簡單分析內(nèi)燃機氣門感應(yīng)熱處理技術(shù)與質(zhì)量控制
2018-01-04 17:10:36· 來源:金屬加工 作者:王忠誠
內(nèi)燃機氣門是汽車發(fā)動機內(nèi)提供動力的重要部件,尤其是排氣門在高溫、腐蝕性介質(zhì)、長期重復(fù)的沖擊,以及廢氣的沖刷作用下工作,因此既要具有良好的組織與強度,又要具有高的耐熱性和熱穩(wěn)定性,良好的耐蝕性、抗咬合性、耐磨性和導(dǎo)熱性等,其工作條件十分苛刻
內(nèi)燃機氣門是汽車發(fā)動機內(nèi)提供動力的重要部件,尤其是排氣門在高溫、腐蝕性介質(zhì)、長期重復(fù)的沖擊,以及廢氣的沖刷作用下工作,因此既要具有良好的組織與強度,又要具有高的耐熱性和熱穩(wěn)定性,良好的耐蝕性、抗咬合性、耐磨性和導(dǎo)熱性等,其工作條件十分苛刻。因為氣門的盤錐面與氣門座圈反復(fù)接觸,要求其有良好的耐磨性,而氣門桿端面與凸輪接觸,要求表面有高的硬度。因此,為滿足其錐面與桿端的耐磨性,需要對氣門進行錐面與桿端的淬回火處理,以獲得要求的高硬度。通常是在馬氏體耐熱鋼調(diào)質(zhì)處理后再進行感應(yīng)熱處理。
本文僅對氣門盤部錐面與桿部的感應(yīng)淬火技術(shù)進行簡單分析,并指出生產(chǎn)過程中出現(xiàn)的質(zhì)量問題,且提出改進措施,旨在提高氣門的感應(yīng)淬火質(zhì)量。
一、感應(yīng)熱處理在氣門上的應(yīng)用
1.感應(yīng)熱處理的特點
感應(yīng)熱處理是生產(chǎn)率高、不污染環(huán)境、易于自動化和節(jié)省能源的一種先進熱處理技術(shù)。這一技術(shù)自問世以來一直在迅速發(fā)展,感應(yīng)熱處理技術(shù)的最大用戶是汽車零部件領(lǐng)域。
感應(yīng)熱處理技術(shù)由于具有優(yōu)質(zhì)、高效、節(jié)能、環(huán)保等諸多優(yōu)點,符合現(xiàn)代汽車生產(chǎn)需要,技術(shù)水平迅速提升[4]。高頻感應(yīng)加熱設(shè)備在汽車零部件領(lǐng)域的應(yīng)用十分廣泛,如氣門、挺桿、連桿、曲軸、凸輪軸、齒輪、萬向節(jié)鐘形殼及半軸等,其中氣門桿端進行連續(xù)淬火或沖擊淬火,錐面進行自動連續(xù)作業(yè)成為國內(nèi)外氣門感應(yīng)熱處理最成功的技術(shù),獲得了氣門制造廠商的青睞,國內(nèi)100余家氣門制造廠商均擁有5臺以上的高頻設(shè)備。其中我公司有30余臺感應(yīng)淬火設(shè)備(或連續(xù)生產(chǎn)線),年產(chǎn)感應(yīng)淬火氣門2000萬支以上,成為中國氣門制造廠商中產(chǎn)量最大與出口數(shù)量最多的制造廠商之一。
2. 內(nèi)燃機氣門感應(yīng)淬火的基本要求
氣門熱處理(調(diào)質(zhì)處理)后進行感應(yīng)淬火,目的是滿足其桿端面(或錐面)耐磨的要求, 《內(nèi)燃機 進、排氣門 技術(shù)條件》(GB/T23337—2009)與《汽車發(fā)動機氣門技術(shù)條件》(QC/T469—2002)中,均指出桿端面經(jīng)過表面淬火后硬度應(yīng)≥48HRC,當(dāng)桿端部長度>4mm時,硬化層深度應(yīng)≥2mm)或淬硬層深度應(yīng)≥0.6mm。盤錐面經(jīng)過表面淬火后的硬化層應(yīng)≥1.5mm,其硬度值應(yīng)符合圖樣規(guī)定,桿端與錐面感應(yīng)淬火晶粒度細于8級??梢妼忾T的錐面與桿部進行感應(yīng)淬火是標(biāo)準所要求的,是提高氣門表面硬度的不可缺少的熱處理手段。
二、氣門感應(yīng)熱處理的技術(shù)要求、感應(yīng)器的形式與選用
1. 技術(shù)要求
氣門進行感應(yīng)淬火的技術(shù)要求包括表面(或端面)硬度、硬化層(淬火)深度或長度、金相組織、畸變量及外觀等。
(1)錐面淬火要求 氣門錐面(閥口)與氣門底座反復(fù)貼合,要求其表面具有高的硬度和良好的耐磨性,感應(yīng)淬火可滿足其要求。錐面淬火的錐面硬度在45~58HRC,硬化層深度一般≥1.5mm,晶粒度細于8級,某氣門錐面淬火技術(shù)要求如圖1所示(圖中A點位置:距盤端面1.7mm,距盤外圓3.3mm。要求在淬火深度測量時應(yīng)透過A點,淬火區(qū)及過渡區(qū)不得超過圖中粗實線)。
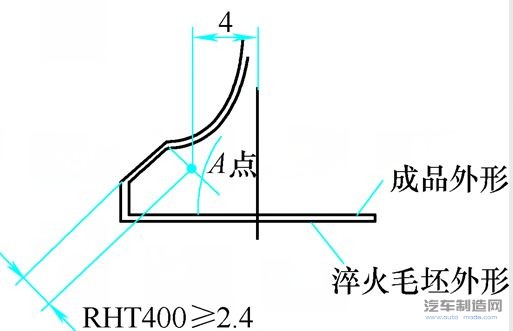
圖1 某氣門錐面工藝要求的淬火深度與硬度
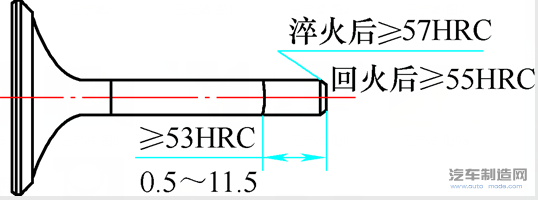
圖2氣門桿部淬透要求
(2)桿端淬火要求 對于氣門桿部的技術(shù)要求為淬火硬度50~60HRC,硬化層深度≥2mm,晶粒度細于8級等,其中工藝要求有桿部淬透、仿形淬火、桿端沖擊淬火等,圖2、圖3、圖4為某些氣門桿部淬透、桿部仿形和桿端沖擊淬火的技術(shù)要求。
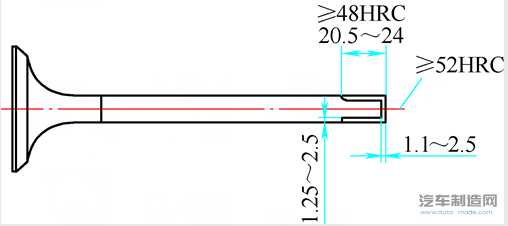
圖3氣門桿部仿形淬火要求
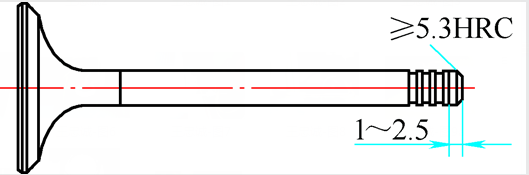
圖4 氣門桿端沖擊淬火要求
2. 感應(yīng)器的形式與選用
(1)錐面淬火感應(yīng)器 錐面淬火采用專用的感應(yīng)器,通常氣門使用的錐面淬火感應(yīng)器有兩種:連續(xù)式感應(yīng)器與單圈感應(yīng)器,其形狀是根據(jù)氣門盤錐面確定的,圖5、圖6為常見的感應(yīng)器形式。

圖5 多工位氣門錐面淬火感應(yīng)器實物形態(tài)
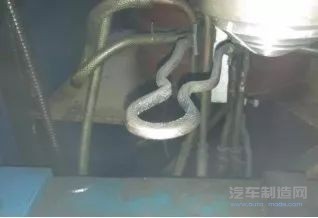
圖6單圈氣門錐面淬火感應(yīng)器
錐面淬火感應(yīng)器的選用原則:感應(yīng)器內(nèi)沿與氣門錐面之間留有間隙為1.5~3mm,氣門的盤部在加熱過程中是旋轉(zhuǎn)的,具體參數(shù)如電流、電壓、頻率、加熱溫度與加熱時間是通過工藝試驗來進行確定的,即滿足硬度與淬火深度合格,晶粒度要細于8級的要求,錐面淬火后的氣門通常進行160~200℃低溫回火或高溫回火處理,以穩(wěn)定組織,減小內(nèi)應(yīng)力與脆性。
(2)桿端淬火感應(yīng)器 氣門的桿端淬火采用特制的感應(yīng)器。這是考慮到其技術(shù)要求的差異而設(shè)計的,同時其工藝參數(shù)也有較大的不同,目的是滿足桿部的不同硬度與淬火長度的要求。圖7、圖8為沖擊與仿形淬火感應(yīng)器,圖9為桿端連續(xù)淬火與連續(xù)淬回火感應(yīng)器,該類感應(yīng)器應(yīng)用十分普遍,生產(chǎn)效率高。
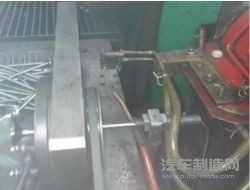
圖7氣門桿端沖擊/仿形淬火感應(yīng)器
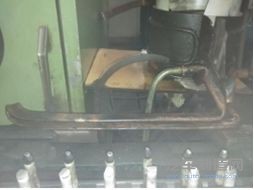
圖8 氣門桿部淬透連續(xù)淬火感應(yīng)器
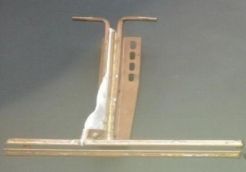
(a)回火感應(yīng)器
(b)淬火感應(yīng)器
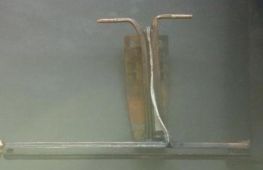
圖9 氣門桿部連續(xù)式淬火與回火感應(yīng)器
三、氣門感應(yīng)熱處理的質(zhì)量控制
1. 過程質(zhì)量控制
為滿足氣門感應(yīng)淬火后的質(zhì)量符合技術(shù)要求,氣門應(yīng)進行錐面和桿端感應(yīng)淬火的加熱與冷卻,選用感應(yīng)器、噴水器的結(jié)構(gòu)、形狀及尺寸應(yīng)滿足使用要求。根據(jù)工藝試驗結(jié)果確定最佳的工藝參數(shù)等,并按如下要求進行:
(1)要確定電壓、電流、加熱溫度、加熱時間或進給速度等。
(2)介質(zhì)溫度、壓力、流量、濃度的范圍及冷卻時間。
(3)感應(yīng)器外觀與冷卻噴淋結(jié)構(gòu)符合要求。
2. 質(zhì)量檢查方法
目前氣門桿部與錐面的硬度、長度或深度、晶粒度等檢查方法采用以下要求進行:
(1)對于要求采用洛氏/維式硬度檢查和淬火長度則采用在錐面或桿部外圓上檢查,圖10為檢查圖片。
(2)對于要求采用維氏硬度(平面)檢查的,則是在剖開錐面或桿部平面上,拋光后硬度與長度等按要求檢查如圖11所示。
(3)晶粒度的檢查按要求拋光腐蝕后進行。
(a)錐面硬度檢查 (b)桿端硬度檢查 (c)桿部淬火長度檢查
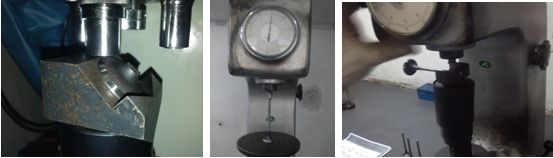
圖10 氣門硬度與淬火長度的硬度檢查法
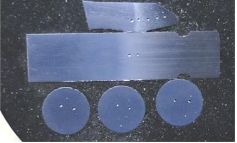
圖11 氣門錐面與桿端與淬火長度檢查(硬度法)
3. 缺陷形式與原因分析
氣門錐面與桿端淬火缺陷形式與原因分析具體見附表。
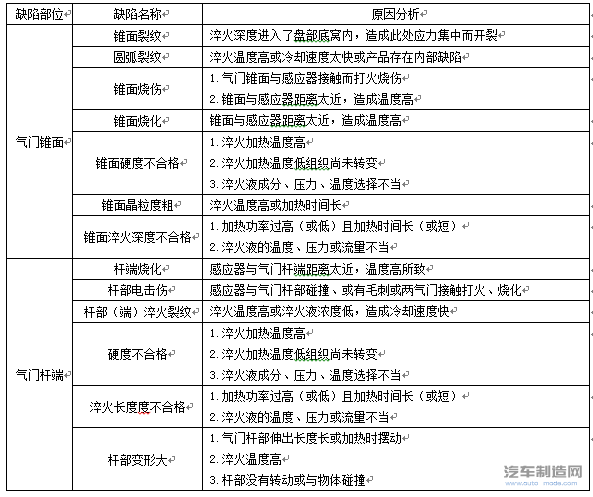
氣門感應(yīng)熱處理缺陷形式與原因分析
四、氣門感應(yīng)熱處理的最新動態(tài)與發(fā)展動向
1.最新動態(tài)
(1)進行頭桿與桿桿焊氣門的摩擦焊接后的快速退火處理,可進行連線加工,氣門在連續(xù)式感應(yīng)器中加熱,取消了焊后氣門集中退火繁瑣工序,實現(xiàn)節(jié)能降耗。國外氣門制造廠商開始在部分氣門生產(chǎn)線上應(yīng)用該技術(shù)。
(2)用于頭桿焊氣門脖頸處校直前的加熱,尤其對于不允許進行冷矯直或錘擊盤部(手工錘擊,容易造成盤部掉塊或存在隱患)的氣門采用此類措施,可根除柴油機氣門早期失效的發(fā)生。
(3)目前奧氏體耐熱鋼條材是制造氣門的原材料,是熱軋材經(jīng)高溫固溶處理制成,為保證氣門的使用性能,固溶處理大多采用電爐、燃氣爐、鹽浴爐等。感應(yīng)加熱固溶處理可以達到傳統(tǒng)固溶處理的目的,采用超音頻電源實現(xiàn)在居里點以下溫度具有良好的電效率,固溶處理溫度在1100~1150℃,時的噸鋼電能消耗為350~400kW·h,加熱系統(tǒng)的電效率可以達到65%左右。
2.發(fā)展動向
(1)向自動化方向發(fā)展,減輕勞動強度,提升生產(chǎn)效率。
氣門采用自動上下料自動進行錐面和桿端的淬火處理,出現(xiàn)異?;蚬收?,設(shè)備自動報警,從根本上解決依靠操作者進行繁瑣的重復(fù)勞動的弊端,產(chǎn)品質(zhì)量穩(wěn)定與生產(chǎn)效率明顯提高。
(2)向智能化方向發(fā)展,進行預(yù)防控制,實現(xiàn)報警、高低溫產(chǎn)品的分離等功能。
1)按工藝要求輸入程序后采用計算機控制,操作屏幕界面清晰,各種動作指令觸屏即可完成,人員進行巡視即可,從而減少人為因素的影響,確保產(chǎn)品質(zhì)量的穩(wěn)定與一致性。
2)對電源的運行狀態(tài)及參數(shù)實時監(jiān)控(如電壓、電流、功率、頻率、溫度等),真正實現(xiàn)實時了在線監(jiān)控。
3)計算機模擬感應(yīng)熱處理已在部分企業(yè)、研究所開展。這樣虛擬試制新技術(shù)將替代繁瑣費時的現(xiàn)場工藝調(diào)整。
本文僅對氣門盤部錐面與桿部的感應(yīng)淬火技術(shù)進行簡單分析,并指出生產(chǎn)過程中出現(xiàn)的質(zhì)量問題,且提出改進措施,旨在提高氣門的感應(yīng)淬火質(zhì)量。
一、感應(yīng)熱處理在氣門上的應(yīng)用
1.感應(yīng)熱處理的特點
感應(yīng)熱處理是生產(chǎn)率高、不污染環(huán)境、易于自動化和節(jié)省能源的一種先進熱處理技術(shù)。這一技術(shù)自問世以來一直在迅速發(fā)展,感應(yīng)熱處理技術(shù)的最大用戶是汽車零部件領(lǐng)域。
感應(yīng)熱處理技術(shù)由于具有優(yōu)質(zhì)、高效、節(jié)能、環(huán)保等諸多優(yōu)點,符合現(xiàn)代汽車生產(chǎn)需要,技術(shù)水平迅速提升[4]。高頻感應(yīng)加熱設(shè)備在汽車零部件領(lǐng)域的應(yīng)用十分廣泛,如氣門、挺桿、連桿、曲軸、凸輪軸、齒輪、萬向節(jié)鐘形殼及半軸等,其中氣門桿端進行連續(xù)淬火或沖擊淬火,錐面進行自動連續(xù)作業(yè)成為國內(nèi)外氣門感應(yīng)熱處理最成功的技術(shù),獲得了氣門制造廠商的青睞,國內(nèi)100余家氣門制造廠商均擁有5臺以上的高頻設(shè)備。其中我公司有30余臺感應(yīng)淬火設(shè)備(或連續(xù)生產(chǎn)線),年產(chǎn)感應(yīng)淬火氣門2000萬支以上,成為中國氣門制造廠商中產(chǎn)量最大與出口數(shù)量最多的制造廠商之一。
2. 內(nèi)燃機氣門感應(yīng)淬火的基本要求
氣門熱處理(調(diào)質(zhì)處理)后進行感應(yīng)淬火,目的是滿足其桿端面(或錐面)耐磨的要求, 《內(nèi)燃機 進、排氣門 技術(shù)條件》(GB/T23337—2009)與《汽車發(fā)動機氣門技術(shù)條件》(QC/T469—2002)中,均指出桿端面經(jīng)過表面淬火后硬度應(yīng)≥48HRC,當(dāng)桿端部長度>4mm時,硬化層深度應(yīng)≥2mm)或淬硬層深度應(yīng)≥0.6mm。盤錐面經(jīng)過表面淬火后的硬化層應(yīng)≥1.5mm,其硬度值應(yīng)符合圖樣規(guī)定,桿端與錐面感應(yīng)淬火晶粒度細于8級??梢妼忾T的錐面與桿部進行感應(yīng)淬火是標(biāo)準所要求的,是提高氣門表面硬度的不可缺少的熱處理手段。
二、氣門感應(yīng)熱處理的技術(shù)要求、感應(yīng)器的形式與選用
1. 技術(shù)要求
氣門進行感應(yīng)淬火的技術(shù)要求包括表面(或端面)硬度、硬化層(淬火)深度或長度、金相組織、畸變量及外觀等。
(1)錐面淬火要求 氣門錐面(閥口)與氣門底座反復(fù)貼合,要求其表面具有高的硬度和良好的耐磨性,感應(yīng)淬火可滿足其要求。錐面淬火的錐面硬度在45~58HRC,硬化層深度一般≥1.5mm,晶粒度細于8級,某氣門錐面淬火技術(shù)要求如圖1所示(圖中A點位置:距盤端面1.7mm,距盤外圓3.3mm。要求在淬火深度測量時應(yīng)透過A點,淬火區(qū)及過渡區(qū)不得超過圖中粗實線)。
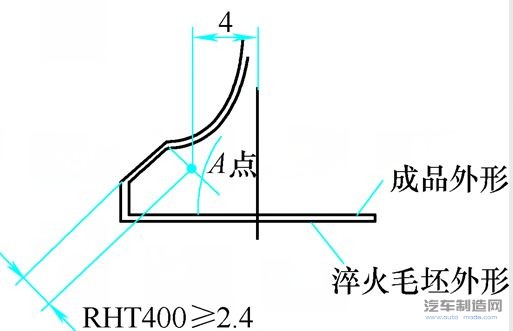
圖1 某氣門錐面工藝要求的淬火深度與硬度
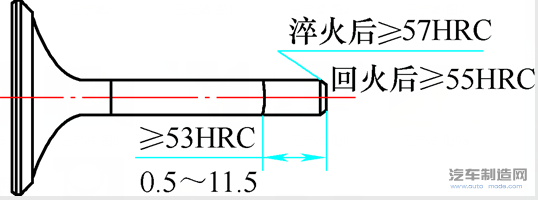
圖2氣門桿部淬透要求
(2)桿端淬火要求 對于氣門桿部的技術(shù)要求為淬火硬度50~60HRC,硬化層深度≥2mm,晶粒度細于8級等,其中工藝要求有桿部淬透、仿形淬火、桿端沖擊淬火等,圖2、圖3、圖4為某些氣門桿部淬透、桿部仿形和桿端沖擊淬火的技術(shù)要求。
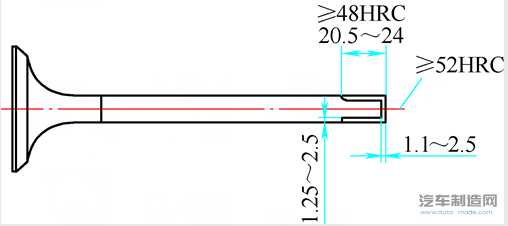
圖3氣門桿部仿形淬火要求
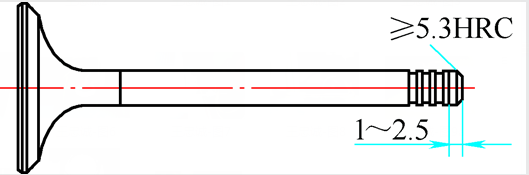
圖4 氣門桿端沖擊淬火要求
2. 感應(yīng)器的形式與選用
(1)錐面淬火感應(yīng)器 錐面淬火采用專用的感應(yīng)器,通常氣門使用的錐面淬火感應(yīng)器有兩種:連續(xù)式感應(yīng)器與單圈感應(yīng)器,其形狀是根據(jù)氣門盤錐面確定的,圖5、圖6為常見的感應(yīng)器形式。

圖5 多工位氣門錐面淬火感應(yīng)器實物形態(tài)
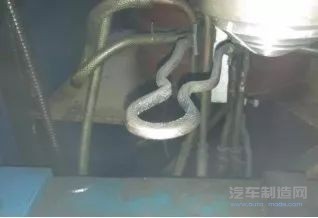
圖6單圈氣門錐面淬火感應(yīng)器
錐面淬火感應(yīng)器的選用原則:感應(yīng)器內(nèi)沿與氣門錐面之間留有間隙為1.5~3mm,氣門的盤部在加熱過程中是旋轉(zhuǎn)的,具體參數(shù)如電流、電壓、頻率、加熱溫度與加熱時間是通過工藝試驗來進行確定的,即滿足硬度與淬火深度合格,晶粒度要細于8級的要求,錐面淬火后的氣門通常進行160~200℃低溫回火或高溫回火處理,以穩(wěn)定組織,減小內(nèi)應(yīng)力與脆性。
(2)桿端淬火感應(yīng)器 氣門的桿端淬火采用特制的感應(yīng)器。這是考慮到其技術(shù)要求的差異而設(shè)計的,同時其工藝參數(shù)也有較大的不同,目的是滿足桿部的不同硬度與淬火長度的要求。圖7、圖8為沖擊與仿形淬火感應(yīng)器,圖9為桿端連續(xù)淬火與連續(xù)淬回火感應(yīng)器,該類感應(yīng)器應(yīng)用十分普遍,生產(chǎn)效率高。
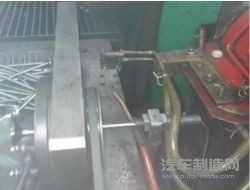
圖7氣門桿端沖擊/仿形淬火感應(yīng)器
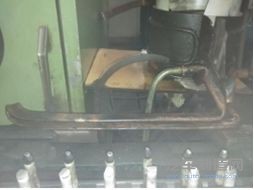
圖8 氣門桿部淬透連續(xù)淬火感應(yīng)器
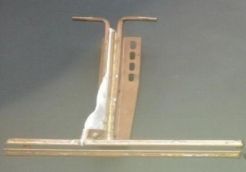
(a)回火感應(yīng)器
(b)淬火感應(yīng)器
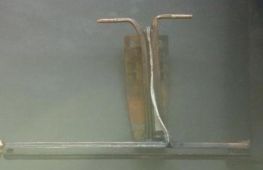
圖9 氣門桿部連續(xù)式淬火與回火感應(yīng)器
三、氣門感應(yīng)熱處理的質(zhì)量控制
1. 過程質(zhì)量控制
為滿足氣門感應(yīng)淬火后的質(zhì)量符合技術(shù)要求,氣門應(yīng)進行錐面和桿端感應(yīng)淬火的加熱與冷卻,選用感應(yīng)器、噴水器的結(jié)構(gòu)、形狀及尺寸應(yīng)滿足使用要求。根據(jù)工藝試驗結(jié)果確定最佳的工藝參數(shù)等,并按如下要求進行:
(1)要確定電壓、電流、加熱溫度、加熱時間或進給速度等。
(2)介質(zhì)溫度、壓力、流量、濃度的范圍及冷卻時間。
(3)感應(yīng)器外觀與冷卻噴淋結(jié)構(gòu)符合要求。
2. 質(zhì)量檢查方法
目前氣門桿部與錐面的硬度、長度或深度、晶粒度等檢查方法采用以下要求進行:
(1)對于要求采用洛氏/維式硬度檢查和淬火長度則采用在錐面或桿部外圓上檢查,圖10為檢查圖片。
(2)對于要求采用維氏硬度(平面)檢查的,則是在剖開錐面或桿部平面上,拋光后硬度與長度等按要求檢查如圖11所示。
(3)晶粒度的檢查按要求拋光腐蝕后進行。
(a)錐面硬度檢查 (b)桿端硬度檢查 (c)桿部淬火長度檢查
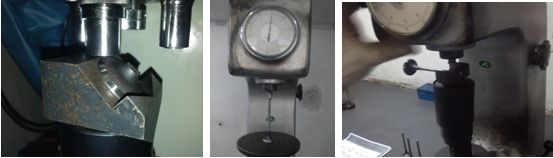
圖10 氣門硬度與淬火長度的硬度檢查法
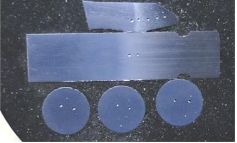
圖11 氣門錐面與桿端與淬火長度檢查(硬度法)
3. 缺陷形式與原因分析
氣門錐面與桿端淬火缺陷形式與原因分析具體見附表。
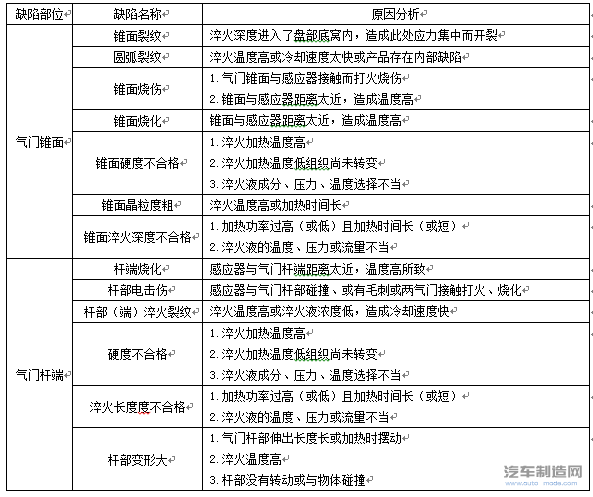
氣門感應(yīng)熱處理缺陷形式與原因分析
四、氣門感應(yīng)熱處理的最新動態(tài)與發(fā)展動向
1.最新動態(tài)
(1)進行頭桿與桿桿焊氣門的摩擦焊接后的快速退火處理,可進行連線加工,氣門在連續(xù)式感應(yīng)器中加熱,取消了焊后氣門集中退火繁瑣工序,實現(xiàn)節(jié)能降耗。國外氣門制造廠商開始在部分氣門生產(chǎn)線上應(yīng)用該技術(shù)。
(2)用于頭桿焊氣門脖頸處校直前的加熱,尤其對于不允許進行冷矯直或錘擊盤部(手工錘擊,容易造成盤部掉塊或存在隱患)的氣門采用此類措施,可根除柴油機氣門早期失效的發(fā)生。
(3)目前奧氏體耐熱鋼條材是制造氣門的原材料,是熱軋材經(jīng)高溫固溶處理制成,為保證氣門的使用性能,固溶處理大多采用電爐、燃氣爐、鹽浴爐等。感應(yīng)加熱固溶處理可以達到傳統(tǒng)固溶處理的目的,采用超音頻電源實現(xiàn)在居里點以下溫度具有良好的電效率,固溶處理溫度在1100~1150℃,時的噸鋼電能消耗為350~400kW·h,加熱系統(tǒng)的電效率可以達到65%左右。
2.發(fā)展動向
(1)向自動化方向發(fā)展,減輕勞動強度,提升生產(chǎn)效率。
氣門采用自動上下料自動進行錐面和桿端的淬火處理,出現(xiàn)異?;蚬收?,設(shè)備自動報警,從根本上解決依靠操作者進行繁瑣的重復(fù)勞動的弊端,產(chǎn)品質(zhì)量穩(wěn)定與生產(chǎn)效率明顯提高。
(2)向智能化方向發(fā)展,進行預(yù)防控制,實現(xiàn)報警、高低溫產(chǎn)品的分離等功能。
1)按工藝要求輸入程序后采用計算機控制,操作屏幕界面清晰,各種動作指令觸屏即可完成,人員進行巡視即可,從而減少人為因素的影響,確保產(chǎn)品質(zhì)量的穩(wěn)定與一致性。
2)對電源的運行狀態(tài)及參數(shù)實時監(jiān)控(如電壓、電流、功率、頻率、溫度等),真正實現(xiàn)實時了在線監(jiān)控。
3)計算機模擬感應(yīng)熱處理已在部分企業(yè)、研究所開展。這樣虛擬試制新技術(shù)將替代繁瑣費時的現(xiàn)場工藝調(diào)整。
最新資訊
-
跨越速運憑什么“圈粉”萬千客戶?“
2025-07-01 14:42
-
數(shù)智破局啟新篇?生態(tài)共生再啟程 —
2025-06-27 20:13
-
助力汽車零部件產(chǎn)線智能化升級,西門
2025-06-27 13:59
-
BBA集體轉(zhuǎn)向!放棄全面電動化
2025-06-26 17:32
-
比換柜省錢,比自研省心,西門子Xcel
2025-06-25 15:07