基于DEFORM的直齒錐齒輪復(fù)合鍛造冷整成形
2018-02-08 15:41:28· 來(lái)源:鍛造與沖壓
齒輪是傳動(dòng)系統(tǒng)和轉(zhuǎn)向系統(tǒng)的關(guān)鍵核心零件,如何改善優(yōu)化齒輪性能得到越來(lái)越多研究學(xué)者的關(guān)注。傳統(tǒng)的齒輪加工方法為切削加工和鍛造,相比切削加工鍛造可獲得完整的金屬流線、更優(yōu)的材料組織和性能,獲得更可靠更安全和使用壽命更長(zhǎng)的齒輪產(chǎn)品。
齒輪是傳動(dòng)系統(tǒng)和轉(zhuǎn)向系統(tǒng)的關(guān)鍵核心零件,如何改善優(yōu)化齒輪性能得到越來(lái)越多研究學(xué)者的關(guān)注。傳統(tǒng)的齒輪加工方法為切削加工和鍛造,相比切削加工鍛造可獲得完整的金屬流線、更優(yōu)的材料組織和性能,獲得更可靠更安全和使用壽命更長(zhǎng)的齒輪產(chǎn)品。雖然熱精鍛加工精度高,但是加工時(shí)由于高溫易發(fā)生氧化作用,影響工件的表面精度和表面質(zhì)量。近年來(lái),熱鍛冷整復(fù)合加工工藝不僅具備熱鍛工藝的優(yōu)勢(shì),獲得具備完整流線的工件,還可減小中間成形步,降低成形載荷,冷整工序可保證工件的尺寸精度和表面質(zhì)量,提高齒輪的使用壽命,是齒輪復(fù)合鍛造成形工藝中重要的一環(huán)。因此有必要對(duì)冷整成形工藝進(jìn)行優(yōu)化設(shè)計(jì),以保證最佳成形質(zhì)量。
隨著計(jì)算機(jī)技術(shù)的不斷發(fā)展,實(shí)際生產(chǎn)中,為優(yōu)化產(chǎn)品工藝、減小生產(chǎn)周期、降低生產(chǎn)成本,數(shù)值模擬方法得到廣泛應(yīng)用。本文基于熱鍛冷整復(fù)合加工工藝,利用DEFORM軟件對(duì)直齒錐齒輪復(fù)合鍛造冷整工序進(jìn)行數(shù)值模擬,提出優(yōu)化方案并進(jìn)行成形驗(yàn)證,對(duì)直齒錐齒輪復(fù)合鍛造成形工藝設(shè)計(jì)具有指導(dǎo)意義。
有限元模型及模擬方案
有限元模型的建立
本文基于熱鍛冷整成形工藝,模擬工序?yàn)闊徨懞蟮睦湔ば?。選取兩個(gè)不同齒高、齒厚的直齒錐齒輪熱鍛成形件,運(yùn)用Pro/E建立直齒錐齒輪與上下模具的三維模型,并保存為stl文件導(dǎo)入DEFORM軟件進(jìn)行有限元數(shù)值模擬。圖1為直齒錐齒輪熱鍛成形件示意圖,圖2為模具的有限元數(shù)值模擬模型。
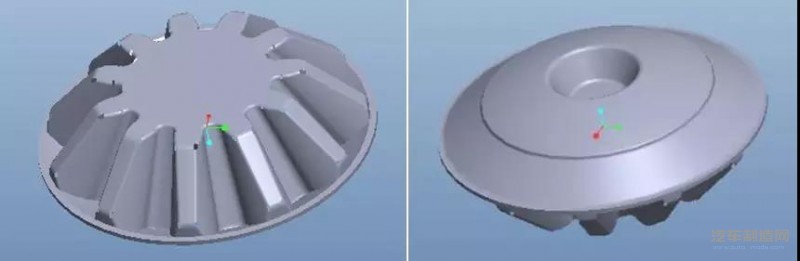
圖1 直齒錐齒輪熱鍛件示意圖
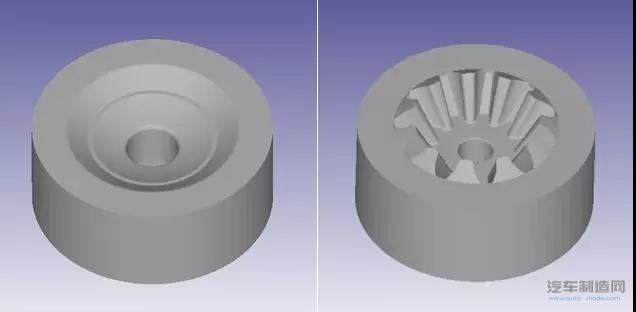
圖2 模具有限元模擬模型
模擬參數(shù)設(shè)置
熱鍛件/冷整成形件尺寸對(duì)比和模擬參數(shù)設(shè)置如表1所示。
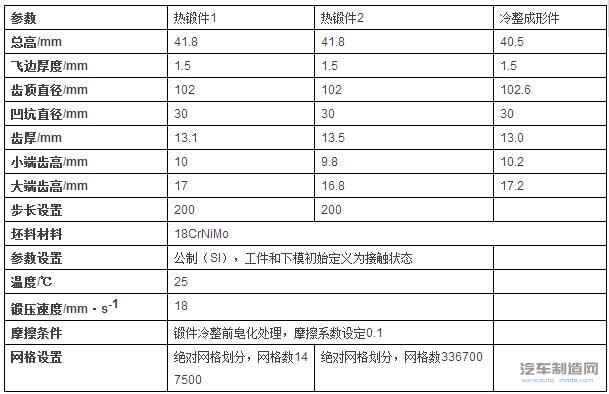
有限元數(shù)值模擬結(jié)果與分析
成形載荷分析
圖3為不同熱鍛件尺寸冷整時(shí)上模對(duì)應(yīng)的行程載荷,二者行程載荷相差較大。這是由于熱鍛件1齒厚較小、齒高較高,冷整時(shí)直齒錐齒輪齒頂和齒根區(qū)域先于齒面區(qū)域與上模發(fā)生并保持接觸,材料流動(dòng)所受阻力增加且材料變形范圍小,齒頂、齒根區(qū)域承受的作用力大,齒面受力較小。熱鍛件2由于減小了齒高增大了齒厚,齒面先于齒頂與上模發(fā)生接觸作用,直齒錐齒輪可自由流動(dòng)材料增加且變形范圍擴(kuò)大,有效降低了成形載荷。
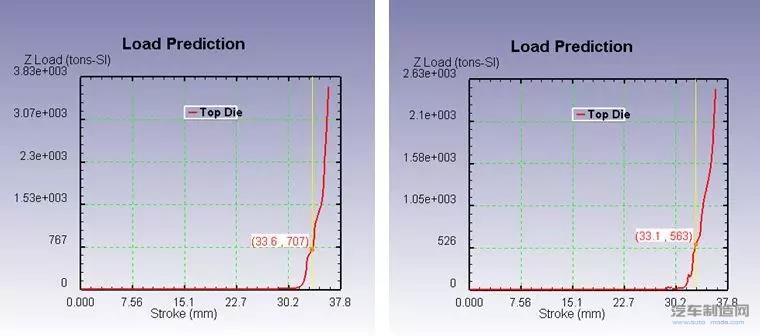
(a)熱鍛件1冷整成形載荷曲線 (b)熱鍛件2冷整成形載荷曲線
圖3 上模載荷行程曲線
金屬流動(dòng)速度場(chǎng)分析
圖4為不同齒高、齒厚熱鍛件冷整工序最終材料流動(dòng)情況。圖4(a)為高齒高薄齒厚的熱鍛件1,上模下行,與工件發(fā)生接觸并發(fā)生擠壓,從而使齒面材料向齒頂流動(dòng),因此齒頂存在一定的速度場(chǎng);下模與工件始終處于接觸階段,在冷整過(guò)程中材料流動(dòng)受到下模限制,其向飛邊區(qū)域以及工件底部流動(dòng);最大流動(dòng)速度在工件底部區(qū)域,為40mm/s。圖4(b)為齒高減小0.2mm、齒厚增加0.4mm的熱鍛成形件,由于齒厚增加,工件受到上模的擠壓作用,齒面材料向齒頂流動(dòng),因此齒頂存在材料流動(dòng)速度場(chǎng),且齒面平均流動(dòng)速度比熱鍛件1增加了約1.5倍,齒面冷整效果良好;由于冷整過(guò)程中下模與工件始終接觸,其材料流動(dòng)受下模的限制作用,所以材料向飛邊區(qū)域和工件底部流動(dòng);最大流動(dòng)速度在工件底部區(qū)域。工件減小齒高、增加齒厚后最大材料流動(dòng)速度減小,可能原因是上模與工件接觸后,工件齒面發(fā)生的形變?cè)龃?,齒頂面受到的擠壓力變小,導(dǎo)致工件底部受到的擠壓力減小,底部材料流動(dòng)速度減小。
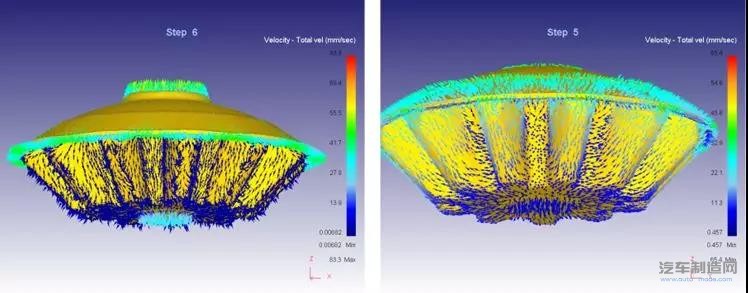
(a)熱鍛件1冷整工序材料流動(dòng)速度場(chǎng) (b)熱鍛件2材料流動(dòng)速度場(chǎng)
圖4 材料流動(dòng)速度場(chǎng)
應(yīng)力應(yīng)變分析
熱鍛件1和熱鍛件2最終成形對(duì)應(yīng)的應(yīng)力、應(yīng)變圖如圖5、圖6所示。通過(guò)對(duì)比可知,隨著變形的完成,熱鍛件1最大應(yīng)力為834MPa,熱鍛件2最大應(yīng)力為827MPa,熱鍛件1齒根處出現(xiàn)了應(yīng)力集中區(qū)域,可能會(huì)導(dǎo)致成形件在工作中更容易失效減小其使用壽命。由圖6可知,熱鍛件2的平均應(yīng)變比熱鍛件1小,熱鍛件1齒根齒頂區(qū)域應(yīng)變大,說(shuō)明熱鍛件2的材料流動(dòng)更為合理。熱鍛件1的應(yīng)變分布差值較大,應(yīng)變分布不均可能會(huì)導(dǎo)致附加應(yīng)力和殘余應(yīng)力的產(chǎn)生,影響成形件精度,影響傳動(dòng)過(guò)程中的平穩(wěn)性。
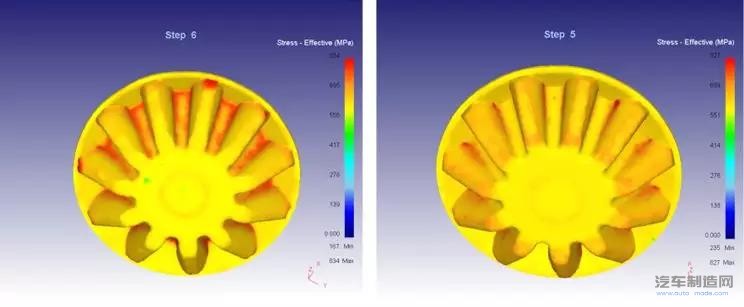
(a)熱鍛件1應(yīng)力分布圖 (b)熱鍛件2應(yīng)力分布圖
圖5 應(yīng)力分布圖
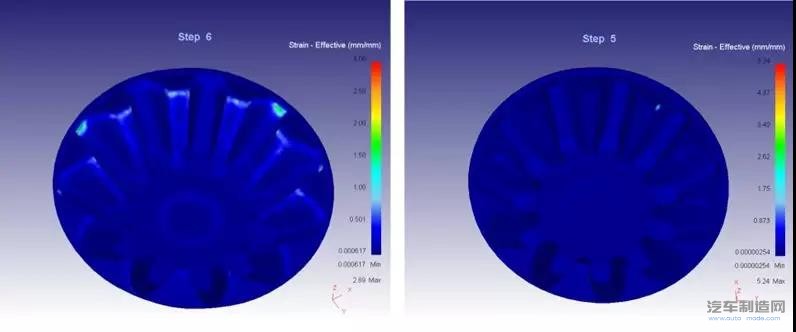
(a)熱鍛件1應(yīng)變分布圖 (b)熱鍛件2應(yīng)變分布圖
圖6 應(yīng)變分布圖
成形對(duì)比試驗(yàn)
傳統(tǒng)單一的熱/溫模鍛造或者冷精鍛工藝無(wú)法滿足產(chǎn)品要求,本文基于復(fù)合鍛造(熱鍛冷整)工藝進(jìn)行成形實(shí)驗(yàn)對(duì)比,將前文中數(shù)值模擬的方案1和方案2進(jìn)行實(shí)際鍛造加工,在冷整上一工序,即熱鍛工序修整直齒錐齒輪齒高、齒厚,圖7為方案1和方案2成形件對(duì)比圖。圖中灰白色部分屬于未精整部分,圖7(a)中大面積灰白色區(qū)域分布在齒面上,可能的原因是熱鍛工序溫度較高,冷卻時(shí)成形件收縮較大,導(dǎo)致冷整時(shí)由于齒厚偏小導(dǎo)致冷整不到位;圖7(b)為優(yōu)化后的冷整件,即增加熱鍛件齒厚減小齒高,增加齒厚充分考慮到熱鍛坯冷收縮量及模具彈性變形,確保齒面被精整達(dá)到加工要求,減小齒高是為了增加材料流動(dòng)空間,減小模具的承載力提高模具使用壽命,從圖中可以看出灰白色區(qū)域分布于成形件的齒頂和齒高部分,齒面被完全精整,符合加工要求。成形試驗(yàn)結(jié)果驗(yàn)證了數(shù)值模擬結(jié)果的可靠性,說(shuō)明了方案2可以有效優(yōu)化復(fù)合鍛造工藝,顯著提高成形質(zhì)量。
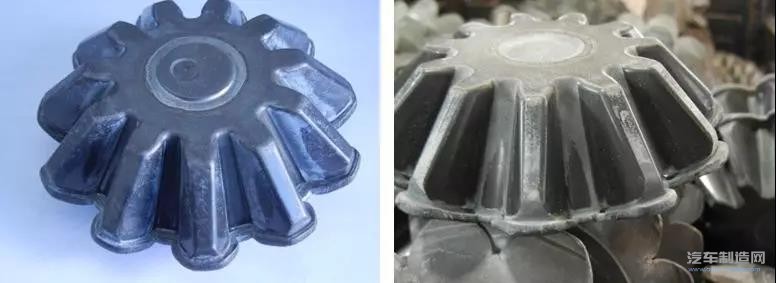
(a)方案1冷整直齒錐齒輪 (b)方案2冷整直齒錐齒輪
圖7 直齒錐齒輪冷整成形件對(duì)比圖
結(jié)論
本文針對(duì)熱鍛冷整復(fù)合鍛造工藝中的冷整工序,對(duì)直齒錐齒輪冷整成形進(jìn)行有限元數(shù)值模擬。通過(guò)對(duì)不同齒厚、齒高的直齒錐齒輪冷整成形過(guò)程中的成形載荷、流動(dòng)速度場(chǎng)、應(yīng)力應(yīng)變的分析,對(duì)直齒錐齒輪齒厚、齒高進(jìn)行了修正和優(yōu)化。通過(guò)成形實(shí)驗(yàn)結(jié)果對(duì)比分析發(fā)現(xiàn),適當(dāng)?shù)脑黾育X厚、減小齒高可有效提高冷整工序的產(chǎn)品合格率,降低模具成形載荷,提高模具使用壽命,對(duì)實(shí)際的鍛造生產(chǎn)加工具有指導(dǎo)意義。
隨著計(jì)算機(jī)技術(shù)的不斷發(fā)展,實(shí)際生產(chǎn)中,為優(yōu)化產(chǎn)品工藝、減小生產(chǎn)周期、降低生產(chǎn)成本,數(shù)值模擬方法得到廣泛應(yīng)用。本文基于熱鍛冷整復(fù)合加工工藝,利用DEFORM軟件對(duì)直齒錐齒輪復(fù)合鍛造冷整工序進(jìn)行數(shù)值模擬,提出優(yōu)化方案并進(jìn)行成形驗(yàn)證,對(duì)直齒錐齒輪復(fù)合鍛造成形工藝設(shè)計(jì)具有指導(dǎo)意義。
有限元模型及模擬方案
有限元模型的建立
本文基于熱鍛冷整成形工藝,模擬工序?yàn)闊徨懞蟮睦湔ば?。選取兩個(gè)不同齒高、齒厚的直齒錐齒輪熱鍛成形件,運(yùn)用Pro/E建立直齒錐齒輪與上下模具的三維模型,并保存為stl文件導(dǎo)入DEFORM軟件進(jìn)行有限元數(shù)值模擬。圖1為直齒錐齒輪熱鍛成形件示意圖,圖2為模具的有限元數(shù)值模擬模型。
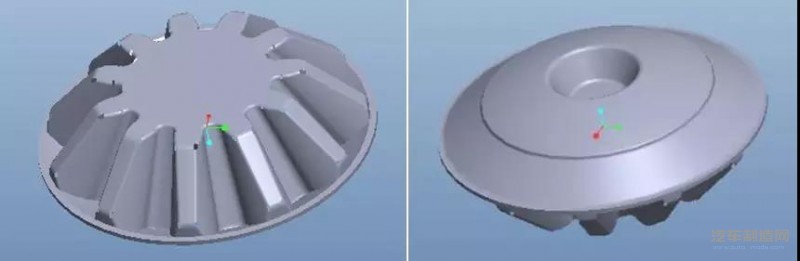
圖1 直齒錐齒輪熱鍛件示意圖
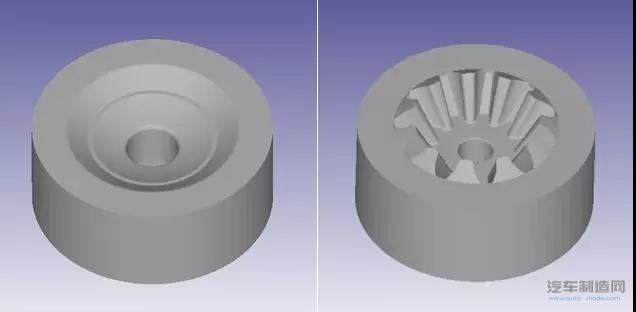
圖2 模具有限元模擬模型
模擬參數(shù)設(shè)置
熱鍛件/冷整成形件尺寸對(duì)比和模擬參數(shù)設(shè)置如表1所示。
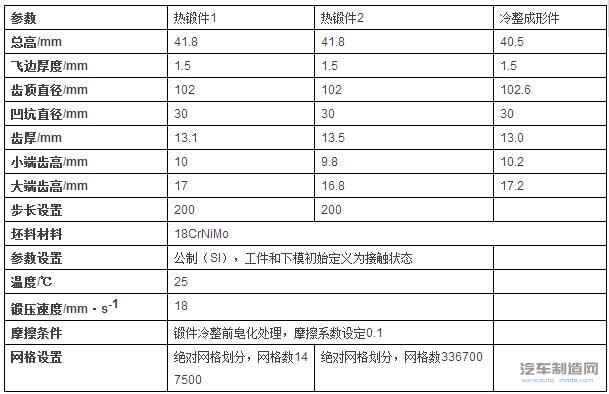
有限元數(shù)值模擬結(jié)果與分析
成形載荷分析
圖3為不同熱鍛件尺寸冷整時(shí)上模對(duì)應(yīng)的行程載荷,二者行程載荷相差較大。這是由于熱鍛件1齒厚較小、齒高較高,冷整時(shí)直齒錐齒輪齒頂和齒根區(qū)域先于齒面區(qū)域與上模發(fā)生并保持接觸,材料流動(dòng)所受阻力增加且材料變形范圍小,齒頂、齒根區(qū)域承受的作用力大,齒面受力較小。熱鍛件2由于減小了齒高增大了齒厚,齒面先于齒頂與上模發(fā)生接觸作用,直齒錐齒輪可自由流動(dòng)材料增加且變形范圍擴(kuò)大,有效降低了成形載荷。
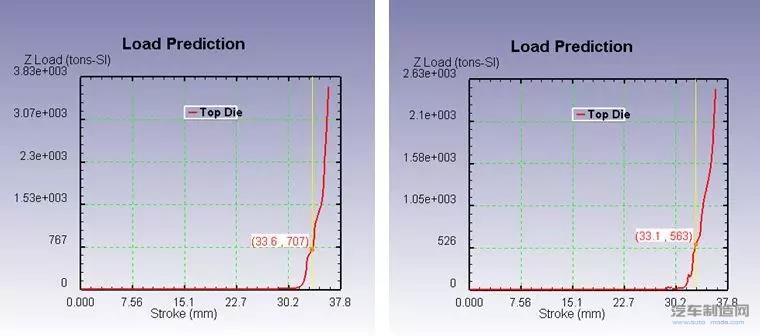
(a)熱鍛件1冷整成形載荷曲線 (b)熱鍛件2冷整成形載荷曲線
圖3 上模載荷行程曲線
金屬流動(dòng)速度場(chǎng)分析
圖4為不同齒高、齒厚熱鍛件冷整工序最終材料流動(dòng)情況。圖4(a)為高齒高薄齒厚的熱鍛件1,上模下行,與工件發(fā)生接觸并發(fā)生擠壓,從而使齒面材料向齒頂流動(dòng),因此齒頂存在一定的速度場(chǎng);下模與工件始終處于接觸階段,在冷整過(guò)程中材料流動(dòng)受到下模限制,其向飛邊區(qū)域以及工件底部流動(dòng);最大流動(dòng)速度在工件底部區(qū)域,為40mm/s。圖4(b)為齒高減小0.2mm、齒厚增加0.4mm的熱鍛成形件,由于齒厚增加,工件受到上模的擠壓作用,齒面材料向齒頂流動(dòng),因此齒頂存在材料流動(dòng)速度場(chǎng),且齒面平均流動(dòng)速度比熱鍛件1增加了約1.5倍,齒面冷整效果良好;由于冷整過(guò)程中下模與工件始終接觸,其材料流動(dòng)受下模的限制作用,所以材料向飛邊區(qū)域和工件底部流動(dòng);最大流動(dòng)速度在工件底部區(qū)域。工件減小齒高、增加齒厚后最大材料流動(dòng)速度減小,可能原因是上模與工件接觸后,工件齒面發(fā)生的形變?cè)龃?,齒頂面受到的擠壓力變小,導(dǎo)致工件底部受到的擠壓力減小,底部材料流動(dòng)速度減小。
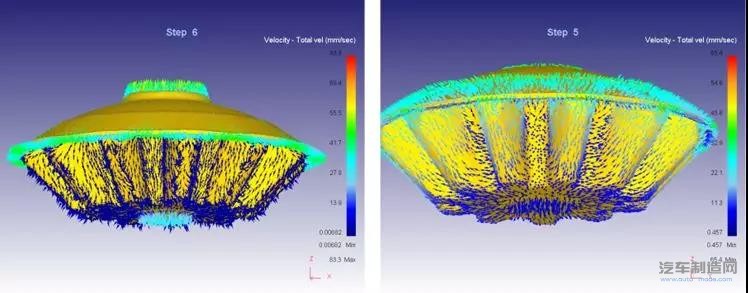
(a)熱鍛件1冷整工序材料流動(dòng)速度場(chǎng) (b)熱鍛件2材料流動(dòng)速度場(chǎng)
圖4 材料流動(dòng)速度場(chǎng)
應(yīng)力應(yīng)變分析
熱鍛件1和熱鍛件2最終成形對(duì)應(yīng)的應(yīng)力、應(yīng)變圖如圖5、圖6所示。通過(guò)對(duì)比可知,隨著變形的完成,熱鍛件1最大應(yīng)力為834MPa,熱鍛件2最大應(yīng)力為827MPa,熱鍛件1齒根處出現(xiàn)了應(yīng)力集中區(qū)域,可能會(huì)導(dǎo)致成形件在工作中更容易失效減小其使用壽命。由圖6可知,熱鍛件2的平均應(yīng)變比熱鍛件1小,熱鍛件1齒根齒頂區(qū)域應(yīng)變大,說(shuō)明熱鍛件2的材料流動(dòng)更為合理。熱鍛件1的應(yīng)變分布差值較大,應(yīng)變分布不均可能會(huì)導(dǎo)致附加應(yīng)力和殘余應(yīng)力的產(chǎn)生,影響成形件精度,影響傳動(dòng)過(guò)程中的平穩(wěn)性。
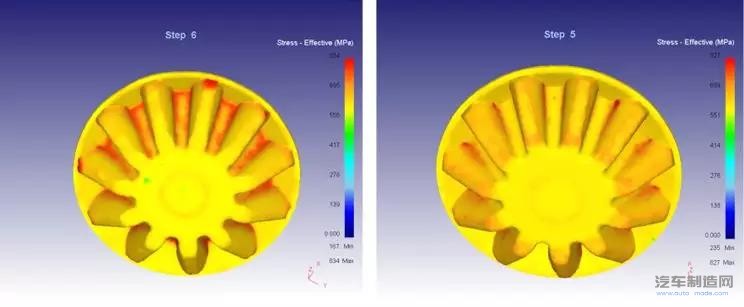
(a)熱鍛件1應(yīng)力分布圖 (b)熱鍛件2應(yīng)力分布圖
圖5 應(yīng)力分布圖
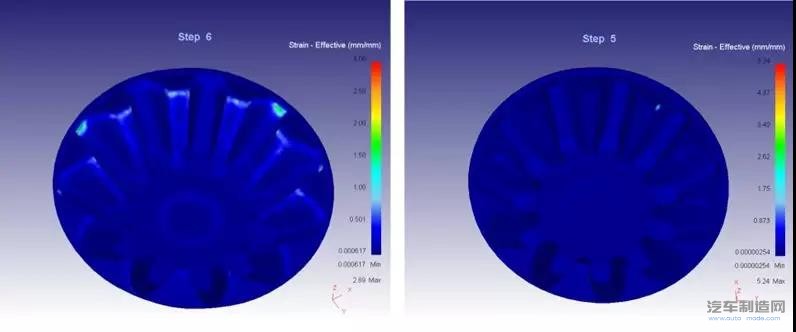
(a)熱鍛件1應(yīng)變分布圖 (b)熱鍛件2應(yīng)變分布圖
圖6 應(yīng)變分布圖
成形對(duì)比試驗(yàn)
傳統(tǒng)單一的熱/溫模鍛造或者冷精鍛工藝無(wú)法滿足產(chǎn)品要求,本文基于復(fù)合鍛造(熱鍛冷整)工藝進(jìn)行成形實(shí)驗(yàn)對(duì)比,將前文中數(shù)值模擬的方案1和方案2進(jìn)行實(shí)際鍛造加工,在冷整上一工序,即熱鍛工序修整直齒錐齒輪齒高、齒厚,圖7為方案1和方案2成形件對(duì)比圖。圖中灰白色部分屬于未精整部分,圖7(a)中大面積灰白色區(qū)域分布在齒面上,可能的原因是熱鍛工序溫度較高,冷卻時(shí)成形件收縮較大,導(dǎo)致冷整時(shí)由于齒厚偏小導(dǎo)致冷整不到位;圖7(b)為優(yōu)化后的冷整件,即增加熱鍛件齒厚減小齒高,增加齒厚充分考慮到熱鍛坯冷收縮量及模具彈性變形,確保齒面被精整達(dá)到加工要求,減小齒高是為了增加材料流動(dòng)空間,減小模具的承載力提高模具使用壽命,從圖中可以看出灰白色區(qū)域分布于成形件的齒頂和齒高部分,齒面被完全精整,符合加工要求。成形試驗(yàn)結(jié)果驗(yàn)證了數(shù)值模擬結(jié)果的可靠性,說(shuō)明了方案2可以有效優(yōu)化復(fù)合鍛造工藝,顯著提高成形質(zhì)量。
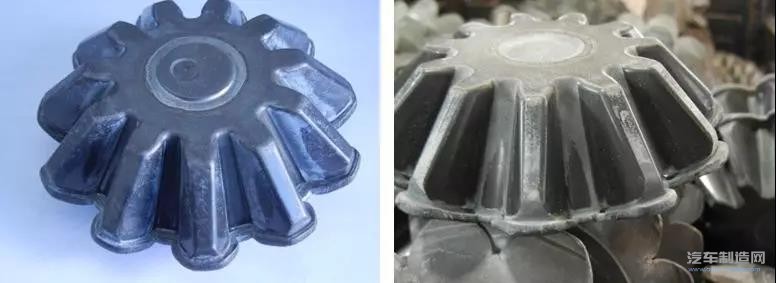
(a)方案1冷整直齒錐齒輪 (b)方案2冷整直齒錐齒輪
圖7 直齒錐齒輪冷整成形件對(duì)比圖
結(jié)論
本文針對(duì)熱鍛冷整復(fù)合鍛造工藝中的冷整工序,對(duì)直齒錐齒輪冷整成形進(jìn)行有限元數(shù)值模擬。通過(guò)對(duì)不同齒厚、齒高的直齒錐齒輪冷整成形過(guò)程中的成形載荷、流動(dòng)速度場(chǎng)、應(yīng)力應(yīng)變的分析,對(duì)直齒錐齒輪齒厚、齒高進(jìn)行了修正和優(yōu)化。通過(guò)成形實(shí)驗(yàn)結(jié)果對(duì)比分析發(fā)現(xiàn),適當(dāng)?shù)脑黾育X厚、減小齒高可有效提高冷整工序的產(chǎn)品合格率,降低模具成形載荷,提高模具使用壽命,對(duì)實(shí)際的鍛造生產(chǎn)加工具有指導(dǎo)意義。
最新資訊
-
跨越速運(yùn)憑什么“圈粉”萬(wàn)千客戶?“
2025-07-01 14:42
-
數(shù)智破局啟新篇?生態(tài)共生再啟程 —
2025-06-27 20:13
-
助力汽車零部件產(chǎn)線智能化升級(jí),西門
2025-06-27 13:59
-
BBA集體轉(zhuǎn)向!放棄全面電動(dòng)化
2025-06-26 17:32
-
比換柜省錢,比自研省心,西門子X(jué)cel
2025-06-25 15:07