OptiStruct在變速器殼體優(yōu)化設計中的應用
2018-07-16 09:37:44· 來源:Altair仿真驅動設計
為了縮短變速器殼體設計周期,提高殼體的性能,并實現殼體輕量化的目標。結合現有結構優(yōu)化方法,不斷地對模型進行優(yōu)化分析,使殼體材料分布達到最優(yōu)狀態(tài)。本文主要利用Altair OptiStruct 軟件中的拓撲優(yōu)化,根據給定的邊界條件、約束條件和目標值,結合變速器實際工況與殼體制造工藝方法,完成殼體的優(yōu)化設計,實現殼體減重1.5Kg,解決局部等效應力超過屈服強度問題,并使一階模態(tài)達到1000以上的目標。
OptiStruct在變速器殼體優(yōu)化設計中的應用
史元元1,2,劉玉蒙1,2,冉昭1,2
( 1.長城汽車股份有限公司技術中心
2.河北省汽車工程技術研究中心 )
摘 要: 為了縮短變速器殼體設計周期,提高殼體的性能,并實現殼體輕量化的目標。結合現有結構優(yōu)化方法,不斷地對模型進行優(yōu)化分析,使殼體材料分布達到最優(yōu)狀態(tài)。本文主要利用Altair OptiStruct 軟件中的拓撲優(yōu)化,根據給定的邊界條件、約束條件和目標值,結合變速器實際工況與殼體制造工藝方法,完成殼體的優(yōu)化設計,實現殼體減重1.5Kg,解決局部等效應力超過屈服強度問題,并使一階模態(tài)達到1000以上的目標。
概 述
近些年來,節(jié)能減排降油耗已經成為汽車行業(yè)發(fā)展的大趨勢,零部件的輕量化設計成為各個車企實現降低油耗的重要措施之一。通過降低汽車本身的重量,提高汽車的燃油經濟性、節(jié)約能耗、減少污染。我司設計人員在不影響汽車的安全性、抗振性以及舒適性的工況下,利用拓撲優(yōu)化方法,對變速器殼體及零部件進行優(yōu)化再設計,既保證了良好使用性能,又實現了變速器殼體輕量化設計。
機構拓撲優(yōu)化設計,開展于概念設計早期,主要研究結構材料布局,由于拓撲優(yōu)化的結果決定了產品的最優(yōu)拓撲,即決定了產品的最終形狀與性能,因此在殼體輕量化設計中大量應用拓撲優(yōu)化技術,可以在很大程度上保證殼體結構設計,后續(xù)的尺寸和形狀優(yōu)化是在材料分布最優(yōu)初始拓撲形式下進行的,能夠極大提高材料利用率。
優(yōu)化前模型的確認
1殼體材料屬性
該變速器殼體的材料為鑄鋁,并采用高壓鑄造工藝,其彈性模量E=72GPa,泊松比μ=0.3,密度為ρ=2.7╳103Kg/m3,屈服強度為160MPa,抗拉極限為270MPa。
2工況及加載驗證
本文綜合考慮了殼體的剛度曲線、箱內軸的擾度、齒輪參數等因素,依據力的平衡和力偶平衡,依據發(fā)動機輸出扭矩計算出在不同擋位時殼體上各個軸承座處受的載荷(力和力矩)。
首先通過OptiStruct軟件完成優(yōu)化前殼體模型的仿真分析。主要對其質量、強度、剛度進行分析確認,確保殼體優(yōu)化前后性能不變,同時為優(yōu)化提供目標值與約束值。
優(yōu)化原模型
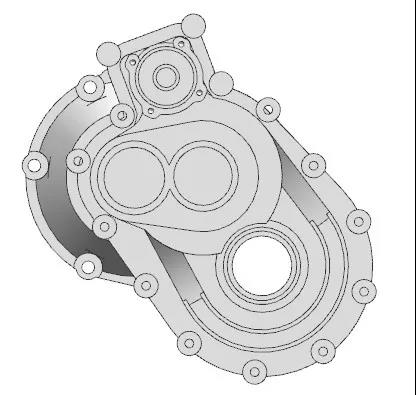

通過仿真分析得到,殼體的等效應力為180MPa,大于殼體材料的屈服強度,一階模態(tài)為680Hz小于1000Hz,故原模型在性能上不滿足設計要求。
優(yōu)化模型的建立
1可設計空間的提取
首先對變速器殼體的可設計空間進行提取,盡量使殼體在進行優(yōu)化前的模型最大程度的充滿設計空間,并且保證殼體與內外零部件的動靜態(tài)連接關系,避免發(fā)生干涉,影響到內外零部件的安裝與工作,除此之外拓撲優(yōu)化使用的模型應滿足結構的制造工藝性,避免后期無法加工制造的問題。對原模型進行可設計空間提取,給出優(yōu)化前最大材料可利用空間,具體如圖所示。
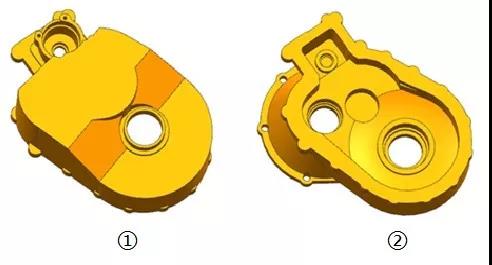
減速器殼體拓撲優(yōu)化模型
2優(yōu)化模型加載及優(yōu)化設置
與優(yōu)化前殼體模型相同,對優(yōu)化模型進行加載,并在加載后完成變量、優(yōu)化響應、約束和目標值得建立。本次優(yōu)化將殼體優(yōu)化模型根據加工制造工藝可行性問題的要求分為多個子優(yōu)化空間進行變量的設置,使優(yōu)化結果更便于加工制造。
將優(yōu)化區(qū)域中每個子區(qū)域分別設置為變量,根據不同部位設計使用不同的拔模方向,循環(huán)對稱數等加工制造約束。
在優(yōu)化過程中,模型響應將會直接影響到優(yōu)化結果是否合理,是否滿足設計要求。本次優(yōu)化模型響應選擇的是體積分數,靜態(tài)位移,靜態(tài)應力、頻率和柔度,在此需要指出的是,由于本次為靜動態(tài)相結合的結構拓撲優(yōu)化,采用的柔度響應為組合柔度指數。
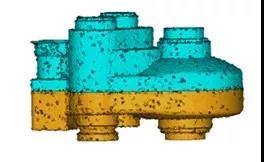
非優(yōu)化區(qū)域
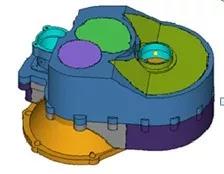
優(yōu)化區(qū)域
3優(yōu)化結果
對于具有復雜結構的殼體,我們一般通過兩個方面對其進行優(yōu)化設計,第一步通過簡單的工程制造約束參數設置,分析得到殼體表面基本的結構;第二步通過細致的工藝制造約束參數的設置,得到殼體表面加強筋的布置結果,最終兩者相結合,得到符合設計要求且性能良好且美觀的殼體結構。通過仿真計算與模型的的調整,最終得到優(yōu)化結果云圖如圖所示:
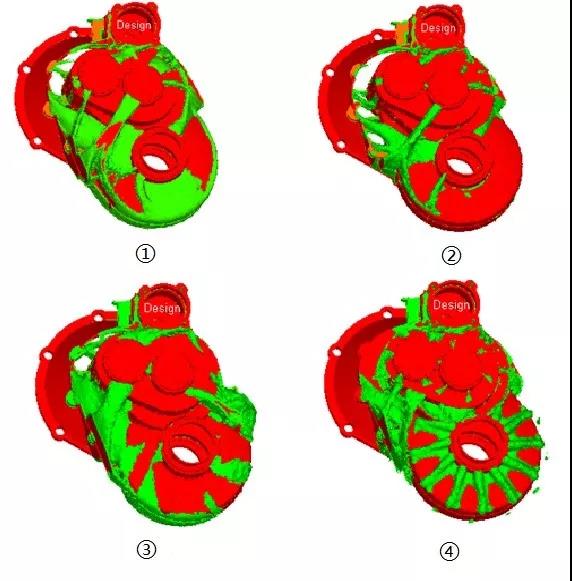
① 1擋工況優(yōu)化結果;②2擋工況優(yōu)化結果
③1擋反拖優(yōu)化結果;④所有工況綜合優(yōu)化結果
通過上圖的對比可以看出,單一擋位重點部位材料的布局形式在多擋位結合是材料的布局上均有體現,因此為了得到良好的剛度、強度、NVH性能,通常我們會以多擋位工況結合的優(yōu)化結果作為殼體整體的分布,但是拓撲優(yōu)化結果通常只是作為結構設計的指導方向,因為優(yōu)化結果大多比較粗糙(如殼體壁厚尺寸過大或部分材料的缺失),因此這僅能作為參考。
優(yōu)化后殼體設計與驗證分析
1優(yōu)化結果
根據優(yōu)化后結果與殼體設計原則[5]通過3D建模軟件完成殼體的優(yōu)化后模型的建立,模型如所示:
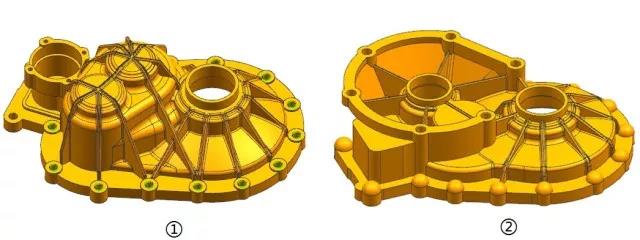
2結果分析驗證
在完成殼體再設計之后,需對優(yōu)化后的模型進行分析驗證,主要從質量、強度、剛度三方面進行驗證并與原方案對比。
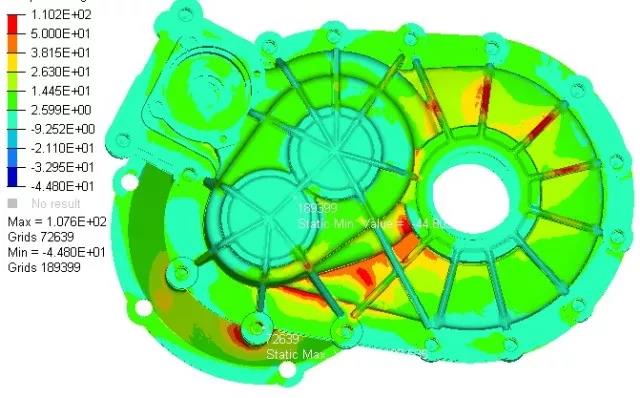
①殼體最大主應力云圖
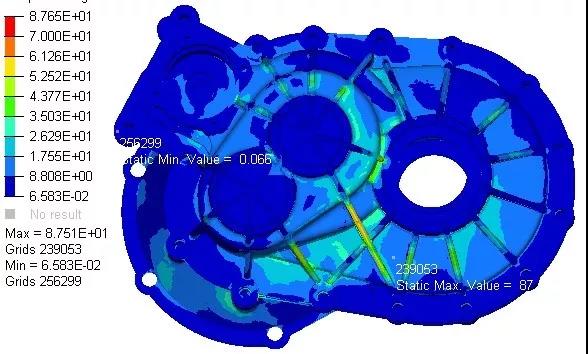
②殼體等效應力云圖
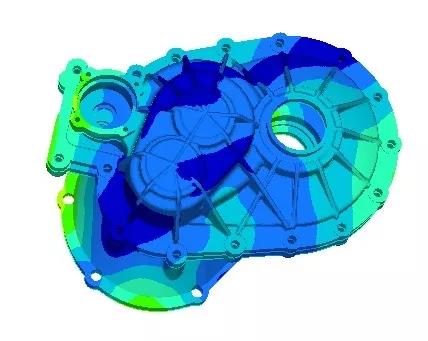
③殼體一階模態(tài)振型
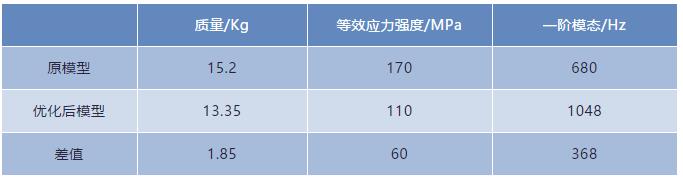
通過過上表對比,可以得到,本次優(yōu)化后殼體質量比原模型減少了1.85Kg,等效應力為110MPa小于原殼體模型的等效應力170MPa,一階模態(tài)為1048Hz達到設計目標,因此本次優(yōu)化在在提升了殼體原有性能的前提下實現了輕量化設計。
結 論
1、通過OptiStruct軟件完成了殼體強量化要求,減重1.85Kg,實現了公司減重目標。
2、通過拓撲優(yōu)化設計提高了材料的利用率,減少冗余復雜結構,從而降低材料成本;同時保證了殼體工藝制造的最佳工藝性,提高了模具使用壽命,降低模具成本;
3、在殼體設計初期充分考慮殼體結構的剛度、強度、模態(tài)等方面,避免重復修改等大量工作,有助于提高設計人員的工作效率,縮短了殼體開發(fā)周期,降低開發(fā)成本;
4、本文未考慮殼體噪音問題,將結合后期相應標準,對殼體噪音質量問題進行提高改善。
2018年8月30-31日,2018 Altair 結構仿真與優(yōu)化技術暨OptiStruct用戶大會將在青島舉行。
8月30日為全體大會,將由各行業(yè)專家分享主題報告;8月31日設置分會場,包含汽車及地面交通、航空航天、電子電器、能源與重工、白色家電等專題,技術內容將涉及結構優(yōu)化、剛度、強度和穩(wěn)定性、噪聲和振動、動力總成系統(tǒng)疲勞、運動學和動力學、熱傳遞分析和復合材料等。
會議同期還將舉辦PBS Works用戶大會,將就HPC最新技術和趨勢、HPC管理套件在業(yè)務流程中的位置探討、公有云應用等方面開展深入交流。
史元元1,2,劉玉蒙1,2,冉昭1,2
( 1.長城汽車股份有限公司技術中心
2.河北省汽車工程技術研究中心 )
摘 要: 為了縮短變速器殼體設計周期,提高殼體的性能,并實現殼體輕量化的目標。結合現有結構優(yōu)化方法,不斷地對模型進行優(yōu)化分析,使殼體材料分布達到最優(yōu)狀態(tài)。本文主要利用Altair OptiStruct 軟件中的拓撲優(yōu)化,根據給定的邊界條件、約束條件和目標值,結合變速器實際工況與殼體制造工藝方法,完成殼體的優(yōu)化設計,實現殼體減重1.5Kg,解決局部等效應力超過屈服強度問題,并使一階模態(tài)達到1000以上的目標。
概 述
近些年來,節(jié)能減排降油耗已經成為汽車行業(yè)發(fā)展的大趨勢,零部件的輕量化設計成為各個車企實現降低油耗的重要措施之一。通過降低汽車本身的重量,提高汽車的燃油經濟性、節(jié)約能耗、減少污染。我司設計人員在不影響汽車的安全性、抗振性以及舒適性的工況下,利用拓撲優(yōu)化方法,對變速器殼體及零部件進行優(yōu)化再設計,既保證了良好使用性能,又實現了變速器殼體輕量化設計。
機構拓撲優(yōu)化設計,開展于概念設計早期,主要研究結構材料布局,由于拓撲優(yōu)化的結果決定了產品的最優(yōu)拓撲,即決定了產品的最終形狀與性能,因此在殼體輕量化設計中大量應用拓撲優(yōu)化技術,可以在很大程度上保證殼體結構設計,后續(xù)的尺寸和形狀優(yōu)化是在材料分布最優(yōu)初始拓撲形式下進行的,能夠極大提高材料利用率。
優(yōu)化前模型的確認
1殼體材料屬性
該變速器殼體的材料為鑄鋁,并采用高壓鑄造工藝,其彈性模量E=72GPa,泊松比μ=0.3,密度為ρ=2.7╳103Kg/m3,屈服強度為160MPa,抗拉極限為270MPa。
2工況及加載驗證
本文綜合考慮了殼體的剛度曲線、箱內軸的擾度、齒輪參數等因素,依據力的平衡和力偶平衡,依據發(fā)動機輸出扭矩計算出在不同擋位時殼體上各個軸承座處受的載荷(力和力矩)。
首先通過OptiStruct軟件完成優(yōu)化前殼體模型的仿真分析。主要對其質量、強度、剛度進行分析確認,確保殼體優(yōu)化前后性能不變,同時為優(yōu)化提供目標值與約束值。
優(yōu)化原模型
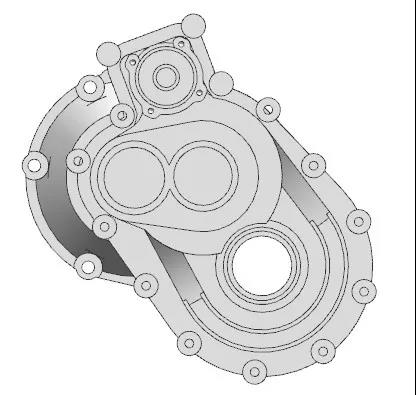

通過仿真分析得到,殼體的等效應力為180MPa,大于殼體材料的屈服強度,一階模態(tài)為680Hz小于1000Hz,故原模型在性能上不滿足設計要求。
優(yōu)化模型的建立
1可設計空間的提取
首先對變速器殼體的可設計空間進行提取,盡量使殼體在進行優(yōu)化前的模型最大程度的充滿設計空間,并且保證殼體與內外零部件的動靜態(tài)連接關系,避免發(fā)生干涉,影響到內外零部件的安裝與工作,除此之外拓撲優(yōu)化使用的模型應滿足結構的制造工藝性,避免后期無法加工制造的問題。對原模型進行可設計空間提取,給出優(yōu)化前最大材料可利用空間,具體如圖所示。
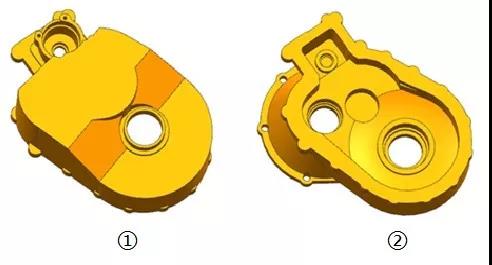
減速器殼體拓撲優(yōu)化模型
2優(yōu)化模型加載及優(yōu)化設置
與優(yōu)化前殼體模型相同,對優(yōu)化模型進行加載,并在加載后完成變量、優(yōu)化響應、約束和目標值得建立。本次優(yōu)化將殼體優(yōu)化模型根據加工制造工藝可行性問題的要求分為多個子優(yōu)化空間進行變量的設置,使優(yōu)化結果更便于加工制造。
將優(yōu)化區(qū)域中每個子區(qū)域分別設置為變量,根據不同部位設計使用不同的拔模方向,循環(huán)對稱數等加工制造約束。
在優(yōu)化過程中,模型響應將會直接影響到優(yōu)化結果是否合理,是否滿足設計要求。本次優(yōu)化模型響應選擇的是體積分數,靜態(tài)位移,靜態(tài)應力、頻率和柔度,在此需要指出的是,由于本次為靜動態(tài)相結合的結構拓撲優(yōu)化,采用的柔度響應為組合柔度指數。
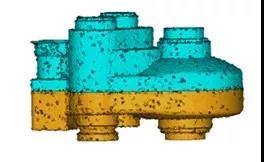
非優(yōu)化區(qū)域
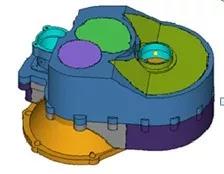
優(yōu)化區(qū)域
3優(yōu)化結果
對于具有復雜結構的殼體,我們一般通過兩個方面對其進行優(yōu)化設計,第一步通過簡單的工程制造約束參數設置,分析得到殼體表面基本的結構;第二步通過細致的工藝制造約束參數的設置,得到殼體表面加強筋的布置結果,最終兩者相結合,得到符合設計要求且性能良好且美觀的殼體結構。通過仿真計算與模型的的調整,最終得到優(yōu)化結果云圖如圖所示:
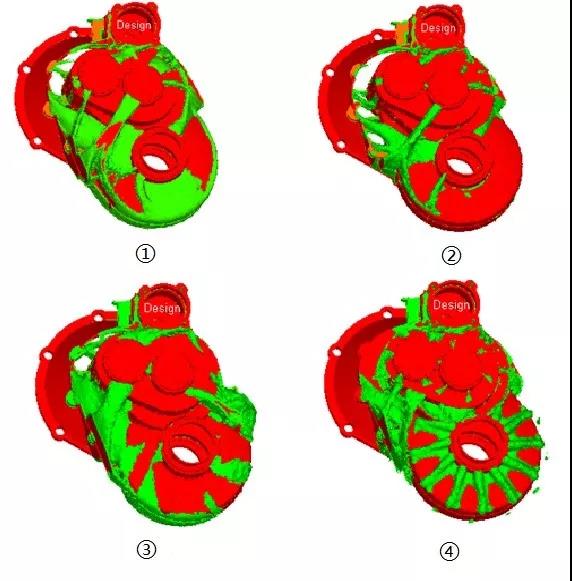
① 1擋工況優(yōu)化結果;②2擋工況優(yōu)化結果
③1擋反拖優(yōu)化結果;④所有工況綜合優(yōu)化結果
通過上圖的對比可以看出,單一擋位重點部位材料的布局形式在多擋位結合是材料的布局上均有體現,因此為了得到良好的剛度、強度、NVH性能,通常我們會以多擋位工況結合的優(yōu)化結果作為殼體整體的分布,但是拓撲優(yōu)化結果通常只是作為結構設計的指導方向,因為優(yōu)化結果大多比較粗糙(如殼體壁厚尺寸過大或部分材料的缺失),因此這僅能作為參考。
優(yōu)化后殼體設計與驗證分析
1優(yōu)化結果
根據優(yōu)化后結果與殼體設計原則[5]通過3D建模軟件完成殼體的優(yōu)化后模型的建立,模型如所示:
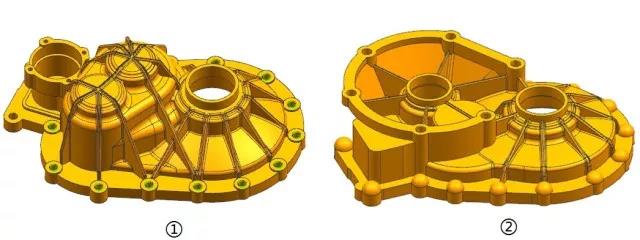
2結果分析驗證
在完成殼體再設計之后,需對優(yōu)化后的模型進行分析驗證,主要從質量、強度、剛度三方面進行驗證并與原方案對比。
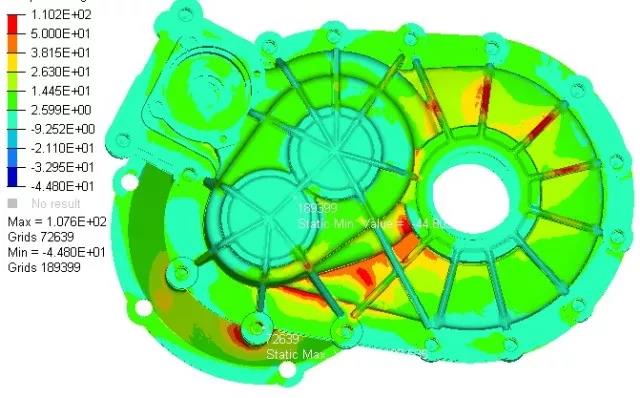
①殼體最大主應力云圖
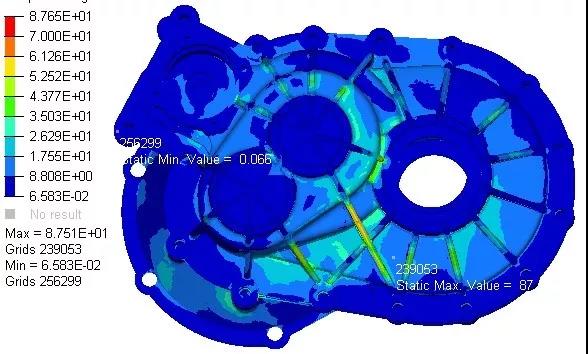
②殼體等效應力云圖
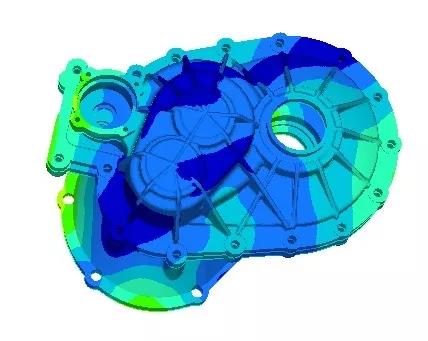
③殼體一階模態(tài)振型
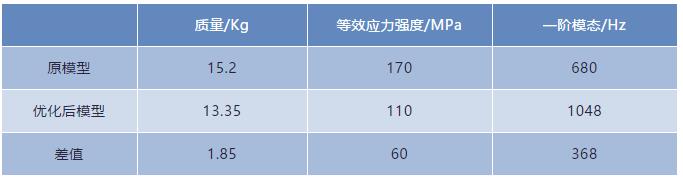
通過過上表對比,可以得到,本次優(yōu)化后殼體質量比原模型減少了1.85Kg,等效應力為110MPa小于原殼體模型的等效應力170MPa,一階模態(tài)為1048Hz達到設計目標,因此本次優(yōu)化在在提升了殼體原有性能的前提下實現了輕量化設計。
結 論
1、通過OptiStruct軟件完成了殼體強量化要求,減重1.85Kg,實現了公司減重目標。
2、通過拓撲優(yōu)化設計提高了材料的利用率,減少冗余復雜結構,從而降低材料成本;同時保證了殼體工藝制造的最佳工藝性,提高了模具使用壽命,降低模具成本;
3、在殼體設計初期充分考慮殼體結構的剛度、強度、模態(tài)等方面,避免重復修改等大量工作,有助于提高設計人員的工作效率,縮短了殼體開發(fā)周期,降低開發(fā)成本;
4、本文未考慮殼體噪音問題,將結合后期相應標準,對殼體噪音質量問題進行提高改善。
2018年8月30-31日,2018 Altair 結構仿真與優(yōu)化技術暨OptiStruct用戶大會將在青島舉行。
8月30日為全體大會,將由各行業(yè)專家分享主題報告;8月31日設置分會場,包含汽車及地面交通、航空航天、電子電器、能源與重工、白色家電等專題,技術內容將涉及結構優(yōu)化、剛度、強度和穩(wěn)定性、噪聲和振動、動力總成系統(tǒng)疲勞、運動學和動力學、熱傳遞分析和復合材料等。
會議同期還將舉辦PBS Works用戶大會,將就HPC最新技術和趨勢、HPC管理套件在業(yè)務流程中的位置探討、公有云應用等方面開展深入交流。
編輯推薦
最新資訊
-
跨越速運憑什么“圈粉”萬千客戶?“
2025-07-01 14:42
-
數智破局啟新篇?生態(tài)共生再啟程 —
2025-06-27 20:13
-
助力汽車零部件產線智能化升級,西門
2025-06-27 13:59
-
BBA集體轉向!放棄全面電動化
2025-06-26 17:32
-
比換柜省錢,比自研省心,西門子Xcel
2025-06-25 15:07