超細(xì)長(zhǎng)鈦合金梁的數(shù)控加工工藝
2018-01-05 14:03:34· 來源:工具技術(shù)
圖1為超細(xì)長(zhǎng)鈦合金梁類零件。其毛料為模鍛件,材料牌號(hào)TA15M,毛料外廓尺寸3500mm×210mm×180mm,毛料重量220.5kg。零件外廓尺寸3450mm×160mm×151mm,最寬處為151mm,最窄處僅為34mm。零件外形為復(fù)雜雙曲面,雙面槽腔,緣條與腹板厚度最小處僅為2mm。尺寸精度及表面質(zhì)量要求較高。
圖1為超細(xì)長(zhǎng)鈦合金梁類零件。其毛料為模鍛件,材料牌號(hào)TA15M,毛料外廓尺寸3500mm×210mm×180mm,毛料重量220.5kg。零件外廓尺寸3450mm×160mm×151mm,最寬處為151mm,最窄處僅為34mm。零件外形為復(fù)雜雙曲面,雙面槽腔,緣條與腹板厚度最小處僅為2mm。尺寸精度及表面質(zhì)量要求較高。
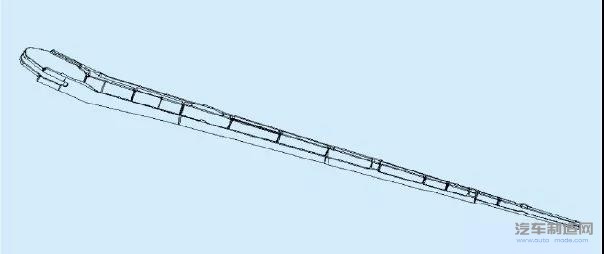
圖1 零件模型
1 確定工藝方案
零件毛料為TA15M自由鍛件,鍛件殘余應(yīng)力導(dǎo)致了機(jī)加過程中零件的變形。零件超長(zhǎng)且窄,長(zhǎng)寬比范圍22.8-101.5。零件結(jié)構(gòu)面多為變角度曲面,所有緣條都為斜面,裝夾定位不可靠。緣條和腹板厚度薄,最小處2mm,公差±0.2mm。緣條較高,角度大,最高處96mm。零件的裝配關(guān)系復(fù)雜,在該梁每一個(gè)位置都有零件與之裝配。表面質(zhì)量要求高,所有轉(zhuǎn)角及底角粗糙度1.6μm。該零件結(jié)構(gòu)屬于工藝性極差的結(jié)構(gòu)類型。在加工中要解決的問題包括:機(jī)加過程中變形的控制、裝夾定位方式的選擇和縮短加工周期。
(1)零件定位方式
超細(xì)長(zhǎng)鈦合金梁在加工過程中,定位方式的選擇至關(guān)重要。該梁長(zhǎng)又細(xì),且為兩面槽結(jié)構(gòu),因此采用緣條定位。由于該零件采用斜緣條直接定位會(huì)大幅降低定位面的精度,對(duì)零件加工質(zhì)量影響很大,所以在緣條上設(shè)置工藝凸臺(tái)來進(jìn)行定位,既可以保證定位基準(zhǔn)精度,又可以避免在加工過程中頻繁的倒壓板工作。工藝凸臺(tái)的距離應(yīng)適當(dāng),如果太近會(huì)增加加工過程中的跳刀頻率,加大工藝凸臺(tái)的去除難度;工藝凸臺(tái)太遠(yuǎn)會(huì)使定位不穩(wěn)定,增加零件在機(jī)加過程中的變形幾率,降低定位準(zhǔn)確度。根據(jù)該梁的結(jié)構(gòu)特點(diǎn),采用階梯工藝凸臺(tái),再在梁身上鉆兩工藝孔聯(lián)合定位,孔徑分別為25H9、12H9,定位穩(wěn)定可靠。工藝凸臺(tái)外形如圖2所示。
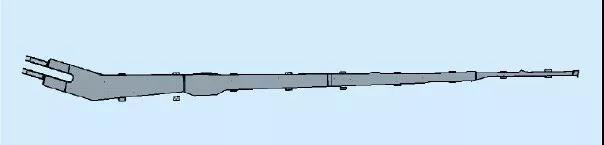
圖2 工藝凸臺(tái)外形
(2)機(jī)床設(shè)備及工裝的選擇
超細(xì)長(zhǎng)鈦合金梁長(zhǎng)約3.5m,零件頭部抬起,并且工裝龐大,零件加上工裝的高度已超過500mm,所以所用機(jī)床的Z向行程必須為700mm左右。通過對(duì)現(xiàn)場(chǎng)機(jī)床進(jìn)行考察,選用機(jī)床工作臺(tái)尺寸3500mm×1250mm,擺角范圍A±30°、B±30°,機(jī)床精度較高,能滿足零件加工要求。
超細(xì)長(zhǎng)鈦合金梁加工采用緣條高工藝凸臺(tái)及梁身基準(zhǔn)孔定位方式。頭部采用輔助可調(diào)支撐,用于頭部變形量的校正以及加工中變形量的去除;壓板選用Z字形壓板,可以有效降低刀具長(zhǎng)度,避免機(jī)床與工裝的干涉,并且提高加工效率,保證零件加工后的表面粗糙度;工裝增加校驗(yàn)塊的使用,用于加工中程序的驗(yàn)證,以及避免工人由于用錯(cuò)刀具造成的零件超差及廢品,提高了產(chǎn)品加工的一次就成功概率。正反面加工各需一套工裝。
超細(xì)長(zhǎng)鈦合金梁緣條兩側(cè)的導(dǎo)孔接近300個(gè),如采用傳統(tǒng)方法,常規(guī)加工難度非常大,費(fèi)時(shí)費(fèi)力,產(chǎn)品質(zhì)量也不易保證。使用數(shù)控機(jī)床鉆導(dǎo)孔,既省時(shí)省力,又能保證產(chǎn)品質(zhì)量。采用數(shù)控鉆導(dǎo)孔需工裝要求較高。緣條兩側(cè)各一套。
(3)確定加工流程
加工流程的合理安排是零件生產(chǎn)研制的重要環(huán)節(jié),加工流程的合理與否是導(dǎo)致零件加工變形的重要原因。加工流程的順序直接決定零件的去量方式、去量大小和去量先后順序,這些都會(huì)影響零件材料的應(yīng)力釋放,以及零件的變形大小、變形方式。合理的加工流程可以大幅降低零件的變形幾率。加工流程不僅要考慮零件的變形因素,還要保證零件尺寸精度。
根據(jù)超細(xì)長(zhǎng)鈦合金梁的零件特點(diǎn),制定零件的加工流程:模鍛件來料—銑基準(zhǔn)面—鏜基準(zhǔn)孔—粗銑航后面(留7mm余量)—粗銑航前面(留7mm余量)—粗銑航前面(留3mm余量)—粗銑航后面(留3mm余量)—粗銑槽一側(cè)(留3mm余量)—粗銑槽另一側(cè)(留3mm余量)—測(cè)量外形及槽口—半精銑外形(留1mm余量)—半精銑航前面(留1mm余量)—半精銑航后面(留1mm余量)—測(cè)量外形及交點(diǎn)孔—精銑槽口—精銑外形—測(cè)量外形及槽口—精銑航前內(nèi)形—精銑航后內(nèi)形—測(cè)量孔位等—數(shù)控鉆緣條導(dǎo)孔—銑工藝凸臺(tái)—鉗工鉆筋條導(dǎo)孔—半檢—清洗—熒光檢驗(yàn)—吹砂—標(biāo)識(shí)—成檢—交付。通過多次不斷的翻面加工以及去量的逐漸遞減,有效消除零件變形,保證產(chǎn)品質(zhì)量。
(4)刀具的選擇及參數(shù)的確定
數(shù)控加工機(jī)床采用冷卻液冷卻,結(jié)合零件的鈦合金材料,應(yīng)以淺切刀具和整體合金直柄立銑刀為主,國產(chǎn)鑲齒合金刀具為輔。由于鈦合金屬于難加工材料,對(duì)刀具的質(zhì)量和性能要求都很高。
依據(jù)現(xiàn)有參數(shù)庫及零件的實(shí)際加工情況來確定刀具加工參數(shù)。在切削中主要的切削參數(shù)有:主軸轉(zhuǎn)速n、切削深度ap、切削寬度ae、每齒進(jìn)給量fz、刀具齒數(shù)Z和進(jìn)給速度vf,其中vf=nZfz。
鈦合金加工刀具的齒數(shù)一般是多齒刀具,在加工該零件選用的刀具絕大多數(shù)都是4齒刀具。影響刀具加工效率的主要參數(shù)是主軸轉(zhuǎn)數(shù)(n)和刀具每齒進(jìn)給量(fz)。表1為參與加工的主要刀具的規(guī)格及加工參數(shù)。
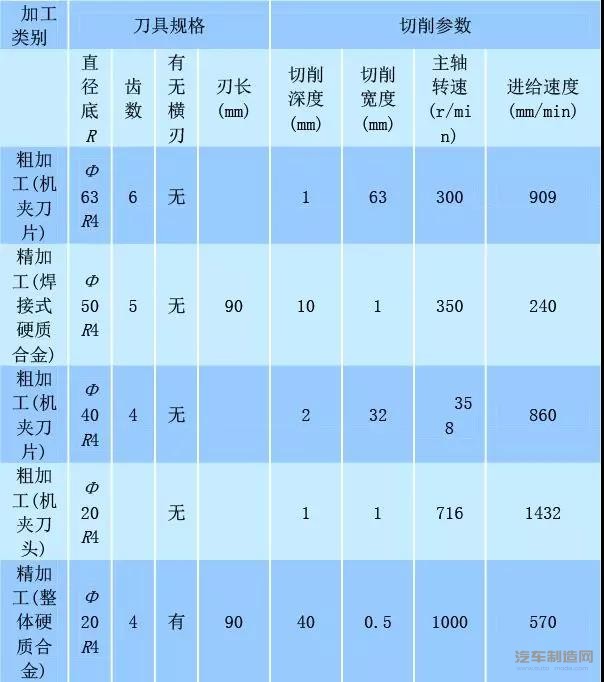
表1 加工刀具選擇及切削參數(shù)數(shù)值
2 數(shù)控程序的編制
根據(jù)零件的變形控制、來料狀態(tài)、零件結(jié)構(gòu)特點(diǎn)、機(jī)床特性、刀具特點(diǎn)等,編制數(shù)控加工程序。在編制程序時(shí)需有效避免一些常見的問題:①避免刀具路徑冗余,減少不必要的跳刀;②盡量采取順銑的走刀方式,保證零件尺寸精度;③針對(duì)不同的余量,采取徑向以及軸向的分層加工,保證刀具切削余量均勻,降低機(jī)床及刀具的損耗;④避免刀具垂直與零件接觸;⑤在轉(zhuǎn)角要降低加工速度,普通轉(zhuǎn)角降速值是正常切削的60%,特殊轉(zhuǎn)角(例如工藝凸臺(tái)內(nèi)側(cè)筋條轉(zhuǎn)角)降速要達(dá)到20%。保證無人工干預(yù)的正常切削;⑥精加工前清轉(zhuǎn)角,保證精銑的銑切量均勻;⑦正確計(jì)算R退縮值。
程序的走刀方式也可以影響零件的變形,比如淺切、順銑等都可以大幅降低零件的變形量。淺切加工不僅可以大幅提高金屬去除率,更重要的是可以降低切削力、減少加工應(yīng)力,有利于減小零件加工中的變形,同時(shí)還可以降低機(jī)床負(fù)荷、保護(hù)數(shù)控機(jī)床。淺切使用的專用的加工刀具,該類型刀具加工效率較高,以D20R4刀具為例,進(jìn)給速度可達(dá)1432mm/min,相比普通的刀具粗銑進(jìn)給速度60mm/min,效率可以高出幾倍甚至十幾倍。淺切加工特別適合超細(xì)長(zhǎng)鈦合金梁的粗加工。
選用“roughing”命令編制淺切程序,在半精加工和精加工過程中采用徑向分層的方式,每層進(jìn)量0.5,在保證零件精度的前提下,可以大幅降低切削應(yīng)力,減小零件的變形量。
小結(jié)
制定一套合理的工藝方案適用于超細(xì)長(zhǎng)鈦合金梁類零件,通過應(yīng)力釋放、優(yōu)化切削方式與合理刀具參數(shù)等方法有效控制了零件變形,采用工藝凸臺(tái)定位的方式也起到了很好的定位效果。該方案已通過加工驗(yàn)證,在實(shí)際加工中取得了非常好的效果,最終生產(chǎn)出了合格的零件,加工過程穩(wěn)定,產(chǎn)品質(zhì)量合格。
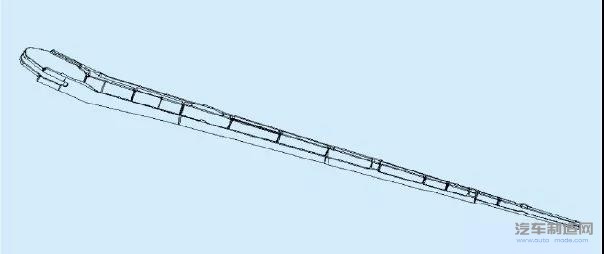
圖1 零件模型
1 確定工藝方案
零件毛料為TA15M自由鍛件,鍛件殘余應(yīng)力導(dǎo)致了機(jī)加過程中零件的變形。零件超長(zhǎng)且窄,長(zhǎng)寬比范圍22.8-101.5。零件結(jié)構(gòu)面多為變角度曲面,所有緣條都為斜面,裝夾定位不可靠。緣條和腹板厚度薄,最小處2mm,公差±0.2mm。緣條較高,角度大,最高處96mm。零件的裝配關(guān)系復(fù)雜,在該梁每一個(gè)位置都有零件與之裝配。表面質(zhì)量要求高,所有轉(zhuǎn)角及底角粗糙度1.6μm。該零件結(jié)構(gòu)屬于工藝性極差的結(jié)構(gòu)類型。在加工中要解決的問題包括:機(jī)加過程中變形的控制、裝夾定位方式的選擇和縮短加工周期。
(1)零件定位方式
超細(xì)長(zhǎng)鈦合金梁在加工過程中,定位方式的選擇至關(guān)重要。該梁長(zhǎng)又細(xì),且為兩面槽結(jié)構(gòu),因此采用緣條定位。由于該零件采用斜緣條直接定位會(huì)大幅降低定位面的精度,對(duì)零件加工質(zhì)量影響很大,所以在緣條上設(shè)置工藝凸臺(tái)來進(jìn)行定位,既可以保證定位基準(zhǔn)精度,又可以避免在加工過程中頻繁的倒壓板工作。工藝凸臺(tái)的距離應(yīng)適當(dāng),如果太近會(huì)增加加工過程中的跳刀頻率,加大工藝凸臺(tái)的去除難度;工藝凸臺(tái)太遠(yuǎn)會(huì)使定位不穩(wěn)定,增加零件在機(jī)加過程中的變形幾率,降低定位準(zhǔn)確度。根據(jù)該梁的結(jié)構(gòu)特點(diǎn),采用階梯工藝凸臺(tái),再在梁身上鉆兩工藝孔聯(lián)合定位,孔徑分別為25H9、12H9,定位穩(wěn)定可靠。工藝凸臺(tái)外形如圖2所示。
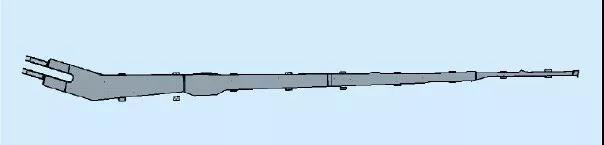
圖2 工藝凸臺(tái)外形
(2)機(jī)床設(shè)備及工裝的選擇
超細(xì)長(zhǎng)鈦合金梁長(zhǎng)約3.5m,零件頭部抬起,并且工裝龐大,零件加上工裝的高度已超過500mm,所以所用機(jī)床的Z向行程必須為700mm左右。通過對(duì)現(xiàn)場(chǎng)機(jī)床進(jìn)行考察,選用機(jī)床工作臺(tái)尺寸3500mm×1250mm,擺角范圍A±30°、B±30°,機(jī)床精度較高,能滿足零件加工要求。
超細(xì)長(zhǎng)鈦合金梁加工采用緣條高工藝凸臺(tái)及梁身基準(zhǔn)孔定位方式。頭部采用輔助可調(diào)支撐,用于頭部變形量的校正以及加工中變形量的去除;壓板選用Z字形壓板,可以有效降低刀具長(zhǎng)度,避免機(jī)床與工裝的干涉,并且提高加工效率,保證零件加工后的表面粗糙度;工裝增加校驗(yàn)塊的使用,用于加工中程序的驗(yàn)證,以及避免工人由于用錯(cuò)刀具造成的零件超差及廢品,提高了產(chǎn)品加工的一次就成功概率。正反面加工各需一套工裝。
超細(xì)長(zhǎng)鈦合金梁緣條兩側(cè)的導(dǎo)孔接近300個(gè),如采用傳統(tǒng)方法,常規(guī)加工難度非常大,費(fèi)時(shí)費(fèi)力,產(chǎn)品質(zhì)量也不易保證。使用數(shù)控機(jī)床鉆導(dǎo)孔,既省時(shí)省力,又能保證產(chǎn)品質(zhì)量。采用數(shù)控鉆導(dǎo)孔需工裝要求較高。緣條兩側(cè)各一套。
(3)確定加工流程
加工流程的合理安排是零件生產(chǎn)研制的重要環(huán)節(jié),加工流程的合理與否是導(dǎo)致零件加工變形的重要原因。加工流程的順序直接決定零件的去量方式、去量大小和去量先后順序,這些都會(huì)影響零件材料的應(yīng)力釋放,以及零件的變形大小、變形方式。合理的加工流程可以大幅降低零件的變形幾率。加工流程不僅要考慮零件的變形因素,還要保證零件尺寸精度。
根據(jù)超細(xì)長(zhǎng)鈦合金梁的零件特點(diǎn),制定零件的加工流程:模鍛件來料—銑基準(zhǔn)面—鏜基準(zhǔn)孔—粗銑航后面(留7mm余量)—粗銑航前面(留7mm余量)—粗銑航前面(留3mm余量)—粗銑航后面(留3mm余量)—粗銑槽一側(cè)(留3mm余量)—粗銑槽另一側(cè)(留3mm余量)—測(cè)量外形及槽口—半精銑外形(留1mm余量)—半精銑航前面(留1mm余量)—半精銑航后面(留1mm余量)—測(cè)量外形及交點(diǎn)孔—精銑槽口—精銑外形—測(cè)量外形及槽口—精銑航前內(nèi)形—精銑航后內(nèi)形—測(cè)量孔位等—數(shù)控鉆緣條導(dǎo)孔—銑工藝凸臺(tái)—鉗工鉆筋條導(dǎo)孔—半檢—清洗—熒光檢驗(yàn)—吹砂—標(biāo)識(shí)—成檢—交付。通過多次不斷的翻面加工以及去量的逐漸遞減,有效消除零件變形,保證產(chǎn)品質(zhì)量。
(4)刀具的選擇及參數(shù)的確定
數(shù)控加工機(jī)床采用冷卻液冷卻,結(jié)合零件的鈦合金材料,應(yīng)以淺切刀具和整體合金直柄立銑刀為主,國產(chǎn)鑲齒合金刀具為輔。由于鈦合金屬于難加工材料,對(duì)刀具的質(zhì)量和性能要求都很高。
依據(jù)現(xiàn)有參數(shù)庫及零件的實(shí)際加工情況來確定刀具加工參數(shù)。在切削中主要的切削參數(shù)有:主軸轉(zhuǎn)速n、切削深度ap、切削寬度ae、每齒進(jìn)給量fz、刀具齒數(shù)Z和進(jìn)給速度vf,其中vf=nZfz。
鈦合金加工刀具的齒數(shù)一般是多齒刀具,在加工該零件選用的刀具絕大多數(shù)都是4齒刀具。影響刀具加工效率的主要參數(shù)是主軸轉(zhuǎn)數(shù)(n)和刀具每齒進(jìn)給量(fz)。表1為參與加工的主要刀具的規(guī)格及加工參數(shù)。
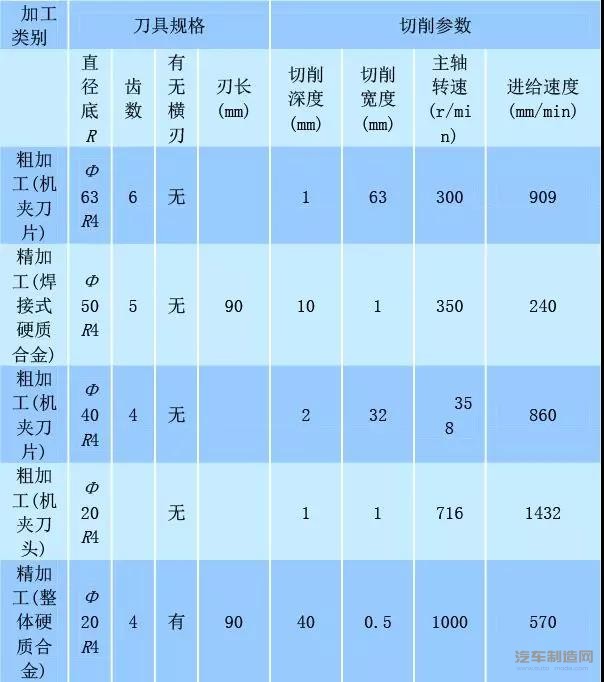
表1 加工刀具選擇及切削參數(shù)數(shù)值
2 數(shù)控程序的編制
根據(jù)零件的變形控制、來料狀態(tài)、零件結(jié)構(gòu)特點(diǎn)、機(jī)床特性、刀具特點(diǎn)等,編制數(shù)控加工程序。在編制程序時(shí)需有效避免一些常見的問題:①避免刀具路徑冗余,減少不必要的跳刀;②盡量采取順銑的走刀方式,保證零件尺寸精度;③針對(duì)不同的余量,采取徑向以及軸向的分層加工,保證刀具切削余量均勻,降低機(jī)床及刀具的損耗;④避免刀具垂直與零件接觸;⑤在轉(zhuǎn)角要降低加工速度,普通轉(zhuǎn)角降速值是正常切削的60%,特殊轉(zhuǎn)角(例如工藝凸臺(tái)內(nèi)側(cè)筋條轉(zhuǎn)角)降速要達(dá)到20%。保證無人工干預(yù)的正常切削;⑥精加工前清轉(zhuǎn)角,保證精銑的銑切量均勻;⑦正確計(jì)算R退縮值。
程序的走刀方式也可以影響零件的變形,比如淺切、順銑等都可以大幅降低零件的變形量。淺切加工不僅可以大幅提高金屬去除率,更重要的是可以降低切削力、減少加工應(yīng)力,有利于減小零件加工中的變形,同時(shí)還可以降低機(jī)床負(fù)荷、保護(hù)數(shù)控機(jī)床。淺切使用的專用的加工刀具,該類型刀具加工效率較高,以D20R4刀具為例,進(jìn)給速度可達(dá)1432mm/min,相比普通的刀具粗銑進(jìn)給速度60mm/min,效率可以高出幾倍甚至十幾倍。淺切加工特別適合超細(xì)長(zhǎng)鈦合金梁的粗加工。
選用“roughing”命令編制淺切程序,在半精加工和精加工過程中采用徑向分層的方式,每層進(jìn)量0.5,在保證零件精度的前提下,可以大幅降低切削應(yīng)力,減小零件的變形量。
小結(jié)
制定一套合理的工藝方案適用于超細(xì)長(zhǎng)鈦合金梁類零件,通過應(yīng)力釋放、優(yōu)化切削方式與合理刀具參數(shù)等方法有效控制了零件變形,采用工藝凸臺(tái)定位的方式也起到了很好的定位效果。該方案已通過加工驗(yàn)證,在實(shí)際加工中取得了非常好的效果,最終生產(chǎn)出了合格的零件,加工過程穩(wěn)定,產(chǎn)品質(zhì)量合格。
編輯推薦
最新資訊
-
跨越速運(yùn)憑什么“圈粉”萬千客戶?“
2025-07-01 14:42
-
數(shù)智破局啟新篇?生態(tài)共生再啟程 —
2025-06-27 20:13
-
助力汽車零部件產(chǎn)線智能化升級(jí),西門
2025-06-27 13:59
-
BBA集體轉(zhuǎn)向!放棄全面電動(dòng)化
2025-06-26 17:32
-
比換柜省錢,比自研省心,西門子Xcel
2025-06-25 15:07