汽車高強鋼發(fā)展現(xiàn)狀及國內(nèi)外典型鋼制輕量化車身開發(fā)案例
1 汽車高強鋼發(fā)展現(xiàn)狀和趨勢
應用于汽車領域的高強鋼根據(jù)強化機理的不同,可分為普通高強鋼(HighSpeedSteels,HSS)、先進高強鋼(AdvancedHighStrengthSteel,AHSS)和超高強鋼(UltraHighStrengthSteel,UHSS),相關鋼材類別及其強度分布如圖1所示。其中,先進高強鋼、超高強鋼具備較高的強度和成形性,是實現(xiàn)車身輕量化和保證安全性的重要材料。近幾十年來,汽車用先進高強鋼是材料的研發(fā)重點,世界鋼協(xié)根據(jù)研發(fā)歷史及其特點,將其分為3代:第1代以鐵素體為基的AHSS鋼的強塑積為10~20GPa·%;第2代以奧氏體為基的AHSS鋼的強塑積為50~60GPa·%,其合金含量高和生產(chǎn)工藝控制困難導致成本高;第3代AHSS鋼以提高第1代AHSS鋼強度、塑性和降低第2代AHSS合金含量、生產(chǎn)成本2方面為目標進行研發(fā),第3代多相AHSS鋼通過多相、亞穩(wěn)和多尺度的組織精細調(diào)控,其強塑積為30~70GPa·%。目前,國內(nèi)鋼廠已經(jīng)具備DP、CP、TRIP、TWIP、Q&P、MS等先進高強鋼的生產(chǎn)能力,分別用于內(nèi)外覆蓋件、各種結(jié)構(gòu)件和梁類等汽車零部件。其力學性能覆蓋面非常寬,滿足汽車對強度、剛度、碰撞吸能安全性、舒適性和可加工性的要求,給汽車用材與選材提供了更多的選擇。
目前,國際主流車型的高強鋼占車身的比例已超過70%,其中自主品牌中高強鋼的應用已達45%。中國是高強度鋼應用最普遍的國家,車身使用比例接近50%,預計未來將達到60%~65%,但是超高強鋼和先進高強鋼使用比例大幅落后,目前僅有5%,預計未來有3倍提升空間。業(yè)內(nèi)專家認為在抗碰撞性能、加工工藝和成本方面,先進高強鋼與超高強鋼比鋁鎂合金具有明顯的優(yōu)勢,能夠滿足減輕汽車質(zhì)量和提高碰撞安全性能的雙重技術需要,甚至從成本與性能角度來看,是目前滿足車身輕量化、提高碰撞安全性的最佳材料。
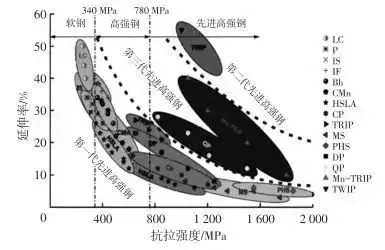
圖 1 先進高強汽車用類別及強度分布
對近年來“歐洲車身會議”和“中國輕量化車身會議”展示車型相關用材數(shù)據(jù)進行了統(tǒng)計分析,我國乘用車高強鋼的應用水平已經(jīng)達到世界先進水平(圖2),歐洲車身會議展示產(chǎn)品的高強鋼用量平均為56.7%,最高為73%,中國輕量化車身會議展示產(chǎn)品的高強鋼用量平均為62%,最高為70.4%。因此,高強鋼在車身上的應用方面,中國處于領先地位,顯示了我國汽車企業(yè)高強鋼的應用水平大幅度提升,從材料生產(chǎn)到零件加工生產(chǎn)體系的日臻完善。
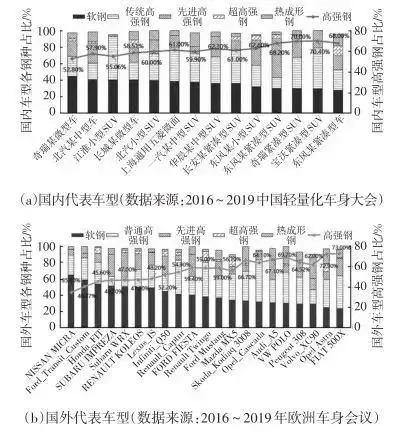
圖 2 全球典型鋼制車身的高強度鋼應用情況
從國際上看,盡管已經(jīng)有了許多鋁合金和碳纖維等材料應用的成功案例,但高強鋼仍然在企業(yè)用材策略中占據(jù)重要地位。從圖 2 可知,各大主機廠在車身用材選擇和成形工藝選擇方面存在不同,而決定其高強鋼用材策略的關鍵因素是鋼鐵企業(yè)的產(chǎn)品規(guī)格、性能、價格以及供應鏈的支撐能力。
綜合以上分析,隨著我國高強鋼生產(chǎn)技術的不斷發(fā)展,在汽車鋼品種和強度級別等方面已經(jīng)與發(fā)達國家基本相當,我國在具有高強度、高塑性特征的第 3 代鋼開發(fā)和生產(chǎn)方面具有的世界領先優(yōu)勢為世界所公認,也為我國進一步推動高強鋼的應用提供有力支撐,以高強鋼相關的一批團體標準的頒布及汽車用鋼上下游產(chǎn)業(yè)鏈 EVI 領域的持續(xù)發(fā)展,將為車企擴大高強鋼應用提供技術依據(jù)和材料保障。相信隨著“高強鋼回彈”“延遲斷裂”等核心技術問題的認知與解決,將為高強鋼在我國新能源汽車產(chǎn)業(yè)內(nèi)的進一步應用開拓更大的空間。
2 國內(nèi)外典型鋼制輕量化車身開發(fā)案例
為提升自身整車EVI技術水平,增強企業(yè)選材和提供鋼鐵輕量化綜合解決方案的能力,近十年來國內(nèi)外主要鋼鐵公司先后開展了多款鋼制輕量化車身與綜合解決方案項目,典型的有浦項PBC-EV、蒂森In-car、安米S-inmotion、寶鋼BCB系列和馬鋼MCEV等。
2.1 浦項 PBC-EV 和 eAutopos 項目
2010~2012年,浦項開發(fā)了首款PBC-EV(POS?COBodyConcept-ElectricVehicle)純電動概念白車身(圖3)。PBC-EV車身采用了先進高強鋼及熱成形、變截面柔性輥壓成形、液壓成形、激光拼焊等先進成形技術,實現(xiàn)輕量化的同時提高了安全性。PBC-EV白車身高強鋼比例達到65%(其中超高強鋼超過40%),車身質(zhì)量由296kg降低至218kg,在成本小幅增加的同時能夠?qū)崿F(xiàn)質(zhì)量降低26%;從制造到報廢回收后的LCA全生命周期評價中溫室氣體排放量減少約50%。
圖 3 浦項 PBC-EV 白車身
2021年,浦項發(fā)布了其新的生態(tài)友好型電動汽車(含純電動汽車和燃料電池汽車)綜合解決方案eAutopos(eco-friendly,ElectrifiedAutomotiveSo?lutionofPOSCO),主要產(chǎn)品包括車身和底盤用高強汽車板、電池包專用鋼材、驅(qū)動電機用節(jié)能高效電工鋼、氫能電動汽車用金屬雙極板和二次電池用正負極材料等(圖4)。針對白車身,eAutopos解決方案為使用多種先進超高強鋼增強車身強度和碰撞安全性。例如,對于吸收車輛前部沖擊力的前縱梁采用了980XF鋼,座椅橫梁和儀表板橫梁外側(cè)件則采用了MS1500等超高強度冷軋板,前側(cè)圍延伸件采用了1500MPa熱成型鋼。經(jīng)過輕量化設計后,白車身質(zhì)量降低至207kg,降低30%。針對懸架系統(tǒng),eAutopos解決方案為采用其研制的高性能軸承鋼、懸架彈簧、輪胎簾線鋼等,在實現(xiàn)輕量化的同時保證了部件良好的加工和使用性能。
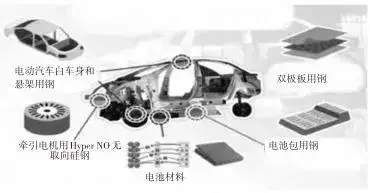
圖 4 eAutopos 電動車綜合解決方案
2.2 蒂森 In-car 項目
2009年,蒂森啟動了面向汽車生產(chǎn)商的創(chuàng)新項目“In-car”。項目聚焦輕量化、降本、減排和提高性能,并引入生命周期分析(LifeCycleAssess?ment,LCA)理念,開發(fā)出了30多種車身、底盤及動力系統(tǒng)的創(chuàng)新解決方案,使整車質(zhì)量減輕一半的同時成本降低20%(表1),在汽車整個生命周期可減少CO2排放量1.6t。
In-car項目是蒂森的菜單式輕量化解決方案,它對車身、懸架、動力總成3大系統(tǒng)的16個主要部件均進行了輕量化設計,每個部件給出了1種以上的解決方案,且每種解決方案提供了對標車和In-car解決方案的用材、質(zhì)量、成本和排放情況,用戶可以根據(jù)應用目的、生產(chǎn)和工藝條件選擇不同的解決方案。
2.3安米S-inmotion項目
從2010年開始,安米陸續(xù)開發(fā)了S-inmotion系列車型(包括燃油車、電動車、轎車、SUV、商用車)輕量化解決方案(圖5),主要通過先進高強鋼的輕量化設計應用,為用戶提供安全、輕量化、低成本、滿足可持續(xù)發(fā)展的全面解決方案。
以2015年北美市場典型SUV和中高級轎車為例,通過S-inmotion解決方案,SUV可實現(xiàn)車身質(zhì)量降低112kg(比例為21%),高強鋼比例由33%提升到51%;轎車有望實現(xiàn)車身質(zhì)量降低100kg(比例為28%),高強鋼比例由68%提升到74%,全生產(chǎn)周期碳排放減少13.5%。
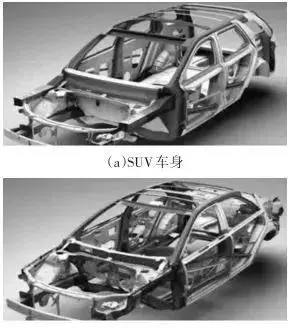
圖 5 S-in motion 輕量化方案
2020年,安米推出了全新的S-inmotion純電動汽車鋼制電池包解決方案(圖6)。該方案應用多種高強鋼,其中關鍵部位(骨架、底部)使用先進高強鋼(包括2GPa鋁硅鍍層熱成形鋼和500MPa馬氏體鋼),在滿足性能的前提下有效控制電池包質(zhì)量,電池盒結(jié)構(gòu)僅占總電池包質(zhì)量的20%。通過對零件的截面設計優(yōu)化,大大降低了模具的成本投入;梁結(jié)構(gòu)采用輥壓成形工藝,底蓋板等采用方板件設計及簡單的淺沖壓或開孔工藝,使得電池包整體材料利用率達到90%以上,可有效控制成本。
2.4 寶鋼 BCB 系列項目
2015年,寶鋼推出了首款超輕型概念白車身BCB(BaosteelCarBody),是國內(nèi)鋼鐵企業(yè)首次按照汽車設計流程和規(guī)則,整合新材料、新工藝和新結(jié)構(gòu)優(yōu)化技術而完成的白車身,在安全性、舒適性和輕量化方面達到國際先進水平(圖7、表2)。
BCB白車身質(zhì)量為284kg,車身大量應用3代汽車用鋼,包括MS1500、B1800HS、TWIP950、QP1180等新材料,高強鋼應用比例為77%;在成形工藝方面,應用了熱沖壓成形、液壓成形、輥壓成形、VRB板成形和激光拼焊板成形等先進成形技術。通過高強減薄輕量化設計,保證整車性能的同時,實車輕量化系數(shù)達到2.7。
圖 6 輕量化鋼制電池包方案(S-in motion)
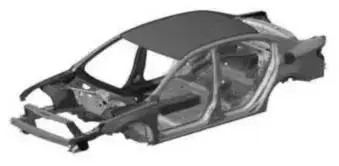
圖 7 寶鋼 BCB 白車身
表 2 寶鋼 BCB 白車身設計指標
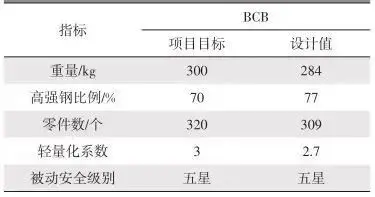
2021年,寶鋼向全球發(fā)布了超輕型純電動高安全車身BCB-EV(BaosteelCarBodyElectricVehi?cle)。BCB-EV以先進材料、成熟工藝和結(jié)構(gòu)優(yōu)化為創(chuàng)新點,打造了以吉帕鋼為主的超輕型高安全純電動車身(圖8)。BCB-EV白車身吉帕鋼比例超50%,電池包框架吉帕鋼100%,最高強度熱成形材料用到2000MPa級別,冷成型材料應用到1700MPa級別;先進高強鋼與7種先進成形、不等厚軋制、拼焊工藝相結(jié)合,實現(xiàn)白車身質(zhì)量達到303kg(質(zhì)量降低57kg,降低比例10%~20%),輕量化系數(shù)達到2.13,滿足整車C-NCAP2021五星碰撞安全、25%小偏置碰GOOD性能要求,實現(xiàn)鋼板生產(chǎn)環(huán)節(jié)CO2減排200kg,電動車使用環(huán)節(jié)CO2減排296kg。
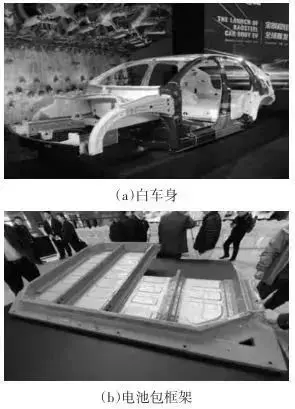
圖 8 寶鋼 BCB-EV
2.5 馬鋼 MCEV 超輕型電動概念車開發(fā)
為了積極響應汽車行業(yè)輕量化需求,充分展示利用鋼鐵的設計靈活性以及使用高強鋼來解決新能源汽車輕量化面臨的難題,2018年馬鋼聯(lián)合中國汽研、中信金屬等啟動了馬鋼電動概念車(MasteelConceptElectricVehicle,MCEV)電動概念車開發(fā)項目。項目選取一款全球先進的電動車為標桿,并結(jié)合行業(yè)電動車先進技術水平,開發(fā)一款基于馬鋼汽車鋼體系的輕量化、高性能、高安全、經(jīng)濟型A級電動概念車(圖9)。 MCEV設計車采用全鋼車身設計,用鋼布局講究“將合理的材料應用于合理的部位”原則,進一步提升高強鋼的比例,達到輕量化效果。其中前橫梁、頂蓋中橫梁、外門環(huán)、門檻梁外板等安全部件采用馬鋼1500MPa級、1800MPa薄鍍層、高冷彎、抗延遲開裂熱成形鋼。MCEV設計車采用了48.08%高強鋼、22.33%先進高強鋼、13.22%熱成形鋼,高強鋼占比達83.63%(其中含Nb高強鋼比例61%),如圖10所示。
圖 9 MCEV 新能源概念車
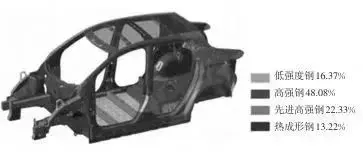
圖 10 MCEV 白車身用材比例
在車身設計上,通過CAD/CAE/SE等計算機技術對白車身的結(jié)構(gòu)和布局進行優(yōu)化分析,通過采用傳力路徑優(yōu)化設計、結(jié)構(gòu)截面優(yōu)化設計等,在實現(xiàn)輕量化的同時進一步提升了車身的安全性。MCEV設計車前防撞梁加長、增加副吸能盒,在MPDB工況下,可使碰撞力的傳遞更加均衡,在小偏置碰撞工況下,抗撞性能有所提高,如圖11、圖12所示。MCEV設計車上縱梁延伸到縱梁前端板形成閉環(huán)環(huán)狀結(jié)構(gòu),有效提升抵抗小偏置碰撞的能力;前艙橫梁的拉通橫梁結(jié)構(gòu)提升了抵抗變形能力,分散傳力路徑,增強安全性能,提高扭轉(zhuǎn)剛度;貫穿式的高強鋼座椅橫梁與B柱、頂蓋中橫梁形成環(huán)狀結(jié)構(gòu),提高局部剛度性能和抗變形能力,有效實現(xiàn)載荷分流,極大增強整車剛度,如圖12所示。 經(jīng)輕量化設計,MCEV白車身質(zhì)量為265kg,質(zhì)量降低10.9%,輕量化系數(shù)為2.62;整車正面100%碰撞、柱碰、MPDB的性能達到C-NCAP五星水平,25%小偏置碰、頂壓性能達到中保研汽車碰撞安全指數(shù)(C-IASI)優(yōu)秀水平,白車身(帶玻璃)扭轉(zhuǎn)剛度≥23000N·m/(°)、彎曲剛度≥15000N/mm,白車身(帶玻璃)扭轉(zhuǎn)模態(tài)≥36Hz、彎曲模態(tài)≥52Hz,具有較高安全性。
圖 11 MCEV 設計車碰撞傳力路徑
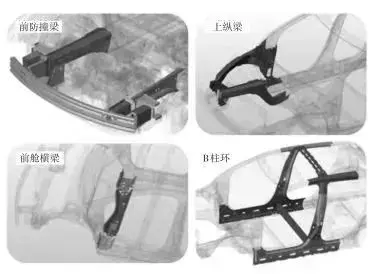
圖 12 MCEV 設計車前防撞梁、上縱梁、前艙橫梁、B 柱環(huán)
MCEV設計車的主要技術性能指標與其它新能源車型對比如表3所示。MCEV概念車不論在輕量化(質(zhì)量)、安全性能(扭轉(zhuǎn)剛度)、高強鋼占比等方面的技術指標水平均優(yōu)于標桿車,達到國際先進水平。
表 3 多款新能源車的高強鋼占比、車身質(zhì)量、扭轉(zhuǎn)剛度、輕量化系數(shù)
3 結(jié)束語
輕量化是以電為核心的新能源化是汽車節(jié)能減排的有效途徑,也是未來全球汽車工業(yè)發(fā)展的必然趨勢。高強鋼由于其高承載安全性、高工藝適應性、高性價比綜合優(yōu)勢,可預見未來至少15年甚至更長時間內(nèi)依舊是全球節(jié)能和新能源汽車材料行業(yè)的最重要發(fā)展方向之一。未來隨著汽車產(chǎn)業(yè)的電動化這一大勢所趨,節(jié)能減排、“碳達峰、碳中和”政策的實施,以及先進高強鋼性能和應用技術愈發(fā)成熟,其必將在汽車輕量化領域發(fā)揮更大的作用。基于新時代的EVI理念,協(xié)同上下游產(chǎn)業(yè)鏈,以國家行業(yè)發(fā)展政策及終端用戶市場共性及個性化需求為牽引,打通不同類別汽車用鋼之于終端車型產(chǎn)品的應用瓶頸鏈,為終端用戶提供汽車鋼成套應用技術解決方案,達成在車型上的集成應用是目前全球汽車鋼業(yè)界的熱點、焦點領域。近十年來國內(nèi)外主要鋼鐵公司先后開展的多款鋼制輕量化車身項目,展示了不同優(yōu)秀鋼制輕量化解決方案的實踐案例,大大促進了全球各類鋼制車型領域的整體輕量化技術水平,尤其促進了各類先進汽車高強鋼的持續(xù)推廣應用。 相對于傳統(tǒng)的燃油汽車,新能源汽車在鋼材應用總體層面不存在本質(zhì)差異性,但是還是會體現(xiàn)出一定的個性化。首先,新能源汽車基于三電系統(tǒng)的存在,其對輕量化和安全性的要求更高,尤其隨著近年來中保研汽車碰撞安全指數(shù)(C-IASI)等更苛刻碰撞安全性能評價方法標準的逐步推廣,強度級更高的鋼種將集成應用于新能源汽車車身和底盤系統(tǒng)。其次,新能源汽車將增加對高品質(zhì)電機用硅鋼片的消耗。
上述新能源車的結(jié)構(gòu)特性將會對鋼企的產(chǎn)品發(fā)展策略產(chǎn)生影響。近年來國內(nèi)如熱成形薄鋁硅鍍層板、DH鋼等單一品種汽車鋼的研發(fā)及推廣及以馬鋼MCEV項目為代表的超輕質(zhì)、高性能、低成本,滿足市場需求的新能源汽車用鋼集成技術解決方案,均是國內(nèi)汽車鋼業(yè)界走出中國特色發(fā)展之路的重要探索。綜上所述,推進中國汽車鋼產(chǎn)業(yè)鏈的協(xié)同、又好又快的發(fā)展,這顯然不是鋼鐵行業(yè)一個領域的事情,必須進一步加強汽車用鋼上下游產(chǎn)業(yè)鏈EVI合作力度,不斷基于新能源汽車產(chǎn)業(yè)的發(fā)展涌現(xiàn)出的新需求,研發(fā)出對口的新鋼種,不斷合作突破更多的產(chǎn)業(yè)鏈技術瓶頸,推進我國汽車鋼事業(yè)邁向新的發(fā)展階段,為中國制造業(yè)早日實現(xiàn)“強國夢”,達成“雙碳”宏偉目標注入強勁的科技動力。
- 下一篇:汽車生產(chǎn)制造流程圖
- 上一篇:汽車智能底盤:未來技術趨勢
-
專家訪談:埃馬克 OCTG 加工的技術密鑰與生產(chǎn)之
2025-06-25 -
Know-How系列 | 石油鉆機核心技術揭秘:埃馬克
2025-06-19 -
聚焦機床 | 埃馬克USC 850數(shù)控萬能車床:突破大
2025-06-11 -
DMC中國國際模具裝備展今日開幕,600+展商齊聚
2025-06-05
編輯推薦
最新資訊
-
跨越速運憑什么“圈粉”萬千客戶?“
2025-07-01 14:42
-
數(shù)智破局啟新篇?生態(tài)共生再啟程 —
2025-06-27 20:13
-
助力汽車零部件產(chǎn)線智能化升級,西門
2025-06-27 13:59
-
BBA集體轉(zhuǎn)向!放棄全面電動化
2025-06-26 17:32
-
比換柜省錢,比自研省心,西門子Xcel
2025-06-25 15:07