汽車轉(zhuǎn)向節(jié)全自動(dòng)柔性線的開發(fā)
2018-04-27 22:10:10· 來源:汽車工藝師 作者:王效勇 孟繁純
隨著重型載貨汽車需求的急劇擴(kuò)張,市場(chǎng)競(jìng)爭(zhēng)日趨激烈,汽車零部件制造水平和生產(chǎn)能力直接或間接地影響著整車的競(jìng)爭(zhēng)。柔性化生產(chǎn)和精益化制造成為汽車零部件制造業(yè)追求的理念,高質(zhì)量、高效率、低成本運(yùn)行的生產(chǎn)制造系統(tǒng)成為汽車零部件企業(yè)的迫切期望。我公司基于柔性制造技術(shù)理念,廣泛應(yīng)用集成加工和復(fù)合加工技術(shù),自主開發(fā)了重型載貨汽車轉(zhuǎn)向節(jié)加工流程和制造工藝,結(jié)合當(dāng)今成熟的“CNC”機(jī)床、機(jī)器人和自動(dòng)化技術(shù),開發(fā)并實(shí)現(xiàn)了重型載貨汽車轉(zhuǎn)向節(jié)全自動(dòng)加工線應(yīng)用。
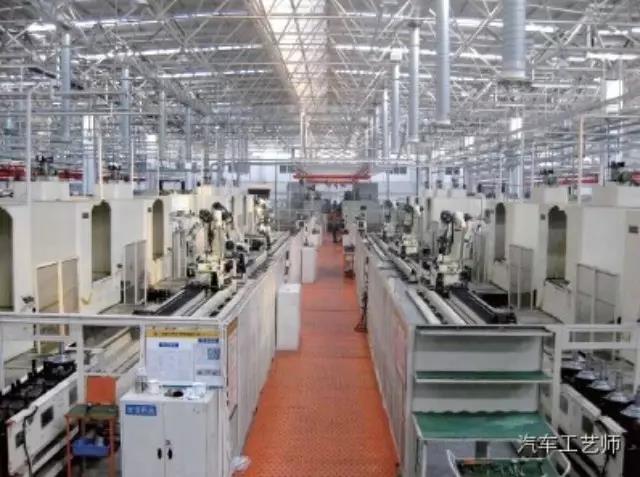
隨著重型載貨汽車需求的急劇擴(kuò)張,市場(chǎng)競(jìng)爭(zhēng)日趨激烈,汽車零部件制造水平和生產(chǎn)能力直接或間接地影響著整車的競(jìng)爭(zhēng)。柔性化生產(chǎn)和精益化制造成為汽車零部件制造業(yè)追求的理念,高質(zhì)量、高效率、低成本運(yùn)行的生產(chǎn)制造系統(tǒng)成為汽車零部件企業(yè)的迫切期望。我公司基于柔性制造技術(shù)理念,廣泛應(yīng)用集成加工和復(fù)合加工技術(shù),自主開發(fā)了重型載貨汽車轉(zhuǎn)向節(jié)加工流程和制造工藝,結(jié)合當(dāng)今成熟的“CNC”機(jī)床、機(jī)器人和自動(dòng)化技術(shù),開發(fā)并實(shí)現(xiàn)了重型載貨汽車轉(zhuǎn)向節(jié)全自動(dòng)加工線應(yīng)用。
重型載貨汽車轉(zhuǎn)向節(jié)加工現(xiàn)狀
1.轉(zhuǎn)向節(jié)加工流程及設(shè)備
國(guó)內(nèi)外對(duì)于轉(zhuǎn)向節(jié)的加工工藝多以專用機(jī)床、通用機(jī)床或以專用機(jī)床、通用機(jī)床、加工中心等組成加工線,分成十幾道或二十幾道加工工序。比較典型的加工流程如圖1所示。
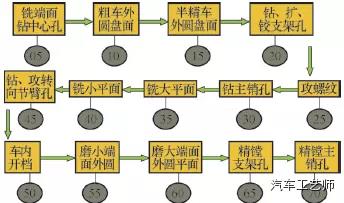
圖1 轉(zhuǎn)向節(jié)典型的加工流程示意
使用專機(jī)加工出用于加工軸頸所需的中心孔(05序),支承軸頸主要以粗車(10序)、精車(15序)、磨削(55、60序)等工藝方法加工完成。法蘭、支架部分主要以鉆、擴(kuò)、鉸、銑、鏜、拉等工藝方法實(shí)現(xiàn)。主要設(shè)備以通用機(jī)床、專機(jī)、數(shù)控車床、加工中心等設(shè)備實(shí)現(xiàn)上述流程??紤]各工序加工能力的平衡,比較成熟的一條加工生產(chǎn)線含20~21臺(tái)設(shè)備,加工能力約240件/天(三班制)。
2.轉(zhuǎn)向節(jié)典型加工流程分析
典型的轉(zhuǎn)向節(jié)加工工藝流程存在下列特征:
1)工序受到傳統(tǒng)加工方式的束縛,雖然使用了數(shù)控車、加工中心等較先進(jìn)的設(shè)備,但基準(zhǔn)多次轉(zhuǎn)換,
數(shù)控設(shè)備難以發(fā)揮最大效率,加工產(chǎn)品的精度不夠穩(wěn)定。
2)因結(jié)構(gòu)特征和工序內(nèi)容約束,加工工序多,產(chǎn)品轉(zhuǎn)型局限性較大。
3)設(shè)備結(jié)構(gòu)和布局限制,生產(chǎn)線較長(zhǎng),在制品占用量大,難以實(shí)現(xiàn)一個(gè)流生產(chǎn),生產(chǎn)效率難以實(shí)現(xiàn)最大化,精益化管理推行困難。
對(duì)國(guó)外多家重型載貨汽車轉(zhuǎn)向節(jié)加工線的了解、考察得知,其主要是以數(shù)控專機(jī)、加工中心等設(shè)備組成的生產(chǎn)線,雖然設(shè)備精度較高,但各工序單機(jī)作業(yè),柔性差,生產(chǎn)管理也同樣受到制約。目前國(guó)內(nèi)外重型載貨汽車轉(zhuǎn)向節(jié)加工基本未實(shí)現(xiàn)將工藝系統(tǒng)、物流系統(tǒng)、信息技術(shù)有效結(jié)合,無法實(shí)現(xiàn)快速、敏捷、柔性化生產(chǎn)。
自動(dòng)線策劃、分析
1.自動(dòng)線策劃的目標(biāo)
國(guó)際先進(jìn)制造技術(shù)系統(tǒng)應(yīng)對(duì)的是市場(chǎng)需求的快速反應(yīng),實(shí)現(xiàn)敏捷化制造。該系統(tǒng)的構(gòu)成應(yīng)該包含了
創(chuàng)新設(shè)計(jì)、前沿技術(shù)、制造組織、監(jiān)控、物流、信息等內(nèi)容的系統(tǒng)化工程。基于企業(yè)自身發(fā)展的需要,對(duì)重型載貨汽車轉(zhuǎn)向節(jié)加工自動(dòng)線的策劃至少應(yīng)實(shí)現(xiàn)先進(jìn)工藝制造技術(shù)、信息技術(shù)、自動(dòng)化技術(shù)、管理技術(shù)的集成應(yīng)用,保證生產(chǎn)線高效率、高質(zhì)量、低成本運(yùn)行,滿足重型汽車對(duì)轉(zhuǎn)向節(jié)產(chǎn)品變化、制造精度、可靠一致性及生產(chǎn)能力的需要。
2.先進(jìn)工藝制造技術(shù)保證流程再造
在金屬切削加工領(lǐng)域,復(fù)合加工技術(shù)正以其獨(dú)特的優(yōu)勢(shì),不斷拓展應(yīng)用空間。如復(fù)合加工機(jī)床一次裝夾可實(shí)現(xiàn)車、銑、鉆、鏜、攻螺紋等多種工序內(nèi)容的加工;復(fù)合刀具實(shí)現(xiàn)多工步加工一次成形。其最突出優(yōu)點(diǎn)是極大縮短工件的制造周期,提高工件加工精度和品質(zhì)一致性。
(1)流程再造的工藝技術(shù)分析 基于復(fù)合加工先進(jìn)技術(shù)理念的認(rèn)識(shí),數(shù)控設(shè)備的集成、精準(zhǔn)、高速、自動(dòng)化、數(shù)字化等功能的發(fā)揮,對(duì)轉(zhuǎn)向節(jié)加工工藝簡(jiǎn)約化處理,達(dá)到流程再造目的實(shí)現(xiàn)。經(jīng)過論證分析,OP10工序,充分利用可交換工作臺(tái)的臥式加工中心將主銷孔(φ 78mm、φ 56mm孔)、支架面、開擋面等粗加工內(nèi)容和中心孔、支銷孔(φ 30mm孔)等精加工用于后續(xù)定位的內(nèi)容在一道工序?qū)崿F(xiàn);OP20工序,將各級(jí)軸頸加工面、盤面螺紋、軸頸端面等內(nèi)容利用高精度數(shù)控車銑復(fù)合機(jī)床實(shí)現(xiàn)粗精加工一次完成;OP30工序,利用軸頸定位,將主銷孔(φ 78mm、φ 56mm孔)、支銷孔(φ 30mm孔)、支架面、開擋面等內(nèi)容的精加工在一道工序完成,三道工序是可以實(shí)現(xiàn)的(工藝流程見圖2)。
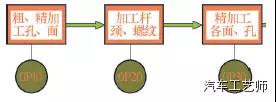
圖 2
(2)工藝過程難點(diǎn)預(yù)測(cè)控制 OP10的加工只能用毛坯面定位,工件抓取、定位、加工的可靠性和準(zhǔn)確性,直接影響后續(xù)基準(zhǔn)和加工精度,乃至設(shè)備運(yùn)行安全性。OP20的加工要實(shí)現(xiàn)定位準(zhǔn)確和夾緊可靠,系統(tǒng)動(dòng)靜平衡,確保軸頸粗精加工,以車代磨一次完成,螺紋加工準(zhǔn)確分度功能實(shí)現(xiàn)。OP30夾具需要保證定位的準(zhǔn)確性,必須具有工件裝夾準(zhǔn)確檢測(cè)功能,保證最終相關(guān)尺寸和位置的正確性,機(jī)械手抓取安全、準(zhǔn)確、正確必須控制。包括工件狀態(tài)識(shí)別、位置控制、夾持控制,信息交換等技術(shù)的把握。
(3)柔性制造技術(shù)的運(yùn)用 自動(dòng)線應(yīng)具備先進(jìn)的柔性制造功能,主要表現(xiàn)在:自動(dòng)線設(shè)備可根據(jù)所加工產(chǎn)品的需要,通過簡(jiǎn)單地更換夾具元器件來實(shí)現(xiàn)零件的多品種加工;對(duì)加工產(chǎn)品的批量可根據(jù)需要迅速調(diào)整,對(duì)加工產(chǎn)品的性能參數(shù)變化,可迅速變更并及時(shí)恢復(fù)生產(chǎn);可迅速而有效地綜合應(yīng)用新技術(shù)、新工藝、新刀具,快速改變生產(chǎn)運(yùn)營(yíng)效率和成本;對(duì)產(chǎn)品換型需求變化及特殊要求能迅速做出反應(yīng),適應(yīng)瞬息萬變的市場(chǎng)需求。
(4)高速加工制造技術(shù)的運(yùn)用 自動(dòng)線對(duì)機(jī)床的要求是高速度、高精度、高精度保持性(工程能力指數(shù)C m/C mk)和高耐久性運(yùn)轉(zhuǎn),對(duì)刀具的要求是利用新材料,以達(dá)到高的切削速度和進(jìn)給速度。
(5)加工能力分析和設(shè)備布局 原有成熟的重型載貨汽車轉(zhuǎn)向節(jié)一條加工生產(chǎn)線(左、右產(chǎn)品混線)含22臺(tái)設(shè)備,加工能力約240件/天(三班制),加工節(jié)拍5min/件。按新策劃的加工工藝流程各工序加工內(nèi)容進(jìn)行節(jié)拍評(píng)估:OP10需要12min/件,OP20需要8min/件,OP30需要12min/件。綜合考慮、生產(chǎn)組織、物料管理和敏捷制造,策劃將新的加工線按左右線分開,以適應(yīng)突發(fā)事件。左線:OP10臥式加工中心三臺(tái),OP20數(shù)控車銑復(fù)合機(jī)床兩臺(tái),OP30臥式加工中心三臺(tái)。右線:OP10臥式加工中心三臺(tái),OP20數(shù)控車銑復(fù)合機(jī)床兩臺(tái),OP30臥式加工中心三臺(tái)。
(6)物料輸送系統(tǒng) 根據(jù)設(shè)備布局結(jié)構(gòu)和生產(chǎn)線各環(huán)境要求控制分析,結(jié)合機(jī)器人運(yùn)行速度和動(dòng)作精度,設(shè)置六臺(tái)機(jī)器人(每條線三臺(tái)),分別完成各工序間工件輸送、上/下料、狀態(tài)識(shí)別和檢測(cè)等工作。輔助設(shè)施由抓取系統(tǒng)、運(yùn)行系統(tǒng)、物料輸入/輸出系統(tǒng)、中間周轉(zhuǎn)/檢測(cè)系統(tǒng)及各類傳感器組成。
(7)控制、信息系統(tǒng) 包括中央控制臺(tái)、網(wǎng)絡(luò)及軟件、警示/報(bào)警/顯示和安全防護(hù)系統(tǒng)。
重型載貨汽車轉(zhuǎn)向節(jié)自動(dòng)加工線
基于上述的策劃和分析,對(duì)重型載貨汽車轉(zhuǎn)向節(jié)自動(dòng)線設(shè)計(jì)開發(fā),并得以順利實(shí)施。這條自動(dòng)加工線由計(jì)算機(jī)網(wǎng)絡(luò)全方位控制,通過機(jī)器人完成數(shù)控加工中心與車銑復(fù)合加工機(jī)床工序交換,實(shí)現(xiàn)了全線從毛坯到成品的自動(dòng)化制造,將原來多道加工工序壓縮為三道,達(dá)到集制造加工技術(shù)、自動(dòng)化技術(shù)和信息技術(shù)于一體的柔性制造技術(shù)應(yīng)用(見圖3)。
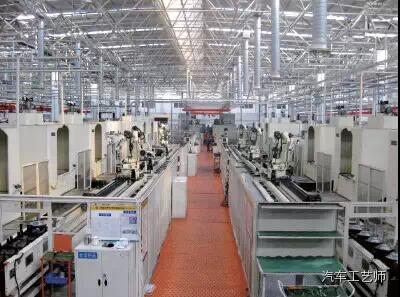
圖3 重型載貨汽車轉(zhuǎn)向節(jié)自動(dòng)加工線
1.中心控制系統(tǒng)介紹
轉(zhuǎn)向節(jié)自動(dòng)線由CNC機(jī)床、機(jī)器人、上下料裝置、周轉(zhuǎn)/檢測(cè)臺(tái)及操作臺(tái)組合,這些部分的動(dòng)作和邏輯控制由系統(tǒng)主控部分負(fù)責(zé),系統(tǒng)主控采用日本三菱的Q系列大型PLC進(jìn)行控制,Q系列CPU是模塊化的PLC,這使系統(tǒng)具有很強(qiáng)的可擴(kuò)展性和可維護(hù)性。PLC的控制程序采用了較為容易理解的梯形圖語言進(jìn)行編程,采用了模塊化編程,方便系統(tǒng)的調(diào)試和后期故障診斷與維修。PLC與CNC機(jī)床之間通信采用了較為流行的Profibus–DP現(xiàn)場(chǎng)總線,這種通信方式能夠使使通信速率和抗干擾性得到保證,而且采用總線結(jié)構(gòu),使系統(tǒng)接線得到了簡(jiǎn)化,對(duì)于后期維護(hù)也提供了方便。
操作臺(tái)硬件采用了PROFACE公司的真彩觸摸屏,觸摸屏與PLC之間通信采用了以太網(wǎng)結(jié)構(gòu)的通信方式,這使系統(tǒng)的控制線路硬件結(jié)構(gòu)和接線大大簡(jiǎn)化,在觸摸屏上不僅能夠?qū)ο到y(tǒng)進(jìn)行操作,而且能夠顯示系統(tǒng)及CNC機(jī)床的報(bào)警信息、產(chǎn)量信息、系統(tǒng)I/O狀態(tài)等信息,還能對(duì)機(jī)床刀具進(jìn)行壽命管理。機(jī)器人程序?yàn)榇ㄆ楣镜腁S編程語言,此語言類似于計(jì)算機(jī)C語言,方便理解,機(jī)器人動(dòng)作由示教方式進(jìn)行確定,這種方式便于后期對(duì)動(dòng)作位置進(jìn)行調(diào)整。機(jī)器人與機(jī)床之間的動(dòng)作邏輯由PLC進(jìn)行控制,保證了動(dòng)作的可靠性。
2.自動(dòng)線運(yùn)行過程實(shí)效簡(jiǎn)介
定時(shí)將工件毛坯放置到上料自動(dòng)輸送裝置上后,上料裝置檢測(cè)開關(guān)檢測(cè)到有工件時(shí)開始運(yùn)行將工件運(yùn)送到等待位,等待位檢測(cè)開關(guān)檢測(cè)到有工件時(shí)機(jī)器人執(zhí)行抓取工件程序,將工件抓到機(jī)器人卡爪上(見圖4)。在卡爪上加裝限位開關(guān),當(dāng)卡爪有工件時(shí),限位開關(guān)動(dòng)作發(fā)出信號(hào),執(zhí)行裝料程序,當(dāng)卡爪上無工件時(shí),限位開關(guān)無動(dòng)作或提示報(bào)警。
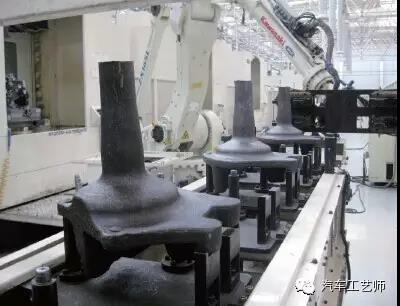
圖 4
當(dāng)加工中心加工完畢時(shí),機(jī)器人將執(zhí)行上下料程序。當(dāng)機(jī)床夾具松開后,機(jī)器人將完成工序加工的工件取出,然后將毛坯工件裝入機(jī)床夾具,夾具夾緊動(dòng)作準(zhǔn)確完成后,機(jī)器人移動(dòng)將已加工工件放入周轉(zhuǎn)/檢測(cè)臺(tái)(見圖5)。
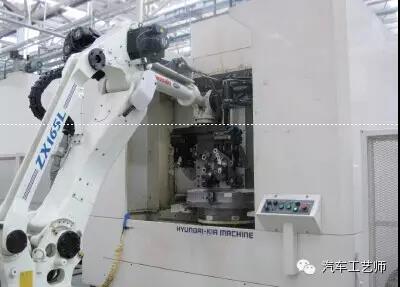
圖 5
通過同樣的控制方式實(shí)現(xiàn)OP20的工件自動(dòng)裝卸。由于OP20復(fù)合加工機(jī)床的結(jié)構(gòu)特點(diǎn)。所以機(jī)床尾座上加裝三個(gè)接近開關(guān),加載工件時(shí)頂尖向前,頂住工件時(shí),觸發(fā)裝載到位接近開關(guān),發(fā)出裝載完畢信號(hào),當(dāng)無工件時(shí),頂尖向前觸發(fā)頂尖過位開關(guān),當(dāng)頂尖退回時(shí),觸發(fā)退回到位接近開關(guān),發(fā)出退回到位信號(hào)(見圖6)。
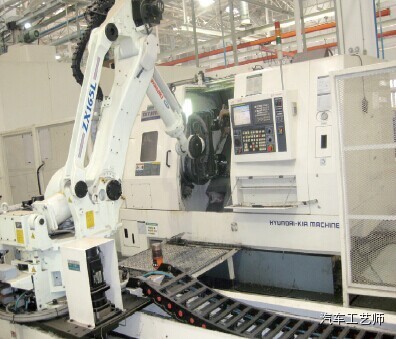
圖 6
OP20工序增加了工件在線檢測(cè)功能。當(dāng)線外檢測(cè)臺(tái)發(fā)出要求檢測(cè)的信號(hào),則機(jī)器人將工件放到檢測(cè)臺(tái)上,檢測(cè)完畢后按下檢測(cè)完畢按鈕,發(fā)出檢測(cè)完畢信號(hào),機(jī)器人再將工件從檢測(cè)臺(tái)上取下。如果沒有要求檢測(cè)信號(hào),則機(jī)器人直接將工件放入下一工序的周轉(zhuǎn)/檢測(cè)臺(tái)上(見圖7)。最后一道工序的工件加工完畢后,機(jī)器人將工件放置到下料輸送裝置上,當(dāng)下料裝置的檢測(cè)開關(guān)檢測(cè)到有工件時(shí)則裝置運(yùn)行,將工件向外移送一步,等待操作工將完工件取走(見圖8)。
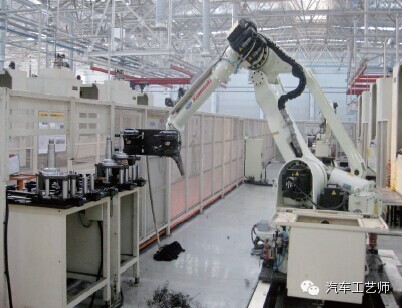
圖 7
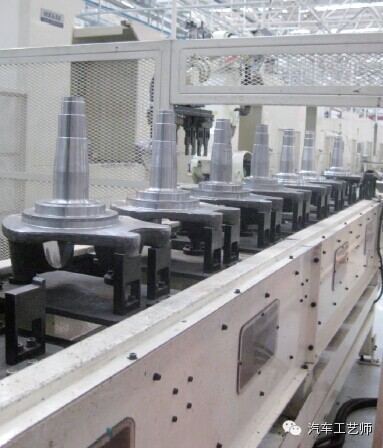
圖 8
在OP30工序同樣增加了工件在線檢測(cè)功能。
自動(dòng)加工線的先進(jìn)技術(shù)及先進(jìn)工藝的應(yīng)用
自動(dòng)生產(chǎn)線運(yùn)用了先進(jìn)的自動(dòng)物料輸入/輸出系統(tǒng)、工件在夾具中自動(dòng)準(zhǔn)確定位系統(tǒng)、氣密檢測(cè)系統(tǒng)、狀態(tài)識(shí)別、在線診斷、檢測(cè)、刀具壽命管理、破損檢測(cè)系統(tǒng)、加工管理系統(tǒng)、柔性、復(fù)合加工技術(shù)和以車削代磨削等多項(xiàng)先進(jìn)技術(shù),創(chuàng)新了重型載貨汽車轉(zhuǎn)向節(jié)加工工藝。
1.自動(dòng)線夾具,氣密檢測(cè)系統(tǒng)
無人操作的自動(dòng)線,系統(tǒng)需有準(zhǔn)確的識(shí)別工件在夾具準(zhǔn)確定位及夾緊狀態(tài)判別功能。氣密檢測(cè)系統(tǒng)應(yīng)用保證了工件在每個(gè)工位夾具的定位正確。在每臺(tái)機(jī)床的夾具各定位面上配有氣道結(jié)構(gòu),工件正確定位后即可把氣道封閉,否則會(huì)漏氣。自動(dòng)線系統(tǒng)配置氣密檢測(cè)裝置,其特點(diǎn)是:可檢測(cè)系統(tǒng)壓力,可自動(dòng)保壓,可調(diào)節(jié)驅(qū)動(dòng)壓力,從而達(dá)到調(diào)節(jié)出口壓力的目的。當(dāng)工件正確定位后系統(tǒng)的壓力保持不變,自動(dòng)線將按正確的程序運(yùn)行。當(dāng)夾具的定位面上氣道漏氣時(shí),系統(tǒng)壓力下降,則系統(tǒng)報(bào)警,程序停止運(yùn)行,確保工件正確安裝。
2.刀具壽命管理、破損檢測(cè)系統(tǒng)
自動(dòng)線配有刀具壽命管理和破損檢測(cè)系統(tǒng)。系統(tǒng)中備有正確的各類關(guān)鍵刀具徑向及軸向尺寸的記憶。刀具在加工完成后需移動(dòng)至檢測(cè)開關(guān)位置進(jìn)行檢測(cè),如與正確記憶發(fā)生偏差,系統(tǒng)將報(bào)警。
對(duì)正常使用的刀具,根據(jù)刀具的切削性能和使用壽命,對(duì)各種刀具的使用狀況進(jìn)行統(tǒng)計(jì)。確定刀具使用壽命,按編制刀具使用/更換說明書執(zhí)行。
3.數(shù)據(jù)管理系統(tǒng)
自動(dòng)線配有先進(jìn)的數(shù)據(jù)管理系統(tǒng)。
(1)生產(chǎn)運(yùn)行的管理 每臺(tái)機(jī)床輸入輸出運(yùn)行狀況,生產(chǎn)量的記憶(包括每個(gè)時(shí)段、每小時(shí)、每個(gè)班、每天、每月產(chǎn)量運(yùn)行狀況)在顯示屏一目了然。
(2)設(shè)備運(yùn)行的管理 自動(dòng)線六臺(tái)臥式加工中心、兩臺(tái)車銑復(fù)合加工機(jī)床和三臺(tái)機(jī)器人在總控制臺(tái)顯示屏中均有標(biāo)識(shí),通過不同顏色顯示設(shè)備運(yùn)行狀態(tài)。設(shè)備如出現(xiàn)故障,系統(tǒng)也將準(zhǔn)確顯示故障的原因。
(3)工件上下料及安裝運(yùn)行狀態(tài)的管理系統(tǒng) 工件在運(yùn)行或安裝中發(fā)生異常,系統(tǒng)也將報(bào)警顯示。
4.在線診斷、檢測(cè)
自動(dòng)線在每個(gè)工位旁均設(shè)有線外檢測(cè)平臺(tái),機(jī)器人將按照設(shè)定的程序、按照工藝要求的檢驗(yàn)頻次,按程序?qū)⒐ぜ胖脵z測(cè)平臺(tái),操作工檢測(cè)后發(fā)出信號(hào),合格件通過機(jī)器人送至下工序運(yùn)行。
5.以車削代替磨削新工藝
汽車制造業(yè)的大多數(shù)零件是在熱處理后進(jìn)行最終精度或形狀的加工,車削正作為替代磨削的一種經(jīng)濟(jì)性方法在普及。目前,國(guó)外越來越多的企業(yè)已認(rèn)識(shí)到車削的優(yōu)點(diǎn)。在發(fā)達(dá)國(guó)家的汽車工業(yè)中,多種軸類、套類零件大多采用車工藝,收到良好效果。
以車代磨存在以下優(yōu)點(diǎn):加工效率高;設(shè)備投資少,維護(hù)費(fèi)用低,適合柔性生產(chǎn)要求;可使零件獲得良好的表面加工質(zhì)量;車削是潔凈加工工藝。在轉(zhuǎn)向節(jié)自動(dòng)線實(shí)施過程中的技術(shù)關(guān)鍵之一在于,工裝配重的調(diào)節(jié)以及因機(jī)床工裝等的問題造成大小頭及橢圓。由于轉(zhuǎn)向節(jié)是不對(duì)稱的回轉(zhuǎn)體,且精車時(shí)切削速度高。要求車夾按每批零件的差異,調(diào)整動(dòng)平衡量。
轉(zhuǎn)向節(jié)全新的加工工藝特點(diǎn)
1)保證工藝的合理性。轉(zhuǎn)向節(jié)加工線使原來的二十幾道工序的加工工藝變?yōu)槿拦ば?。工序集中使相互位置精度質(zhì)量有極大的提高,工藝流程實(shí)現(xiàn)了國(guó)內(nèi)首創(chuàng)。
2)從毛坯到成品的上下料全部由機(jī)器人控制、操作。各工序運(yùn)轉(zhuǎn)安全、可靠,實(shí)現(xiàn)了柔性制造技術(shù)在國(guó)內(nèi)中、大型零件的應(yīng)用。
3)自動(dòng)線工件的上料、定位需正確、可靠,夾具配有氣密檢測(cè)機(jī)構(gòu),通過氣密檢測(cè)工件定位的正確與否。
4)通過配置高精度平衡夾具,實(shí)現(xiàn)了先進(jìn)冷擠壓刀具的應(yīng)用。總結(jié)出合理的加工參數(shù),保證工件的表面粗糙度,達(dá)到了材料表面變性處理的效果,提高了工件的材料強(qiáng)度性能。
5)自動(dòng)線運(yùn)行過程中,通過工件加工質(zhì)量的在線檢測(cè),保證在線工件的加工質(zhì)量。在線檢測(cè)刀具的磨損狀況,及時(shí)校正刀具補(bǔ)償環(huán)節(jié),保證工件加工質(zhì)量水平的準(zhǔn)確性和一致性。
6)配有自動(dòng)線配有嚴(yán)密管理系統(tǒng),包括生產(chǎn)運(yùn)行的管理、設(shè)備運(yùn)行的管理、工件上下料及安裝運(yùn)行狀態(tài)的管理系統(tǒng)等。
結(jié)語
由我公司自主開發(fā)的轉(zhuǎn)向節(jié)柔性自動(dòng)線,具有高精度、高效和自動(dòng)化等特點(diǎn),使生產(chǎn)線僅需操作工36人,與原來兩條轉(zhuǎn)向節(jié)線所需168名操作工相比減少了132人,僅此一項(xiàng)每年可節(jié)約人工成本264萬元。自動(dòng)線的加工效率比以專機(jī)組成的加工線提高了30%,年利潤(rùn)增加近1000萬元。同時(shí)消除了人為因素在生產(chǎn)制造過程中的影響,極大地提高工程保證能力,體現(xiàn)了產(chǎn)品制造的高品質(zhì)和高一致性。
該生產(chǎn)線方案新穎、簡(jiǎn)捷、超前,加工流程自動(dòng)化程度高,產(chǎn)品質(zhì)量穩(wěn)定,已經(jīng)獲得國(guó)內(nèi)外許多用戶及同行的贊譽(yù),也得到了機(jī)床裝備業(yè)的高度認(rèn)可,極大提高了公司的在國(guó)內(nèi)外重型載貨汽車零部件領(lǐng)域的地位及知名度,推動(dòng)了中國(guó)汽車工藝裝備邁向世界,提升了制造工藝流程創(chuàng)新發(fā)展。
編輯推薦
最新資訊
-
跨越速運(yùn)憑什么“圈粉”萬千客戶?“
2025-07-01 14:42
-
數(shù)智破局啟新篇?生態(tài)共生再啟程 —
2025-06-27 20:13
-
助力汽車零部件產(chǎn)線智能化升級(jí),西門
2025-06-27 13:59
-
BBA集體轉(zhuǎn)向!放棄全面電動(dòng)化
2025-06-26 17:32
-
比換柜省錢,比自研省心,西門子Xcel
2025-06-25 15:07