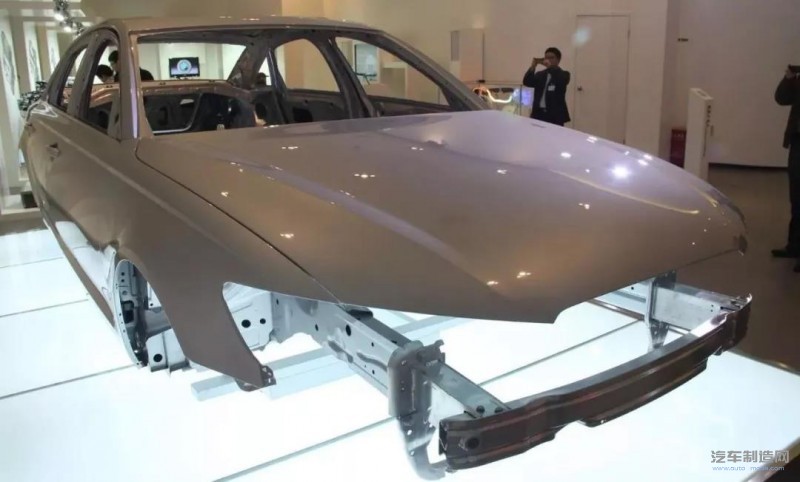
第三階段應(yīng)用的連接技術(shù)主要是MIG焊和鋁合金點(diǎn)焊。MIG焊主要應(yīng)用在A柱、B柱、頂蓋橫梁、消聲器和減振塔等部位,優(yōu)點(diǎn)是擁有更優(yōu)的保護(hù)氣氛、焊絲無焊渣,可焊接鋁合金,但成本較高,操作難度大,細(xì)微缺陷都會造成嚴(yán)重的不良率。鋁合金點(diǎn)焊主要應(yīng)用于白車身及外覆蓋件,優(yōu)勢是生產(chǎn)一致性高,表面質(zhì)量高,變形小;缺點(diǎn)是需對原有鋼產(chǎn)線進(jìn)行大幅度改造,設(shè)備投入高,因此目前主機(jī)廠應(yīng)用少,借鑒點(diǎn)少。
第四階段應(yīng)用的連接技術(shù)主要有摩擦塞鉚焊(Friction Elment Welding FEW)和Δα—SPR鎖鉚連接。摩擦塞鉚焊可以解決鋁合金與高強(qiáng)鋼、熱成形鋼之間的連接,且不需預(yù)先開孔,可以和膠混合使用,缺點(diǎn)是需要額外的緊固件,增加了自重,另外頭部凸起2.5?mm需預(yù)防干涉,潮濕環(huán)境還需要在頭部一側(cè)增加PVC密封膠。Δα—SPR鎖鉚連接解決了碳纖維和鋁合金膨脹系數(shù)不同在涂裝過程中導(dǎo)致的鉚點(diǎn)損壞問題,不過僅適用于膨脹率相差較大的材料連接。
結(jié)論
輕量化白車身方面,以奧迪為代表的白車身的發(fā)展與用材可歸納為四個階段:鋁合金覆蓋件開發(fā)階段、鋁合金外覆蓋件成熟應(yīng)用階段、全鋁車身開發(fā)應(yīng)用階段和多材料混合應(yīng)用階段,總體趨勢為鋁合金應(yīng)用量上升,軟鋼及熱成形鋼的應(yīng)用量相應(yīng)下降,材料應(yīng)用趨于多樣化,白車身重量逐步下降。國外白車身技術(shù)發(fā)展的進(jìn)程中,德系車身用材較為激進(jìn),美系車身用材略顯中庸,日系車型用材較為滯后。
車身多材料連接技術(shù)方面,針對輕量化白車身的四個發(fā)展階段,多材料連接技術(shù)可對應(yīng)規(guī)劃為四個應(yīng)用階段,以適應(yīng)不同階段輕量化白車身的研發(fā)與生產(chǎn);根據(jù)不同主機(jī)廠其白車身的用材發(fā)展現(xiàn)狀,可對應(yīng)規(guī)劃并投入其對應(yīng)階段的多材料連接技術(shù)。多材料連接技術(shù)的應(yīng)用階段越高,其工藝應(yīng)用越不成熟,尚需探索和改進(jìn)。
汽車輕量化是節(jié)能減排的一個有效途徑,而汽車輕量化最有效的手段就是輕質(zhì)合金材料的應(yīng)用,目前國外已開發(fā)出多種多材料應(yīng)用的輕量化白車身,但其連接問題成為瓶頸,目前通用的點(diǎn)焊連接技術(shù)已無法滿足要求,各種新晉的連接技術(shù)層出不窮。
隨著國外輕量化白車身的發(fā)展,白車身的用材由鋼板應(yīng)用階段逐步發(fā)展到多材料混合應(yīng)用階段。本文以奧迪品牌的白車身發(fā)展進(jìn)程為例,歸納了其白車身用材演化的四個階段,分析了典型歐系、美系和日系車型白車身用材發(fā)展現(xiàn)狀及用材趨勢。
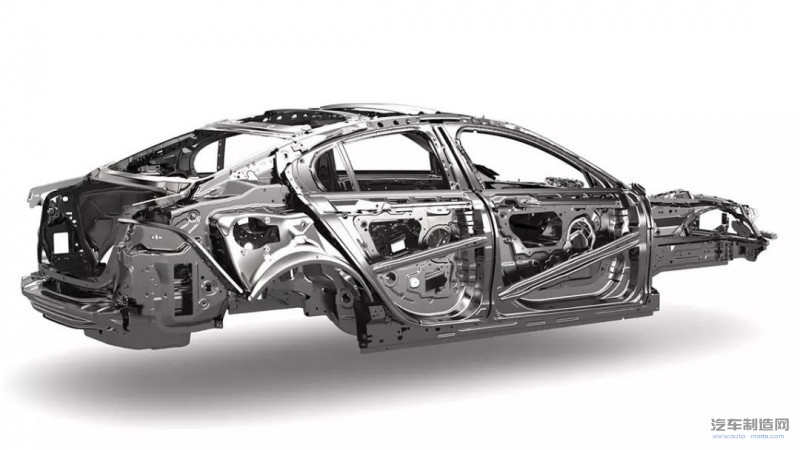
伴隨著輕量化白車身的發(fā)展,其相應(yīng)的多材料連接技術(shù)也隨之發(fā)展迅速。針對四個白車身發(fā)展階段,列舉了目前9種常用的多材料連接技術(shù),也對應(yīng)規(guī)劃為4個不同階段,分析了每個階段進(jìn)程的多材料連接技術(shù)的適用范圍與優(yōu)劣勢。
國外輕量化車身發(fā)展過程
縱觀國外白車身的發(fā)展趨勢,奧迪公司的白車身發(fā)展趨勢極具代表性,到目前為止,其白車身的發(fā)展過程可分為四個階段:
第一階段:鋁合金覆蓋件開發(fā)階段
這個階段主要是為了增加材料強(qiáng)度級別,熱成形鋼逐步用于車身,還有少量鋁合金覆蓋件的應(yīng)用。典型的車型代表為奧迪A3車型(見圖1)。
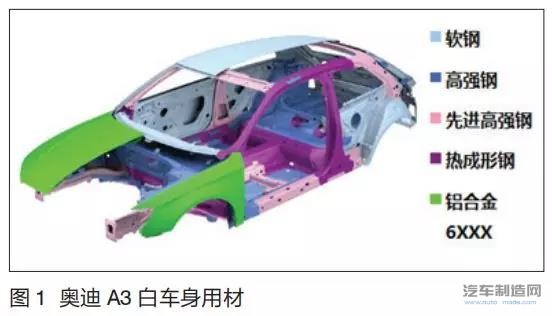
零部件用材方面,機(jī)蓋、翼子板使用鋁合金材質(zhì)(3.2%),后座椅橫梁、中通道、A柱、B柱、機(jī)艙縱梁后段、前圍下板、后地板橫梁和后地板縱梁等位置采用熱成形鋼(21.7%)。
第二階段:鋁合金外覆蓋件成熟應(yīng)用階段
這一階段,外覆蓋件大量采用鋁合金,鋁合金覆蓋件比重顯著增加,熱成形鋼比重相對減少,典型的車型代表是奧迪A6車型(見圖2)。
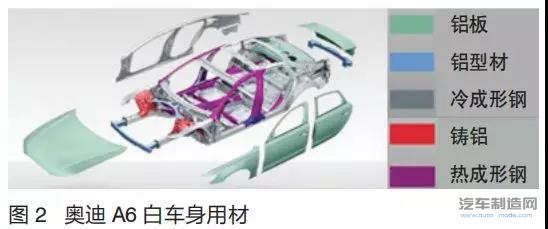
零部件用材方面,機(jī)蓋、前后車門、翼子板、行李箱蓋板、頂蓋和前后防撞梁(鋁型材)應(yīng)用鋁合金。鋁合金用量較第一階段增加至18%,中通道、座椅橫梁、A柱和B柱等位置保留熱成形鋼,熱成形鋼的用量比例減少至11.3%。
第三階段:全鋁車身開發(fā)應(yīng)用階段
這個階段,車身外覆蓋件全部應(yīng)用鋁合金(鋁板材)、鋁型材和鑄鋁開始應(yīng)用到車身結(jié)構(gòu)件,輕量化效果顯著,與此同時,高強(qiáng)鋼和軟鋼板的用量急劇減少,典型的車型代表是奧迪TT車型(見圖3)。
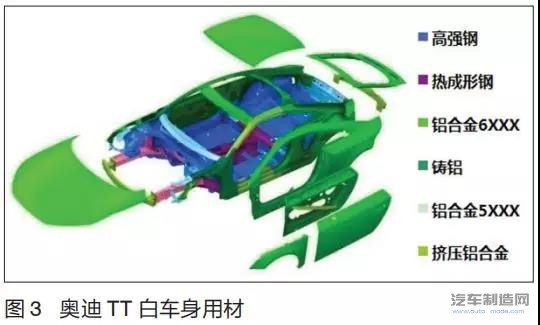
零部件用材方面,增加了A柱、C柱、側(cè)圍和頂蓋橫梁等位置的鋁合金,鋁合金用量由18%增加到35.8%,中通道、座椅橫梁采用熱成形鋼,軟鋼應(yīng)用量由35.2%下降到5.3%。
第四階段:多材料混合應(yīng)用階段
這一階段以鋁合金為主要車身材料,鋁型材和鑄鋁件大量應(yīng)用到車身結(jié)構(gòu)件。高強(qiáng)鋼、軟鋼和碳纖維為輔助用材,典型的車型代表是奧迪Q7車型(見圖4)。

零部件用材方面,地板、前縱梁等位置應(yīng)用鋁合金,鋁合金用量較上一階段由35.8%增加到49.9%,中通道采用的是鋁板和熱成形鋼的混合結(jié)構(gòu),熱成形鋼的用量減少至9.2%。
車身用材比較及發(fā)展趨勢
以上四款車型的白車身用材比例如表1所示。
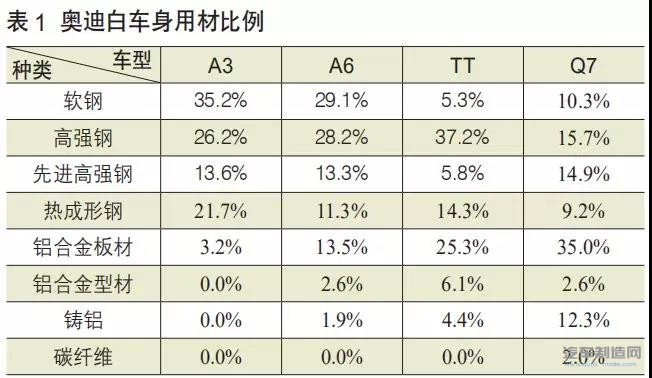
分析奧迪用材趨勢如下:
鋁合金用量上升趨勢明顯(3.2%→18.0%→35.8%→49.9%);
熱成形鋼整體用量呈下降趨勢(21.7%→11.3%→14.3%→9.2%);
軟鋼用量下降趨勢明顯(35.2%→29.1%→5.3%→10.3%)。
除歐系的奧迪車型外,美系福特和日系車的用材比例如表2、表3所示。
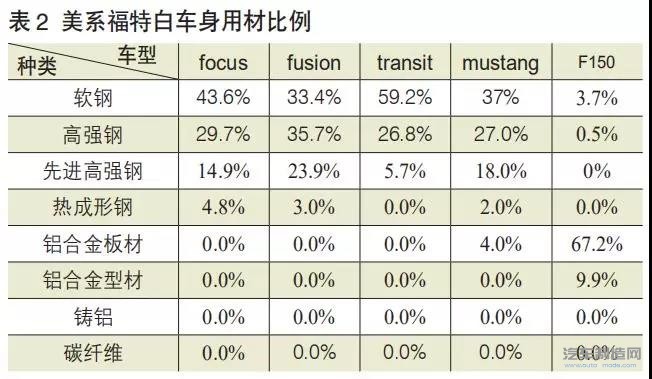
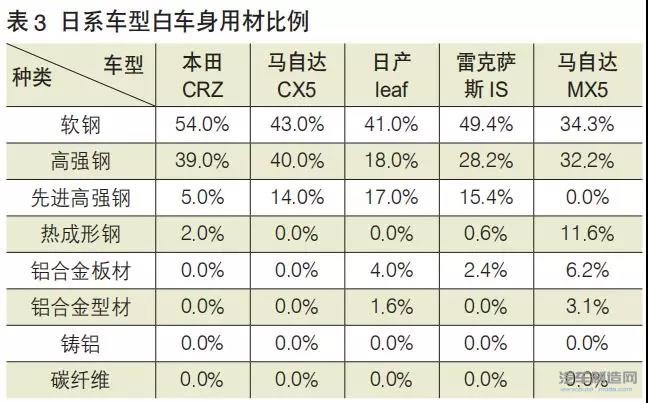
表2中,福特focus、福特fusion、福特transit和福特mustang處于奧迪輕量化白車身第一階段用材水平,且只有福特mustang的機(jī)蓋、翼子板應(yīng)用鋁合金(4%),福特F150處于奧迪輕量化白車身第三階段用材水平,車身結(jié)構(gòu)件和覆蓋件大量應(yīng)用鋁合金。
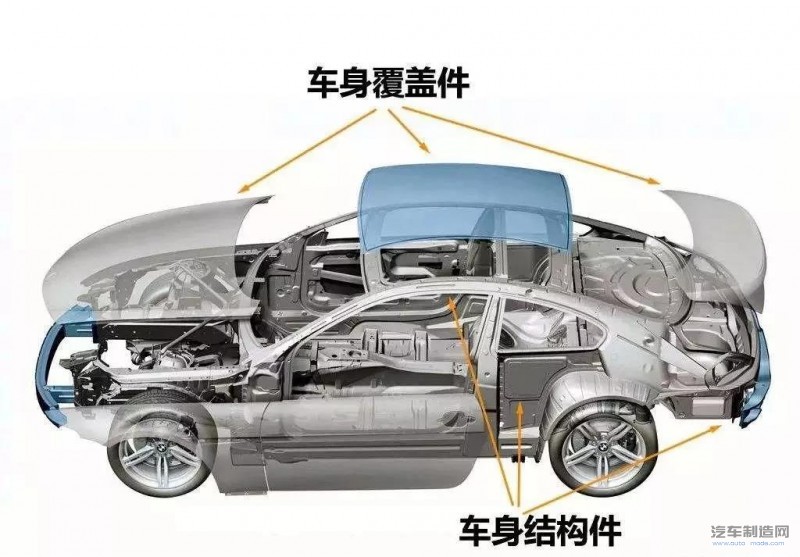
表3中的5款日系車型均處于奧迪輕量化白車身第一階段用材水平。在日系車型中,只有對輕量化要求較高的跑車、電動車及部分高端車中少量應(yīng)用鋁合金(2%~10%),主要應(yīng)用在防撞梁、機(jī)蓋和翼子板三個部位。
車身多材料連接技術(shù)
四個白車身發(fā)展階段,每個階段都有與之相應(yīng)的多材料連接技術(shù),表4列舉了不同的白車身發(fā)展階段與之對應(yīng)的多材料連接技術(shù)與主要應(yīng)用部位。
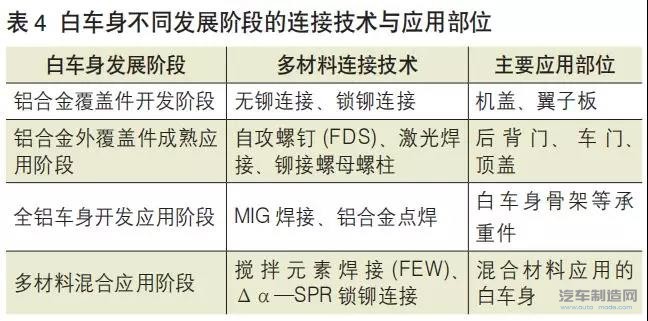
針對四個階段輕量化白車身的用材,圖5共歸納了目前最流行的9種白車身多材料連接技術(shù)。
根據(jù)奧迪車身發(fā)展的四個階段,所對應(yīng)的四個多材料連接技術(shù)發(fā)展階段如下:
第一階段應(yīng)用的連接技術(shù)主要是無鉚連接和鎖鉚連接(SPR)。無鉚連接適合于不同金屬材料及不同厚度連接,過程簡單,一步完成且不需要預(yù)先打孔,能耗低,但連接強(qiáng)度略低。鎖鉚連接(SPR)具有很高的動態(tài)疲勞強(qiáng)度(約為焊點(diǎn)的2倍),碰撞吸收的能量較焊點(diǎn)高,鉚接材料組合廣泛,不過鉚釘增加了車身自重。
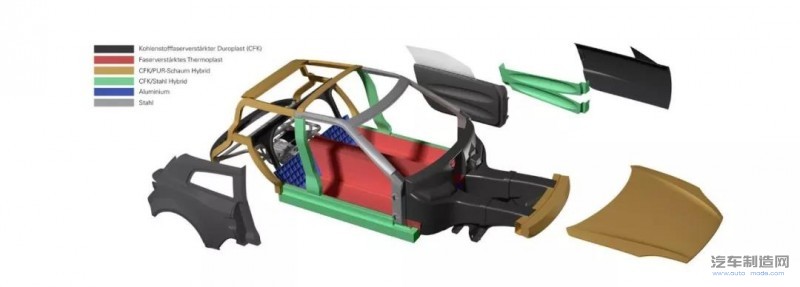
第二階段應(yīng)用的連接技術(shù)主要是自攻螺絲(FDS)、激光焊接和鉚接螺母螺柱。自攻螺絲(FDS)機(jī)械強(qiáng)度高,動態(tài)連接強(qiáng)度高,單面連接,可與折邊膠結(jié)合使用,拆卸更換螺絲方便;劣勢是防腐蝕能力降低,增加了車身自重,可能會產(chǎn)生金屬飛屑誤傷工人。激光焊接速度快,焊點(diǎn)排布方式更靈活,焊點(diǎn)寬深比大,變形??;缺點(diǎn)是異種材料不可直接焊接,需焊部位務(wù)必非常精確,需在激光束的聚焦范圍內(nèi)。鉚接螺母螺柱可集成在沖壓模具中,減少工序,靜態(tài)和動態(tài)載荷高,對涂層無損傷,適用板材范圍廣,鉚點(diǎn)可以防液、防氣,防止腐蝕,成品也容易檢驗(yàn);劣勢是一次性投資大,連接高強(qiáng)度鋼板時需預(yù)先開孔,工藝繁瑣。
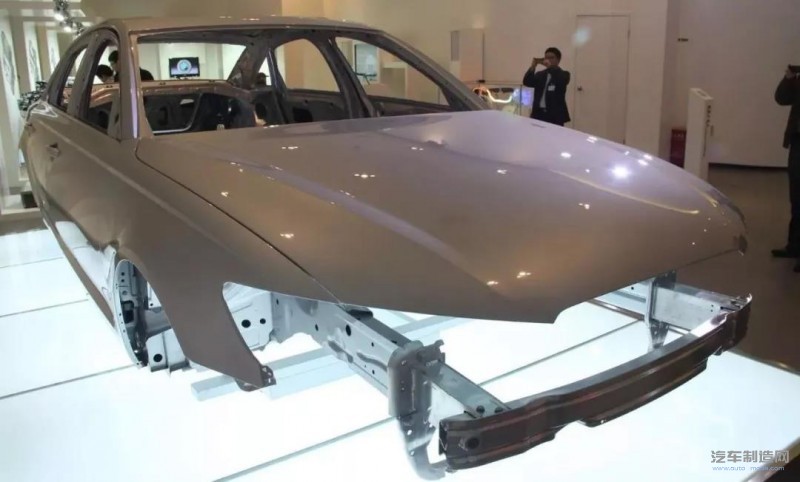
第三階段應(yīng)用的連接技術(shù)主要是MIG焊和鋁合金點(diǎn)焊。MIG焊主要應(yīng)用在A柱、B柱、頂蓋橫梁、消聲器和減振塔等部位,優(yōu)點(diǎn)是擁有更優(yōu)的保護(hù)氣氛、焊絲無焊渣,可焊接鋁合金,但成本較高,操作難度大,細(xì)微缺陷都會造成嚴(yán)重的不良率。鋁合金點(diǎn)焊主要應(yīng)用于白車身及外覆蓋件,優(yōu)勢是生產(chǎn)一致性高,表面質(zhì)量高,變形小;缺點(diǎn)是需對原有鋼產(chǎn)線進(jìn)行大幅度改造,設(shè)備投入高,因此目前主機(jī)廠應(yīng)用少,借鑒點(diǎn)少。
第四階段應(yīng)用的連接技術(shù)主要有摩擦塞鉚焊(Friction Elment Welding FEW)和Δα—SPR鎖鉚連接。摩擦塞鉚焊可以解決鋁合金與高強(qiáng)鋼、熱成形鋼之間的連接,且不需預(yù)先開孔,可以和膠混合使用,缺點(diǎn)是需要額外的緊固件,增加了自重,另外頭部凸起2.5?mm需預(yù)防干涉,潮濕環(huán)境還需要在頭部一側(cè)增加PVC密封膠。Δα—SPR鎖鉚連接解決了碳纖維和鋁合金膨脹系數(shù)不同在涂裝過程中導(dǎo)致的鉚點(diǎn)損壞問題,不過僅適用于膨脹率相差較大的材料連接。
結(jié)論
輕量化白車身方面,以奧迪為代表的白車身的發(fā)展與用材可歸納為四個階段:鋁合金覆蓋件開發(fā)階段、鋁合金外覆蓋件成熟應(yīng)用階段、全鋁車身開發(fā)應(yīng)用階段和多材料混合應(yīng)用階段,總體趨勢為鋁合金應(yīng)用量上升,軟鋼及熱成形鋼的應(yīng)用量相應(yīng)下降,材料應(yīng)用趨于多樣化,白車身重量逐步下降。國外白車身技術(shù)發(fā)展的進(jìn)程中,德系車身用材較為激進(jìn),美系車身用材略顯中庸,日系車型用材較為滯后。
車身多材料連接技術(shù)方面,針對輕量化白車身的四個發(fā)展階段,多材料連接技術(shù)可對應(yīng)規(guī)劃為四個應(yīng)用階段,以適應(yīng)不同階段輕量化白車身的研發(fā)與生產(chǎn);根據(jù)不同主機(jī)廠其白車身的用材發(fā)展現(xiàn)狀,可對應(yīng)規(guī)劃并投入其對應(yīng)階段的多材料連接技術(shù)。多材料連接技術(shù)的應(yīng)用階段越高,其工藝應(yīng)用越不成熟,尚需探索和改進(jìn)。
編輯推薦
最新資訊
-
跨越速運(yùn)憑什么“圈粉”萬千客戶?“
2025-07-01 14:42
-
數(shù)智破局啟新篇?生態(tài)共生再啟程 —
2025-06-27 20:13
-
助力汽車零部件產(chǎn)線智能化升級,西門
2025-06-27 13:59
-
BBA集體轉(zhuǎn)向!放棄全面電動化
2025-06-26 17:32
-
比換柜省錢,比自研省心,西門子Xcel
2025-06-25 15:07