汽車加油口支架沖壓成形工藝分析探討
2018-07-26 16:12:18· 來源:汽車實(shí)用技術(shù)雜志社
加油口是典型的異形復(fù)雜件。頂部左邊面積小,右邊長而窄,且偏離中心,高度差大,周界輪廓右大左小,法蘭面是空間曲面。其成形工藝有兩種方案:一次成形,模具少,工序集中,但成形時(shí)自由懸空區(qū)大,易起皺、開裂; 分二次成形,多一道工序,但成形可靠性強(qiáng)。不管哪種方案,關(guān)鍵與難點(diǎn)都在第一道工序中。下面分別就第一道工序進(jìn)行模擬。
作者:張瑜,邱藝琪
單位:一汽轎車股份有限公司
1加油口沖壓成形數(shù)值模擬
加油口是典型的異形復(fù)雜件。頂部左邊面積小,右邊長而窄,且偏離中心,高度差大,周界輪廓右大左小,法蘭面是空間曲面。其成形工藝有兩種方案:一次成形,模具少,工序集中,但成形時(shí)自由懸空區(qū)大,易起皺、開裂; 分二次成形,多一道工序,但成形可靠性強(qiáng)。不管哪種方案,關(guān)鍵與難點(diǎn)都在第一道工序中。下面分別就第一道工序進(jìn)行模擬。
1.1 模擬基本參數(shù)
(1)材料特性
厚度0.7mm(寶鋼的BUFD;楊氏模量E=206MPa。
(2)工藝條件
摩擦系數(shù)f=0.15;壓邊力p=2.5MPa;沖壓速度v=8m/s;凸凹模間隙C=1.1t(t為材料厚度)。
(3)有限元模型
為盡量減少可能產(chǎn)生的數(shù)據(jù)錯(cuò)誤和丟失,在UG軟件中抽取數(shù)據(jù)并導(dǎo)出.iges格式文件,通過標(biāo)準(zhǔn)的iges數(shù)據(jù)轉(zhuǎn)換接口導(dǎo)AutoForm軟件中,采用BT殼單元對(duì)幾何模型進(jìn)行離散劃分網(wǎng)格,建立零件的有限元網(wǎng)格模型。
1.2 模擬過程
(1)選擇拉深類型:本零件的拉延過程采用單動(dòng)拉深。
(2)選擇沖壓方向:選擇沖壓方向,既可根據(jù)用戶的經(jīng)驗(yàn)和設(shè)備情況進(jìn)行確定,也可根據(jù)最小拉延深度、最小過切(UnderCut)等準(zhǔn)則自動(dòng)確定。
(3)創(chuàng)建壓料面與工藝補(bǔ)充:如果是已經(jīng)設(shè)計(jì)好的模具型面,可跳過壓料面和工藝補(bǔ)充面設(shè)計(jì)環(huán)節(jié),制定沖壓方向,確定工藝參數(shù)進(jìn)行有限元分析。如果輸入的僅僅是零件模型,在工件修改完成后,要進(jìn)行壓料面和工藝補(bǔ)充面的設(shè)計(jì)。用戶可讓系統(tǒng)生成參數(shù)化的壓料面和工藝補(bǔ)充面,然后制定沖壓方向,確定工藝參數(shù),在前在前處理中可完成多道工序模具和工藝參數(shù)的設(shè)定,一次性地進(jìn)行有限元模擬。
(4)參數(shù)修改:在有限元分析后,可根據(jù)需要對(duì)自動(dòng)生成的參數(shù)進(jìn)行修改,避免了返回通用 CAD 軟件進(jìn)行重新設(shè)計(jì),縮短了設(shè)計(jì)周期,降低了設(shè)計(jì)工作量。經(jīng)過若干次有限元模擬后,可獲得工藝性比較滿意的工件。
(5)最后通過修邊(Trim)模塊和優(yōu)化模塊對(duì)工藝參數(shù)進(jìn)行優(yōu)化。
1.3 模擬結(jié)果及工藝改進(jìn)
(1)一次成形工藝成形工序模擬結(jié)果
圖1為加油口一次成形工藝成形完成后的網(wǎng)格圖及 FLD 圖。一次成形自由懸空區(qū)大,在到底7mm左右步已產(chǎn)生內(nèi)皺,以后隨沖壓的進(jìn)行,這種皺紋進(jìn)一步加劇,在最后到底前5mm左右步已出現(xiàn)嚴(yán)重的折皺(有了第一次成型開裂的數(shù)據(jù),我們可以方便做出第一次成型的工藝面與第二次成型的工藝面的成型高度差),同時(shí)最薄弱的區(qū)域已破裂。這里破裂的產(chǎn)生一方面是由于這些區(qū)域產(chǎn)品形狀變化急劇,造成應(yīng)力集中;另一方面是由于因起皺而造成的局部拉應(yīng)力過大。若起皺不消除,破裂就很難消除。因此,這種方案沖壓成形是很困難的。
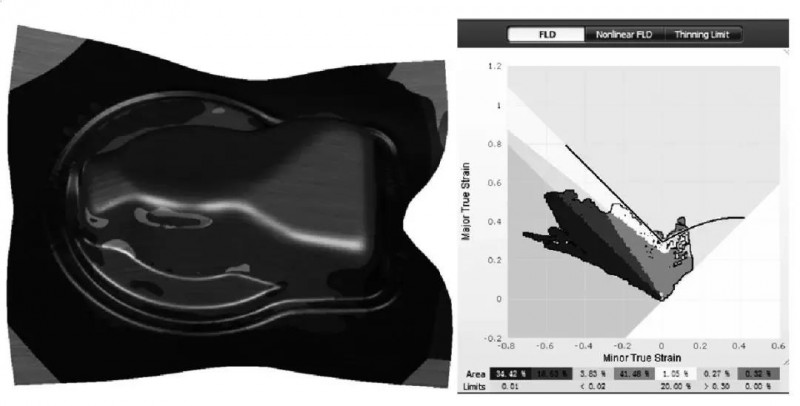
圖1
(2)二次成形工藝成形工序模擬結(jié)果
圖2為加油口二次成形工藝成形完成后的網(wǎng)格圖及 FLD圖。沖壓仍有皺紋和破裂,但程度比圖1改善了許多。其中起皺是主要問題,破裂是在到底前1-1.5mm步后才產(chǎn)生的。起皺很早就產(chǎn)生了,主要是成形件沿周邊進(jìn)料不均勻,局部區(qū)域起皺是因產(chǎn)品形狀拔模面變化急劇產(chǎn)生的。比較起來,二次成形工藝起皺程度減小,范圍也減?。缓裣驊?yīng)變減小,最大應(yīng)力值也減小,周邊材料流動(dòng)均勻,成形性能也有所改觀,但仍有破裂及起皺現(xiàn)象。因此決定采用兩次成形工藝方案,但相應(yīng)工藝參數(shù)還應(yīng)調(diào)整。
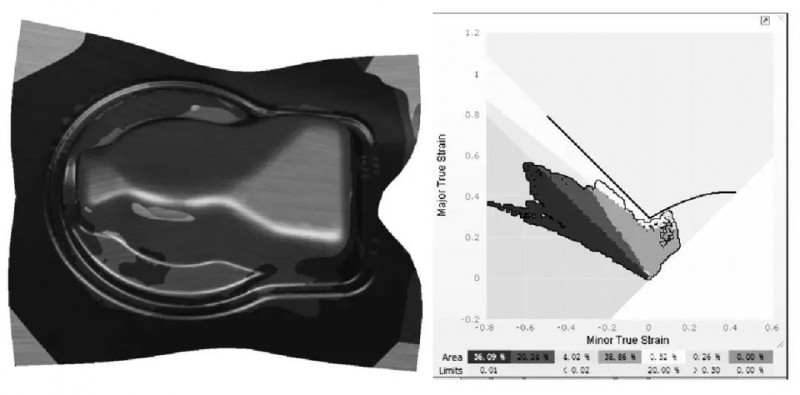
圖2
(3)成形工藝改進(jìn)
成形中,一旦產(chǎn)生了皺紋,并殘留在制件上,不僅使制件的尺寸精度、表面質(zhì)量等降低,而且也造成后續(xù)成形產(chǎn)生破裂。因此,在零件成形過程中,如何防止和消除皺紋,即成功的解決起皺問題,對(duì)獲得高質(zhì)量的產(chǎn)品至關(guān)重要。加油口起皺主要原因:坯料形狀不合理,沖件法蘭邊不均勻;產(chǎn)品局部形狀過渡劇烈;周邊因產(chǎn)品形狀不同,導(dǎo)致材料流動(dòng)不均勻。加油口的破裂既有塑性破裂,又有強(qiáng)度破裂。產(chǎn)品頸部的破裂是強(qiáng)度破裂,其他主要是在角部,是變形超過塑性而產(chǎn)生的塑性破裂。針對(duì)成形缺陷,主要采取如下措施: ①確定合理的坯料,實(shí)際生產(chǎn)中,為剪料的方便,常采用形狀料或者矩形件截角;②選擇合適的凹模圓角。前述工藝中,模具凹模圓角徑沿周邊取相同值,但由于成形形狀的不均勻性引起起皺。因此,模具凹模圓角半徑在材料流動(dòng)較慢的區(qū)域應(yīng)加大;③調(diào)整產(chǎn)品局部形狀。產(chǎn)品局部半徑需作調(diào)整,適當(dāng)加大。變動(dòng)的形狀在二序工序中整形回來??墒怯捎谟行┊a(chǎn)品的特殊性,本例子為例,看圖紙發(fā)現(xiàn)涂膠面與安裝孔相對(duì)要求比較高以外,其他面要求不高,可以與主機(jī)廠提“ECR”可以適當(dāng)優(yōu)化容易開裂地方,整改圓角與零件的拔模面。
(4)最后工藝改進(jìn)后模擬結(jié)果
圖3是工藝參數(shù)優(yōu)化后模擬的網(wǎng)格圖及FLD。除了局部料最小厚度為0.435mm,比原始厚度0.7mm薄25.6%,在許可范圍內(nèi)。其他單元對(duì)應(yīng)變形點(diǎn)都在安全區(qū)內(nèi)。到實(shí)際生產(chǎn)的時(shí)候,鉗工修磨局部圓角及模具表面的熱處理,方可以解決此類問題。
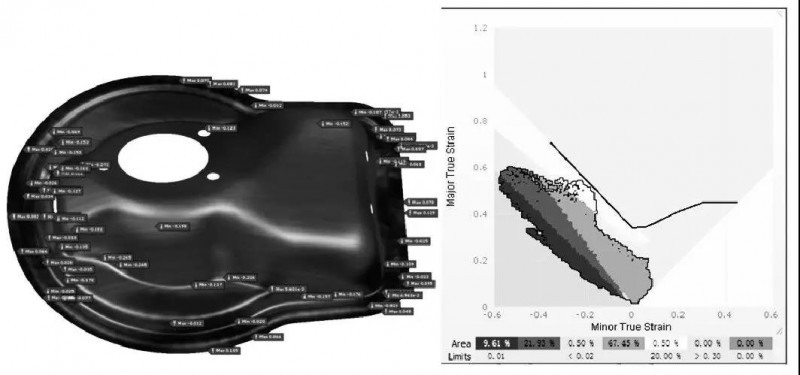
圖3
2實(shí)驗(yàn)結(jié)果
根據(jù)數(shù)值模擬結(jié)果制造模具。在調(diào)配模具時(shí),特別要求對(duì)圓角進(jìn)行研磨,盡量提高圓角部分光度,以提高材料流動(dòng)性。試模生產(chǎn)得到加油口產(chǎn)口輪廓清晰,經(jīng)檢測合格。
3結(jié)束語
基于Auotform軟件的板料仿真技術(shù),以某汽車覆蓋件為例,探討了從CAD工藝造型到CAE仿真分析的板料成形的全過程,預(yù)測了板料在成形過程中可能出現(xiàn)的成型缺陷,從而在模具制造前可以及時(shí)修改沖壓工藝方案,實(shí)現(xiàn)了覆蓋件拉深模設(shè)計(jì)及優(yōu)化,能有效地解決模擬后模具的形狀參數(shù)化調(diào)整問題,節(jié)省了大量時(shí)間成本,提高了設(shè)計(jì)的可靠性。
單位:一汽轎車股份有限公司
1加油口沖壓成形數(shù)值模擬
加油口是典型的異形復(fù)雜件。頂部左邊面積小,右邊長而窄,且偏離中心,高度差大,周界輪廓右大左小,法蘭面是空間曲面。其成形工藝有兩種方案:一次成形,模具少,工序集中,但成形時(shí)自由懸空區(qū)大,易起皺、開裂; 分二次成形,多一道工序,但成形可靠性強(qiáng)。不管哪種方案,關(guān)鍵與難點(diǎn)都在第一道工序中。下面分別就第一道工序進(jìn)行模擬。
1.1 模擬基本參數(shù)
(1)材料特性
厚度0.7mm(寶鋼的BUFD;楊氏模量E=206MPa。
(2)工藝條件
摩擦系數(shù)f=0.15;壓邊力p=2.5MPa;沖壓速度v=8m/s;凸凹模間隙C=1.1t(t為材料厚度)。
(3)有限元模型
為盡量減少可能產(chǎn)生的數(shù)據(jù)錯(cuò)誤和丟失,在UG軟件中抽取數(shù)據(jù)并導(dǎo)出.iges格式文件,通過標(biāo)準(zhǔn)的iges數(shù)據(jù)轉(zhuǎn)換接口導(dǎo)AutoForm軟件中,采用BT殼單元對(duì)幾何模型進(jìn)行離散劃分網(wǎng)格,建立零件的有限元網(wǎng)格模型。
1.2 模擬過程
(1)選擇拉深類型:本零件的拉延過程采用單動(dòng)拉深。
(2)選擇沖壓方向:選擇沖壓方向,既可根據(jù)用戶的經(jīng)驗(yàn)和設(shè)備情況進(jìn)行確定,也可根據(jù)最小拉延深度、最小過切(UnderCut)等準(zhǔn)則自動(dòng)確定。
(3)創(chuàng)建壓料面與工藝補(bǔ)充:如果是已經(jīng)設(shè)計(jì)好的模具型面,可跳過壓料面和工藝補(bǔ)充面設(shè)計(jì)環(huán)節(jié),制定沖壓方向,確定工藝參數(shù)進(jìn)行有限元分析。如果輸入的僅僅是零件模型,在工件修改完成后,要進(jìn)行壓料面和工藝補(bǔ)充面的設(shè)計(jì)。用戶可讓系統(tǒng)生成參數(shù)化的壓料面和工藝補(bǔ)充面,然后制定沖壓方向,確定工藝參數(shù),在前在前處理中可完成多道工序模具和工藝參數(shù)的設(shè)定,一次性地進(jìn)行有限元模擬。
(4)參數(shù)修改:在有限元分析后,可根據(jù)需要對(duì)自動(dòng)生成的參數(shù)進(jìn)行修改,避免了返回通用 CAD 軟件進(jìn)行重新設(shè)計(jì),縮短了設(shè)計(jì)周期,降低了設(shè)計(jì)工作量。經(jīng)過若干次有限元模擬后,可獲得工藝性比較滿意的工件。
(5)最后通過修邊(Trim)模塊和優(yōu)化模塊對(duì)工藝參數(shù)進(jìn)行優(yōu)化。
1.3 模擬結(jié)果及工藝改進(jìn)
(1)一次成形工藝成形工序模擬結(jié)果
圖1為加油口一次成形工藝成形完成后的網(wǎng)格圖及 FLD 圖。一次成形自由懸空區(qū)大,在到底7mm左右步已產(chǎn)生內(nèi)皺,以后隨沖壓的進(jìn)行,這種皺紋進(jìn)一步加劇,在最后到底前5mm左右步已出現(xiàn)嚴(yán)重的折皺(有了第一次成型開裂的數(shù)據(jù),我們可以方便做出第一次成型的工藝面與第二次成型的工藝面的成型高度差),同時(shí)最薄弱的區(qū)域已破裂。這里破裂的產(chǎn)生一方面是由于這些區(qū)域產(chǎn)品形狀變化急劇,造成應(yīng)力集中;另一方面是由于因起皺而造成的局部拉應(yīng)力過大。若起皺不消除,破裂就很難消除。因此,這種方案沖壓成形是很困難的。
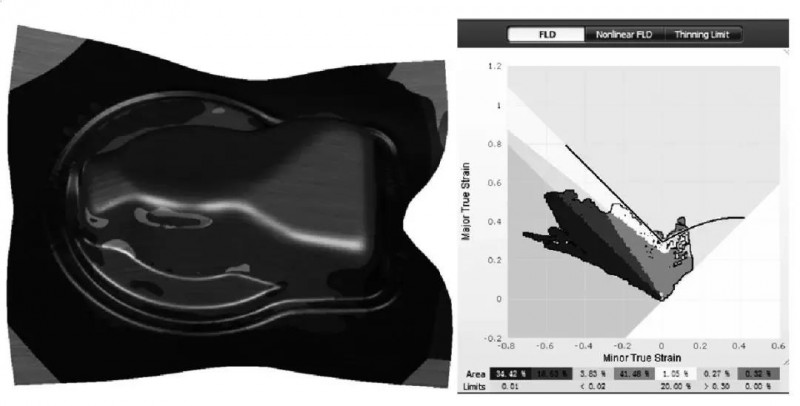
圖1
(2)二次成形工藝成形工序模擬結(jié)果
圖2為加油口二次成形工藝成形完成后的網(wǎng)格圖及 FLD圖。沖壓仍有皺紋和破裂,但程度比圖1改善了許多。其中起皺是主要問題,破裂是在到底前1-1.5mm步后才產(chǎn)生的。起皺很早就產(chǎn)生了,主要是成形件沿周邊進(jìn)料不均勻,局部區(qū)域起皺是因產(chǎn)品形狀拔模面變化急劇產(chǎn)生的。比較起來,二次成形工藝起皺程度減小,范圍也減?。缓裣驊?yīng)變減小,最大應(yīng)力值也減小,周邊材料流動(dòng)均勻,成形性能也有所改觀,但仍有破裂及起皺現(xiàn)象。因此決定采用兩次成形工藝方案,但相應(yīng)工藝參數(shù)還應(yīng)調(diào)整。
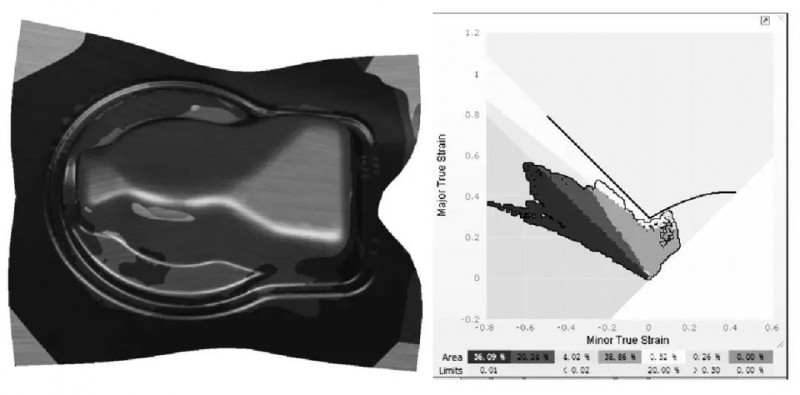
圖2
(3)成形工藝改進(jìn)
成形中,一旦產(chǎn)生了皺紋,并殘留在制件上,不僅使制件的尺寸精度、表面質(zhì)量等降低,而且也造成后續(xù)成形產(chǎn)生破裂。因此,在零件成形過程中,如何防止和消除皺紋,即成功的解決起皺問題,對(duì)獲得高質(zhì)量的產(chǎn)品至關(guān)重要。加油口起皺主要原因:坯料形狀不合理,沖件法蘭邊不均勻;產(chǎn)品局部形狀過渡劇烈;周邊因產(chǎn)品形狀不同,導(dǎo)致材料流動(dòng)不均勻。加油口的破裂既有塑性破裂,又有強(qiáng)度破裂。產(chǎn)品頸部的破裂是強(qiáng)度破裂,其他主要是在角部,是變形超過塑性而產(chǎn)生的塑性破裂。針對(duì)成形缺陷,主要采取如下措施: ①確定合理的坯料,實(shí)際生產(chǎn)中,為剪料的方便,常采用形狀料或者矩形件截角;②選擇合適的凹模圓角。前述工藝中,模具凹模圓角徑沿周邊取相同值,但由于成形形狀的不均勻性引起起皺。因此,模具凹模圓角半徑在材料流動(dòng)較慢的區(qū)域應(yīng)加大;③調(diào)整產(chǎn)品局部形狀。產(chǎn)品局部半徑需作調(diào)整,適當(dāng)加大。變動(dòng)的形狀在二序工序中整形回來??墒怯捎谟行┊a(chǎn)品的特殊性,本例子為例,看圖紙發(fā)現(xiàn)涂膠面與安裝孔相對(duì)要求比較高以外,其他面要求不高,可以與主機(jī)廠提“ECR”可以適當(dāng)優(yōu)化容易開裂地方,整改圓角與零件的拔模面。
(4)最后工藝改進(jìn)后模擬結(jié)果
圖3是工藝參數(shù)優(yōu)化后模擬的網(wǎng)格圖及FLD。除了局部料最小厚度為0.435mm,比原始厚度0.7mm薄25.6%,在許可范圍內(nèi)。其他單元對(duì)應(yīng)變形點(diǎn)都在安全區(qū)內(nèi)。到實(shí)際生產(chǎn)的時(shí)候,鉗工修磨局部圓角及模具表面的熱處理,方可以解決此類問題。
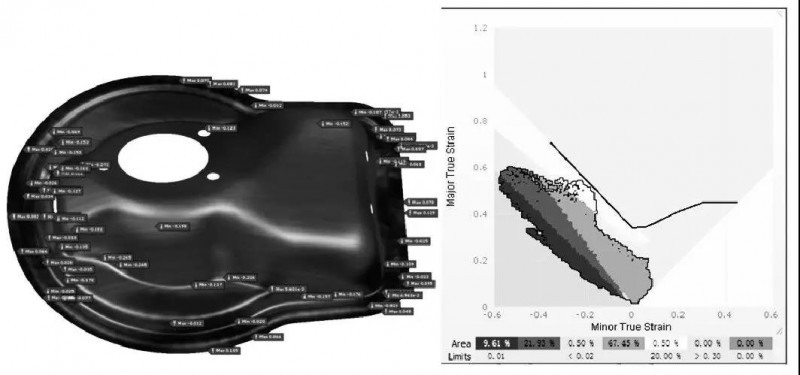
圖3
2實(shí)驗(yàn)結(jié)果
根據(jù)數(shù)值模擬結(jié)果制造模具。在調(diào)配模具時(shí),特別要求對(duì)圓角進(jìn)行研磨,盡量提高圓角部分光度,以提高材料流動(dòng)性。試模生產(chǎn)得到加油口產(chǎn)口輪廓清晰,經(jīng)檢測合格。
3結(jié)束語
基于Auotform軟件的板料仿真技術(shù),以某汽車覆蓋件為例,探討了從CAD工藝造型到CAE仿真分析的板料成形的全過程,預(yù)測了板料在成形過程中可能出現(xiàn)的成型缺陷,從而在模具制造前可以及時(shí)修改沖壓工藝方案,實(shí)現(xiàn)了覆蓋件拉深模設(shè)計(jì)及優(yōu)化,能有效地解決模擬后模具的形狀參數(shù)化調(diào)整問題,節(jié)省了大量時(shí)間成本,提高了設(shè)計(jì)的可靠性。
最新資訊
-
跨越速運(yùn)憑什么“圈粉”萬千客戶?“
2025-07-01 14:42
-
數(shù)智破局啟新篇?生態(tài)共生再啟程 —
2025-06-27 20:13
-
助力汽車零部件產(chǎn)線智能化升級(jí),西門
2025-06-27 13:59
-
BBA集體轉(zhuǎn)向!放棄全面電動(dòng)化
2025-06-26 17:32
-
比換柜省錢,比自研省心,西門子Xcel
2025-06-25 15:07