汽車沖壓件工藝參數(shù)優(yōu)化及回彈控制
2018-08-14 16:30:58· 來(lái)源:鍛壓技術(shù)
針對(duì)汽車沖壓件的回彈問(wèn)題, 研究了某汽車后地板零件的回彈控制問(wèn)題。首先借助數(shù)值模擬軟件Auto Form建立汽車后地板零件沖壓成形的全流程的有限元模型, 然后采用工藝參數(shù)優(yōu)化和回彈補(bǔ)償相結(jié)合來(lái)共同控制該零件的回彈。工藝參數(shù)優(yōu)化借助了Auto Form的西格瑪優(yōu)化模塊, 優(yōu)化目標(biāo)為最小回彈量, 優(yōu)化得到最優(yōu)組的壓邊力為798 k N, 摩擦系數(shù)為0.14。然后采用回彈補(bǔ)償策略對(duì)拉延工序的模具進(jìn)行回彈補(bǔ)償, 當(dāng)回彈補(bǔ)償循環(huán)迭代2次后, 零件的回彈滿足尺寸公差要求。最后進(jìn)行了模具加工和試模驗(yàn)證。實(shí)驗(yàn)結(jié)果表明將工
摘要
針對(duì)汽車沖壓件的回彈問(wèn)題, 研究了某汽車后地板零件的回彈控制問(wèn)題。首先借助數(shù)值模擬軟件Auto Form建立汽車后地板零件沖壓成形的全流程的有限元模型, 然后采用工藝參數(shù)優(yōu)化和回彈補(bǔ)償相結(jié)合來(lái)共同控制該零件的回彈。工藝參數(shù)優(yōu)化借助了Auto Form的西格瑪優(yōu)化模塊, 優(yōu)化目標(biāo)為最小回彈量, 優(yōu)化得到最優(yōu)組的壓邊力為798 k N, 摩擦系數(shù)為0.14。然后采用回彈補(bǔ)償策略對(duì)拉延工序的模具進(jìn)行回彈補(bǔ)償, 當(dāng)回彈補(bǔ)償循環(huán)迭代2次后, 零件的回彈滿足尺寸公差要求。最后進(jìn)行了模具加工和試模驗(yàn)證。實(shí)驗(yàn)結(jié)果表明將工藝參數(shù)優(yōu)化和回彈補(bǔ)償相結(jié)合的方法能夠有效地控制沖壓零件的回彈。
一、有限元模型
汽車后地板是汽車生產(chǎn)中的典型薄板類零件, 該零件的生產(chǎn)批量大、尺寸精度要求高、模具開發(fā)成本高。有限元軟件可以在模具開發(fā)前期來(lái)預(yù)測(cè)零件的成形缺陷和回彈量, 此外有限元軟件還可以根據(jù)預(yù)測(cè)的回彈量來(lái)對(duì)模具進(jìn)行回彈補(bǔ)償, 從而有效降低模具開發(fā)成本。
以某汽車后地板為研究對(duì)象, 該零件的成形工藝流程為拉延、切邊、沖孔、翻邊。在板料沖壓成形分析軟件Auto Form中建立汽車后地板的全流程的有限元模型如圖1所示, 模型中包括拉延工序、切邊工序和翻邊工序。拉延工序采用倒裝的單動(dòng)拉延工藝, 拉延工序成形工具包括凹模、壓邊圈和凸模。翻邊工序的成形工具有托料器、壓料器和翻邊工具。
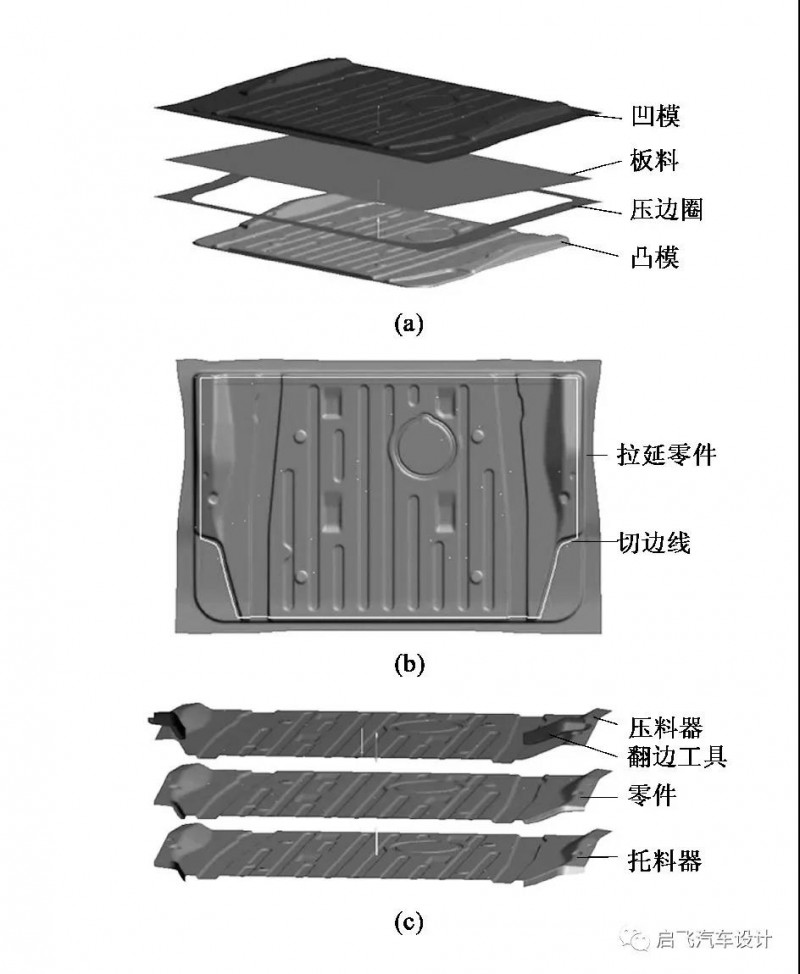
圖1 汽車后地板有限元模型 (a) 拉延工序 (b) 切邊工序 (c) 翻邊工序
該零件的材料為寶鋼材料DC03鋼, 材料厚度為0.7 mm。表1為數(shù)值模擬中材料的力學(xué)性能。Auto Form中有兩種單元類型:膜單元和殼單元, 為了提高數(shù)值模擬的計(jì)算精度, 在有限元模型中選擇單元類型為彈塑性殼單元。成形模擬中板料一般設(shè)置為5層, 為了準(zhǔn)確預(yù)測(cè)零件成形后的回彈量, 在模擬中設(shè)置板料為11層。
表1 DC03鋼的材料力學(xué)性能
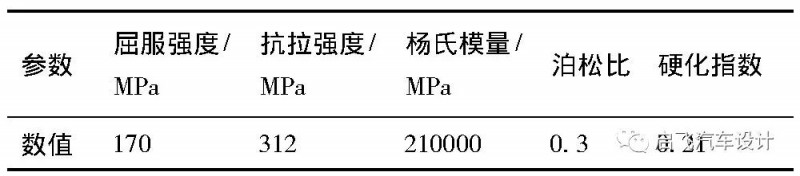
二、工藝參數(shù)優(yōu)化
零件回彈的影響因素較多, 包括材料參數(shù)和成形工藝參數(shù)。而當(dāng)零件的材料確定后, 材料參數(shù)已確定, 不能進(jìn)行更改, 因此, 為了降低成形后零件的回彈量, 對(duì)汽車后地板的成形工藝參數(shù)進(jìn)行優(yōu)化, 確定回彈量較小的工參數(shù)。
在對(duì)汽車沖壓件的回彈控制中, 得出影響零件回彈的主要工藝參數(shù)有壓邊力、模具間隙、摩擦系數(shù)。對(duì)于汽車后地板模具開發(fā)中, 最后凸凹要完全閉合, 因此, 在對(duì)汽車后地板的工藝參數(shù)優(yōu)化中主要考慮了成形過(guò)程中的壓邊力和摩擦系數(shù)。
工藝參數(shù)優(yōu)化借助Auto Form的西格瑪優(yōu)化模塊 (RE:Performance Analysis Design) , 該模塊用于沖壓工藝參數(shù)優(yōu)化。優(yōu)化分析的設(shè)計(jì)變量見表2。優(yōu)化分析中優(yōu)化目標(biāo)為零件的回彈量, 進(jìn)行30組模擬, 得到的模擬結(jié)果見圖2, 由圖2可知, 第24組為回彈最小的模擬組, 因此, 將該模擬組的參數(shù)作為最優(yōu)參數(shù)組合, 即最優(yōu)組的壓邊力為798k N, 摩擦系數(shù)為0.14。優(yōu)化后的零件的回彈分布如圖3所示, 圖3中采用橢圓圈出的區(qū)域A~D為該零件回彈較大的4個(gè)區(qū)域, 其中零件的最大回彈量為1.78 mm。
表2 優(yōu)化分析的設(shè)計(jì)變量
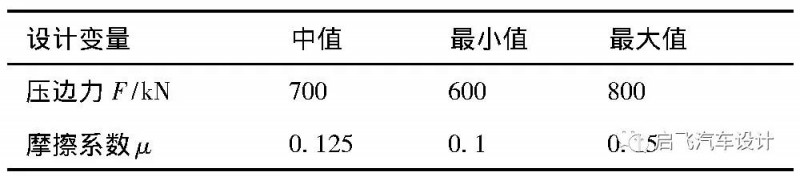
三、回彈補(bǔ)償
采用工藝參數(shù)優(yōu)化只能減小零件的回彈, 但不能完全控制零件的回彈量。因此, 接下來(lái)采用回彈補(bǔ)償方法來(lái)進(jìn)一步控制回彈。對(duì)拉延工序的模具進(jìn)行補(bǔ)償, 回彈補(bǔ)償方法如圖4所示, 將拉延模模面分為3個(gè)區(qū)域, 切邊線以內(nèi)區(qū)域定義為直接補(bǔ)償區(qū)域, 壓料面部分定義為固定補(bǔ)償區(qū)域, 壓料面和切邊線之間區(qū)域定義為過(guò)渡補(bǔ)償區(qū)域。采用Auto Form軟件進(jìn)行回彈補(bǔ)償, 當(dāng)回彈補(bǔ)償循環(huán)迭代2次后, 成形后零件的回彈滿足尺寸公差要求。第1次回彈補(bǔ)償后, 零件的回彈相對(duì)于未補(bǔ)償時(shí)回彈量有所降低, 圖3中4個(gè)橢圓區(qū)域A~D的最大回彈量分別為1.28, 1.14, 1.21和0.96 mm。第2次回彈補(bǔ)償后的零件的回彈分布如圖5所示, 4個(gè)橢圓區(qū)域A~D的最大回彈量分別為0.68, 0.63, 0.62和0.45mm。圖6為回彈補(bǔ)償前后的模面, 可以看出零件的型面補(bǔ)償主要在零件區(qū)域和過(guò)渡補(bǔ)償區(qū)域, 壓料面在補(bǔ)償前后未發(fā)生變化。
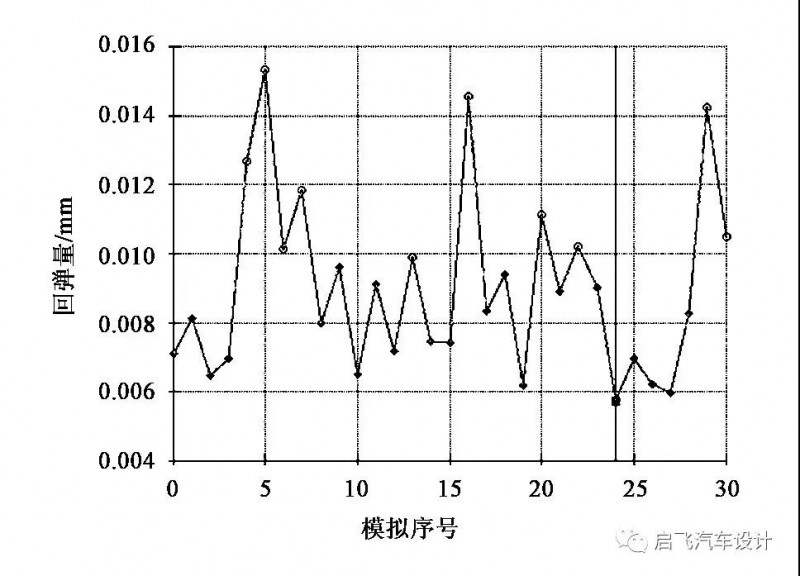
圖2 優(yōu)化分析的回彈結(jié)果
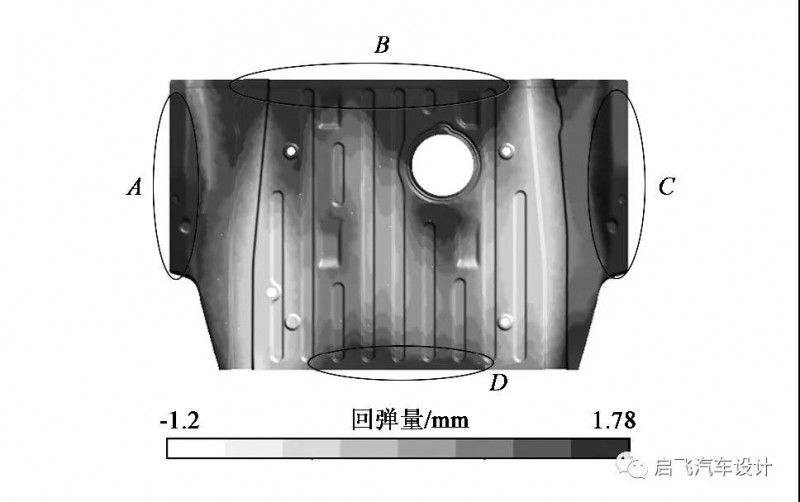
圖3 優(yōu)化后的零件的回彈分布
四、實(shí)驗(yàn)驗(yàn)證
為驗(yàn)證數(shù)值模擬結(jié)果進(jìn)行了模具加工和試模實(shí)驗(yàn), 得到試模零件如圖7所示。由圖7可知, 該零件成形充分, 無(wú)成形缺陷。采用模具檢具對(duì)零件進(jìn)行檢查, 重點(diǎn)測(cè)量圖3所示的4個(gè)橢圓區(qū)域, 得到橢圓區(qū)域A~D的最大回彈量分別為1.20, 0.96, 1.14和0.66 mm。由于零件的允許最大偏差為±0.7 mm, 因此, 還需要對(duì)超出區(qū)域進(jìn)行試模修改, 通過(guò)再一次對(duì)模具型面進(jìn)行修改加工, 最終得到零件的回彈偏差滿足零件尺寸要求。雖然本文提出的方法沒(méi)有達(dá)到一次控制零件的回彈, 但相對(duì)于傳統(tǒng)回彈補(bǔ)償方法, 能縮短試模調(diào)試時(shí)間, 降低模具成本。
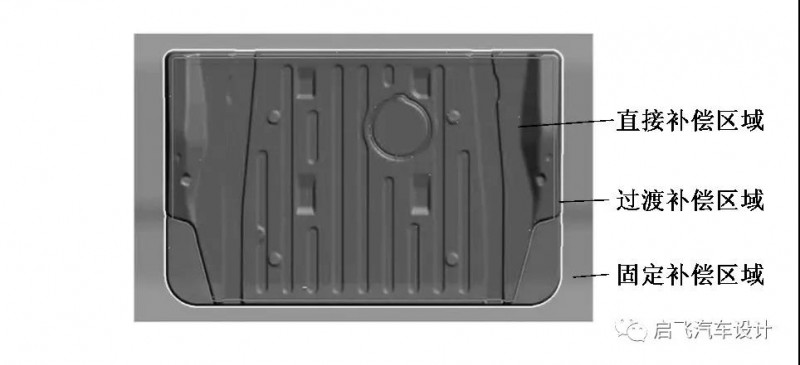
圖4 回彈補(bǔ)償策略
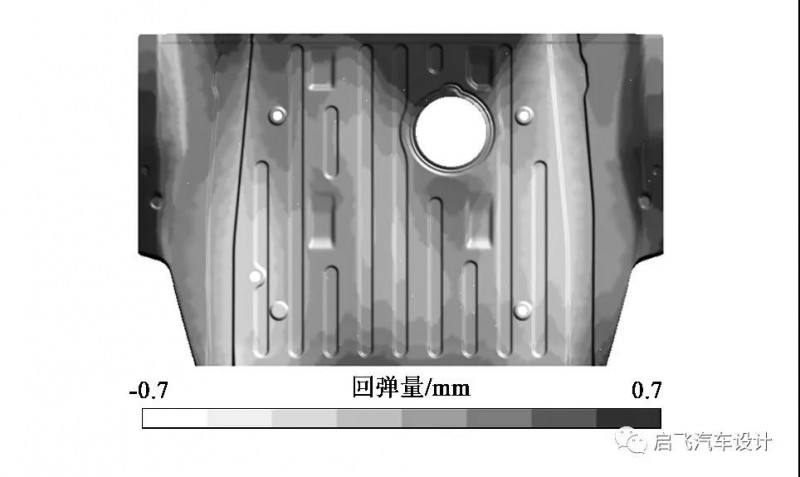
圖5 第2次回彈補(bǔ)償后的零件的回彈分布
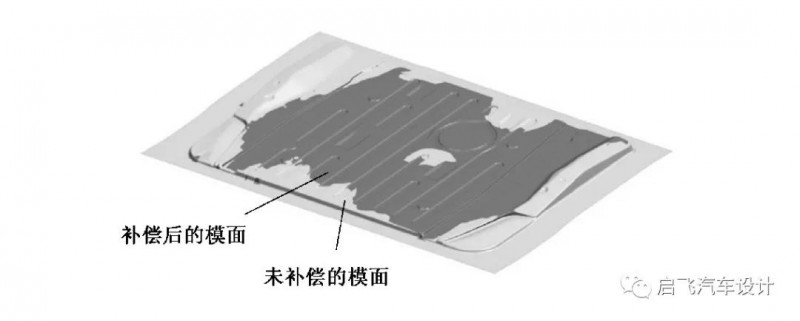
圖6 回彈補(bǔ)償前后的模面
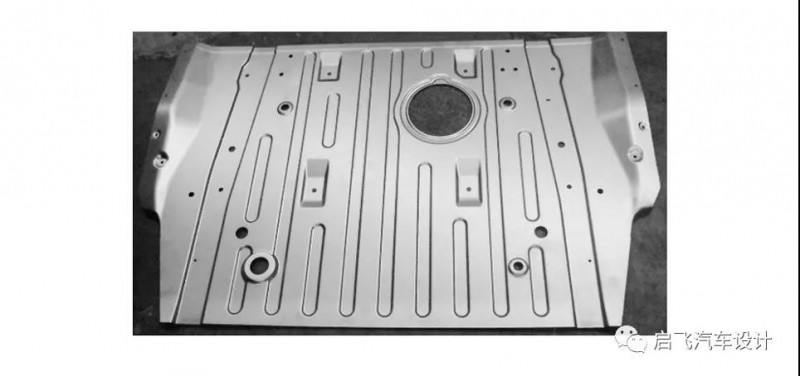
圖7 試模零件
五、結(jié)論
(1) 針對(duì)汽車沖壓件的回彈問(wèn)題, 借助數(shù)值模擬軟件Auto Form建立汽車后地板零件沖壓成形的全流程的有限元模型, 然后采用工藝參數(shù)優(yōu)化和回彈補(bǔ)償來(lái)控制該零件的回彈。
(2) 工藝參數(shù)優(yōu)化中得到最優(yōu)組的壓邊力為798 k N, 摩擦系數(shù)為0.14。采用回彈補(bǔ)償策略對(duì)拉延模具進(jìn)行回彈補(bǔ)償, 當(dāng)回彈補(bǔ)償循環(huán)迭代兩次后成形后零件的回彈滿足尺寸公差要求。
(3) 實(shí)驗(yàn)結(jié)果表明將工藝參數(shù)優(yōu)化和回彈補(bǔ)償相結(jié)合的方法能夠有效地控制零件的回彈, 縮短試模調(diào)試時(shí)間, 降低模具成本。
作者:茍春梅; 吳民; 董靜; 孫華偉
針對(duì)汽車沖壓件的回彈問(wèn)題, 研究了某汽車后地板零件的回彈控制問(wèn)題。首先借助數(shù)值模擬軟件Auto Form建立汽車后地板零件沖壓成形的全流程的有限元模型, 然后采用工藝參數(shù)優(yōu)化和回彈補(bǔ)償相結(jié)合來(lái)共同控制該零件的回彈。工藝參數(shù)優(yōu)化借助了Auto Form的西格瑪優(yōu)化模塊, 優(yōu)化目標(biāo)為最小回彈量, 優(yōu)化得到最優(yōu)組的壓邊力為798 k N, 摩擦系數(shù)為0.14。然后采用回彈補(bǔ)償策略對(duì)拉延工序的模具進(jìn)行回彈補(bǔ)償, 當(dāng)回彈補(bǔ)償循環(huán)迭代2次后, 零件的回彈滿足尺寸公差要求。最后進(jìn)行了模具加工和試模驗(yàn)證。實(shí)驗(yàn)結(jié)果表明將工藝參數(shù)優(yōu)化和回彈補(bǔ)償相結(jié)合的方法能夠有效地控制沖壓零件的回彈。
一、有限元模型
汽車后地板是汽車生產(chǎn)中的典型薄板類零件, 該零件的生產(chǎn)批量大、尺寸精度要求高、模具開發(fā)成本高。有限元軟件可以在模具開發(fā)前期來(lái)預(yù)測(cè)零件的成形缺陷和回彈量, 此外有限元軟件還可以根據(jù)預(yù)測(cè)的回彈量來(lái)對(duì)模具進(jìn)行回彈補(bǔ)償, 從而有效降低模具開發(fā)成本。
以某汽車后地板為研究對(duì)象, 該零件的成形工藝流程為拉延、切邊、沖孔、翻邊。在板料沖壓成形分析軟件Auto Form中建立汽車后地板的全流程的有限元模型如圖1所示, 模型中包括拉延工序、切邊工序和翻邊工序。拉延工序采用倒裝的單動(dòng)拉延工藝, 拉延工序成形工具包括凹模、壓邊圈和凸模。翻邊工序的成形工具有托料器、壓料器和翻邊工具。
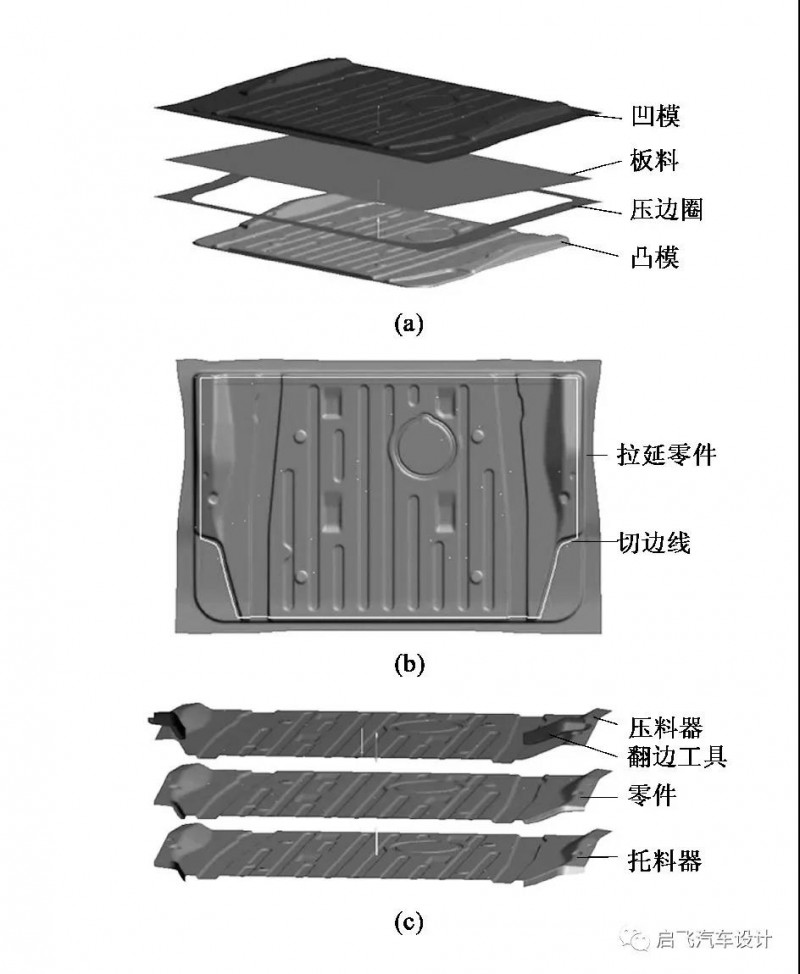
圖1 汽車后地板有限元模型 (a) 拉延工序 (b) 切邊工序 (c) 翻邊工序
該零件的材料為寶鋼材料DC03鋼, 材料厚度為0.7 mm。表1為數(shù)值模擬中材料的力學(xué)性能。Auto Form中有兩種單元類型:膜單元和殼單元, 為了提高數(shù)值模擬的計(jì)算精度, 在有限元模型中選擇單元類型為彈塑性殼單元。成形模擬中板料一般設(shè)置為5層, 為了準(zhǔn)確預(yù)測(cè)零件成形后的回彈量, 在模擬中設(shè)置板料為11層。
表1 DC03鋼的材料力學(xué)性能
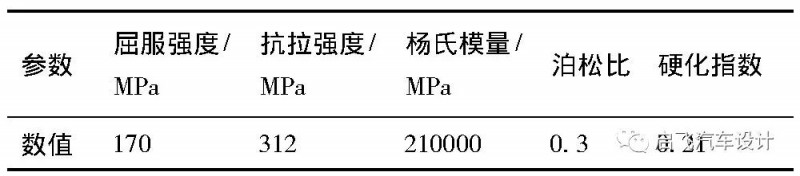
二、工藝參數(shù)優(yōu)化
零件回彈的影響因素較多, 包括材料參數(shù)和成形工藝參數(shù)。而當(dāng)零件的材料確定后, 材料參數(shù)已確定, 不能進(jìn)行更改, 因此, 為了降低成形后零件的回彈量, 對(duì)汽車后地板的成形工藝參數(shù)進(jìn)行優(yōu)化, 確定回彈量較小的工參數(shù)。
在對(duì)汽車沖壓件的回彈控制中, 得出影響零件回彈的主要工藝參數(shù)有壓邊力、模具間隙、摩擦系數(shù)。對(duì)于汽車后地板模具開發(fā)中, 最后凸凹要完全閉合, 因此, 在對(duì)汽車后地板的工藝參數(shù)優(yōu)化中主要考慮了成形過(guò)程中的壓邊力和摩擦系數(shù)。
工藝參數(shù)優(yōu)化借助Auto Form的西格瑪優(yōu)化模塊 (RE:Performance Analysis Design) , 該模塊用于沖壓工藝參數(shù)優(yōu)化。優(yōu)化分析的設(shè)計(jì)變量見表2。優(yōu)化分析中優(yōu)化目標(biāo)為零件的回彈量, 進(jìn)行30組模擬, 得到的模擬結(jié)果見圖2, 由圖2可知, 第24組為回彈最小的模擬組, 因此, 將該模擬組的參數(shù)作為最優(yōu)參數(shù)組合, 即最優(yōu)組的壓邊力為798k N, 摩擦系數(shù)為0.14。優(yōu)化后的零件的回彈分布如圖3所示, 圖3中采用橢圓圈出的區(qū)域A~D為該零件回彈較大的4個(gè)區(qū)域, 其中零件的最大回彈量為1.78 mm。
表2 優(yōu)化分析的設(shè)計(jì)變量
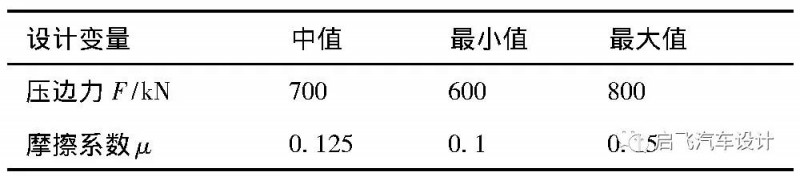
三、回彈補(bǔ)償
采用工藝參數(shù)優(yōu)化只能減小零件的回彈, 但不能完全控制零件的回彈量。因此, 接下來(lái)采用回彈補(bǔ)償方法來(lái)進(jìn)一步控制回彈。對(duì)拉延工序的模具進(jìn)行補(bǔ)償, 回彈補(bǔ)償方法如圖4所示, 將拉延模模面分為3個(gè)區(qū)域, 切邊線以內(nèi)區(qū)域定義為直接補(bǔ)償區(qū)域, 壓料面部分定義為固定補(bǔ)償區(qū)域, 壓料面和切邊線之間區(qū)域定義為過(guò)渡補(bǔ)償區(qū)域。采用Auto Form軟件進(jìn)行回彈補(bǔ)償, 當(dāng)回彈補(bǔ)償循環(huán)迭代2次后, 成形后零件的回彈滿足尺寸公差要求。第1次回彈補(bǔ)償后, 零件的回彈相對(duì)于未補(bǔ)償時(shí)回彈量有所降低, 圖3中4個(gè)橢圓區(qū)域A~D的最大回彈量分別為1.28, 1.14, 1.21和0.96 mm。第2次回彈補(bǔ)償后的零件的回彈分布如圖5所示, 4個(gè)橢圓區(qū)域A~D的最大回彈量分別為0.68, 0.63, 0.62和0.45mm。圖6為回彈補(bǔ)償前后的模面, 可以看出零件的型面補(bǔ)償主要在零件區(qū)域和過(guò)渡補(bǔ)償區(qū)域, 壓料面在補(bǔ)償前后未發(fā)生變化。
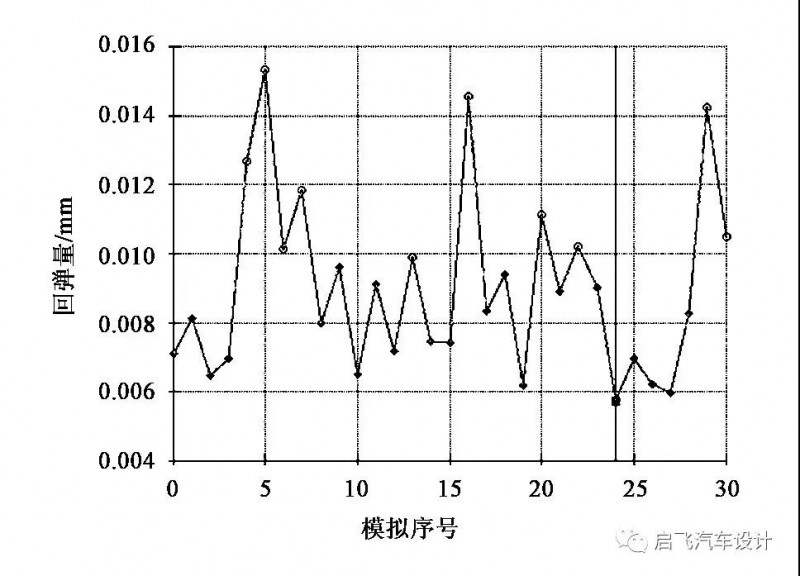
圖2 優(yōu)化分析的回彈結(jié)果
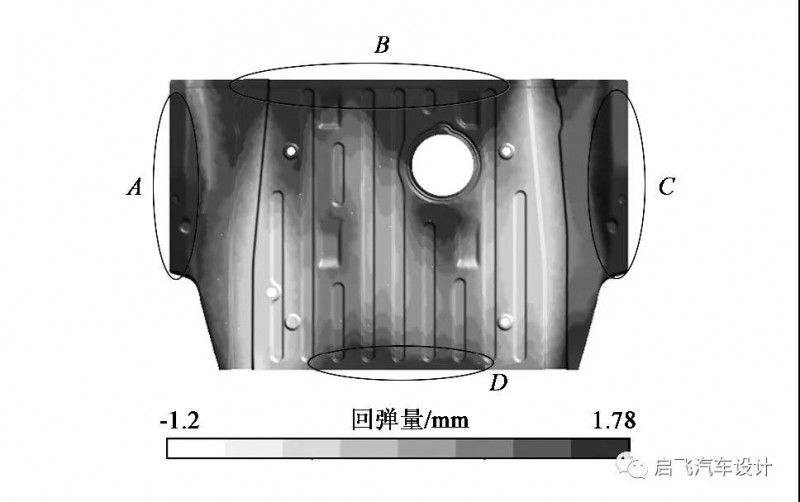
圖3 優(yōu)化后的零件的回彈分布
四、實(shí)驗(yàn)驗(yàn)證
為驗(yàn)證數(shù)值模擬結(jié)果進(jìn)行了模具加工和試模實(shí)驗(yàn), 得到試模零件如圖7所示。由圖7可知, 該零件成形充分, 無(wú)成形缺陷。采用模具檢具對(duì)零件進(jìn)行檢查, 重點(diǎn)測(cè)量圖3所示的4個(gè)橢圓區(qū)域, 得到橢圓區(qū)域A~D的最大回彈量分別為1.20, 0.96, 1.14和0.66 mm。由于零件的允許最大偏差為±0.7 mm, 因此, 還需要對(duì)超出區(qū)域進(jìn)行試模修改, 通過(guò)再一次對(duì)模具型面進(jìn)行修改加工, 最終得到零件的回彈偏差滿足零件尺寸要求。雖然本文提出的方法沒(méi)有達(dá)到一次控制零件的回彈, 但相對(duì)于傳統(tǒng)回彈補(bǔ)償方法, 能縮短試模調(diào)試時(shí)間, 降低模具成本。
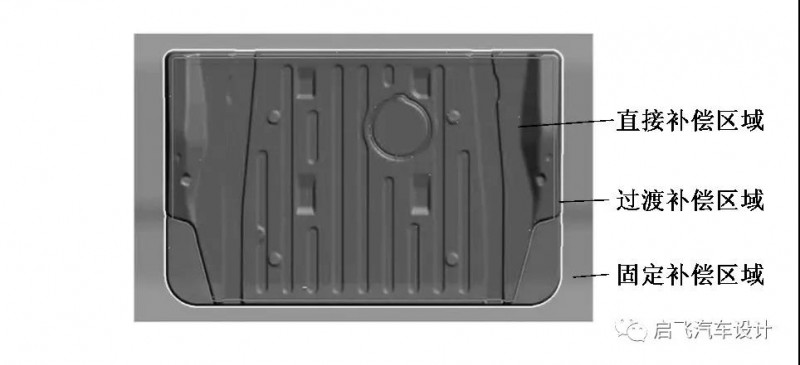
圖4 回彈補(bǔ)償策略
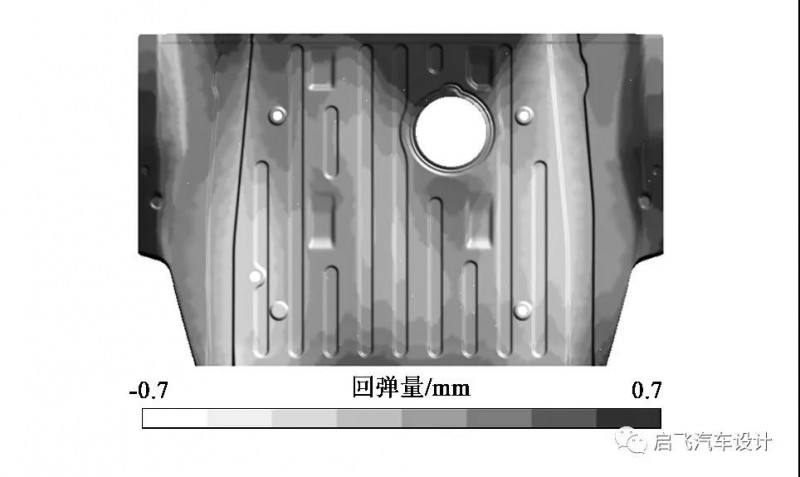
圖5 第2次回彈補(bǔ)償后的零件的回彈分布
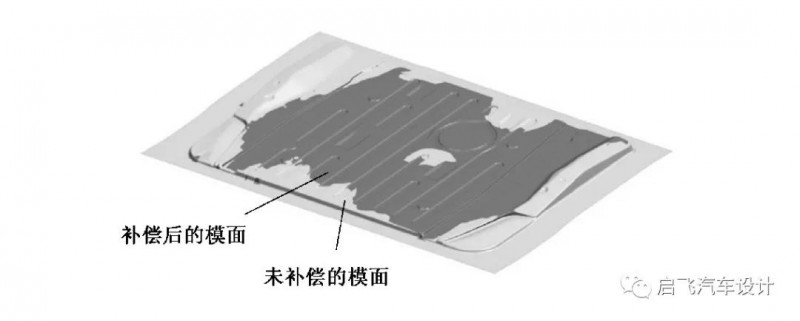
圖6 回彈補(bǔ)償前后的模面
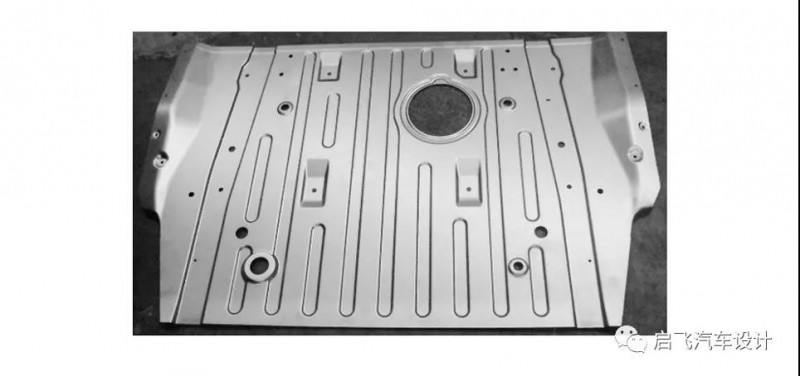
圖7 試模零件
五、結(jié)論
(1) 針對(duì)汽車沖壓件的回彈問(wèn)題, 借助數(shù)值模擬軟件Auto Form建立汽車后地板零件沖壓成形的全流程的有限元模型, 然后采用工藝參數(shù)優(yōu)化和回彈補(bǔ)償來(lái)控制該零件的回彈。
(2) 工藝參數(shù)優(yōu)化中得到最優(yōu)組的壓邊力為798 k N, 摩擦系數(shù)為0.14。采用回彈補(bǔ)償策略對(duì)拉延模具進(jìn)行回彈補(bǔ)償, 當(dāng)回彈補(bǔ)償循環(huán)迭代兩次后成形后零件的回彈滿足尺寸公差要求。
(3) 實(shí)驗(yàn)結(jié)果表明將工藝參數(shù)優(yōu)化和回彈補(bǔ)償相結(jié)合的方法能夠有效地控制零件的回彈, 縮短試模調(diào)試時(shí)間, 降低模具成本。
作者:茍春梅; 吳民; 董靜; 孫華偉
最新資訊
-
跨越速運(yùn)憑什么“圈粉”萬(wàn)千客戶?“
2025-07-01 14:42
-
數(shù)智破局啟新篇?生態(tài)共生再啟程 —
2025-06-27 20:13
-
助力汽車零部件產(chǎn)線智能化升級(jí),西門
2025-06-27 13:59
-
BBA集體轉(zhuǎn)向!放棄全面電動(dòng)化
2025-06-26 17:32
-
比換柜省錢,比自研省心,西門子X(jué)cel
2025-06-25 15:07