碳纖維復(fù)合材料翼子板在某車型上的應(yīng)用
2018-06-21 10:26:01· 來源:汽車實(shí)用技術(shù)雜志社
汽車輕量化是實(shí)現(xiàn)汽車節(jié)能減排的重要途徑,已成為世界汽車發(fā)展的潮流,研究表明,汽油乘用車每減重100kg將節(jié)油0.39L/100km,汽車質(zhì)量每降低10%,可降低油耗6%~8%,排放下降4%。各大主機(jī)廠已紛紛采取不同技術(shù)降低汽車整備質(zhì)量,其中以復(fù)合材料代替鋼板材料成為輕量化技術(shù)的重要發(fā)展方向,目前應(yīng)用在汽車零部件的復(fù)合材料主要有碳纖維和玻璃纖維兩大類,碳纖維復(fù)合材料擁有絕佳的任性和抗拉強(qiáng)度,其密度在1.45~1.6g/cm3,拉伸強(qiáng)度可達(dá)1.5GPa以上,超過鋁合金的3倍,接近超高強(qiáng)度鋼的水平。碳纖維復(fù)合材
作者:王雪爭
單位:華晨汽車工程研究能量管理室
前言
汽車輕量化是實(shí)現(xiàn)汽車節(jié)能減排的重要途徑,已成為世界汽車發(fā)展的潮流,研究表明,汽油乘用車每減重100kg將節(jié)油0.39L/100km,汽車質(zhì)量每降低10%,可降低油耗6%~8%,排放下降4%。各大主機(jī)廠已紛紛采取不同技術(shù)降低汽車整備質(zhì)量,其中以復(fù)合材料代替鋼板材料成為輕量化技術(shù)的重要發(fā)展方向,目前應(yīng)用在汽車零部件的復(fù)合材料主要有碳纖維和玻璃纖維兩大類,碳纖維復(fù)合材料擁有絕佳的任性和抗拉強(qiáng)度,其密度在1.45~1.6g/cm³,拉伸強(qiáng)度可達(dá)1.5GPa以上,超過鋁合金的3倍,接近超高強(qiáng)度鋼的水平。碳纖維復(fù)合材料翼子板在保證普通鋼板材料翼子板性能外減重約50%,有效的降低汽車整備質(zhì)量達(dá)到節(jié)能減排目的。
1 碳纖維復(fù)合材料應(yīng)用到汽車上的優(yōu)勢
碳纖維復(fù)合材料零部件已成為各大主機(jī)廠重要發(fā)展方向,其應(yīng)用到汽車上的七大優(yōu)勢如下:
a)輕量化:提高車體本身性能,減重50%,節(jié)能省油;
b)安全性:同等體積,碳纖維本身拉伸強(qiáng)度是鋼板材料的7-9倍,能最大減少傳到駕駛室的能量;
c)抗疲勞性:碳纖維較細(xì),缺陷少,機(jī)體塑形好,可以抑制裂紋發(fā)展,具有良好的抗疲勞性;
d)減震能力強(qiáng):碳纖維復(fù)合材料比模量大,自震頻率高,不易出現(xiàn)共震;
e)抗老化性:碳纖維復(fù)合材料在500攝氏度以上才會被空氣中的氧氧化,而且它被機(jī)體完全保護(hù)起來了;
f)可設(shè)計(jì)性強(qiáng):碳纖維復(fù)合材料可編織性強(qiáng);
g)高溫抗性:碳纖維復(fù)合材料可承受2000攝氏度高溫,而強(qiáng)度不變。
2 碳纖維翼子板制作工藝
碳纖維復(fù)合材料翼子板成型工藝分為兩類:1)熱固性工藝;2)熱塑性工藝。
熱固性工藝包括:高壓RTM,濕法模壓,干法模壓,Hybird。
熱塑性工藝包括:LFT-D,TailoredBlank Line。下表1為熱固性工藝和熱塑性工藝的區(qū)別。
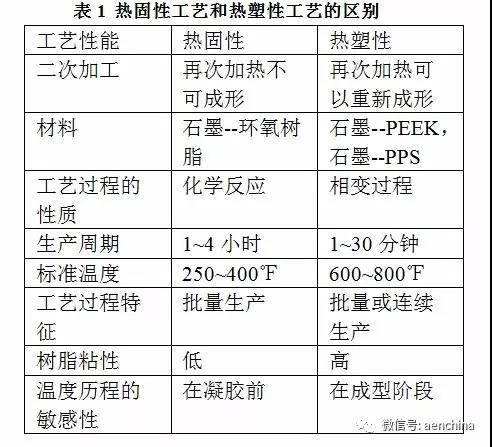
本文主要介紹汽車零部件主要成型工藝:高壓TRM和濕法模壓。
濕法模壓:一種批量生產(chǎn)使用的工藝,適合外形簡單零部件成型。首先進(jìn)行碳纖維原絲鋪層編制、切割、涂膠,最后入模加熱固化成型,見流程圖1。
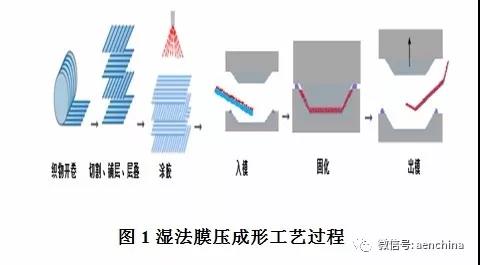
HP-RTM: 一種批量生產(chǎn)使用的工藝,適合外形復(fù)雜零部件成型。首先進(jìn)行碳纖維原絲鋪層編制、切割、入模、預(yù)成型、合模置入樹脂,最后固化成型,見流程圖2。
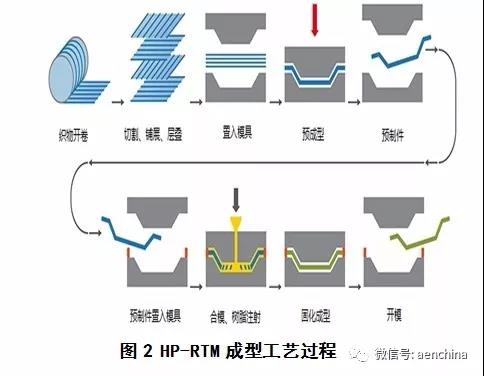
3 某車型碳纖維翼子板設(shè)計(jì)
碳纖維復(fù)合材料在整車上設(shè)計(jì)流程如圖3。
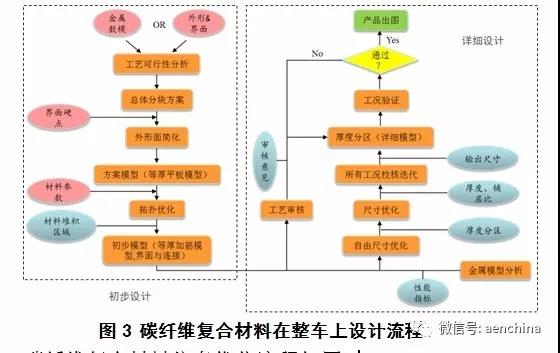
碳纖維復(fù)合材料仿真優(yōu)化流程如圖4
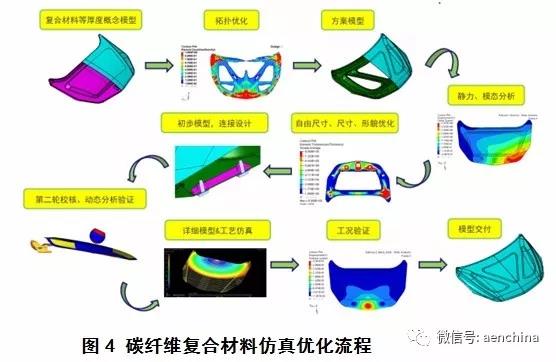
翼子板作為重要的車身組成部分,剛度是首先需要滿足的性能要求,任何輕量化技術(shù)的研究也應(yīng)以滿足剛度為前提,表2示出某車型1.6mm碳纖維翼子板和0.7mm鋼板翼子板性能參數(shù)對比。
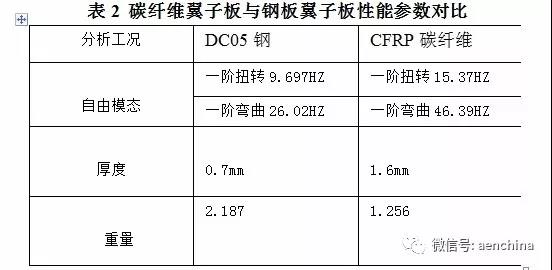
本次某車型碳纖維翼子板厚度選用的是1.6mm,重量為1.256kg。制作翼子板使用材料為平紋機(jī)織CFRP,單層厚度為0.2mm,材料強(qiáng)度為300Mpa,通過Abaqus軟件仿真計(jì)算得到1.6mm厚度碳纖維翼子板滿足部件性能要求,且剛度遠(yuǎn)遠(yuǎn)超過要求,表明翼子板存在很大的優(yōu)化設(shè)計(jì)空間。
采用OptiStruct軟件中的尺寸優(yōu)化方法進(jìn)行CFRP翼子板的結(jié)構(gòu)優(yōu)化設(shè)計(jì),結(jié)果如圖5。根據(jù)設(shè)計(jì)經(jīng)驗(yàn)并考慮制造工藝,休整改進(jìn)優(yōu)化結(jié)果,改進(jìn)后翼子板的造型面及安裝面保持不變,以保證翼子板外形及正常裝配,改變翼子板厚度,以便在減重的同時(shí)滿足性能要求,優(yōu)化結(jié)果表示1.4mmCFRP翼子板就滿足了性能要求。
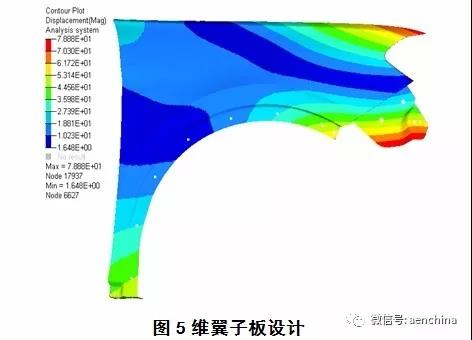
碳纖維增強(qiáng)復(fù)合材料的特性主要表現(xiàn)在力學(xué)性能、熱物理性能、熱燒蝕性能、可設(shè)計(jì)性和耐沖擊性等幾個(gè)方面,碳纖維復(fù)合材料翼子板優(yōu)點(diǎn):
a) 阻尼較高,較好的隔音性能;
b) 剛度較高,提高閥蓋抗凹性;
c) 減重50%以上,提高鎖、鉸鏈耐久性;
d) 較高的模態(tài),提高NVH性能;
e) 集成化設(shè)計(jì),內(nèi)板可集成加強(qiáng)板,減少零件個(gè)數(shù)
f) 直接安裝,不需要改線。
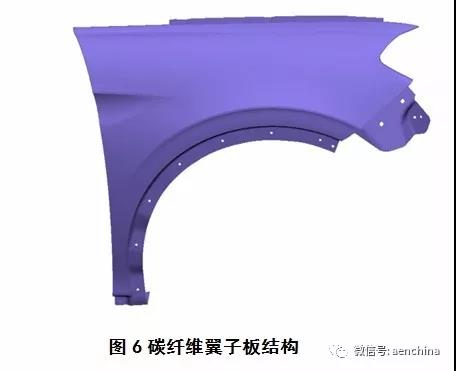
4 結(jié) 論
降低車重只有三種途徑,一是結(jié)構(gòu)優(yōu)化設(shè)計(jì),二是先進(jìn)的工藝,三是輕量化材料應(yīng)用。前兩者在現(xiàn)有技術(shù)上已很難再繼續(xù)突破,只有應(yīng)用輕量化材料才是最有效的減重徑。碳纖維復(fù)合材料是未來汽車輕量化發(fā)展的重要方向,但成本高、樣件制造周期長、設(shè)計(jì)不成熟和維修問題是當(dāng)前國內(nèi)需要主要攻破的瓶頸。因此,要想使碳纖維復(fù)合材料在汽車輕量化中大量應(yīng)用必須首先要降低碳纖維的生產(chǎn)成本,通過改進(jìn)原絲生產(chǎn)工藝,降低原絲成本;發(fā)展新的預(yù)氧化、碳化和石墨化技術(shù),縮短預(yù)氧化時(shí)間,降低碳化、石墨化成本,從而達(dá)到降低碳纖維成本達(dá)到汽車節(jié)能減排的作用。
單位:華晨汽車工程研究能量管理室
前言
汽車輕量化是實(shí)現(xiàn)汽車節(jié)能減排的重要途徑,已成為世界汽車發(fā)展的潮流,研究表明,汽油乘用車每減重100kg將節(jié)油0.39L/100km,汽車質(zhì)量每降低10%,可降低油耗6%~8%,排放下降4%。各大主機(jī)廠已紛紛采取不同技術(shù)降低汽車整備質(zhì)量,其中以復(fù)合材料代替鋼板材料成為輕量化技術(shù)的重要發(fā)展方向,目前應(yīng)用在汽車零部件的復(fù)合材料主要有碳纖維和玻璃纖維兩大類,碳纖維復(fù)合材料擁有絕佳的任性和抗拉強(qiáng)度,其密度在1.45~1.6g/cm³,拉伸強(qiáng)度可達(dá)1.5GPa以上,超過鋁合金的3倍,接近超高強(qiáng)度鋼的水平。碳纖維復(fù)合材料翼子板在保證普通鋼板材料翼子板性能外減重約50%,有效的降低汽車整備質(zhì)量達(dá)到節(jié)能減排目的。
1 碳纖維復(fù)合材料應(yīng)用到汽車上的優(yōu)勢
碳纖維復(fù)合材料零部件已成為各大主機(jī)廠重要發(fā)展方向,其應(yīng)用到汽車上的七大優(yōu)勢如下:
a)輕量化:提高車體本身性能,減重50%,節(jié)能省油;
b)安全性:同等體積,碳纖維本身拉伸強(qiáng)度是鋼板材料的7-9倍,能最大減少傳到駕駛室的能量;
c)抗疲勞性:碳纖維較細(xì),缺陷少,機(jī)體塑形好,可以抑制裂紋發(fā)展,具有良好的抗疲勞性;
d)減震能力強(qiáng):碳纖維復(fù)合材料比模量大,自震頻率高,不易出現(xiàn)共震;
e)抗老化性:碳纖維復(fù)合材料在500攝氏度以上才會被空氣中的氧氧化,而且它被機(jī)體完全保護(hù)起來了;
f)可設(shè)計(jì)性強(qiáng):碳纖維復(fù)合材料可編織性強(qiáng);
g)高溫抗性:碳纖維復(fù)合材料可承受2000攝氏度高溫,而強(qiáng)度不變。
2 碳纖維翼子板制作工藝
碳纖維復(fù)合材料翼子板成型工藝分為兩類:1)熱固性工藝;2)熱塑性工藝。
熱固性工藝包括:高壓RTM,濕法模壓,干法模壓,Hybird。
熱塑性工藝包括:LFT-D,TailoredBlank Line。下表1為熱固性工藝和熱塑性工藝的區(qū)別。
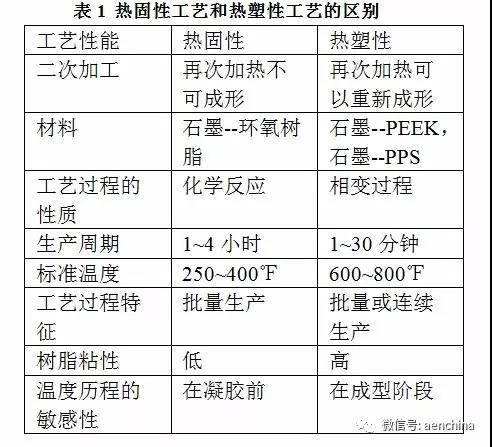
本文主要介紹汽車零部件主要成型工藝:高壓TRM和濕法模壓。
濕法模壓:一種批量生產(chǎn)使用的工藝,適合外形簡單零部件成型。首先進(jìn)行碳纖維原絲鋪層編制、切割、涂膠,最后入模加熱固化成型,見流程圖1。
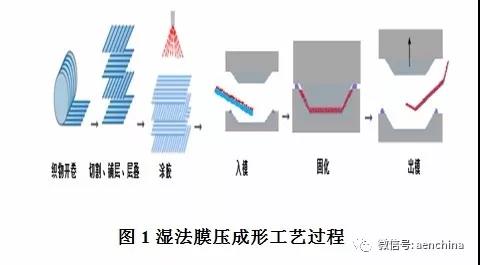
HP-RTM: 一種批量生產(chǎn)使用的工藝,適合外形復(fù)雜零部件成型。首先進(jìn)行碳纖維原絲鋪層編制、切割、入模、預(yù)成型、合模置入樹脂,最后固化成型,見流程圖2。
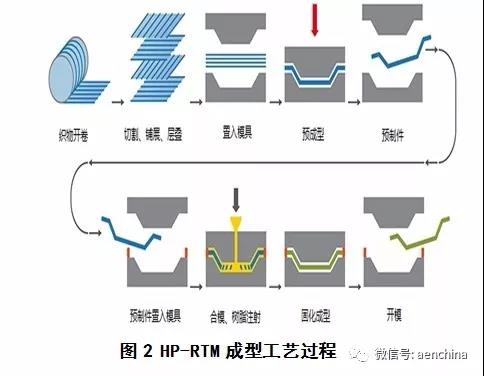
3 某車型碳纖維翼子板設(shè)計(jì)
碳纖維復(fù)合材料在整車上設(shè)計(jì)流程如圖3。
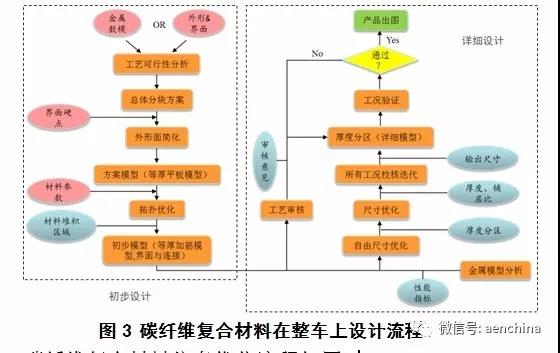
碳纖維復(fù)合材料仿真優(yōu)化流程如圖4
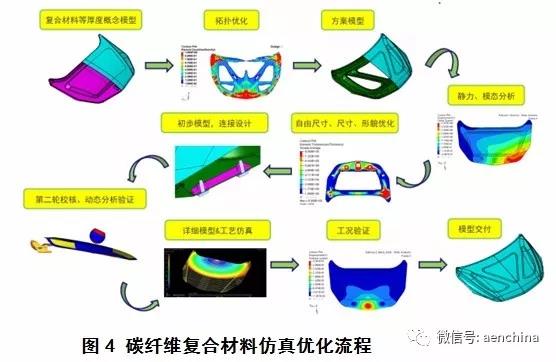
翼子板作為重要的車身組成部分,剛度是首先需要滿足的性能要求,任何輕量化技術(shù)的研究也應(yīng)以滿足剛度為前提,表2示出某車型1.6mm碳纖維翼子板和0.7mm鋼板翼子板性能參數(shù)對比。
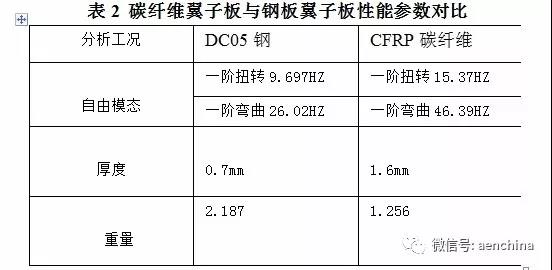
本次某車型碳纖維翼子板厚度選用的是1.6mm,重量為1.256kg。制作翼子板使用材料為平紋機(jī)織CFRP,單層厚度為0.2mm,材料強(qiáng)度為300Mpa,通過Abaqus軟件仿真計(jì)算得到1.6mm厚度碳纖維翼子板滿足部件性能要求,且剛度遠(yuǎn)遠(yuǎn)超過要求,表明翼子板存在很大的優(yōu)化設(shè)計(jì)空間。
采用OptiStruct軟件中的尺寸優(yōu)化方法進(jìn)行CFRP翼子板的結(jié)構(gòu)優(yōu)化設(shè)計(jì),結(jié)果如圖5。根據(jù)設(shè)計(jì)經(jīng)驗(yàn)并考慮制造工藝,休整改進(jìn)優(yōu)化結(jié)果,改進(jìn)后翼子板的造型面及安裝面保持不變,以保證翼子板外形及正常裝配,改變翼子板厚度,以便在減重的同時(shí)滿足性能要求,優(yōu)化結(jié)果表示1.4mmCFRP翼子板就滿足了性能要求。
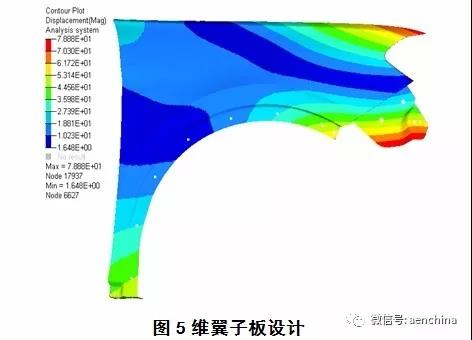
碳纖維增強(qiáng)復(fù)合材料的特性主要表現(xiàn)在力學(xué)性能、熱物理性能、熱燒蝕性能、可設(shè)計(jì)性和耐沖擊性等幾個(gè)方面,碳纖維復(fù)合材料翼子板優(yōu)點(diǎn):
a) 阻尼較高,較好的隔音性能;
b) 剛度較高,提高閥蓋抗凹性;
c) 減重50%以上,提高鎖、鉸鏈耐久性;
d) 較高的模態(tài),提高NVH性能;
e) 集成化設(shè)計(jì),內(nèi)板可集成加強(qiáng)板,減少零件個(gè)數(shù)
f) 直接安裝,不需要改線。
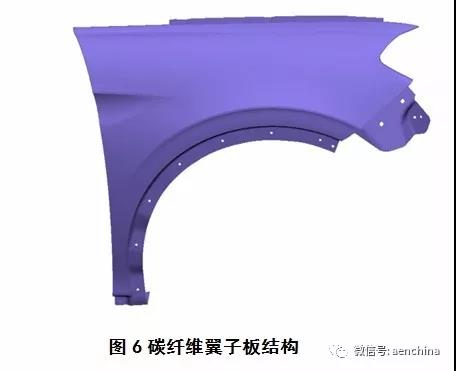
4 結(jié) 論
降低車重只有三種途徑,一是結(jié)構(gòu)優(yōu)化設(shè)計(jì),二是先進(jìn)的工藝,三是輕量化材料應(yīng)用。前兩者在現(xiàn)有技術(shù)上已很難再繼續(xù)突破,只有應(yīng)用輕量化材料才是最有效的減重徑。碳纖維復(fù)合材料是未來汽車輕量化發(fā)展的重要方向,但成本高、樣件制造周期長、設(shè)計(jì)不成熟和維修問題是當(dāng)前國內(nèi)需要主要攻破的瓶頸。因此,要想使碳纖維復(fù)合材料在汽車輕量化中大量應(yīng)用必須首先要降低碳纖維的生產(chǎn)成本,通過改進(jìn)原絲生產(chǎn)工藝,降低原絲成本;發(fā)展新的預(yù)氧化、碳化和石墨化技術(shù),縮短預(yù)氧化時(shí)間,降低碳化、石墨化成本,從而達(dá)到降低碳纖維成本達(dá)到汽車節(jié)能減排的作用。
編輯推薦
最新資訊
-
跨越速運(yùn)憑什么“圈粉”萬千客戶?“
2025-07-01 14:42
-
數(shù)智破局啟新篇?生態(tài)共生再啟程 —
2025-06-27 20:13
-
助力汽車零部件產(chǎn)線智能化升級,西門
2025-06-27 13:59
-
BBA集體轉(zhuǎn)向!放棄全面電動化
2025-06-26 17:32
-
比換柜省錢,比自研省心,西門子Xcel
2025-06-25 15:07